铌微合金化对光纤激光-CMT复合焊接A7204P-T4 铝合金接头组织和力学性能的影响
下载: 766次
1 引言
A7204P-T4铝合金属于Al-Zn-Mg-Cu可热处理强化铝合金,具有较高的强度和良好的挤压性能,已被广泛应用于航空航天、汽车、高速列车等领域[1-3]。焊接技术已被证明在降低成本和减轻重量方面比传统的机械紧固连接方式更具优势[4]。然而,在传统的电弧焊接过程中,较大的焊接热输入容易使热处理强化铝合金产生严重的接头软化现象,严重影响了结构的安全[5]。激光-冷金属过渡电弧(激光-CMT)复合焊接技术结合了激光和电弧两种热源的优势,可以有效提高焊接接头的间隙适应性和焊接过程的稳定性。此外,CMT焊接过程中的焊丝回抽可将短路电流降低到非常低的水平,有效降低了焊接热输入;而且,在CMT焊接过程中,不需要大电流就能使液桥断裂,从而避免了飞溅。因此,采用激光-CMT焊接工艺焊接铝合金具有较大优势。
A7204P-T4铝合金中含有大量的低熔点元素镁和锌,焊接过程中镁、锌强化相的溶解引起的接头软化是一个突出难题[6-7]。人们通常采用添加合金元素的方法对焊接接头进行改性,这是因为某些元素的微量添加甚至是痕量添加就会显著改善铝合金的微观组织与综合性能[8-9],因此,微合金化已逐渐成为提高铝合金焊接接头性能的重要途径和手段。
目前,钪(Sc)微合金化的研究引起了很多关注。研究表明,铝、钪固溶体中会形成稳定的具有L12结构的Al3Sc金属间化合物,钪在铝中的溶解度较低,可以产生显著的强化效应[10]。邹亮等[11]研究了微量钪对超高强Al-Zn-Cu-Mg-Zr合金组织与性能的影响,结果发现,在合金中添加钪可以有效细化铸态组织的晶粒,提高合金的力学性能。目前,钪的添加已被证明对铝合金的焊接性和力学性能具有有益影响。Huang等[12]研究了微量钪对Al-Zn-Mg-Zr铝合金熔化极惰性气体保护焊(MIG)焊接接头焊缝组织和力学性能的影响,结果表明,钪的添加可以显著细化焊缝晶粒,提高熔合区的强度和显微硬度。但钪的成本较高,难以在工业领域获得广泛应用。早期的研究表明,第V族过渡元素铌(Nb)在铝中具有比钪更低的扩散系数,这使得其具有较高的抗粗化能力;同时,铌在铝基体中能形成Al3M金属间化合物,该化合物是高强度热稳定铝基合金中理想的分散强化相,可以对合金的力学性能产生有利影响[9]。Erdeniz等[13]通过在Al-Zr-Sc-Er-Si铝合金中添加质量分数为0.08%的铌研究了铌的添加对析出强化Al-Zr-Sc-Er-Si合金强度的影响,结果发现,铌的添加不仅提高了合金的显微硬度,而且抑制了沉淀相的粗化。Wang等[14]研究了包晶溶质对铝晶粒细化的影响,结果表明,铌可以通过形成析出相来促进形核,使晶粒细化。然而目前关于铌的研究主要集中在金属材料的调质中,与钪的研究相比,铌的添加对铝合金焊接接头组织、性能影响的研究还比较少。
本文采用激光-CMT焊接工艺对A7204P-T4铝合金进行了对接焊接,并在对接界面处预置了不同尺寸的铌箔,对比研究了铌含量对焊缝显微组织和力学性能的影响及影响的机理,并分析了焊接接头的拉伸断裂机理和断口形貌。
2 试验材料及方法
试验材料为6 mm厚的A7204P-T4铝合金板材,其供货状态为T4态,试板的表面尺寸为300 mm×150 mm。焊接填充材料均选择直径为1.2 mm的ER5356焊丝。铝合金母材与焊丝的化学成分如
表 1. A7204P-T4铝合金及焊丝的化学成分
Table 1. Chemical composition of A7204P-T4 aluminum alloy and welding wire
|
采用对接焊的方式对铝合金板材进行光纤激光-CMT电弧复合焊接,
焊接前先用刮刀刮削试板焊接区,直至露出金属光泽,然后用蘸有丙酮的无尘布对焊接区域进行擦拭。在确定的复合焊接工艺参数下,在对接界面处预置两种不同尺寸的铌箔来控制焊缝中的铌含量,其中铌箔厚度为0.01 mm。焊后通过计算焊缝横截面中添加铌箔的面积和焊缝横截面面积均值得到焊缝中铌的面积分数,然后根据铝和铌的密度进一步计算得到焊缝中铌的质量分数分别约为0.74%和1.36%。
焊接试验结束后,在焊接接头的焊缝横截面上制备金相试样。采用Keller试剂对金相试样进行腐蚀,然后采用Leica DMI8C金相显微镜观察焊缝横截面的显微组织;采用JSM-7001F扫描电镜对焊接接头进行电子背散射衍射(EBSD)分析;采用Quanta 650场发射扫描电子显微镜对焊缝和拉伸断口进行分析;采用JXA-8100电子探针(EPMA)对焊缝中的铌元素进行面扫描分析;采用Olympus SZ61体式显微镜观察拉伸断裂位置;采用WILSON VH1102 硬度计对焊接接头的显微硬度进行测试,加载载荷为0.98 N,加载时间为10 s;将焊接试样去除余高后制成光滑试样,然后采用MTS 370 Load Frame型材料试验机进行拉伸试验。拉伸试样尺寸如
3 试验结果和分析
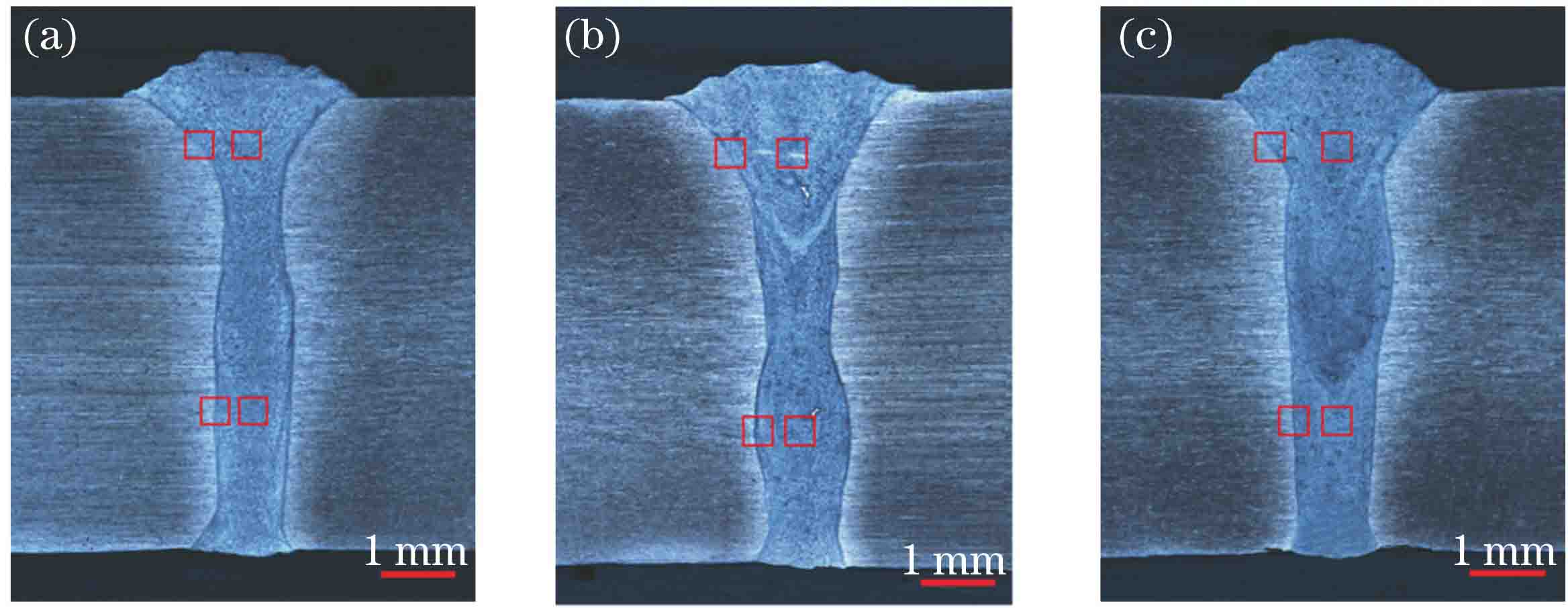
图 3. 焊缝的横截面形貌。(a)未加铌;(b)铌的质量分数为0.74%;(c)铌的质量分数为1.36%
Fig. 3. Cross-sectional morphologies of welds. (a) Without niobium; (b) niobium with a mass fraction of 0.74%; (c) niobium with a mass fraction of 1.36%
zone bottom part
3.1 微量铌对接头显微组织的影响
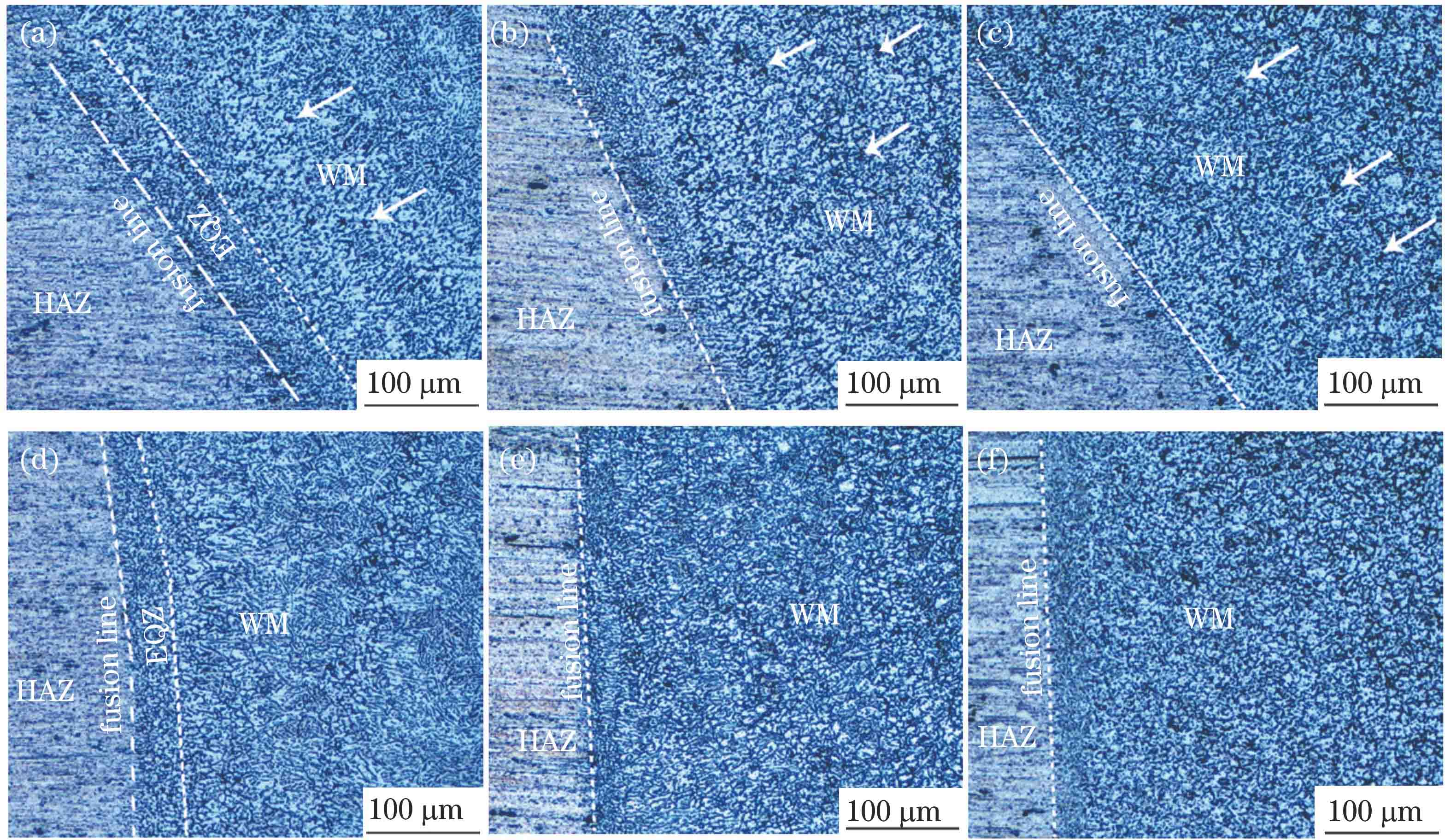
图 4. 焊缝熔合区的显微组织。(a)未加铌,熔合区上部;(b)铌的质量分数为0.74%,熔合区上部;(c)铌的质量分数为1.36%,熔合区上部;(d)未加铌,熔合区下部;(e)铌的质量分数为0.74%,熔合区下部;(f)铌的质量分数为1.36%,熔合区下部
Fig. 4. Microstructures of weld fusion zone. (a) Without niobium, fusion zone upper part; (b) niobium with a mass fraction of 0.74%, fusion zone upper part; (c) niobium with a mass fraction of 1.36%, fusion zone upper part; (d) without niobium, fusion zone bottom part; (e) niobium with a mass fraction of 0.74%, fusion zone bottom part; (f) niobium with a mass fraction of 1.36%, fusion
由
未加铌以及铌的质量分数分别为0.74%和1.36%的焊缝中心的显微组织如
为了定量研究铌对焊缝组织的影响,需要对EBSD反极图(IPF)进行系统比较,并对焊缝晶粒进行统计。如
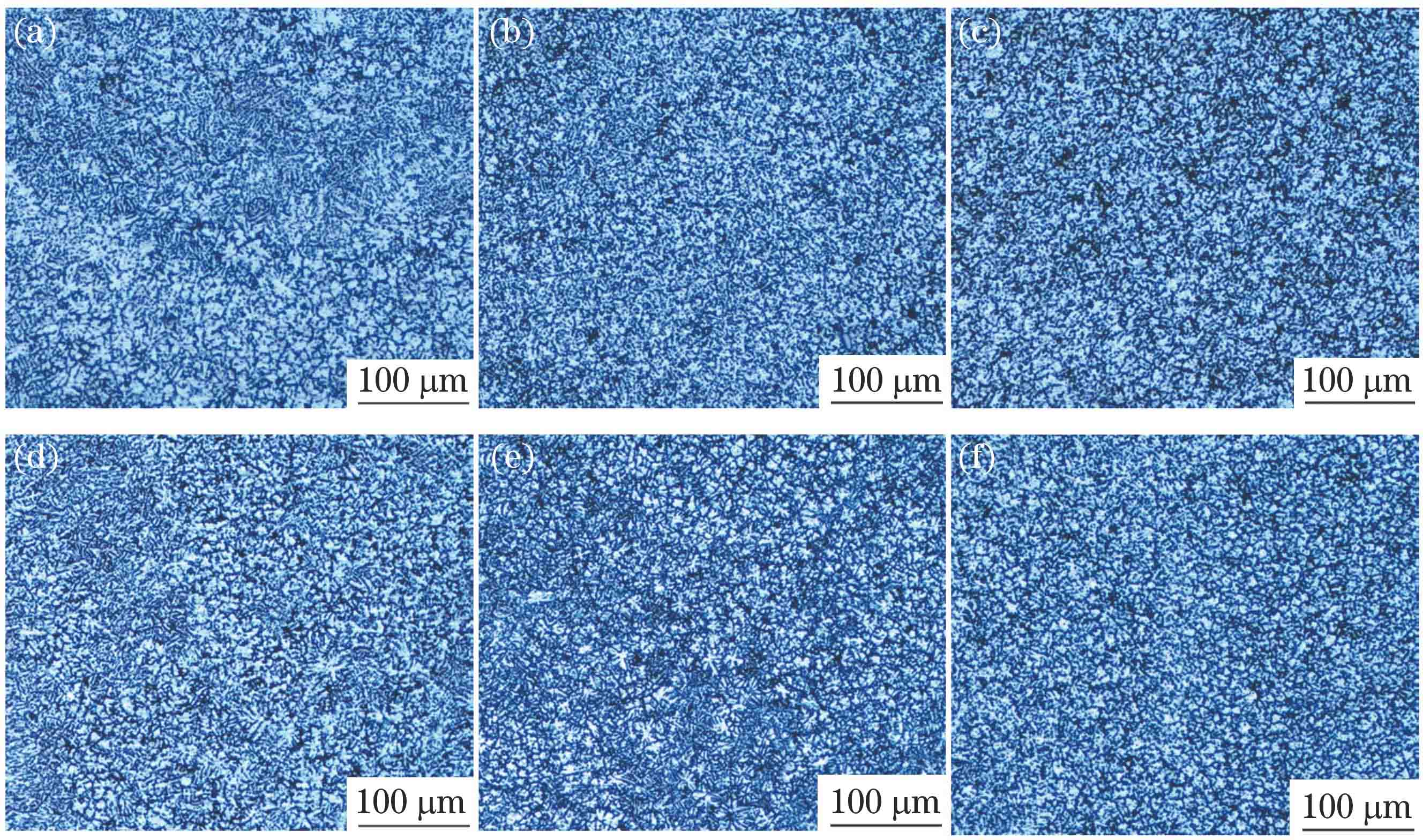
图 5. 焊缝中心的显微组织。(a)未加铌,焊缝中心上部;(b)铌的质量分数为0.74%,焊缝中心上部;(c)铌的质量分数为1.36%,焊缝中心上部;(d)未加铌,焊缝中心下部;(e)铌的质量分数为0.74%,焊缝中心下部;(f)铌的质量分数为1.36%,焊缝中心下部
Fig. 5. Microstructures of weld center. (a) Without niobium, weld center upper part; (b) niobium with a mass fraction of 0.74%, weld center upper part; (c) niobium with a mass fraction of 1.36%, weld center upper part; (d) without niobium, weld center bottom part; (e) niobium with a mass fraction of 0.74%, weld center bottom part; (f) niobium with a mass fraction of 1.36%, weld center bottom part
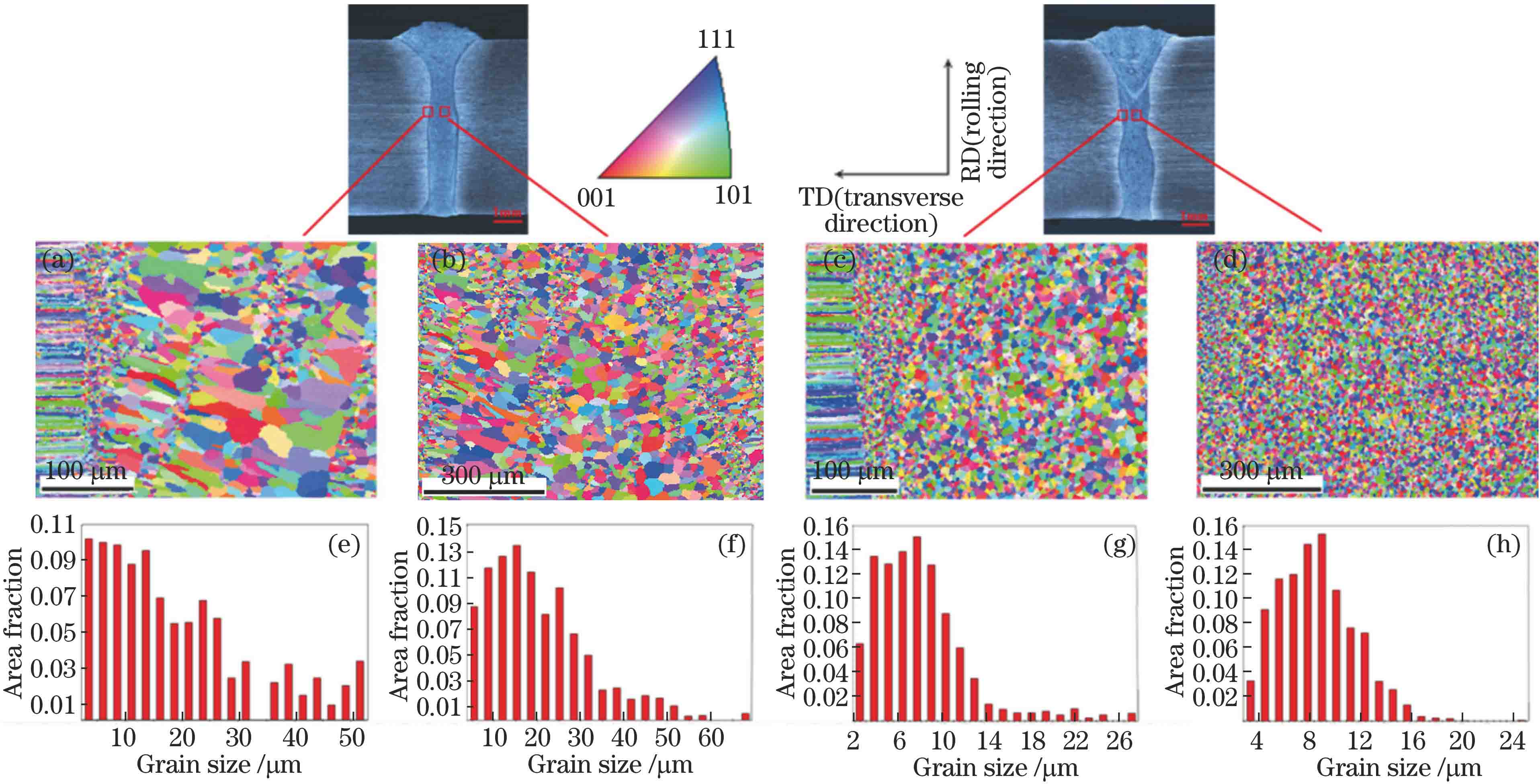
图 6. 显微组织的EBSD测试结果以及晶粒统计结果。(a)未加铌,熔合区的EBSD测试结果;(b)未加铌,焊缝中心区的EBSD测试结果;(c)铌的质量分数为0.74%,熔合区的EBSD测试结果;(d)铌的质量分数为0.74%,焊缝中心区的EBSD测试结果;(e)未加铌,熔合区的晶粒统计结果;(f)未加铌,焊缝中心区的晶粒统计结果;(g)铌的质量分数为0.74%,熔合区的晶粒统计结果;(h)铌的质量分数为0.74%,焊缝中心区的晶粒统计结果
Fig. 6. EBSD of microstructures and grain statistical results. (a) Without niobium, EBSD of fusion zone; (b) without niobium, EBSD of weld center; (c) niobium with a mass fraction of 0.74%, EBSD of fusion zone; (d) niobium with a mass fraction of 0.74%, EBSD of weld center; (e) without niobium, grain statistical result of fusion zone; (f) without niobium, grain statistical result of weld center; (g) niobium with a mass fraction of 0.74%, grain statistical result of fusion zone; (h) niobium with a mass f
晶粒尺寸统计结果表明,未加铌焊缝的熔合区与中心区的平均晶粒尺寸分别为19 μm和20 μm。铌的加入可以消除熔合区中的柱状晶结构,有效细化焊缝晶粒,细化后的焊缝晶粒保持着良好的均匀性。对于铌质量分数为0.74%的焊缝,其熔合区与中心区的平均晶粒尺寸分别减小为8 μm和9 μm,与未加铌时的平均晶粒尺寸相比分别减小了57.9%和55%。
3.2 接头中的合金元素与析出相
将基于原子序数差异的扫描电镜背散射技术用于检测合金元素和析出相的分布,并采用扫描电镜附带的能谱仪(SEM-EDS)对析出相成分进行分析,结果如
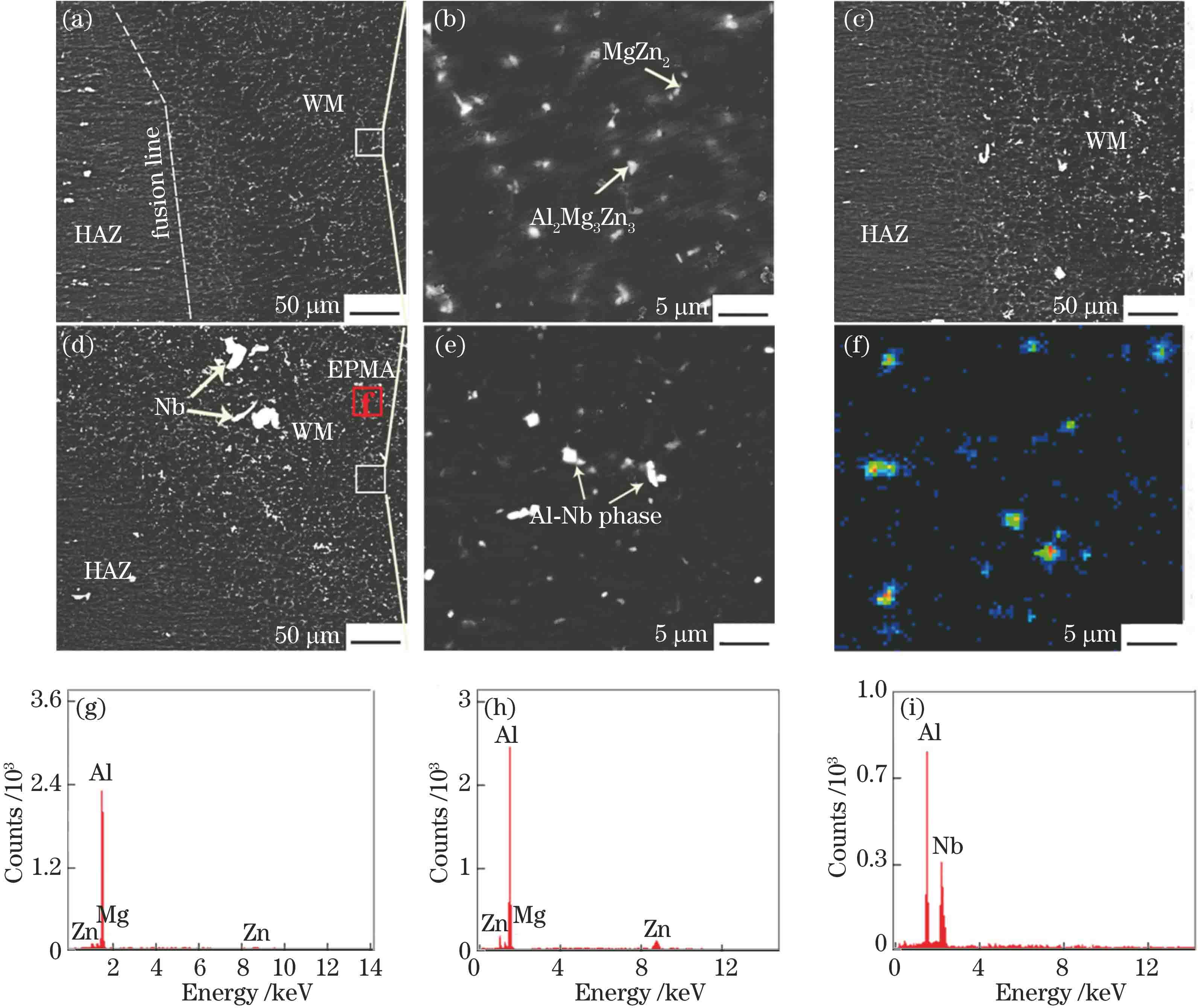
图 7. 焊缝的SEM背散射照片和析出相的EDS结果。(a)(b)未加铌,熔合区及其局部放大图;(c)铌的质量分数为0.74%,熔合区;(d)(e)铌的质量分数为1.36%,熔合区及其局部放大图;(f)铌元素的EPMA面扫描结果; (g) Al2Mg3Zn3析出相的EDS结果;(h) MgZn2析出相的EDS结果;(i) Al-Nb析出相的EDS结果
Fig. 7. SEM backscattered photos of weld and EDS results of precipitated phases. (a)(b) Without niobium, fusion zone and its partial enlargement; (c) niobium with a mass fraction of 0.74%, fusion zone; (d)(e) niobium with a mass fraction of 1.36%, fusion zone and its partial enlargement; (f) EPMA area scan result of niobium; (g) EDS of Al2Mg3Zn3 precipitated phase; (h) EDS of MgZn2 precipitated phase; (i) EDS of Al-Nb precipitated phase
在
根据晶体分离理论,焊缝晶粒的形核、长大与固液界面的溶质偏析程度有关。焊缝中铌溶质的局部偏析会引起晶粒内晶体的分离,产生新的结晶形核点,促进了焊缝晶粒的形核;同时溶质的加入产生了成分过冷作用,这种作用为晶粒在衬底上进一步成核提供了驱动力。上述两种因素共同促进了晶粒的细化。
3.3 铌对接头力学性能的影响
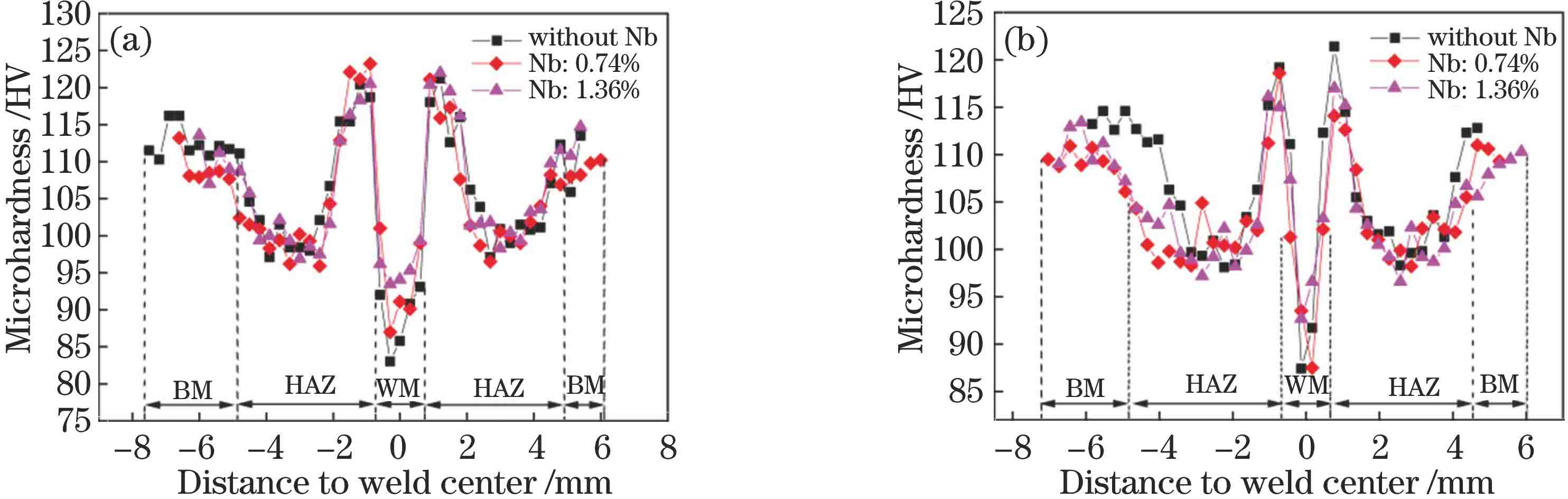
图 8. 焊缝上部和下部的显微硬度分布。(a)焊缝上部;(b)焊缝下部
Fig. 8. Microhardness distribution of the top and bottom of the weld. (a) Top; (b) bottom
人们通常采用Hall-Petch公式来评价晶粒尺寸与显微硬度之间的关系。铌的添加细化了焊缝晶粒,提供了晶界强化作用,因此焊缝在添加铌后显微硬度提高。在靠近焊缝的近缝热影响区,焊接的峰值温度超过了η'和η相的完全溶解温度,母材中的析出相发生溶解,GPI区在随后的冷却过程中析出,GPI区与基体共格,产生的强化作用使焊缝显微硬度迅速提高。靠近母材的热影响区称为过时效区,该区域的焊接峰值温度高于η'相的析出温度,大量η'相转变为与基体非共格的平衡相η相,导致显微硬度降低[24-25]。
但过量的铌不利于焊接接头力学性能的提高,当铌的质量分数增加到1.36%后,焊接接头的断后延伸率降低为4%。
3.4 拉伸断口分析
在
对于铌的质量分数为0.74%的试样,其拉伸断口上未发现明显的微气孔和微裂纹,而且韧窝尺寸明显减小,这与铌对晶粒的细化作用有关。晶粒细化使得沿晶分布的析出相之间的距离缩短,从而使得与晶界相形成有关的韧窝尺寸减小。
随着铌含量增加,断口中可以观察到明显的层状断裂形貌特征,并伴有二次裂纹,如
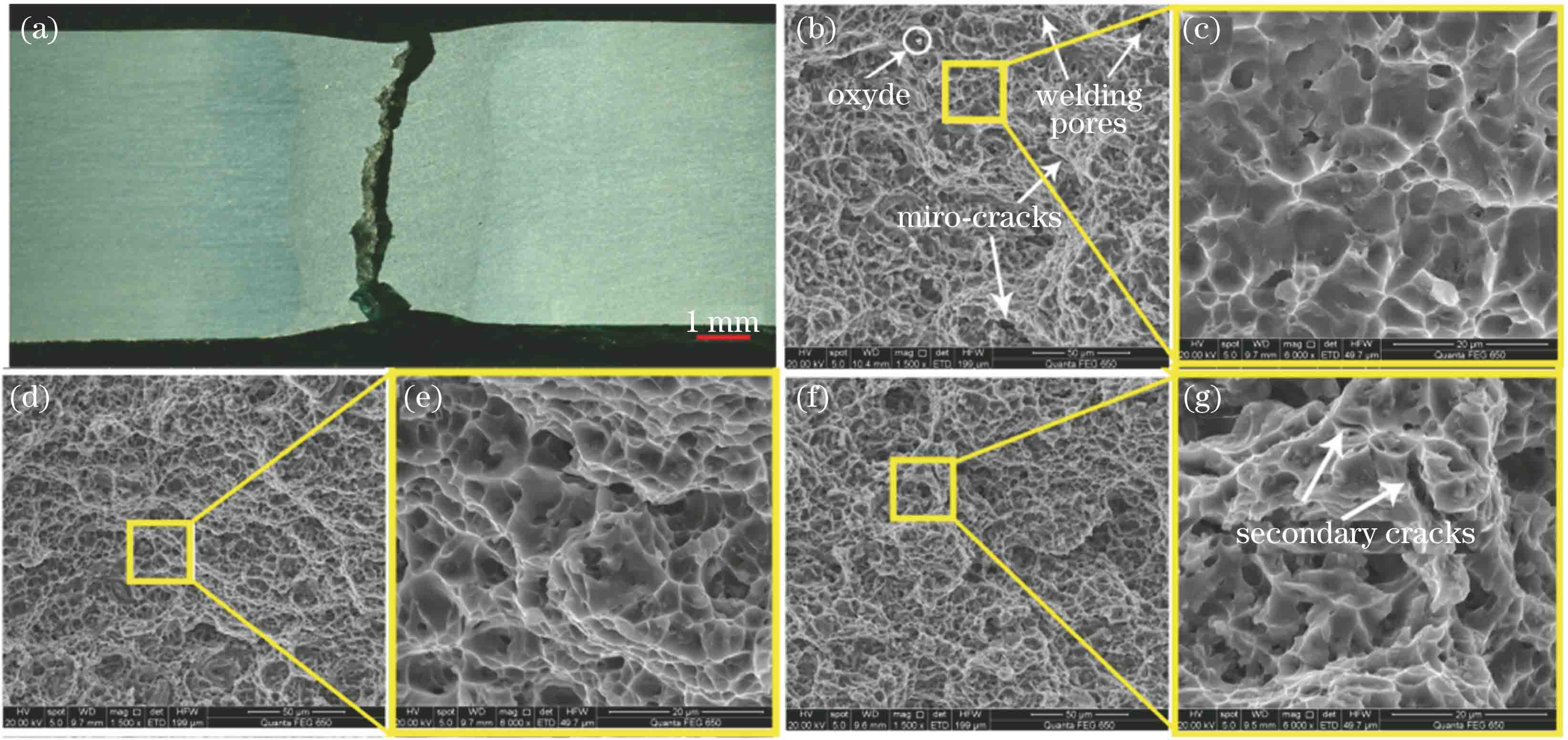
图 10. 拉伸试样的宏观断裂位置以及微观断口形貌。(a)宏观断裂位置;(b)(c)未加铌,微观断口及其局部放大图;(d)(e)铌的质量分数为0.74%,微观断口及其局部放大图;(f)(g)铌的质量分数为1.36%,微观断口及其局部放大图
Fig. 10. Macroscopic fracture position and microscopic fracture of tensile samples. (a) Macro fracture location; (b)(c) without niobium, microscopic fracture and its partial enlargement; (d)(e) niobium with a mass fraction of 0.74%, microscopic fracture and its partial enlargement; (f)(g) niobium with a mass fraction of 1.36%, microscopic fracture and its partial enlargement
4 结论
采用激光-CMT焊接工艺以对接焊的方式对A7204P-T4铝合金进行焊接,在优化的工艺参数下获得了成形良好的焊接接头。适量铌的添加可使偏析于晶界的合金元素和析出相减少,但随着铌含量增加,焊缝中未熔金属铌的数量和尺寸明显增加。
激光-CMT焊缝组织主要由熔合区的等轴晶、柱状晶和焊缝中心区的树枝晶组成,熔合区与焊缝中心区的平均晶粒尺寸分别为19 μm和20 μm。铌的添加使得焊缝晶粒明显细化,柱状晶和枝晶组织基本消失。对于铌质量分数为0.74%的焊缝,其熔合区与焊缝中心区的平均晶粒尺寸分别为8 μm和9 μm。晶粒细化主要是源于铝、铌析出相的异相形核以及铌溶质偏析引起的晶界分离和成分过冷。
强化相的溶解以及铝、镁、锌粗化相的析出使得焊缝成为焊接接头中软化最为严重的区域。添加铌后产生的晶粒细化作用可使焊缝的平均显微硬度略有提升。不含铌以及铌质量分数分别为0.74%和1.36%的焊缝试样的平均抗拉强度分别为325,334.5,328 MPa。对于铌的质量分别为0.74%的焊接接头,其断后延伸率相比未加铌的焊接接头增大了约71%。三种试样拉伸断口的微观形貌均主要以韧窝为主,并伴有明显的撕裂棱。
[1] Zhang K, Chen J Q, Ma P Z, et al. Effect of welding thermal cycle on microstructural evolution of Al-Zn-Mg-Cu alloy[J]. Materials Science and Engineering A, 2018, 717: 85-94.
[2] Qiao J N, Lu J X, Wu S K. Fatigue cracking characteristics of fiber laser-VPTIG hybrid butt welded 7N01P-T4 aluminum alloy[J]. International Journal of Fatigue, 2017, 98: 32-40.
[3] Dursun T, Soutis C. Recent developments in advanced aircraft aluminium alloys[J]. Materials & Design, 2014, 56: 862-871.
[4] Wang Q Z, Zhao Y, Yan K, et al. Corrosion behavior of spray formed 7055 aluminum alloy joint welded by underwater friction stir welding[J]. Materials & Design, 2015, 68(5): 97-103.
[5] Zhang C, Gao M, Zeng X Y. Effect of microstructural characteristics on high cycle fatigue properties of laser-arc hybrid welded AA6082 aluminum alloy[J]. Journal of Materials Processing Technology, 2016, 231: 479-487.
[6] 王启明, 乔俊楠, 邹江林, 等. A7N01铝合金光纤激光-变极性TIG复合填丝焊接工艺研究[J]. 中国激光, 2016, 43(6): 0602004.
[7] 王灿, 吕俊霞, 张建超, 等. 填充焊丝对A7204铝合金光纤激光-VPTIG复合焊接头的影响[J]. 中国激光, 2018, 45(3): 0302002.
[8] 聂祚仁, 文胜平, 黄晖, 等. 铒微合金化铝合金的研究进展[J]. 中国有色金属学报, 2011, 21(10): 2361-2370.
Nie Z R, Wen S P, Huang H, et al. Research progress of Er-containing aluminum alloy[J]. The Chinese Journal of Nonferrous Metals, 2011, 21(10): 2361-2370.
[9] Knipling K E, Dunand D C, Seidman D N. Criteria for developing castable, creep-resistant aluminum-based alloys: a review[J]. Zeitschrift Fur Metallkunde, 2006, 97(3): 246-265.
[10] Yang D X, Li X Y, He D Y, et al. Effect of minor Er and Zr on microstructure and mechanical properties of Al-Mg-Mn alloy (5083) welded joints[J]. Materials Science and Engineering A, 2013, 561: 226-231.
[11] 邹亮, 潘清林, 何运斌, 等. 微量钪对超高强Al-Zn-Cu-Mg-Zr合金组织与性能的影响[J]. 中国稀土学报, 2007, 25(4): 448-453.
Zou L, Pan Q L, He Y B, et al. Effect of minor scandium addition on microstructures and tensile properties of super-high strength Al-Zn-Cu-Mg-Zr alloys[J]. Journal of the Chinese Rare Earth Society, 2007, 25(4): 448-453.
[12] Huang X, Pan Q L, Li B, et al. Effect of minor Sc on microstructure and mechanical properties of Al-Zn-Mg-Zr alloy metal-inert gas welds[J]. Journal of Alloys and Compounds, 2015, 629: 197-207.
[13] Erdeniz D, de Luca A, Seidman D N, et al. Effects of Nb and Ta additions on the strength and coarsening resistance of precipitation-strengthened Al-Zr-Sc-Er-Si alloys[J]. Materials Characterization, 2018, 141: 260-266.
[14] Wang F, Liu Z L, Qiu D, et al. Revisiting the role of peritectics in grain refinement of Al alloys[J]. Acta Materialia, 2013, 61(1): 360-370.
[15] Gutierrez A, Lippold J C. A proposed mechanism for equiaxed grain formation along the fusion boundary in aluminum-copper-lithium alloys[J]. Welding Journal, 1998, 77(6): 23-132.
[16] 孔晓芳, 李飞, 吕俊霞, 等. 5083铝合金光纤激光填丝焊接工艺[J]. 中国激光, 2014, 41(10): 1003007.
[17] Katayama S. Solidification phenomena of weld metals (1st report): characteristic solidification morphologies, microstructures and solidification theory[J]. Welding International, 2000, 14(12): 939-951.
[18] Hu Y N, Wu S C, Chen L. Review on failure behaviors of fusion welded high-strength Al alloys due to fine equiaxed zone[J]. Engineering Fracture Mechanics, 2019, 208: 45-71.
[19] Zhang X X, Zhou X R, Hashimoto T, et al. Corrosion behaviour of 2A97-T6 Al-Cu-Li alloy: the influence of non-uniform precipitation[J]. Corrosion Science, 2018, 132: 1-8.
[20] Zhang L, Li X Y, Nie Z R, et al. Comparison of microstructure and mechanical properties of TIG and laser welding joints of a new Al-Zn-Mg-Cu alloy[J]. Materials & Design, 2016, 92: 880-887.
[21] Wu S C, Hu Y N, Song X P, et al. On the microstructural and mechanical characterization of hybrid laser-welded Al-Zn-Mg-Cu alloys[J]. Journal of Materials Engineering and Performance, 2015, 24(4): 1540-1550.
[22] Lathabai S, Lloyd P G. The effect of scandium on the microstructure, mechanical properties and weldability of a cast Al-Mg alloy[J]. Acta Materialia, 2002, 50(17): 4275-4292.
[23] 胡雅楠, 吴圣川, 宋哲, 等. 激光复合焊接7020铝合金的疲劳性能及损伤行为[J]. 中国激光, 2018, 45(3): 0302003.
[24] Zhang Y, Milkereit B, Kessler O, et al. Development of continuous cooling precipitation diagrams for aluminium alloys AA7150 and AA7020[J]. Journal of Alloys and Compounds, 2014, 584(25): 581-589.
[25] Zhang L, Li X Y, Nie Z R, et al. Microstructure and mechanical properties of a new Al-Zn-Mg-Cu alloy joints welded by laser beam[J]. Materials & Design, 2015, 83: 451-458.
[26] 吴东江, 房振安, 吴冬冬, 等. 铌粉添加量对铝合金激光-电弧复合焊接气孔率的影响[J]. 焊接技术, 2016, 45(8): 10-13.
Wu D J, Fang Z A, Wu D D, et al. Effect of niobium powder addition on porosity of aluminum alloy laser-arc hybrid welding[J]. Welding Technology, 2016, 45(8): 10-13.
栗忠秀, 温鹏, 张松, 吴世凯. 铌微合金化对光纤激光-CMT复合焊接A7204P-T4 铝合金接头组织和力学性能的影响[J]. 中国激光, 2020, 47(9): 0902001. Li Zhongxiu, Wen Peng, Zhang Song, Wu Shikai. Effects of Nb Micro-Alloying on Microstructure and Mechanical Properties of A7204P-T4 Aluminum Alloy Joint by Fiber Laser-CMT Hybrid Welding[J]. Chinese Journal of Lasers, 2020, 47(9): 0902001.