工艺参数对H13钢激光选区熔化成形缺陷的影响
下载: 1614次
1 引言
金属零件激光增材制造技术经过近二十年的发展,在航空航天、船舶工业、生物医学等诸多领域得到了很好的应用[1-2]。现有的激光增材制造金属零件的材料主要有钛合金、镍基合金、铝合金等[3-6]。然而,在轨道交通、装备制造业和**工业等领域发挥重要作用的高性能合金钢材料,其激光增材制造的发展仍受诸多技术难题制约[7-8]。
激光选区熔化(SLM)技术利用激光选择性熔化金属粉末,逐点逐层凝固成形,具有成形精度高、柔性高、可成型复杂结构等特点。针对激光选区增材技术,国内外学者已开展了较多的理论与实验研究,并取得了大量的成果[9-12]。H13是一种热作模具钢,是在碳工钢的基础上加入合金元素而形成的高性能合金钢,应用非常普遍。高性能合金钢由于其合金成分、物相和相变过程复杂,其SLM过程存在易产生缺陷、性能难以控制等问题。关于高性能合金钢激光选区增材过程中工艺参数对成形及缺陷的影响规律缺乏系统全面的研究。因此,本文以H13模具钢为对象,研究了SLM过程中工艺参数(激光功率、扫描速度、扫描间距、扫描方式)对成形及缺陷的影响规律。
2 实验设备与材料
采用广东汉邦激光科技有限公司的SLM-280型SLM设备,该设备采用了波长为1064~1100 nm的光纤激光器。主要参数指标如下:最大激光功率500 W,扫描速度100~7000 mm/s,铺粉厚度20~80 μm,最大成形尺寸250 mm×250 mm×300 mm。
实验所用材料为H13模具钢气雾化粉末,粉末粒径为15~45 μm,其成分见
表 1. H13钢的成分(质量分数,%)
Table 1. Compositions of H13 steel (mass fraction, %)
|
3 实验结果与分析
3.1 单层单道成形研究
对H13合金钢粉末进行单道扫描分析,以确定激光功率、扫描速度对单道形貌的影响规律,并分析其成形特征。单层单道成形参数见
表 2. 单层单道成形参数
Table 2. Single-layer single-channel forming parameters
|
3.1.1 激光功率的影响研究
设定扫描速度为
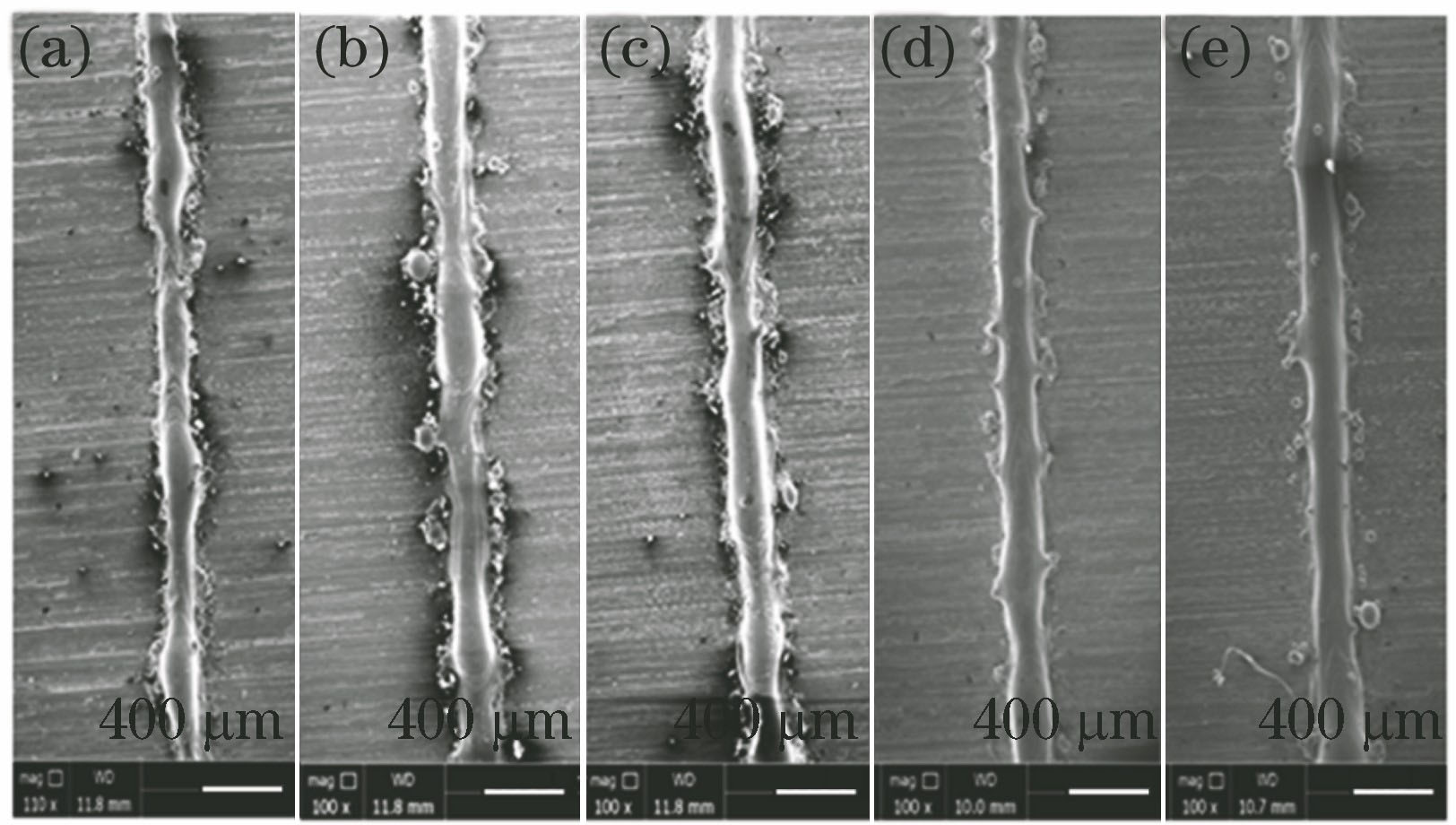
图 1. 不同激光功率下的单道形貌。(a) 250 W;(b) 300 W;(c) 350 W;(d) 400 W;(e) 450 W
Fig. 1. Single-channel morphologies under different laser powers. (a) 250 W; (b) 300 W; (c) 350 W; (d) 400 W; (e) 450 W
为了更好地研究工艺参数对成形质量的影响规律,引入激光能量密度(LED)[13]表征输入的能量,定义为
式中
通过分析可知,在铺粉层厚度和扫描速度等一定的条件下,当激光功率较小时,输入的能量较小,金属粉末的熔化量也相对较少,导致所形成的熔池尺寸较小[14];未熔化的金属粉末在冷却时会形成不连续的熔池,影响熔融层的外形,增大了熔融层的表面粗糙度。随着激光功率的增大,
3.1.2 扫描速度的影响研究
当激光功率为
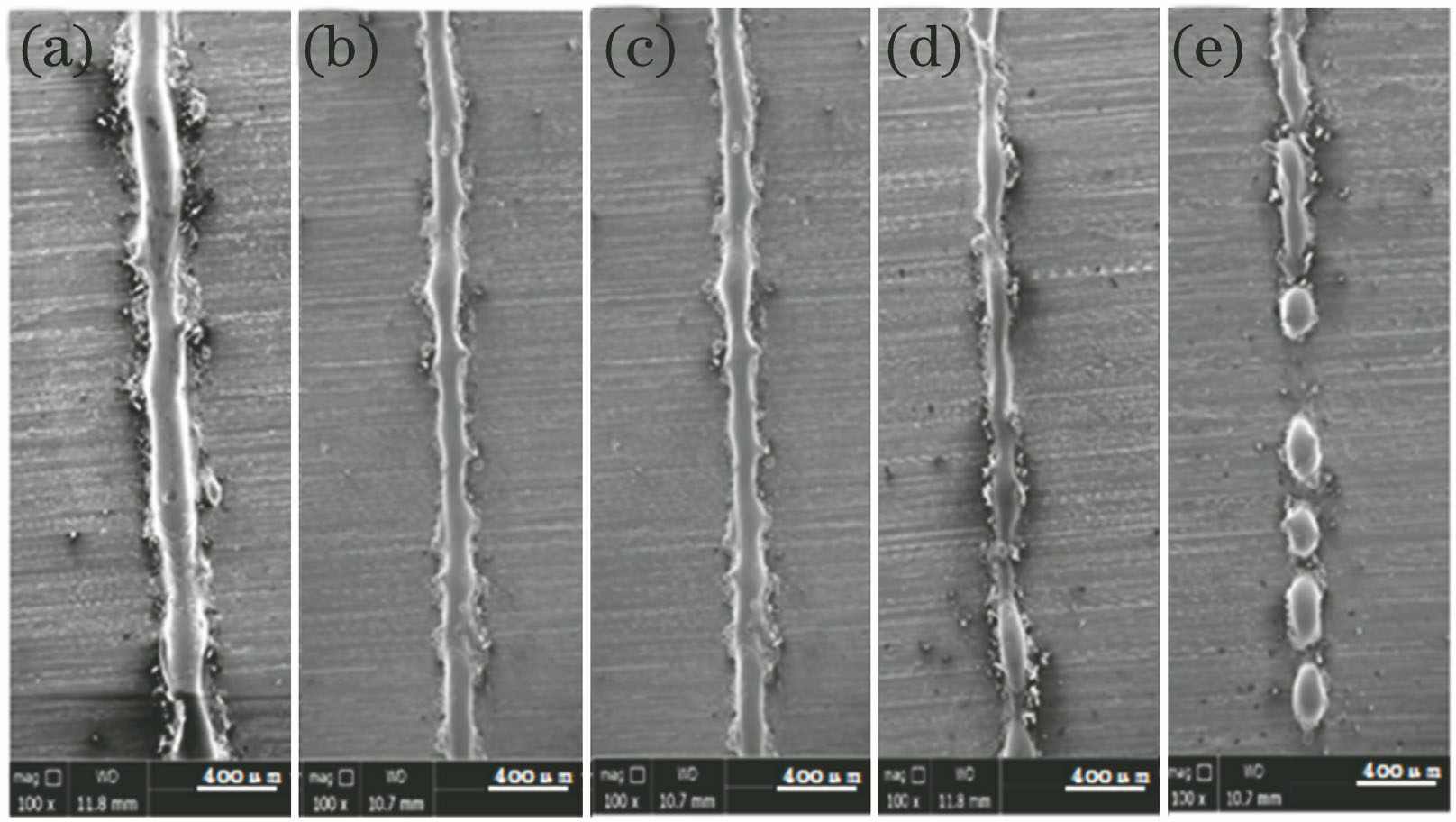
图 2. 不同扫描速度下的单道形貌。(a) 800 mm/s;(b) 1000 mm/s;(c) 1200 mm/s;(d) 1400 mm/s;(e) 1600 mm/s
Fig. 2. Single-channel morphologies under different scanning speeds. (a) 800 mm?s-1; (b) 1000 mm?s-1; (c) 1200 mm?s-1; (d) 1400 mm?s-1; (e) 1600 mm?s-1
当其他参数一定时,随着扫描速度的增大,
此外,当扫描速度为800 mm/s时,发现有明显的飞溅现象;当速度达到1000 mm/s和1200 mm/s时,飞溅现象有所减少;扫描速度进一步增大至1400 mm/s和1600 mm/s时,飞溅现象再次增多。分析原因可知,当激光功率一定时,金属粉末在高能量激光的照射下吸收了大量能量,温度上升到熔点以上,有时甚至在沸点以上。在金属气流以及粉层气体受热膨胀的影响下,金属粉末会飞离熔池发生飞溅。飞溅主要受以下两方面因素影响:一是金属粉末的气化量;二是金属蒸气从熔池溢出的溢出量。当扫描速度较小时,金属粉末发生大量气化,飞溅现象明显;随着扫描速度的增大,金属气化量减少,且大部分溢出,飞溅现象减少;而当扫描速度过大时,虽然金属粉末气化量少,但是由于熔池反应速度较快,大部分金属蒸气来不及溢出,飞溅现象又明显增多。
3.2 多层多道成形研究
在单层单道的实验基础上,进行了多层多道实验,分析工艺参数在成形过程中的影响规律,实验所采用的工艺参数见
3.2.1 激光功率的影响研究
在扫描速度
表 3. 多层多道成形参数
Table 3. Multi-layer multi-channel forming parameters
|
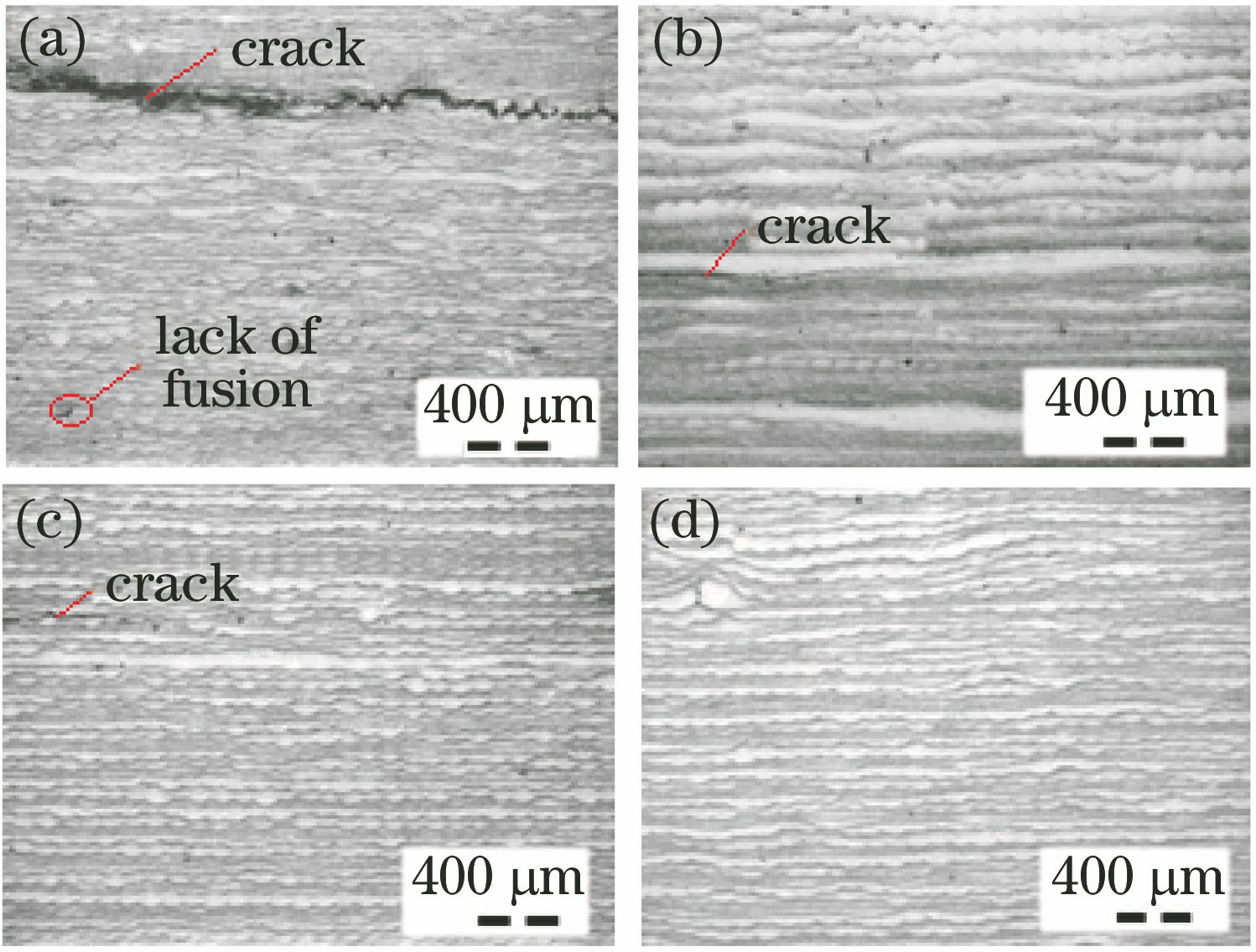
图 3. 激光功率对成形件质量的影响。(a) 250 W;(b) 350 W;(c) 400 W;(d) 450 W
Fig. 3. Effect of laser power on forming part quality.(a) 250 W; (b) 350 W; (c) 400 W; (d) 450 W
由
3.2.2 扫描速度的影响研究
设定功率为
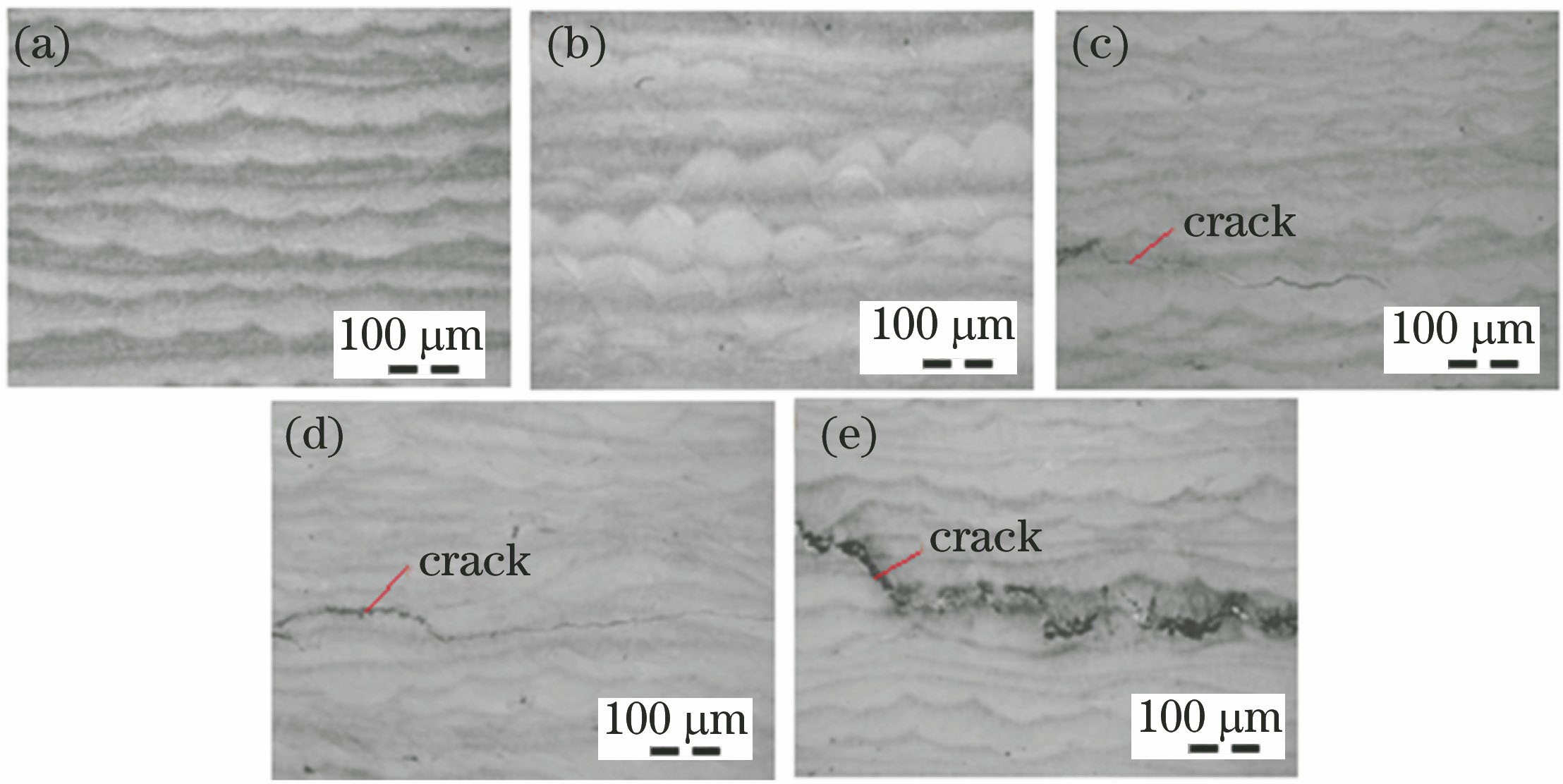
图 4. 扫描速度对成形件质量的影响。(a) 300 mm/s;(b) 400 mm/s;(c) 500 mm/s;(d) 800 mm/s;(e) 1200 mm/s
Fig. 4. Effect of scanning speed on forming part quality. (a) 300 mm?s-1; (b) 400 mm?s-1; (c) 500 mm?s-1; (d) 800 mm?s-1; (e) 1200 mm?s-1
通过分析可知,扫描速度主要影响加工过程中激光与粉末之间的作用时间。当扫描速度较小时,金属粉末充分熔化,无明显缺陷产生;熔池的温度梯度较小,残余应力较小。随着扫描速度的增大,金属粉末及基体的加热时间减少,粉末吸收的能量减少,甚至可能有部分金属粉末未熔化或熔化不充分,形成未熔合或夹渣缺陷。当内应力较大时,会在缺陷处形成应力集中,造成裂纹的产生。
3.2.3 扫描间距的影响研究
在激光功率350 W和扫描速度1000 mm/s不变的情况下,分析扫描间距对成形件质量的影响规律。扫描间距是两相邻扫描激光束之间的距离,在加工过程中将影响成形件熔道之间的搭接率。由于激光光斑内的能量呈高斯分布,光斑中心的能量密度最大,离中心较远的边缘处的能量密度较小。为了保证金属粉末能够完全熔化,一般扫描间距应比激光光斑直径小,使熔道之间有一定的搭接。扫描间距不同,则搭接率不同,搭接率可定义如下
式中
在本次实验中,扫描间距
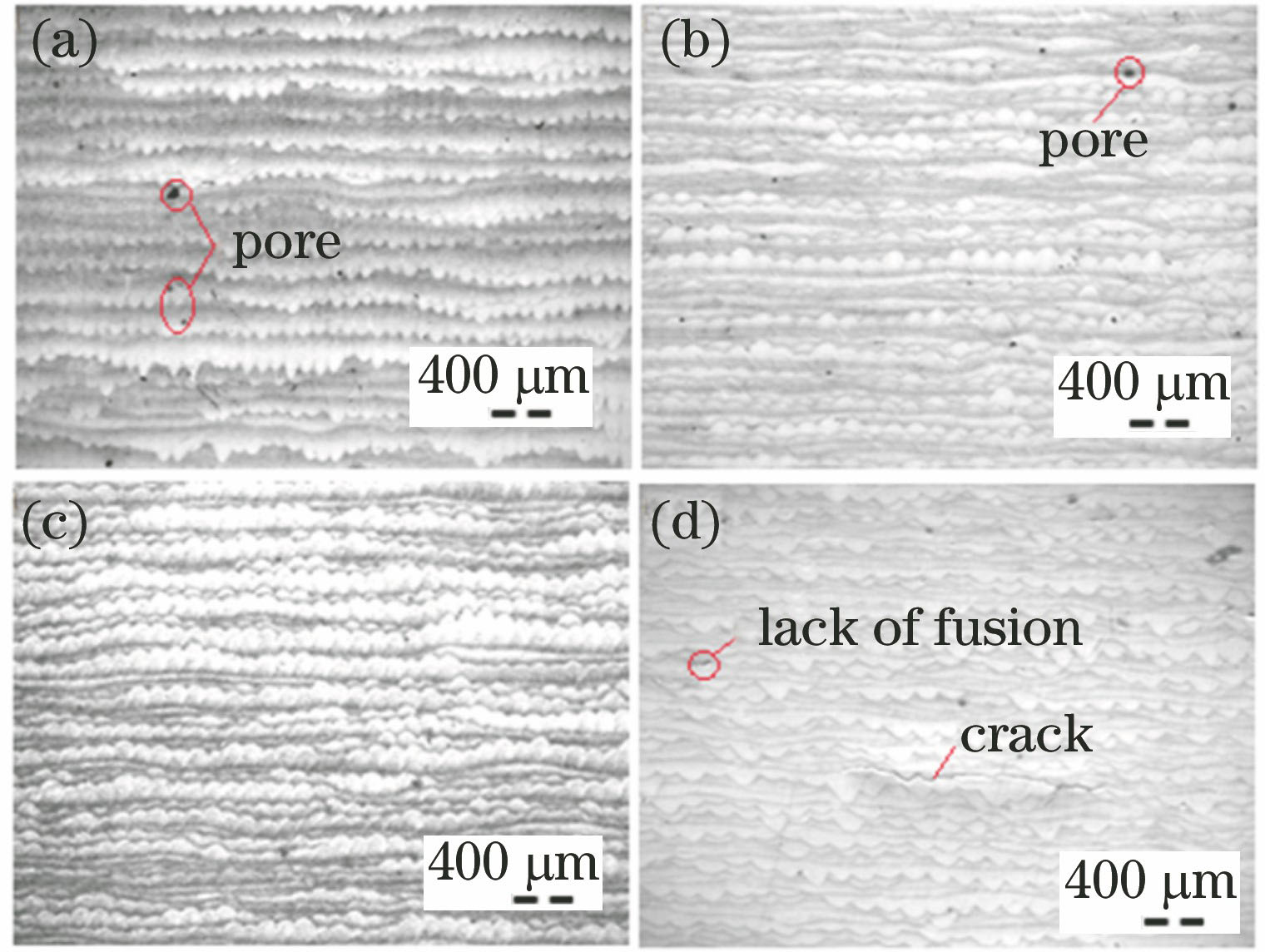
图 5. 扫描间距对成形件质量的影响。(a) 40 μm;(b) 60 μm;(c) 70 μm;(d) 80 μm
Fig. 5. Effect of scanning spacing on forming part quality. (a) 40 μm; (b) 60 μm; (c) 70 μm; (d) 80 μm
通过分析可知,当扫描间距
3.2.4 扫描方式的影响研究
加工过程中的扫描方式对零件的成形质量有很大的影响,不同的扫描方法下会有不同的热循环过程,从而影响零件的应力状态和组织性能[16]。采用三种扫描方式:单
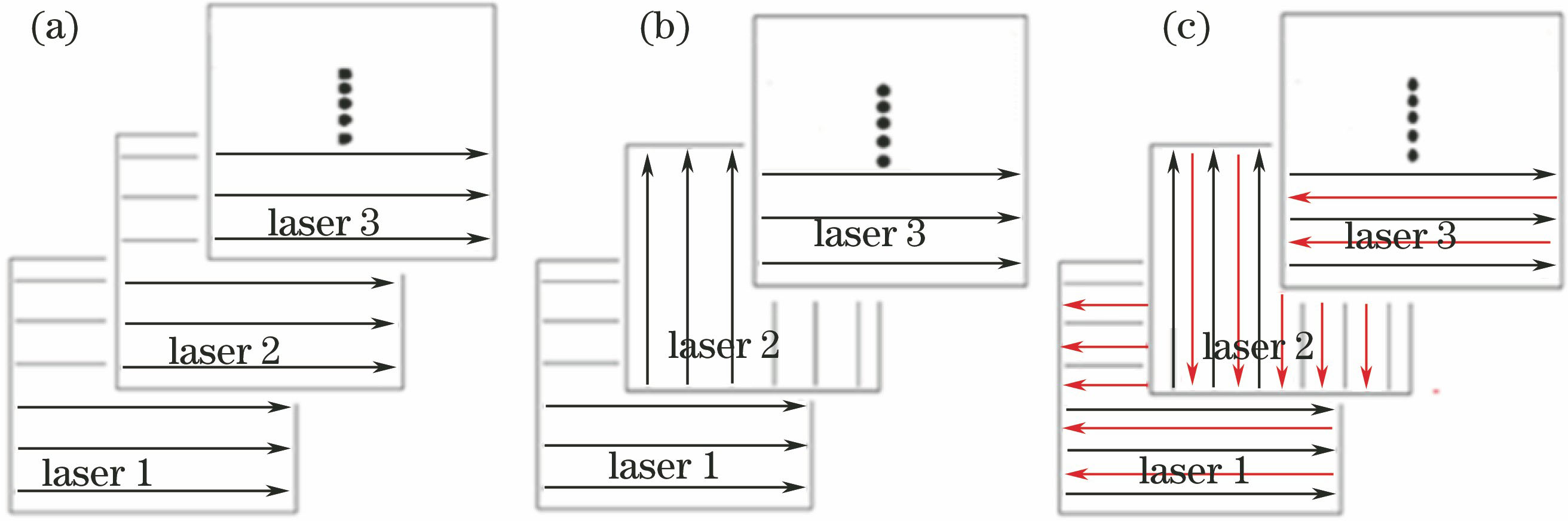
图 6. SLM扫描方式示意图。(a) 单X方向扫描;(b) Z型正交扫描;(c) S型正交扫描
Fig. 6. Schematic of SLM scanning strategy. (a) Single X direction scanning; (b) Z-shaped orthogonal scanning; (c) S-shaped orthogonal scanning
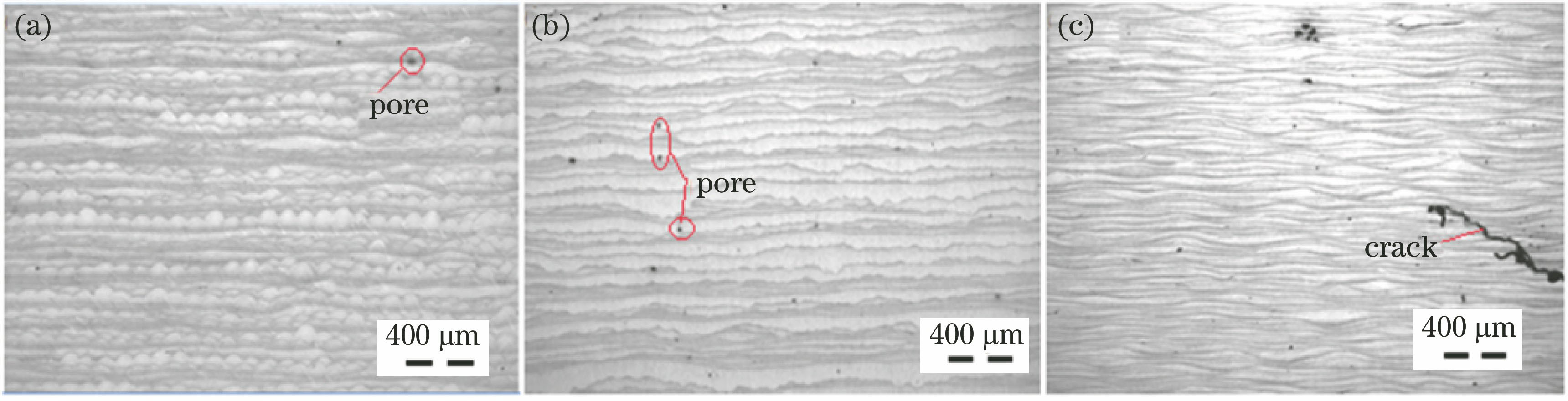
图 7. 不同扫描方式下的成形质量。(a) S型正交扫描;(b) Z型正交扫描;(c)单X方向扫描
Fig. 7. Forming quality under different scanning modes. (a) S-shaped orthogonal scanning; (b) Z-shaped orthogonal scanning; (c) single X direction scanning
在单
4 结论
以H13模具钢为对象,研究了SLM过程中激光功率、扫描速度、扫描间距和扫描方式对成形及缺陷的影响规律,得到以下结论。
1) 通过对单层单道工艺以及多层多道工艺的研究发现,在SLM成形过程中,激光功率、扫描速度都会影响到成形质量。在相同的扫描速度下,激光功率在一定范围内增加会改善成形过程中的未熔合等现象,从而提高成形质量;在相同的激光功率下,扫描速度的增加能够减少热输入,从而改善成形件的残余应力状态,但当扫描速度过大时,能量输入不足会造成未熔合等缺陷。
2) 在多层多道成形中,扫描间距过小时易发生过烧,形成气孔缺陷;扫描间距过大时,易产生未熔合缺陷。同时,相对于单
3) 对H13钢粉末而言,优化的工艺参数范围为:激光功率400~450 W,扫描速度400~500 mm/s,扫描间距60~70 μm,光斑直径100 μm,铺粉厚度40 μm。
[1] 刘业胜, 韩品连, 胡寿丰, 等. 金属材料激光增材制造技术及在航空发动机上的应用[J]. 航空制造技术, 2014, 454(10): 62-67.
Liu Y S, Han P L, Hu S F, et al. Development of laser additive manufacturing with metallic materials and its application in aviation engines[J]. Aeronautical Manufacturing Technology, 2014, 454(10): 62-67.
[2] 林鑫, 黄卫东. 高性能金属构件的激光增材制造[J]. 中国科学:信息科学, 2015, 45(9): 1111-1126.
Lin X, Huang W D. Laser additive manufacturing of high-performance metal components[J]. Scientia Sinica (Informationis), 2015, 45(9): 1111-1126.
[3] 肖振楠, 刘婷婷, 廖文和, 等. 激光选区熔化成形TC4钛合金热处理后微观组织和力学性能[J]. 中国激光, 2017, 44(9): 0902001.
[4] 钱德宇, 陈长军, 张敏, 等. 选区激光熔化成形多孔铝合金的显微组织及微观力学性能研究[J]. 中国激光, 2016, 43(4): 0403002.
[5] 潘爱琼, 张辉, 王泽敏. 选区激光熔化镍基单晶高温合金的熔池显微组织[J]. 激光与光电子学进展, 2017, 54(7): 071402.
[6] 林辉, 杨永强, 张国庆, 等. 激光选区熔化医用钴铬钼合金的摩擦性能[J]. 光学学报, 2016, 36(11): 1114003.
[7] 杨强, 鲁中良, 黄福享, 等. 激光增材制造技术的研究现状及发展趋势[J]. 航空制造技术, 2016, 507(12): 26-31.
Yang Q, Lu Z L, Huang F X, et al. Research on status and development trend of laser additive manufacturing[J]. Aeronautical Manufacturing Technology, 2016, 507(12): 26-31.
[8] 尹华, 白培康, 刘斌, 等. 金属粉末选区激光熔化技术的研究现状及其发展趋势[J]. 热加工工艺, 2010, 39(1): 140-144.
Yin H, Bai P K, Liu B, et al. Present situation and development trend of selective laser melting technology for metal powder[J]. Hot Working Technology, 2010, 39(1): 140-144.
[11] 王沛, 黄正华, 戚文军, 等. 基于SLM技术的3D打印工艺参数对316不锈钢组织缺陷的影响[J]. 机械制造文摘(焊接分册), 2016, 23(2): 2-7.
Wang P, Huang Z H, Qi W J, et al. Effect of the 3D printing process parameters based on SLM technology on the structure defect of 316 stainless steel[J]. Welding Digest of Machinery Manufacturing, 2016, 23(2): 2-7.
[12] 王迪, 杨永强, 黄延录, 等. 层间扫描策略对SLM直接成型金属零件质量的影[J]. 激光技术, 2010, 34(4): 447-451.
[14] 王黎, 魏青松, 贺文婷, 等. 粉末特性与工艺参数对SLM成形的影响[J]. 华中科技大学学报(自然科学版), 2012, 40(6): 20-23.
Wang L, Wei Q S, He W T, et al. Influence of powder characteristic and process parameters on the SLM formability[J]. Journal of Huazhong University of Science and Technology (Natural Science Edition), 2012, 40(6): 20-23.
[15] 刘锦辉, 史金光, 李亚. 选择性激光熔化AlSi10Mg合金粉末的成形工艺[J]. 黑龙江科技大学报, 2015, 25(5): 509-515.
Liu J H, Shi J G, Li Y. Study on selective laser melting process and forming of AlSi10Mg alloy powder[J]. Journal of Heilongjiang University of Science and Technology, 2015, 25(5): 509-515.
[16] 邓诗诗, 杨永强, 李阳, 等. 分区扫描路径规划及其对SLM成型件残余应力分布的影响[J]. 中国激光, 2016, 43(12): 1202003.
Article Outline
徐锦岗, 陈勇, 陈辉, 杨冰. 工艺参数对H13钢激光选区熔化成形缺陷的影响[J]. 激光与光电子学进展, 2018, 55(4): 041405. Jingang Xu, Yong Chen, Hui Chen, Bing Yang. Influence of Process Parameters on Forming Defects of H13 Steel Processed by Selective Laser Melting[J]. Laser & Optoelectronics Progress, 2018, 55(4): 041405.