Performance improvement in double-ended RDTS by suppressing the local external physics perturbation and intermodal dispersion
Download: 863次
Distributed fiber temperature sensors exploit specific optical effects along optical fibers to obtain a spatially distributed profile of environmental temperature[13" target="_self" style="display: inline;">–
The temperature demodulation method is a crucial factor for improving the performance of the RDTS system. At present, there are two types of temperature demodulation methods, the self-demodulation method and dual-demodulation method. The self-demodulation method uses the Raman anti-Stokes backscattered light to determine the temperature through the sensing optical fiber[8,9]. The dual-demodulation method uses the ratio of the backscattered light of anti-Stokes over Rayleigh[10] or Stokes[1113" target="_self" style="display: inline;">–
To decrease the measurement error due to the local external physics perturbation, the dual-ended configuration RDTS has been proposed[15], and the double-ended configuration with self-demodulation can demodulate the temperature along the sensing fiber. But, the self-demodulation method has a high demand for the stability of the system[16], which limits the temperature accuracy and engineering applicability. In addition, the temperature demodulation methods based on the single-ended and double-ended configurations must execute the pre-calibration process. It requires the entire sensing fiber to be placed in a constant temperature field[1113" target="_self" style="display: inline;">–
In this paper, a novel double-ended RDTS system with a reference temperature and dynamic dispersion difference compensation method is proposed to improve the temperature accuracy and engineering applicability, which is available to suppress the fiber intermodal dispersion and local external physics perturbation. In addition, it can omit the pre-calibration process by using the reference temperature before the temperature measurement.
In the RDTS system, a short pulse of light is launched into the sensing fiber, generating two Raman backscattered components[18], which are measured as a function of time at the receiver side. While the intensity of the Raman down-shifted frequency component (Stokes) is only slightly temperature-dependent, the intensity of the up-shifted frequency component (anti-Stokes) strongly depends on the temperature of the sensing fiber. However, depending on the fiber attenuation and local loss, the anti-Stokes signal alone is usually not employed for absolute temperature measurements[16]. Actually, the dependence must be cancelled out by normalizing the anti-Stokes with a temperature-independent signal such as the Stokes. Thus, the ratio of anti-Stokes over Stokes intensity can be used to demodulate the temperature along the sensing fiber.
In the RDTS system, the backscattered light of Stokes and anti-Stokes is misaligned at the same position of the sensing fiber due to the fiber intermodal dispersion[13]. As shown in Fig.
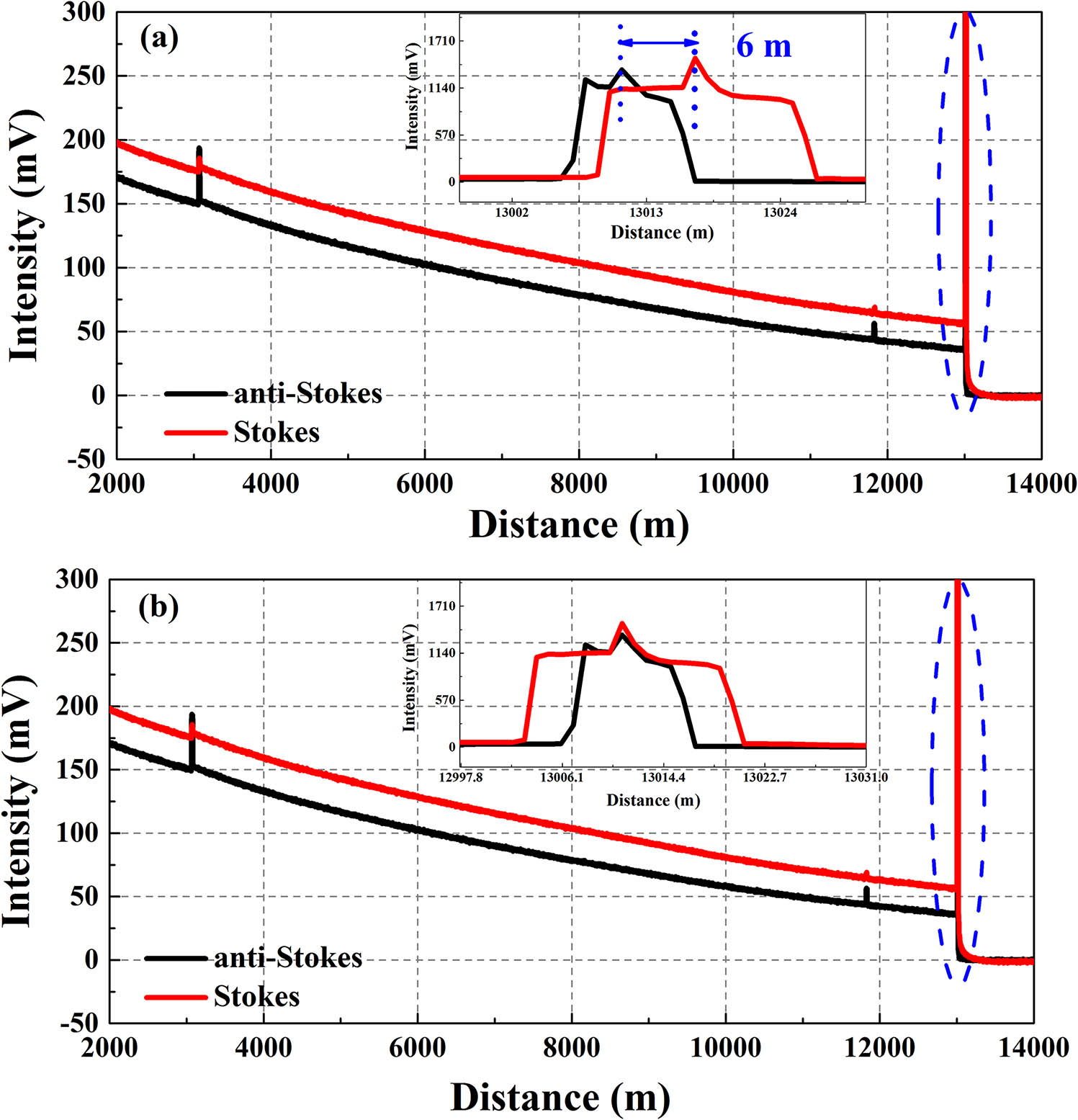
Fig. 1. Anti-Stokes and Stokes backscattered signal intensities (a) before the dispersion compensation and (b) after the dispersion compensation.
The dual-source calibration system[19] and the self-calibration speed algorithm[20] can also correct the effect of fiber dispersion on the RDTS. The dual-source calibration system utilizes two lasers (with a wavelength separation of 100 nm) to achieve the self-correction of the fiber dispersion. The self-calibration speed algorithm is used to calibrate the effect of fiber dispersion on the temperature demodulation of the RDTS. However, this method needs to measure the speed of Stokes and anti-Stokes before the temperature measurement. In this paper, the dynamic dispersion difference compensation method can establish an equation that uses the position of the dispersion compensation fiber and Fresnel reflection. It can calibrate the position of Stokes to match the position of anti-Stokes light. Compared with the above system, the dynamic dispersion difference compensation method does not add any devices to the RDTS, which reduces the cost of the system. In addition, this method does not require the calibration process when performing the temperature measurement.
In addition, the local fiber loss is not constant with time, since the sensing fiber may be exposed to environmental conditions that spectrally change the local fiber loss during the sensor lifetime[15]. The Raman backscattered intensity in the fiber is not only modulated by the temperature, but also related to local external physics perturbation. The traditional RDTS system based on the single-ended configuration does not consider the effect of local external physics perturbation on the temperature measurement results. Hence, significant errors can be induced when no further calibration is performed.
In order to eliminate this measurement error, the double-ended RDTS is proposed, which can obtain the forward and backward Raman backscattered signal, as shown in Fig.
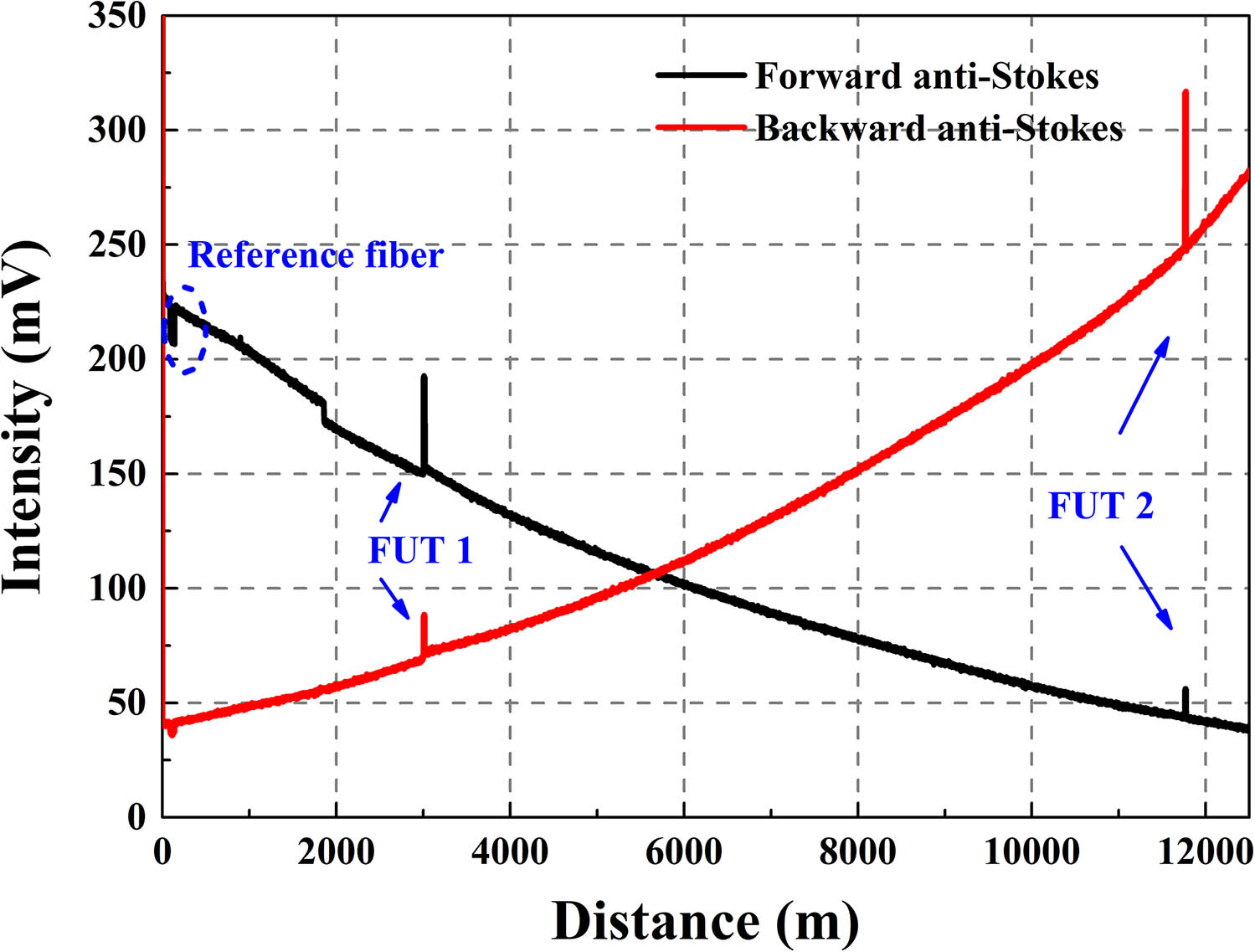
Fig. 2. Anti-Stokes backscattering signal intensity in both forward and backward directions.
Among them,
From Eq. (
In order to make the Raman signal only be modulated by the temperature along the fiber, the demodulation method needs to calibrate the difference attenuation of anti-Stokes and Stokes light before the temperature measurement, which limits the engineering application of RDTS[15,17]. In the double-ended RDTS, we set up a segment of reference fiber at the front of the sensing fiber, which can generate a reference temperature. The reference signal intensity in the double-ended configuration can be obtained from the geometric mean of the normalized single-ended system in both forward and backward directions according to the following formula:
Using Eqs. (
The experimental setup shown in Fig.
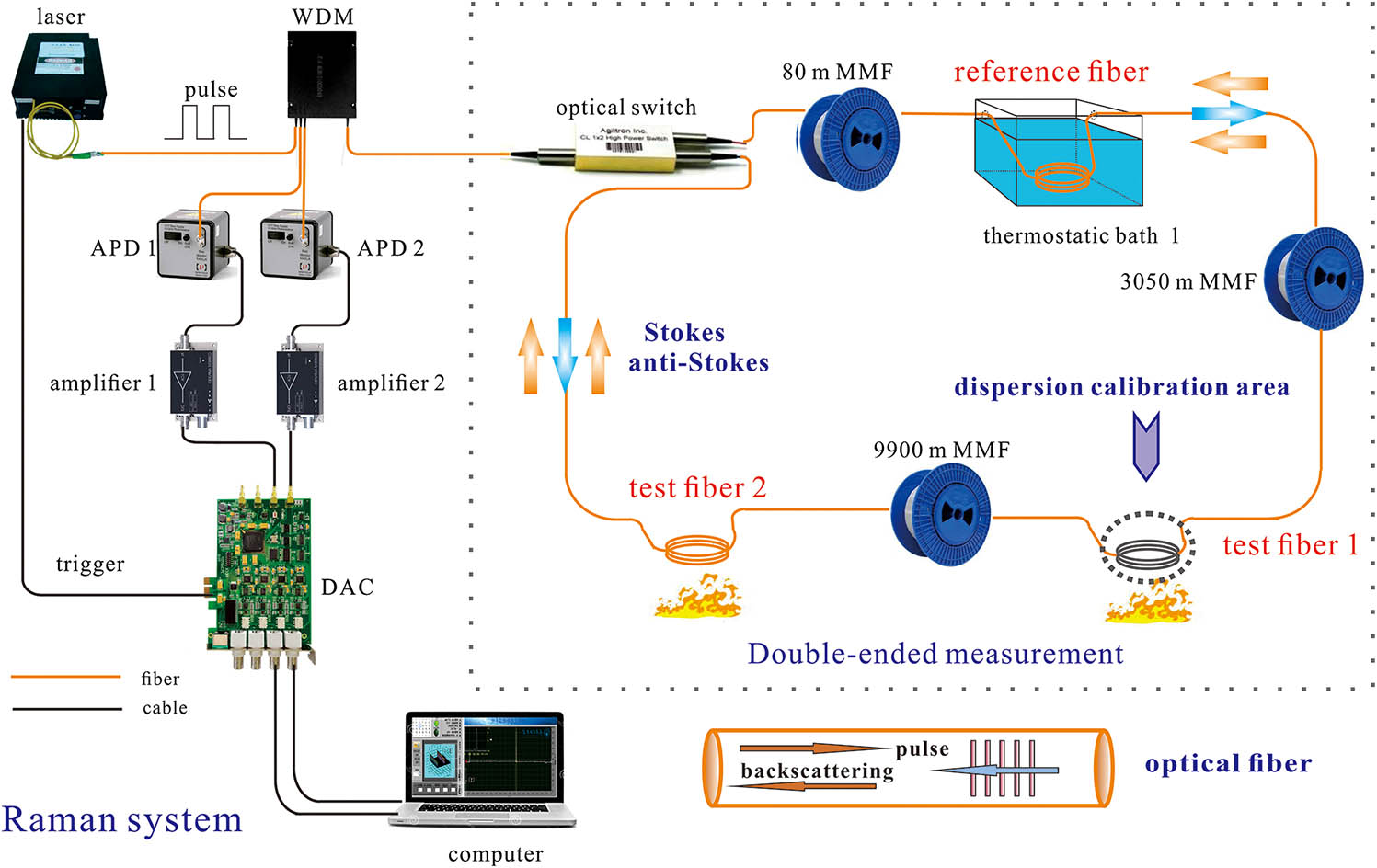
Fig. 3. Experimental setup of double-ended RDTS. WDM, wavelength division multiplexer; APD, avalanche photodiode; DAC, high-speed data acquisition card; PC, personal computer.
The temperature measurement experiment based on double-ended RDTS is carried out at room temperature of 30.0°C. The sensing fiber with the length of 13.0 km is used in the experiment. The FUTs are set at a distance of 3.07 and 11.83 km, respectively. The length of each FUT is about 15 m. The temperatures of FUTs are controlled by a water bath and are set at 40°C, 45°C, 50°C, 55°C, 60°C, and 65°C. The distributed temperature results after eliminating the ground noise[13] (with 15,000 time-averaged traces) are shown in Fig.
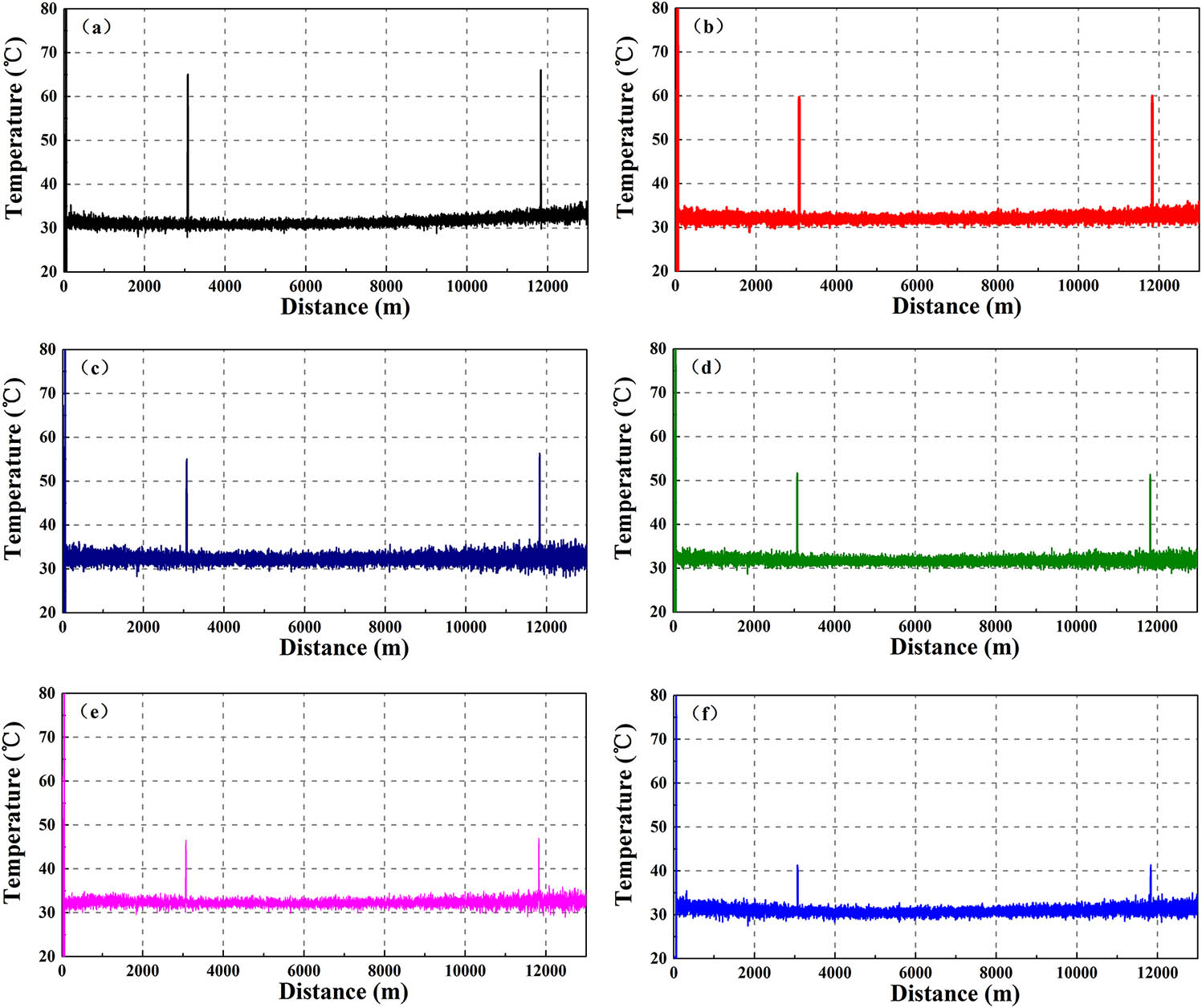
Fig. 4. Temperature measurement results along the sensing fiber under the temperature control of (a) 65°C, (b) 60°C, (c) 55°C, (d) 50°C, (e) 45°C, and (f) 40°C.
As shown in Fig.
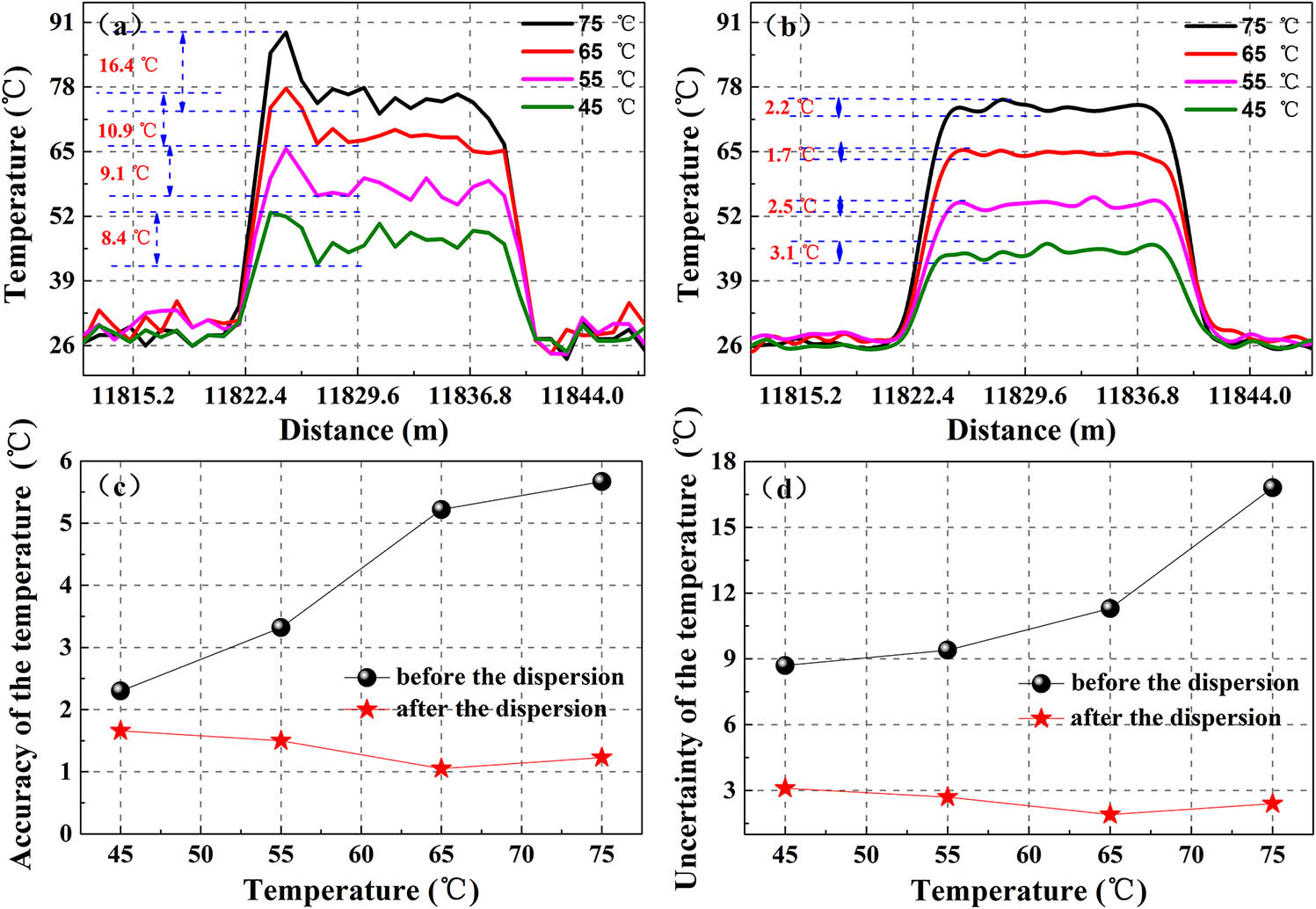
Fig. 6. Temperature measurement results of FUTs. (a) Results of measured temperature before the dispersion compensation. (b) Results of measured temperature after the dispersion compensation. (c) The temperature accuracy before the dispersion compensation and after the dispersion compensation. (d) The uncertainty of temperature before and after the dispersion compensation.
In order to eliminate the misalignment information caused by fiber dispersion, the Stokes signal needs to be compensated before the temperature measurement, and Fig.
During the long-term operation of the system, the single-ended configuration RDTS cannot avoid the measurement error caused by the local external physics perturbation with the environment change. The reason for this measurement error is that the local fiber loss is inconsistent at the calibration and measurement stages. As shown in Fig.

Fig. 7. Temperature demodulation results in (a) the single-ended configuration system and (b) the double-ended configuration system.
Among them,
We can see that the Raman signal is not only modulated by the temperature, but also related to local external physics perturbation (
These three methods mainly increase the temperature measurement accuracy and engineering applicability of the RDTS system. Firstly, the double-ended configuration can eliminate the influence of local external physics perturbation on measurement results, which can improve the engineering applicability. In addition, the function of the reference fiber can omit the calibration process before the temperature measurement (improve the engineering applicability). Finally, the dynamic dispersion difference compensation method can compensate the fiber intermodal dispersion for improving the temperature accuracy. Although an optical switch is introduced into the double-ended RDTS, compared to the single-ended RDTS, the double-ended RDTS requires twice the length of the fiber at the same sensing distance.
In conclusion, we propose and experimentally demonstrate a double-ended RDTS with a reference temperature to improve the temperature accuracy and engineering applicability. The double-ended configuration can eliminate local external physics perturbation of the sensing fiber with environmental change. The dynamic dispersion difference compensation method is used to compensate the fiber dispersion for improving the temperature accuracy. The experimental results indicate that the temperature accuracy optimizes from 5.6°C to 1.2°C, the relative errors decrease from 7.4% to 1.6%, and the temperature uncertainty optimizes from 16.8°C to 2.4°C. In addition, the function of the reference fiber can omit the calibration process before the temperature measurement. The proposed method is expected to be a good solution for the systems that require auto-correction functionality for improving the performance of RDTS.
[1]
[2]
[3]
[4]
[5]
[6]
[7]
[8]
[9]
[10]
[11]
[12]
[13]
[14]
[15]
[16]
[17]
[18]
[19]
Jian Li, Yang Xu, Mingjiang Zhang, Jianzhong Zhang, Lijun Qiao, Tao Wang. Performance improvement in double-ended RDTS by suppressing the local external physics perturbation and intermodal dispersion[J]. Chinese Optics Letters, 2019, 17(7): 070602.