高功率固体激光器微通道冷却结构的数值研究
下载: 964次
1 引言
在激光器的发展历程中,热效应问题一直是制约激光器向超高功率和优质光束质量方向发展的一个主要障碍。对于高功率固体激光器而言,由于受到外部冷却影响,以及泵浦光光强沿传输方向呈指数衰减[1-3],增益介质内部各个方向上均存在较大的温度梯度,与之对应的热应力、热应变及增益介质折射率的改变最终导致激光输出功率和光束质量下降[4-5]。
在端面泵浦的高功率板条激光器中,板条被封装在两个金属冷却热沉之间,受到封装结构的限制,板条内部的温度分布无法测量,这给板条热应变及由此造成的波前畸变的准确计算带来很大的困难。国内外的科研工作者纷纷基于数值传热学,通过数值计算得到了不同热源和冷却条件下板条内部的温度分布。在众多文献中,一部分仅建立了板条和冷却结构的局部模型,无法完整研究整体流动结构对板条温度分布的影响[6-7],另一部分仅建立了板条的计算模型,在给定板条表面恒定温度或恒定对流换热系数的边界条件下[8-9],计算得出板条的热分布。然而,板条是一个非均匀分布的体热源,在冷却过程中受到冷却结构内部流体分布的影响时,其表面的温度和对流换热系数必然呈现为非均匀分布的结果,因此前述文献中的方法均无法得出准确的晶体内部温度分布结果。
本文建立了包含微通道热沉和增益介质的全尺寸计算模型,针对典型的板条内部非均匀热分布关系式,在给定冷却液入口温度和流量和的边界条件下,通过热-流-固耦合的数值计算方法得到板条表面和内部的温度分布,及热沉的整体压降,分析冷却结构对激光晶体热分布的影响,为下一步冷却结构的优化设计提供理论支持。本文的计算模型中含有完整的微通道区域,计算模型的结构和尺寸与实际模型完全一致,计算边界条件与实际完全一致,克服了其他文献中假定晶体表面温度或表面换热系数等边界条件的简化算法的缺点,计算结果更能揭示微通道热沉结构及流场分布对晶体冷却效果的影响。
2 理论分析与数值计算
2.1 计算模型
本文建立了冷却液沿板条宽度方向流动的双面串联冷却结构的物理模型,模型中冷却水从板条一侧的下端入口进入热沉,从板条另一侧的下端出口流出热沉。计算的物理模型如

图 1. 双面串联冷却结构的计算模型示意图。(a)等轴视图;(b)正视图
Fig. 1. Schematic of calculation model of two-sided tandem cooling structure. (a) Isometric view; (b) front view
2.2 板条热源分布
泵浦光光强在增益介质中沿传输方向呈现指数衰减,其中转化为热量的比例与增益介质的掺杂浓度和传输路径有关。双端泵浦的板条可视为一个产热量非均匀分布的体热源,体热源中热流密度的分布关系式[10]为
式中:q为泵浦光在增益介质内的热流密度;ηheat为泵浦光的光-热转换系数;P为泵浦光功率;α为增益介质对泵浦光的吸收系数;w为板条的宽度;t为板条的厚度;L为总吸收长度;x为吸收长度方向的坐标,以增益介质几何中心点为原点。
2.3 边界条件
由于较大的冷却液流量会导致流动阻力急剧上升,因此设定冷却液流量分别为5,10,15,20,25 L/min,入口温度均为25 ℃。对于单相强制对流换热,微通道内冷却液的流动形态对换热效果有着较大的影响,按照雷诺数的计算公式,在设定最大流量为25 L/min时,微通道内的流动雷诺数为857,尚未达到湍流的临界值[11],因此所有计算模型中的流动按照层流模型进行计算。
相对于铜热沉而言,板条自身的导热系数极小[12],板条自身热量扩散能力极弱,在空气自然对流时对流换热系数也较小;在晶体两个大侧面同时冷却的情况下,可认为板条中所有热量通过热沉被冷却液带走,板条的端头和上下两个小侧面可设定为绝热。计算中铜热沉及Nd∶YAG板条的热物性参数如
表 1. 铜热沉及Nd∶YAG板条热物性参数
Table 1. Thermophysical parameters of cooper heat sink and Nd∶YAG slab
|
2.4 计算结果及分析
在不同冷却液流量下,本文分别计算了模型中晶体的温度分布及流体区域的压力分布,计算结果如
表 2. 不同冷却液流量下的计算结果
Table 2. Computation results under different volume flow rates
|
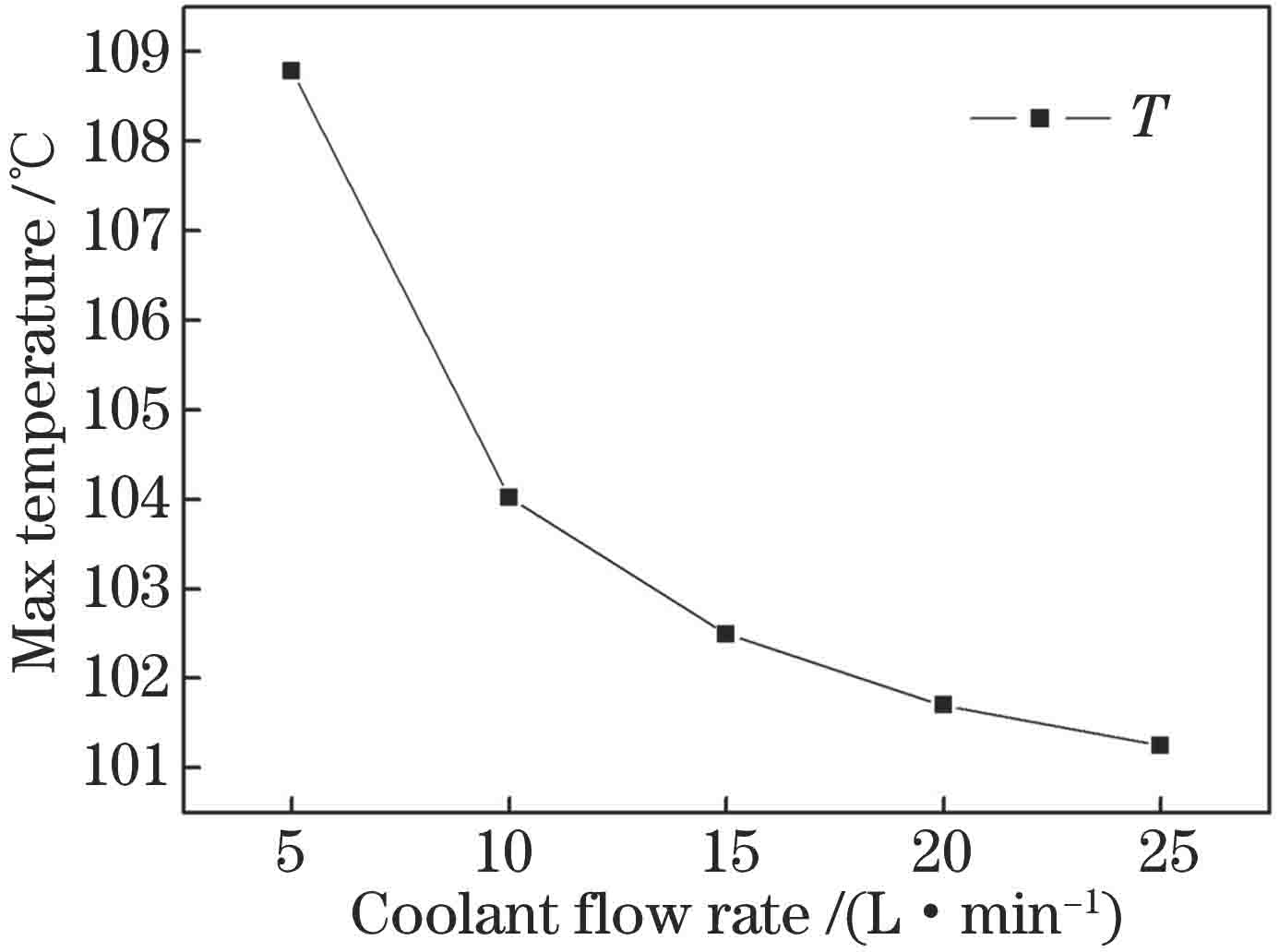
图 3. 晶体中心面最高温度随冷却液流量的变化曲线
Fig. 3. Max temperature on middle face versus coolant flow rate
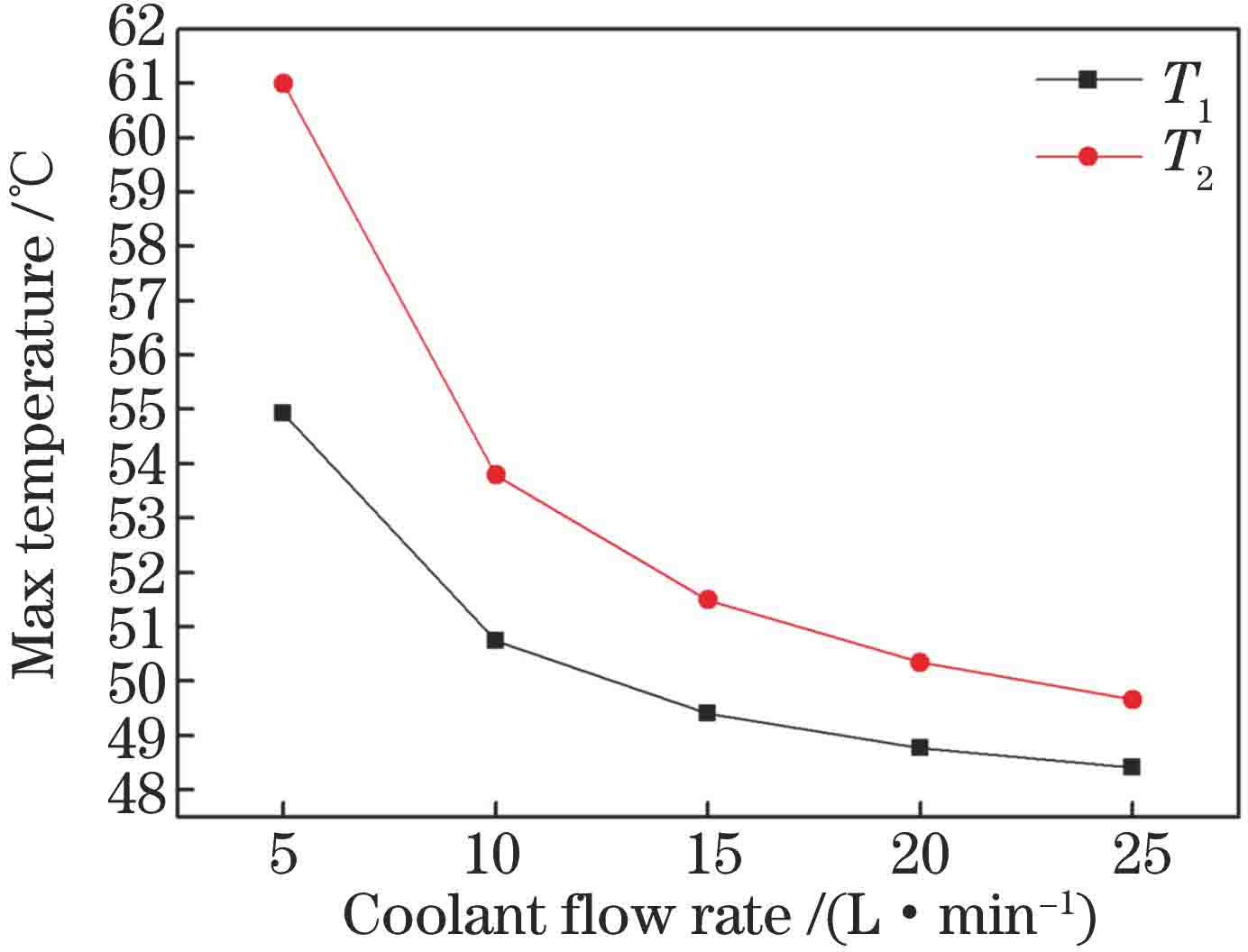
图 4. 晶体两个冷却面最高温度随冷却液流量的变化曲线
Fig. 4. Max temperature of two cooling surfaces of crystal versus coolant flow rate
在激光放大链路中,每一级放大器由LD泵浦源和晶体组成,冷却液从放大器的入口进入后,经分流装置分别流入LD泵浦源和晶体的冷却结构,最后汇集到一起从放大器的出口流出。在所计算的模型中,单个LD泵浦源的泵浦功率为3000 W,电光效率约为50%,冷却液流量一般为9 L/min,则可得LD泵浦源进出口冷却液的温差为4.8 ℃。当板条内冷却液的流量为15 L/min 时,板条冷却液的进出口温差为5.17 ℃,即从板条冷却结构流出的冷却液的温度与从LD冷却结构流出的冷却液的温度非常接近,二者汇集后在极短时间内即可混合均匀,这可以有效保证冷却系统回液温度的一致性,有利于冷却系统的高精度温控设计。因此在该泵浦功率下,板条冷却结构的冷却液流量应取15 L/min。
流量为15 L/min时,板条中心面、入口侧冷却表面及出口侧冷却表面的温度分布如
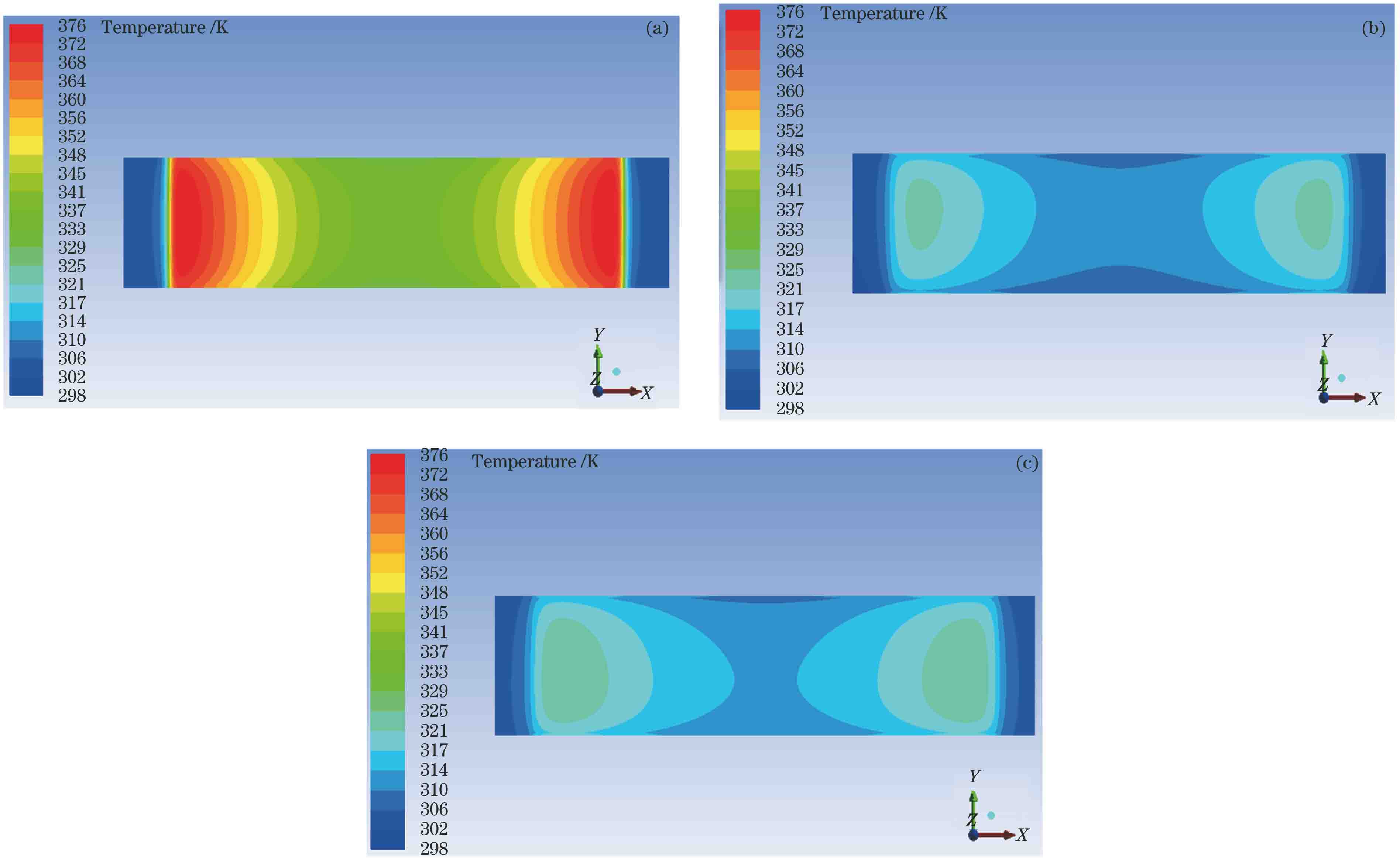
图 5. 板条典型特征截面的温度分布云图。(a)板条中心面;(b)入口侧冷却表面;(c)出口侧冷却表面
Fig. 5. Temperature distributions of representative sections of slab. (a) Middle face of slab; (b) cooling surface near inlet; (c) cooling surface near outlet
在板条掺杂区域的中心面上距离键合线1,2,3,4,5 mm处分别取一条直线,命名为a、b、c、d、e。所取直线均沿着板条宽度方向。
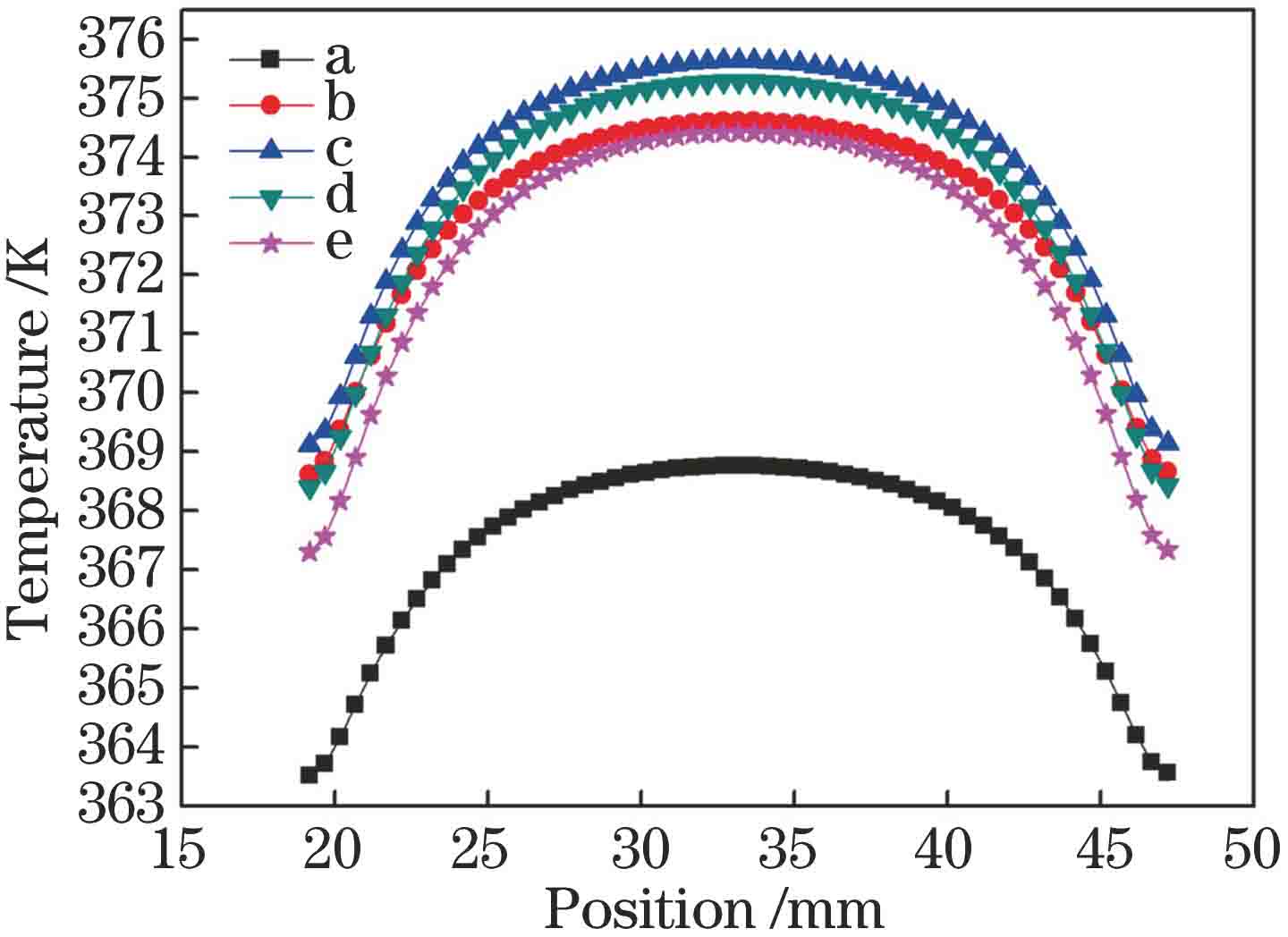
图 6. 距离键合线不同位置处板条宽度方向上的温度分布曲线
Fig. 6. Temperature distribution curves in width direction of strip at different length from bonding line
在板条掺杂区域离键合面3 mm的平面上,沿着板条厚度方向分别取距离出口侧板条冷却面0.5 mm和距离入口侧板条冷却面0.5 mm的两条直线,分别命名为m和n,这两条直线以板条的中心面为对称面呈左右对称分布。
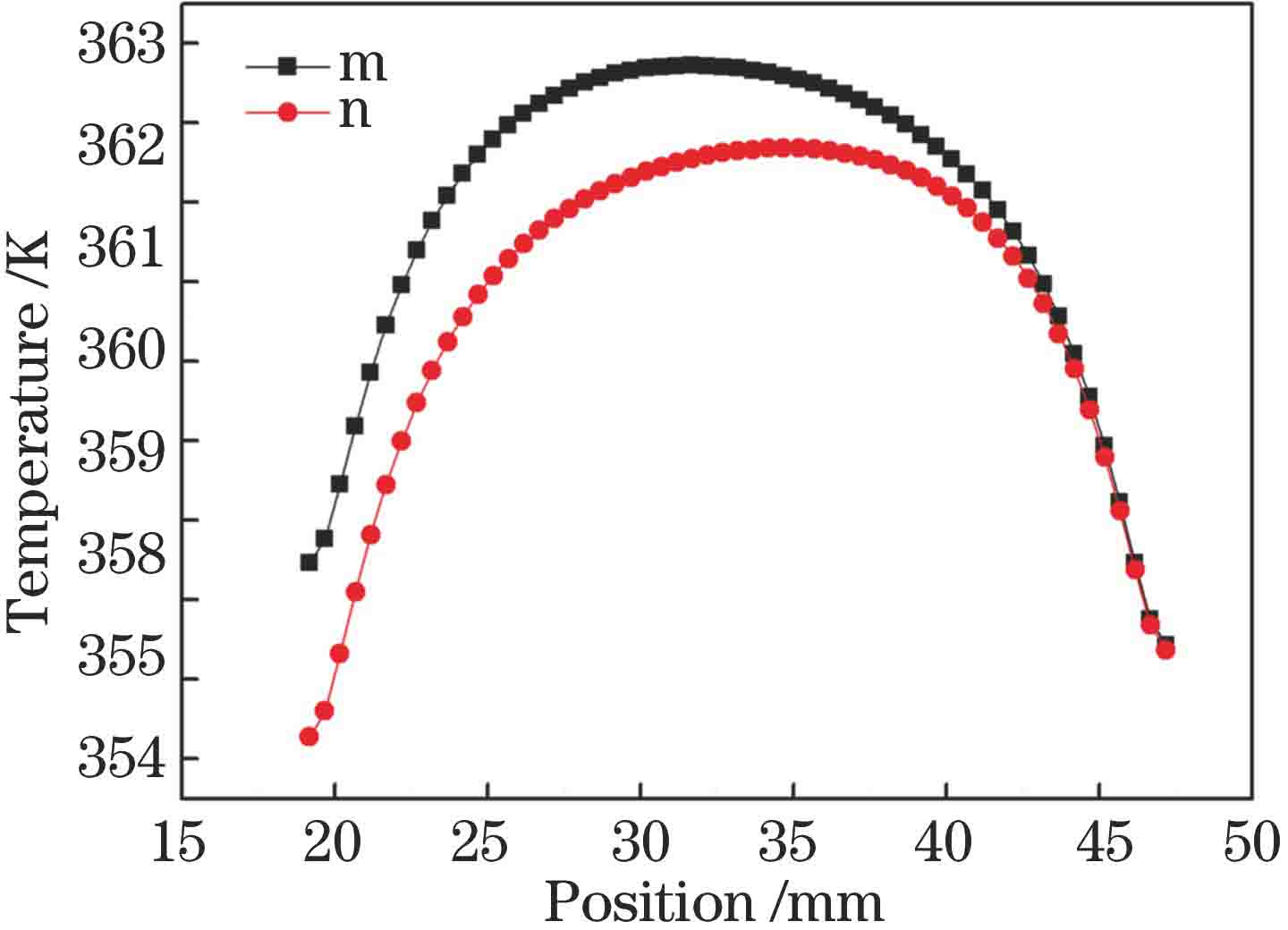
图 7. 离键合面3 mm的平面上板条宽度方向上的温度分布曲线
Fig. 7. Temperature distribution curves in width direction of strip on plane 3 mm away from bonding surface
3 实验验证
由于封装后增益介质内部的温度无法直接测量,只能通过红外热像仪测量晶体上表面的温度,并与数值计算的结果进行对比,以验证数值计算结果的正确性和合理性。温度测量采用的FLIR红外热像仪在0~200 ℃范围内的测量误差为5%。实际测试前,将红外热像仪的测量发射率设置为晶体辐射率的0.75,测试在十万级恒温净化间中进行,可忽视环境因素对测量的影响,并确保测量角度小于30°,以期尽可能减小测量误差。
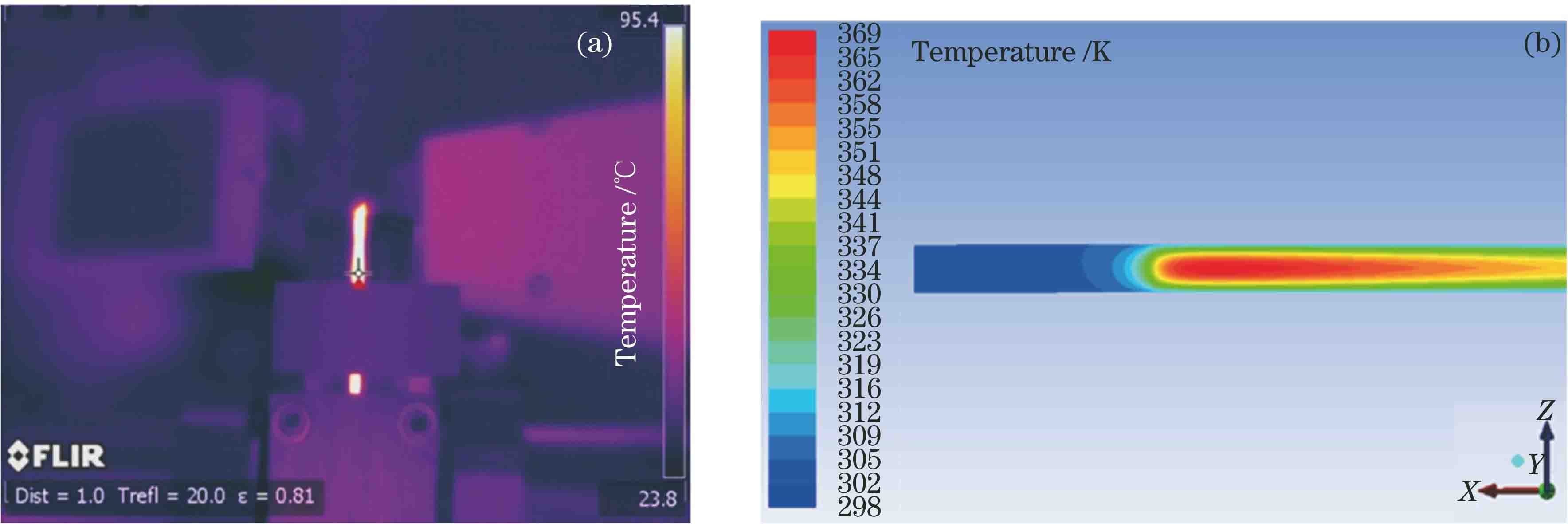
图 8. 实验结果与数值计算结果对比图。(a)板条上表面红外热像图;(b)板条上表面数值计算温度分布云图
Fig. 8. Comparison of experimental result and numerical simulation. (a) Infrared thermal image of upper surface of slab; (b) calculated result of temperature distribution of upper surface of slab
4 结论
本文建立了含有激光晶体和微通道热沉的全尺寸封装结构模型,通过对微通道内冷却液流量及换热特性进行数值计算,得到了非均匀热源分布下晶体的温度分布情况,并利用红外热像仪测量了激光放大实验中晶体上表面的温度分布,实际测量结果与数值计算结果基本一致,验证了数值计算具有较高的准确度。计算结果表明:激光晶体的冷却液流量并非越大越好,而是存在一个最佳值,为15 L/min;此外,微通道内部的流场分布对晶体表层及内部的温度分布影响较大,充分证明了其他文献中不考虑流场而直接假设晶体表面恒定温度和表面恒定换热系数进行计算是不合理的。本文的计算结果可以为下一步固体激光器冷却结构的改进提供有力的数值依据和理论基础。
[1] 张建军, 李金平, 王锐. 激光二极管双侧泵平板Nd∶LuVO4晶体热效应[J]. 红外与激光工程, 2012, 41(3): 607-611.
[2] 杨鸿儒, 左铁钏. 全固体小型Yb∶YAG 激光器热效应及输出特性研究[J]. 光子学报, 2003, 32(8): 907-910.
[3] 田长青, 徐洪波, 曹宏章, 等. 高功率固体激光器冷却技术[J]. 中国激光, 2009, 36(7): 1686-1692.
[4] 耿鹰鸽, 李隆, 潘晓瑞, 等. LD端面泵浦变热导率圆片Yb∶YAG激光器的热效应[J]. 光学技术, 2017, 43(2): 103-107.
[5] 王建磊, 李磊, 施翔春, 等. 高功率板条放大器冷却系统模拟及优化设计[J]. 中国激光, 2010, 37(6): 1553-1559.
[6] 杨丽颖, 李嘉强, 张金玉, 等. 半导体激光泵浦复合晶体固体激光器的热效应[J]. 发光学报, 2017, 38(6): 742-746.
[7] 关丽. Nd∶YAG固体激光器的热效应研究[D]. 南京: 南京邮电大学, 2012.
GuanL. Research on the thermal effects of Nd∶YAG laser[D]. Nanjing: Nanjing University of Posts and Telecommunications, 2012.
[8] 张震. LD端泵固体激光器微通道冷却技术研究[D]. 哈尔滨: 哈尔滨工业大学, 2008.
ZhangZ. Study of the micro-channel cooling technology for LD end-pumped solid state lasers[D]. Harbin: Harbin Institute of Technology, 2008.
[9] 李锋, 刘蓉, 白晋涛, 等. LD抽运复合YAG晶体温度场及热透镜效应研究[J]. 激光技术, 2008, 32(1): 101-104.
[10] 王明哲. 高功率固体激光器热管理新技术研究[D]. 长沙: 国防科学技术大学, 2011.
Wang MZ. Research on new cooling technology for thermal management of high power solid-state lasers[D]. Changsha: National University of Defense Technology, 2011.
[11] 景思睿, 张鸣远. 流体力学[M]. 西安: 西安交通大学出版社, 2001.
Jing SR, Zhang MY. Fluid mechanics[M]. Xi'an: Xi'an Jiaotong University Press, 2001.
[12] KoechnerW. Solid-state laser engineering[M]. 6th ed. New York: Springer, 2006.
吕坤鹏, 刘震宇, 杨雪, 王柯. 高功率固体激光器微通道冷却结构的数值研究[J]. 中国激光, 2020, 47(6): 0601010. Lü Kunpeng, Liu Zhenyu, Yang Xue, Wang Ke. Numerical Research on Microchannel Cooling Structure of High Power Solid-State Lasers[J]. Chinese Journal of Lasers, 2020, 47(6): 0601010.