激光抛光H13模具钢自由表面演变的数值模拟与验证
下载: 1384次
1 引言
激光抛光是一种新型的抛光技术,与传统的抛光方法相比,其具有非接触、高效率、自动化、清洁环保等诸多优点[1-3]。目前,国内外学者针对工具钢[4-6]、模具钢[7-10]、不锈钢[11-12]、钛合金[13-14]、镍合金[15-16]等金属材料,进行了大量的抛光实验,获得了较好的抛光效果。
激光抛光是通过材料浅表层的熔化实现的,熔池中材料的流动对激光抛光效果具有显著影响。然而,激光抛光过程中熔池材料的流动过程非常复杂,且难以观测。为了研究这一激光抛光过程的核心难题,国内外学者开展了激光抛光的数值模拟研究。如:Mai等[11]建立了二维有限差分热传导模型,用以模拟快速熔化和凝固过程,解决固/液相变中非线性移动边界的问题,得到有效的二维(2D)熔池尺寸;Ukar等[17]建立了三维温度场模型,该模型能用于计算激光抛光过程中不同能量密度下的温度及熔池尺寸。Momin等[18]建立了移动激光下的激光抛光温度场模型,该模型考虑了Marangoni效应对温度场的影响,得到了激光功率和扫描速度对激光抛光温度场的影响。
上述模型仅考虑了激光抛光过程的温度场,能模拟激光抛光过程的温度变化及熔池尺寸的变化,但却忽视了熔池表面形貌的演变过程。Ma等[19-20]建立了二维轴对称瞬态模型,该模型耦合了流动场和温度场,可以模拟激光抛光过程中自由平面在热毛细力下的形貌演变过程,解释脉冲抛光产生额外粗糙度的原因。Shen等[21]建立了二维轴对称瞬态模型,采用该模型模拟了自由平面在激光辐射下产生凸起的过程,分析了毛细力和热毛细力影响表面形貌演变的机制。Zhang等[22]模拟了激光辐射下熔池表面演变的过程,并分析了毛细力和热毛细力对自由表面平滑的作用。
目前,在激光抛光模拟方面的研究主要涉及固定激光束下熔池表面的演变过程,而在移动激光束热源下自由表面形貌的演变规律尚未完善。鉴于此,本文采用数值模拟的方法,研究了移动激光束条件下激光抛光自由表面的演变过程,分析了毛细力和热毛细力对熔池自由表面形貌演变的影响,并与实际抛光实验的熔池、表面粗糙度进行对比,以验证模型的准确性。
2 抛光实验
2.1 实验材料
实验材料为H13热作模具钢。激光抛光前先对样品进行线切割加工,得到表面粗糙度
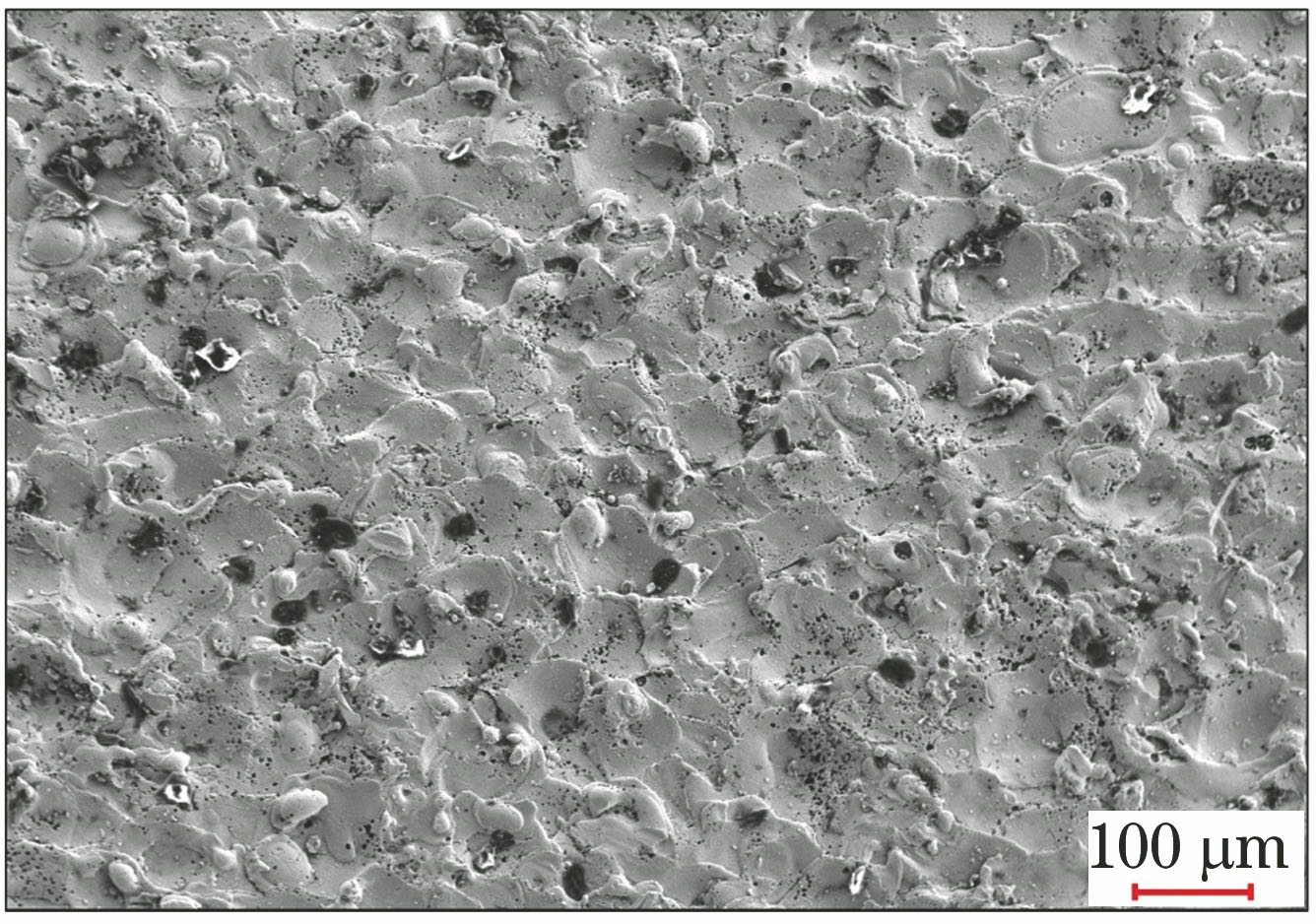
图 1. 线切割加工H13模具钢的表面形貌
Fig. 1. Surface morphology of H13 tool steel after wire-electrode cutting machining
2.2 抛光设备及参数
抛光实验装置如
经过多次实验,最终确定了一组能达到较好抛光效果的抛光参数,如
表 1. 激光抛光参数
Table 1. Laser-polishing parameters
|
2.3 抛光实验结果
抛光后H13钢的表面形貌如
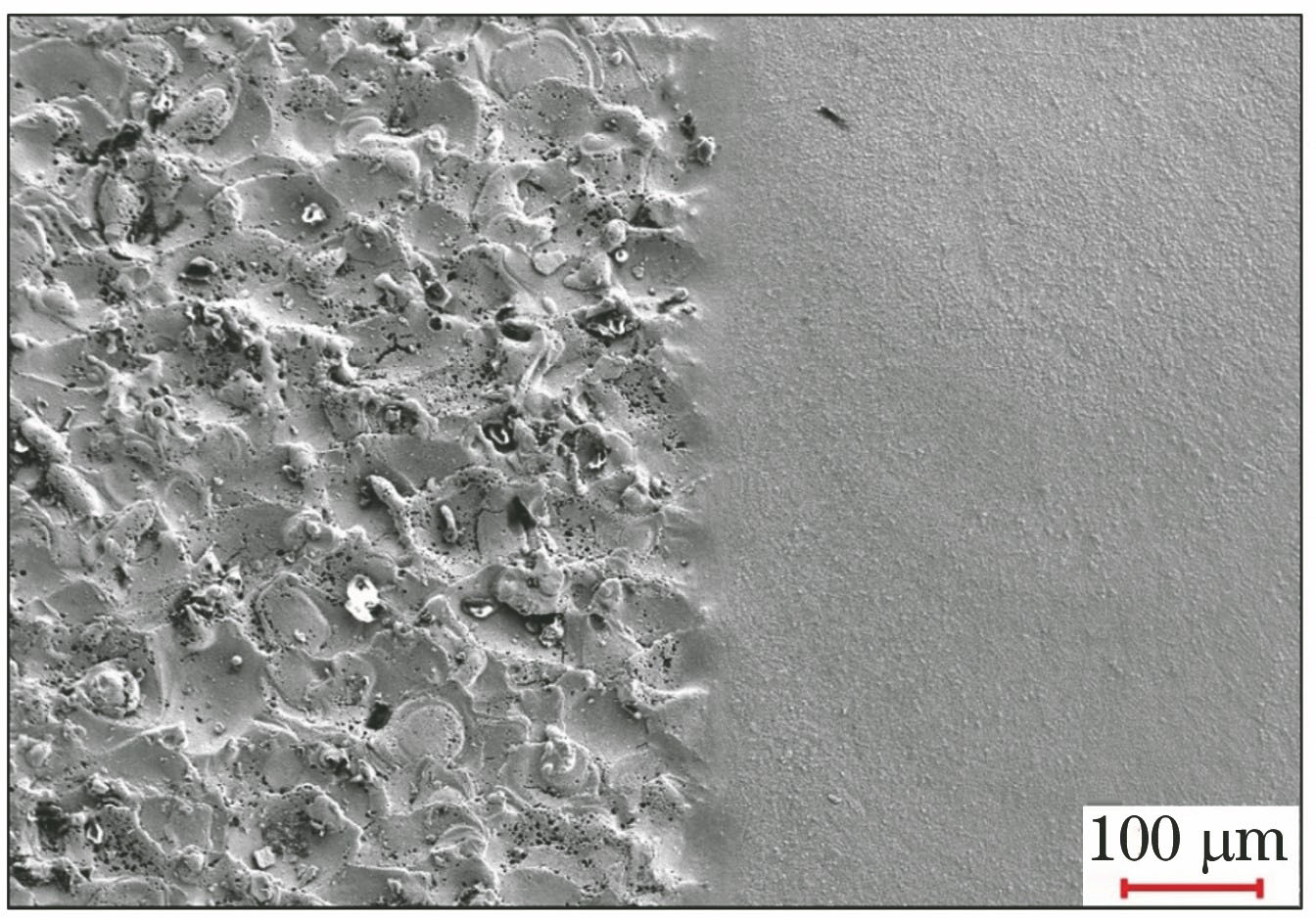
图 3. H13模具钢抛光前(左)和抛光后(右)的表面形貌
Fig. 3. Unpolished (left) and polished (right) surface morphologies of H13 tool steel
测量激光抛光前后的H13模具钢,得到其表面轮廓图,如
采用频谱分析方法对表面轮廓进行分析,得到激光抛光前后的功率谱密度曲线图,如
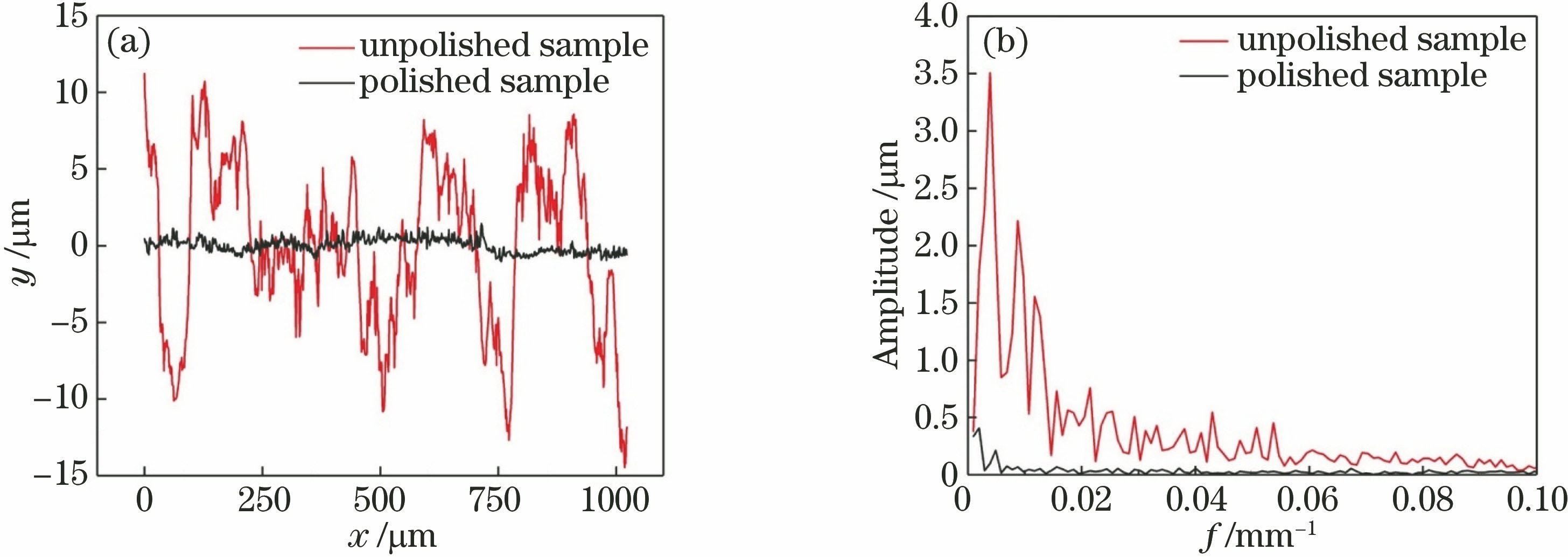
图 4. H13模具钢抛光前后的表面轮廓和频谱图。(a)表面轮廓;(b)频谱图
Fig. 4. Unpolished and polished surface profiles and frequency spectra of H13 tool steel. (a) Surface profiles; (b) frequency spectra
3 数值模型的建立
3.1 模型假设
为了简化计算,结合实际激光抛光过程,对模型做出如下假设:1)材料模型为二维瞬态模型,激光光源在材料表面移动;2)不考虑激光束在金属表面离焦的影响;3)金属处于氩气保护氛围内,不考虑金属的表面氧化;4)金属视为各向同性,材料的热物性参数只与温度有关;5)激光抛光过程仅考虑材料表面的熔化,熔池的最高温度控制在沸点以下,不考虑产生的金属蒸气和等离子效应;6)抛光过程中金属熔体视为不可压缩层流。
3.2 材料属性
本研究所采用的实验材料为H13模具钢。根据假设,模拟过程的热物性参数只与温度有关,其中主要与温度有关的参数为材料密度
在流动模拟中,固液相均使用
抛光过程中,材料在激光辐射下存在固液相转变过程,H13模具钢的熔化过程发生在固相线(
式中:
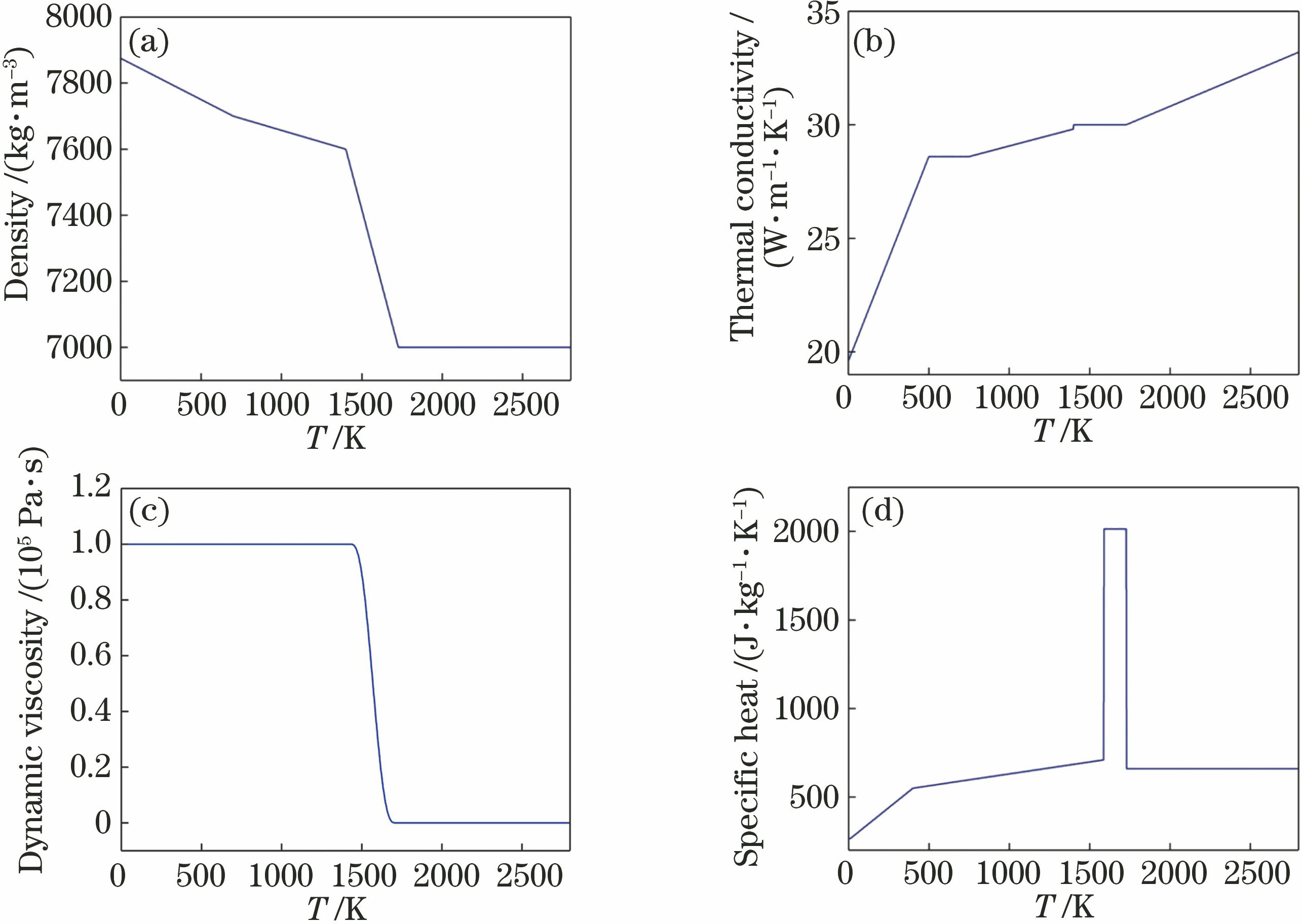
图 5. H13模具钢的热物性参数。 (a)密度;(b)热导率;(c)动力黏度;(d)等效比热容
Fig. 5. Thermophysical properties of H13 tool steel. (a) Density; (b) thermal conductivity; (c) dynamic viscosity; (d) equivalent specific heat capacity
表 2. H13模具钢的材料属性[23-24]
Table 2. Material properties of H13 tool steel[23-24]
|
3.3 控制方程
基于模型的假设条件,在COMSOL软件中设置激光抛光过程的控制方程。温度场控制方程可以表示为
其中,
式中:
熔池为不可压缩的层流,考虑到重力的影响,流动场的控制方程可由(5)式所示的N-S方程以及(6)式所示的连续性方程表示:
式中:
为了模拟流动过程中自由表面的形变过程,模拟过程采用移动网格(ALE)方法,ALE方法是Euler方法与Lagrange方法的结合,既能处理畸变较大的流动,又能准确描述流体内部的运动。流动场自由变形的网格的控制方程[25]可表示为
式中:
3.4 模型初始表面的建立
初始表面的不同会导致抛光结果的不同,故初始表面在模拟中的定义十分重要,仅通过简单的
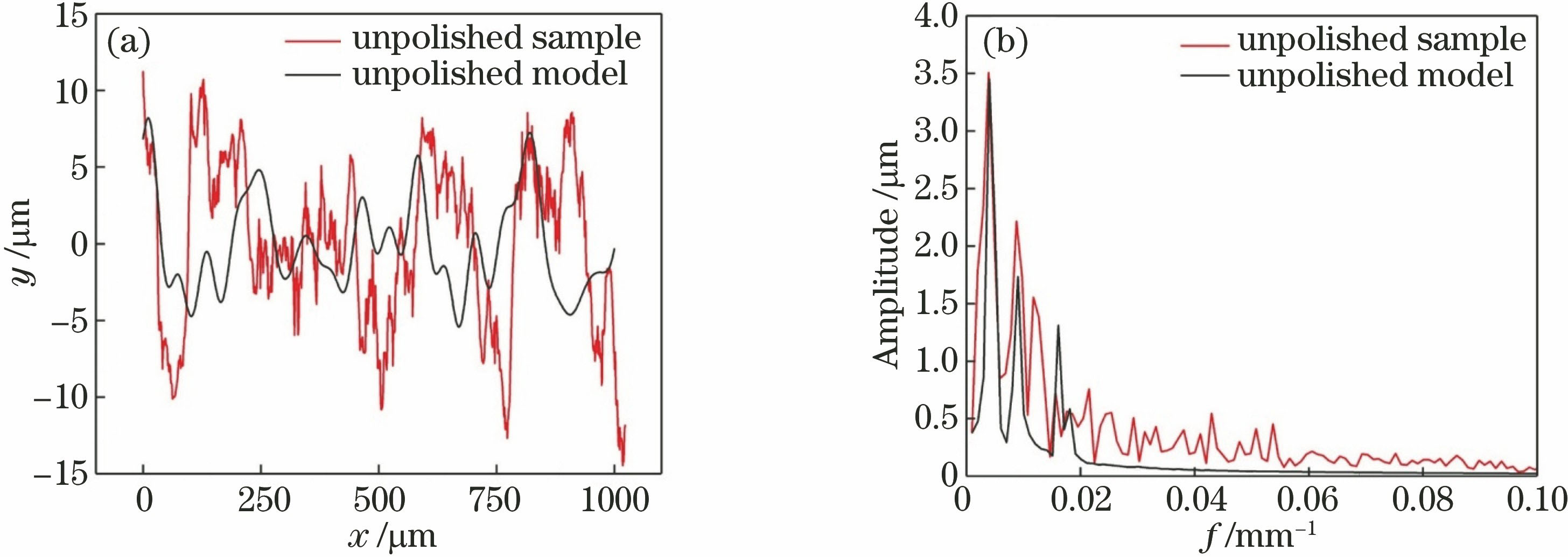
图 6. 模型与样品抛光前的表面轮廓和频谱图。 (a)表面轮廓;(b)频谱图
Fig. 6. Surface profiles and frequency spectra of unpolished sample and model. (a) Surface profiles; (b) frequency spectra
3.5 边界条件
模型的计算域如
边界热源主要包括激光热源、对流换热、热辐射,它们表达式分别为
式中:
式中,
式中:
ALE边界需要考虑不同的边界情况,对于自由表面需要指定法向网格速度,可表示为
式中,
具体各边界条件如
表 3. 边界条件
Table 3. Boundary conditions
|
3.6 网格划分
基于以上控制方程和边界条件,模型采用流动与传热耦合的非等温恒流。模型的网格移动主要发生在自由表面区域,较深的区域不发生形变,综合考虑计算精度和计算速度,在COMSOL软件中,表层熔池网格划分时采用极细化,非熔化区域网格划分采用超细化,具体网格划分参数如
表 4. 网格尺寸
Table 4. Element size
|
4 模拟结果分析
4.1 模拟物理场结果
当激光以300 mm·s-1的速度在样品表面移动照射时,样品表面的温度处于动态变化中,
在
熔池的形成与演变是激光抛光的关键过程,影响液相材料的流动过程与效果,实际抛光过程中捕捉熔池较为困难,通过模拟能更好地观测和分析熔池的形成和演变。
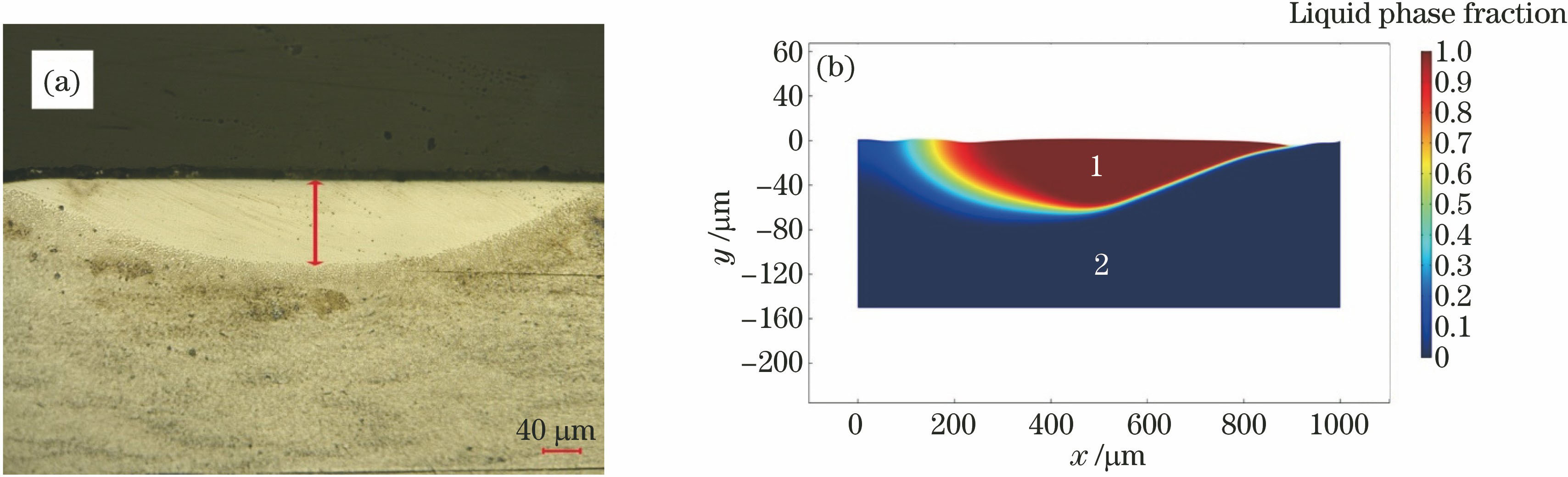
图 9. 实验熔池和模拟熔池。 (a)实验熔池;(b)模拟熔池
Fig. 9. Molten pools in experiment and simulation. (a) Molten pool in experiment; (b) molten pool in simulation
模型为二维模型,主要研究激光扫描方向的表面演变及熔池大小,
在激光抛光过程中,熔池形成后,液相材料的动力黏度变低,能在表面张力的作用下进行流动,流动的情况影响熔池形貌的演变。
当激光继续扫描时,
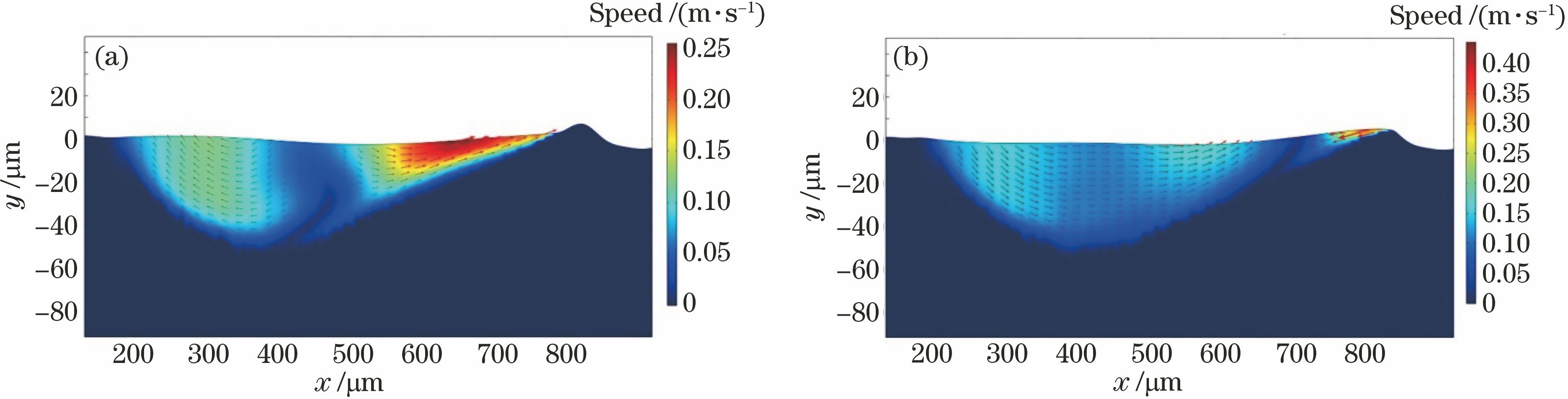
图 10. 局部速度场。 (a)热毛细力主导时的速度场分布; (b)毛细力主导时的速度场分布
Fig. 10. Local velocity fields. (a) Velocity field dominated by thermocapillary forces; (b) velocity field dominated by capillary force
4.2 模型表面轮廓
对抛光后表面轮廓进行频谱分析后可得到功率谱密度曲线,如
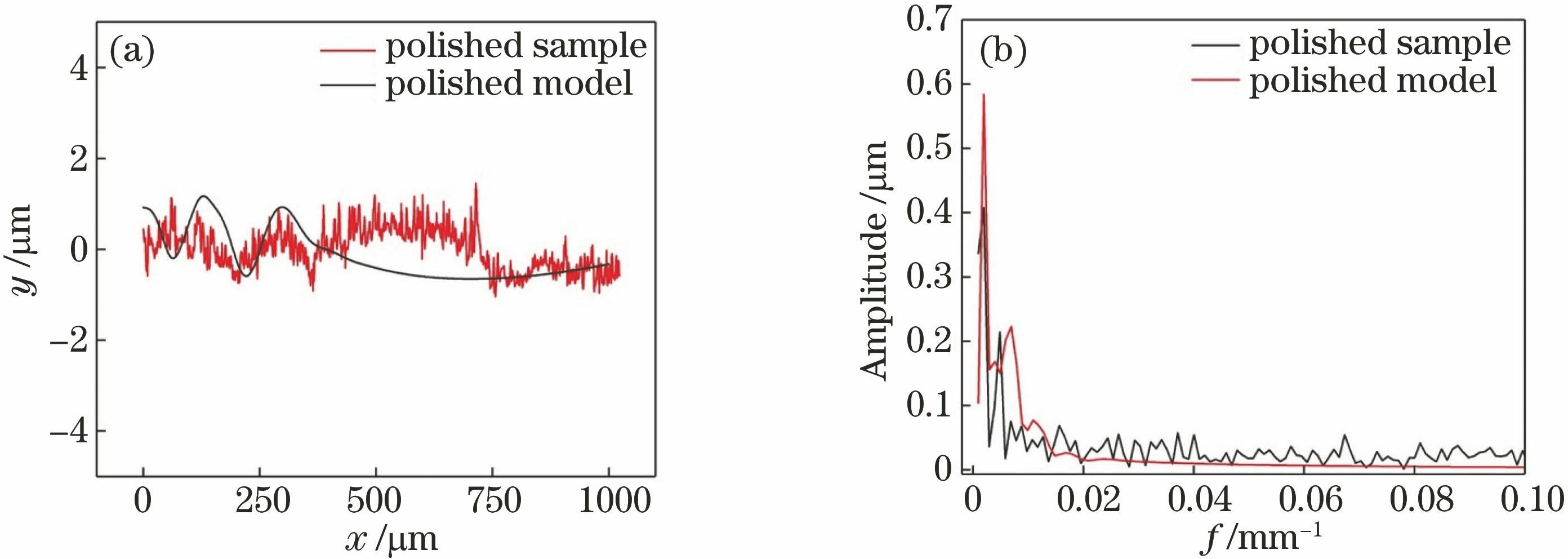
图 11. 抛光后样品及模拟表面的轮廓图和频谱图。(a)表面轮廓;(b)频谱图
Fig. 11. Surface profiles and frequency spectra of polished sample and model. (a) Surface profile; (b) frequency spectra
4.3 激光抛光参数的影响机理
激光抛光过程中的影响因素众多,其中激光功率与激光扫描速度是重要的工艺参数。在模拟过程中改变功率和速度,对模拟结果也有较大影响。
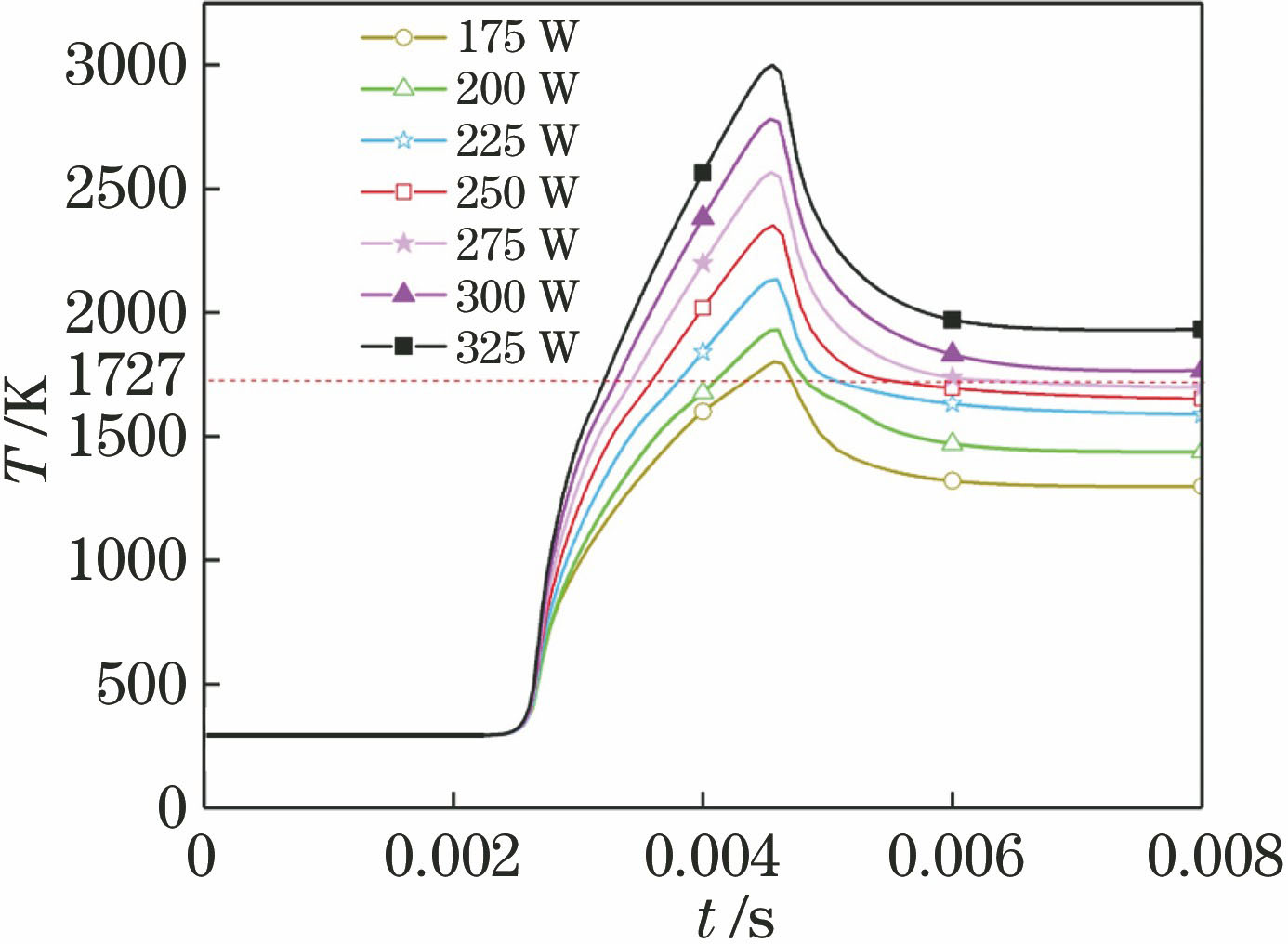
图 12. 不同功率下表面x=500 μm处的温度曲线
Fig. 12. Temperature curves at x=500 μm of surface under different laser powers
改变模型的激光功率,可以得到不同功率下的熔池深度和表面粗糙度,统计结果如
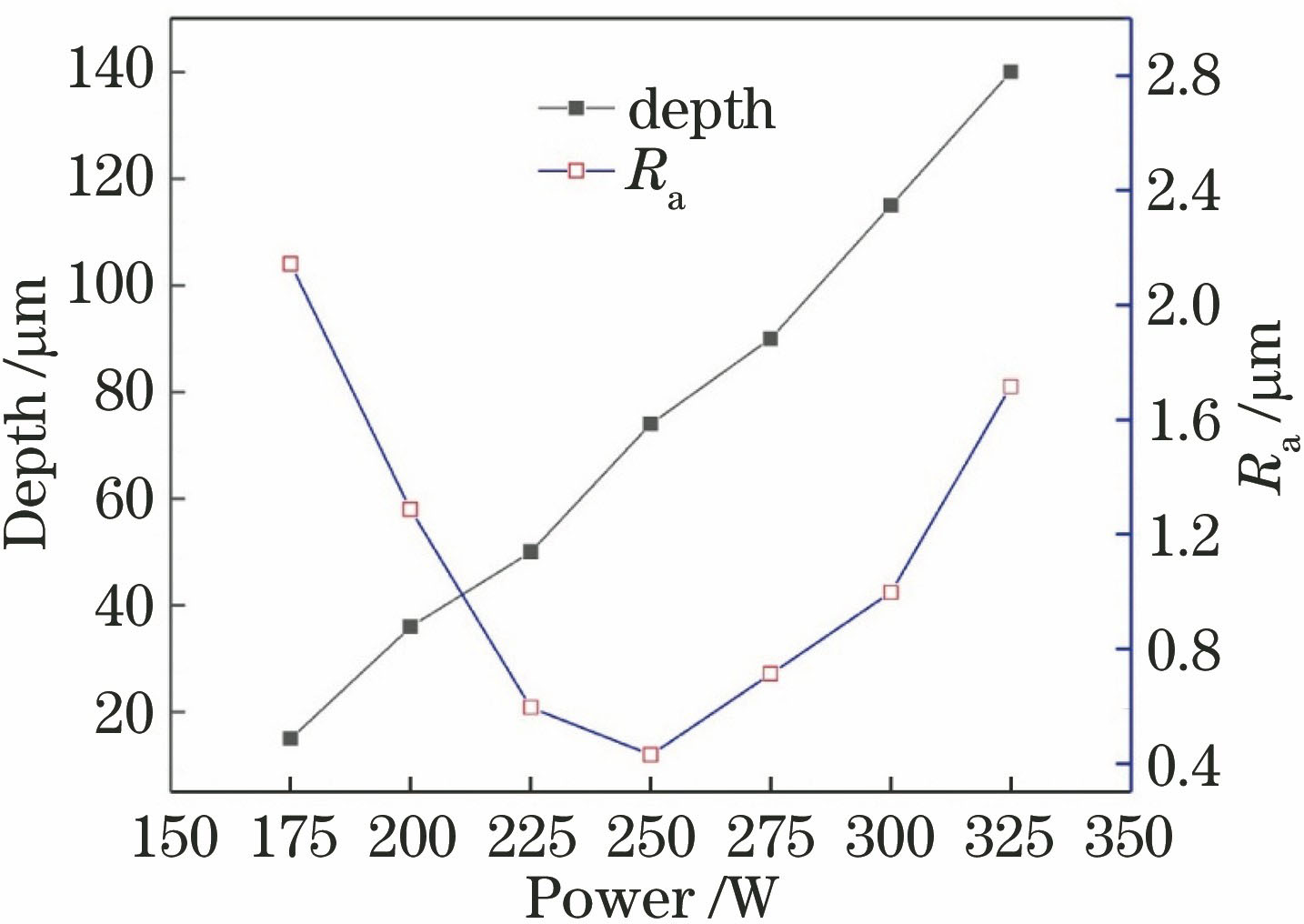
图 13. 不同功率下的熔池深度和表面粗糙度
Fig. 13. Depth of molten pool and surface roughness under different laser powers
基于不同功率下的表面流动场分布来分析表面粗糙度与功率的关系。当功率为175 W时,熔池深度为15 μm左右。随着激光光源的移动,当时间为0.00312 s时,如
当功率为300 W时,熔池深度达到110 μm。当时间为0.00226 s时,初始粗糙表面在毛细力作用下已经变得平滑,如
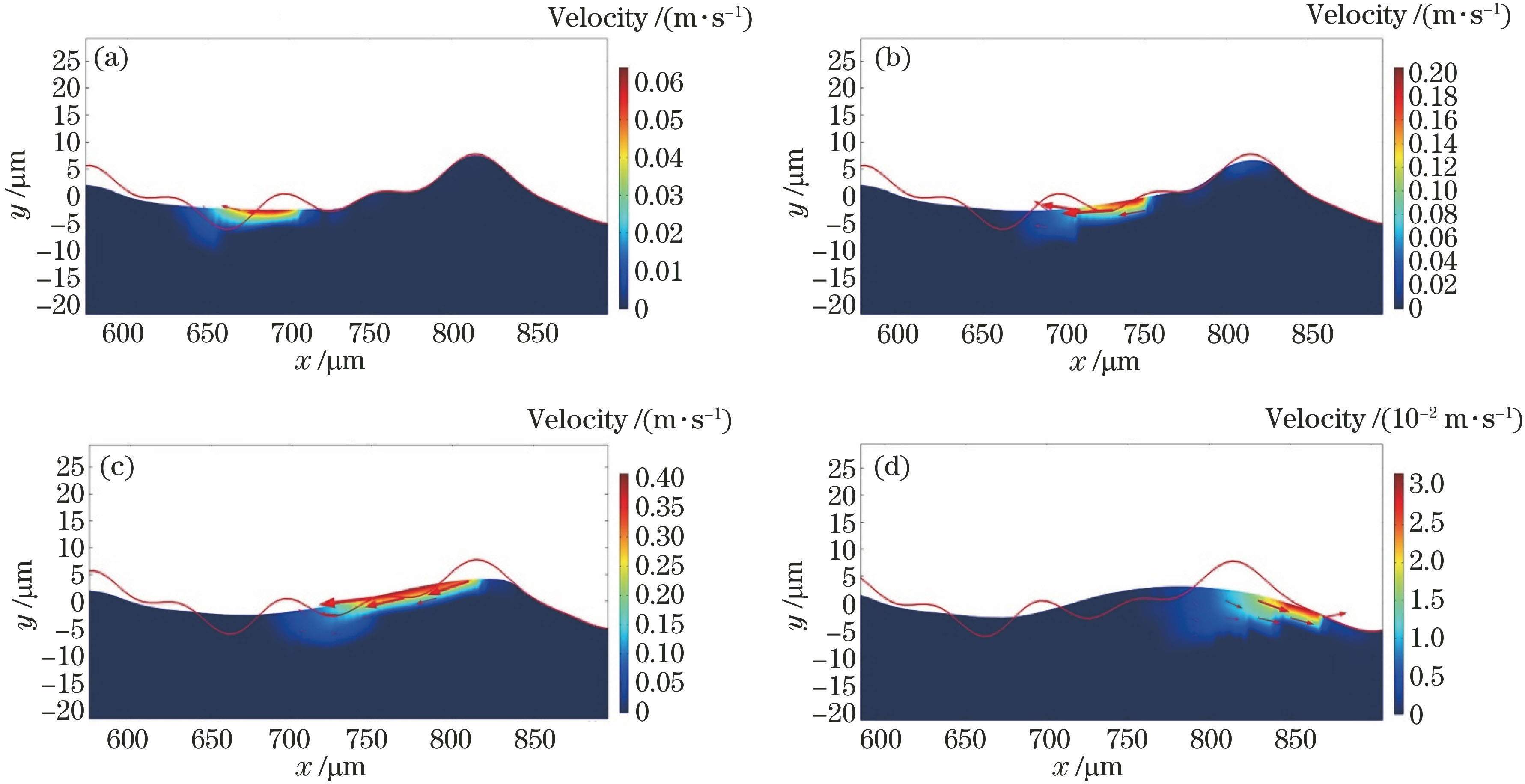
图 14. 175 W功率下不同时刻的局部速度场。(a) t=0.00312 s;(b) t=0.00322 s;(c) t=0.0033 s;(d) t=0.00355 s
Fig. 14. Local velocity fields at different moments under laser power of 175 W. (a) t=0.00312 s; (b) t=0.00322 s; (c) t=0.0033 s; (d) t=0.00355 s
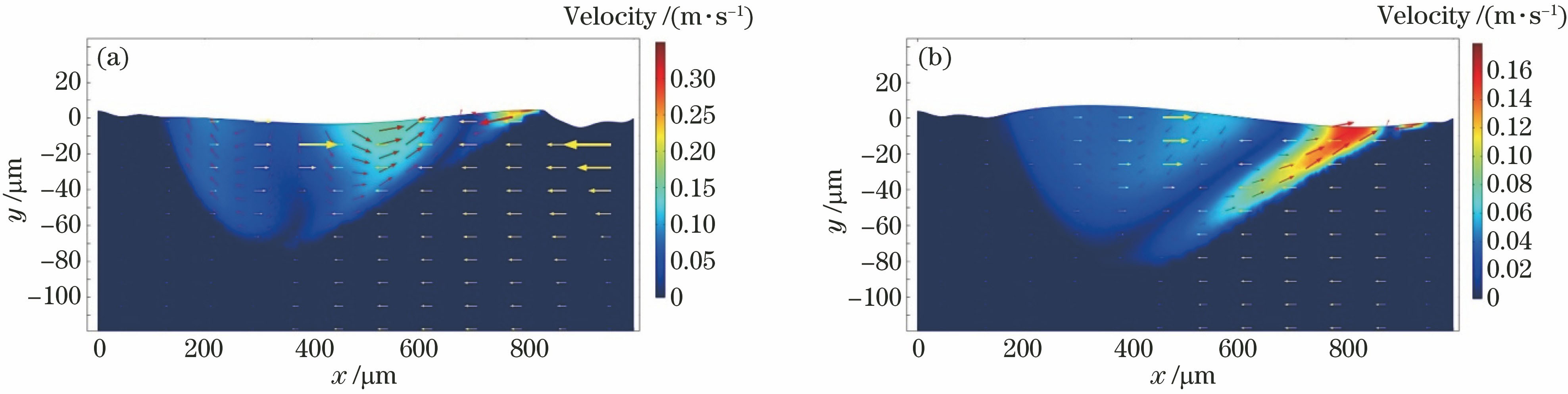
图 15. 300 W功率下不同时刻的局部速度场。(a) t=0.00226 s;(b) t=0.00267 s
Fig. 15. Local velocity fields at different moments under laser power of 300 W. (a) t=0.00226 s; (b) t=0.00267 s
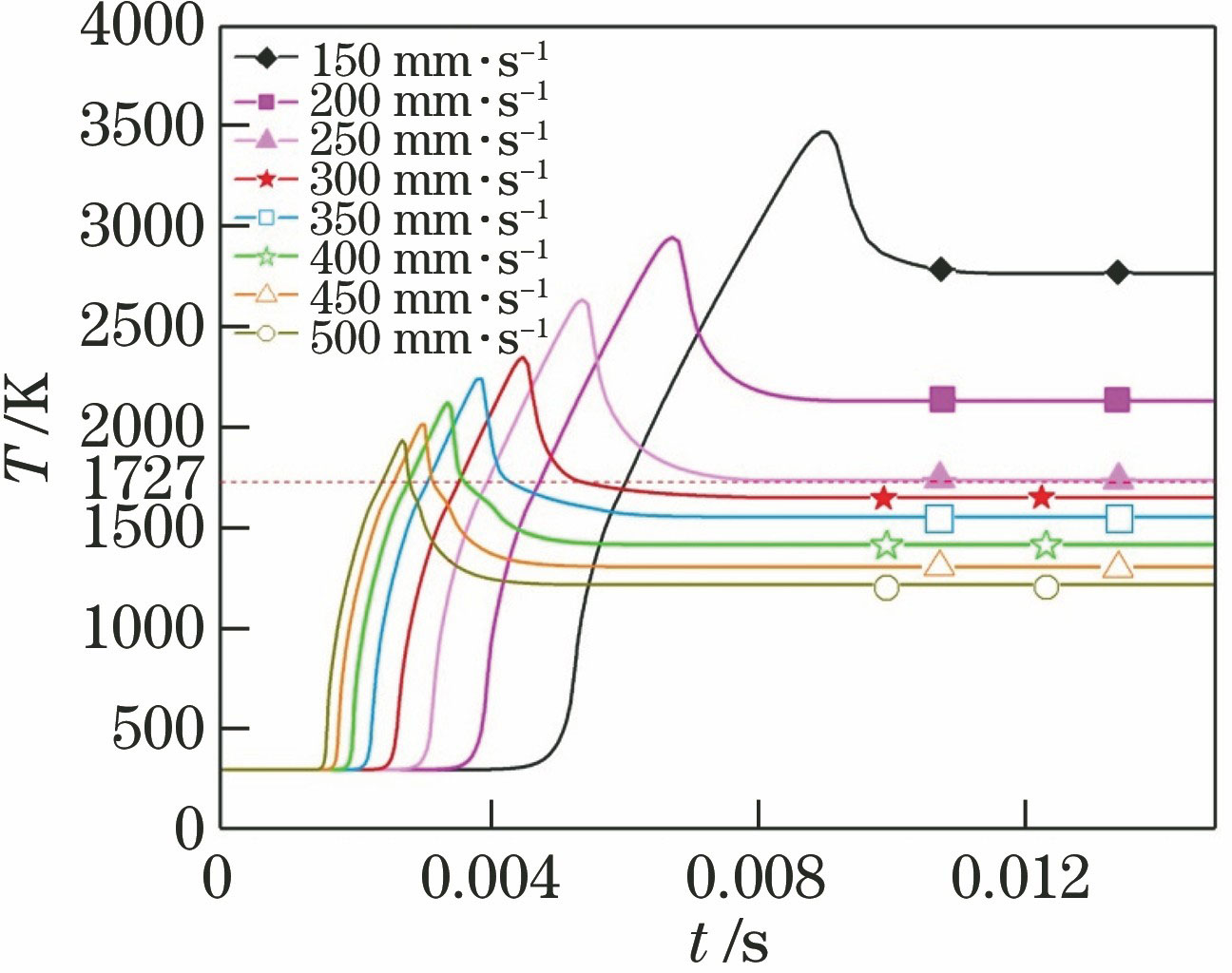
图 16. 不同扫描速度下表面x=500 μm处的温度曲线
Fig. 16. Temperature curves at x=500 μm of surface under different scanning velocities
改变激光扫描速度,统计不同速度下熔池的深度和抛光后的表面粗糙度,结果如
表面粗糙度与扫描速度的关系也成U型关系。其原理与功率对表面粗糙度的影响机理类似。当扫描速度较小时,单位区域的热输入较大,形成的熔池的持续时间长,粗糙表面在表面张力作用下平滑后熔池仍然存在,此时熔池内温度梯度占据主导,熔池中心的熔体流向边缘,导致边缘材料累积,凝固后形成新的不平整表面,导致额外粗糙度的产生。当扫描速度较大时,样品表面的熔池持续时间短,凸起的材料没有充分的时间进行流动而凝固,造成不理想的抛光效果。
综合上述激光功率、扫描速度对抛光结果的影响可知,在抛光过程中,需要合理控制热输入,过低的热输入导致熔池持续时间短,粗糙的表面流动时间不充足,抛光效果不理想;而过大的热输入导致熔池持续时间长,已平滑的熔池表面在热毛细力作用下形成新的不平整表面,导致额外粗糙度的产生。

图 17. 不同扫描速度下的熔池深度和表面粗糙度
Fig. 17. Depth of molten pool and surface roughness under different scanning velocities
5 结论
在多物理场耦合软件COMSOL中,以移动激光束为热源,利用实际自由表面频谱构建模拟表面,耦合激光抛光过程中的流动场和温度场,综合考虑毛细力和热毛细力的共同作用,建立了激光抛光的二维瞬态模型,模拟了激光抛光过程材料表面形貌的演变过程。主要得到以下结论:1)通过合成构建了模型的初始表面,该表面可以有效地呈现实际的表面轮廓。2)当熔池的表面曲率较大时,毛细力占主导作用,波峰材料流向波谷,当熔池平滑后,温度差导致的热毛细力占主导作用,熔池中心的材料流向边缘。3)过小的激光功率或过大的速度会导致热输入不足,粗糙的材料表面没有足够的时间流动,会而产生较差的抛光效果;而过大的激光功率或过小的速度则会导致热输入过量,熔池持续时间过长,材料流向熔池边缘,产生额外的粗糙度。4)表面粗糙度的模拟结果与实验结果之间的误差为7.4%,熔池深度误差为7.5%,误差都小于8%,表明建立的模型具有较高的精度。
所建模型为二维模型,下一步将建立三维模型,以便能够模拟出激光光斑直径等参数的影响,并将其用于实际抛光工艺的选取,提高抛光的效率和精度。
[1] 黄加福, 魏昕, 谢小柱, 等. 影响激光抛光效果的因素分析[J]. 激光与光电子学进展, 2008, 45(12): 20-24.
[2] Bordatchev E V. Hafiz A M K, Tutunea-Fatan O R. Performance of laser polishing in finishing of metallic surfaces[J]. The International Journal of Advanced Manufacturing Technology, 2014, 73: 35-52.
[3] 戴伟, 郑志镇, 李建军, 等. 金属材料表面的激光抛光研究进展[J]. 激光与光电子学进展, 2015, 52(11): 110001.
[4] Lamikiz A, Sánchez J A. López de Lacalle L N, et al. Surface roughness improvement using laser-polishing techniques[J]. Materials Science Forum, 2006, 526: 217-222.
[5] Ukar E, Lamikiz A. López de Lacalle L N, et al. Laser polishing of tool steel with CO2 laser and high-power diode laser[J]. International Journal of Machine Tools and Manufacture, 2010, 50(1): 115-125.
[7] Brinksmeier E, Riemer O, Gessenharter A, et al. Polishing of structured molds[J]. CIRP Annals, 2004, 53(1): 247-250.
[10] Miller J D. Tutunea-Fatan O R, Bordatchev E V. Experimental analysis of laser and scanner control parameters during laser polishing of H13 steel[J]. Procedia Manufacturing, 2017, 10: 720-729.
[16] Perry T L, Werschmoeller D, Duffie N A, et al. Examination of selective pulsed laser micropolishing on microfabricated nickel samples using spatial frequency analysis[J]. Journal of Manufacturing Science and Engineering, 2009, 131(2): 021002.
[17] Ukar E, Lamikiz A. López de Lacalle L N, et al. Thermal model with phase change for process parameter determination in laser surface processing[J]. Physics Procedia, 2010, 5: 395-403.
[21] Shen H, Pan Y Q, Zhou J, et al. Forming mechanism of bump shape in pulsed laser melting of stainless steel[J]. Journal of Heat Transfer, 2017, 139(6): 062301.
[22] Zhang C, Zhou J, Shen H. Role of capillary and thermocapillary forces in laser polishing of metals[J]. Journal of Manufacturing Science and Engineering, 2017, 139(4): 041019.
[23] Mohajerani S, Miller J D. Tutunea-Fatan O R, et al. Thermo-physical modelling of track width during laser polishing of H13 tool steel[J]. Procedia Manufacturing, 2017, 10: 708-719.
[24] 袁章福, 柯家骏, 李晶. 金属及合金的表面张力[M]. 北京: 科学出版社, 2006: 22- 23.
Yuan ZF, Ke JJ, LiJ. Surface tension of metals and alloys[M]. Beijing: Science Press, 2006: 22- 23.
[25] Carin M. Square drop oscillation under surface tension 2D axisymmetric model[EB/OL]. ( 2014-05-27)[2018-12-01]. https:∥www.comsol.fr/community/exchange/121/.
Article Outline
张伟康, 戴伟, 郑志镇, 李建军, 邓湉湉. 激光抛光H13模具钢自由表面演变的数值模拟与验证[J]. 中国激光, 2019, 46(7): 0702002. Weikang Zhang, Wei Dai, Zhizhen Zheng, Jianjun Li, Tiantian Deng. Numerical Simulation and Verification of Free-Surface Evolution in Laser Polishing of H13 Tool Steel[J]. Chinese Journal of Lasers, 2019, 46(7): 0702002.