双相钢激光胶接点焊及接头强度分析
下载: 977次
1 引言
汽车轻量化不仅可以减小能耗,而且能减少尾气排放,已成为21世纪汽车技术的前沿和关注点之一[1]。用双相高强度钢取代传统的低碳钢可有效减轻汽车的重量,达到汽车轻量化的目的[2]。汽车车身构件主要通过焊接的方式进行连接[3],电阻点焊与粘接技术的结合,可以使整个接头的应力分布更加均匀,提高接头的耐疲劳性能[4],但电阻点焊使用的胶粘剂需具有导电性,增加了成本。而激光胶焊技术对胶层无特殊要求,且具有焊接速度快、精度高、热输入量小、工件变形小等诸多优点,具有广泛的应用前景[5-6]。
针对激光胶接点焊工艺和焊接过程存在的问题,国内外学者开展了大量的研究。任大鑫等[7]通过采集分析激光焊接过程的焊接光谱,发现胶层增大了试件对激光的吸收率。Messler等[8]分析发现,焊点周围施加压力可减小金属板间胶层受热气化后对熔池的冲击作用。王铭茂等[9]研究了不同胶层的气体排开方式,设计了脉冲波形以适应不同粘度的胶层。刘申等[10]以钛合金为对象,研究发现胶层分解后产生的残余碳使激光点焊-胶接复合接头出现了碳化钛(TiC),从而增大了接头的显微硬度,但同时削弱了接头的承载能力。对于点焊接头的无损检测,Liu等[11]通过分析时域和频域的特征信号,获得了不锈钢点焊接头的超声C扫描图像,并设计了当量计算程序来自动计算焊核直径。Sun等[12]将电阻点焊接头的超声C扫描图像划分为不同的区域,可以表征飞溅、焊穿等焊接缺陷。然而,目前通过正交试验来研究不同焊接工艺参数对激光胶焊接头质量的影响规律,以及分析接头超声C扫描图像特征的文献鲜有报道。
本文以焊接功率、离焦量和焊接时间为参数,对DP590双相钢进行了激光胶接点焊的正交试验,借助电液伺服材料试验机对接头进行了拉剪试验,分析了不同工艺参数对接头拉剪性能的影响,并对失效接头进行了断口分析;借助超声波扫描显微镜研究了不同参数下接头的超声C扫描图像的特性和不同区域的超声A扫描信号特征。
2 试验方法
2.1 材料和试样制备
用于激光胶接点焊连接的母材是规格为110 mm×20 mm×1.5 mm的DP590双相钢钢片,其化学成分如
采用的激光焊接系统为德国IPG公司生产的YLG-6000光纤激光器。胶焊过程的具体步骤为:1) 用砂纸对母材表面进行打磨,再用丙酮溶液擦拭去掉表面氧化物;2) 对搭接区域定量施胶,并用夹子将搭接好的试件夹紧,以确保胶层厚度的一致性;3) 将粘接后的试件进行激光点焊;4) 把试件放入恒温箱24 h,对搭接区的胶层进行固化。焊接过程中采用的保护气体为氩气,吹气方式为侧吹,气流速率为15 L/min。
表 1. DP590化学成分(质量分数,%)
Table 1. Chemical compositions of DP590 (mass fraction, %)
|
表 2. DP590的拉伸性能
Table 2. Tensile properties of DP590
|
2.2 正交试验设计
选择焊接功率、离焦量和焊接时间为变量进行三因素三水平胶焊正交试验,焊接功率选择1400,1600,1800 W,离焦量选择3,0,-3 mm,焊接时间设定为200,600,1000 ms,制定9组试验方案,如
表 3. 正交试验方案
Table 3. Scheme of orthogonal experiment
|
2.3 点焊接头质量检测
借助超声波扫描显微镜,采用超声波水浸聚焦入射法得到激光胶接点焊接头的超声A扫描信号和超声C扫描图像。试验所用检测系统的探头频率为15 MHz,分辨率为95 μm,耦合剂为水。
采用MTS公司的电液伺服材料试验机对9组激光胶接点焊接头进行拉剪试验,拉伸过程中加载速度设为2 mm·min-1。为克服试件拉伸过程中产生的弯矩,在试件夹持部分贴上25 mm×20 mm×1.5 mm的垫片。拉剪过程结束后,采用SEM对胶焊接头的断口进行宏观和微观形貌分析。
3 试验结果与分析
3.1 胶焊接头的形貌特征
依照
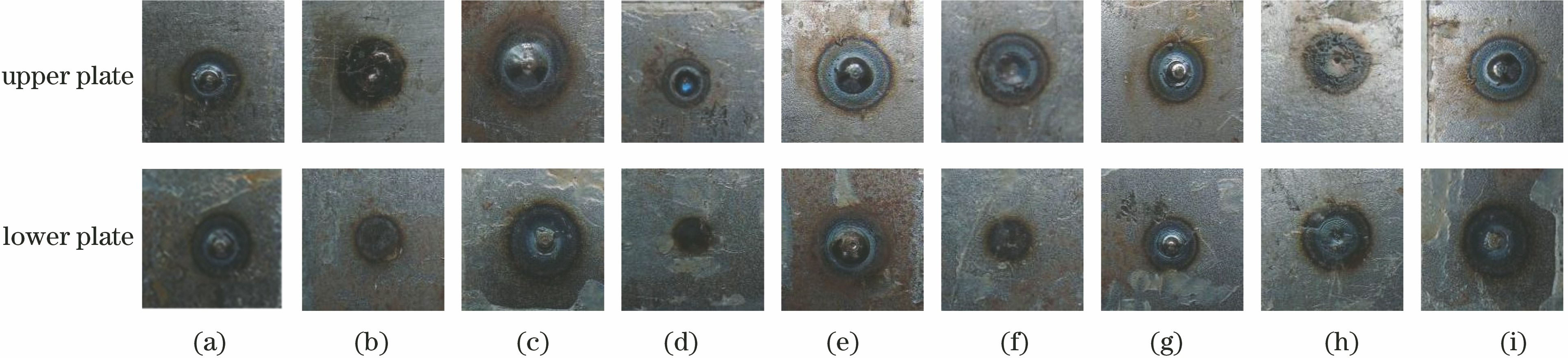
图 3. 1~9组焊点表面形态。 (a)第1组;(b)第2组;(c)第3组;(d)第4组;(e)第5组;(f)第6组;(g)第7组;(h)第8组;(i)第9组
Fig. 3. Surface morphologies of solder joints in 1-9 groups. (a) Group 1; (b) group 2; (c) group 3; (d) group 4; (e) group 5; (f) group 6; (g) group 7; (h) group 8; (i) group 9

图 4. 超声C扫描图像。(a)第1组;(b)第7组;(c)第9组
Fig. 4. Ultrasonic C-scanning images. (a) Group 1; (b) group 7; (c) group 9
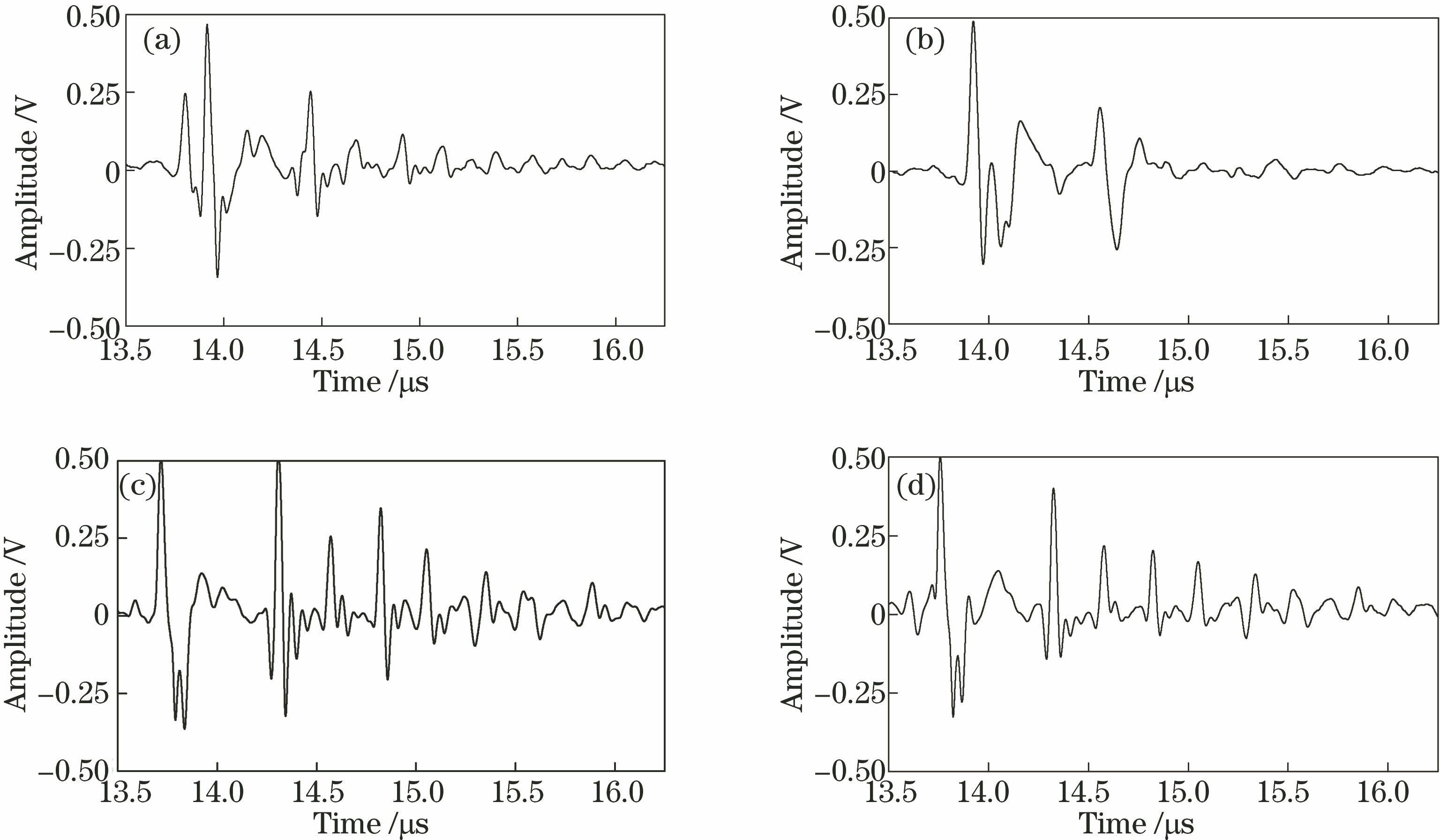
图 5. 接头不同区域的超声A扫描信号。(a)焊核区;(b)热影响区;(c)胶层区;(d)空腔区
Fig. 5. Ultrasonic A-scan signals of joints in different regions. (a) Nugget zone; (b) heat-affected zone; (c) adhesive zone;(d)cavity zone
3.2 工艺参数与拉剪性能
对正交试验后得到的9组接头进行重复的拉伸剪切试验,获得了接头的平均峰值载荷数据,如
表 4. 接头的峰值载荷
Table 4. Peak load of joints
|
对三个工艺参数对应的峰值载荷进行计算后得到极差数据,如
表 5. 三个工艺参数下峰值载荷的极差分析
Table 5. Range analysis for peak loads under three process parametersN
|
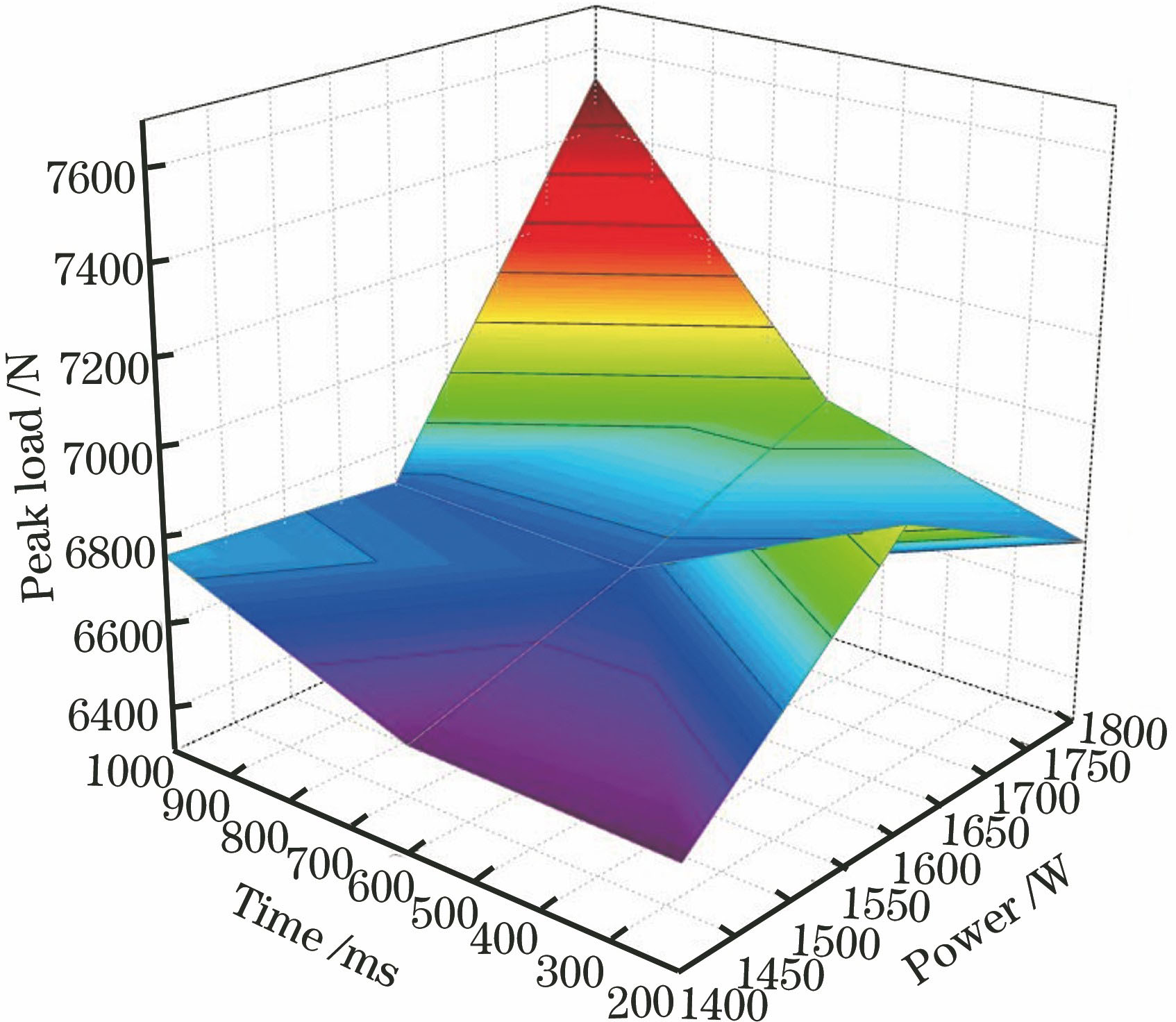
图 6. 焊接时间和焊接功率对峰值载荷的交互作用
Fig. 6. Interactive effect of laser power and welding time with peak loads
3.3 拉剪断口分析
选取正交试验中峰值载荷高、中、低三个水平的点焊接头,利用SEM观察其拉剪断口宏观形貌和不同位置的微观断口形貌。第1,7,9组的拉剪断口宏观形貌如
激光胶接点焊接头焊点断裂区不同位置的拉剪微观断口如
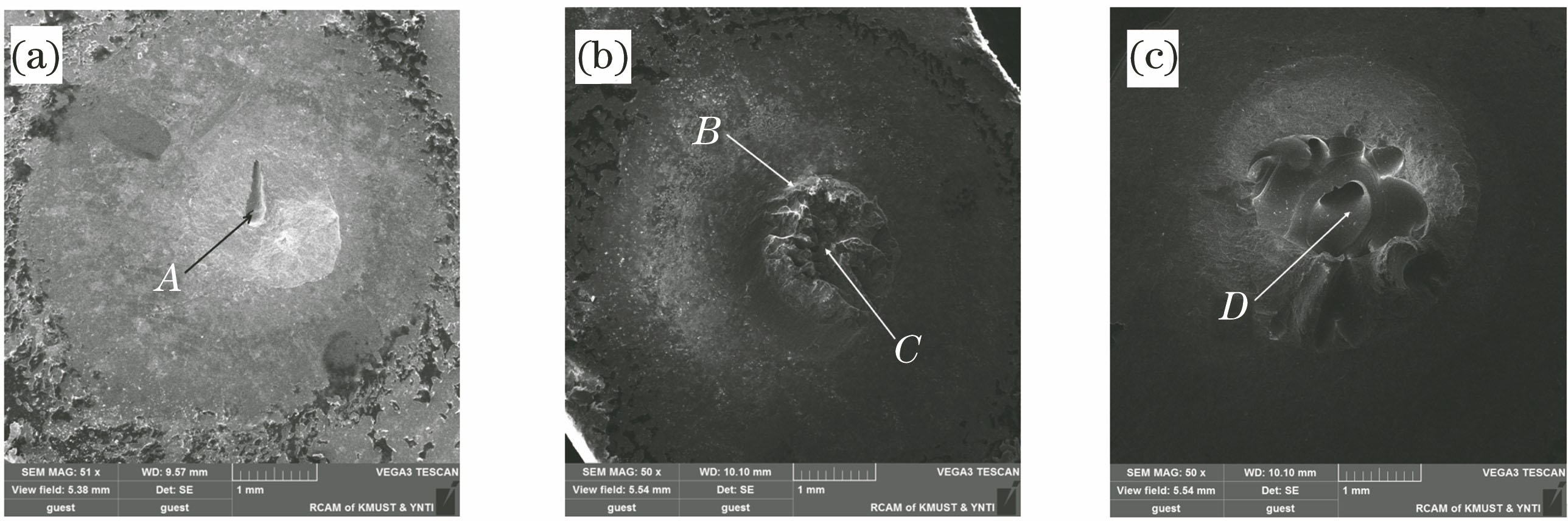
图 7. 断口的宏观形貌。(a)第1组;(b)第7组;(c)第9组
Fig. 7. Macro-morphologies of fatigue fractures. (a) Group 1; (b) group 7; (c) group 9
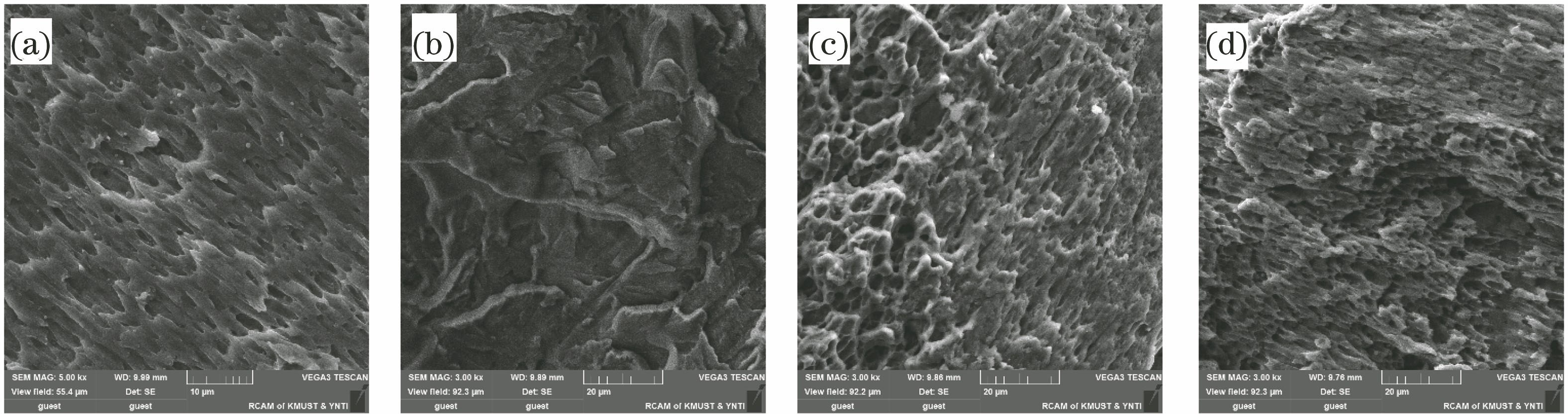
图 8. 断口的微观形貌。(a) A点;(b) B点;(c) C点;(d) D点
Fig. 8. Micro-morphologies of fatigue fractures. (a) Point A; (b) point B; (c) point C; (d) point D
4 结论
以焊接功率、离焦量和焊接时间为参数,对DP590双相钢钢板进行了激光胶接点焊的正交试验,得到如下结论。
1) 当焊接功率为1800 W、焊接时间为1000 ms、离焦量为-3 mm时,激光胶接点焊接头的平均峰值载荷最大,为7529.30 N。通过极差分析可知,焊接功率对接头的静强度影响最大,焊接时间次之,离焦量的影响最小。
2) 结合超声A扫描信号,可将激光胶接点焊接头超声C扫描图像分为焊核区、热影响区、空腔区及胶层区,且能有效测量激光焊点的直径,高、中、低失效载荷下接头对应的焊核直径分别为2.27,2.99,3.23 mm,胶焊接头抗拉强度与激光焊点直径呈正相关。
3) 平均峰值载荷分别为高、中、低的三组接头在拉剪过程中的失效过程均为胶层先断裂,随后激光焊点界面处发生断裂失效,在激光焊点断裂区的断口处观察到剪切力作用下形成的拉长韧窝。
[1] 范子杰, 桂良进, 苏瑞意. 汽车轻量化技术的研究与进展[J]. 汽车安全与节能学报, 2014, 5(1): 1-16.
Fan Z J, Gui L J, Su R Y. Research and development of automotive lightweight technology[J]. Journal of Automotive Safety and Energy, 2014, 5(1): 1-16.
[2] 周惦武, 李宁宁, 徐少华, 等. 双相钢/铝合金激光胶接焊胶层作用分析[J]. 机械工程学报, 2016, 14: 25-30.
Zhou D W, Li N N, Xu S H, et al. Analysis of the adhesive layer of laser weld bonding joints in dual phase steel/aluminum alloy[J]. Journal of Mechanical Engineering, 2016, 14: 25-30.
[3] 董丹阳, 王观军, 马敏, 等. 车用双相钢激光焊接接头组织性能研究[J]. 中国激光, 2012, 39(9): 0903002.
[5] 马轶男, 陶汪, 陈彦宾. LF6铝合金双光束激光点焊工艺研究[J]. 红外与激光工程, 2014, 43(3): 707-711.
Ma Y N, Tao W, Chen Y B. Laser spot welding of LF6 aluminum with double laser beams[J]. Infrared and Laser Engineering, 2014, 43(3): 707-711.
[6] 吕涛, 雷正龙, 陈彦宾, 等. 焊点形状对TC4钛合金激光点焊力学性能的影响[J]. 中国激光, 2013, 40(12): 1203002.
[7] 任大鑫, 刘黎明. 镁合金激光胶接焊胶层作用分析[J]. 机械工程学报, 2009, 45(8): 266-270.
Ren D X, Liu L M. Analysis of the adhesive layer of laser weld bonding joints in magnesium alloy[J]. Journal of Mechanical Engineering, 2009, 45(8): 266-270.
[9] 王铭茂, 陶汪, 马轶男, 等. 激光胶接复合点焊工艺特性[J]. 焊接学报, 2012, 33(7): 101-104.
Wang M M, Tao W, Ma Y N. Research on laser spot weld-bonding process characteristics[J]. Transactions of the China Welding Institution, 2012, 33(7): 101-104.
[10] 刘申, 马轶男, 陶汪, 等. 钛合金激光点焊胶接复合接头组织性能研究[J]. 中国激光, 2014, 41(12): 1203004.
Article Outline
冯煜阳, 曾凯, 何晓聪, 孙鑫宇, 韦涛. 双相钢激光胶接点焊及接头强度分析[J]. 激光与光电子学进展, 2018, 55(3): 031404. Yuyang Feng, Kai Zeng, Xiaocong He, Xinyu Sun, Tao Wei. Laser Spot Weld Bonding and Joint Strength Analysis of Dual-Phase Steels[J]. Laser & Optoelectronics Progress, 2018, 55(3): 031404.