Rapid fabrication of mini droplet lens array with tunable focal length
Download: 590次
In the traditional manufacture of glass or silica optical lenses, milling techniques are widely used. The techniques can precisely fabricate the lenses of complex structures. Nevertheless, the whole fabrication process including cutting, grinding, and polishing is time consuming. It requires professional engineers to design the lenses and skillful technicians to operate high-cost facilities for lens fabrication. In addition, the lenses produced by the milling method have a fixed focal length.
Various techniques have been proposed to fabricate focal-length-tunable lenses. The focal length tuning can be realized by either adjusting the refractive index of the lens[1,2] or changing the shape of the lens[35" target="_self" style="display: inline;">–
Liquid lenses can be fabricated by infusing high-refractive-index liquid into a chamber. An elastic membrane tightly seals the lens chamber[8,9]. By squeezing the chamber, the curvature of the elastic membrane can be adjusted, and the tuning of the focal length can be realized. In Ref. [10], the chamber was designed as a communicating vessel and sealed by an elastic membrane and a photo-polymer. The deformation of the photo-polymer driven by UV light could indirectly bend the elastic membrane and tune the focal length. The mechano-fluidic technique provides an alternative way for focal length tuning[11,12]. By controlling the volume of the liquid in the chamber, the elastic membrane could be deformed, and the focal length could be tuned. Besides sealing liquid in a chamber covered by an elastic membrane, a liquid lens can be formed by using two immiscible liquids. Focal length tuning can be realized by the electrowetting technique for manipulating the interface of the liquids[13,14]. Nevertheless, the interface of the liquids might be deformed by the external undesired force, such as the gravity effect, when the lens is placed at a vertical position, and the lens made of the liquid phase would be affected. As a result, the imaging quality degrades due to the deformation of the lens profile.
Recently, a novel liquid-filled droplet lens was proposed[15]. In the fabrication of the lens, a high-refractive-index and high-density droplet sinks to the bottom of a liquid-state polymer of relatively low refractive index and low density. Once the forces applied to the droplet, i.e., tension force, gravity, buoyant force, and normal force, are balanced, the polymer is solidified to an elastomer, and the plano-convex-shaped droplet at the bottom of the elastomer is still in a liquid state, forming a mini lens. The focal length can be flexibly and widely tuned by squeezing the elastomer.
Lens arrays are essential optical components widely used in lots of applications, such as three-dimensional (3D) imaging, 3D display[16], multispectral imaging[17], and efficiency enhancement for photovoltaic cells[18,19]. Lens arrays can be fabricated by many techniques, including thermal reflow[20], laser direct writing[21,22], inkjet printing[23], and photolithography[24]. The thermal reflow technique can rapidly produce a lens array by melting an array of pre-prepared cylindrical polymers into a hemispherical shape. To have a complex profile of lenses, the laser direct writing technique can be used to realize 3D structural modification. Besides, the inkjet printing technique can print out lenses one by one according to a pre-defined program, and the curvature of the lenses can be controlled by the surface modification of the substrate. The photolithography technique can directly fabricate an array of highly uniform lenses by transferring a pattern of a lens-array structure from a gray-scale mask to photoresist. Although the techniques can fabricate high-quality lens arrays, the focal length of the lenses can only be determined during the fabrication stage and cannot be tuned once the lens arrays are developed.
In this Letter, a rapid fabrication technique to produce mini droplet lens arrays is proposed. The focal length of the lenses can be flexibly adjusted by squeezing the lens array. Optical imaging is demonstrated by using the fabricated focal-length-tunable mini lens array.
Figure
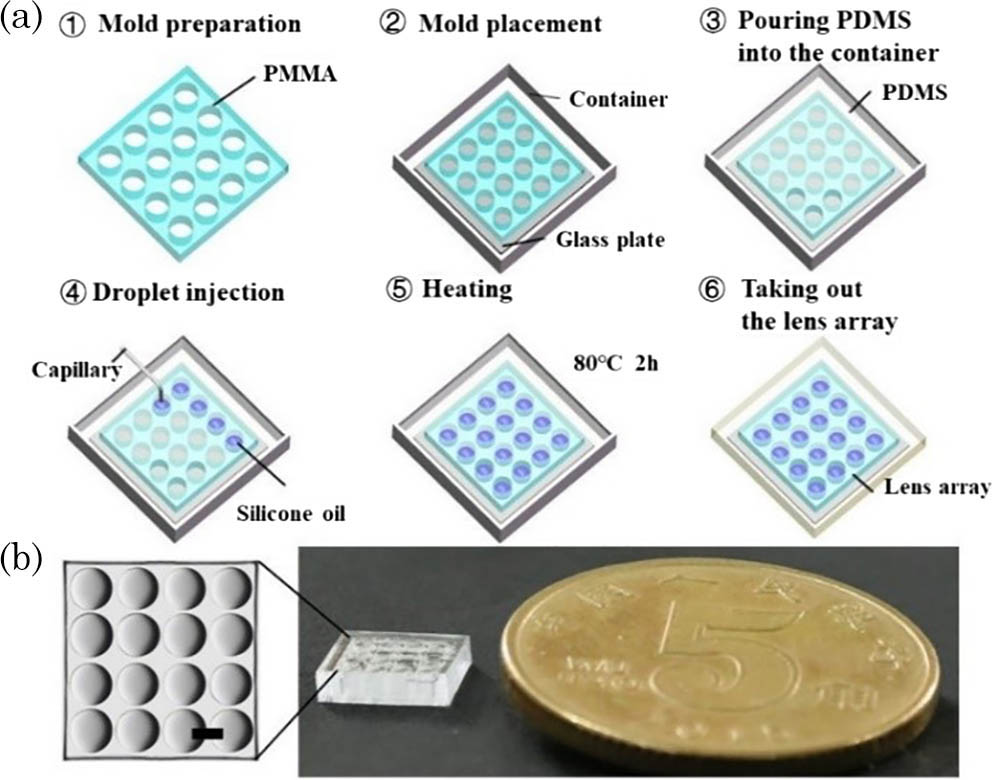
Fig. 1. (a) Fabrication process of the droplet-filled convex lens array. (b) Photo of the fabricated lens array and the top-view microscopic image of the lens array.
A fabricated
Figure
In addition, to investigate the tolerance of the fabrication, the silica capillary aims a 1 mm diameter hole with a deviation from the center by 200 μm. The droplet sinks towards the hole away from the center, as shown in Fig.
Figure
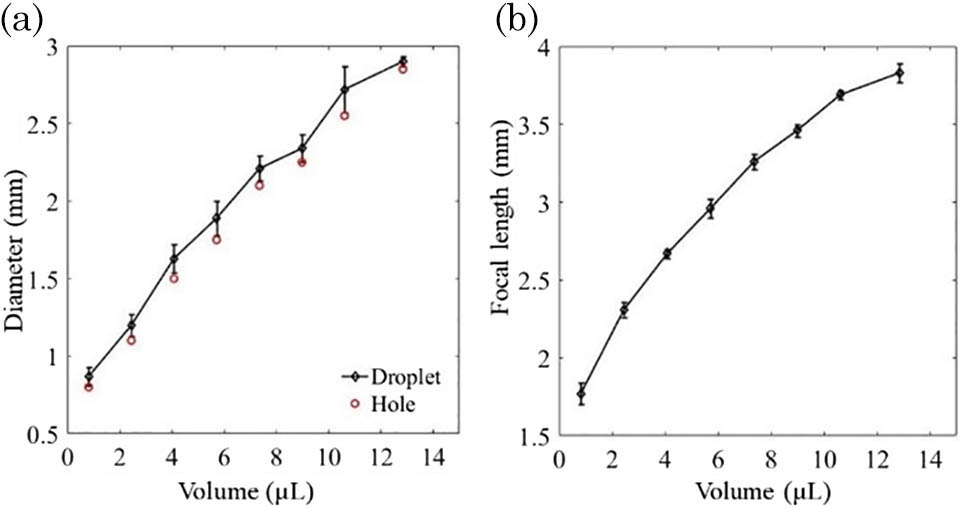
Fig. 4. (a) Relation of the droplet volume and the diameter of the droplet at the bottom of the PDMS without the mold. The designed holes are slightly smaller than the diameter of the droplet. (b) Focal length of the lenses made of silicone oil droplets with different volumes.
The focal length of the lenses is experimentally measured, as shown in Fig.
The droplet lenses inside the solidified PDMS elastomer can be easily deformed by applying a force on the PDMS. Thus, the curvature of the interface of the silicone oil and PDMS can be manipulated. Figure

Fig. 5. (a) Focal length tuning of the lens array. Ray fan diagrams for analyzing the aberration of the lens made of a 6.5 μL droplet (b) without pressure and (c) with 16 N pressure. Blue, 486 nm; green, 588 nm; red, 656 nm.
The aberration for the lens made of a 6.5 μL droplet is calculated by using ZEMAX software based on the profile of the lens, as shown in Figs.
An optical imaging experiment is conducted to evaluate the optical performance of the lens array. The setup of the imaging system is shown in Fig.
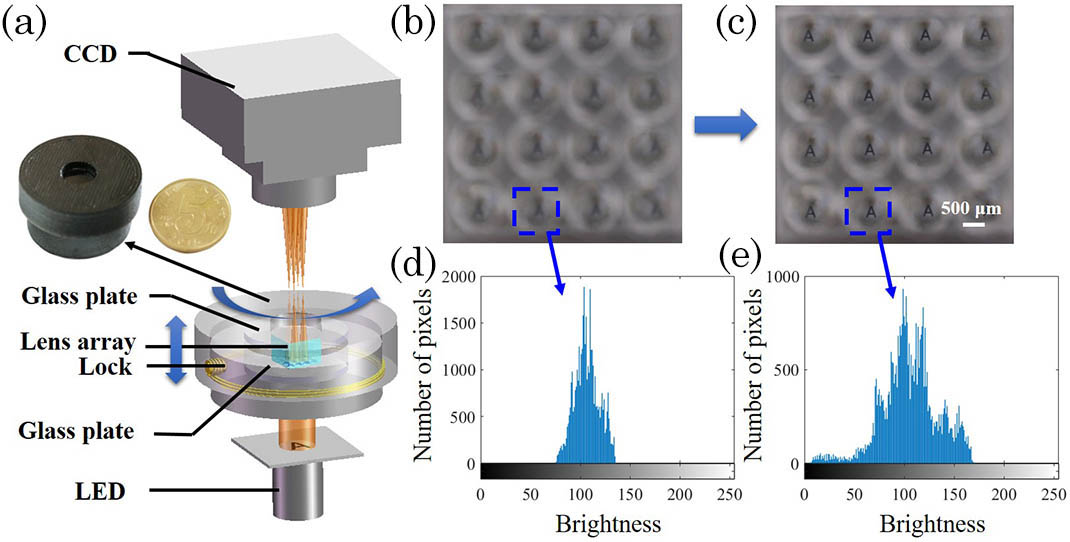
Fig. 6. (a) Imaging system for evaluating the imaging performance of the lens array. Inset: the customized lens mount. The image array of the letters (b) before and (c) after the tuning. The contrast of the image formed by a lens (d) before and (e) after the tuning.
In conclusion, a rapid fabrication technique for producing focal-length-tunable lens array is proposed. High-refractive-index and high-density silicone oil droplets sink to the bottom of liquid-state PDMS and form convex lenses with a curved interface between the silicone oil and the PDMS. The focal length and aperture of the lenses can be controlled by using different-sized silica capillaries to generate the droplets of different volumes. The deviation of the fabrication is less than 6.9%. Furthermore, the solidified PDMS has the property of elastic deformation. By applying an external force vertically on the lens array, the focal length of the lens array could be flexibly extended by about 50%. In the demonstration of optical imaging, the fabricated lens array placed in a customized lens mount is used for focal length tuning, and a clear image array is obtained at the focal plane. The proposed fabrication technique could be an efficient way to produce diverse tunable optical components.
[2] 2HwangS. J.LiuY. X.PorterG. A., Opt. Express21, 30731 (2013).OPEXFF1094-408710.1364/OE.21.030731
[3] 3FengG. H.LiuJ. H., Appl. Opt.52, 829 (2013).APOPAI0003-693510.1364/AO.52.000829
[4] 4KuiperS.HendriksB. H. W., Appl. Phys. A85, 1128 (2004).
[5] 5WangL.HayakawaT.IshikawaM., Opt. Express25, 31708 (2017).OPEXFF1094-408710.1364/OE.25.031708
[6] 6RenH.RenD.WuS., Opt. Express17, 24183 (2009).OPEXFF1094-408710.1364/OE.17.024183
[7] 7RenH.WuS., Opt. Express14, 11292 (2006).OPEXFF1094-408710.1364/OE.14.011292
[8] 8WangL.OkuH.IshikawaM., Opt. Express22, 19448 (2014).OPEXFF1094-408710.1364/OE.22.019448
[9] 9WangL.OkuH.IshikawaM., JPN J. Appl. Phys.56, 122501 (2017).10.7567/JJAP.56.122501
[13] 13ChoiH.WonY., Opt. Lett.38, 2197 (2013).OPLEDP0146-959210.1364/OL.38.002197
[14] 14LiL.LiuC.RenH.DengH.WangQ., Opt. Lett.40, 1968 (2015).OPLEDP0146-959210.1364/OL.40.001968
[18] 18ChoM.DanshpanahM., Proc. IEEE99, 556 (2010).IEEPAD0018-9219
[22] 22PanA.ChenT.LiC. X.HouX., Chin. Opt. Lett.14, 052201 (2016).CJOEE31671-769410.3788/COL
[24] 24PengQ.GuoY.LiuS.CuiZ., Opt. Lett.27, 1720 (2002).OPLEDP0146-959210.1364/OL.27.001720
Bo Dai, Huansi Wang, Qiao Xu, Zhenqing Li, Chunxian Tao, Dawei Zhang. Rapid fabrication of mini droplet lens array with tunable focal length[J]. Chinese Optics Letters, 2018, 16(12): 122201.