火炮身管内壁检测系统的数据处理方法研究
1 引言
管道在生活中的应用随处可见,其中火炮身管[1-3]是**领域中应用最广泛的管道,其质量对火炮的射击精度和其它技术指标都有着重要的影响。身管参数对于身管使用寿命的评估有重要的参考价值,直径、椭圆度、膛线深度等都是身管测量中重要的测试指标。同时,在某些情况下,为了能够直观地获得身管内壁表面信息,身管的轮廓重建也是测量系统的重要组成部分。但是由于火炮身管长径比大,内部存在膛线,所以身管内壁检测技术一直是研究的难点和热点。
随着光电及激光技术的发展,基于结构光法[4]、激光投影[5]、激光扫描法[6]等光电检测法[7]逐步成为主要的检测方法。光电检测法可以通过非接触测量实现身管内壁的检测,且装置的自动化程度、工作效率等均高于传统的检测方法。激光扫描法通过逐点扫描实现测量,可以实现管道内壁的局部和整体的检测,实现身管参数的定量测量。但是基于激光扫描的检测方法数据采集量大,数据转换环节复杂,选取合适的数据处理方法获取身管信息也是检测系统的重要环节。
吕乐[8]基于激光测距传感器的原理设计了管道内径测量仪,提出了内径数据的处理方法。但是对于带有膛线这样特殊结构的管道,该方法并不适用。龙续林[9]基于激光三角法设计了火炮身管内壁检测系统并进行了数据的采集,实现了身管内壁表面的三维轮廓重建,对于身管参数的检测并没有提出具体的方法。杨璐[10]基于激光三角法设计了身管内膛检测系统,将图像与传感器信息相结合获取身管内壁信息,只能获取瑕疵信息。崔唯佳[11]基于激光位移传感器设计了内径测量系统,实现了内径的测量,对于膛线部分数据的处理以及其他参数的测量并没有提出具体的数据处理方法。
针对激光扫描法测量数据量大,数据处理环节复杂且身管结构复杂,对于如何从大量数据中获取身管有效信息的问题,在完成基于激光位移传感器[12]系统搭建的基础上,根据实际测量中的数据采集情况,提出了完整的数据处理方法,分析了系统存在的误差并采取方法控制与校正,并基于最小二乘法[13-14]获取了身管内壁内径,膛线深度等参数。
1 数据采集方法及测量模型
检测系统主要由爬行子系统、测量子系统、位置测量单元和控制子系统构成。系统所采用的测量方案如
数据采集的流程如
基于激光位移传感器的测量子系统是整个测量系统的核心,激光位移传感器发出的激光在管壁发生散射或者反射,返回的光线进入接收器,获得管壁每一点的距离信息。激光位移传感器的安装方式如
本文中的待测对象为155 mm口径的身管,膛线深度约为3 mm,选取的激光位移传感器的测量范围为−10 mm~10 mm,激光位移传感器最佳测量范围为距离待测物体50 mm,所以测量模型中的具体参数为:
测量系统在实际测量中选取的参数如
表 1. 测量系统参数
Table 1. Measuring system parameters
|
2 系统误差与修正方法
2.1 系统姿态误差
由于机械结构加工存在一定误差,且在系统安装的过程容易出现轴向倾斜及周向偏移的情况。在轴倾斜的情况下,激光位移传感器扫描一周所成的闭合曲线为椭圆,示意图如
系统的轴向倾斜量不会很大,假设轴向倾斜量为1
系统发生周向偏移的情况下,激光位移传感器采集数据的起点会发生变化,对于轴向不同位置处截面的同一点直径的测量,会发生偏差,示意图如
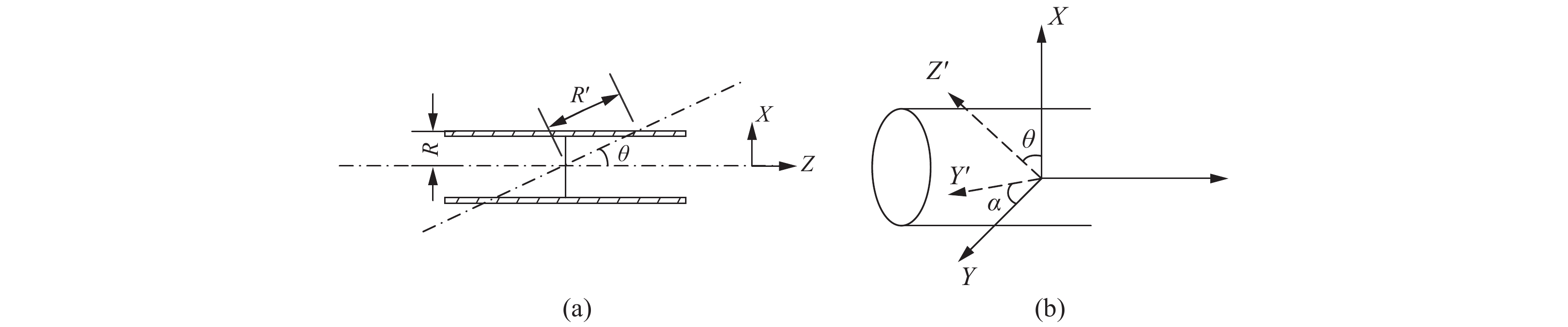
图 4. Schematic diagram of system position error
Fig. 4. Schematic diagram of system position error
设每一点的半径测量值为
2.2 激光位移传感器安装误差
激光位移传感器理想的安装情况是激光束垂直于待测表面,但是由于安装误差的存在,激光束与待测表面可能存在一定角度[15],如
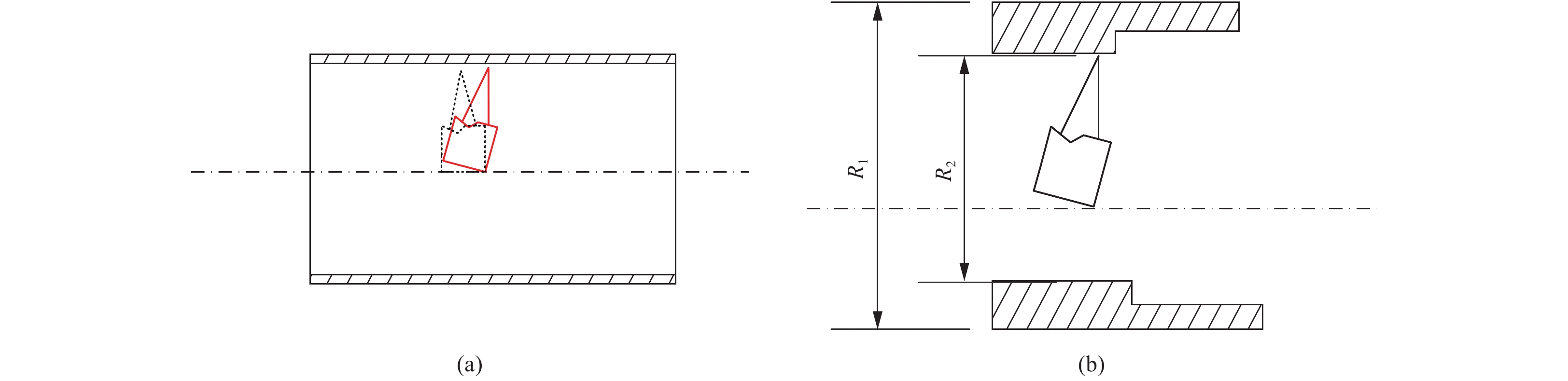
图 5. Schematic diagram of laser displacement sensor installation error and correction
Fig. 5. Schematic diagram of laser displacement sensor installation error and correction
同时激光位移传感器安装还存在常数误差,在线性补偿值确定后,任意选取某一半径的圆环进行测量,将测量值
在补偿激光位移传感器误差之后,可以修正(1)式为
对激光位移传感器的安装误差修正后,还需要对系统的偏心情况进行分析,系统的偏心示意图如
对于同一个圆而言,不同位置处的半径值相同。根据(5)式~(7)式可以看出,半径值测量结果与角度大约成余弦平方根曲线关系。系统对于偏心误差的修正方法为:首先根据最小二乘法获取该截面的圆心,然后重新计算每一点相对于该圆心的新的坐标值,将重新计算后的数据作为每一测量点修正偏心误差后的值。
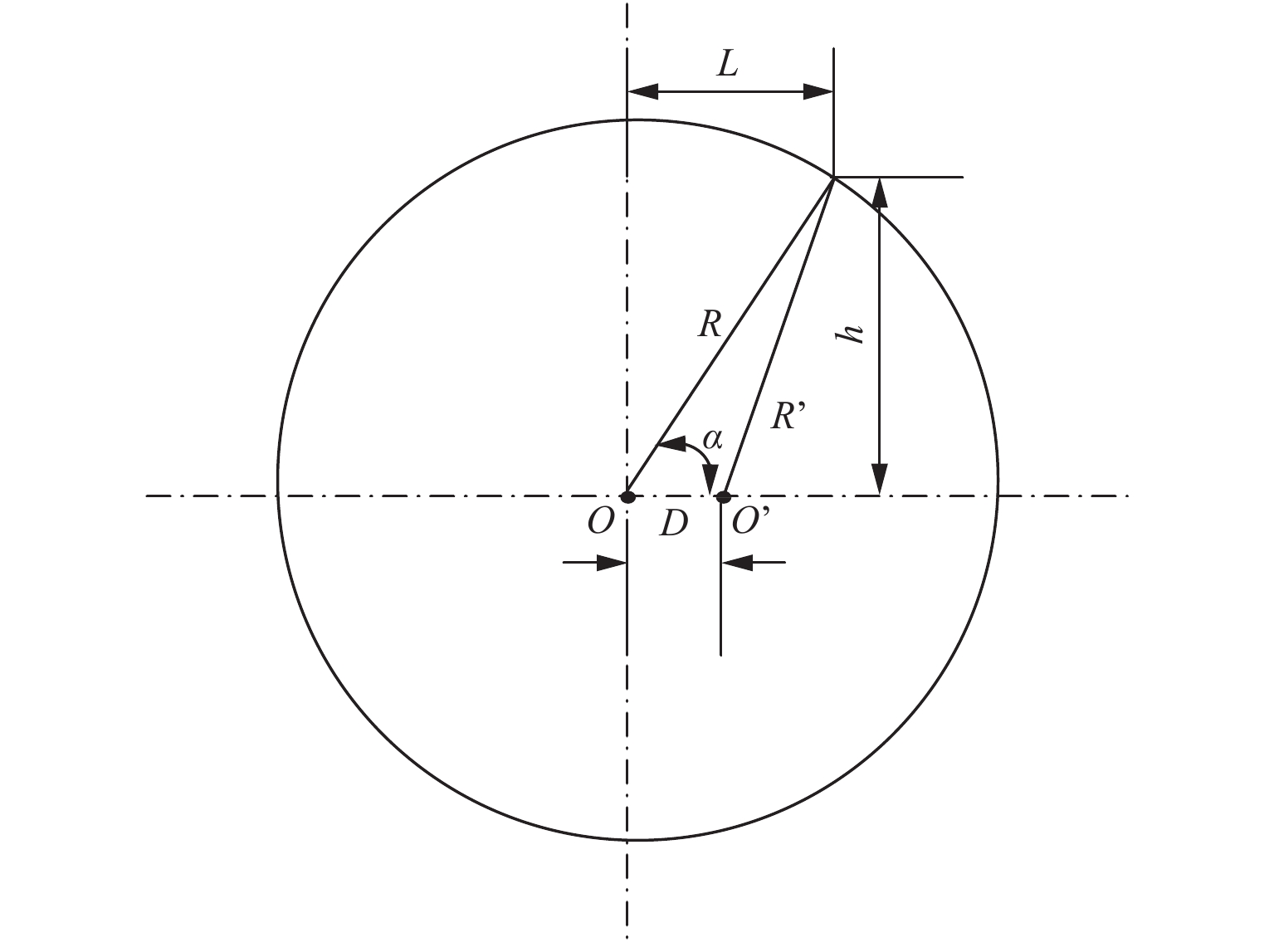
图 6. Schematic diagram of measuring eccentricity
Fig. 6. Schematic diagram of measuring eccentricity
3 轮廓与参数获取算法
3.1 轮廓还原算法
激光位移传感器在在管中测量情况如
根据多次测量结果分析,当旋转速度为0.01 r/s时,基本不存在数据丢失情况。但是身管长径比大,如果数据采集速度很慢,测量整个身管花费时间长,实际使用时非常不方便。这也是选取0.1 r/s作为测量系统的默认旋转速度的原因,对于错误数据通过后续的数据处理来进行修正。
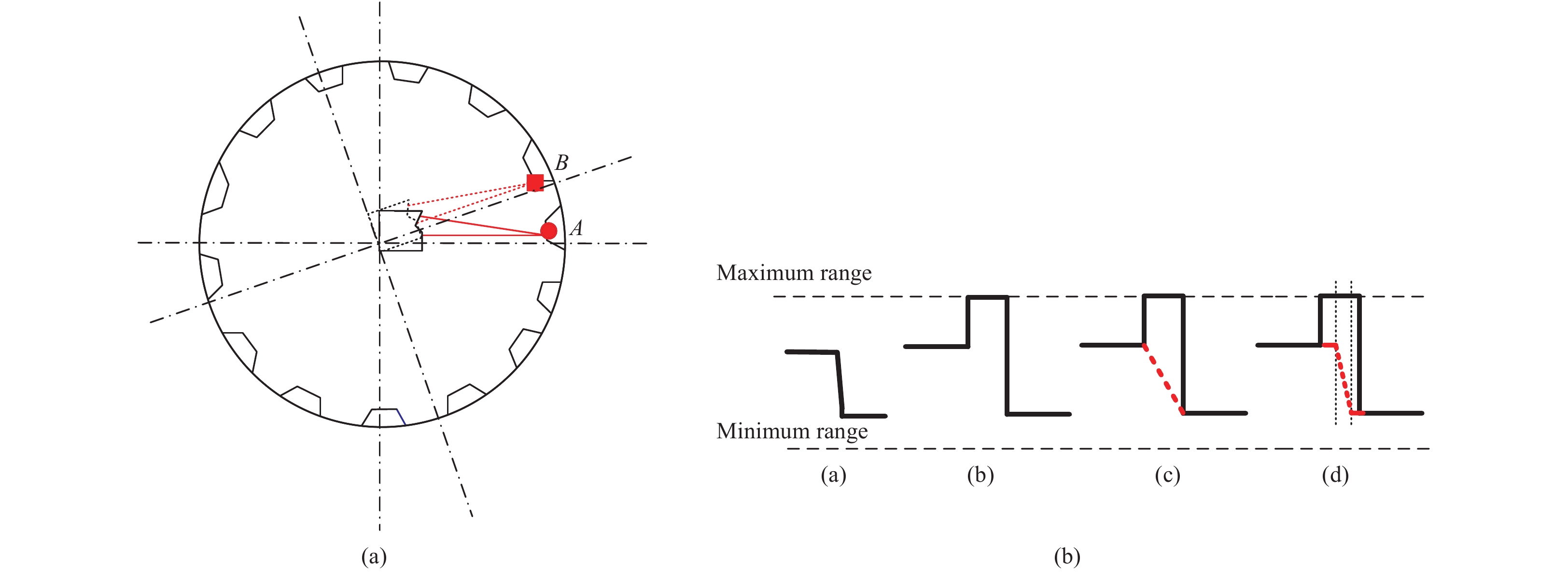
图 7. Schematic diagram of laser displacement sensor measurement
Fig. 7. Schematic diagram of laser displacement sensor measurement
正常情况下测量的数据如
根据实际中测量情况,提出了两种数据修正的方法。第一种方法是直接查找错误点的区间,对于区间内的错误点直接进行插值计算,从而还原膛线形状,示意图如
3.2 参数获取算法
身管结构特殊,内部存在膛线,在利用最小二乘法拟合求取身管内壁参数时,发现膛线的过渡部分对于实际的拟合结果存在很大的影响。同时为了准确获取身管内壁参数,设计了分离膛线数据的算法,对分离后的数据进行最小二乘法拟合,可以进一步提高测量精度。
分离膛线的数据过程如
对于提取后的数据进行极坐标系和直角坐标系的转换后,通过最小二乘法拟合,即可更准确地获取身管的内径、椭圆度[16]以及膛线深度参数。
4 实验
4.1 标定管实验
对系统进行误差修正以后,选取标定半径值为77.537 0 mm的截面进行测量。将激光位移传感器测试数据转换为半径值后,绘制每一点半径值与角度的关系,如
选取标定管另一半径为77.535 3 mm的圆环进行测量,对采集后的数据进行误差修正后转换到直角坐标系下,其测量结果如
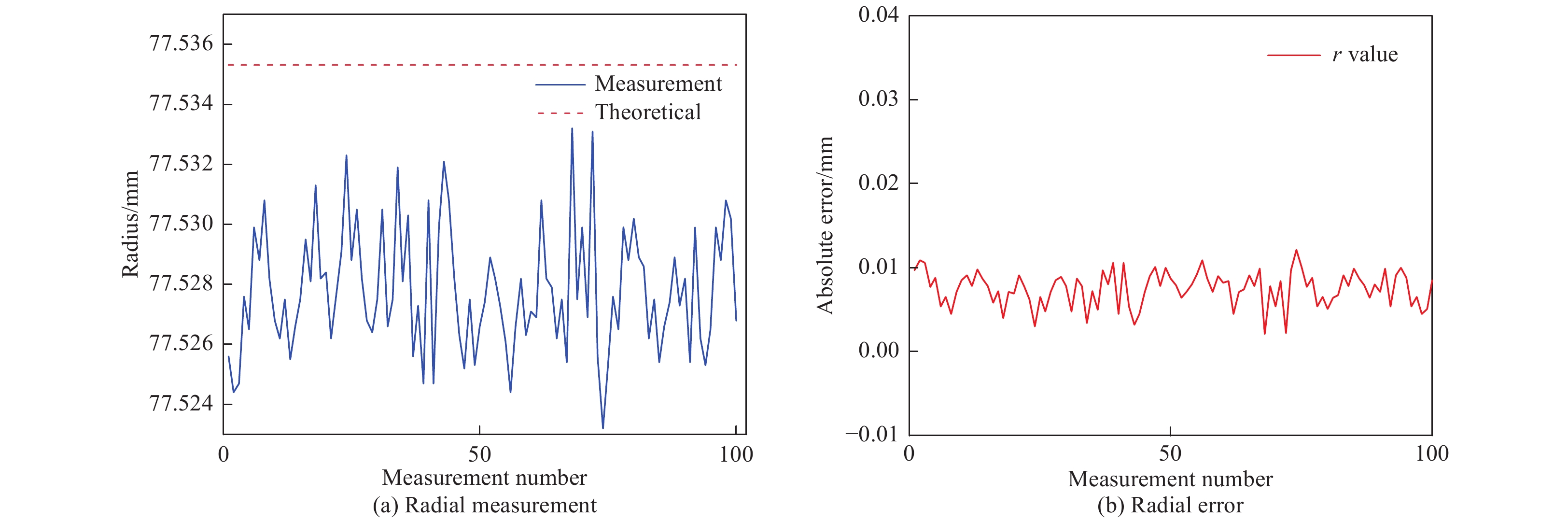
图 10. Measurement results of calibration barrel
Fig. 10. Measurement results of calibration barrel
4.2 实际测量实验
利用标定后的系统对实际身管以轴向间隔200 mm测量35次,以距离管口位置100 mm处的位置为初始位置,系统的位置测量单元实时记录系统在身管内的轴向位置,利用上位机软件处理系统对于某一截面处的原始数据进行处理,测量结果如
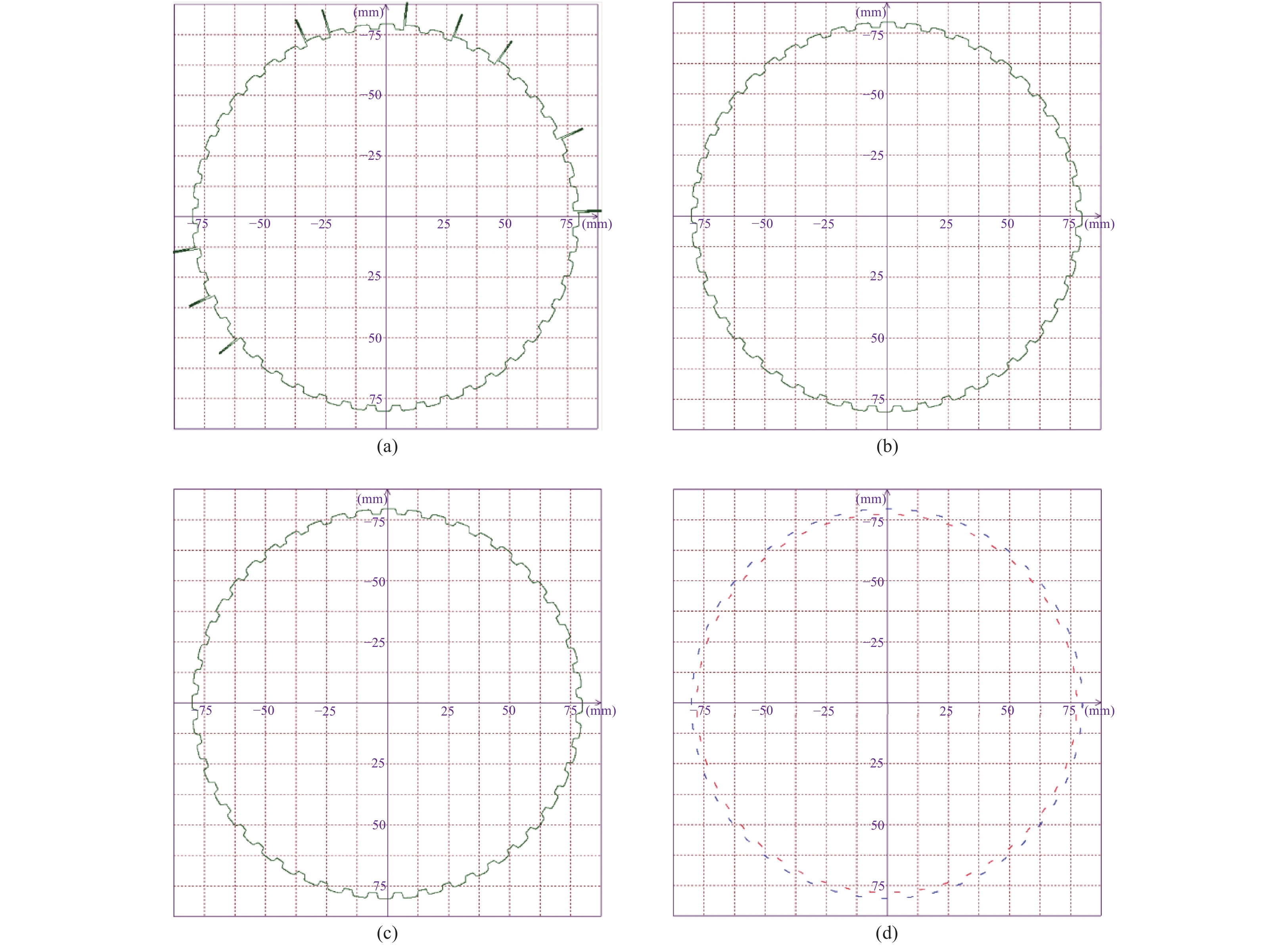
图 11. Interface display of data processing software
Fig. 11. Interface display of data processing software
将两种处理方法处理后的数据与慢速采集(0.01 r/s)的正确数据对比,对应数据点之间的半径误差计算通过逐点求差得到。运行时间取多次运行时间的平均值,结果如
分别选取轴向距离1 500 mm、3 500 mm和5 500 mm处的测量数据进行身管内壁参数的求取。分别获取阴线和阳线的内径、椭圆度以及膛线深度,测量结果如
表 3. 轴向位置1 500 mm、3 500 mm和5 500 mm处测量数据
Table 3. Measurement data at axial positions 1 500 mm, 3 500 mm and 5 500 mm
|
5 结论
火炮身管内壁检测系统是重要的检测系统,可以为管道寿命等使用参数的评估提供重要的依据。火炮身管内壁结构复杂导致检测困难以及数据采集质量不高,数据处理和分析方法不足导致系统一直未能发挥应有的作用。本文在完成搭建基于激光位移传感器火炮身管内膛参数检测系统的基础上,提出了身管内壁轮廓还原方法和膛线数据分离方法,通过最小二乘法拟合获得身管内壁参数,同时对系统在测量过程中可能存在的误差进行了分析和控制校正。通过实际测量实验验证了数据处理方法的正确性以及系统的精度,对火炮身管的检测有重要的参考价值。
[3] 蒋泽一, JIANG Zeyi, LI Qiang, 李强, 薄玉成, BAO Yucheng. Study on the life of gun body tube[J]. Mechanical Engineering & Automation, 2014(2): 221-222.
[5] 王坚, WANG Jian, 任现君, REN Xianjun, SU Jiangang, 苏建刚. Measurement for the flaws in the inner wall of a artillery pipe based on laser projection method[J]. China Measurement & Testing Technology, 2004(5): 16-17, 54.
[7] 邱娜, QIU Na, YU Xiaolong, 于小龙. Application analysis of photoelectric technology in automated measurement and detection[J]. Technology Innovation and Application, 2019(21): 167-168.
[8] 吕乐, LYU Yue, WANG Changming, 王昌明, 包建东, BAO Jiandong. Inner diameter measurement system of small-caliber based on LabVIEW[J]. Journal of Test and Measurement Technology, 2014, 28(2): 123-126.
[9] 龙续林. 基于激光位移传感器的火炮身管内膛检测系统研究[D]. 南京: 南京大学, 2015.LONG Xulin. Research on gun barrel be detecting system based on laser displacement sens[D]. Nanjing: Nanjing University, 2015.
[10] 杨璐, YANG Lu, 王惠源, WANG Huiyuan, 张鹏军, ZHANG Pengjun. Design of artillery barrel inner bore detection system based on laser triangulation[J]. Automation & Instrumentation, 2018, 33(12): 44-48.
[11] 崔唯佳. 高精度内径测量系统的研究与设计[D]. 太原: 中北大学, 2013.CUI Weijia. The research design of highprecision diameter measurement system[D]. Taiyuan: Nth University of China, 2013.
[12] 朱万彬, ZHU Wanbin. Laser displacement sensor using in shape measurement[J]. Ome Information, 2010, 27(10): 70-72.
[13] 鲁铁定, LU Tieding, DENG Xiaoyuan, 邓小渊, 常晓涛, CHANG Xiaotao. Analysis of total least squares algorithms for circular curve fitting[J]. Science of Surveying and Mapping, 2019, 44(2): 33-37.
[14] 苏楠, 朱大明. 圆曲线拟合两种求解方法的比较研究[C]云南省测绘地理信息学会2016年学术年会论文集. 昆明: 云南省科学技术协会, 2016: 144148.SU Nan, ZHU Daming. Comparative study of two methods f solving circular curve fitting[C]Proceedings of 2016 Academic Annual Meeting of Yunnan Surveying Mapping Geographic Infmation Society, Kunming: Yunnan Science Technology Association, 2016: 144148.
[15] 刘红轩, LIU Hongxuan, QU Xinghua, 曲兴华, 邢书剑, XING Shujian. Large-scale diameter measuring system based on laser triangulation[J]. Computer Measurement & Control, 2011, 19(3): 506-508.
Article Outline
黄战华, 岳富军, 张光, 王星宇, 张尹馨. 火炮身管内壁检测系统的数据处理方法研究[J]. 应用光学, 2020, 41(2): 248. Zhanhua HUANG, Fujun YUE, Guang ZHANG, Xingyu WANG, Yinxin ZHANG. Research on data processing method of gun barrel inner wall detection system[J]. Journal of Applied Optics, 2020, 41(2): 248.