激光工艺参数对激光熔化沉积纯钛样品残余应力的影响
下载: 1048次
1 引言
近年来,基于“分层制造、逐层叠加”的激光增材制造 (3D打印) 技术[1]受到了广泛关注,与传统制造方法[2]相比,其具有快速设计到投入生产,可实现复杂几何形状制造的优点。这一新兴技术在医学领域得到快速发展,其打印材料主要为钛及钛合金[3]、不锈钢及与人体组织相容性较好的生物材料。然而,在激光增材制造过程中,局部集中的能量输入导致了成形件温度梯度高、温度场分布不均匀且非稳态,以及热影响区的非均匀热膨胀和收缩,这些因素直接导致成形件残余应力的形成[4]。从一层到另一层,大量的残余应力在样件内部堆积,如果不加以调控,将导致成品变形、裂纹形成的敏感性增加及疲劳性能降低[5]。为了调控这种复杂的制造过程,需要正确理解与之相关的许多物理现象[6]。在选区激光熔覆(SLM)制造过程中,使用不正确的工艺参数,可能会导致不良的零部件性能 (例如内部气孔、夹渣及裂纹等) 和过高的热应力集中[7]。
因此,工艺参数对激光增材制造构件残余应力的影响[4,5,8-14]已是当前的研究热点。Dunbar等[15]的研究结果表明,随着扫描层数的增加,基体和成形体变形程度有所降低,同时研究结果还发现采用SLM制备的零件不同方向残余应力也会有所差异。Cheng等[16]发现了SLM过程中扫描矢量方向的残余应力远大于横向方向的残余应力,SLM零件或基体沿扫描方向比横向方向的变形更大[16-17]。但这些研究大多以研究单一工艺参数条件下结构件残余应力分布为主,而采用激光增材制造制备的构件的残余应力的分布强烈依赖于激光工艺参数、扫描方式及材料物理性质等因素,激光工艺参数对不同材料构件的残余应力分布的影响及其机理还有待深入研究。
基于此,本文以纯钛作为研究对象,采用同轴送粉激光沉积技术,在不同的激光工艺参数下制备纯钛试样,并采用小孔法对沉积态试样扫描面上的残余应力进行测试,研究激光功率、扫描速度及送粉率等工艺参数对激光沉积纯钛样件残余应力场分布规律的影响。
2 实验方法
2.1 原材料与样品制备
实验选用氩气雾化纯钛球形粉,粒度分布情况如下:
激光增材制造工艺参数对样件质量有重要影响,这些工艺参数包括激光参数、材料特性参数、加工工艺参数、加工策略和加工环境这5类参数,其中影响较为显著的参数有激光功率
表 1. 激光增材制造工艺参数
Table 1. Process parameters for laser additive manufacturing
|
为了研究不同工艺参数对成形件表面上的残余应力分布特征的影响,本研究采用小孔法,对
2.2 小孔法残余应力测试原理
目前残余应力的检测方法主要分为两大类:一种是以X射线法为代表的物理检测法,另一种是以小孔法为代表的机械法,前者精度高但成本也高且可操作性较差,后者虽具有一定的破坏性但更方便
快捷且技术成熟。因此,采用小孔法对扫描面上的残余应力进行测试。
小孔法是在待测量残余应力位置粘贴好应变花,在应变花标定位置钻孔时伴随着孔附近应力的释放,应力释放产生不同方向上的应变的释放,通过应变花测量得到的数值,根据弹性力学理论推算出小孔处的残余应力[19]。为降低实验误差,对每个成形件进行弹性模量
具体的实验方法是先将测试位置用金相砂纸轻微打磨,然后用丙酮对其进行进一步的清洗。一方面,去除表面氧化皮层,适度提高表面光洁度;另一方面,防止打磨过程中因外力作用引入二次应力。考虑到钻削热的影响,实验过程中采取求平均值的方法计算应变值。
3 实验结果与分析
3.1 扫描面上的残余应力分布
本研究采用小孔法,对采用不同激光工艺参数得到的试样的扫描面的残余应力分布进行测试,其测试结果如
表 2. 残余应力测试结果
Table 2. Measurement results of residual stressesMPa
|
由
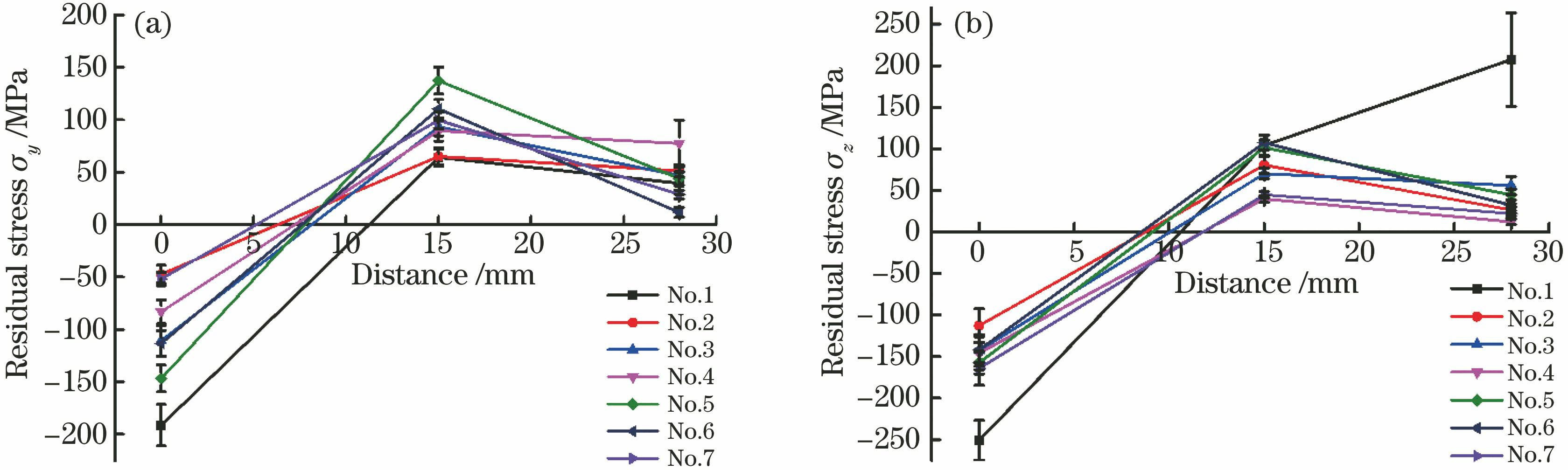
图 3. 不同方向的残余应力分布。(a)水平方向;(b)高度方向
Fig. 3. Residual stress distributions along different directions. (a) Horizontal direction; (b) height direction
3.2 工艺参数对残余应力分布影响
为研究工艺参数对沉积态样件残余应力的影响,分别对激光功率、扫描速度及送粉率与残余应力之间的关系进行分析,其结果如
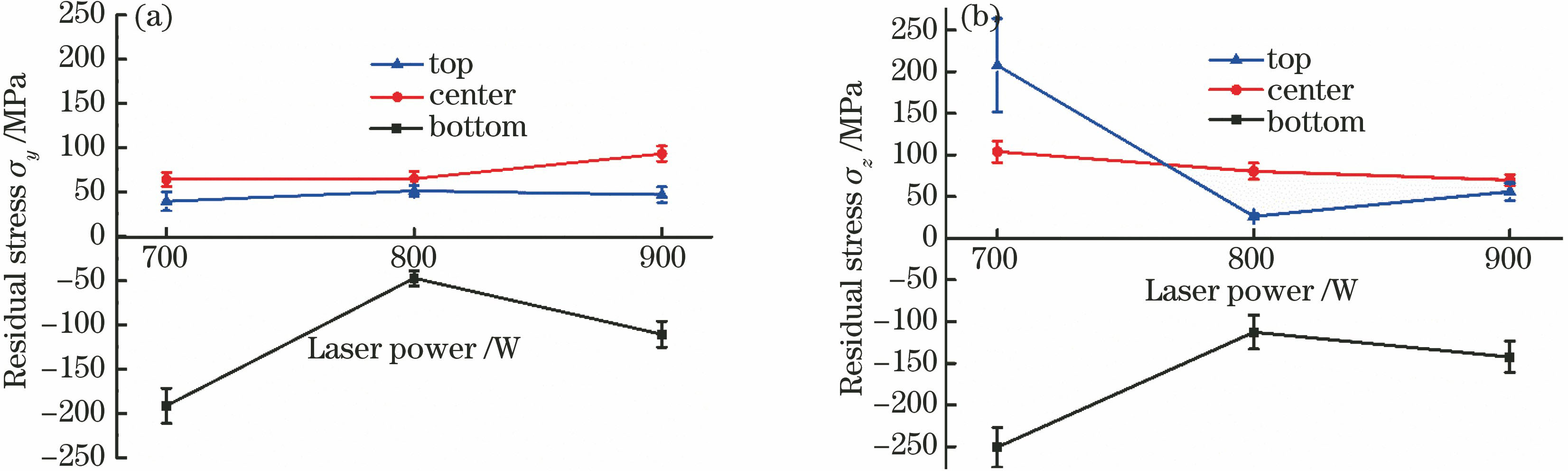
图 4. 不同方向上,激光功率对残余应力影响。(a)水平方向;(b)高度方向
Fig. 4. Residual stress versus laser power under different directions. (a) Horizontal direction; (b) height direction
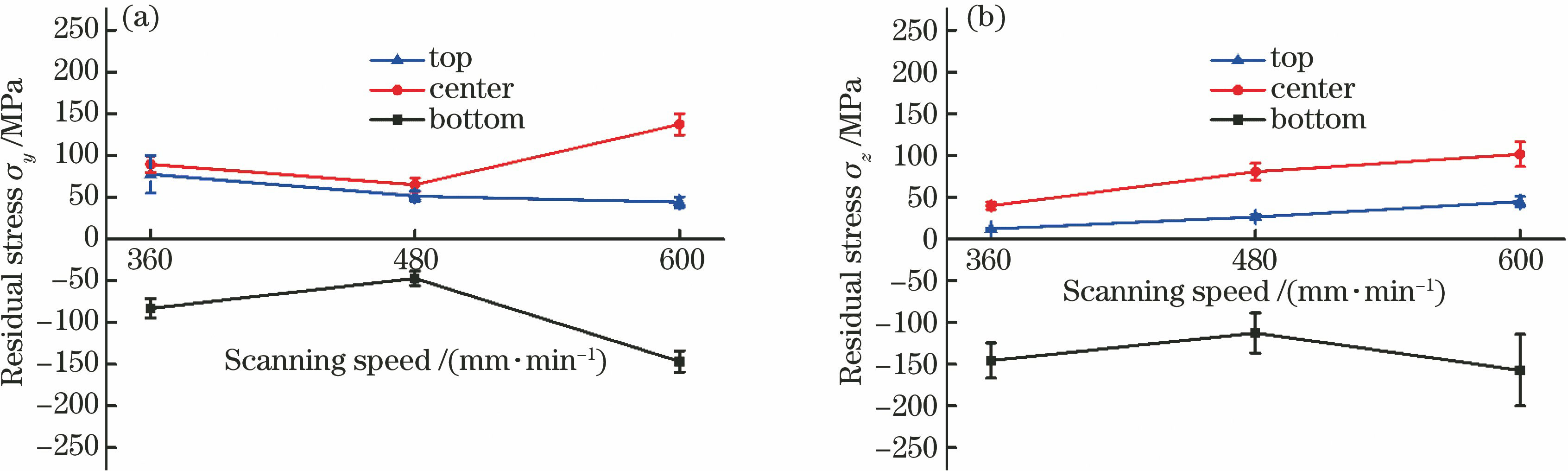
图 5. 不同方向上,扫描速度对残余应力的影响。(a)水平方向;(b)高度方向
Fig. 5. Residual stress versus scanning speed under different directions. (a) Horizontal direction; (b) height direction
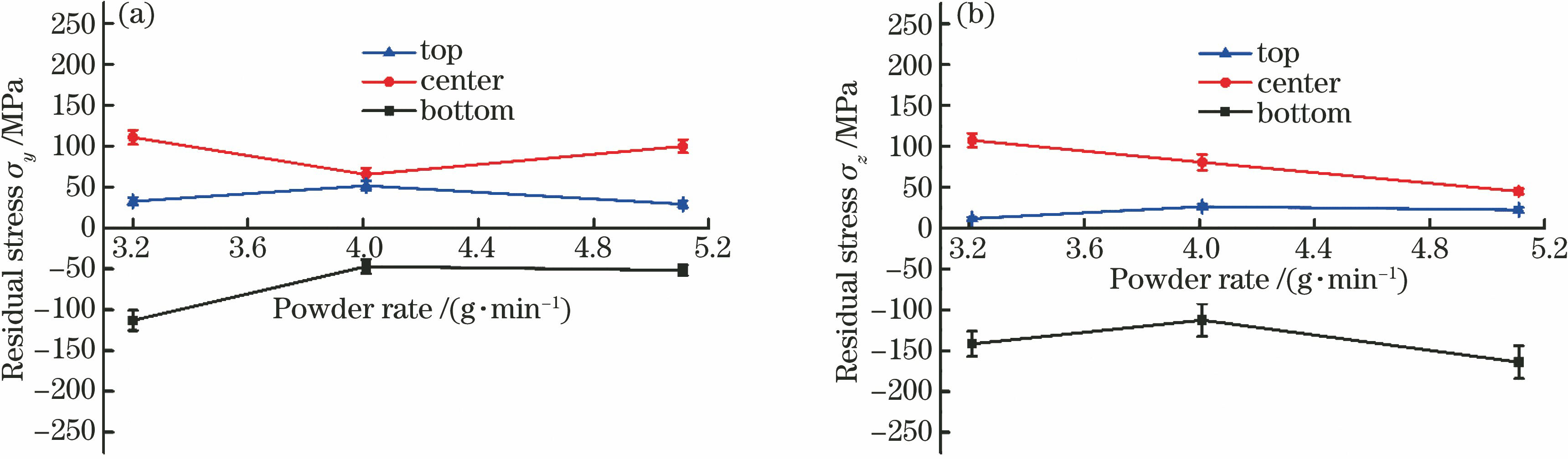
图 6. 不同方向上,送粉率对残余应力的影响。(a)水平方向;(b)高度方向
Fig. 6. Residual stress versus powder feeding rate under different directions. (a) Horizontal direction; (b) height direction
由以上结果可以看出,激光工艺参数对样件底部的残余应力的分布有较大影响,而对样件顶部区域的残余应力影响不大。对于样件底部区域,随着激光功率、扫描速度及送粉率的增加,样件底部与基体结合区扫描方向和增材方向的残余应力均呈先增加后减小的变化趋势。激光功率为800 W、扫描速度为480 g/min,送粉率为4.02 g/min 时扫描方向和增材方向的残余应力最小,分别为-47.293 MPa、-112.631 MPa,且沉积件外观质量最好,如
对于样件中部区域,其增材高度方向上的残余应力随激光功率和送粉率的增加而减小。在激光功率和送粉率一定时,其增材高度方向上的残余应力随扫描速度的增加而增大;扫描方向的残余应力随功率的增加而增大,随着扫描速度和送粉率的增加则表现为先减小后增大。对比沿增材高度方向与沿扫描方向的残余应力测试结果不难发现,随激光参数的改变两者表现出不同变化规律。沿增材高度方向的残余应力随激光功率增加而减小,随扫描速度的增加而增大,随送粉率的增加而减小;沿扫描方向的残余应力随功率的增加而增大,而随着扫描速度及送粉率的增加则表现为先减小后增大的变化趋势。
4 分析与讨论
从上述实验结果可以看出,激光沉积样件的扫描面上的残余应力分布十分复杂,容易受激光工艺参数的影响,而且残余应力分布具有局域性。
沉积样件残余应力表现出来的应力分布规律主要受温度梯度及激光冲击的影响[22-23],而底部与基材结合位置的残余应力除了受温度梯度的影响还受基材的影响,
在激光沉积的初始阶段,基体材料正处于较低的温度,高能量的热源迅速熔化上层的粉末导致结合区域的温度梯度非常大且增材方向的温度梯度远远大于扫描方向的温度梯度,而且随着激光沉积的进行,基材温度逐渐上升,热积累导致温度梯度逐渐下降,直至顶部温度梯度最小。温度梯度越大,残余应力越大[20],因此沉积体结合区域的残余应力最大,且增材方向的残余应力大于扫描方向的残余应力。
激光功率的增加,一方面,熔池将会得到更高的能量,温度分布不均匀情况加剧,温度梯度增加使得底部残余压应力增加;另一方面,由于层与层之间扫描方向一致,扫描过程中第二层会对第一层产生影响,适度地增加激光功率有利于第一层热处理效应,进而降低第一层的残余应力,但过高的激光功率则会产生更大冲击变形诱导新的残余应力的产生。
除了底部的温度梯度大之外,扫描速度的适度降低,一方面使得激光束对熔池的作用时间增加,对下一层的热处理效果增强有利于残余应力的降低,另一方面,过低的扫描速度会增加激光对下一层的冲击影响进而增大残余应力。送粉率较低时,高能量的热源足够熔化粉体但同时也会对成形熔覆层产生较大的冲击影响,但当送粉率过高时,高能量的热源会使熔池凝固后的体积收缩量变大,这两种因素分别与底部温度梯度大的因素相互作用,均会导致底部的残余应力变大。
而在构件中部,激光工艺参数对该区域的影响规律较为复杂,激光功率的增加使得正在进行激光沉积过程中的沉积体整体温度升高,大大降低了增材方向的温度梯度,因此残余应力随之降低;扫描速度增加即激光能量作用于沉积体的时间减少,增材方向的温度梯度随之升高,残余应力增大;送粉率对增材方向残余应力的影响主要表现为受粉体与激光光束之间的相互作用,单位体积熔池中的能量输入减小,增材方向的温度梯度随之降低,因而残余应力随送粉率的增加而减小。因此,激光功率越大使得扫描方向的温度梯度大,从而导致残余应力增加。而在较高的扫描速度下,单层增量降至0.6 mm,激光束作用在熔池上的时间减少,导致扫描路径方向的温度梯度变大,残余应力变大;相比之下,在低的扫描速度下,扫描路径方向受激光冲击影响比较大,因而产生的残余应力较大。送粉率的增加使得熔池凝固后的体积收缩量变大,从而使得残余应力变大,但过低的送粉率受粉体与激光束相互作用的影响,单位体积熔池中能量输入增加,温度梯度增大,残余应力增大。基于上述原因,在沉积态构件的中部,其沿增材高度方向的残余应力与沿扫描方向的残余应力随激光参数的变化规律不同。
由此可见,通过调节激光工艺参数,可以控制构件的残余应力分布。对于纯钛合金,在激光功率为800 W,扫描速度为480 g/min,送粉率为4.02 g/min时,所制备的构件的扫描方向和增材方向的残余应力最小,分别为-47.293 MPa和-112.631 MPa。
5 结论
测试分析了不同工艺参数下激光熔化沉积纯钛构件的残余应力,与现有的研究结果相比,本研究侧重于扫描面沉积高度方向的应力分布随工艺参数变化的规律。通过分析不同区域的残余应力发现:沉积体与基材结合区残余应力为压应力,构件中部和顶部区域均为拉应力,构件沿增材高度方向的残余应力要略大于沿扫描方向的残余应力;沉积件的顶部区域为残余应力最小区域,且工艺参数对该区域的残余应力影响不大;沉积体与基材结合区是激光熔化沉积纯钛样件高残余应力区,随激光功率、扫描速度及送粉率的增加,该区域的残余应力均呈先减小后增加的趋势;在沉积构件的中部区域,沿增材高度方向的残余应力与沿扫描方向的残余应力随激光工艺参数的改变表现出不同变化规律,分析认为,激光沉积件沉积过程中形成残余应力主要受到激光冲击、温度梯度、熔池热收缩等因素交互作用的影响。
实验中激光熔化沉积纯钛样件未经退火处理,因此为了降低残余应力,得到力学性能优良的样件,接下来将会进行一系列的去应力退火处理,并进一步分析退火后的样件残余应力分布规律及其与工艺参数之间的关系。
[2] HopkinsonN, HagueR, DickensP. Rapid manufacturing: an industrial revolution for the digital age[M]. Chichester: John Wiley & Sons, 2006: 228- 229.
[3] YadroitsavaI, GrewarS, HattinghD, et al. Residual stress in SLM Ti6Al4V alloy specimens[J]. Materials Science Forum, 2015, 828/829: 305- 310.
[4] CasavolaC, S L, Campanelli C. Pappalettere C. Experimental analysis of residual stresses in the selective laser melting process[C]. Proceedings of the XIth International Congress and Exposition, 2008: 18270126.
[9] Kruth J P, Deckers J, Yasa E, et al. Assessing and comparing influencing factors of residual stresses in selective laser melting using a novel analysis method[J]. Proceedings of the Institution of Mechanical Engineers, Part B: Journal of Engineering Manufacture, 2012, 226(6): 980-991.
[10] Kruth JP, BadrossamayM, YasaE, et al. Part and material properties in selective laser melting of metals[C]. International Symposium on Electromachining, 2010, 16: 3- 14.
[13] Roberts IA. Investigation of residual stresses in the laser melting of metal powders in additive layer manufacturing[D]. Wolverhampton: University of Wolverhampton, 2012: 246.
[15] Dunbar A J, Denlinger E R, Heigel J, et al. Development of experimental method for in situ distortion and temperature measurements during the laser powder bed fusion additive manufacturing process[J]. Additive Manufacturing, 2016, 12: 25-30.
[18] 朱刚, 张晖, 张旺峰, 等. 高强度钛合金管材残余应力测试及对比分析[J]. 稀有金属材料与工程, 2014, 43(10): 2492-2496.
[19] 杨健, 陈静, 杨海欧, 等. 激光快速成形过程中残余应力分布的实验研究[J]. 稀有金属材料与工程, 2004, 33(12): 1304-1307.
[22] 蔡春波, 李美艳, 韩彬, 等. 不同预热温度下宽带激光熔覆铁基涂层数值模拟[J]. 应用激光, 2017, 37(1): 66-71.
[23] 罗开玉, 周阳, 鲁金忠, 等. 激光冲击强化对316L不锈钢熔覆层微观结构和性能的影响[J]. 中国激光, 2017, 44(4): 0402005.
[24] 杨健, 黄卫东, 陈静, 等. 激光快速成形金属零件的残余应力[J]. 应用激光, 2004, 24(1): 5-8.
Article Outline
孙洪吉, 韦靖, 郑兆宏, 张德闯, 林建国. 激光工艺参数对激光熔化沉积纯钛样品残余应力的影响[J]. 中国激光, 2019, 46(3): 0302014. Hongji Sun, Jing Wei, Zhaohong Zheng, Dechuang Zhang, Jianguo Lin. Effects of Laser Process Parameters on Residual Stress of Pure Titanium Samples Prepared by Laser Melting Deposition[J]. Chinese Journal of Lasers, 2019, 46(3): 0302014.