基于机器视觉的纱线质量检测系统设计
下载: 1187次
1 引言
在纱线质量检测中,纱线条干均匀度、纱线毛羽数量和长度是评定纱线质量好坏的重要指标,也是影响后期织物质量的关键因素[1]。若纱线条干不均匀,就会在织物上会出现各种疵点;而毛羽较多,则会导致织物表面不清晰,严重影响后期的染色效果[2]等。因此,纱线条干和毛羽的检测对提高纱线质量具有重要意义。
目前,企业在检测纱线条干方面利用的是电容式条干仪[3]。但该仪器对环境要求较高,且容易受温湿度的影响。在检测毛羽方面主要利用光电法和目测法。但光电法分辨率低,容易造成误差;目测法易受检测人员主观因素的影响,精确度较差。
近年来,计算机技术及图像处理技术迅速发展,越来越多地被用于纺织品外观检测,解决了传统方法存在的不足。国内外众学者利用图像处理技术检测纱线条干[4-6]及纱线毛羽[7-8]。如在检测纱线条干方面,Ozkaya等[9]重点研究了运用图像处理方法检测纱线条干均匀性时,光照条件对检测结果的影响。研究发现,背光条件下的均匀度测量结果更准确,检测得到的条干均匀度变异系数(CV)值与Uster仪器的测量结果很相近,但与理论值相比均偏小。在检测纱线毛羽方面,孙银银等[10-11]提出了毛羽跟踪算法,该算法可以准确地计算出每根毛羽的长度,并通过不断地扩大毛羽端点像素领域来搜寻断开毛羽,但在扩大搜寻过程中可能搜寻到其他毛羽的端点,从而引入了误差。
针对上述问题,本文设计了一种基于机器视觉的纱线质量检测系统,该系统特点如下:1) 可同时检测纱线直径、纱线条干均匀度变异系数、纱线毛羽长度和毛羽指数等指标;2) 实现了纱线质量的实时检测,同时也可利用单幅检测功能查看某一片段的纱线质量;3) 可检测棉、化纤以及两者混纺的纱线,也可检测多种规格纱线。经验证,本系统稳定性强,具有较高的精确度,能够实现纱线检测自动化和纱线条干及毛羽的检测指标评估,具有一定的学术研究价值及应用推广价值。
2 系统总框架
系统总框架如
3 系统硬件结构
3.1 硬件结构
系统硬件结构主要包括图像采集装置、纱线牵引装置和控制装置。装置如
3.2 图像采集装置
图像采集装置包括BASLER公司的Basler acA2500-14gc面阵相机、镜头、LED光源和黑色背景板。此外,为了获取清晰的纱线图像,需对相机参数进行设置。本系统中相机采集的纱线图像的分辨率为256 pixel×256 pixel,相机光圈为4、曝光量为3900,相机采集帧率为30 frame/s。
3.3 纱线牵引装置和控制装置
纱线牵引装置主要由转速为16 r/min的大扭矩低速电机和支架组成。主要作用是牵引纱线匀速通过图像采集装置。控制装置为一台计算机,配置为Intel Core i5-4460 3.2 GHz CPU、8 GB主内存、NVIDIA GeForce GT 705显卡和Windows 8.1操作系统。其主要作用是通过千兆网线控制采集装置,保存和处理采集的纱线图像。
3.4 工作原理
系统工作时,纱线在低速电机的牵引下从两个LED光源之间、背景板上方2~4 mm处匀速通过。相机安装在纱线正上方,相机采集到纱线图像后,通过千兆网线传输到计算机中进行处理或保存。
4 系统软件设计
4.1 软件框架
本系统软件主要分为3部分:1)图像采集控制程序;2)纱线条干检测算法与纱线毛羽检测算法;3)人机交互界面。软件框图如
4.2 图像采集控制
1) 参数设置程序。① 选择纱线图像的保存路径。② 输入纱线规格和纱线所含成分比例,主要用于计算纱线理论直径、误差等指标。③ 设置检测时间,用于控制相机工作时间及检测时长。
2) 相机控制。这部分主要利用了Open CV中的相机控制模块,作用是打开相机和设置定时程序关闭相机。
3) 纱线图像保存。根据预先设置的检测时间,计算出每张图像的保存时间,设置定时程序,保存纱线图像于选择的文件夹中,系统可定时保存数百张纱线图像。
4) 计算每个像素点代表的实际大小,用于计算直径和毛羽长度等指标。计算方法为:将1 cm×1 cm的标定板放置在与纱线水平的位置,利用相机采集标定板图像,通过实际长度与其所占像素数目计算出每个像素代表的实际长度。重复上述过程10次,取其平均值,该值即为每个像素代表的实际长度。
4.3 图像检测算法的实现
4.3.1 纱线条干检测
利用图像处理技术检测纱线的平均直径及条干均匀度,提取纱线条干。本研究利用双边滤波、Otsu阈值和形态学开运算相结合的方法提取纱线条干。具体过程如下:
1) 将相机获取的RGB图像转换为单通道的灰度图像。
2) 对纱线灰度图像进行双边滤波处理。双边滤波在滤除噪声的同时可完整地保留纱线的边缘,且可增强纱线特征。
3) 滤波后利用Otsu(大津阈值)分割法提取纱线的条干。从
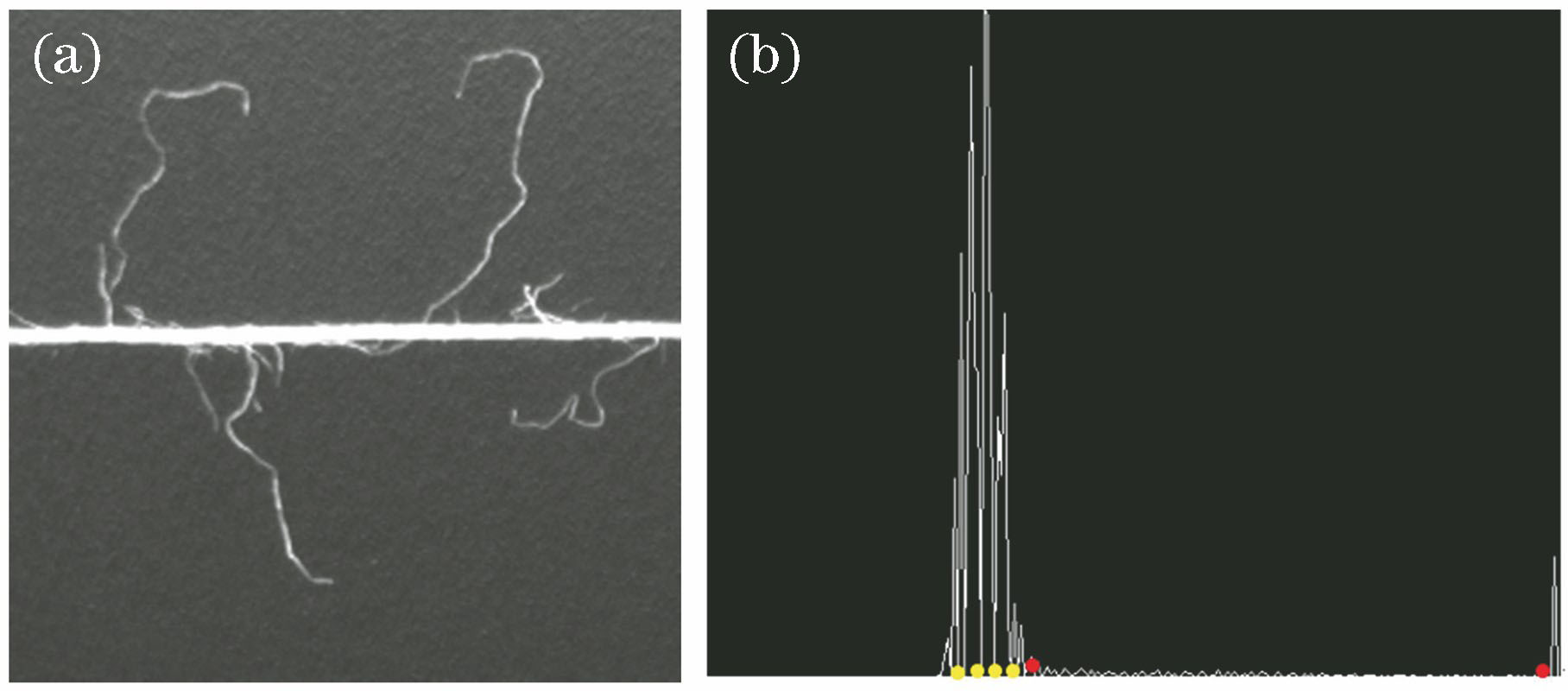
图 4. 纱线图像及灰度直方图。(a)纱线图像;(b)纱线图像灰度直方图
Fig. 4. Yarn image and gray histogram. (a) Yarn image; (b) gray histogram of yarn image
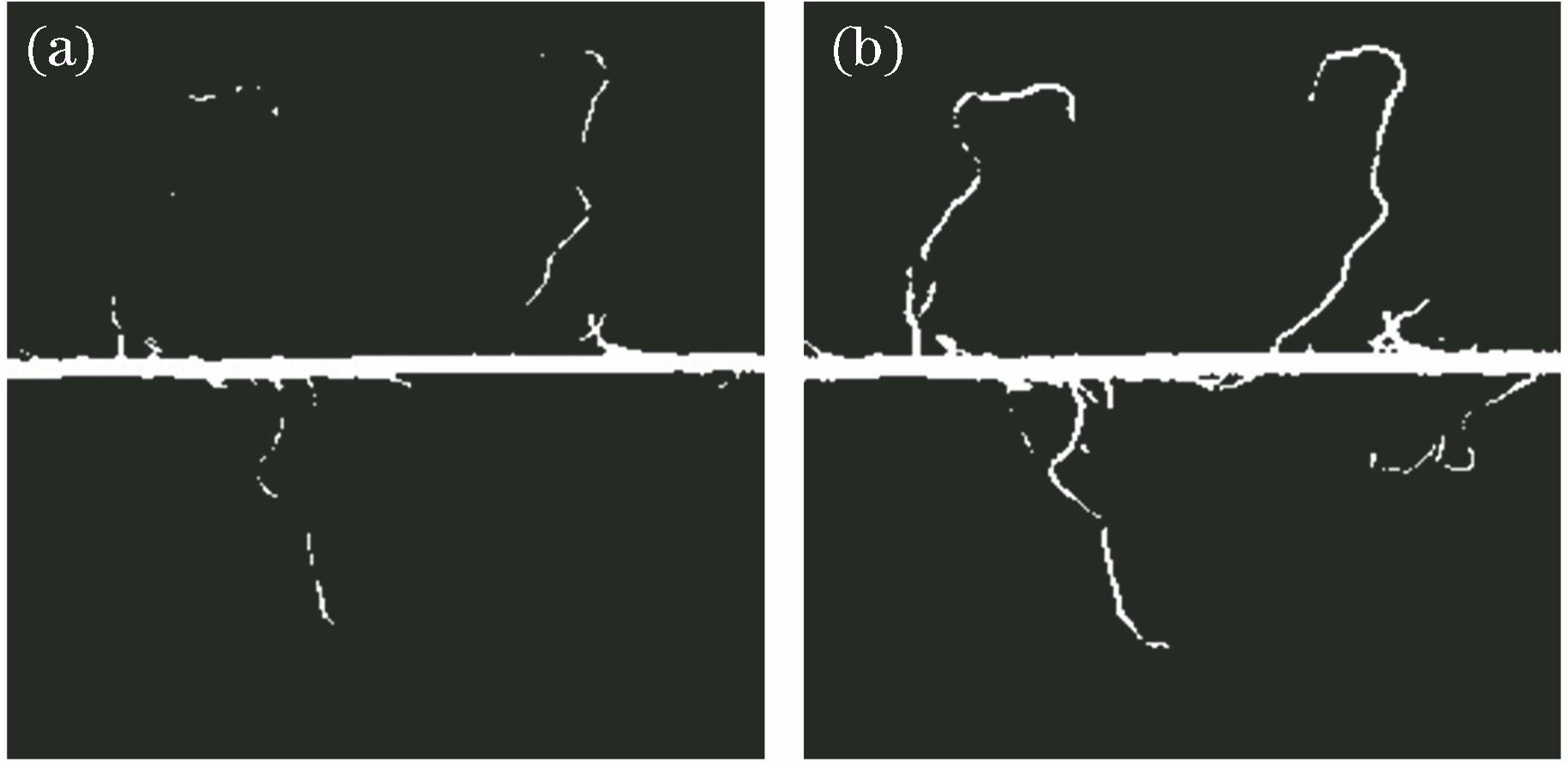
图 5. 阈值算法对比.(a) Otsu阈值;(b)迭代阈值
Fig. 5. Comparison of threshold algorithms. (a) Otsu threshold; (b) iteration threshold
4)利用形态学开运算处理细小疵点。开运算处理后纱线条干周围的疵点已被完全去除,纱线条干被完整地提取出来。
纱线图像经过上述4步处理后,纱线条干被完整地提取出来,此时可用于计算纱线的平均直径和条干均匀度。
纱线平均直径的计算方法为:提取出纱线条干后,计算纱线的平均直径。计算过程为从上往下、从左往右扫描图像,统计像素值为255的数目,用统计后的总数目除以该段纱线在图像中所占的像素数,然后用得到的结果乘以该图单个像素的长度,就可以得到纱线直径的平均值,即为纱线平均直径。
条干均匀度变异系数(CV)指纱线在长度方向的横截面均匀度。条干均匀度变异系数
式中:
4.3.2 纱线毛羽检测
根据纱线毛羽特征,设计的检测毛羽的算法步骤如下:
1) EM分割。从
2) 去除条干并细化。EM分割后需去除纱线条干,首先对上文提取的条干进行膨胀,目的是消除纱线条干周围短小毛羽对毛羽统计造成的影响,然后用分割后的图像减去膨胀后的条干,提取出毛羽后进行细化处理。
3) 毛羽计数。根据时效性和精确性的要求,在实时检测毛羽部分时利用的方法是画等距线,先找出条干边缘,然后基于条干边缘每隔一定距离画一条线,最后统计线上的毛羽根数。利用具有噪声的基于密度的聚类方法(DBSCAN)进行单幅检测[14],不但可直接统计出毛羽根数,还可直接计算出每根毛羽的具体长度。此外,该算法在毛羽小范围断开以及毛羽弯曲的情况下不受影响。因此,在不考虑毛羽交叉的情况下,提取的纱线毛羽呈离散分布,利用密度聚类可计算出根数及长度。
除了毛羽根数及长度外,毛羽的指标还有毛羽指数(1 cm长度的纱线条干上毛羽长度的总和),其计算方法是统计细化后毛羽图像中像素点的个数,然后计算毛羽指数。
此外,本系统还检测了纱线毛羽CV值,计算公式与(1)式相同。但
5 实验结果
5.1 软件界面
根据上述软件框架及算法,利用VS2013 MFC与OpenCV库设计了纱线检测系统界面。界面主要作用是实现人机交互,为用户提供简单、直接、方便的操作系统。界面主要包括参数设置模块、图像和检测结果显示模块。
1) 参数设置模块。在纱线检测之前,需要在此模块中设置保存路径、纱线规格等参数,用于程序中保存图像及计算指标等。
2) 图像和检测结果显示模块。此模块包括实时检测与单幅检测两部分。实时检测部分主要用于实时显示待检测纱线和所检测的纱线指标;单幅检测模块主要显示待检测纱线图像、提取的纱线条干图像、纱线毛羽图像和所检测的纱线指标。
5.2 纱线直径及CV值
本实验分别对18.2 tex、14.5 tex样品进行5次检测,其检测结果如
表 1. 18.2 tex纱线直径与CV值
Table 1. 18.2 tex yarn diameter and CV value
|
表 2. 14.5 tex纱线直径与CV值
Table 2. 14.5 tex yarn diameter and CV value
|
5.3 纱线毛羽实验结果
本次实验中对7段纱线进行采样,每段纱线采集图像40张。图像分辨率为256 pixel×256 pixel。系统计算出的像素点对应实际长度的关系为1 pixel=0.024 mm, 40张纱线图像对应的长度为24.576 cm。在不考虑毛羽交叉的情况下,检测结果如
表 3. 图像法检测结果
Table 3. Test results of image method
|
为凸显本系统算法的优势,将检测结果与目测法进行比较,结果如
表 4. 图像法与目测法比较
Table 4. Comparison of image method and visual method
|
6 结论
针对目前企业检测纱线方法误差较大的缺点,设计了基于机器视觉的纱线质量检测系统。根据纱线的结构,设计了由图像采集单元、纱线牵引装置和系统控制装置组成的硬件系统。在检测软件部分,设计了图像采集控制程序、纱线条干检测算法、纱线毛羽检测算法和纱线指标计算程序,最后将这些算法和VS2013、OpenCV库相结合,设计了人机交互界面。多次实验测试结果表明,本系统的检测结果相对精确,误差较小且运行稳定,可以应用到纱线工业检测中。
[1] 姚穆. 纺织材料学[M]. 3版. 北京: 中国纺织出版社, 2009: 145- 153.
YaoM. Textile material science[M]. 3rd ed. Beijing: China Textile & Apparel Press, 2009: 145- 153.
[2] 高卫东, 王鸿博. 纱线毛羽危害程度的探讨[J]. 纺织学报, 1998, 19(6): 347-348.
Gao W D, Wang H B. An investigation on harmfulness of yarn hairiness[J]. Journal of Textile Research, 1998, 19(6): 347-348.
[3] 钱云青, 秦曾荫, 俞海熊. 电容式条干仪检测器计量检定专用检具的研讨[J]. 纺织学报, 1991, 12(12): 544-546, 538.
Qian Y Q, Qin Z Y, Yu H X. Developmennt of special tool for metrological verification of evenness tester monitor[J]. Journal of Textile Research, 1991, 12(12): 544-546, 538.
[4] 李变变, 李忠健, 潘如如, 等. 纱线条干均匀性序列图像测量方法[J]. 纺织学报, 2016, 37(11): 26-31.
Li B B, Li Z J, Pan R R, et al. Measurement of yarn evenness using sequence images[J]. Journal of Textile Research, 2016, 37(11): 26-31.
[5] Li Z J, Pan R R, Zhang J, et al. Measuring the unevenness of yarn apparent diameter from yarn sequence images[J]. Measurement Science and Technology, 2016, 27(1): 015404.
[6] 景军锋, 张婉婉, 李鹏飞. 应用显著性算法的纱线条干均匀度检测[J]. 纺织学报, 2017, 38(6): 130-135.
Jing J F, Zhang W W, Li P F. Yarn evenness detection based on saliency algorithm[J]. Journal of Textile Research, 2017, 38(6): 130-135.
[7] Jing J F, Huang M Y, Li P F, et al. Automatic measurement of yarn hairiness based on the improved MRMRF segmentation algorithm[J]. The Journal of the Textile Institute, 2018, 109(6): 740-749.
[8] Wang XH, Wang JY, Zhang JL, et al. Study on the detection of yarn hairiness morphology based on image processing technique[C]∥2010 International Conference on Machine Learning and Cybernetics, July 11-14, 2010, Qingdao, China. New York: IEEE, 2010: 2332- 2336.
[9] Ozkaya Y A. Digital image processing and illumination techniques for yarn characterization[J]. Journal of Electronic Imaging, 2005, 14(2): 023001.
[10] 孙银银. 基于图像技术的纱线毛羽检测与分析[D]. 无锡: 江南大学, 2017: 71- 89.
Sun YY. Yarn hairiness detection and analysis based on image technology[D]. Wuxi: Jiangnan University, 2017: 71- 89.
[11] Sun Y Y, Li Z J, Pan R R, et al. Measurement of long yarn hair based on hairiness segmentation and hairiness tracking[J]. The Journal of the Textile Institute, 2016, 108(7): 1271-1279.
[12] TatirajuS, MehtaA. Image segmentation using k-means clustering, EM and normalized cuts[Z/OL].[2017-03-20].http:∥www.dca.fee.unicamp.br/~leopini/DISCIPLINAS/IA369T-22014/Seminarios-entregues/Grupos-BigData/BigData-Gr-LuisPattam-paperdeapoio-3.pdf.
[13] 赵慧洁, 曲磊, 程宣. 基于期望值最大化的高光谱图像迭代复原算法[J]. 光学学报, 2009, 29(8): 2164-2168.
[14] Rodriguez A, Laio A. Clustering by fast search and find of density peaks[J]. Science, 2014, 344(6191): 1492-1496.
Article Outline
张缓缓, 严凯, 李鹏飞, 景军锋, 苏泽斌. 基于机器视觉的纱线质量检测系统设计[J]. 激光与光电子学进展, 2019, 56(16): 161504. Huanhuan Zhang, Kai Yan, Pengfei Li, Junfeng Jing, Zebin Su. Design of Yarn Quality Detection System Based on Machine Vision[J]. Laser & Optoelectronics Progress, 2019, 56(16): 161504.