基于线结构光的核燃料棒表面裂缝尺寸测量
下载: 831次
1 引言
核电站燃料组件工作环境恶劣,核燃料棒作为燃料的载体是核电站安全运行的重要环节。
按照核燃料棒的安全运行标准,直径为9.67mm的燃料棒表面的裂缝的安全宽度不应超过0.3mm,加之受水深15m和水下杂质等因素的干扰,准确测量裂缝尺寸的难度较大,但是对核燃料棒表面裂缝尺寸的准确把控对核电站的安全运行具有重要意义。在这种特殊环境下采用非接触测量最为合适,机器视觉检测是非接触测量的典型代表[1],相比于超声波检测法[2]、声发射检测法[3]、光纤传感检测法[4]等,视觉检测具有更加便捷、直观、效率高的特点,考虑到水下的复杂环境以及核电站的环境问题,采用线结构光视觉检测方法最为合适。
目前广大学者利用视觉检测对物体表面缺陷的处理已经取得了诸多研究成果,但是对于核燃料棒表面缺陷的研究文献较少。卢荣胜等[5]以智能制造业表面缺陷在线自动检测为应用背景,系统地综述了自动光学(视觉)检测技术。刘丹等[6]对于复杂背景下微小圆柱体芯块的端面缺陷检测,采用了基于线结构光的三角剖分技术进行了缺陷检测,有很好的检测效果。高军强等[7]为实现钢轨表面缺陷的实时全方位检测,提出基于多摄像机线结构光的三维检测方法,实现了钢轨表面缺陷的准确检测。Tsai等[8]对规则纹理表面(机械加工表面、天然木材、纺织面料)的缺陷进行复原,利用高频的傅里叶分量对应表面纹理线型区域,低频的傅里叶分量对应表面缺陷区域,实现了缺陷的检测。李书华等[9]将投影法、区域生长法、分块法应用到表面缺陷检测中,能够精确检测PVC管材的细小缺陷。Alippi等[10]利用图像对铁轨的表面质量进行自动检测,利用车载检测系统对铁轨的表面质量进行实时检测和分类。王颖等[11]通过判断相邻点法线夹角的变化进行管道内表面缺陷的识别,简化了三角剖分过程。刘婷婷等[12]基于Zernike矩亚像素的高反光金属工件缺陷检测算法,有效地解决了放光问题的干扰。王耀东等[13]提出了一种基于连通区域的多级滤波算法,结合全局与局部的预处理算法,较好地实现地铁隧道表面裂缝的智能检测。苏俊宏等[14]针对圆柱型高精密零件高曲率表面缺陷检测的问题,设计了一套基于机器视觉的检测系统,可有效解决圆柱型高精密零件表面缺陷在线检测的问题。李克斌等[15]采用高、低角度光源组合打光方式提取感兴趣区域,构建划痕形态学的中值滤波核,获取了准确的背景图像,再经背景差分后提取出划痕缺陷。
燃料棒表面裂缝细小,并且相机被置于深水下距离燃料棒65cm处进行拍摄,受水下的杂质和辐射等影响,测量难度大。针对以上问题,搭建了
2 测量系统模型及标定
基于线结构光的水下视觉检测系统,主要由CCD相机、激光器以及旋转驱动组成,测量系统的数学模型如
系统标定时需要建立从图像二维坐标(u,v)到空间三维坐标(Xw,Yw,Zw)之间的转换关系,转换公式为
式中:Zc为转换矩阵;fx=
利用立体靶标法标定激光平面方程和旋转中心[16],得到激光平面方程为
联立 (1) 式和(2) 式实现了二维坐标到空间三维坐标之间的转换,获得了被测物体的(Xw,Yw,Zw)空间坐标。
检测设备是利用伺服电机带动摄像机和激光器的平台对待检测物体进行扫描拍摄,所以电机每转一个角度,对应的空间坐标系也随之发生改变,如
其中,(Xr,Yr,Zr)为旋转中心在原始空间坐标系下的坐标,θ为相机与激光器平台转过的角度。
3 核燃料棒表面裂缝测量算法
3.1 感兴趣区域的定位框选
由于拍摄距离远,图像尺寸为2464pixel×2056pixel,结构光区域大小为40pixel×130pixel。为了观察方便,将燃料棒表面图像裁剪放大为如
1) 根据测量的图像灰度值分布特点,设定一个灰度阈值K,作为灰度值的对比参考值;
2) 对图像进行逐行灰度值遍历,搜索出该行灰度值最大值Gmax对应的像素点,当第一次出现Gmax≥K时,若该点周围像素点的灰度值均不小于K,则把该点作为区域的起始定位点Ps;
3) 继续对图像进行逐行搜索,搜索出每行灰度值最大值Gmax的点,如果Gmax<K,则将该点作为待测量区域定位的结束点Pe;
4) 根据所搜索出的Ps和Pe点,计算出待处理区域的中心坐标为
5) 根据结构光的像素尺寸大小特点,设定框选矩形的长H、宽W,以Co为矩形的中心坐标,框选出待处理区域。
该方法能够准确快速地搜索出需要处理的结构光区域,能够有效地将部分噪点隔离在矩形框之外,为之后的图像处理缩小了范围,提高了处理效率,框选效果如
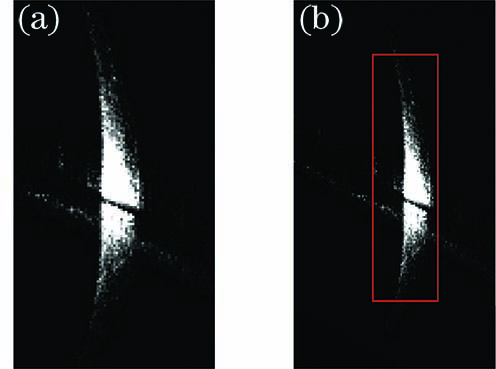
图 4. 感兴趣区域的定位框选。(a)原始图像;(b)框选效果图
Fig. 4. Position and frame selection for region of interest. (a) Original image; (b) diagram of frame selection effect
3.2 灰度值水平投影与微分处理
通过分析裂缝的灰度特点,对已经框选定位的图像区域进行灰度值水平投影和一阶微分差值求取。然后将每行值统计到统一的坐标系下,对灰度值变化情况进行分析,最终确定出裂缝区域。
第i行的图像灰度的水平投影值为
式中:x(i,j)为图像中第i行第j列像素点的灰度值。对燃料棒灰度水平投影值中相邻两行的灰度值求取一阶微分差值,可得
式中:Co-
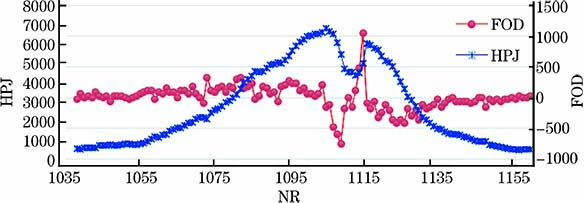
图 5. 燃料棒水平投影与一阶微分结果
Fig. 5. Horizontal projection and first-order differential results for fuel rods
1) 利用水平投影可以确定结构光水平投影值最大时所处的像素行ih,再利用一阶微分差值可以确定最大值所处的像素行 if。
2) 比较ih与if的大小,确定裂缝处在水平投影灰度值最大处的左右区域。
3) 判断裂缝位置。对于右区域:以微分最大值点为基础点,在其左右寻找微分大于等于0的点,直到值小于0为止,如该区域最小行为is,最大行为im,则裂缝的结束像素行为im,因为裂缝近似对称,可以确定裂缝的开始行为(2is-im)。对于左区域:以微分最小值点为基础点,在其左右寻找微分小于等于0的点,直到值大于0为止,该区域最小行为is,最大行为im,则裂缝的起始像素行为is,可以确定裂缝的结束行为(2im-is)。
4) 为了更完整地定位裂缝区域,将框选区域适当地扩大。
(1) |im-is|≥6,则有:右区域中起始行为(2.5is-1.5im),结束行为(1.5im-0.5is);左区域中起始行为(1.5is-0.5im),结束行为(2.5im-1.5is),如
(2) |im-is|<6,则有:右区域中起始行为(3is-2im),结束行为(2im-is);左区域中起始行为(2is-im),结束行为(3im-2is),如
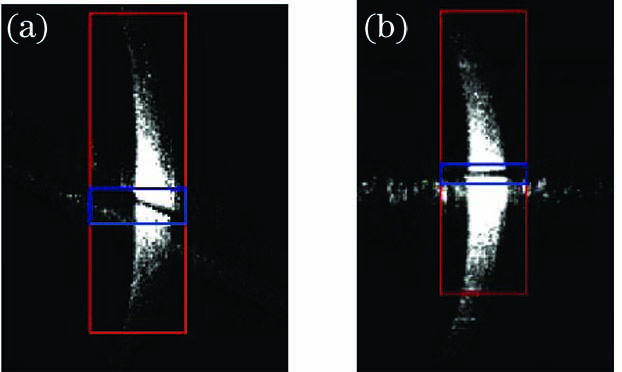
图 6. 框选区域的扩大。(a) |im-is|≥6; (b)|im-is|<6
Fig. 6. Expansion of the frame selection area. (a) |im-is|≥6; (b)im-is|<6
3.3 裂缝边界点判定
对已经确定的裂缝区域进行进一步处理,需要确定出裂缝的具体边界点,首先利用阈值分割分割出裂缝区域,进一步缩小裂缝范围;然后,设定种子点类别,根据种子点的特征缩小裂缝区域,判定边界点,并将其分为上下两个边界点集合,具体步骤如下:
1) 对待处理区域进行阈值分类,并对裂缝区域进行灰度统计,如
2) 对裂缝区域进行像素灰度值遍历,遍历分为上下边界两种边界类型,利用种子点进行判定,如
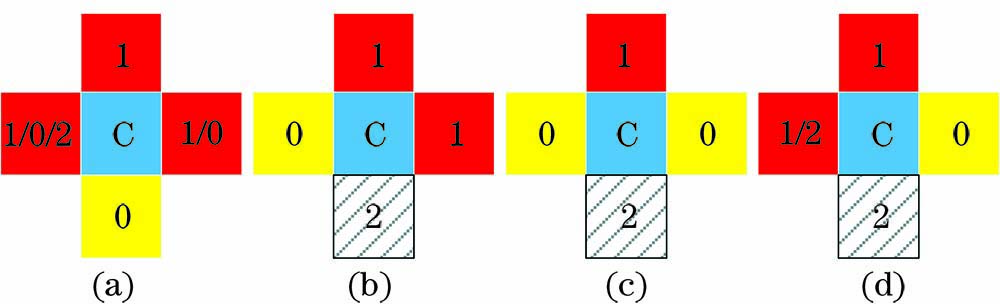
图 9. 上边界判断方法。(a)边界像素点类型一;(b)边界像素点类型二;(c)边界像素点类型三;(d)边界像素点类型四
Fig. 9. Upper boundary judgment method. (a) Boundary pixel type one; (b) boundary pixel type two; (c) boundary pixel type three; (d) boundary pixel type four
通过以上步骤可以得到裂缝的上下边界点,实现边界点划分和提取,为之后裂缝边界的准确定位提供基础。
3.4 结构光中心提取及裂缝边界点定位
线结构光视觉测量技术的关键在于线结构光中心的提取,这意味着单张图像中只需在裂缝缺陷的上下边界上各获取一个像素点即可。针对该问题,采用了中心线曲线拟合,利用中心线方程与裂缝边界求交集,确定裂缝的准确位置,具体步骤如下:
1) 自适应阈值处理
计算两像素点间灰度梯度值和每行灰度梯度的平均值,表达式分别为
式中:Gij是指图像第i行第j列的灰度值;ST是第i行灰度梯度值Tij之和;Wd表示线结构光宽度。
阈值GT和线结构光宽度Wd之间的关系为
其中Gim表示每行灰度值的最大值。
通过该方法求取每行阈值,可以保证不同区域的灰度值不存在相互干扰。依赖与像素所在行的灰度特点设定阈值,如
2) 结构光中心提取及曲线拟合
对非裂缝区域进行光条中心提取,记录每行灰度值大于0的起始点Sp和每行灰度值不为0的最后一个点Ep。经过以上的自适应行阈值处理,可以确定梯度值对应的梯度位置Pij为
根据梯度重心法,计算第i行的结构光条中心,表达式为
对待处理区域采用梯度中心法处理,即可得到结构光条纹的中心亚像素坐标, 根据非裂缝区域的结构光条纹中心坐标,将亚像素坐标点用曲线拟合,拟合公式为
(12) 式是关于a0,a1,…,an-1和b的线性方程。利用最小二乘法建立曲线拟合的数学模型,根据结构光条纹点集合,建立需求目标函数:
拟合裂缝区域的正常结构光条中心曲线方程的关键在于曲线最高阶次的确定,拟合过程需防止过拟合和拟合不准确的问题。对于同一个实验,结构光能量强度和分布特点是相似的,所以带有裂缝的结构光[
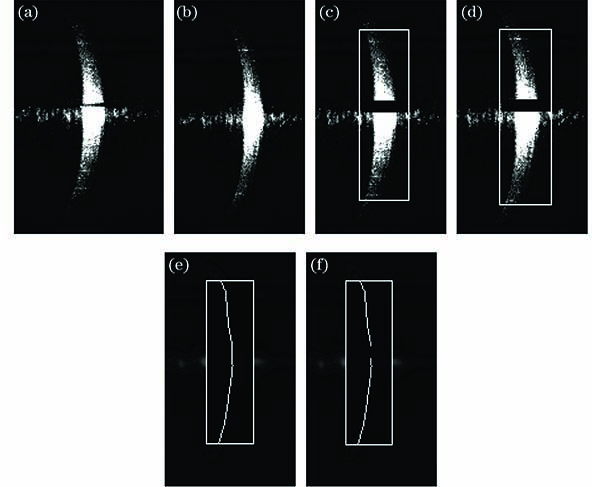
图 11. 裂缝处结构光中心线的获取。(a)带有裂缝;(b)不带有裂缝;(c) (a)图去除裂缝区域;(d) (b)图去除裂缝区域;(e)正常光条中心;(f)残缺光条中心
Fig. 11. Acquisition of structured light bar center at the crack. (a) With a crack; (b) without cracks;(c) removing cracked area for Fig. 11 (a); (d) removing cracked area for Fig. 11 (b); (e) normal light bar center; (f) incomplete light bar center
利用梯度重心法提取
接着利用去除段的拟合曲线值(x,y(x))与
其中,ib为裂缝段起始行,ie为裂缝段结束行。采用不同阶次的曲线进行最小二乘拟合,计算结果如
表 1. 中心线拟合误差表
Table 1. Center line fitting errors
|
观察发现,σs,σo在采用8阶拟合函数拟合时总体误差趋于平缓,当拟合阶次达到12时,出现了过拟合现象,拟合误差较大,且误差值上下波动。所以考虑到计算的精度和复杂度,最终确定拟合曲线的最高拟合阶次为8,拟合的曲线如
3) 利用拟合曲线方程在裂缝区域的坐标值,计算裂缝区间内曲线在每行处的坐标值并取整,即
yi=
其中,yi为曲线在第i行处的取整值,ko为y(i)的小数部分,floor[·]为向上取整,ceiling[·]为向下取整。
若计算出的上边界点多于一点,如
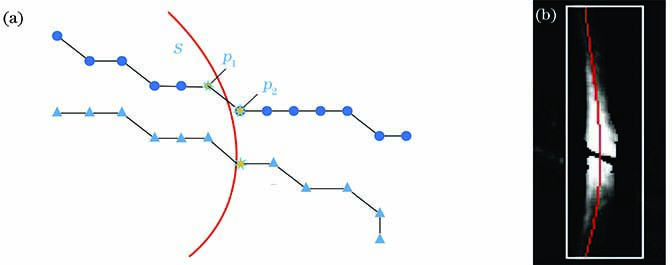
图 13. 裂缝边界处理。(a)边界判定示意图;(b)中心线与边界相交示意图
Fig. 13. Crack boundary treatment. (a) Diagram of boundary decision; (b) intersection diagram of center line and boundary
3.5 裂缝尺寸计算方法
利用标定好的旋转平移矩阵将裂缝边界像素的二维坐标转化为三维空间坐标,再将得到的三维坐标点集分为上边界裂缝点集Pu以及下边界裂缝点集Pd,由于裂缝倾斜,测量出来的裂缝宽度其实是倾斜裂缝的斜线长度,如
其中,(xui,yui,zui)为上边界裂缝点集Pu的第i个点Pui,以Pui为球心,以Di为半径划分出一个采样球形范围如
x∈
y∈
x∈
下边界点集在此范围以内的点为点Pui的局内点Nui,计算Pui与局内点Nui的距离,再取距离最小值代表裂缝在上边界点Pui处的实际宽度Dui,计算出的基于上边界的平均宽度Au为
同理可以计算出下边界在每个边界点Pdi处的实际宽度Ddi及下边界裂缝平均宽度Ad,计算燃料棒裂缝平均宽度Aud,即
4 实验部分
为了验证本文算法的适用性,采用win7 64位系统,使用可跨平台的QT5.8.0和VS2013作为开发工具进行程序编写,开发了核燃料组件的测量平台,完成了对核燃料棒的在线扫描测量。该平台的运行流程如
1) 运行程序需要先连接好相机和电机,并设置好相关参数。电机旋转带动相机及激光器旋转,通过旋转拍摄实时获取图像。设定每20ms获取一次当前位置的扫描图像。
表 2. 裂缝尺寸测量结果
Table 2. Tabel 2 Test results of crack size
|
2) 基于相机实时拍摄的图像,使用文中设计的裂缝测量算法对图像进行处理,采用多线程运行,使图像处理和点云生成同时进行,互不干扰,计算燃料棒表面裂缝的尺寸,并反映出裂缝所处的位置和形态。
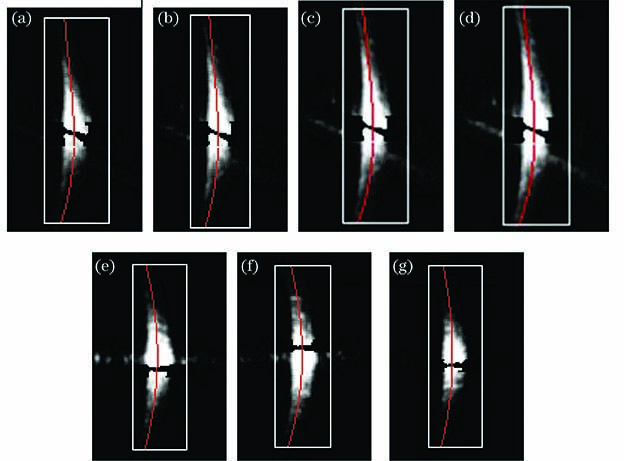
图 17. 相机拍摄图片。(a)曝光度为200;(b)曝光度为300;(c)曝光度为400;(d)曝光度为500;(e)裂缝尺寸为190.0μm;(f)裂缝尺寸为181.6μm;(g)裂缝尺寸为 128.6μm
Fig. 17. Photos taken. (a) Exposure of 200; (b) exposure of 300; (c) exposure of 400; (d) exposure of 500; (e) crack size of 190.0μm; (f) crack size of 181.6μm; (g) crack size of 128.6μm
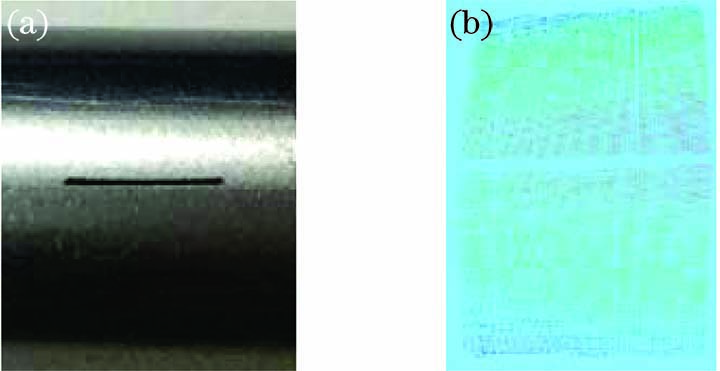
图 18. 核燃料棒表面裂缝。(a)燃料棒表面裂缝;(b)燃料棒表面裂缝点云图
Fig. 18. Cracks on the surface of nuclear fuel rods. (a) Crack on the surface of fuel rod; (b) point cloud of crack on fuel rod surface
5 结论
针对核燃料棒表面细小裂缝测量问题,提出了一种基于结构光扫描的视觉测量方法。该方法通过灰度二维搜索、水平投影和一阶微分,实现了裂缝区域的准确定位,提高了后续处理的计算效率和准确率。然后,利用裂缝区域阈值分割法、种子点判断法,将边界像素点准确地提取和分类。最后,使用最小二乘法拟合结构光中心线,用中心线方程与裂缝边界点集求交点,确定裂缝具体位置,再将裂缝边界点转为三维坐标进行距离采样,计算实际尺寸。实验证明,使用该方法实现了水下65cm处燃料棒表面裂缝尺寸的测量,测量误差保持在0.03mm以内,有效地满足了测量的便捷性和精确性,对核电站的安全运行具有重要意义。
[1] 汤勃, 孔建益, 伍世虔. 机器视觉表面缺陷检测综述[J]. 中国图象图形学报, 2017, 22(12): 1640-1663.
[2] 胡晨旭. 核电厂一回路管座焊缝超声波检测仿真研究[J]. 核动力工程, 2020, 41(2): 145-149.
[3] 孙永生, 李猛, 刘恒, 等. 基于声发射检测技术的滚动轴承缺陷检测[J]. 无损检测, 2015, 37(8): 17-20, 60.
Sun Y S, Li M, Liu H, et al. Bearing fault detection based on acoustic emission technique[J]. Nondestructive Testing Technologying, 2015, 37(8): 17-20, 60.
[4] 文玉忠. 基于分布式光纤传感检测法的水利施工混凝土裂缝检测效果分析[J]. 水利技术监督, 2019, 27(2): 18-20, 154.
[5] 卢荣胜, 吴昂, 张腾达, 视觉, 等. 检测技术及其在缺陷检测中的应用综述[J]. 光学学报, 2018, 38(8): 0815002.
[6] 刘丹, 张斌, 李慧娴, 等. 复杂背景下微小圆柱端面缺陷检测方法研究[J]. 激光与光电子学进展, 2018, 55(6): 061006.
[7] 高军强, 刘桂华. 多摄像机线结构光的钢轨表面三维缺陷检测[J]. 机械设计与制造, 2017( 3): 170- 172, 176.
Gao JQ, Liu GH. 3D defect detection technology for rail surface with multi-camera line structure light[J]. Machinery Design & Manufacture, 2017( 3): 170- 172, 176.
[8] Tsai D M, Hsieh C Y. Automated surface inspection for directional textures[J]. Image and Vision Computing, 1999, 18(1): 49-62.
[9] 李书华, 周亚同, 王丹, 等. 基于机器视觉的聚氯乙烯管材表面缺陷检测[J]. 激光与光电子学进展, 2019, 56(13): 131006.
[10] Alippi C, Casagrande E, Scotti F, et al. Composite real-time image processing for railways track profile measurement[J]. IEEE Transactions on Instrumentation and Measurement, 2000, 49(3): 559-564.
[11] 王颖, 韩静文, 金翠云, 等. 圆结构光视觉三维点管道缺陷检测及重构[J]. 应用光学, 2014, 35(3): 441-445.
[12] 刘婷婷, 王培光, 张娜. 基于Zernike矩亚像素的高反光金属工件缺陷检测[J]. 激光与光电子学进展, 2019, 56(12): 121203.
[13] 王耀东, 余祖俊, 白彪, 等. 基于图像处理的地铁隧道裂缝识别算法研究[J]. 仪器仪表学报, 2014, 35(7): 1489-1496.
Wang Y D, Yu Z J, Bai B, et al. Research on image processing based subway tunnel crack identification algorithm[J]. Chinese Journal of Scientific Instrument, 2014, 35(7): 1489-1496.
[14] 苏俊宏, 刘胜利. 圆柱型高精密零件表面缺陷检测及形貌分析[J]. 激光与光电子学进展, 2014, 51(4): 041202.
[15] 李克斌, 余厚云, 周申江. 基于形态学特征的机械零件表面划痕检测[J]. 光学学报, 2018, 38(8): 0815027.
[16] 刘志伟. 基于线结构光的核燃料组件缺陷水下检测装置研究[D]. 上海: 东华大学, 2019: 17- 21.
Liu ZW. Research on underwater detection device for nuclear fuel assembly defects based on line structured light[D]. Shanghai: Donghua University, 2019: 17- 21.
[17] . A threshold selection method from gray-level histograms[J]. IEEE Transactions on Systems, Man, and Cybernetics, 1979, 9(1): 62-66.
Article Outline
咸凯强, 庞静珠, 胡俊. 基于线结构光的核燃料棒表面裂缝尺寸测量[J]. 激光与光电子学进展, 2020, 57(22): 221013. Kaiqiang Xian, Jingzhu Pang, Jun Hu. Surface Crack Size Detection in Nuclear Fuel Rods Based on Line Structured Light[J]. Laser & Optoelectronics Progress, 2020, 57(22): 221013.