基于宏微复合标定的跨尺度零件测量方法
Complex parts in the aerospace field need to deal with high temperature, high pressure, high speed and complex electromagnetic environment, and other new service environments, parts usually need to design some precision microstructures such as micropores to bear the function of heat dissipation and pressure resistance, which puts forward extremely high requirements for the manufacturing accuracy of the parts themselves, and also requires the measurement equipment to take into account the dimensional accuracy and positioning accuracy of the parts. At present, the measurement technology of multiple sensor combinations is mainly adopted, and the macro and micro feature data is obtained by using the measurement characteristics of each sensor, and finally the data is registered and fused or three-dimensional stitching, the main registration fusion method is to downsample the microscale measurement data of high-precision large data and upsample the large-scale measurement data with relatively low accuracy and small data volume, and finally make the data of these two scales achieve similar accuracy to register them, but this method does not form a more correct and mature method in the upsampling process, which makes the accuracy of upsampling unsatisfactory, resulting in doubts about the correctness of the final result. In addition, the current multi-sensor integration method is mostly limited to sensors of similar scale, so this paper proposes an integrated calibration method between sensors with large scale differences, which can overcome the problem of coordinate integration difficulties caused by the difference in accuracy and resolution between sensors, and use typical aerospace parts for measurement verification, which proves that this method can be effectively applied to such parts with cross-scale structural features.
By preliminarily establishing a model of multi-sensor combination measurement to derive the coordinate system conversion closed loop, due to the relative position of the probe and the microscope camera is constant, which is the invariants in the closed loop and the key link to complete the accuracy conversion in the conversion closed loop. This paper innovatively uses a special calibration block as a transit target to calibrate this conversion relationship, this calibration block is designed and processed from the perspective of controlling the accuracy of coordinate conversion, it contains sixteen macro feature points and eight micro feature points, because the field of view of zoom scanning microscopy equipment is extremely small, and calibration requires at least six feature points to be set in such a field of view, so this paper designs such a microstructure into a square groove structure, using its corner points as marker points, This also facilitates the search for more accurate feature point coordinates in microscopic reconstruction results. In addition, silicon is used for the processing of this calibration block, so that the tiny square groove structure can be precisely machined. Finally, the above coordinate transformation relationship is solved by a relatively simple quaternion method, that is, the calibration of the geo-coordinate system of two sensors of different scales is completed.
Using the above model and the fixed conversion relationship solved by the calibration method proposed in this paper, the data of each local measurement can be converted to the same coordinate system. The experiment in this paper chose an injector, a space cross-scale part with a conical surface. There are 12 holes with a diameter of about 0.5 mm evenly distributed above, measure them one by one while using a binocular camera to record the global control points distributed on the microprobe during each measurement, use these global control points to calculate their conversion relationship to the binocular system, and then the pose matrix represented by the left multiplication calibration result can obtain the conversion relationship from a specific point to the global coordinate system, respectively apply the conversion relationship to the measurement results of specific points (represented as point cloud datasets), you can obtain each local area data with the same coordinate system, and make them a simple collection to obtain a complete high-precision large-scale topography dataset. The central coordinates of each hole on its surface and the direction vector of each hole axis are obtained by solving some processing algorithms, because these quantities can accurately represent the positioning accuracy of holes, compare them with the theoretical model to obtain error values, and then compare the error values with the processing accuracy of parts, which can verify the final accuracy of the measurement method and the degree of improvement of accuracy. The final result is that the central coordinate error is 0.029 mm, the axial error of the hole is 0.1140°, which is greatly improved compared with the central coordinate error of 0.05 mm and the axial error of the hole of 0.167° in the machining accuracy requirements, in addition, the results of this paper are more accurate than the scanning results of the single-scan measuring instrument Gocator sensor.
In this paper, a cross-scale measurement method based on macro-micro composite calibration is proposed for precision three-dimensional optical measurement of parts with cross-scale micro-nano structure, which takes into account the accuracy difference of macro-micro measurement equipment and the integrity and correctness of microscopic raw data, and completes the conversion relationship and accuracy transition of the global model of the binocular-microscopic combined measurement system by designing and precision processing the macro-micro composite calibration block, so as to realize the global calibration of cross-scale measurement equipment. By comparing with the roundness and flatness of the center point set of each hole in the theoretical model to analyze the splicing accuracy, it is concluded that the roundness error of the coordinate distribution of the hole surface of the microhole is 0.0438 mm and the flatness error is 0.0252 mm, and the positioning accuracy of the parts measured by this method is analyzed by comparing with the position of each hole center pose in the theoretical model, and the point error value is less than 0.029 mm and the axial error is less than 0.1140°. The experimental results show that compared with direct measurement methods such as surface structured light, this measurement method has the advantages of higher accuracy and more accurate morphology reconstruction, and is suitable for the measurement of microstructure, topography, dimensional accuracy, and positioning accuracy of a type of cross-scale parts.
1 引言
航空航天领域的复杂零件需要应对高温、高压、高转速,以及复杂电磁环境等新型服役环境,这对零件自身的制造精度提出了极高的要求。以航空燃气发动机涡轮叶片为例,为应对高温环境,目前常用的气膜冷却技术是在发动机叶片表面设计气膜孔,使叶片内外形成热循环以提升叶片的冷却性能[1],气膜孔按照设计的排布尺寸分布于叶片表面,其尺寸精度以及定位精度均会影响涡轮叶片的冷却性能[2]。跨尺度零件是指具有微孔、沟槽等微尺度特征结构的整体尺寸较大的零件,该类零件的加工精度和测量精度一般要求在微米级,微尺度结构尺寸在毫米级,零件整体尺寸在米级,由于它们的测量要求通常包含微尺度结构的尺寸精度及其定位精度,因此要想提高测量的效率就需要提供一种能够同时满足多个尺度测量需求的测量方法。为了满足精度、分辨率、视场不同情况下的跨尺度测量要求,目前主要采用多个传感器组合的测量技术[3],利用各个传感器的测量特点分别获取宏微特征数据,最后对数据进行配准融合或事先标定好各传感器的空间位姿,通过该位姿实现数据的三维拼接。
目前对多尺度点云数据进行配准融合一般采用以下方法:对高分辨率高数据量的微尺度数据进行下采样处理,同时对低数据量的大尺度数据进行上采样处理,最后对两种数据进行配准融合。该方法衍生出多种点云下采样技术如基于分形维数表征和基于离散小波变换的技术,以及多种点云上采样技术如基于深度学习和基于多项式插值的技术,但在点云上采样领域采用的方法尚不成熟,原始数据传递的正确性存疑[4]。而要想实现三维数据的自动拼接,各传感器空间位姿的标定是最重要的步骤,目前有以下常用的标定方法:使用各传感器测量同一个特征如标准球[5]、环规标准器[6]、精密球板阵列[7]等,再解算各传感器坐标系间的转换关系以统一全局坐标系,但这些集成方法要求每个测头都测量大量重合点或相同特征,故当各传感器的测量原理相差较大时,这类集成方法将无法实现;Wen等[8]提出一种配准方法,通过设计特殊的几何体组合标准器,利用传感器各自测量特性测量不同的特征,从而对多个测头进行坐标统一,该方法适用于测量特性相差较大的多传感测量场合,但这种组合标准器的特征尺度差异较小,对于尺度差异较大的场合,它的精度会迅速下降甚至方法本身失效。综上,对于米级宏结构,毫米级微结构和微米级精度组合的跨尺度测量场合,目前特别缺少能够准确实现多传感器标定的方法。
针对以上方法的局限性,本文提出一种基于宏微复合标定的跨尺度零件测量方法,通过设计同样具有宏微结构特征的标定块,建立中转坐标系同时完成不同尺度下精度的过渡,最后解算出宏微尺度转换中的关键位姿,实现局部区域测量点云的全局拼接。本文以火箭推力室喷注器为检测对象,利用变焦扫描显微系统[9]获取各喷注孔三维形貌点云数据,对其应用所提方法解算出转换关系,进而实现所有局部数据的统一,最后得到喷注孔圆阵列整体形貌数据集,实现零件尺寸精度和定位精度的测量。
2 基本原理
2.1 宏微复合标定及测量模型
所提测量模型中包含变焦扫描显微镜和双目立体视觉两个传感器。其中:变焦扫描显微镜的基本原理是通过光栅尺记录相机垂直位置,利用超声电机垂直移动相机对零件表面由下至上采集阶梯图像组,随后对每张图像进行聚焦评估并提取其中的对焦像素点,最后依据记录的垂直位置重建出零件的三维形貌点云;双目立体视觉的作用主要是重建各种标志点[10],其基本原理是利用两台工业相机的光心与被测物体构成的三角形,通过三角视差原理,对目标进行三维信息的计算获取,最后采用圆轮廓提取算法提取出圆标志点的圆心三维坐标。显微测量系统采用数值孔径(NA)为0.1、放大倍率为4×、分辨率为2.75 µm的显微物镜[11]和分辨率为2448×2048、水平像素为3.45 µm、垂直像素为3.45 µm的工业相机,经由系统光路,相机视场将被修正为2 mm×2 mm,系统超声电机的垂直距离为0.001~10 mm,系统超声电机的垂直距离为0.001~10 mm。该系统最终重建出的点云数据横向分辨率为1.86 µm,纵向分辨率为3.58 µm,系统测量的整体精度为0.12 µm,整个系统由Universal机器人搭载。双目测量系统采用两个同样配置的工业相机,整个系统视场为1.5 m×1.5 m×1.5 m,搭建系统后需要对其进行标定[12]。
依据所面对的跨尺度测量场景的要求,组合式测量模型的基本思路是将变焦扫描显微系统在各不同位置测量重建出的点云坐标系转换至双目坐标系下,实现这些点云坐标系的统一从而完成全局拼接[13],这种转换的前置条件是可求解点云坐标系与变焦扫描显微设备坐标系(即其上设置的全局控制点建立的坐标系)之间的关系,而由于点云坐标系为虚拟坐标系,并且变焦扫描显微镜无法测量自身设备上的控制点,所以该转换关系无法通过实时测量直接获得。因此本文建立了特殊的组合式标定模型,这种模型涉及视场、精度和分辨率相差较大的两种传感器的集成,在该标定模型中设计加工了特殊的标定块,将其物体坐标系作为中转坐标系,以求解上述转换关系。
根据组合式测量系统中显微和双目系统的视场特点,该标定块需要包含毫米级视场(2 mm×2 mm×2 mm)以内的微结构以及米级视场(1.5 m×1.5 m×1.5 m)以内的宏结构。由于变焦扫描显微测量设备的重建结果是零件表面形貌的三维点云[14],这要求标定块上需要包含多个容易准确选取的点,这些点将对应于数模中的特征点,因此可以考虑将这些点设计为圆心和角点,此外考虑到显微视场较小,使用圆心作为特征点要求加工出多个圆柱结构如微孔,这将会大大提高加工难度,而使用方槽结构则可以在有限的空间中提供多个角点,因此最终将标定块的微结构特征设计为方槽。而对于双目系统,其视场较大,并且识别圆轮廓比识别角点要更加准确[15],因此将标定块的宏结构特征设计为圆孔阵。该宏微复合标定块的整体加工精度以微结构精度为基准,由于数控机床精加工对圆角的依赖性,故将标定块整体加工材料设置为硅材,微结构部分采用刻蚀加工。标定块特征点数量及其分布将结合其对坐标转换精度的影响设计。由以上建立组合式标定模型及其坐标转换闭环,如
该测量模型包含4个坐标系和5组靶标点,将宏结构在自身数模坐标系{M}下的点集表示为
在实际测量场景中,变焦扫描显微设备外壳与其中的显微相机之间位姿相对固定,测量零件表面形貌时,显微相机每像素实际距离固定且由于显微镜焦深是设备的固有参数,所以物镜工作距离固定,设备上的控制点建立的坐标系与变焦扫描显微法重建出的物体三维形貌点云坐标系的转换关系也是固定的。因此,可以通过求解闭环模型中另一个路径的所有相邻点集间的转换关系推导得出该转换关系,将其表示为位姿
随着机器人引导显微系统移动,全局控制点相对于固定的双目系统位置变化,全局控制点坐标系和双目坐标系之间的转换关系也会变化,因此全局控制点每移动到一个新位置都会对应一组新的位姿。将标定过程中全局控制点的位置作为其初始位置,此时用双目相机采集控制点,重建得出每个控制点的圆心坐标,将其记为点集
由数模坐标的整体性可以整合点集
在测量跨尺度零件的过程中,双目相机和待测零件及转台始终固定在原地,显微相机由机器人驱动对微尺度特征进行逐一测量,根据跨尺度零件宏微结构尺寸以及所使用的变焦扫描显微测量系统的视场将待测的跨尺度零件划分成
当变焦扫描显微系统移动到第
接着对该区域局部测量重建出的三维点云
2.2 绝对定向问题求解
摄影测量相关实验和应用表明单位四元数具有约束条件少以及对初值精度依赖性小的特点[17],因此本文采用单位四元数法解算任意两组拥有一一对应特征点的点集。在组合式系统标定模型中,这种问题存在于双目左相机坐标系与数模坐标系和显微相机坐标系与数模坐标系的转换关系求解中。
设其中转换目标坐标系中特征点坐标为
将其表示为四元数:
在
将
根据四元数矩阵形式转换法则可将上式等价为
该矩阵可由各点集内点的坐标计算获得,假设实对称矩阵
2.3 坐标转换精度与标定块设计
在以上问题的三维坐标转换模型中,将特征点坐标
设特征点设置个数为n,将上式表示为
利用整体最小二乘法对转换参数
由估值计算转换参数方差阵可得
则点
点
根据以上精度分析,并且考虑到双目系统在实际重建时存在的部分特征点轮廓不明显导致无法重建的问题,本文测量模型中标定块和全局控制点个数设置为16,重建时选取其中重建成功、测量误差较小且分布较为分散的8个点,微结构的特征点个数设置为8。经设计,本文采用的宏微复合标定块的结构包括刻蚀加工的微型方槽,该结构为深0.5 mm的边长0.5 mm的正方形到标定块上表面的质心平面坐标与其相同的边长为1.5 mm的正方形的放样,此外标定块还包含直径15 mm的16个盲孔组成的无规律孔阵,则该宏微复合标定块包含16个宏结构特征点和8个微结构特征点,宏微结构分别作为双目相机和变焦扫描显微相机标定时的测量对象,标定块模型如
3 实验与分析
3. 1 组合式系统搭建与标定实验
依照
表 1. 宏微复合标定块特征点坐标
Table 1. Macro-micro composite calibration block feature point coordinates
|
表 2. 重建特征点坐标
Table 2. Coordinates of reconstructed feature points
|
选取对应点集建立绝对定向问题模型,利用
其次选取
最后选取
利用
3.2 喷注孔圆阵列拼接实验
本文以某航天喷注器为实验对象,喷注器正面整体图像如
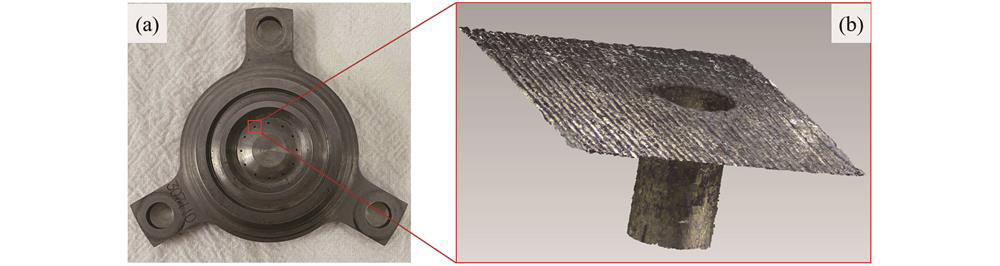
图 5. 喷注器及局部测量结果:(a)喷注器表面;(b)喷注孔点云数据
Fig. 5. Injector and local measurement results: (a) Injector surface; (b) injection hole point cloud data
实验使用的变焦扫描显微形貌测量仪测量视场为1.5 mm×2 mm,如
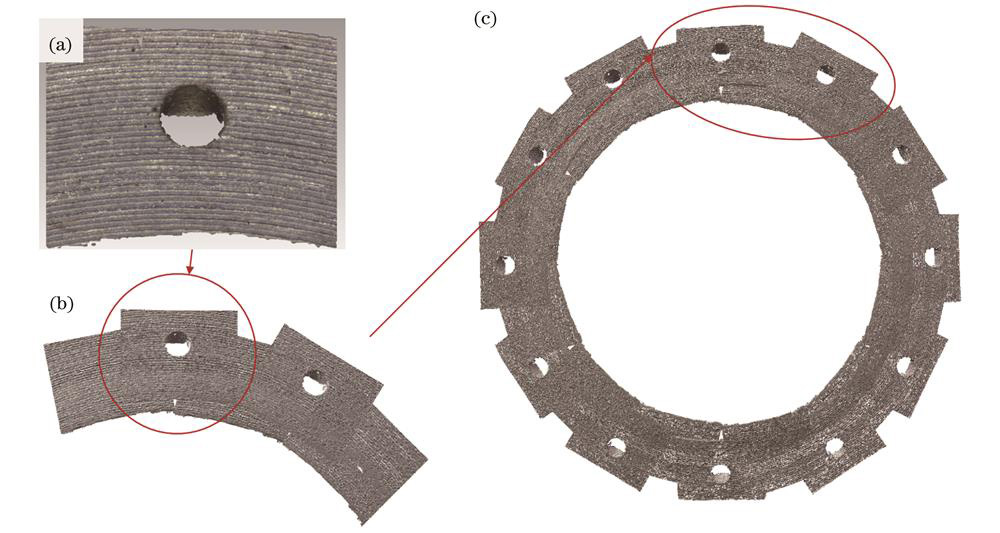
图 6. 孔阵列表面三维重建结果。(a)单个喷注孔;(b)其中两个喷注孔拼接结果;(c)所有喷注孔拼接结果
Fig. 6. Results of 3D reconstruction of the surface of the hole array. (a) Single injection hole; (b) two of the injection hole stitching results; (c) all injection hole stitching results
表 3. 局部区域位姿(部分)
Table 3. Pose of the local area (partial)
|
3.3 与理论模型及结构光精度对比
由于所提测量方法得到的最终结果实际上是显微系统测量结果的合集,因此所提方法的最终分辨率取决于前文给出的显微系统重建点云分辨率,即横向分辨率为1.86 µm,纵向分辨率为3.58 µm,此外最终精度根据显微系统精度将有0.12 µm的上下浮动。
对于本文的三维形貌拼接结果数据集,结合喷注器参数的测量需求,通过求解各孔出口表面圆心集的圆度、平面度来评价测量模型的拼合精度,通过分析每个圆心坐标与理论值的误差来评价测量模型对零件跨尺度特征的表征精度。在每个喷注孔的局部测量点云中,对孔壁部分采用随机采样一致(RANSAC)算法拟合圆柱体,分析圆柱体特征可以获取孔轴向以及起点轴心坐标即出口表面圆心坐标,对圆心坐标应用
表 4. 孔表面圆心坐标测量值、理论值,以及两者之间的误差
Table 4. Measured and theoretical values of the center coordinates of the hole surface, as well as the error between them
|
表 5. 孔轴向测量值、理论值,以及两者之间的误差
Table 5. Measured and theoretical values of the axial direction of the hole, as well as the error between them
|
为了将所提组合式测量模型与目前较为精密的单传感器进行对比,实验还使用Gocator 3506面结构光传感器对喷注器进行了测量,如
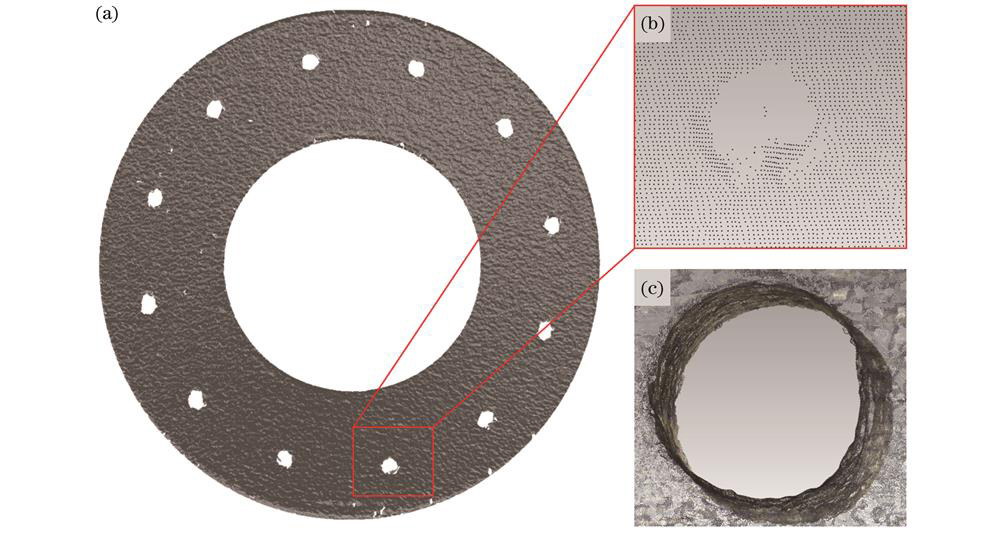
图 8. 面结构光扫描仪测量结果。(a)整体形貌;(b)局部细节;(c)所提方法局部细节
Fig. 8. Measured results of the surface structured light scanner. (a) Overall topography; (b) local details; (c) local details of the methods in this paper
4 结论
提出一种基于宏微复合标定的跨尺度测量方法,用于对具有跨尺度微纳结构的零件进行精密三维光学测量,此方法考虑到宏微测量设备的精度差异以及微观原始数据的完整性和传递的正确性,通过设计并精密加工宏微复合标定块完成双目-显微组合式测量系统全局模型的转换关系和精度过渡,实现跨尺度测量设备的全局标定。利用标定后的系统对火箭喷注器表面微孔阵列进行测量,求解出每个局部区域的位姿,将其应用于对应区域基于变焦原理重建出的三维形貌点云数据,将所有结果统一至一个数据集中以完成所有局部区域的拼接。通过与理论模型中各孔圆心点集的圆度和平面度对比以分析拼接精度,得出微孔的孔表面圆心坐标分布圆度误差为0.0438 mm,平面度误差为0.0252 mm,通过与理论模型中各孔圆心位姿对比以分析所提方法测量出的零件的定位精度,点误差值小于0.029 mm,轴向误差小于0.1140°。实验结果表明,该测量方法相较于面结构光等直接测量方法具有精度更高,形貌重建更准确的优点,适用于跨尺度零部件的微结构形貌尺寸精度和定位精度的测量场合。
[1] 倪萌, 朱惠人, 裘云, 等. 航空发动机涡轮叶片冷却技术综述[J]. 燃气轮机技术, 2005, 18(4): 25-33, 38.
Ni M, Zhu H R, Qiu Y, et al. Review of aero-turbine blade cooling technologies[J]. Gas Turbine Technology, 2005, 18(4): 25-33, 38.
[2] 戴萍, 林枫. 气膜孔几何结构对涡轮叶片气膜冷却影响的研究进展[J]. 热能动力工程, 2009, 24(4): 415-420, 539.
Dai P, Lin F. Recent advances in the study of influence of air-film hole geometrical structures on turbine blade air-film cooling[J]. Journal of Engineering for Thermal Energy and Power, 2009, 24(4): 415-420, 539.
[4] 汪千金, 崔海华, 张益华, 等. 面向光学测量跨源点云的多尺度采样配准方法[J]. 光学学报, 2022, 42(10): 1015002.
[5] Xie Z X, Wang J G, Zhang Q M. Complete 3D measurement in reverse engineering using a multi-probe system[J]. International Journal of Machine Tools and Manufacture, 2005, 45(12/13): 1474-1486.
[6] 位恒政, 王为农, 裴丽梅, 等. 用于多传感器坐标测量机探测误差评价的薄环规标准器[J]. 光学 精密工程, 2016, 24(3): 521-525.
[7] Li F, Longstaff A P, Fletcher S, et al. A practical coordinate unification method for integrated tactile-optical measuring system[J]. Optics and Lasers in Engineering, 2014, 55: 189-196.
[8] Wen X, Fu L H, Zhao Y, et al. Coordinate unification method of high-precision composite measurement in two dimensions[J]. Journal of Measurement Science and Instrumentation, 2016, 7(3): 205-213.
[9] 卞新光. 基于对焦显微法的微纳表面形貌光学测量技术研究[D]. 南京: 南京航空航天大学, 2018.
BianX G. Study on optical measurement technology of micro-nano surface topography based on focusing microscopy[D]. Nanjing: Nanjing University of Aeronautics and Astronautics, 2018.
[10] 罗桂娥. 双目立体视觉深度感知与三维重建若干问题研究[D]. 长沙: 中南大学, 2012.
LuoG E. Research on depth perception and 3D reconstruction of binocular stereo vision[D]. Changsha: Central South University, 2012.
[11] 杨艺哲, 刘中法, 方宇, 等. 聚焦型折射率显微成像系统空间分辨率的影响因素及改进方法[J]. 光学学报, 2021, 41(17): 1726001.
[12] 许勇, 郭鹏宇, 龙古灿, 等. 摄像机全自动标定方法研究[J]. 光学学报, 2013, 33(6): 0612007.
[13] 王赫. 视觉测量点云数据拼接方法及关键技术研究[D]. 哈尔滨: 哈尔滨理工大学, 2011.
WangH. Research on mosaic method and key technology of point cloud data in visual measurement[D]. Harbin: Harbin University of Science and Technology, 2011.
[14] 靳宇婷, 张益华, 崔海华, 等. 一种基于轮廓特征约束的飞机蒙皮配准方法[J]. 光学学报, 2021, 41(3): 0312001.
[15] 杨霈, 殷玉龙, 卢荣胜, 等. 基于方向性靶标和多约束优化的双目相机标定[J]. 光学学报, 2022, 42(8): 0815002.
[16] 孟飙, 曲学军. 大尺寸复杂形状组合测量系统的全局标定与多视数据融合[J]. 自动化学报, 2017, 43(11): 2051-2060.
Meng B, Qu X J. Global calibration and multi-view data fusion for combination measurement system of large complicate shapes[J]. Acta Automatica Sinica, 2017, 43(11): 2051-2060.
[17] 张可. 基于单位四元数描述的摄影测量相机自检校算法研究[D]. 徐州: 中国矿业大学, 2022.
ZhangK. Research on self-calibration algorithm of photogrammetry camera based on unit quaternion description[D]. Xuzhou: China University of Mining and Technology, 2022.
[18] 林嘉睿, 邾继贵, 郭寅, 等. 现场大空间测量中精密三维坐标控制网的建立[J]. 机械工程学报, 2012, 48(4): 6-11.
Lin J R, Zhu J G, Guo Y, et al. Establishment of precise three-dimensional coordinate control network in field large-space measurement[J]. Journal of Mechanical Engineering, 2012, 48(4): 6-11.
[19] 马少尉. 基于ICP点云数据拼接的多视角图像三维重建研究[D]. 哈尔滨: 哈尔滨理工大学, 2022.
MaS W. Research on 3D reconstruction of multi-view images based on ICP point cloud data mosaic[D]. Harbin: Harbin University of Science and Technology, 2022.
Article Outline
宋瑞, 张益华, 崔海华. 基于宏微复合标定的跨尺度零件测量方法[J]. 光学学报, 2024, 44(6): 0612001. Rui Song, Yihua Zhang, Haihua Cui. Cross-Scale Part Measurement Method Based on Macro-Micro Composite Calibration[J]. Acta Optica Sinica, 2024, 44(6): 0612001.