多激光束与中轴热丝复合沉积(熔覆)结合的新工艺
下载: 700次
1 引言
金属激光直接沉积的同步送料方式主要有送粉和送丝两种,同步送粉方式的原料是金属粉末,以高压气体为载体将金属粉末送入加工区,在激光的作用下熔化、凝固成形。该方法具有沉积效率高、成形零件致密度高等优点,但具有一定的不确定性,粉末流一部分不经过激光的作用区域,导致粉末利用率低,易造成浪费和环境污染;且未被激光熔化的粉末粘附于工件表面,会在一定程度上影响工件的表面精度与粗糙度;金属粉末的制备工艺复杂、成本高,这也影响了送粉激光沉积成形技术的进一步应用[1-3]。
近年来,一种以丝材为原料、激光为热源的送丝激光沉积技术逐渐发展[4],丝材成本相对较低且易获得,送粉方式为刚性送入,易实现精确控制,沉积效率高,利用率可达100%,具有良好的发展前景。丝材的喂入方式主要包括侧向送丝和同轴送丝,其中侧向送丝方式是在激光垂直照射基板时,丝材以一定的角度送入,并在工件表面与激光束进行耦合。该方法在某一个扫描方向进行沉积时可以成形,在另外一个方向无法保持稳定的沉积过程,所以,熔道方向性问题极大地限制了其进一步应用。
苏州大学石世宏等[5]提出了“光束中空,光内送丝”的同轴送丝激光沉积技术,该技术采用圆锥-圆环双反射镜将入射的实心圆形激光束在工件表面变换为一束环形光,丝材垂直于工件表面送入。该方法基本消除了沉积时熔道的方向性问题,在采用丝材进行连续三维实体沉积上迈出了重要一步,但丝材到达工件表面之前要穿过激光束,这就使得工作头结构、送丝管设置和激光功率分布都有严格限制。此外,由于基体材料和丝材只靠激光熔化成形,丝材与激光耦合的精度要求高、工艺窗口小,沉积效率难以提高[6-7]。激光热丝焊利用电阻热将焊丝预热后送入熔池,减小了焊丝熔化对激光能量的依赖,不仅降低了焊丝与激光相对位置的精度要求,同时提升了填充效率,是一种具有良好发展前景的技术[8-10]。基于目前送粉和送丝激光沉积技术的现状,本文提出一种多激光束与中轴热丝复合直接沉积相结合的新工艺。
2 基本原理
多激光束与中轴热丝直接沉积结合的技术具有如下特点:1)丝材、送丝通道与多激光束同轴且垂直于基板表面,成形过程中不受扫描方向的影响,丝材不与多激光束发生干涉,送丝圆弧通道曲率大,丝材变形小;2)丝材被多个激光束均匀包裹,受热均匀,熔池形成均匀,有助于提高熔覆层质量;3)不同离焦量下丝材与多激光束同轴,实现了光、丝精确耦合;4)加热电流可以减小对激光能量的依赖,有助于扩大工艺窗口,提高加工效率。
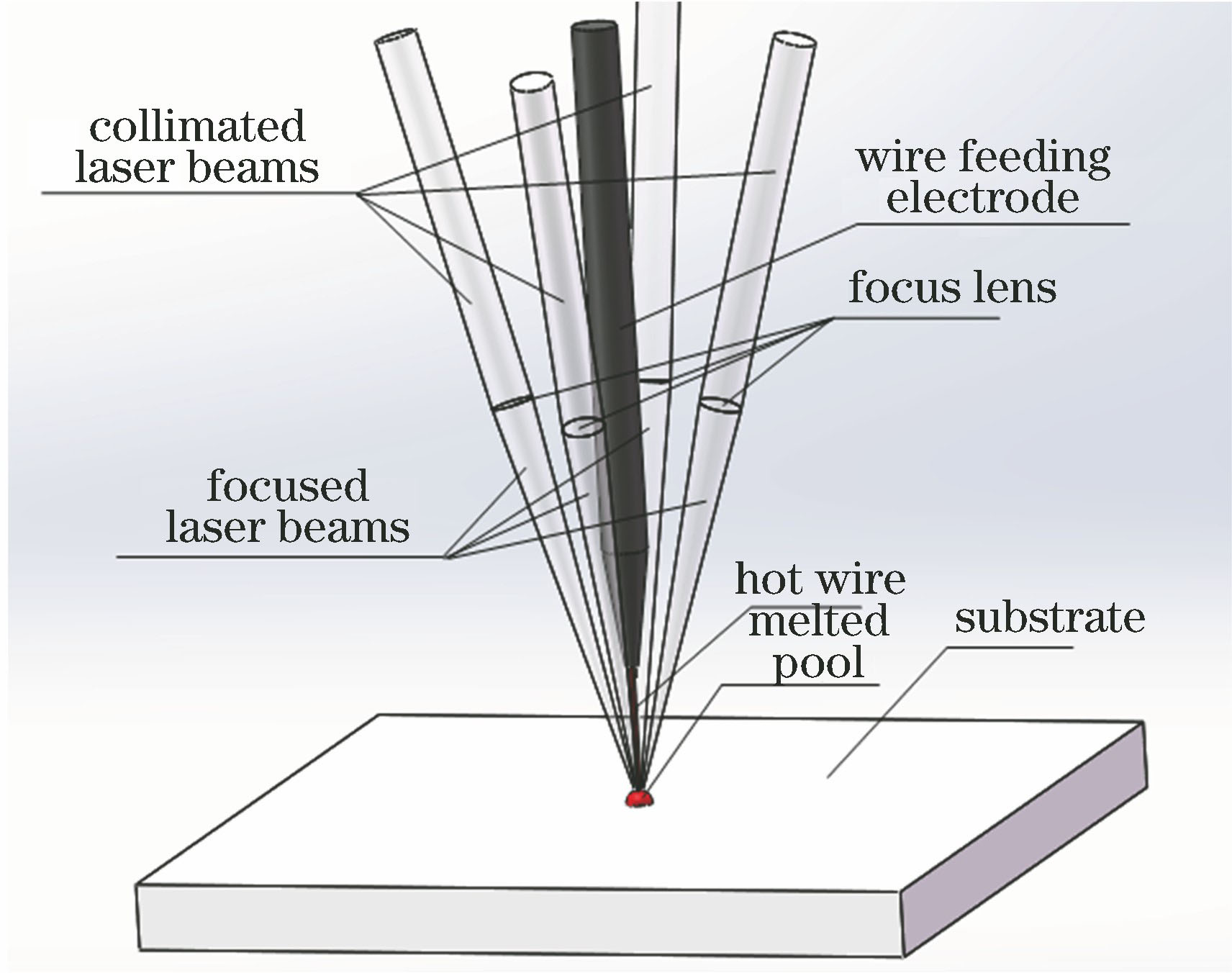
图 1. 多激光束结合中轴热丝复合沉积示意图
Fig. 1. Schematic of multi-beam laser and on-centerline hot wire hybrid deposition
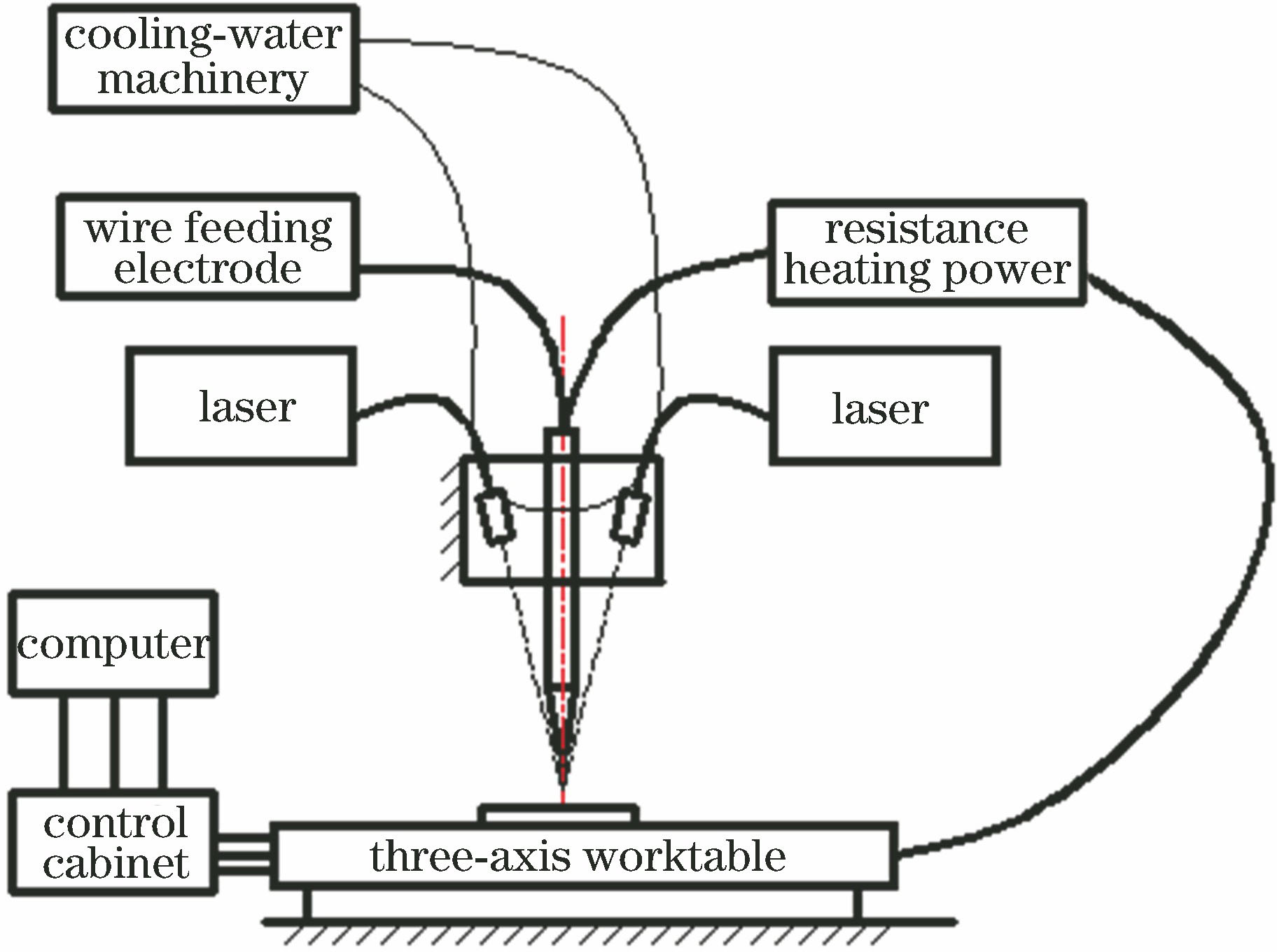
图 2. 多激光束结合中轴热丝复合沉积系统
Fig. 2. System of multi-beam laser and on-centerline hot wire hybrid deposition
3 试验装置
设计最简易的2束激光进行试验。
4 沉积试验
4.1 单道沉积试验
分别进行激光冷丝单道沉积试验和激光热丝单道沉积试验。其中激光冷丝沉积试验的主要工艺参数为激光总功率、送丝速度、扫描速度,激光热丝沉积试验则多了1个工艺参数——加热电流。
由前期试验可知,为了使得沉积过程稳定且可持续,必须采取激光焦点负离焦。采用直径为0.8 mm的镀锌铁丝,基板材料为45钢,单道冷丝激光沉积试验工艺参数如下:扫描速度为2.5 mm/s,送丝速度为10 mm/s,激光总功率为500 W(各组试验中2束激光功率都相同,求和得到激光总功率)。结果如
单道热丝激光沉积试验工艺参数如下:扫描速度为5 mm/s,送丝速度为20 mm/s,激光总功率为500 W,加热电流为20 A。结果如
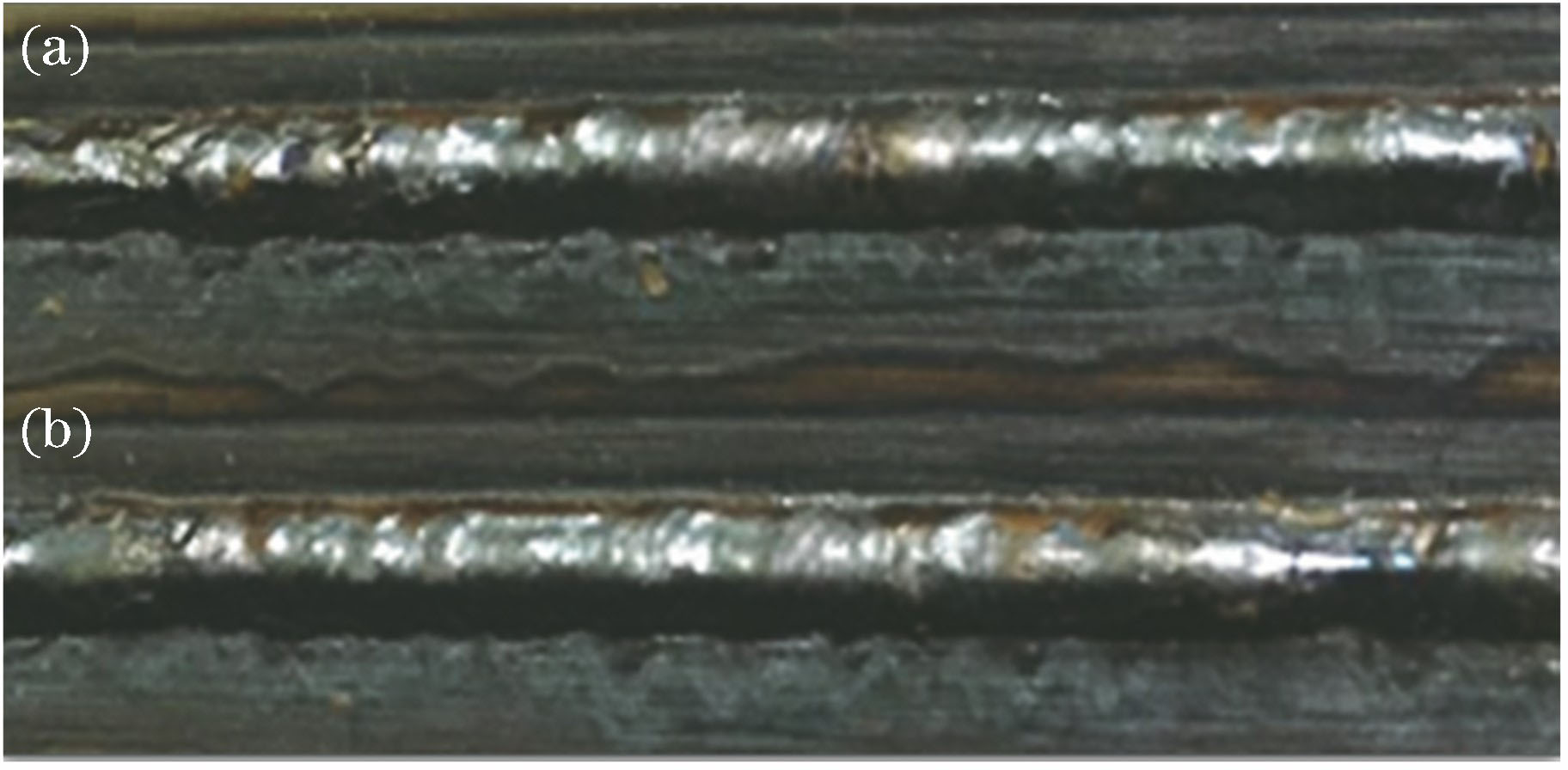
图 3. 不同沉积方式的单道沉积形貌。(a)冷丝沉积;(b)热丝沉积
Fig. 3. Morphologies of single-pass deposition with different deposition methods. (a) Deposition of cold wire; (b) deposition of hot wire
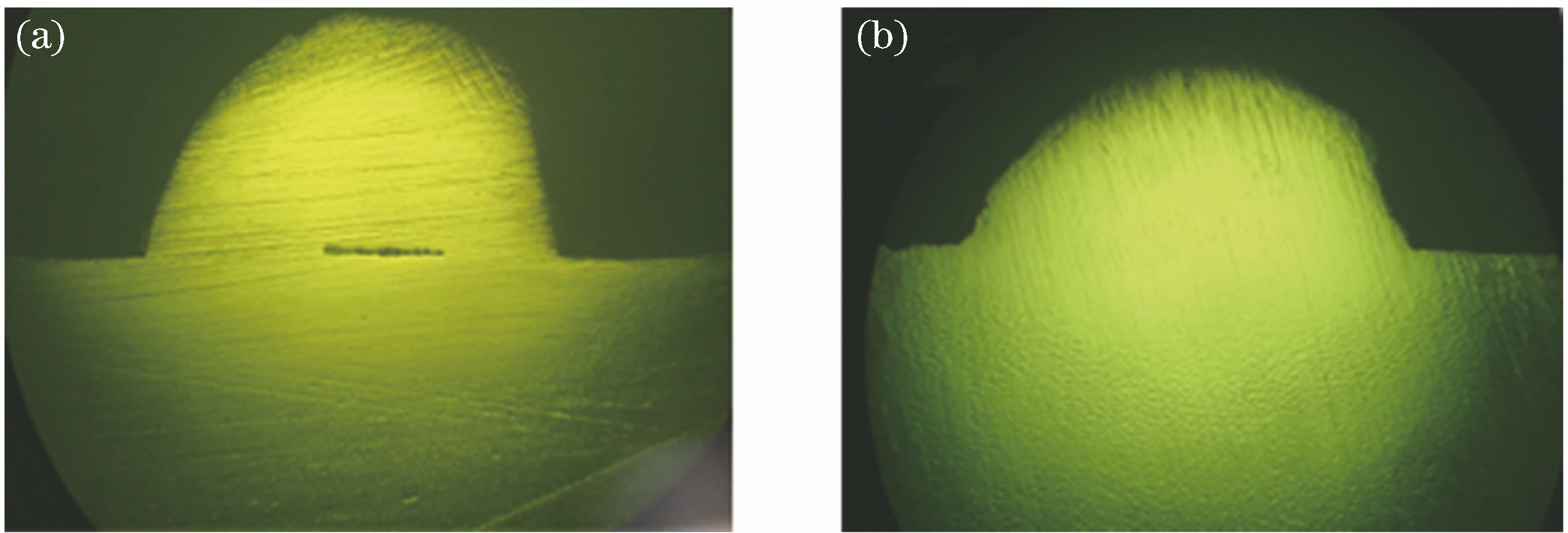
图 4. 不同沉积方式的单道沉积带横截面。 (a)冷丝沉积; (b)热丝沉积
Fig. 4. Cross-sections of single-pass deposition bead of wire with different deposition methods. (a) Deposition of cold wire; (b) deposition of hot wire
激光热丝沉积试验中新引入了一个工艺参数——加热电流,加热电流与激光束在沉积过程中所扮演的角色类似,都是为送丝沉积过程提供热量。加热电流虽然不能完全代替激光在工件表面上形成熔池,但是几乎可以在丝材进入熔池前将丝材烧到红热状态,因为在整个加热电流形成的回路中,熔池的温度最高,故其电阻也相应最大,加热电流在熔池中产生的热量也最多,即在适宜的工艺参数下,工件表面一旦形成熔池,加热电流即可为熔池持续输入能量而不破坏熔池的稳定性。
4.2 沉积扫描方向试验
2束激光围绕送丝中轴线在同一平面入射工作区,丝材在中轴线垂直进入工作区,在不同的扫描方向,丝材与工件表面的角度无变化,工件表面均可形成熔池。采用直径为0.8 mm的镀锌铁丝,基板材料为45钢,选取扫描速度为5 mm/s,送丝速度为20 mm/s,激光总功率为500 W,加热电流为20 A,沿着2束激光所形成平面的法线方向来回沉积单道,结果如
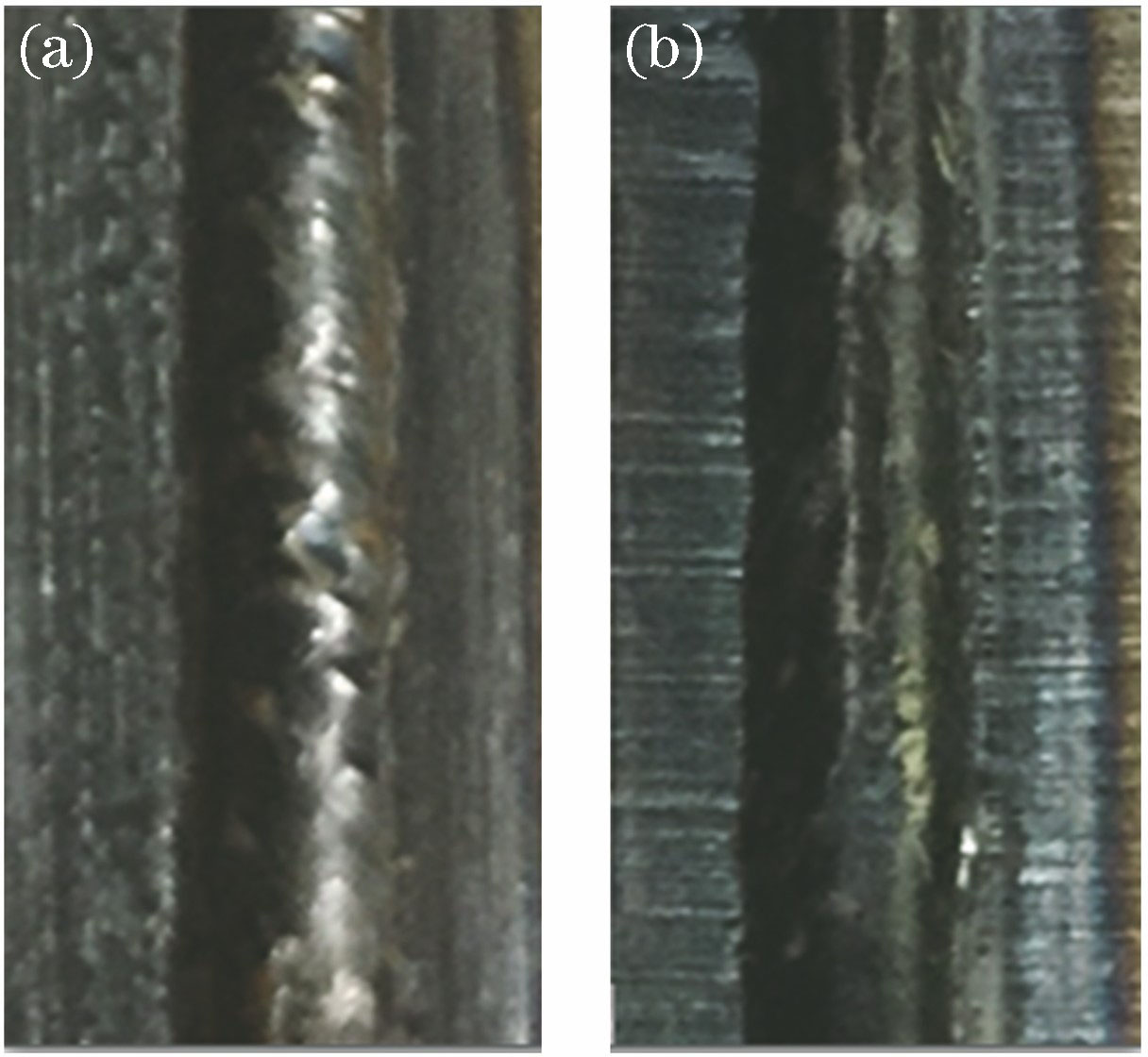
图 6. 不同扫描方向对沉积试验的影响。(a)从上至下; (b)从下至上
Fig. 6. Influence of scanning direction on deposition. (a) From top to bottom; (b) from bottom to top
4.3 单层多道搭接沉积试验
在单道沉积试验的基础上,进行单层多道搭接沉积试验,采用直径为0.8 mm的镀锌铁丝,基板材料为45钢,选取主要的工艺参数如下:扫描速度为5 mm/s,送丝速度为20 mm/s,激光总功率为500 W,加热电流为20 A,搭接率为35%,结果如
4.4 薄壁沉积试验
薄壁加工现场如
4.5 实体沉积试验
实体沉积试验的参数如下:镀锌铁丝的直径为0.8 mm,基板材料为45钢,选取扫描速度为5 mm/s,送丝速度为20 mm/s,第1层激光总功率为700 W,后将激光总功率逐层减小,加热电流为20 A,搭接率为40%。成形件为高15 mm、长40 mm、宽10 mm的长方体实体,如
5 结论
提出一种“众星捧月”式多激光束于中轴热丝复合直接沉积相结合新工艺,该工艺沉积过程稳定且可持续,熔道表面光滑、均匀,无毛刺、球化等缺陷。冷丝与热丝单道沉积对比试验结果表明,输入相同的激光总功率时,热丝激光沉积的效率高于冷丝激光沉积的效率,且熔覆带与基板容易结合,晶粒细小,组织均匀。进一步采用多激光束与中轴热丝复合直接沉积相结合的新工艺进行单层、薄壁与实体等沉积成形,发现沉积表面搭接良好,不受扫描方向的影响,实体高度均匀,表面无塌陷,表明该工艺具有很好的应用前景。已知丝材的利用率达到100%,引入加热电流后加工效率提高,而电流加热是能源利用率最高的手段之一,故此项新工艺具有巨大的应用价值和现实意义。
[1] 梁朝罡, 邓琦林. 5): 26-28, Ⅳ[J]. . 激光熔覆制造致密金属零件送料方式的分析和比较. 电加工与模具, 2003.
Liang C G. 5): 26-28, Ⅳ[J]. Deng Q L. A comparison with different material feeding methods of laser direct manufacturing metallic dense-component based on laser cladding technology. Electromachining & Mould, 2003.
[2] 董敢. 同轴送粉激光熔覆熔池数值模拟[D]. 长沙: 湖南大学, 2013.
DongG. Numerical simulation of molten pool in coaxial powder-feed laser cladding[D]. Changsha: Hunan University, 2013.
[3] 杨楠, 杨洗陈. 激光熔覆中粉嘴流场的数值模拟[J]. 中国激光, 2008, 35(3): 452-455.
[4] 任丽丽, 刘金平, 冯英超. 金属部件送丝增材制造工艺研究现状[J]. 金属加工(热加工), 2017( 12): 64- 68.
Ren LL, Liu JP, Feng YC. Research status of manufacturing technology of wire feeding and adding materials for metal components[J]. MW Metal Forming, 2017( 12): 64- 68.
[5] 石世宏, 傅戈雁, 李龙, 等. 中空激光光内同轴送丝熔覆工艺的实现及其试验研究[J]. 中国激光, 2010, 37(1): 266-270.
[6] 李洪远. 激光光内同轴送丝熔覆快速制造技术研究[D]. 苏州: 苏州大学, 2012.
Li HY. Research on laser cladding rapid manufacturing with coaxial inside-beam wire feeding[D]. Suzhou: Soochow University, 2012.
[7] 杨国家. 激光光内同轴送丝熔覆工艺研究[D]. 苏州: 苏州大学, 2008.
Yang GJ. Study on inside-laser coaxial wire feeding process of laser cladding[D]. Suzhou: Soochow University, 2008.
[8] NurminenJ, RiihimakiJ, NakkiJ, et al. Comparison of laser cladding with powder and hot and cold wire techniques[C]∥International Congress on Applications of Lasers & Electro-Optics, October 30-November 2, 2006, Scottsdale, Arizona, USA. USA: AIP, 2006: 634- 637.
[9] 肖荣诗, 左铁钏, Günter A, 等. 电流强化铝合金CO2激光焊接[J]. 中国激光, 2004, 31(3): 359-362.
[10] 温鹏, 郑世卿, 单际国, 等. 36(9): 17-20, Ⅱ[J]. . 激光热丝焊电阻热控制及送丝参数优化. 焊接学报, 2015.
Wen P, Zheng S Q, Shan J G, et al. 36(9): 17-20, Ⅱ[J]. optimization of wire feeding parameters in laser hot wire welding. Transactions of the China Welding Institution, 2015.
陈金选, 刘继常. 多激光束与中轴热丝复合沉积(熔覆)结合的新工艺[J]. 激光与光电子学进展, 2019, 56(24): 241402. Jinxuan Chen, Jichang Liu. Novel Process of Multi-Beam Laser and On-Centerline Hot Wire Hybrid Deposition (Cladding)[J]. Laser & Optoelectronics Progress, 2019, 56(24): 241402.