Polarization insensitive arrayed-input spectrometer chip based on silicon-on-insulator echelle grating
Download: 871次
Imaging spectrometers are most commonly used on satellites and aircrafts, including unmanned aerial vehicles (UAVs), where the spare volume and weight are limited. Recently, the development of a UAV in precision agriculture, local water quality, and forest disaster monitoring[1] calls for higher demands in the compactness of imaging spectrometers. A compact Fabry–Perot interferometer (FPI) hyperspectral imager has been reported[2]. However, the wavelength switching (by tuning the FPI air gap) takes 2 ms, which means a slow scan rate at high number of wavelength channels.
Integrated photonics have achieved great success in next-generation optical networks, optical interconnects, wavelength division multiplexing systems, coherent transceivers, and lab-on-a-chip applications[3,4]. Also, many on-chip spectrometers have been reported[5
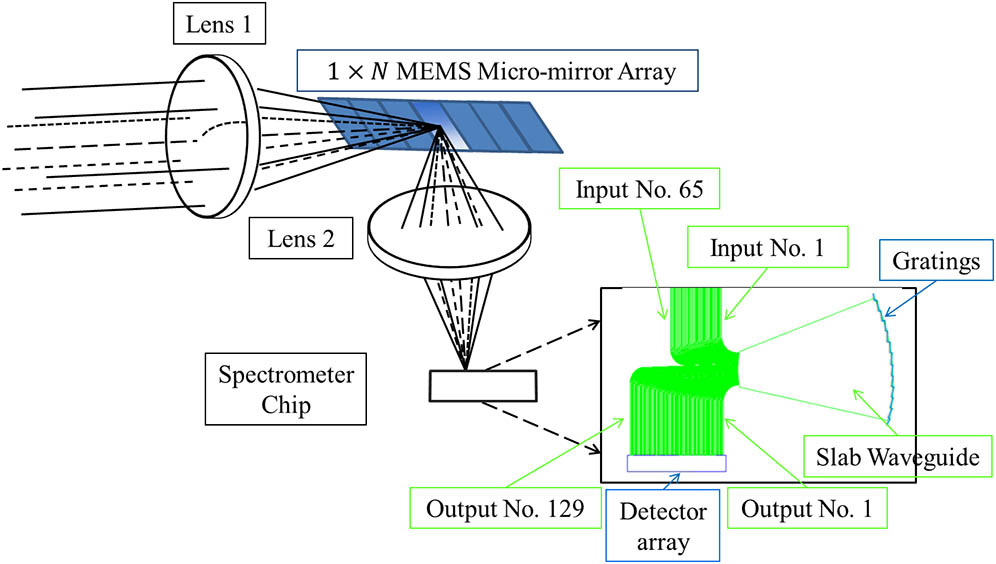
Fig. 1. Schematic diagram of the imaging spectrometer, where the arrayed-input EDG is used. Lens 1 represents the fore-optic lens, and the micro-electromechanical system (MEMS) mirror array operates as an optical switch array for N pixels. The chip structure is enlarged, and the arrayed input waveguides receive the N corresponding pixels one by one. Thus, the spectrum of each pixel is obtained in a time division multiplexing fashion.
To achieve high optical étendue and low polarization dependence, we choose a 3 μm thick silicon-on-insulator (SOI) platform[1214" target="_self" style="display: inline;">–

Fig. 2. (a) Scanning electron microscope (SEM) images of the cross-section of a deep etched strip waveguide, (b) cross-section of a shallow etched ridge waveguide, (c) tapers between ridge waveguides and deep etched strip waveguides, (d) cross-section of the Al coated surface, and (e) the grating facets of the EDG. (f) The photograph of the EDG chip compared with one yuan coin.
The design of the EDG follows Rowland mounting with one stigmatic point method[17]. The input beam from one of the input waveguides on the Rowland circle radiates to the slab region and is reflected by the gratings. After being diffracted, light of different wavelengths will be focused onto different output waveguides on the Rowland circle. The grating diffraction is described by
Considering the imaging spectrometer application and the fabrication tolerance, we choose a wide range for the working spectrum, from 1250 to 1750 nm, with a diffraction order
The structure of the slab waveguide consists of a 0.3 μm buried oxide (BOX) layer, a 3 μm silicon layer, and a 0.6 μm silicon oxide upper cladding. The effective index difference between the TE and TM modes produces a less than 0.55 nm polarization dependent wavelength shift (
A shallow etch of 1.2 μm is used to form the single mode ridge input waveguide. It is tapered into a deep etched strip waveguide to guide the light into the slab region. Due to the fabrication requirement, the deep etched waveguides are aligned along the Rowland circle at the slab interface with a spacing of about 5 μm, forming 2 μm wide and 3 μm deep slots between the waveguides. The output angle
The blazed angles of the gratings are adjusted to balance the loss of two edge wavelength channels, 1250 and 1750 nm, according to the Fraunhofer diffraction formula. Also as an EDG device, the blazed condition of the gratings remain for all 65 input waveguides, and the loss of all of the input waveguides is similar, which is proved by the simulation of a similar device[20].
As shown in Fig.
To measure the spectral response of the device with such a wide wavelength band, we use a supercontinuum source (YSL photonics SC-5 series) and an eight-channel acousto-optic tunable filter (AOTF) tunable filter to provide light into the input waveguide via a polarization-maintaining lensed fiber. To collect the energy from the output waveguide, another lensed fiber connected to the optical spectrum analyzer (OSA, Agilent 86146B) is used. Due to the 1700 nm upper limit of the OSA, only 58 of the 65 channels could be tested. The measured spectrum is normalized with respect to the transmission spectrum of a straight waveguide to account for the coupling loss (about 7 dB) and eliminate the shape of the supercontinuum source spectrum. We measured the 58-channel spectra of the center and edge (Nos. 1, 33, and 65) input waveguides. For the No. 33 input waveguide, both the TE and TM polarizations are tested to show the polarization insensitive characteristics of the device.
As shown in Fig.
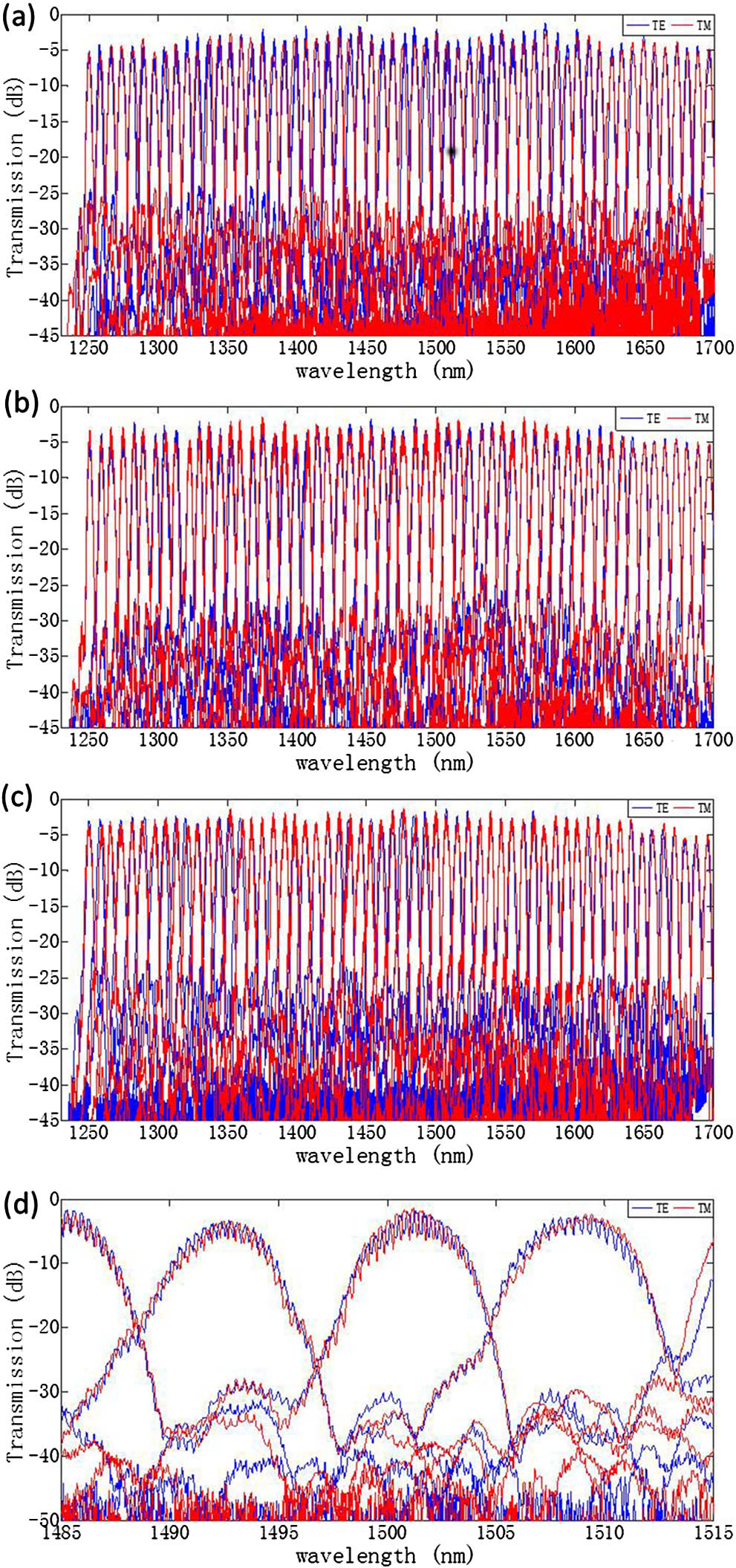
Fig. 3. (Color online) Transmission spectra for (a) input waveguide No. 1, (b) input waveguide No. 33, and (c) input waveguide No. 65. The enlarged spectra for output channel Nos. 32 to 34 of input waveguide No. 33 are given in (d), showing the detailed polarization insensitive characteristics.
In conclusion, we demonstrate a push-broom micro-imaging spectrometer using an on-chip EDG, which is highly compact and can achieve high resolution imaging. As the first demonstration, we design and fabricate a 65 input and 129 output EDG with a 500 nm spectral range. A low on-chip loss of 2 dB and a crosstalk below
Table 1. Design Parameters of the EDG
|
[1]
[2]
[3]
[4]
[5]
[6]
[7]
[8]
[10]
[11]
[12]
[15]
[16]
[17]
[18]
[19]
[21]
Minyue Yang, Mingyu Li, Jianjun He. Polarization insensitive arrayed-input spectrometer chip based on silicon-on-insulator echelle grating[J]. Chinese Optics Letters, 2017, 15(8): 081301.