3A21铝合金表面激光毛化坑点形貌演变规律
下载: 995次
1 引言
经毛化处理的金属薄板具有优良的表面涂镀性能和摩擦性能[1],在航空航天、生物医学、装备制造与维护、消费电子产业[2-5]等领域应用广泛。目前主要的毛化方式有喷丸毛化[6]、电火花毛化[7]和激光毛化[8]等。喷丸毛化主要存在噪声大、粉尘污染严重、功耗和设备成本较高等问题,并且加工时受材料硬度、喷丸尺寸和冲击速率等因素的影响,毛化坑点具有随机性。电火花毛化的形貌均匀性和重复性比喷丸毛化好,但也存在着耗电量大、维修成本高和污染严重的问题[9]。为探索一种低能耗、清洁无污染的毛化方案,激光毛化技术引起了人们的关注[10-12]。激光毛化技术是采用高能量密度、窄脉冲宽度的脉冲激光辐照材料表面,使材料出现熔化甚至气化等离子体现象[13],在材料表面形成烧蚀坑点,从而改变材料表面形貌及性能的激光加工技术。激光毛化过程不会对环境造成污染,并且由于激光器的可控性好,可以精确控制工艺参数,保证了毛化坑点的一致性。
目前,激光毛化的研究主要集中在探索材料性能的改善和坑点形貌的演变规律这两方面。其中,坑点的典型形貌为球冠状[14]、M状[15]和火山口状[16]。Chilamakuri等[17]通过设计的算法得到火山口状坑点形貌的仿真结果。刘莹等[18]使用YAG脉冲激光毛化装备制备出带有表面微凸体的火山口坑点。Vilhena等[19]对比了不同激光模式下火山口毛化坑点的成形特征。符永宏等[20]研究了激光参数对坑点形貌的作用规律,分析了火山口状坑点的形成机理。Ukar等[21]使用连续激光毛化设备进行工艺实验,通过选取合适的工艺参数验证了连续激光器也可以应用于激光毛化的研究中。Hu等[22]对比了水下和空气中火山口凹坑的形貌区别,得出了水蒸气的反冲压力可以有效增大凹坑尺寸的结论。虞宙等[23]探讨了皮秒脉冲激光工艺参数对火山口微沟槽形貌的作用规律,探索了最优的工艺参数,并采用该工艺参数实现了钛合金微造型样件的制备。Nandakumar等[5]采用激光毛化的方式在发动机活塞表面构建了火山口状微沟槽,达到了降低发动机油耗的目的。综上可知,国内外对火山口状激光毛化坑点的相关报道,通常以倒三角状表征坑点的形貌特征,而忽视了激光光场分布以及相关工艺参数对坑点形貌转变的影响。
本文采用近平顶光场分布的窄脉冲激光束对3A21铝合金表面进行毛化处理,研究毛化坑点及微凸体的形成机理,通过调整工艺参数揭示了坑点形貌由倒梯形向倒三角形演变的规律。形貌工艺试验可为激光毛化改性方面的研究提供参考,并有助于激光毛化板的规模化应用。
2 激光毛化试验
2.1 试验装置
激光毛化试验装置由LD泵浦窄脉冲激光器、扩束准直系统、扫描系统、侧吹装置、控制系统以及三维运动平台构成,如
用于毛化工艺试验的激光源为MOPA(master oscillator power amplifier)结构的LD泵浦窄脉冲Nd∶YAG激光器,激光器输出的光场为近平顶分布,激光器性能参数如
表 1. LD泵浦Nd∶YAG脉冲激光器的主要性能参数
Table 1. Main performance parameters of Nd∶YAG pulsed laser pumped by LD
|
2.2 试验方案
为改善卫星热辐射器壳体表面的摩擦性能和涂层的附着力,以壳体用Al-Mn系3A21铝合金(主要成分如
表 2. 3A21型铝合金的主要成分
Table 2. Main components of 3A21 aluminum alloy
|
采用单因素分析法研究激光参数对毛化坑点形貌的影响规律,试验过程中脉冲激光器的工作频率固定为1 Hz,主要考虑以下4个参数:单脉冲能量(
2.3 形貌表征
激光毛化坑点呈现出火山口形状,如
表 3. 激光毛化工艺参数
Table 3. Parameters of laser texturing process
|
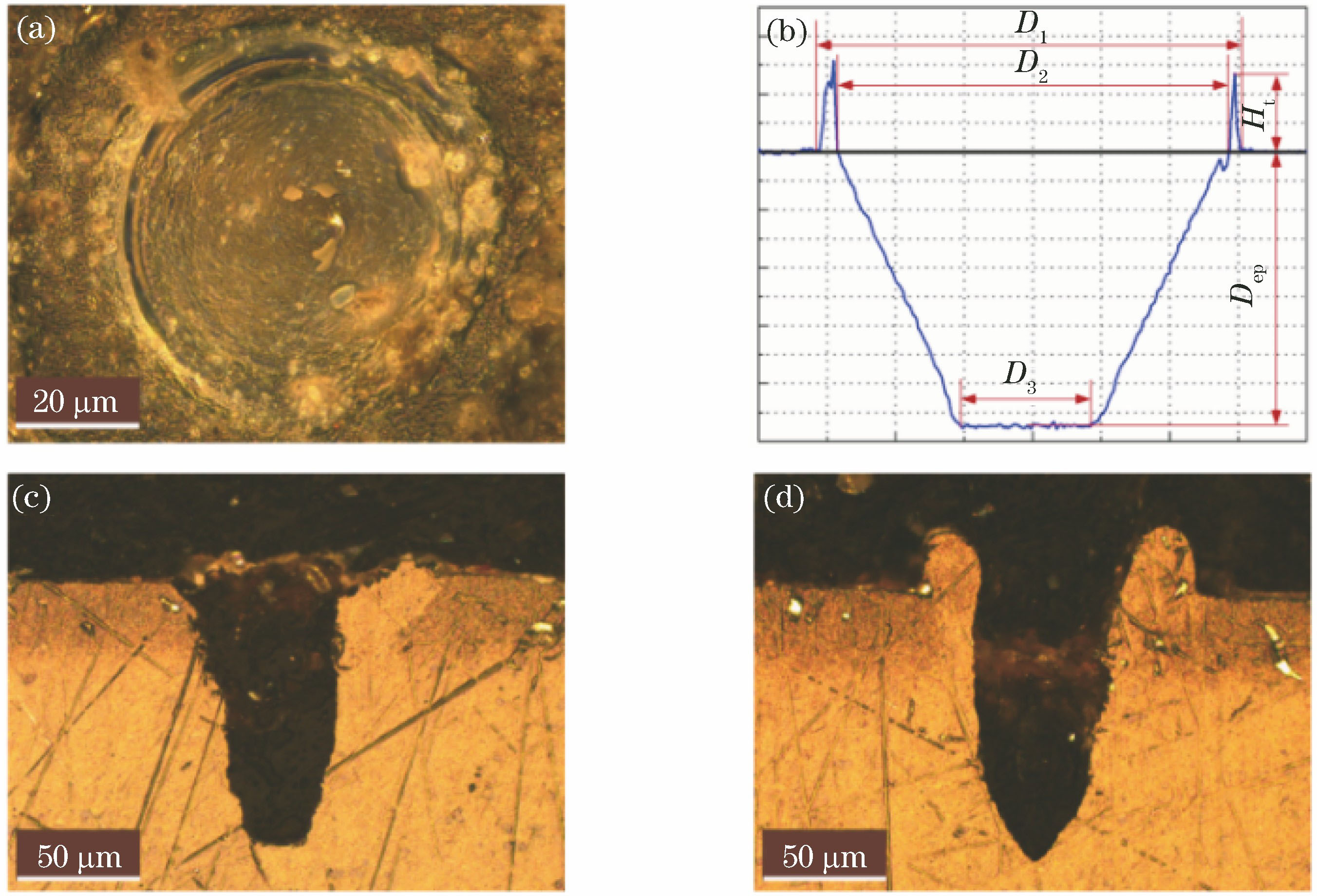
图 2. 毛化坑点的形貌。(a)二维金相图;(b)横截面示意图;(c)倒梯形截面金相图;(d)倒三角形截面金相图
Fig. 2. Morphologies of the texturing pits. (a) Two-dimensional metallographic diagram; (b) cross-section schematic; (c) inverted trapezoid metallographic diagram; (d) inverted triangle metallographic diagram
3 试验结果分析
3.1 单脉冲能量对特征参数的影响
在脉冲宽度为200 μs的条件下,单脉冲能量由100 mJ增大至250 mJ,间隔为25 mJ,坑点特征参数的变化曲线如
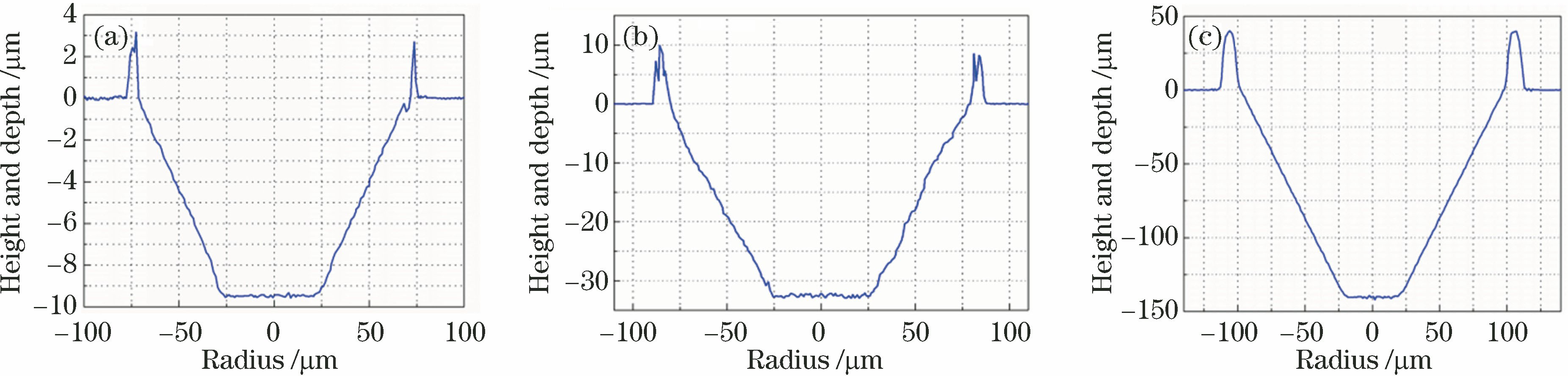
图 4. 不同脉冲能量下得到的典型坑点的形貌。(a) E =150 mJ;(b) E =200 mJ;(c) E =250 mJ
Fig. 4. Morphologies of typical pits obtained at different pulse energies. (a) E =150 mJ; (b) E =200 mJ; (c) E =250 mJ
3.2 脉冲宽度对特征参数的影响
在单脉冲能量为150 mJ的情况下,脉冲宽度由50 μs增大到250 μs,间隔为25 μs,坑点特征参数的变化曲线如

图 6. 不同脉冲宽度下得到的坑点的形貌。(a) τ =200 μs;(b) τ =100 μs;(c) τ =50 μs
Fig. 6. Morphologies of pits obtained at different pulse widths. (a) τ =200 μs; (b) τ =100 μs; (c) τ =50 μs
在研究凹坑形貌变化的过程中发现,当脉冲宽度为100 μs时,在材料表面开始出现围绕坑点的黑色熔渣。为探究黑色熔渣的形成原因及演变过程,本试验将脉冲宽度在50~100 μs范围内以10 μs为间隔继续细分,分别在50,60,80,90 μs的脉冲宽度下得到材料表面典型形貌变化,如
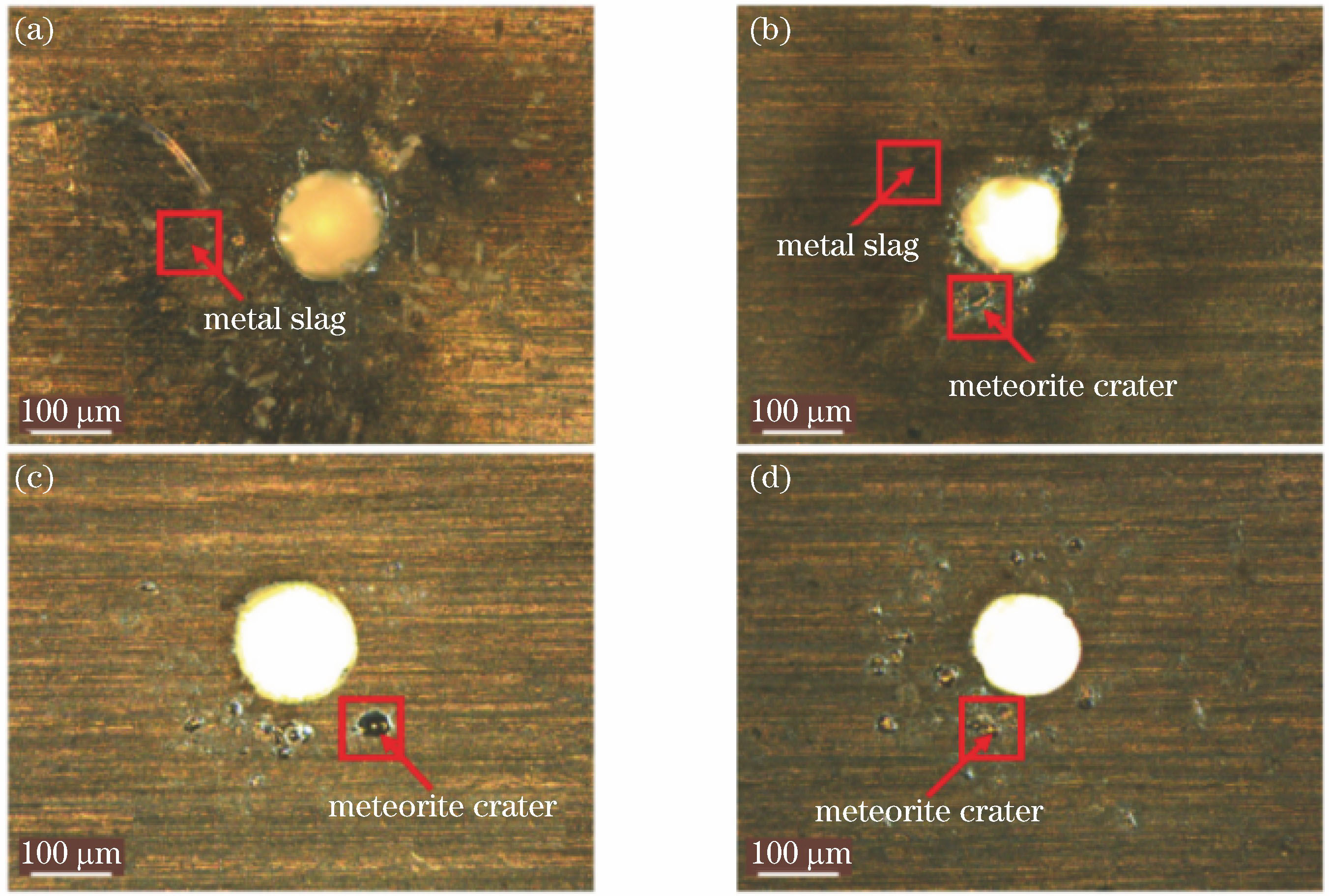
图 7. 不同脉冲宽度下得到的毛化坑点的表面形貌。(a) τ =90 μs;(b) τ =80 μs;(c) τ =60 μs;(d) τ =50 μs
Fig. 7. Laser texturing pits' surface morphology obtained at different pulse widths. (a) τ =90 μs; (b) τ =80 μs; (c) τ =60 μs; (d) τ =50 μs
当脉冲宽度小于100 μs时,激光毛化过程大部分依靠气化去除材料,在反冲压力和辅助气体压力的共同作用下,凹坑内的熔融金属被驱至材料表面。起初反冲压力较小,并且激光与材料作用的时间相对较长,热扩散时间也相对较长,扩散至材料表面的熔融金属冷却后形成了黑色的金属熔渣;随着脉冲宽度变窄,材料气化现象明显,致使反冲压力作用加剧,一部分熔融金属携带大量热量以迸溅的形式溅出熔池,然后回落至材料表面并释放热量,形成烧蚀陨石坑,这种情况下金属熔渣和陨石坑同时存在;随着脉冲宽度继续变窄,材料内部的热扩散速率增大,表面冷却随之加快,金属熔渣无法存留在材料表面,更多的熔融金属以冲击形式被驱至材料表面,材料表面呈现为完全的陨石坑形貌。在激光毛化过程中,辅助气体以45°吹射试件表面改变了熔融金属的流动,在辅助气体压力作用下,各脉冲宽度下得到的黑色熔渣及陨石坑均存在向吹气方向聚集的趋势。在实际应用中,毛化坑点周围呈陨石坑形貌的材料可以作为摩擦副,进一步改善材料的摩擦学性能。
3.3 脉冲数对特征参数的影响
在单脉冲能量为150 mJ、脉冲宽度为200 μs的情况下,采用不同的脉冲数(1、2、3、5、10、15、20)进行试验,得到了坑点特征参数随脉冲数的变化曲线,如
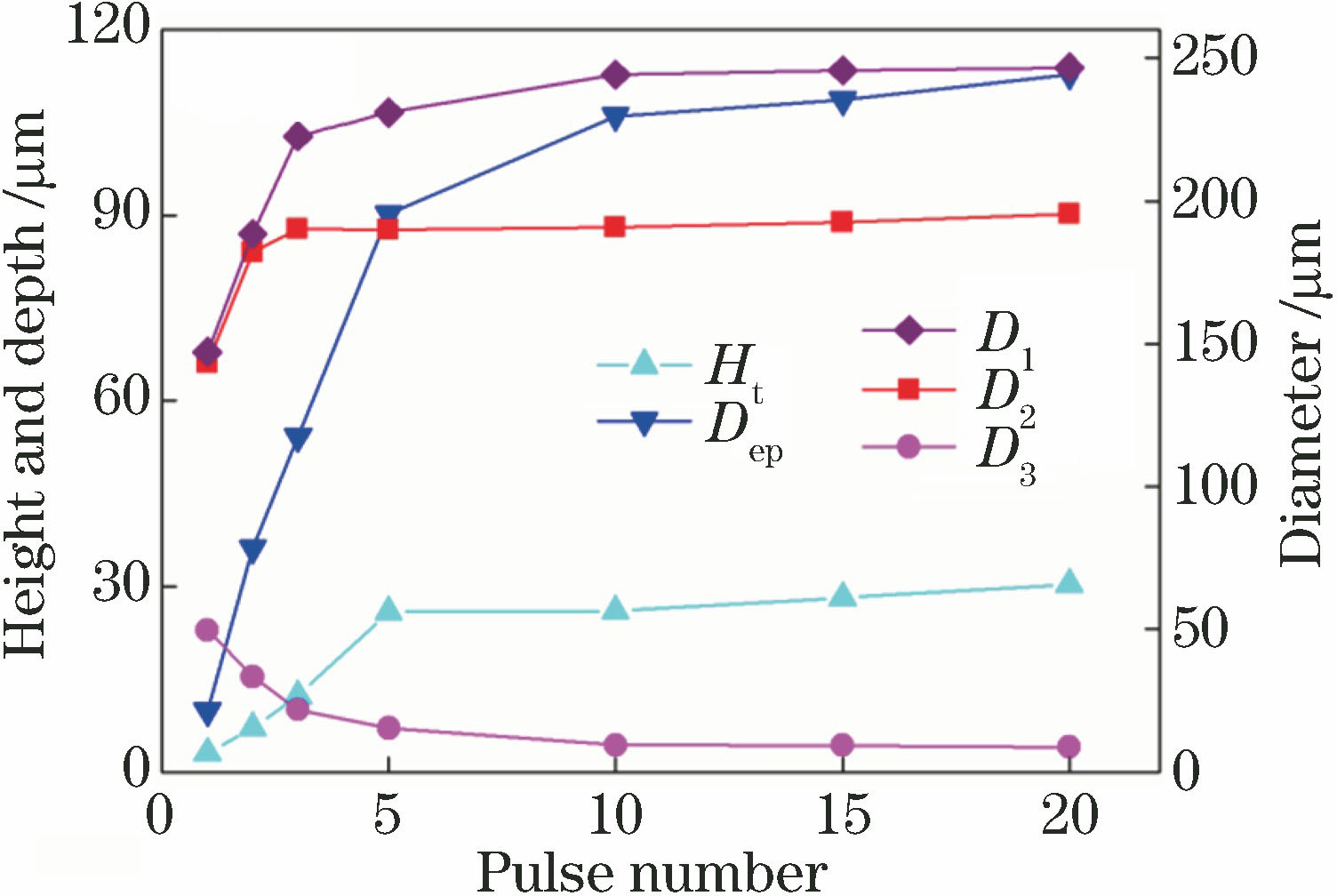
图 8. 坑点特征参数随脉冲个数变化的曲线
Fig. 8. Characteristic parameters of pits versus number of laser pulses
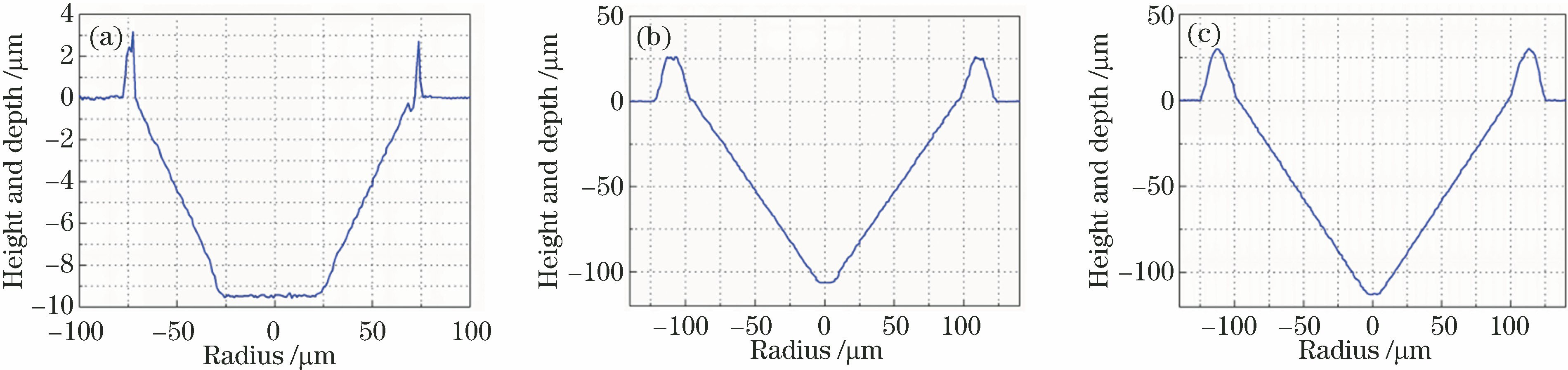
图 9. 不同脉冲数下得到的坑点形貌。(a) n =1;(b) n =10;(c) n =20
Fig. 9. Morphologies of pits obtained at different number of laser pulses. (a) n =1; (b) n =10; (c) n =20
3.4 离焦量对特征参数的影响
在单脉冲能量为150 mJ、脉冲宽度为200 μs的条件下,采用不同的离焦量(±2 mm、±1 mm、±0.5 mm和0 mm)进行试验,得到了坑点特征参数随离焦量变化的曲线,如
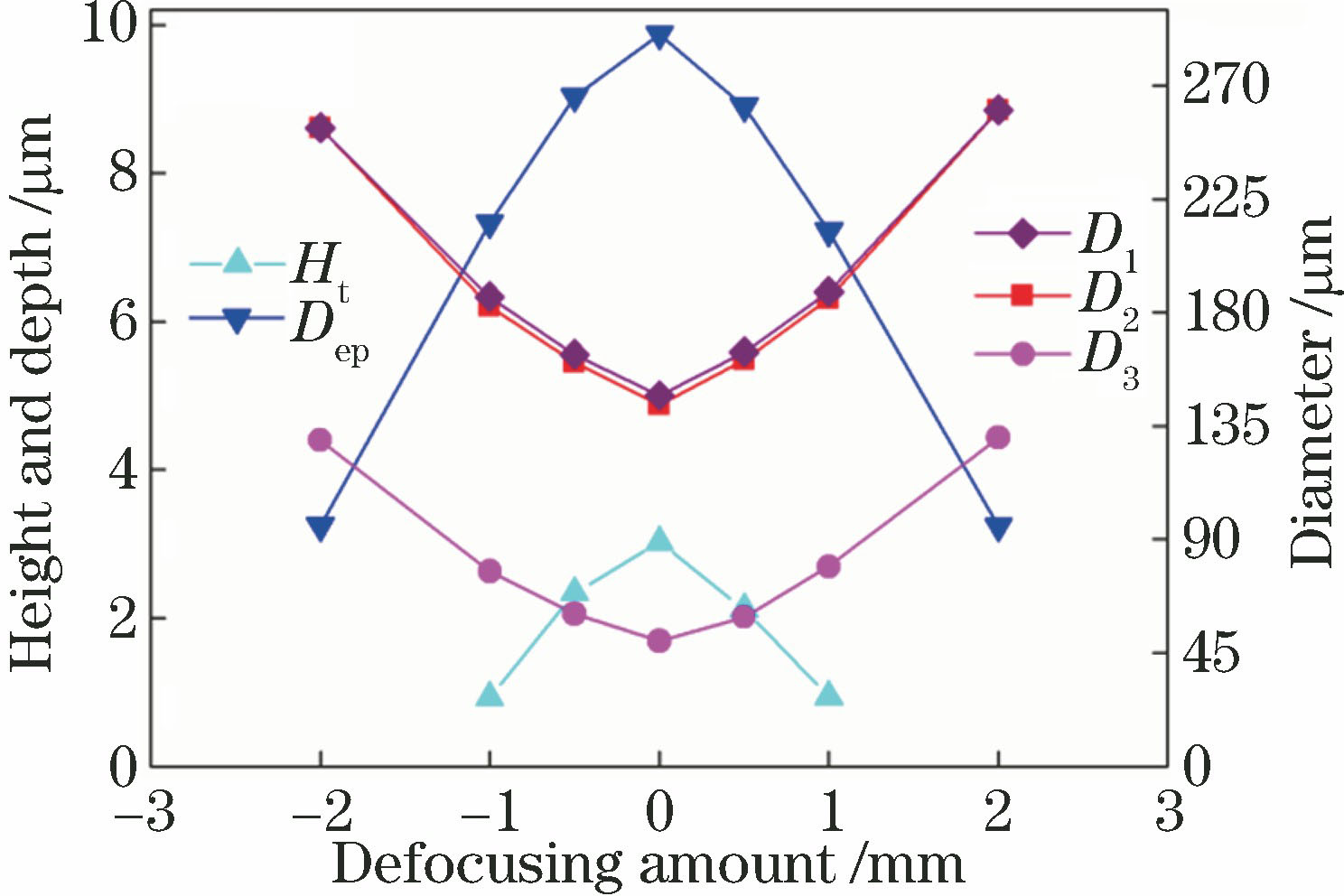
图 10. 坑点特征参数随离焦量变化的曲线图
Fig. 10. Characteristic parameters of pits versus defocusing amount
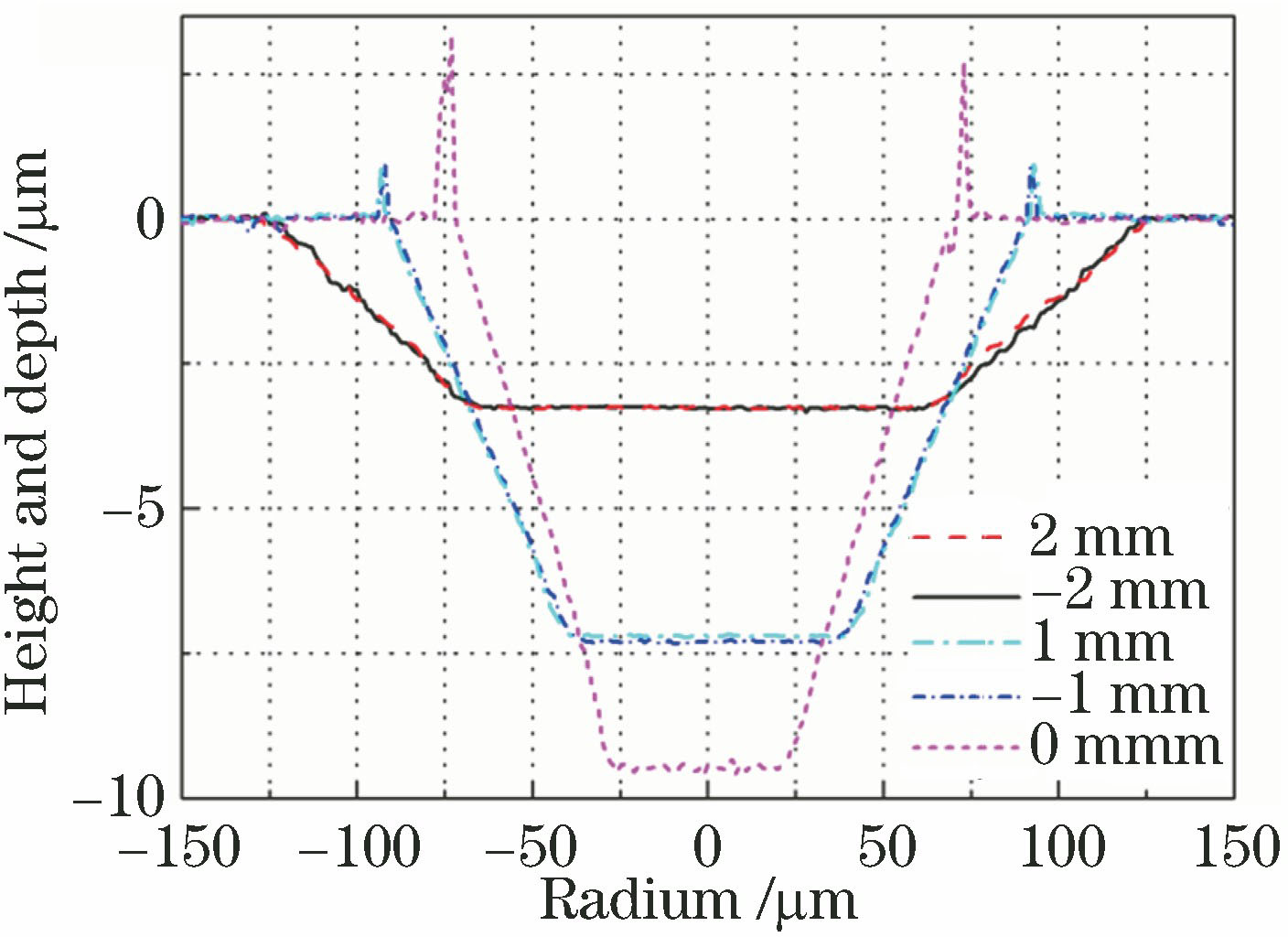
图 11. 不同离焦量Δ 下得到的典型坑点的形貌
Fig. 11. Morphologies of typical pits obtained at different defocusing amount Δ
4 结论
通过激光毛化试验探索了单脉冲能量、脉冲宽度、脉冲数以及离焦量对毛化坑点火山口形貌的影响,经过分析总结得出了以下结论。
1)在能量逐渐增大及脉冲宽度逐渐减小的过程中,熔融金属的堆积作用增大了表面微凸体的体积,激光对试件的烧蚀作用由熔凝去除向气化去除转变,坑点形貌由倒梯形向倒三角形转变;但随之出现的等离子体现象屏蔽了能量的进一步作用。因此,合理选取激光参数可以在避免等离子屏蔽作用的前提下,获取较深的坑点尺寸。
2)激光毛化过程大部分依靠气化去除材料,其试件表面出现了存在竞争关系的金属熔渣和陨石坑。在脉冲宽度相对较宽时,试件表面出现了黑色的金属熔渣;随着脉冲宽度减小,脉冲峰值功率增大,试件表面呈金属熔渣和陨石坑共存的形貌,最终转变为陨石坑形貌。
3)在离焦情况下可以获得较大的坑点尺寸以及去除体积,随着离焦量的数值增大,在试件表面几乎无法观察到明显的微凸体,坑点呈完全的倒梯形形貌。
通过试验建立了工艺参数与毛化形貌及尺寸的联系,说明可以通过控制激光光场及相关工艺参数精确控制毛化坑点的形貌。在此基础上还可以进一步研究激光毛化形貌对材料性能的改进,以构建材料性能与表面形貌特征之间的联系。
[1] Bathe R, Sai Krishna V, Nikumb S K, et al. Laser surface texturing of gray cast iron for improving tribological behavior[J]. Applied Physics A, 2014, 117(1): 117-123.
[2] Romoli L, Moroni F. Khan M M A. A study on the influence of surface laser texturing on the adhesive strength of bonded joints in aluminium alloys[J]. CIRP Annals, 2017, 66(1): 237-240.
[3] Razi S, Madanipour K, Mollabashi M. Laser surface texturing of 316L stainless steel in air and water: a method for increasing hydrophilicity via direct creation of microstructures[J]. Optics & Laser Technology, 2016, 80: 237-246.
[8] Zheng X H, Tan J, Zhang Q, et al. Effect of laser surface texturing depth on the adhesion of electroless plated nickel coating on alumina[J]. Surface and Coatings Technology, 2017, 311: 151-156.
[10] Bonse J, Kirner S V, Griepentrog M, et al. Femtosecond laser texturing of surfaces for tribological applications[J]. Materials, 2018, 11(5): 801.
[11] Guo J D, Li Y, Lu H L, et al. An effective method of edge deburring for laser surface texturing of Co-Cr-Mo alloy[J]. The International Journal of Advanced Manufacturing Technology, 2018, 94: 1491-1503.
[12] Kümmel J, Braun D, Gibmeier J, et al. Study on micro texturing of uncoated cemented carbide cutting tools for wear improvement and built-up edge stabilisation[J]. Journal of Materials Processing Technology, 2015, 215: 62-70.
[13] 蔡颂, 陈根余, 周聪, 等. 单脉冲激光烧蚀青铜砂轮等离子体物理模型研究[J]. 光学学报, 2017, 37(4): 0414001.
[14] Li X L, Yue W, Huang F, et al. Tribological behaviour of textured titanium under abrasive wear[J]. Surface Engineering, 2019, 35(4): 378-386.
[15] 叶云霞, 贾子扬, 符昊, 等. 脉冲激光作用下45#钢表面微凸起形貌演变规律的研究[J]. 激光与光电子学进展, 2016, 53(3): 031408.
[16] Pardal G, Meco S, Dunn A, et al. Laser spot welding of laser textured steel to aluminium[J]. Journal of Materials Processing Technology, 2017, 241: 24-35.
[17] Chilamakuri S, Bhushan B. Effect of peak radius on design of W-type donut shaped laser textured surfaces[J]. Wear, 1999, 230(2): 118-123.
[18] 刘莹, 陈大融, 杨文言. 轧辊表面微凸体形貌激光毛化技术的试验研究[J]. 机械工程学报, 2003, 39(7): 107-110.
[19] Vilhena L M. Sedla ek M, Podgornik B, et al. Surface texturing by pulsed Nd∶YAG laser[J]. Tribology International, 2009, 42(10): 1496-1504.
[20] 符永宏, 王浩, 杨烨刚, 等. 不锈钢光纤激光毛化及其摩擦性能[J]. 表面技术, 2015, 44(1): 96-101.
[22] Hu J, Xu H B. Friction and wear behavior analysis of the stainless steel surface fabricated by laser texturing underwater[J]. Tribology International, 2016, 102: 371-377.
[23] 虞宙, 张文杰, 胡俊. 皮秒激光对医用钛合金植入物表面微加工及生物相容性的研究[J]. 中国激光, 2017, 44(1): 0102014.
Article Outline
陈爔, 王菲, 吴琼, 底才翔, 田明, 崔庆新. 3A21铝合金表面激光毛化坑点形貌演变规律[J]. 激光与光电子学进展, 2019, 56(24): 241404. Xi Chen, Fei Wang, Qiong Wu, Caixiang Di, Ming Tian, Qingxin Cui. Pit Morphology Evolution Law of 3A21 Aluminum Alloy Surface in Laser Texturing[J]. Laser & Optoelectronics Progress, 2019, 56(24): 241404.