约束面投影成型室基底微观特征对透光性的影响
下载: 621次
0 引言
由产品原型快速制造向功能零件大规模直接制造是3D打印技术发展的趋势.面投影光固化3D打印一次成型一个零件截面轮廓[1-3],其打印效率适应直接制造的需求.约束面投影相对于自由面投影工艺具有节约材料、变形小、固化效率高等优点,但其主要工艺问题是固化层在反复从作为成型约束壁面的树脂槽底剥离过程中会发生剥离失效,造成打印失败,从而降低了工艺的可靠性[4-6].
解决打印固化层-基底界面粘附引起的工艺可靠性问题的常规方法主要包括:延长固化时间使树脂过固化以增加层间的结合强度[7];采用具有低表面能的离型膜层减小固化层在基底的粘附力[8-10];优化工艺,如采用两通道系统,使得界面分离所需要克服的法向固相界面间的粘结力转换成的侧向剪切力[11-12],或者通过倾斜剥离使界面分离过程由面分离转变为线分离[13-14].上述方法在一定程度解决了固化层的粘附问题,但同时存在各自的不足:过固化方法存在曝光时间延长制约打印速度,以及变形影响成型精度的问题;采用中间功能膜层方法主要问题是功能膜在基底附着强度不足;优化的剥离方式在减小粘附力的同时附加了多余的动作,从而降低了成型效率.连续液面成型(Continuous Liquid Interface Production, CLIP)工艺利用氧气阻止光固化反应发生,在固化层和树脂槽底面间形成通常称为“阻聚区”的液态树脂区域,从而大大减小粘附力[15].CLIP工艺是目前解决固化层在基底粘附问题最为有效的方案,已经得到一定的应用[16-18],但是该技术采用非晶氟树脂透氧窗,成本高,是规模化应用的障碍.采用核孔膜等代替非晶树脂作为透氧窗在一定程度上可以解决成本问题[19],但是膜的变形影响成型精度.
针对形成阻聚区所需的透氧基底成本和基底变形问题,本文提出一种多孔石英玻璃+聚二甲基硅氧烷(Polydimethylsiloxane,PDMS)膜低成本实现阻聚区的成型室约束基底方案,通过石英玻璃刚性支撑解决膜的变形问题,通过石英玻璃的微孔和PDMS实现透氧.为了探究支撑基底上微孔的引入如何影响透光性及光强分布,从而影响成型精度,对基底表面微孔几何特征对透光性特别是对固化成型区光强分布的影响规律进行了模拟和实验研究.
1 成型基底方案及阻聚区形成机理
1.1 成型室约束基底方案
提出用于形成阻聚区的成型室基底方案如
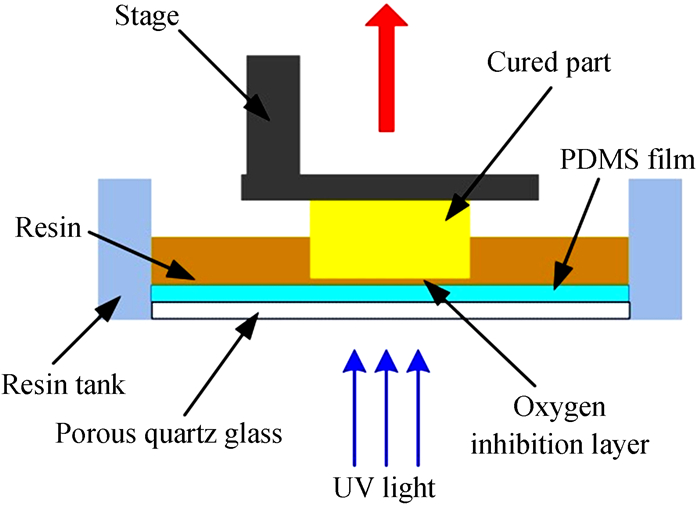
图 1. CLIP工艺中阻聚区形成原理示意图Schematic diagram for the principle of oxygen inhibition layer formation in CLIP process
Fig. 1. CLIP工艺中阻聚区形成原理示意图Schematic diagram for the principle of oxygen inhibition layer formation in CLIP process
1.2 阻聚区形成机理及影响因素
氧的阻聚又称氧的抑制,其基本机理是在聚合反应中,氧气与自由基结合生成比较稳定的过氧化物,造成了自由基的消耗,降低了聚合反应的速率.自由基与氧气的反应速率比与单体分子的聚合反应速率快104~105倍,因此,当存在氧气时,自由基与氧气会快速反应,从而抑制了聚合反应的发生.氧气通过透氧基底扩散到树脂中,树脂中的氧气浓度随着离基底的距离而衰减,直至氧气的抑制能力弱于自由基的聚合能力,树脂的聚合反应才开始[22-24].在消耗所有氧气并且自由基仍然存在的临界距离处,树脂开始完全固化,而这一临界距离就是阻聚区的厚度H,即[15]
式中,ф0为单位时间单位面积入射的光子数量;αPI为光引发剂浓度和波长相关吸收率的乘积;Dc0为树脂的反应活性;C为比例常数.
从式(1)中可以看出,基底的透光性是影响阻聚区的主要因素之一.在PDMS膜与多孔支撑体构成的约束基底条件下,多介质及复杂界面是固化光源的传播路径,固化光源在约束基底的透光率以及通过约束基底后的光强分布特征影响固化效率和精度,因此需要对微观孔隙特征影响光传输特性的规律进行研究.
2 基底微观特征对基底透光性能影响的仿真
基底微观结构将影响阻聚区形成的主要因素之一—透光性,特别是透氧窗的孔隙特征影响固化光源透光基底后在成型区的光强分布,从而影响成型零件的精度.因此通过时域有限差分(Finite Difference Time Domain,FDTD)法对基底微观特征影响透光性能的规律进行了仿真计算,旨在为基底制备提供理论指导.
2.1 计算模型
建立的成型室基底透光性能计算模型如
2.2 求解计算相关说明
采用FDTD Soluions软件进行仿真计算,石英玻璃折射率为2.1,PDMS膜折射率为1.3,光固化树脂折射率为1.8.微孔特征尺寸以固化光源波长为基础在一定范围内取值,其它尺寸参数:多孔玻璃和PDMS厚度均为600 nm,近场监视器距PDMS膜上表面50 nm,远场监视器距PDMS膜上表面1 100 nm.本文所建模型无复杂结构,故选用默认的网格划分.模型边界选用周期性边界条件,用微小单位的透光性能模拟整个约束基底.
2.3 仿真结果及分析
2.3.1 微孔几何形状对透光性的影响
建立了基底具有三角形、方形和圆形三种不同微孔阵列的模型进行了仿真,研究基底微孔几何形状对透光性的影响.其中圆孔直径D=200 nm,三角孔和方形孔的数量和微孔面积率与圆孔相同,除微孔形状外其他参数均一致.结果如
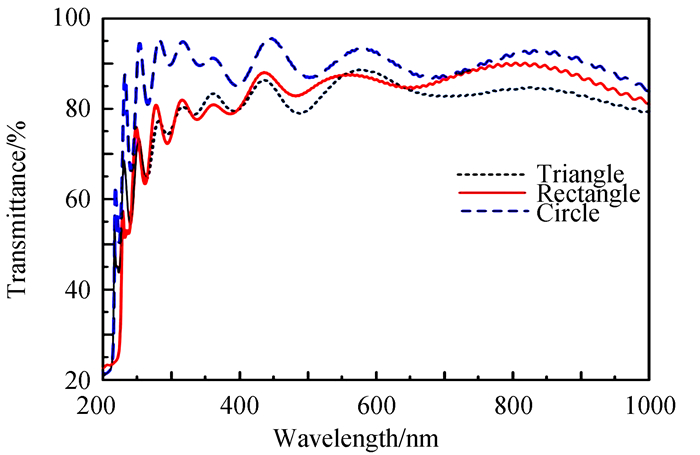
图 3. 不同形状微孔的约束基底的透光率Light transmittance of constraint substrate formed micro-pores with different shapes
Fig. 3. 不同形状微孔的约束基底的透光率Light transmittance of constraint substrate formed micro-pores with different shapes
从
2.3.2 微孔尺寸及周期对不同波长光透过基底后光强分布均匀性的影响
对于约束面投影光固化3D打印,每层固化的截面形状是由经过基底的光源投影决定的,如果基底引入的微孔影响固化区的投影图案,则必然会对成型精度甚至形状产生影响.因此,研究了基底微孔对固化区光强分布的影响规律,主要研究了微孔直径和疏密程度的影响.为了方便起见,定义参数rdw=D/W表达微孔的疏密程度,其中D为圆孔直径,W为孔边缘之间的距离.对波长为400~700 nm的光透过基底后在固化层的光强分布进行了仿真,其中,基底含有不同周期的孔径为200 nm与400 nm圆孔,结果如
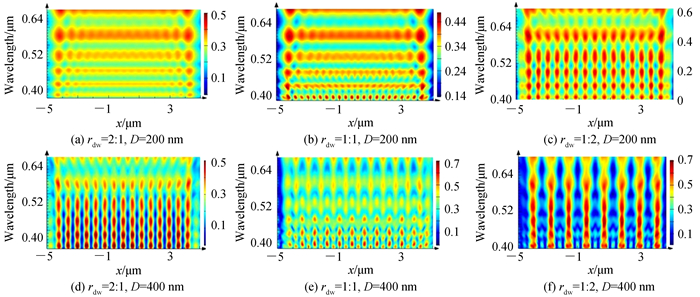
图 4. 微孔尺寸及周期对不同波长光在固化区光强分布均匀性的影响Effect of the size and period of micro-pores on light intensity distribution uniformity with different wavelength in curing zone
Fig. 4. 微孔尺寸及周期对不同波长光在固化区光强分布均匀性的影响Effect of the size and period of micro-pores on light intensity distribution uniformity with different wavelength in curing zone
从
2.3.3 微孔尺寸对特定波长光源透过基底光强分布特征的影响
石英基底纳米尺度微孔阵列加工对制备工艺提出了很高的要求,为了降低基底微孔阵列加工难度,探索了大孔径微孔阵列作为透氧窗在约束投影光固化成型应用的可能性.采用三维计算模型,研究不同尺寸微孔条件下,在固化区的光强分布特征,仿真计算中以实验采用的波长为405 nm的紫外光作为光源,计算基底微孔直径分别为0 nm (即无孔石英玻璃)、200 nm、400 nm、800 nm、1 600 nm时,光源透过基底在成型区一侧的光强分布特征.通过对比不同孔径条件下光强分布与无孔基底光强分布,分析基底微孔尺寸对成型质量的影响,结果如
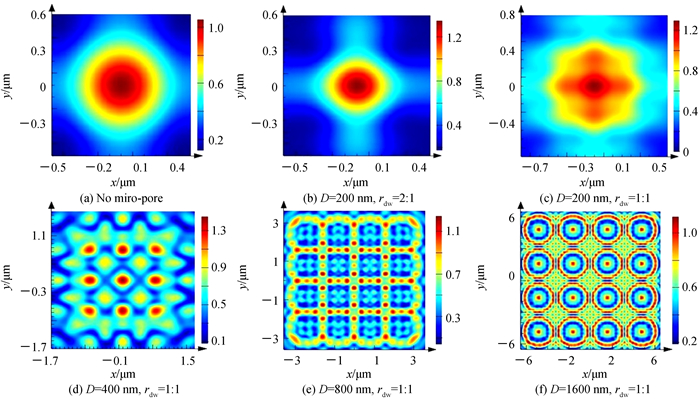
图 5. 不同孔径微孔基底条件下405 nm UV光源在固化区的光强分布特征Light intensity distribution characteristics of 405 nm UV light in curing zone with different size micro-pores
Fig. 5. 不同孔径微孔基底条件下405 nm UV光源在固化区的光强分布特征Light intensity distribution characteristics of 405 nm UV light in curing zone with different size micro-pores
从
3 实验
制备了多孔石英玻璃支撑基底和PDMS膜,并通过搭建的约束投影式光固化成型装置进行了实验研究,通过对固化层表面微观形貌的表征分析和与仿真结果的对比,验证了仿真结果的正确性.
3.1 实验装置及实验方法
采用自行研制的约束面投影光固化成型装置进行实验,实验装置如
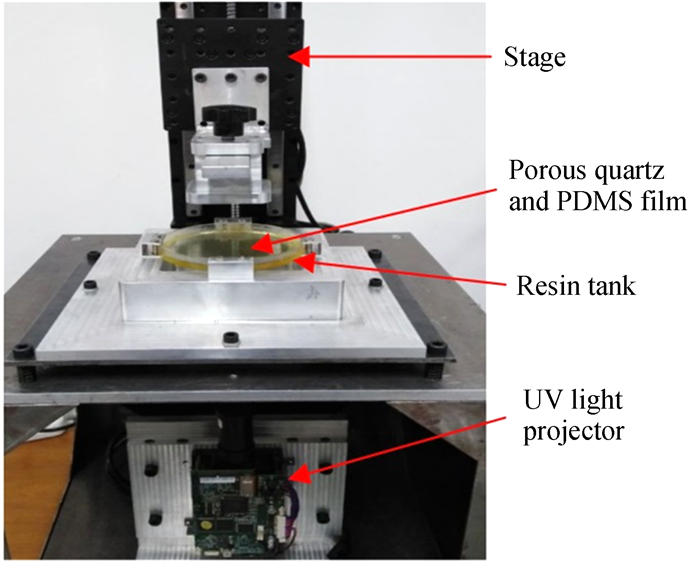
图 6. 约束面投影光固化成型装置Setup of constrained-surface projection-based stereolithography
Fig. 6. 约束面投影光固化成型装置Setup of constrained-surface projection-based stereolithography
玻璃基底的微孔阵列采用纳秒激光加工方法制备,PDMS薄膜的制备采用液态浇铸法,主要工艺流程包括聚合物(PDMS胶)的浇铸、真空去气泡、加热固化等.将PDM膜粘附在多孔玻璃表面作为约束基底进行实验,并采用Leica DCM 3D型共聚焦干涉显微镜对固化成型件的表面进行观测.
3.2 实验结果与讨论
受制备工艺条件的限制,玻璃基底的微孔较大,微孔直径为400 μm,制备结果如
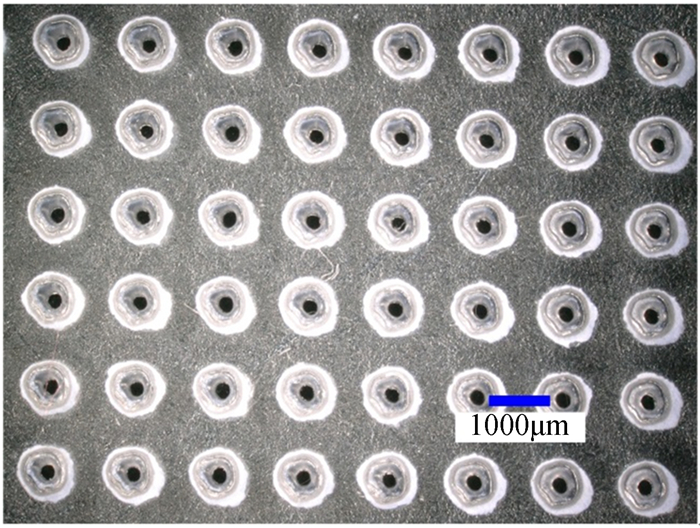
图 7. 通过激光加工在石英玻璃基底上制备的微孔阵列Micro-pore array on quartz substrate fabricated through laser etching
Fig. 7. 通过激光加工在石英玻璃基底上制备的微孔阵列Micro-pore array on quartz substrate fabricated through laser etching
采用共聚焦干涉显微镜观测结果如
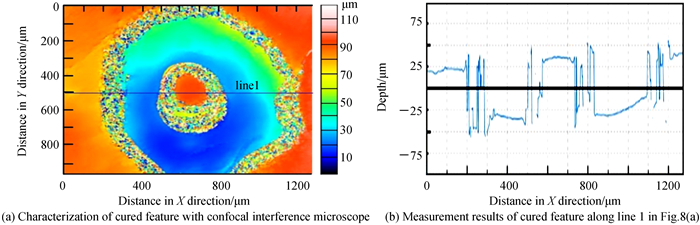
图 8. 微孔固化成型图案共聚焦显微镜表征结果Cured pattern characterization result of micro-pore through confocal interferometric microscope
Fig. 8. 微孔固化成型图案共聚焦显微镜表征结果Cured pattern characterization result of micro-pore through confocal interferometric microscope
4 结论
本文针对形成阻聚区所需的透氧基底成本以及基底变形问题,提出了一种多孔透明支撑板+PDMS膜的低成本实现阻聚区的方案,并围绕支撑基底上微孔对透光性及固化区光强分布的规律进行了数值模拟和实验研究.结果表明,相对于基底微结构形状,其尺寸和周期对基底的透光性及其透过基底在成型区的光强分布的影响更显著;微孔直径小于固化光源半波长时对光强分布的均匀性影响有限,而当微孔直径远大于半波长时,将在固化区形成规则明暗图形阵列,在固化层形成不期望的附加结构,从而降低制造精度甚至形状;为了减小基底微孔对成型精度的影响,应将基底所制备的微孔直径控制在半波长以下;为了降低对制备工艺的要求,在实际应用中应根据精度要求在成型精度和工艺难度之间进行平衡.实验与仿真结果吻合较好,说明了仿真结果的正确性,研究结果可以为基底制备提供工艺改进的方向和理论依据.
[10] PAN Y Y, CHEN Y, ZHOU C. Fast recoating methods f the projectionbased stereolithography process in micro macroscales[C]. Proceeding of solid freefm fabrication symposium, Austin, Texas, August 810, 2012: 846862.
[13] SRIVATSAN T S, SUDARDHAN T S. Additive manufacturing:innovations, advances, and applications[M]. New York:Taylor & Francis Group, 2016.
Article Outline
王权岱, 梁民, 程林凯, 杨明顺, 李鹏阳, 李言. 约束面投影成型室基底微观特征对透光性的影响[J]. 光子学报, 2020, 49(1): 0124001. Quan-dai WANG, Min LIANG, Lin-kai CHENG, Ming-shun YANG, Peng-yang LI, Yan LI. Influence of Micro-feature parameters of Substrate on Light Transmittance in Constraint Surface Projection Stereolithography[J]. ACTA PHOTONICA SINICA, 2020, 49(1): 0124001.