圆柱面任意方向裂纹的双线阵激光热像检测
0 引 言
在生产过程中,由于加工工艺问题,材料表面易产生裂纹。裂纹将会影响材料的强度、特性以及寿命,造成安全隐患[1]。激光热成像具有直观、高效、无污染、无耦合等优点,能检测微米级裂纹[2-3],被广泛应用于化工、航天、核工业等行业。
激光热成像通过激光扫描激励样品表面,并用热像仪、计算机进行图像处理,根据热阻效应检出裂纹[3]。不同激光功率分布对任意方向裂纹检测具有不同效果。王晓宁[4]等人用点激光检测铁氧体表面裂纹时,她发现点光斑中心能量集中,平行激光扫描方向的裂纹信噪比低;J.Schlichting[5]等人用“飞点”激光检测金属样品表面裂纹,通过空间一阶导数成像裂纹,但检测对象都为垂直激光扫描方向裂纹;Li Teng[6]等人用线激光检测钛试件表面开口裂纹,相比点激光,裂纹成像信噪比显著提高,但激光线长方向热流均匀,平行线激光扫描方向裂纹无法检出;姚行洲[7-8]等人用线激光检测圆柱铁氧体裂纹,相邻热信号法检测出轴向裂纹,但周向裂纹无法检出;西安交通大学Pei C[9-11]等人用9×9棋盘式点阵列激光检测金属表面裂纹,他们发现裂纹在点光斑中心、光斑间隙成像不连续。以上激光功率分布在任意方向裂纹检测上均存在不足。
针对任意方向裂纹检测不足,王晓宁[5]等人深入研究了提高点激光热成像信噪比的多项关键技术,她提出的对称点温差算法有效解决了平行点激光运动方向裂纹信噪比低的问题;S.Hermosilla[12]等人采用“飞点”相机,通过主成分析法提高了“飞点”激光在恶劣工况的检测能力;姚行洲[9]等人研究了线激光系统各参数对成像信噪比的影响,并采用BPNN成像算法进一步提高了线激光裂纹成像信噪比;许颖[13]等人针对水平与垂直裂纹分别采用了线激光垂直扫描与线激光水平扫描;王晓娜[14]等人采用线激光正交扫描,解决了线激光无法检出平行扫描方向裂纹的问题;西安交通大学Pei C[9-11]等人通过改进激光传输组件、聚光组件以及光斑排布,有效改善了激光的激励效果,提高了成像信噪比。通过光斑设计的改进,他们发现密集激光可以增强裂纹成像。同时,小波变换、神经网络等算法的应用,进一步提高了裂纹成像信噪比。
文中采用双线阵激光功率分布设计,构筑任意方向热流,实现任意方向裂纹检测。文中通过数值仿真,验证了双线阵激光检测任意方向裂纹的可行性,并研究了双线阵激光激励参数、运动参数的优化,从而获得高信噪比裂纹成像图。另外,文中据此设计,提出了一套基于双线阵激光的任意方向裂纹成像算法。最终,文中将该检测方法用于真实铁氧体裂纹检测,成像结果清晰、直观地显示出任意方向裂纹。
1 双线阵激光检测系统和检测方法
1.1 检测系统基本结构
双线阵激光检测圆柱铁氧体柱面裂纹的系统结构如图1(a)所示,该系统主要有热像仪、线阵激光、柱体转动机构、计算机四部分构成。热像仪垂直位于圆柱铁氧体上方,两束线阵激光位于热像仪视场两侧。检测时,样品旋转,激光持续激励样品表面,热像仪记录两束光斑之间的温度数据。计算机通过相应信号提取算法,实现圆柱铁氧体表面裂纹检出。
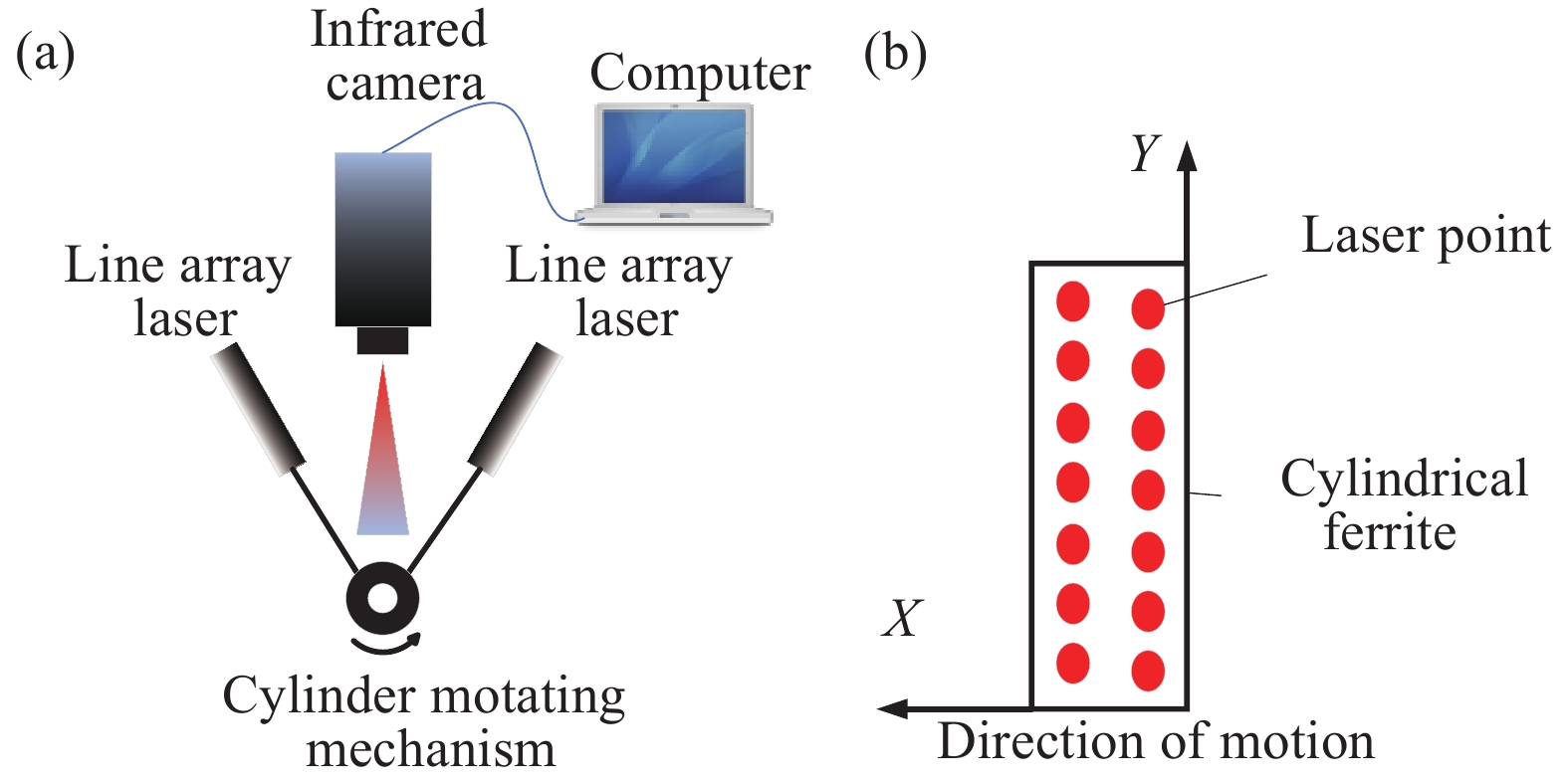
图 1. (a)系统结构图;(b)双线阵激光示意图
Fig. 1. (a) System structure; (b) Dual linear array laser schematic diagram
1.2 任意方向裂纹检测原理
试样表面存在裂纹时,裂纹会阻碍不平行裂纹方向热流,导致样品表面温度梯度发生变化。线阵激光能打断激光线长方向热流的均匀性,因此,具备任意方向裂纹的检测能力。当有裂纹经过线阵激光时,裂纹会阻挡激光点热流。由此,热量在裂纹两端积聚,导致裂纹处或裂纹附近产生较大温度梯度。但线阵激光存在光斑中心掩盖裂纹特征和光斑间隙激励不足的问题,导致裂纹漏检或成像不连续。为解决以上不足,文中采用两束错位排布的线阵激光,如图1(b)所示。该设计目的在于两束激光检测得到互补的裂纹片段,尽可能弥补线阵激光所带来的裂纹漏检或成像不连续。同时,两束激光间可以产生不同方向热流,使得任意方向裂纹检测效果不同。
1.3 双线阵激光检测仿真验证
1.3.1 仿真模型
为简化模型、减少计算量,文中建立了长6.3 mm,宽6 mm,厚7 mm的均值平板数值仿真模型,相关材料参数如表1所示。仿真样品裂纹深2 mm,宽1 μm,存在0°、45°、90°不同方向裂纹,如图2(a)所示。
表 1.
Material parameter
材料参数
Table 1.
Material parameter
材料参数
|
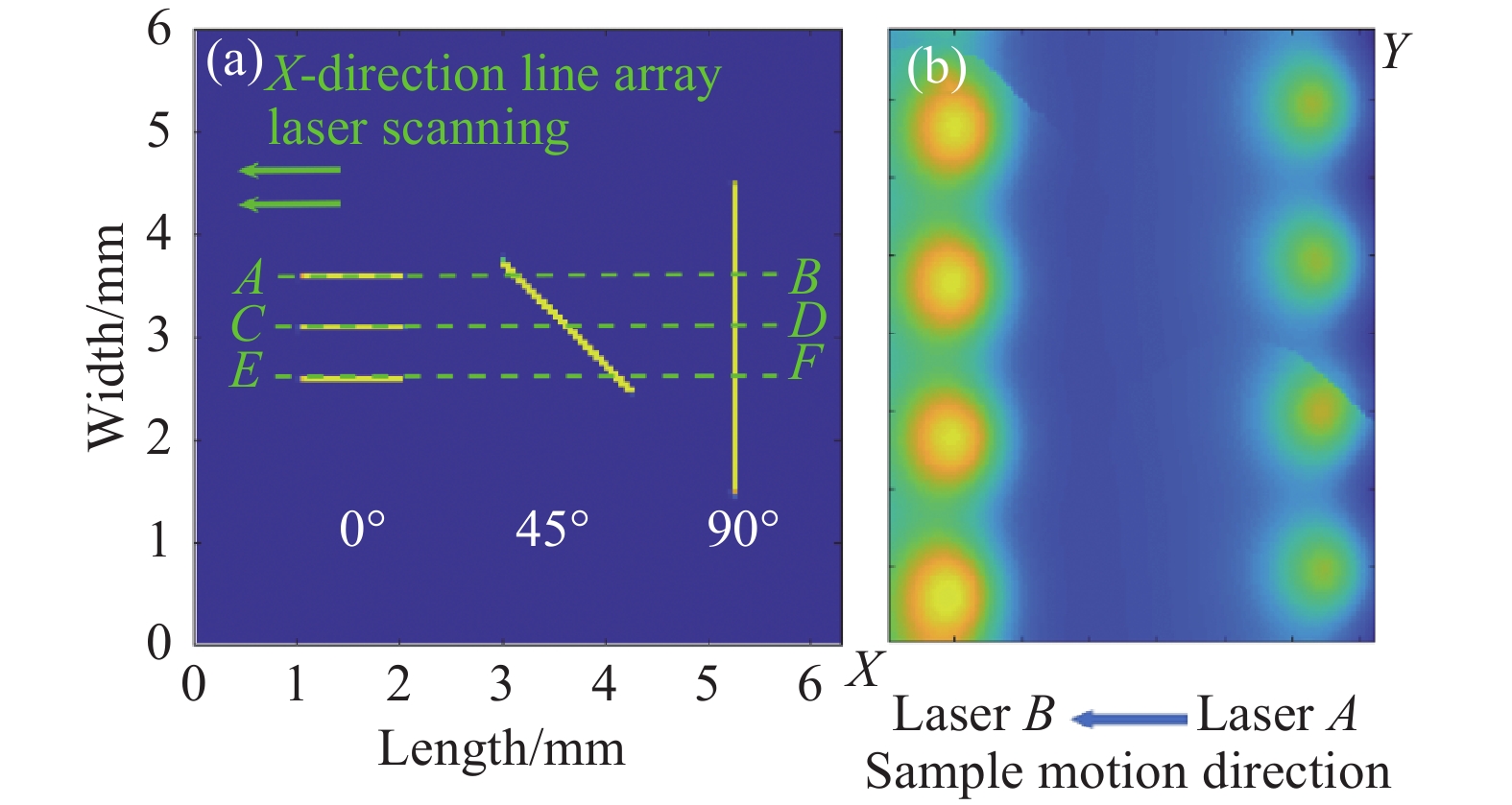
图 2. (a)仿真模型, (b)表面温度分布
Fig. 2. (a) Simulation model, (b) Surface temperature distribution
均质各向同性材料的非稳态三维热传导方程描述为:
ρ、c、λ、τ分别为微元体的密度、比热容、导热系数和时间。其温度边界条件表示为:
L为样品几何尺寸;q为激光功率密度(高斯分布);t0为激励时间。
图2(b)为激光激励下的样品表面温度分布图,图2(a)中的AB、CD、EF3行分别位于图2(b)激光A光斑间隙、光斑中心与间隙中点、光斑中心。激光静止,样品自右向左运动,空间分辨率50 μm。相邻激光点的圆心距为2 mm,半径为0.7 mm,各点功率为1 W,功率分布呈高斯分布。两束激光间距4.5 mm,光斑中心相互错开0.4 mm,激光与样品的相对速度为3 mm/s。在温度图中,完整裂纹不能直接观察到。
1.3.2 裂纹梯度成像
图3(a)、(b)为与水平方向呈0°、45°、90°的三条裂纹经过X方向单束线阵激光(激光A)一维扫描后,X、Y梯度成像结果。图中,X梯度检测到45°、90°裂纹,而Y梯度检测到0°、45°裂纹。Y梯度图中位于光斑间隙、光斑中心的0°裂纹发生了漏检。图4(a)为单束线阵激光激励,直线AB (光斑间隙)、CD (光斑中心与间隙中点)、EF (光斑中心)上各点的X、Y温度梯度曲线。从图中可以看到,0°裂纹光斑中心(AB-Y)以及光斑间隙(EF-Y)的Y梯度明显小于光斑中心与间隙中点(CD-Y)的Y梯度。这是因为光斑中心掩盖裂纹特征、光斑间隙激励不足导致的裂纹梯度下降。
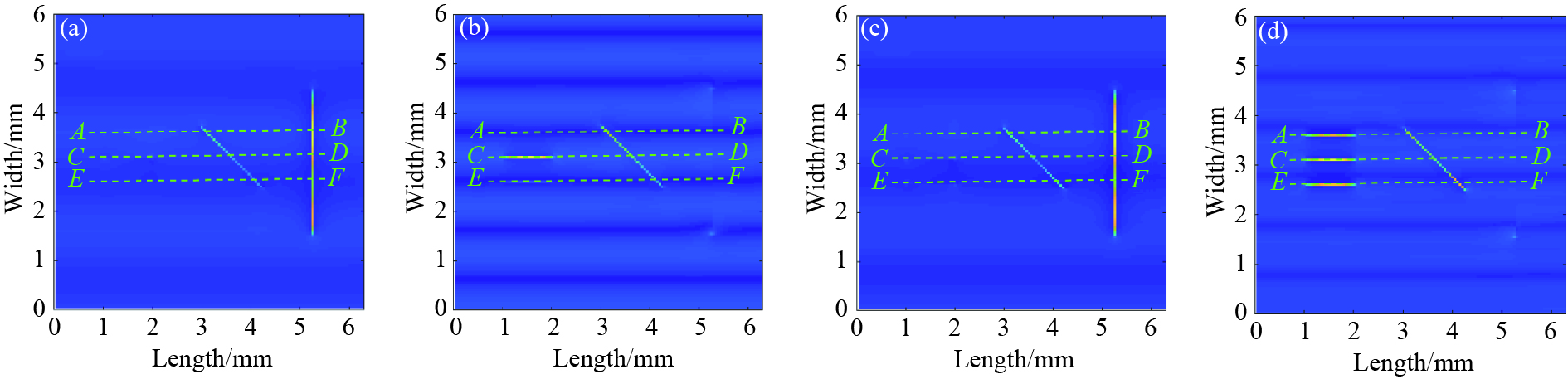
图 3. (a)线阵激光X 梯度成像图;(b)线阵激光Y 梯度成像图;(c)双线阵激光X 梯度成像图, (d)双线阵激光Y 梯度成像图
Fig. 3. (a) Line array laser X gradient; (b) Line array laser Y gradient; (c) Dual linear array laser X gradient; (d) Dual linear array laser Y gradient
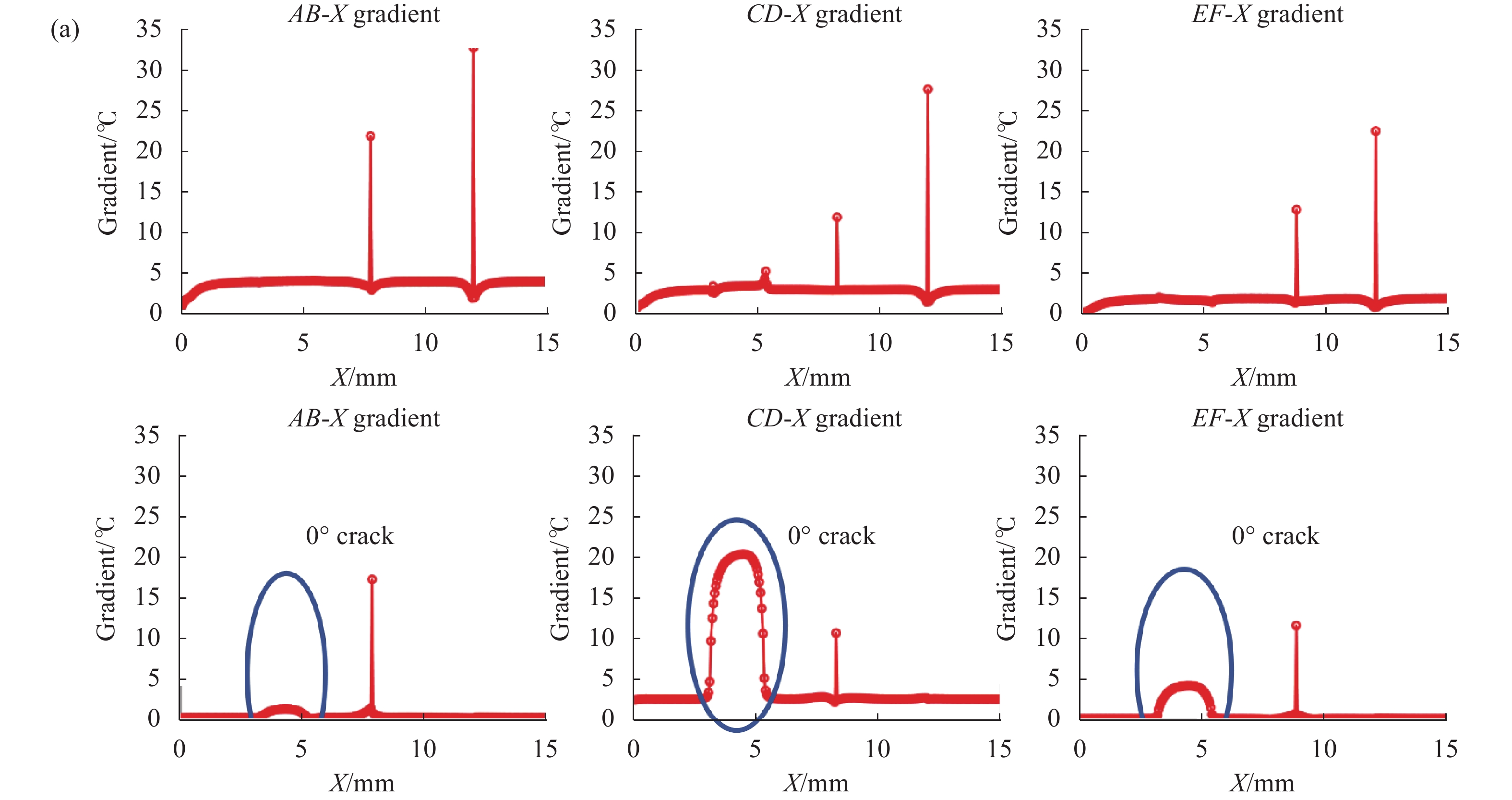
图 4. (a)线阵激光直线AB 、CD 、EF 温度梯度;(b)双线阵激光直线AB 、CD 、EF 温度梯度
Fig. 4. (a) Line array laser AB , CD , EF temperature gradient; (b) Dual linear array laser AB , CD , EF temperature gradient
双线阵激光检测效果如图3(c)、(d)所示,三种裂纹能在X、Y梯度图中分别成像,并且0°裂纹在光斑中心(AB-Y)、光斑间隙(EF-Y)的梯度都得到了有效提高,如图4(b)所示。
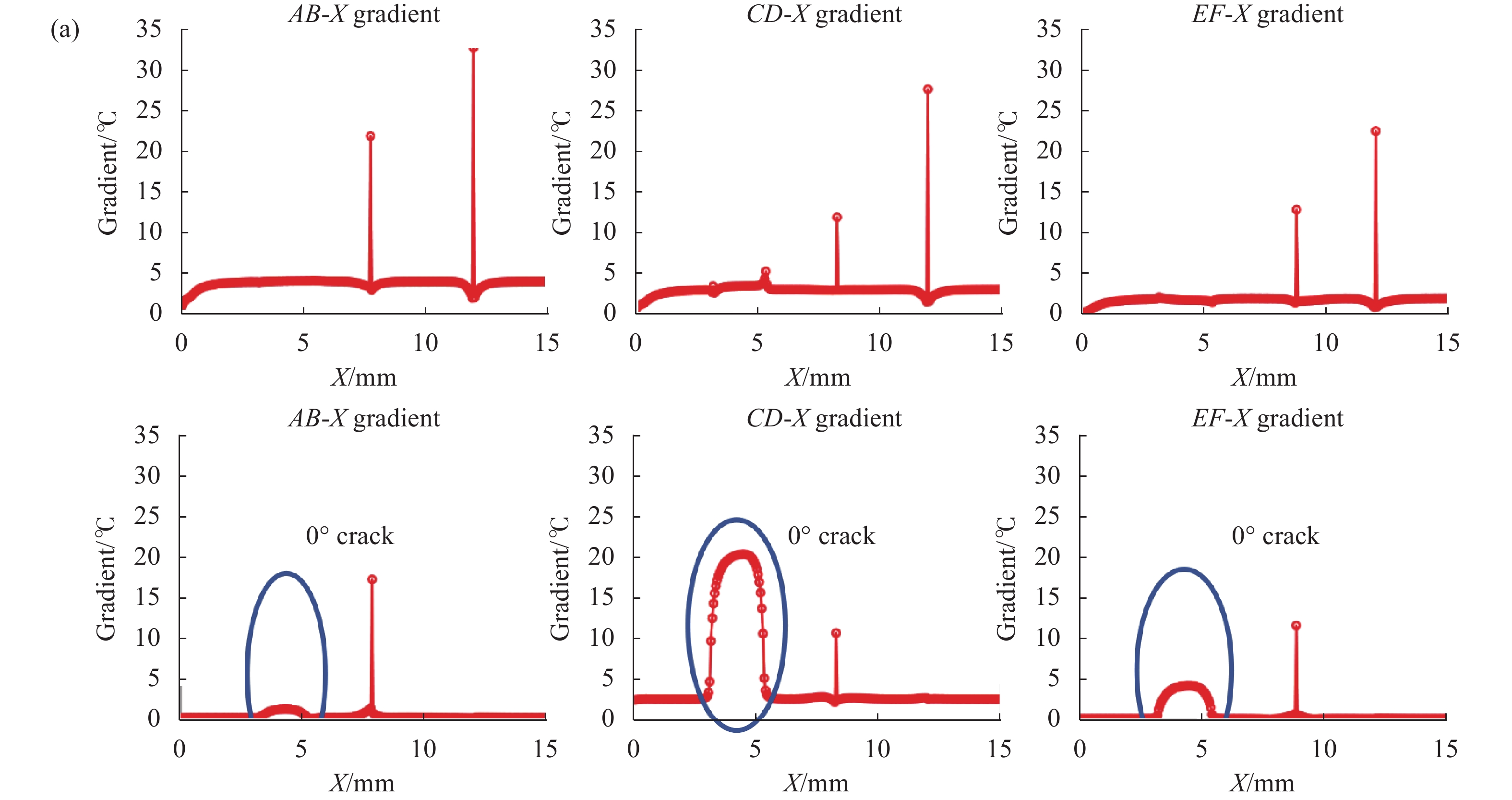
图 4. (a)线阵激光直线AB 、CD 、EF 温度梯度;(b)双线阵激光直线AB 、CD 、EF 温度梯度
Fig. 4. (a) Line array laser AB , CD , EF temperature gradient; (b) Dual linear array laser AB , CD , EF temperature gradient
2 系统参数优化设计
双线阵激光所产生的热流环境复杂,系统参数对裂纹检测带来不确定性影响。此节研究了系统各参数对裂纹检测的影响,通过仿真结果确定优化系统的相应参数,从而提升了裂纹成像信噪比。
信噪比采用主动热成像领域R. Hidalgo-Gato[15]等人提出的评价方式,缺陷区域与非缺陷区域的平均幅值之差
2.1 激光激励条件优化
2.1.1 点光斑半径
当点光斑功率一定时,点光斑的半径越小,能量越集中,裂纹热阻效应越明显,裂纹更易检出[11]。对于线阵激光,光斑越密集,裂纹成像也就越清晰完整。由于线阵激光为非均匀激光,梯度图存在如图5(a)、(b)所示的条纹状干扰。过小的光斑半径导致光斑中心能量集中,背景非均匀性增强,裂纹对比度降低,且样品有烧蚀风险。综上,过大过小的点光斑都会造成不利影响。图5(c)、(d)为0.4~0.9 mm半径点光斑与背景梯度的幅值关系,光斑半径越小,梯度起伏越大,背景非均匀性越强。裂纹梯度一般在5 ℃以上,为保证裂纹良好的对比度,背景最大梯度不能超过5 ℃。由此,激光半径折衷设计在0.6~0.7 mm。
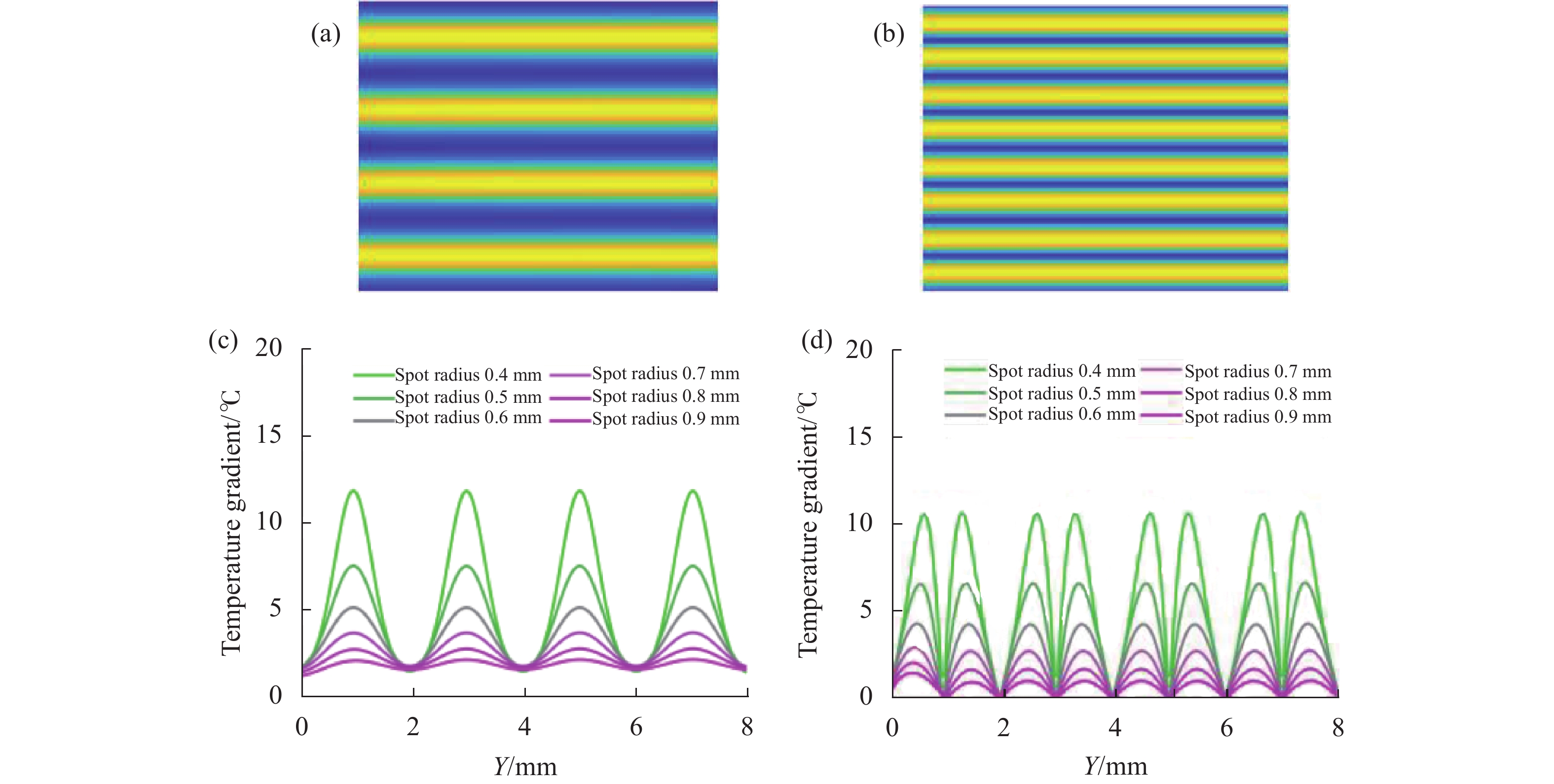
图 5. (a) X 梯度背景非均匀性;(b) Y 梯度背景非均匀性;(c)点光斑半径与X 梯度幅值关系;(d)点光斑半径与Y 梯度幅值关系
Fig. 5. (a) X gradient background heterogeneity; (b) Y gradient background heterogeneity; (c) Relationship between spot radius and X gradient amplitude; (d) Relationship between spot radius and Y gradient amplitude
2.1.2 相邻激光点中心距
相邻激光点中心距影响成像裂纹梯度幅值,过小的间距热流相互干扰,检测效果接近线激光,平行扫描方向裂纹漏检。而过大的点光斑中心距使得两个点光斑连线的中间区域激励不足,容易导致裂纹漏检或成像不连续。2.1.1节设计中,激光引起的最大梯度变化在5 ℃左右,因而,梯度幅值大于10 ℃的裂纹较易检出。图6(a)为半径0.7 mm相邻点光斑中心距与裂纹平均梯度值关系。90°裂纹梯度幅值在维持在10 ℃以上,受激光点中心距影响较小,而0°裂纹受激光点中心距影响较大。当点光斑中心距在1.5 mm以内,光斑之间热流相互干扰,0°裂纹梯度幅值较低,裂纹易漏检;当激光点距离在2 ~ 3 mm以上,裂纹梯度幅值较高,相邻光斑热流干扰较少;当激光间距超过3 mm,此时只有一个光斑的热流有效,0°、90°裂纹梯度都不再明显变化,但点光斑连线的中间区域开始出现激励不足。为保证良好的裂纹成像质量且任意方向裂纹不被漏检,0.7 mm半径点激光中心距可设计在2~3 mm。

图 6. (a)光斑中心距与裂纹梯度值关系; (b)错位间距与裂纹梯度值关系;(c)激光间距与裂纹信噪比关系; (d)扫描速度与裂纹信噪比关系
Fig. 6. (a) Relationship between center distance and crack gradient; (b) Relationship between dislocation distance and crack gradient; (c) Relationship between laser spacing and crack SNR; (d) Relationship between scanning speed and crack SNR
2.1.3 双线阵激光错位间距
双线阵激光错位使得两束激光拥有不同的检测效果,裂纹梯度幅值发生变化。若错位太少,两束激光不能得到互补的成像效果,裂纹成像漏检或不连续;若完全错开,不能避免光斑中心能量集中引起的裂纹漏检或不连续。图6(b)为双线阵激光错位间距与裂纹梯度幅值关系。90°裂纹梯度维持在26 ℃左右,裂纹梯度幅值受激光错位间距影响小,在任意激光错位间距下都能良好成像。而0°裂纹在激光错位间距0.3~0.7 mm时,裂纹梯度幅值相对较高,因此,错位间距设计在0.3~0.7 mm。
2.1.4 双线阵激光间距
双线阵激光间距过近,易相互干扰,产生斜向热流,影响裂纹成像信噪比,因此需要保证足够的间距,但同时激光又不能超出热像仪视场。图6(c)为双线阵激光间距与裂纹成像信噪比关系,当激光间距大于2 mm,信噪比不再发生变化,两束激光不会产生相互影响。因此,热像仪在选型时,视场宽度至少大于4 mm (保证两束激光完全进入视场)。
2.2 运动参数优化
激光扫描速度设置与温升需求、热像仪采样帧频、样品导热系数等有关。一方面,热像仪采样帧频有限,运动速度过高,不易捕捉裂纹温升变化,并带来运动模糊,裂纹检测灵敏度下降。另一方面,激光运动速度过慢,激光易烧蚀样品表面;运动速度过快,激光激励不充分。
图6(d)为双线阵激光扫描速度与X、Y梯度裂纹成像信噪比关系,扫描速度越快,成像信噪比越低。非制冷型热像仪帧频在窗口模式下可以达到200 Hz,同时为获得良好成像信噪比,双线阵激光运动速度设置3~6 mm/s为宜。当扫描速度在3 mm/s时,激光引起样品温升80 ℃左右,对于铁氧体、金属样品也不易发生烧蚀。
3 任意方向裂纹成像算法
双线阵激光检测系统仅记录两束激光间温度数据,如图2(b)所示,由于两束激光的检测效果不同,数据采用两束激光各自附近的X、Y梯度。整个检测平面的梯度图通过两束激光间某个特定位置所有时刻的梯度数据拼接而成,而不同方向梯度的最佳特征提取位置不同。最终检测结果由激光A附近X、Y梯度图以及激光B附近X、Y梯度图融合而成。由于X、Y梯度幅值、两束激光引起的梯度幅值变化均存在差异,不能直接进行图像融合。针对以上问题,文中研究了样品在激光间不同相对位置X、Y梯度变化以及图像融合算法。
3.1 梯度与激光相对位置
图7为样品运动在两束激光间不同相对位置时的梯度大小关系,尽可能选择能准确区分裂纹与背景的相对位置。文中选择样品运动至距离激光1光斑中心0.6、3.8 mm各时刻的X梯度数据作为检测数据,距离激光1光斑中心1、4 mm各时刻的Y梯度数据作为检测数据。通过图像拼接、时间同步和背景差分成像,成像出4幅具有不同裂纹片段的裂纹图,如图8(a)~(d)所示。
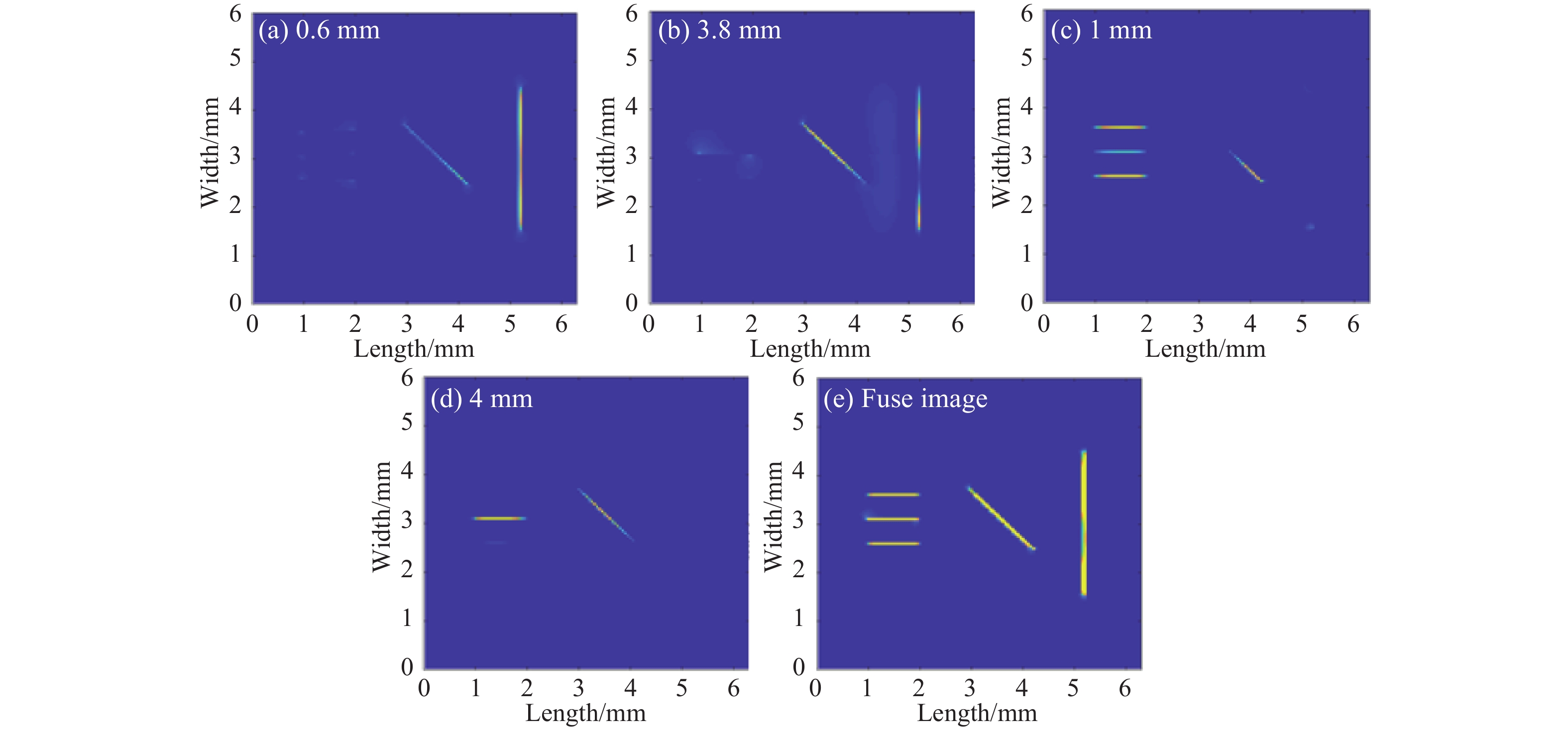
图 8. (a) 0.6 mm X 梯度图; (b) 3.8 mm X 梯度图; (c) 1 mm Y 梯度图;(d) 4 mm Y 梯度图; (e)融合图
Fig. 8. (a) 0.6 mm X gradient image; (b) 3.8 mm X gradient image; (c) 1 mm Y gradient image; (d) 4 mm Y gradient image; (e) fuse image
3.2 图像融合
对于一条任意方向裂纹,它在不同梯度提取时刻、不同梯度图中都只能成像部分裂纹,不利于裂纹识别,成像结果需要图像融合。图像叠加是常用的图像融合手段,但4幅梯度图幅值差异较大,直接叠加易导致裂纹缺失,背景噪声加重。因此,文中在图像叠加前,采用最大最小归一化。0°、45°、90°裂纹的融合成像效果如图8(e)所示。
4 实验及结果分析
4.1 实验装置
实验装置如图9(a)所示。检测时,样品在热像仪视场中心旋转,激光激励样品表面,热像仪记录其温度数据。该系统主要由自动化检测设备、线阵激光和热像仪三部分组成。自动化设备主要用于送样和样品旋转检测,样品转速为3 mm/s,逆时针旋转。线阵激光波长为915 nm,每束线阵激光具有14个点光斑,激光功率分布热图如图9(b)所示。各光斑点直径为1.4 mm,圆心距为2 mm,两束激光间距为4 mm,各点光斑功率为1 W,功率分布为高斯分布。热像仪为FLIR A655SC,实验帧频为200 Hz,测温灵敏度为30 mk,分辨率为120×640,空间分辨率为50 μm。

图 9. (a)实验装置;(b)激光功率分布热图
Fig. 9. (a) Experimental device; (b) laser power distribution heat map
4.2 实验样品
圆柱铁氧体样品直径为18.98 mm,高为30.30 mm。为方便识别裂纹,文中在裂纹附近用黑色马克笔做了标记。图10展示了40X光学显微镜多角度拍照拼接得到的裂纹区域,裂纹均为自然裂纹,宽度范围在10~60 μm。其中,样品1、2具有接近0°、90°裂纹,而样品3、4具有不同倾斜程度的裂纹。
4.3 实验裂纹成像效果
实验方法与仿真一致,图10为4个实验样品的热成像结果和显微镜成像结果,水平、垂直、倾斜的自然裂纹都能检出,但部分裂纹片段成像不连续。整体成像背景噪声少,但部分区域存在条纹、随机噪声,部分马克笔标记也会在裂纹附近显现,一定程度影响了裂纹识别。
这是因为圆柱铁氧体表面较为粗糙,使得样品表面发射率有较大范围的变化,从而影响了成像。另一方面,热像仪景深、柱体轴向移动、激光功率分布、柱体径向跳动等带来了一系列系统噪声。由此,该系统成像虽能检测任意方向裂纹,但整体抗噪声能力较弱,下一步将围绕如何提高裂纹成像质量展开工作。
5 结 论
文中针对任意方向裂纹检测,设计了一套双线阵激光裂纹检测系统,研究了激光激励参数、运动参数对裂纹检测的影响,并开发了任意方向裂纹检测的成像算法,得出以下结论:
(1)错位双线阵激光能检测任意方向裂纹,合理的激励条件、运动参数能有效提高裂纹成像信噪比以及成像完整度。对于线阵激光,点光斑半径应折衷设计在0.6~0.7 mm,相应光斑中心距在1.0~2.0倍光斑直径。此双线阵激光在排布时,间距应大于2 mm,光斑相互错开0.3~0.7 mm,扫描速度3~6 mm/s。
(2)该成像算法只利用了多个不同激光相对位置所有时刻的梯度特征,并没有完全利用裂纹运动在两束激光不同相对位置的温度梯度特征。因此裂纹整体抗噪声能力差,成像表面粗糙的样品检测效果不佳。下一步拟利用裂纹运动在两束激光间的全部梯度特征区分裂纹与噪声,提高裂纹成像完整度以及信噪比。
[2] 王昵辰. 金属表面开口裂纹的激光扫描和显微热成像检测研究[C]远东无损检测新技术论坛, 2018: 450455.Wang Nichen. Research on detection of metal surface opening cracks based on laser scanning thermography microthermography[C]FAR EAST NDT, 2018: 450455.(in Chnise)
[3] 王博正, Wang Bozheng, Kang Jiajie, 康嘉杰, 董丽虹, Dong Lihong. Research progress on laser infrared thermography detecting material surface crack[J]. Laser & Infrared, 2019, 49(10): 1165-1171.
[4] 王晓宁. 激光热成像检测中信噪比改善若干关键技术[D]. 杭州: 中国计量大学, 2016.Wang Xiaoning. Key technologies in improving the SNR of the laser thermography detection[D]. Hangzhou: China Jiliang University, 2016.
[5] Schlichting J, Maierhofer C, Kreutzbruck M. Crack sizing by laser excited thermography[J]. NDT & E International, 2012, 45(1): 133-140.
[6] Li T, Almond D P, Rees D A S. Crack imaging by scanning laser-line thermography and laser-spot thermography[J]. Measurement Science & Technology, 2011, 22(3): 315-322.
[8] 姚行洲. 基于激光热成像的圆柱铁氧体表面裂纹检测[D]. 杭州: 中国计量大学, 2018.Yao Xingzhou. Superficial crack detection of cylinder ferrite based on laser thermography[D]. Hangzhou: China Jiliang University, 2018.
[9] Pei C, Qiu J, Liu H. Simulation of surface cracks measurement in first walls by laser spot array thermography[J]. Fusion Engineering & Design, 2016, 109: 1237-1241.
[10] Qiu J, Pei C, Liu H. Remote inspection of surface cracks in metallic structures with fiber-guided laser array spots thermography[J]. NDT & E International, 2017, 92: 213-220.
[11] Pei C, Qiu J, Liu H. Detection of surface cracks by laser spot thermography at elevated temperature[J]. International Journal of Applied Electromagnetics and Mechanics, 2018, 1: 1-7.
[13] 许颖, Xu Ying, Wang Qingyuan, 王青原, 罗聪聪, Luo Congcong. Chip crack imaging detection based on line laser lock-in thermography[J]. Laser & Optoelectronics Progress, 2020, 57(6): 1-14.
[15] Hidalgogato R, Andrés J R, Lópezhiguera J M. Quantification by signal to noise ratio of Active infrared thermography data processing techniques[J]. Optics & Photonics Journal, 2013, 03(4): 20-26.
Article Outline
朱鑫浩, 侯德鑫, 叶树亮. 圆柱面任意方向裂纹的双线阵激光热像检测[J]. 红外与激光工程, 2020, 49(9): 20200097. Xinhao Zhu, Dexin Hou, Shuliang Ye. Dual linear array laser thermography detection of arbitrary direction cracks on cylindrical surface[J]. Infrared and Laser Engineering, 2020, 49(9): 20200097.