Pulse reference-based compensation technique for intensity-modulated optical fiber sensors
Download: 713次
Intensity-modulated optical fiber sensors (IM-OFSs) are one of the most important and earliest developed OFSs for their simplicity, using inexpensive light sources, and potential low cost. In past decades, IM-OFS have been well studied to detect several types of physical quantities such as displacement[1], temperature[2,3], bending[4], strain[5], magnetic field intensity[6], and others[7,8]. However, owing to directly using optical intensity as the information carrier, IM-OFSs have the problem that the output might be affected by the fluctuation of the light source, the change of optical components transmission loss, and the coupler splitting ratio, as well as other factors with time and external perturbations. Many compensation techniques were proposed to solve this problem: the light source negative-feedback compensation technique[9], the light split compensation technique[3,10], the twin-receiving-fiber compensation technique[11], the dual-wavelength compensate technique[12], the network-based compensation technique[13], and the neural-network compensation technique[14]. The performances of the IM-OFSs were improved[15
In this Letter, we propose a compensation technique based on pulse reference. This compensation technique can compensate the power fluctuation of the light source, the change of optical components transmission loss, and the coupler splitting ratio, while at the same time keeping the structure simple and the design flexible for a wide application range. Another advantage of this compensation technique is that it is completely compatible with optical time division multiplexing system, which can integrate a large number of sensors and decrease the cost of per sensor. After the explanation of this technique, an optical microfiber temperature sensor was carried out to demonstrate the good compensation effect of this technique.
The schematic diagram of the pulse reference-based compensation technique is shown in Fig.
The time delay
Here,
We define a measurement parameter, relative loss (RL) of the sensing part, from Eqs. (
It is obvious that RL is unrelated to the initial light pulse intensity
So, if we keep
To demonstrate the effect of the pulse reference-based compensation technique, a temperature-sensing experiment based on a fiber coating-covered optical microfiber was carriedout with this techniqueout, as shown in Fig.
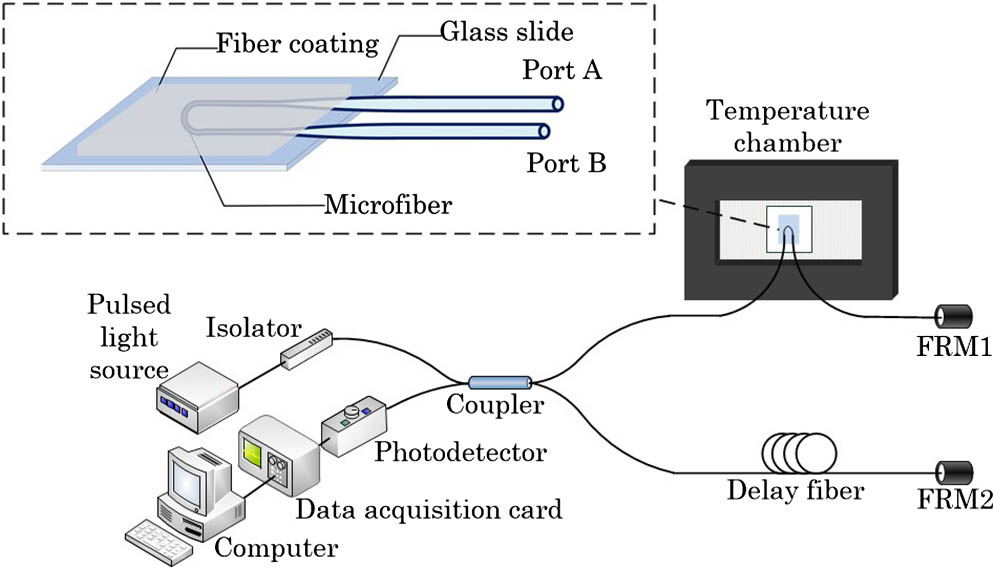
Fig. 2. Schematic diagram of the temperature OFS based on the fiber coating-covered optical microfiber with the pulse reference-based compensation technique.
A 1.55 μm wavelength semiconductor pulsed laser (Connet, Pulsed Fiber Laser Source, VSLC-1559-M-P) with 250 ns pulse width and 10 kHz repeat frequency was used as the light source. The laser line width is about 40 nm. The relative length between the sensing fiber and the delay fiber was set to be 60 m, providing a 600 ns time delay. Two Faraday rotating mirrors (FRMs) were used as reflectors. The sensing head, which was fabricated utilizing an optical microfiber covered by a fiber coating, was placed in a temperature chamber. The pulses were detected by the photodetector (New Focus, Model 2053) with an 80 MHz bandwidth. The amplitudes of the signal pulses and reference pulses were converted into digital data by data acquisition card NI PXIe-5122 with a 100M sample rate. All data was dealt by LabVIEW software in a computer to get the average voltage value of each pulse for further calculation.
The sensing optical microfiber used in this experiment was drawn from a conventional single-mode fiber (SMF) with the modified flame-brush method[20]. The diameter of the drawn optical microfiber is
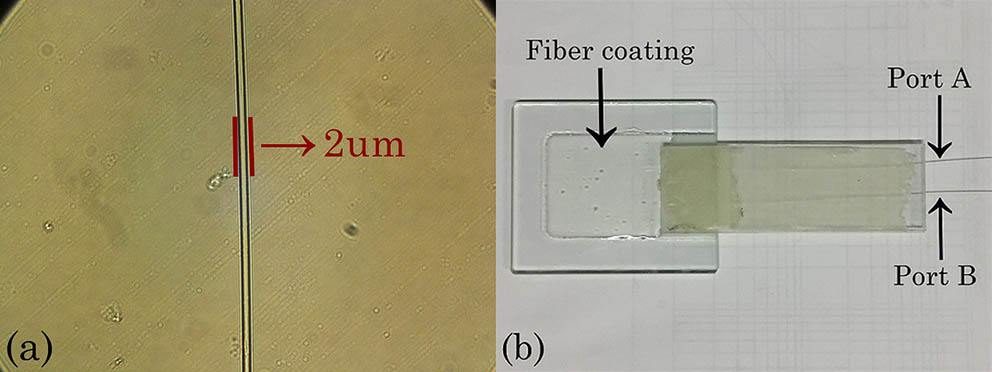
Fig. 3. (a) The microscope photograph of the drawn optical microfiber. (b) The photograph of the optical microfiber covered by fiber coating
Because of the optical microfiber’s excellent optical properties, such as large evanescent field, compact size, and low loss, it can be utilized as a good alternative material for sensing. When light passes through the optical microfiber, there is a large fraction of power propagating outside the optical microfiber as an evanescent field that makes it very sensitive to the change of external physical quantities[21]. The absorption coefficient of the fiber coating changes accordingly when the external temperature changes, altering the transmittance of the fiber coating-covered optical microfiber in the meantime[3]. In this experiment,
For convenience we choose a specific
The external temperature of the sensing head was controlled by the temperature chamber. The RL decreases from
The system noise is much lower than that of conventional IM-OFSs[3,21–
Long-term stability is also a key index for a temperature sensor. The
To evaluate the influence of the fluctuation of the light source and the change of optical components transmission loss and coupler loss, an attenuator was inserted between the isolator and the fiber optic coupler to simulate those influences at room temperature. By setting the attenuator, the light intensity of the incident pulse decreased by 1 dB per minute until the loss reached 3 dB and then gradually returned to its original value in the next few minutes. We detected
In conclusion, a compensation technique for IM-OFSs based on pulse reference is proposed in this Letter. A temperature sensing experiment using fiber coating-covered optical microfiber was designed and carried out to demonstrate the compensation effect. With this compensation technique, the system noise is only 0.0005 dB, much lower than that of conventional IM-OFSs. The sensitivity of the temperature sensor is
The further improvement on this compensation effect can be done in terms of the polarization state, the laser line width, and the bias problem. The compensation technique also shows its potential in time division multiplexing and quasi-distributed sensing in the case of a suitable lightpath design. Our follow-up work will be carried out in these aspects.
[1]
[2]
[3]
[4]
[6]
[7]
[8]
[9]
[10]
[11]
[12]
[13]
[14]
[15]
[17]
[18]
[19]
[20]
[21]
[22]
[23]
[24]
Qiang Bian, Zhangqi Song, Yuzhong Chen, Xueliang Zhang. Pulse reference-based compensation technique for intensity-modulated optical fiber sensors[J]. Chinese Optics Letters, 2017, 15(12): 120603.