5052铝合金高频微振激光焊接疲劳性能及损伤行为
下载: 1258次
1 引言
5052铝合金属于Al-Mg系不可热处理强化铝合金,其焊接结构件具有优良的焊接性能、疲劳性能和耐腐蚀性能,在汽车、船舶、航空等制造领域具有极好的应用价值[1-2]。使用合适强度的铝合金结构件替代传统的钢结构件,能够节能减排,符合时代发展的需求[3]。与传统焊接相比,激光焊接具有能量密度集中、热影响区小、自动化程度高、效率高等优势,是铝合金焊接的有效方法之一[4-5]。铝合金的热膨胀系数高,易产生焊接变形。焊接变形与焊缝区及附近分布的残余应力密切相关[6]。在铝合金焊接过程中控制减少残余应力有利于省去焊后加工处理步骤,提高制造效率,节约综合成本。焊接残余应力会受到材料特性、热输入条件、结构刚度等因素的影响[7]。振动焊接是由振动时效发展而来的工艺方法,是在焊接过程中对构件施加振动场,从而达到细化晶粒、消除残余应力[8-9]等目的,进一步提高焊接接头的品质。Zeidabadi等[10]在工件的钨极惰性气体保护焊(GTAW)过程中引进机械振动,发现与无振动焊缝组织相比,机械振动焊缝组织的粗大柱状晶数量减少,等轴晶结构区域增加。
疲劳失效是焊接承载结构件中常见的失效方式之一。目前,对铝合金焊接接头疲劳行为的研究主要集中于疲劳损伤机制和数值仿真方面。Xu等[11]通过对AA2197-T7铝合金的高周疲劳行为进行研究,观察到两种不同的疲劳裂纹起始机制和内部或表面裂纹萌生机制,并且裂纹萌生及扩展阶段消耗了大部分的疲劳寿命。Xie等[12]研究了DP590双相不锈钢激光焊接接头,发现裂纹主要从表面蚀孔和缺陷萌生并沿着马氏体组织扩展,在组合应力水平下,裂纹尖端附近发生急剧局部变形过程。胡雅楠等[13]利用同步辐射X射线三维成像工具对疲劳裂纹萌生及扩展路径进行表征,疲劳裂纹沿最薄弱的熔合线扩展,气孔对其扩展过程影响较小。乔俊楠等[14]对A7N01铝合金进行激光电弧变极性复合填丝焊,疲劳裂纹倾向于在焊缝上表面的应力集中处萌生,并观察了裂纹处的金相,发现裂纹沿晶扩展。
本文从激光振动热力耦合焊接得到的5052铝合金焊接接头入手,观察该接头的组织结构,测试其残余应力和疲劳寿命,并分析了断口和疲劳损伤行为。
2 实验材料与方法
2.1 实验材料及实验过程
本实验选取5052铝合金来研究振动工艺对焊接接头残余应力及疲劳性能的影响。待焊样板的尺寸为300 mm×250 mm×5 mm。5052铝合金的化学成分见
表 1. 5052铝合金的化学成分
Table 1. Chemical compositions of 5052 aluminum alloy
|
焊接前对铝合金表面进行打磨并清洗,去除氧化层及杂质后吹干待焊。如
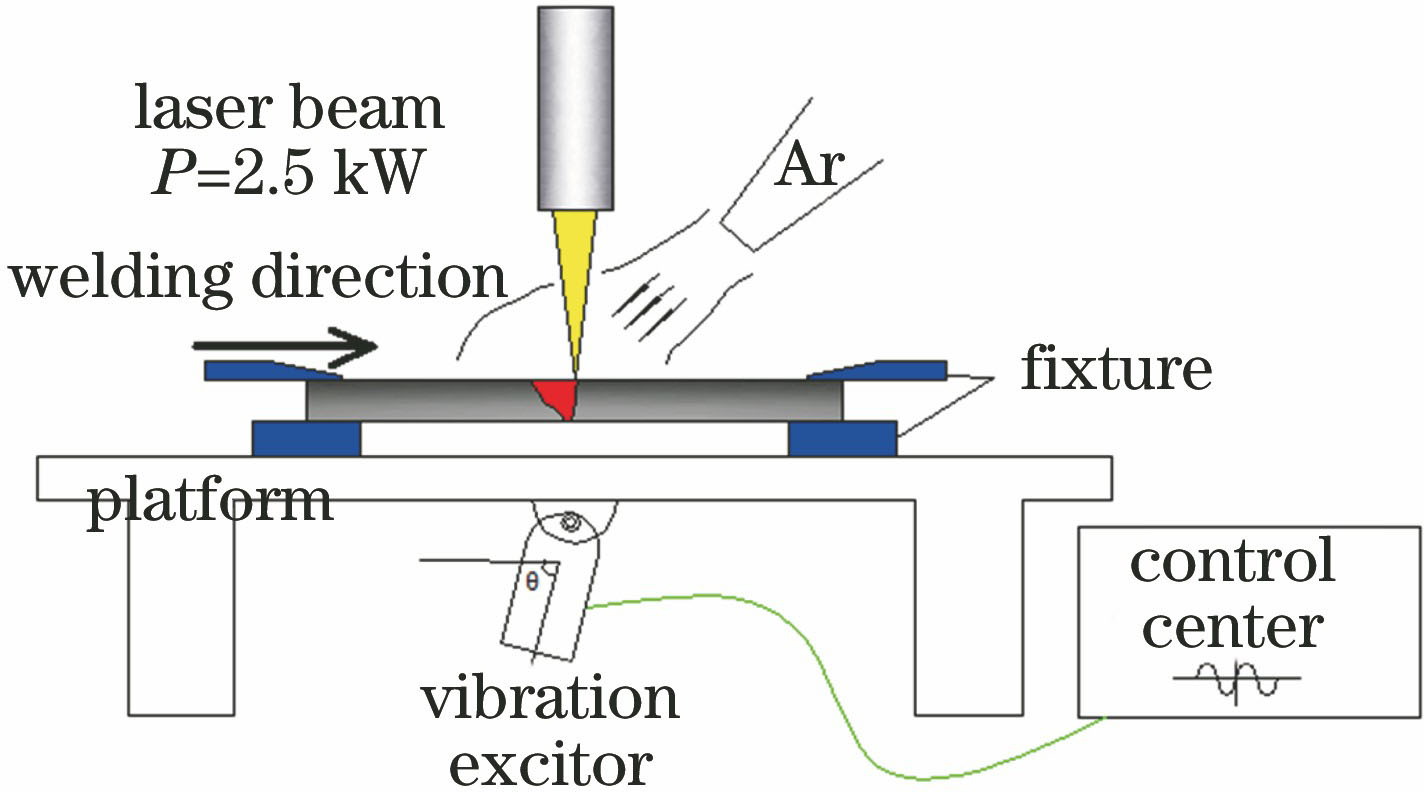
图 1. 高频微振激光焊接实验平台示意图
Fig. 1. Schematic of experimental platform for high frequency micro-vibration laser welding
表 2. 实验参数表(P=5 kW; v=0.03 m·s-1; DDA=-15 mm)
Table 2. Parameters for test (P=5 kW; v=0.03 m/s; DDA=-15 mm)
|
本实验所选取金相为焊缝横截面。腐蚀液配方为190 mL H2O、5 mL HNO3溶液、3 mL HCl溶液和2 mL HF溶液,腐蚀时间为90 s。使用超景深数码光学显微镜(VHX-600K,基恩士公司,德国)观察接头的金相组织。采取钻孔应变释放法测量焊缝残余应力,具体位置如
3 实验结果与分析
3.1 接头微观组织
5052铝合金常规无振激光焊接和振动激光焊接接头的显微组织如
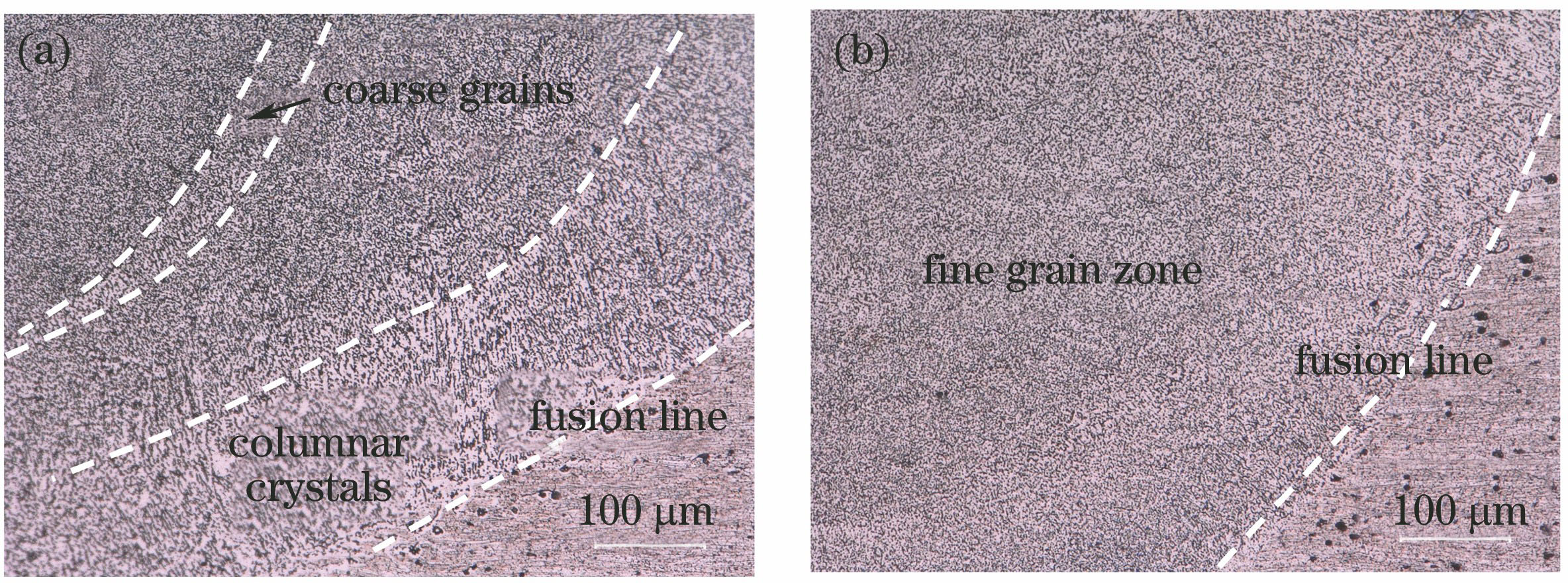
图 3. 熔合线处微观组织。(a) 1号焊缝熔合线;(b) 5号焊缝熔合线
Fig. 3. Microstructures at fusion lines. (a) Weld fusion line 1; (b) weld fusion line 5
3.2 残余应力
焊接残余应力在宏观的尺寸范围内存在并保持平衡,通过钻孔应变释放法来测量焊接残余应力的大小和方向。根据CB3395—1992计算得到残余应力,本文中残余应力均为拉应力。
焊缝残余应力测量结果如
3.3 疲劳性能
本疲劳实验为高周疲劳实验,纯铝及铝合金材料没有明显的疲劳寿命极限,将循环次数为107对应的循环载荷作为焊接接头的疲劳寿命极限,得到的加载应力和寿命周次关系可根据Basquin类型公式拟合。
式中:
在双对数坐标中,lg(
由(3)式可求出5052铝合金母材和焊缝在循环次数≤107时任意应力所对应的条件疲劳极限强度,即母材在寿命为107循环次数时对应的条件疲劳极限为153.1 MPa。对比母材和双道焊接接头试样的疲劳寿命曲线,发现焊接后板材的疲劳强度明显降低。这是因为铝合金在焊接后,熔池凝固产生的表面粗糙不平,与母材平整的表面相比,其更易产生裂纹。焊缝的熔合区是焊缝最薄弱的区域,而裂纹在此区域最容易扩展,疲劳强度明显降低。在无振与振动组合的A、B试样中,接头率先在1、3号无振激光焊缝处断裂。在低频与高频振动参数组合的C试样的多个疲劳接头中,疲劳断裂发生在5号或6号焊缝处。在E、F试样中,当频率相同时,随着振动加速度的逐渐加大,10号和12号焊缝处率先断裂。其余在疲劳实验中未失效的焊缝的疲劳寿命均高于对应失效的焊缝。采取振动工艺的激光焊接接头的疲劳性能优于常规无振接头。在振动工艺中,低振动频率与高振动加速度的匹配度较高,高振动频率与低振动加速度的匹配度也较高。在本疲劳实验中,F试样的疲劳寿命比C、E试样长,为得到良好疲劳性能的焊接接头,建议采用高振动频率与低振动加速度的组合。
疲劳强度系数
表 3. 残余应力与疲劳强度指数
Table 3. Residual stress and fatigue strength coefficient
|
焊接接头的疲劳裂纹多由集中应力造成,焊接接头表面粗糙不平,内部也存在焊接缺陷。应力集中是由实验主动施加的名义应力与缺陷的几何形状共同决定,而残余应力的存在会提高应力峰值。因此,采用降低残余应力来提高疲劳寿命的方法具有可行性。
裂纹扩展与裂纹尖端的应力集中程度Δ
式中:d
3.5 疲劳断口分析
对5052铝合金母材及焊接接头的疲劳断口进行扫描电子显微镜(SEM)分析,
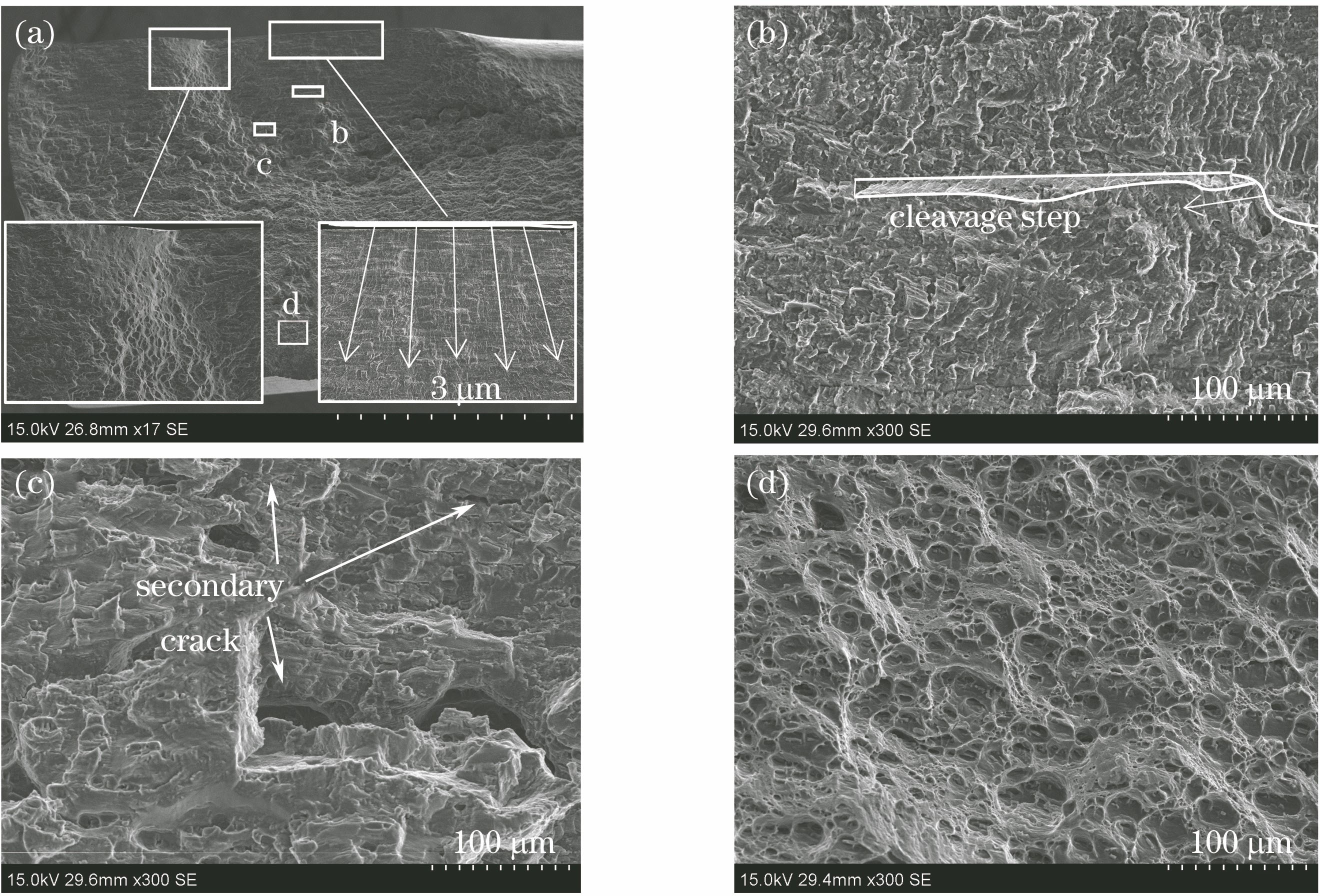
图 6. 5052铝合金母材疲劳断口形貌。(a)断口形貌及位置示意图;(b)疲劳台阶;(c)二次裂纹;(d)韧窝
Fig. 6. BM fatigue fracture morphology of 5052 aluminum alloy. (a) Fracture morphology and position diagram; (b) fatigue step; (c) secondary crack; (d) dimple
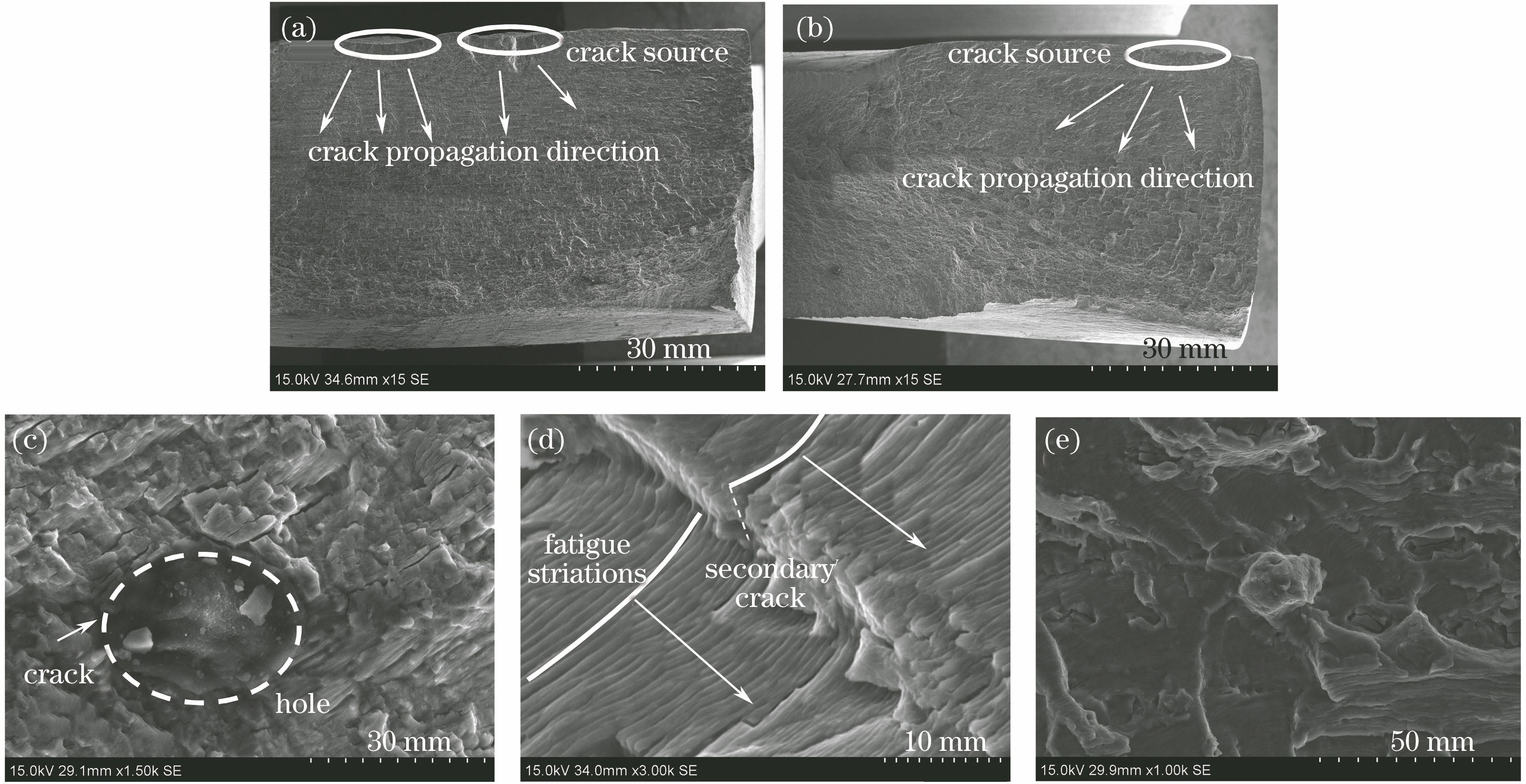
图 7. 焊接接头疲劳断口形貌。(a)多疲劳源的断口;(b)单疲劳源的断口;(c)气孔;(d)疲劳辉纹;(e)裂纹尖端交汇处
Fig. 7. Fatigue fracture morphologies of welded joints. (a) Fracture of multiple fatigue sources; (b) fracture of single fatigue source; (c) hole; (d) fatigue striations; (e) crack tip junctions
4 结论
振动焊接工艺能够有效改善焊接接头组织,并降低其残余拉应力水平,从而提高接头的疲劳寿命。焊接接头的蚀孔和缺陷加速了疲劳裂纹的萌生速度,疲劳断裂特征体现韧性断裂。设计了两种提高疲劳性能的有效途径,通过降低焊缝残余应力或消除表面蚀坑和缺陷来提高疲劳寿命。在后续工作中,结合有限元分析和实时观测手段进一步研究疲劳失效的过程,并找出提高接头性能的最优方法。
[1] Feng F, Li J J, Chen R C, et al. Effect of die geometry on the formability of 5052 aluminum alloy in electromagnetic impaction deformation[J]. Materials, 2018, 11(8): 1379.
[2] 孔晓芳, 李飞, 吕俊霞, 等. 5083铝合金光纤激光填丝焊接工艺[J]. 中国激光, 2014, 41(10): 1003007.
[3] Zhang C, Gao M, Zeng X Y. Effect of microstructural characteristics on high cycle fatigue properties of laser-arc hybrid welded AA6082 aluminum alloy[J]. Journal of Materials Processing Technology, 2016, 231: 479-487.
[4] 朱加雷, 徐世龙, 焦向东, 等. 304不锈钢薄板激光搭接焊工艺研究[J]. 激光与光电子学进展, 2015, 52(7): 071404.
[5] 刘东宇, 李东, 李凯斌, 等. 相同激光线能量对焊缝组织和性能的影响[J]. 激光与光电子学进展, 2015, 52(10): 101402.
[6] Ganev N, Kolarík K, Pala Z, et al. Influence of beam speed on residual stresses in the vicinity of laser welds[J]. Advanced Materials Research, 2014, 996: 463-468.
[7] Okano S, Mochizuki M. Experimental and numerical investigation of trailing heat sink effect on weld residual stress and distortion of austenitic stainless steel[J]. ISIJ International, 2016, 56(4): 647-653.
[8] Puga H, Costa S, Barbosa J, et al. Influence of ultrasonic melt treatment on microstructure and mechanical properties of AlSi9Cu3 alloy[J]. Journal of Materials Processing Technology, 2011, 211(11): 1729-1735.
[9] 尹何迟, 陈立功, 张光业, 等. 振动焊接工艺效果研究[J]. 振动与冲击, 2006, 25(4): 132-134.
Yin H C, Chen L G, Zhang G Y, et al. Study on effect of vibrating welding technique[J]. Journal of Vibration and Shock, 2006, 25(4): 132-134.
[10] Zeidabadi H, Mirdamadi S, Godarzi M. Effect of vibration during GTAW welding on microstructure and mechanical properties of Ti6Al4V[J]. Russian Journal of Non-Ferrous Metals, 2015, 56(2): 217-221.
[11] Xu L P, Wang Q Y, Zhou M. Micro-crack initiation and propagation in a high strength aluminum alloy during very high cycle fatigue[J]. Materials Science and Engineering A, 2018, 715: 404-413.
[12] Xie C J, Yang S L, Liu H B, et al. Microstructure and fatigue properties of laser welded DP590 dual-phase steel joints[J]. Journal of Materials Engineering and Performance, 2017, 26(8): 3794-3801.
[13] 胡雅楠, 吴圣川, 宋哲, 等. 激光复合焊接7020铝合金的疲劳性能及损伤行为[J]. 中国激光, 2018, 45(3): 0302003.
[14] 乔俊楠, 王启明, 邹江林, 等. 光纤激光-变极性TIG复合填丝焊接A7N01铝合金接头的组织与力学性能[J]. 中国激光, 2016, 43(9): 0902001.
[15] 李巧艳, 罗宇, 王亚军, 等. 5052铝合金双光点激光焊接组织与性能[J]. 焊接学报, 2007, 28(12): 105-108.
Li Q Y, Luo Y, Wang Y J, et al. Microstructure and mechanical properties of twin spot laser welding of 5052 aluminum[J]. Transactions of the China Welding Institution, 2007, 28(12): 105-108.
[16] Jia J, Yang S L, Ni W Y, et al. Microstructure and mechanical properties of fiber laser welded joints of ultrahigh-strength steel 22MnB5 and dual-phase steels[J]. Journal of Materials Research, 2014, 29(21): 2565-2575.
[17] Mecholsky J J. Jr. Fractography: determining the sites of fracture initiation[J]. Dental Materials, 1995, 11(2): 113-116.
张巍, 卢庆华, 任新怀, 白永真, 金杰文, 欧徉伶. 5052铝合金高频微振激光焊接疲劳性能及损伤行为[J]. 中国激光, 2019, 46(3): 0302012. Wei Zhang, Qinghua Lu, Xinhuai Ren, Yongzhen Bai, Jiewen Jin, Yangling Ou. Fatigue Properties and Fracture Behavior of 5052 Aluminum Alloys Welded by High Frequency Micro-Vibration Laser[J]. Chinese Journal of Lasers, 2019, 46(3): 0302012.