激光冲击强化H62黄铜摩擦磨损性能研究
下载: 835次
1 引言
磨损、腐蚀、断裂是材料失效的3种主要形式,其中由摩擦所导致的磨损失效是包括航空材料在内的机电材料失效的主要原因,70%~80%的设备损坏是由各种形式的磨损引起的[1]。磨损失效不仅造成零部件的浪费,严重时甚至会造成灾难性的后果,因此提高材料的耐磨性、延长其服役寿命成为当前亟需解决的问题之一。表面强化是提高金属材料耐磨性的一种有效方法,如利用喷丸[2]、表面机械研磨[3]、等通道转角挤压[4]等技术能够使材料发生塑性变形,以提高材料的硬度及强度,并在表面生成残余压应力层、诱导表面晶粒细化等,从而提高材料耐磨性。但这些表面处理技术均存在应变率较低、塑性变形层深度较浅、载荷较大时容易产生应力松弛等问题,为了解决以上问题,人们研究出了一种新的表面处理技术——激光冲击强化(LSP)。
LSP是一种新型的表面处理技术,在材料的表面改性方面具有巨大优势。LSP通过高能激光束辐照在贴有吸收层的金属材料表面,瞬间的高温促使吸收层汽化并产生等离子体冲击波,通过外部约束层作用于金属材料表面,并向材料内部传播,从而在材料内部产生较大的残余压应力,使材料内部发生塑性变形,产生高密度的位错、孪晶、层错等晶体缺陷以及晶粒细化,从而提高金属材料的机械性能。由于金属材料存在吸收层,故LSP不会在其表面产生热损伤,属于冷加工;但由于冲击波的力学效应,金属表面会发生塑性变形,从而引起表面的微观形貌和粗糙度的改变[5]。研究表明,LSP能够显著提高材料的疲劳寿命[6]及耐腐蚀[7]和耐磨损[8-9]的能力。何换菊等[10]研究了LSP对AZ31镁合金的摩擦磨损性能的影响,发现激光冲击可提高镁合金的表面显微硬度,其磨损量和磨屑都变得更小,经激光冲击后AZ31镁合金的耐磨性明显提高。本课题组[11]研究了激光冲击AISI 8620合金钢的摩擦学特性,发现激光冲击在AISI 8620合金钢表面形成了较深的残余压应力层,从而显著提高了表面硬度和耐磨性,多次冲击后可获得耐磨性能更好的AISI 8620合金。张兴权等[12]研究了激光喷丸强化对调质40Cr钢组织及耐磨性能的影响,研究结果表明,激光喷丸细化了40Cr钢表层的微观组织,强化后的显微硬度提高了30 %,强化后试样的磨损失重比原始试样减少了29 %,激光喷丸强化明显提高了40Cr钢的耐磨性,而且强化次数越多,耐磨性越好。
铜和铜合金是工业生产中广泛使用的金属材料之一,具有优良的导热性、导电性以及良好的切削加工性能。但较低的硬度和较差的耐磨性限制了其在某些对耐磨性要求较高领域的应用,如汽车变速器同步环、电机换向器的主要材料为黄铜,但未经强化处理的黄铜难以满足耐磨损的使用要求,容易发生磨损失效,因此需要对其表面进行改性处理以提高其耐磨性。研究表明,LSP可明显提高镁合金、不锈钢等材料的耐磨性,然而关于LSP对铜和铜合金摩擦磨损性能影响的研究却鲜有报道。本文以H62黄铜为研究对象,研究了不同层数激光冲击H62黄铜微观组织、显微硬度和表面粗糙度的变化,并通过对不同层数激光冲击后的H62黄铜进行室温下的往复干摩擦实验,研究了原始试样和LSP试样摩擦系数、磨损率以及磨痕形貌的变化,主要研究了不同层数激光冲击对H62黄铜摩擦磨损性能的影响,并揭示了其磨损机制。
2 实验材料及实验方法
2.1 实验材料
实验材料选用H62黄铜,其主要化学成分如
表 1. H62黄铜的化学成分
Table 1. Chemical composition of H62 brass
|
2.2 实验方法
LSP实验采用江苏大学激光研究所的Nd ∶YAG大功率激光器,选用的激光脉冲能量为6 J,冲击频率为1 Hz,波长为1064 nm,脉宽为10 ns,光斑直径为3 mm,横向纵向光斑搭接率为50 %,采用厚度为0.1 mm的专用铝箔(美国3M)作为吸收层,进行多层LSP实验时在每层激光冲击前需要更换吸收层,以防止多层重复冲击导致吸收层发生破裂,影响实验效果。采用厚度为1~2 mm的流水作为约束层,激光冲击区域关于试样中心对称分布,冲击面积为21 mm×21 mm,冲击路径如
采用高温摩擦磨损实验机(CETR UMT-2,CETR公司,美国)对原始试样、LSP-1试样和LSP-3试样进行往复式干摩擦实验,接触方式为球-盘式,实验磨球选用硬度为770 HV、直径为9.58 mm的440C不锈钢球,往复式干摩擦实验选用载荷为10 N,滑动速度为8 mm/s,滑动幅度为15 mm,每次往复干摩擦实验时间为30 min,实验温度为室温(25 ℃),相对湿度为60%。采用激光共聚焦显微镜(LEXT OLS4000,奥林巴斯公司,日本)测量磨痕的横截面积,在测量磨痕横截面积之前,将试样浸泡在丙酮溶液中进行超声波冲洗以清除磨损表面的碎片,然后冷风吹干。
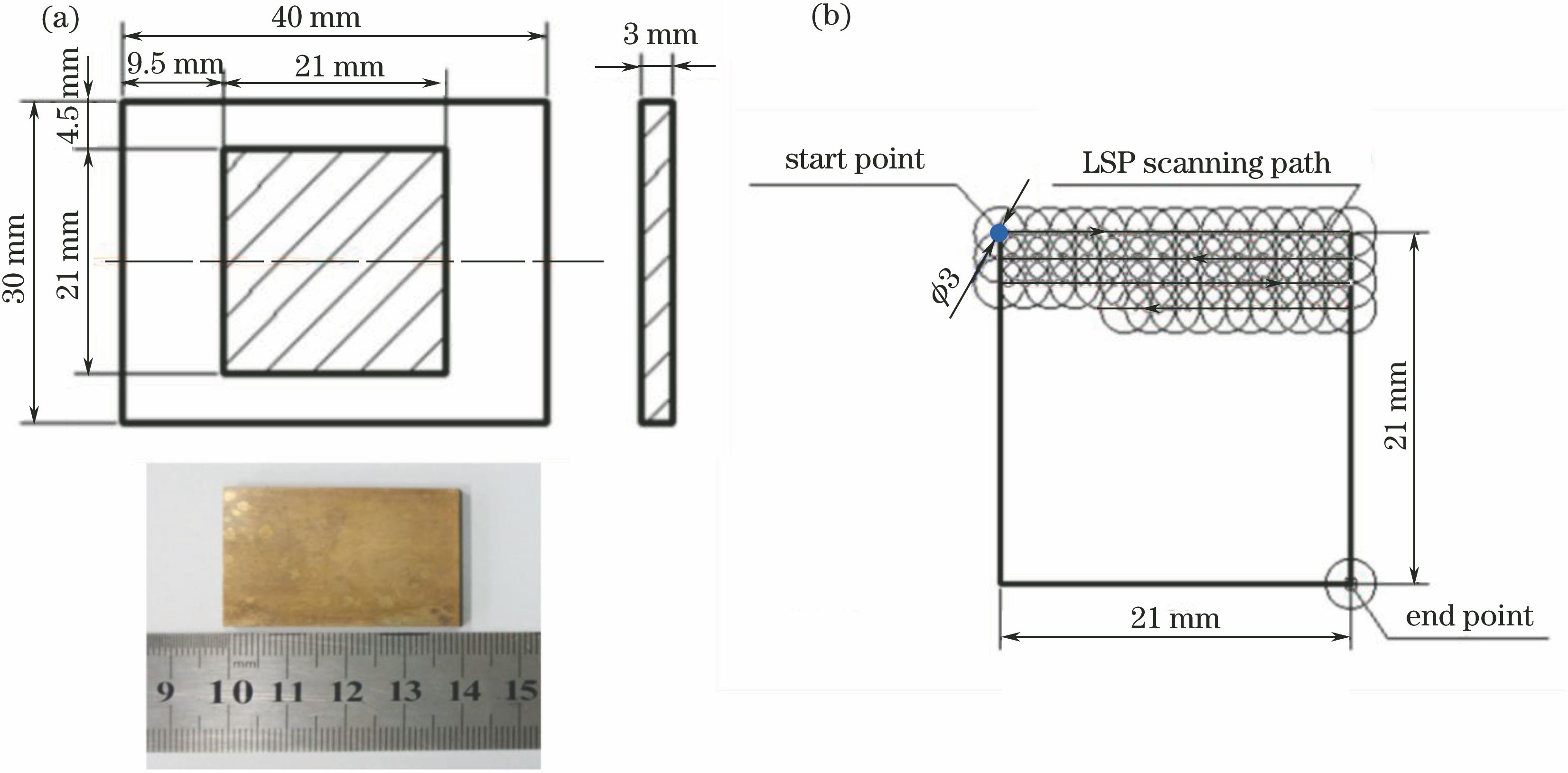
图 1. LSP试样。(a)尺寸; (b)冲击区域扫描路径
Fig. 1. LSP sample. (a) Dimension; (b) laser scanning path for impact area
激光冲击H62黄铜试样的截面显微硬度采用显微硬度测试仪(HXD-1000 TMC,上海泰明光学仪器公司,中国)测量,显微硬度测量时的载荷为0.49 N,保压时间为10 s,为获得较为准确的数据,在同一深度处的不同位置测量5次,并取其平均值作为该深度处的显微硬度值。采用真彩色共聚焦材料显微镜(Axio CSM 700,蔡司公司,德国)分别测量3种试样表面粗糙度,每个试样测量9次粗糙度,并取其平均值。采用江苏大学分析测试中心的型钨灯丝扫描电子显微镜(SEM,JSM-6390LV,电子株式会社,日本)观察磨损形貌。采用透射电子显微镜(TEM,JEM-2100,电子株式会社,日本)观察激光冲击前后H62黄铜的表层微观结构。
3 实验结果
3.1 显微硬度
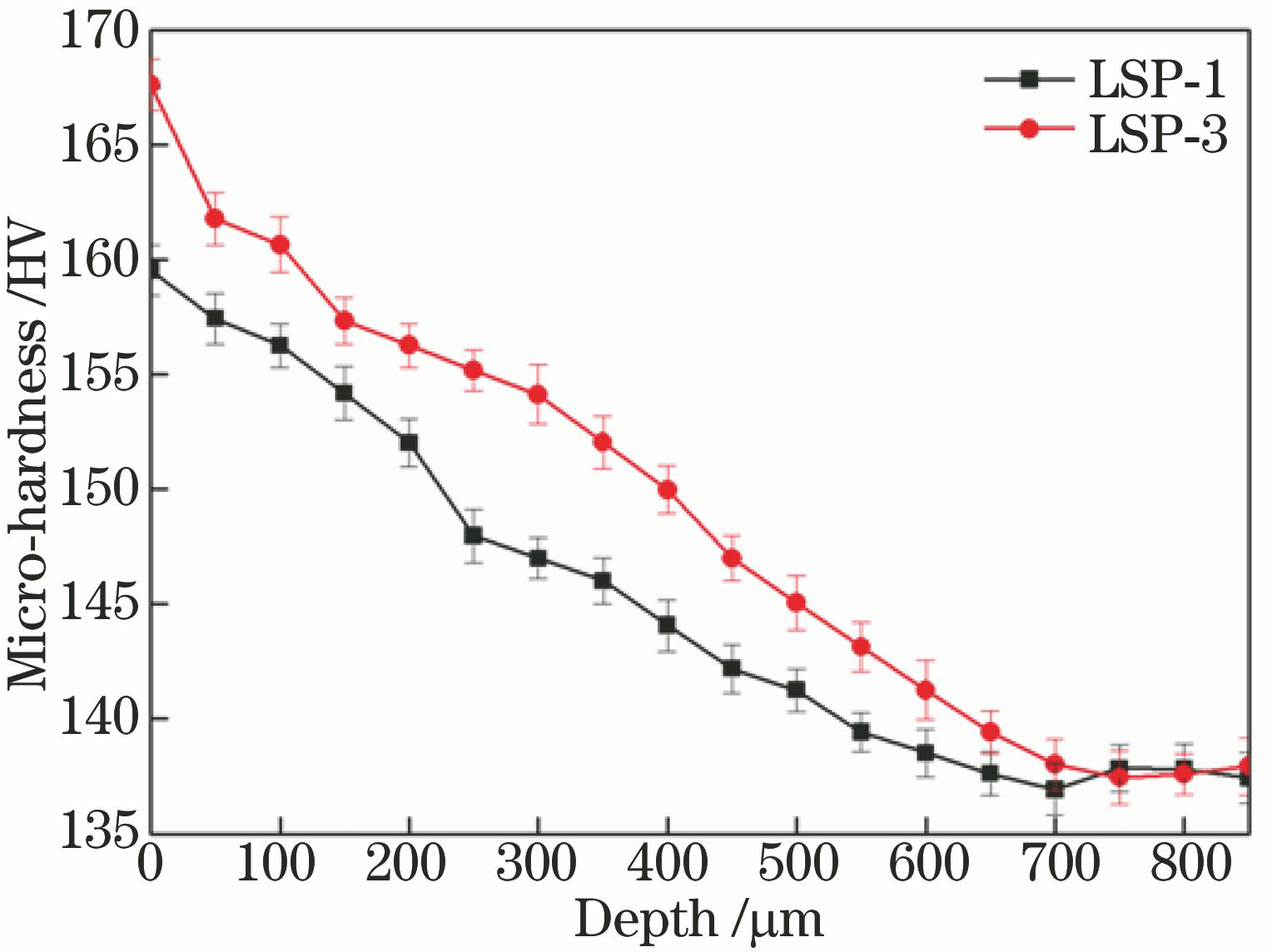
图 2. 不同层数激光冲击试样的截面显微硬度曲线
Fig. 2. Micro-hardness curves of cross-section in the samples subjected to LSP with different coverage layers
别为159.5 HV和167.6 HV,与原始试样相比,分别增加了15.9 %和21.8 %,表明LSP能够明显提高材料的显微硬度。但相比于LSP-1试样,LSP-3试样的显微硬度增加幅度较小,在AM50镁合金的LSP过程中也发现了同样的现象[13]。这是由于相比于第一层激光冲击在靶材内部产生的冷作硬化,随后的激光冲击难以生成同等程度的硬化[14]。随着冲击层数的增加,材料内部的塑性变形逐步趋于饱和,越来越难以发生塑性变形,因此硬度的变化也变得更不明显。
3.2 表面粗糙度
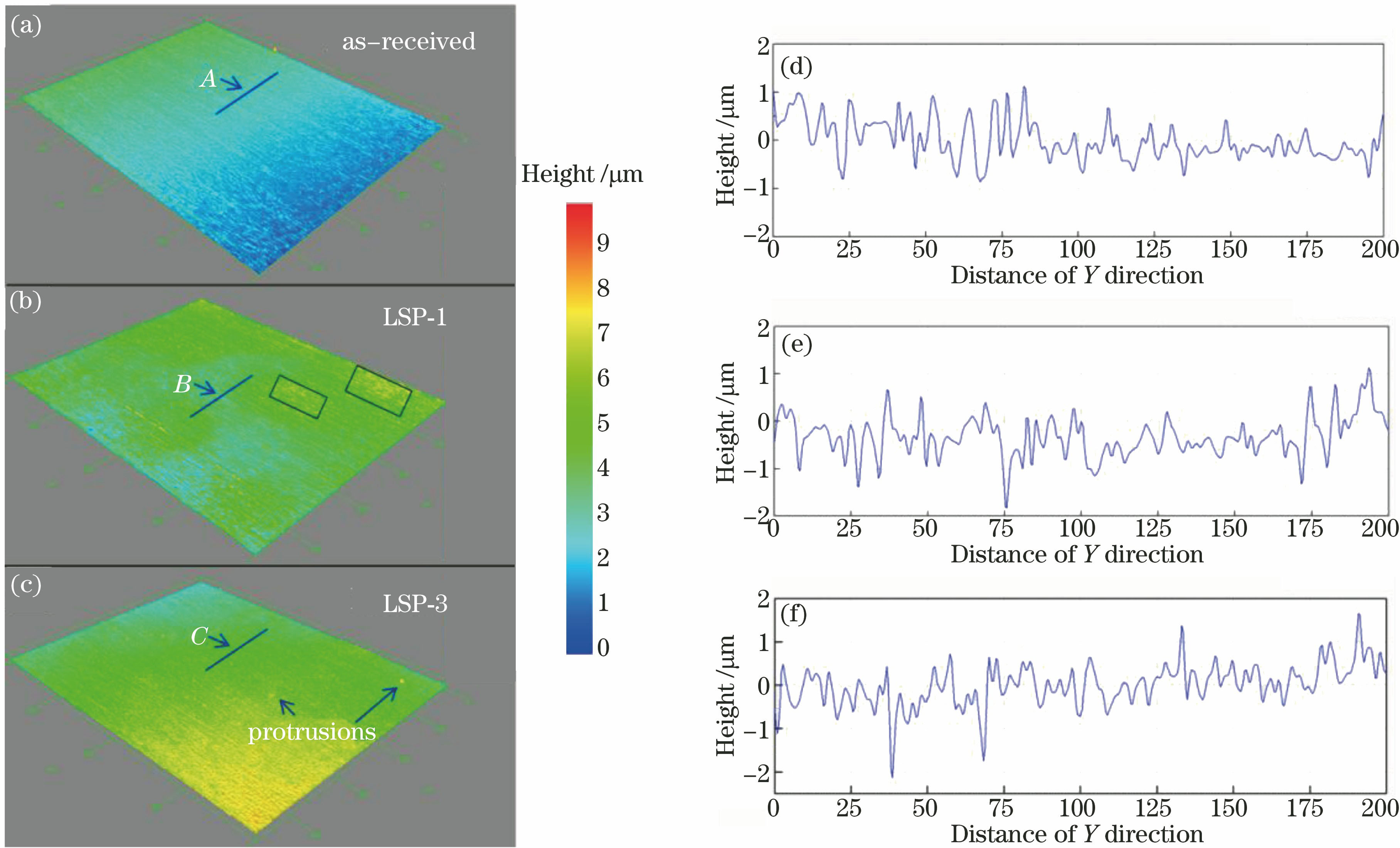
图 3. 三维和二维微观结构形貌。(a)原始试样的三维微观结构形貌; (b) LSP-1试样的三维微观结构形貌; (c) LSP-3试样的三维微观结构形貌; (d)原始试样的二维微观结构形貌; (e) LSP-1试样的二维微观结构形貌; (f) LSP-3试样的二维微观结构形貌
Fig. 3. Three-dimensional and two-dimensional micro-structure topographies. (a) Three-dimensional topographies of as-received sample; (b) three-dimensional topographies of LSP-1 sample; (c) three-dimensional topographies of LSP-3 sample; (d) two-dimensional topographies of as-received sample; (e) two-dimensional topographies of LSP-1 sample; (f) two-dimensional topographies of LSP-3 sample
此外,测量了原始试样、LSP-1试样和LSP-3试样的表面平均粗糙度值,本研究中平均粗糙度值是同一试样9个不同区域测得的粗糙度值的平均值。原始试样表面的平均粗糙度值为0.258 μm,LSP-1试样表面的平均粗糙度值为0.317 μm,而LSP-3试样表面的平均粗糙度值为0.366 μm,结果表明激光冲击增大了H62黄铜的表面粗糙度,且三层激光冲击后的表面粗糙度变得更大,这与
3.3 摩擦系数和磨损率
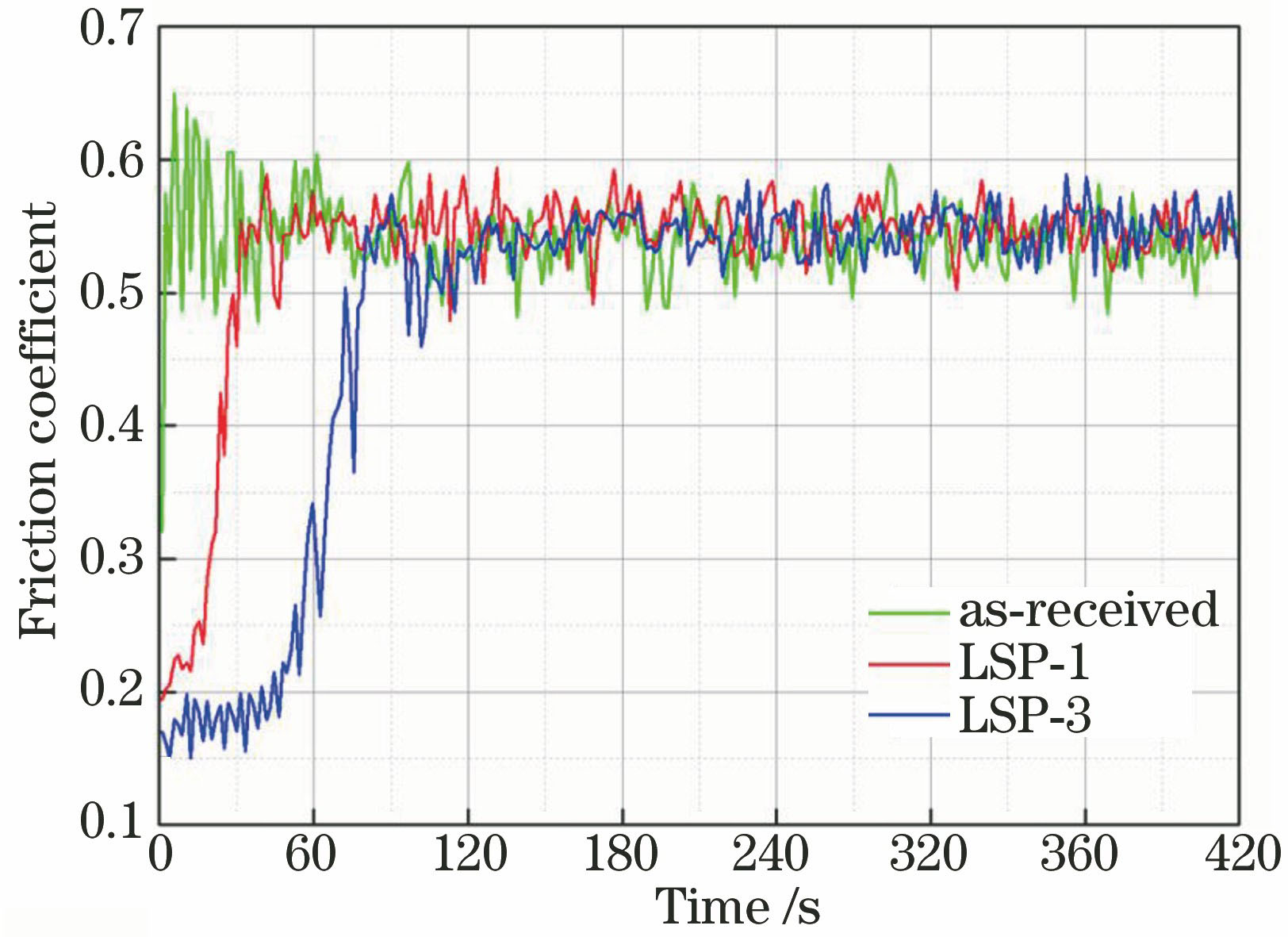
图 4. 原始试样和LSP试样摩擦系数随时间的变化曲线
Fig. 4. Curves of friction coefficients of as-received sample and LSPed samples varied with time
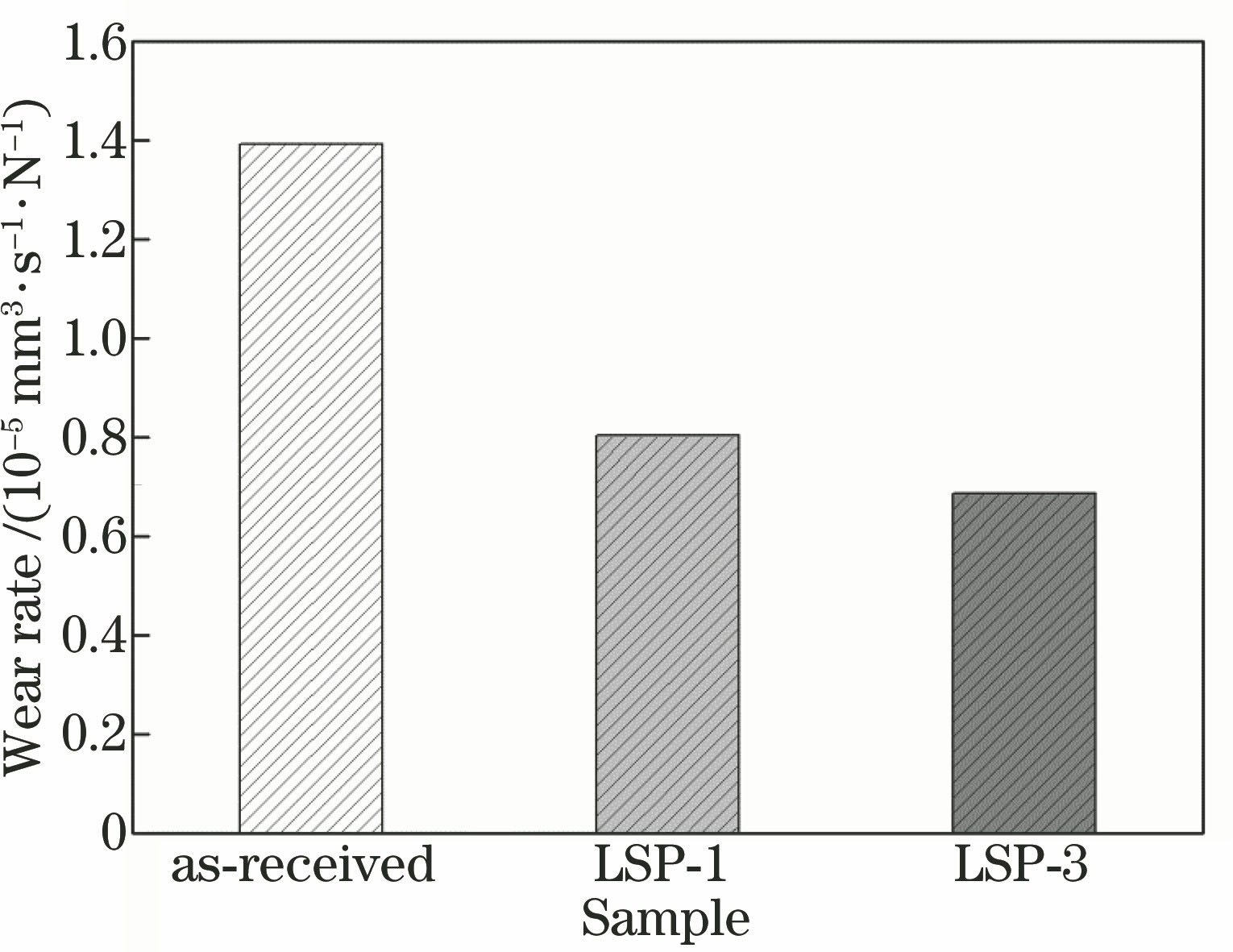
图 5. 相同载荷和滑动速度下原始试样和LSP试样的磨损率
Fig. 5. Wear rate of as-received sample and LSPed samples with same load and sliding velocity
为了更全面地研究LSP对材料耐磨性的影响,还研究了原始试样和LSP试样在磨损过程中的磨损率变化,并以此表征材料的耐磨性。
式中,
3.5 磨痕形貌
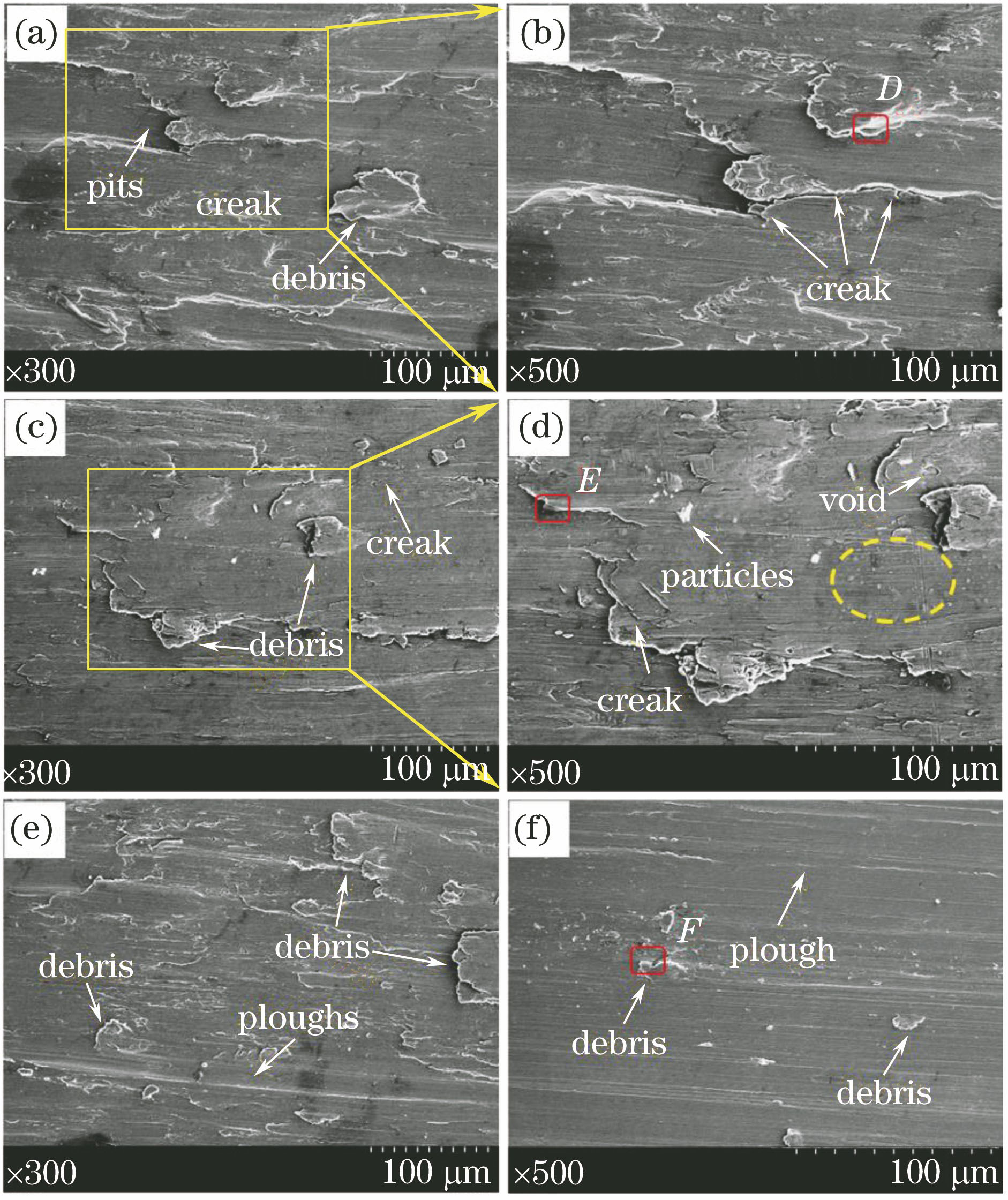
图 6. 不同试样磨损表面的典型SEM形貌。(a)、(b)原始试样;(c)、(d) LSP-1试样;(e)、(f) LSP-3试样
Fig. 6. Typical SEM micrographs of wear surface in different samples. (a), (b) As-received sample; (c), (d) LSP-1 sample; (e), (f) LSP-3 sample
综上所述,原始试样在磨擦过程中发生了磨粒磨损、剥层磨损和氧化磨损,主要的磨损形式为剥层磨损。LSP-1试样在磨擦过程中发生了磨粒磨损、剥层磨损、黏着磨损和氧化磨损,主要的磨损形式为剥层磨损。LSP-3试样在摩擦过程中发生了磨粒磨损、剥层磨损和氧化磨损,主要的磨损形式为磨粒磨损。
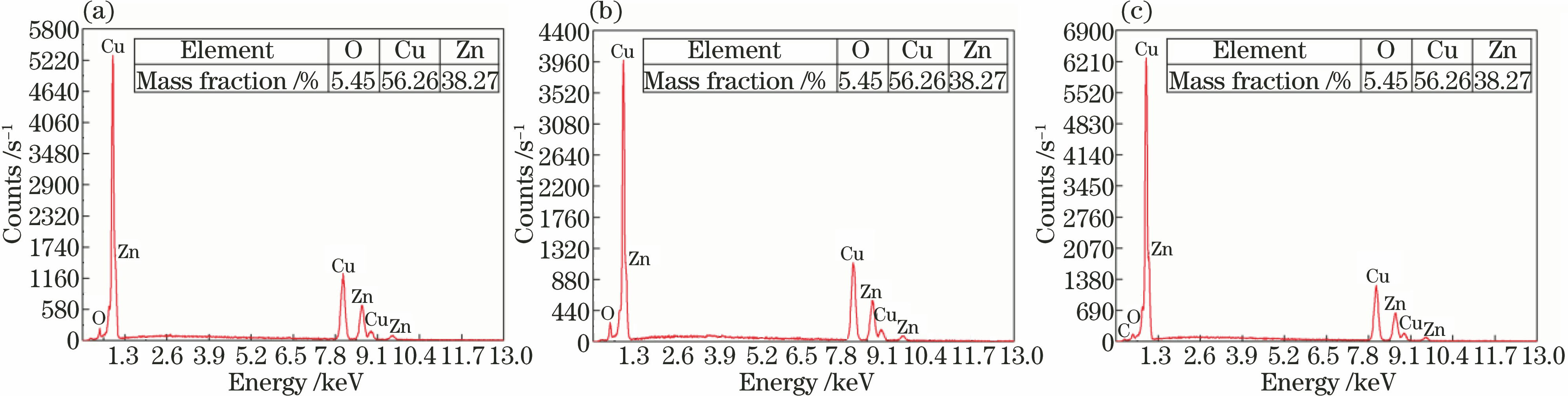
图 7. 不同试样磨损表面的EDS分析。 (a) 原始试样; (b) LSP-1试样; (c) LSP-3试样
Fig. 7. Analysis of EDS of wear surface in different samples. (a) As-received sample; (b) LSP-1 sample; (c) LSP-3 sample
4 分析与讨论
研究表明[16-17],激光冲击后的材料表面发生塑性变形,会在冲击光斑处形成微凹坑。这是H62黄铜表面粗糙度随冲击层数增加而增大的主要原因。
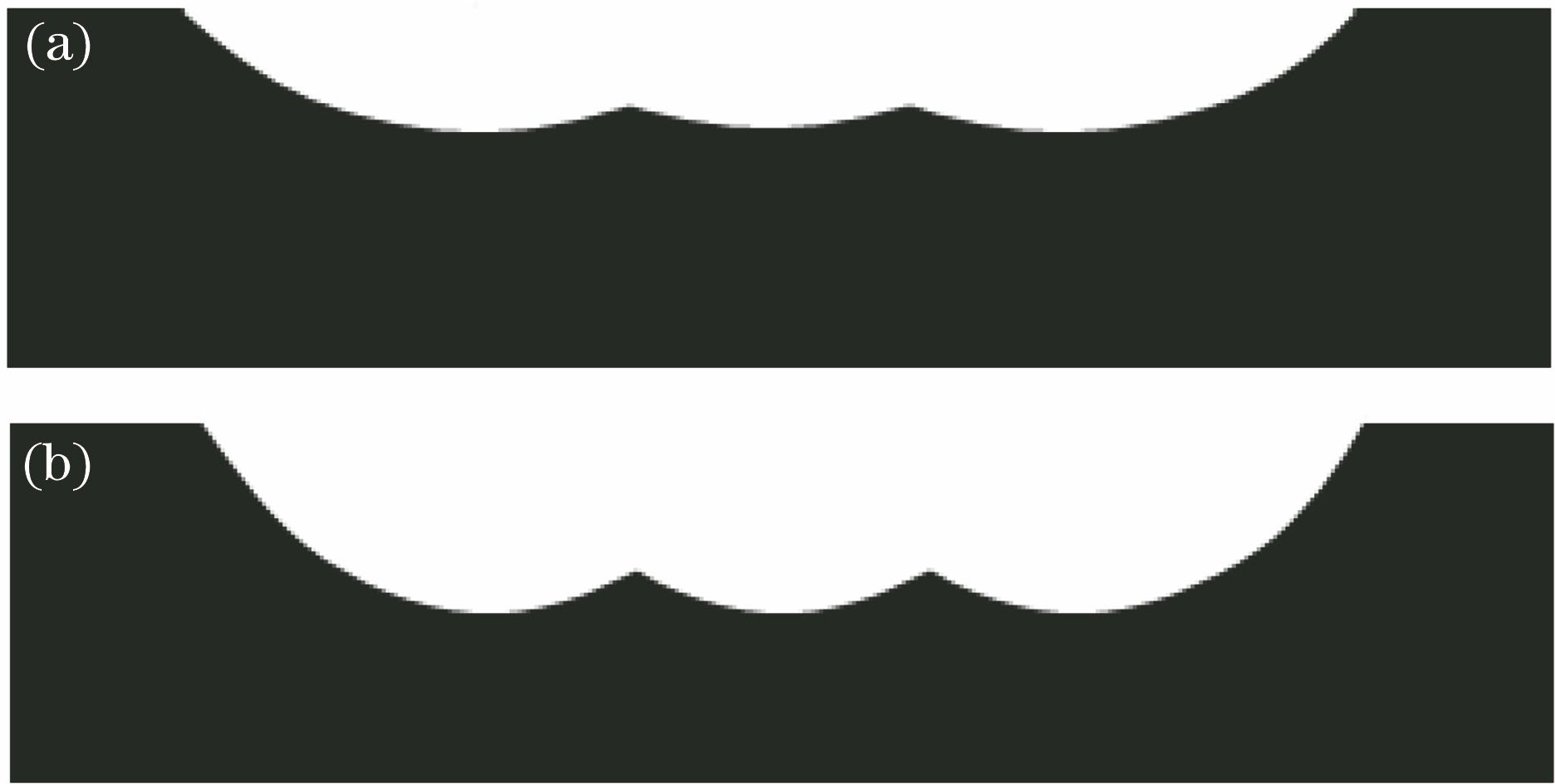
图 8. 冲击层数对H62黄铜表面粗糙度影响。 (a)一层冲击; (b)三层冲击
Fig. 8. Effect of coverage layer number on the surface roughness of H62 brass. (a) One coverage layer; (b) three coverage layers
通常情况下,表面粗糙度越大,磨损率就越大。然而从
实验现象表明LSP能够明显提高H62黄铜的耐磨性,且多层激光冲击后H62黄铜的耐磨性更好,这主要是因为LSP细化了H62黄铜的晶粒,在表面形成了纳米结构层。
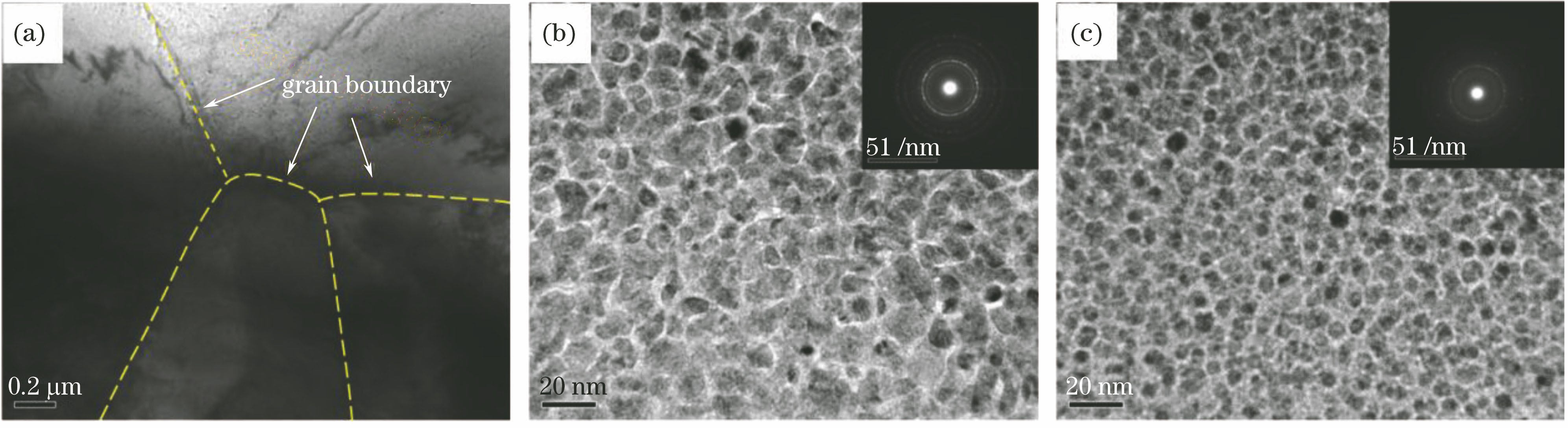
图 9. 激光冲击前后H62黄铜表面微观组织TEM图。 (a) 原始试样; (b) LSP-1试样; (c) LSP-3试样
Fig. 9. TEM images of microstructure in the top surface of H62 brass before and after LSP. (a) As-received sample; (b) LSP-1 sample; (c) LSP-3 sample
晶粒细化能明显提高材料的显微硬度,根据Hall-Petch理论,显微硬度与晶粒尺寸呈反相关,晶粒尺寸越小,材料的显微硬度越高。显微硬度与晶粒尺寸的关系可表示为
式中,
5 结论
为了进一步提高H62黄铜的耐磨性,扩大其应用范围,采用LSP技术对H62黄铜进行表面改性,并研究不同层数激光冲击对H62黄铜耐磨性能的影响。研究结果表明:
1)LSP处理明显细化了H62黄铜表层晶粒,在H62黄铜表面形成了纳米结构层,晶粒细化导致了表面显微硬度的提高,表面显微硬度从原始试样的137.6 HV,提高到单层激光冲击后的159.5 HV和三层激光冲击后的167.6 HV,分别提高了15.9%和21.8%。随着激光冲击层数的增加,H62黄铜的显微硬度值逐渐增加,但显微硬度增加的幅度减小,同一试样的显微硬度随着距表面深度的增加而逐渐减小。
2)LSP处理增大了H62黄铜的表面平均粗糙度,且表面平均粗糙度随着冲击层数的增加而增大。这主要是因为原始试样经较高粒度的砂纸打磨后,表面质量较高,LSP处理诱导H62黄铜产生了塑性变形,在试样表面形成了大量的凹凸微结构,从而增加了表面粗糙度。多层LSP在同一位置引发了多重塑性变形,微凹坑的变形得到了加强,从而导致其表面平均粗糙度更大。
3)LSP处理提高了H62黄铜的耐磨性。与原始试样相比,冲击后试样的摩擦系数和磨损率均减小,三层激光冲击后的摩擦系数和磨损率更小,但减小的幅度略有降低,表明冲击层数对材料耐磨性的提高有着显著影响,但这种强化效果的变化幅度随着冲击层数的增大而逐渐减小。激光冲击后,H62黄铜的磨损机制从以剥层磨损为主转变为以磨粒磨损为主。
[1] 屈晓斌, 陈建敏, 周惠娣, 等. 材料的磨损失效及其预防研究现状与发展趋势[J]. 摩擦学学报, 1999, 19(2): 187-192.
[2] 杨诗婷, 邢永明, 郎风超, 等. 喷丸强化316L不锈钢表面的摩擦磨损性能[J]. 金属热处理, 2016, 41(11): 35-39.
[5] 冯亚云, 叶云霞, 连祖焻, 等. 激光冲击强化对铜表面质量影响的实验研究[J]. 激光与光电子学进展, 2015, 52(10): 101401.
[10] 何换菊, 张凌峰, 杨根妹, 等. 激光冲击强化AZ31镁合金摩擦磨损性能的研究[J]. 中国激光, 2015, 42(9): 0906003.
[11] 钟俊伟, 鲁金忠, 罗开玉, 等. AISI 8620合金钢激光冲击强化层摩擦学特性[J]. 中国激光, 2012, 39(1): 0103001.
[12] 张兴权, 何广德, 汪世益, 等. 激光喷丸强化对调质40Cr钢组织及耐磨性的影响[J]. 材料热处理学报, 2011, 32(5): 138-142.
[13] 刘波, 罗开玉, 吴刘军, 等. 激光冲击强化对AM50镁合金性能和结构的影响[J]. 光学学报, 2016, 36(8): 0814003.
[16] 裴旭, 任爱国, 顾永玉, 等. AZ91镁合金激光冲击强化力学性能研究[J]. 激光技术, 2010, 34(4): 552-556.
[17] 王成, 胡家诚, 许杨剑, 等. 重复多次激光喷丸强化高导无氧铜的数值研究[J]. 激光与光电子学进展, 2016, 53(9): 091402.
[19] 田峰, 杨辉. 40Cr钢表面高能喷丸纳米化及其耐磨性能[J]. 表面技术, 2013, 42(5): 52-54.
[20] 钟金杉, 鲁金忠, 罗开玉, 等. 激光冲击对AISI304不锈钢拉伸性能和摩擦磨损性能的影响[J]. 中国激光, 2013, 40(5): 0503002.
[21] 庄乔乔, 张培磊, 李明川, 等. 铜合金表面激光熔覆Ni-Ti-Si涂层微观组织及耐磨性能[J]. 中国激光, 2017, 44(11): 1102002.
[22] LuK, Lu J. Nanostructured surface layer on metallic materials induced by surface mechanical attrition treatment[J]. Materials Science and Engineering:A, 2004, 375/376/377: 38- 45.
[23] 王镇波, 雍兴平, 陶乃殚, 等. 表面纳米化对低碳钢摩擦磨损性能的影响[J]. 金属学报, 2001, 37(12): 1251-1255.
Article Outline
段海峰, 罗开玉, 鲁金忠. 激光冲击强化H62黄铜摩擦磨损性能研究[J]. 光学学报, 2018, 38(10): 1014002. Haifeng Duan, Kaiyu Luo, Jinzhong Lu. Friction and Wear Properties of H62 Brass Subjected to Laser Shock Peening[J]. Acta Optica Sinica, 2018, 38(10): 1014002.