GCr15轴承钢表面的激光凹/凸微织构工艺
下载: 1002次
1 引言
表面织构作为改善摩擦副表面性能的一种新型技术,对提高机械系统承载能力和使用寿命有着积极的作用[1-4]。在诸多的表面织构技术中,激光织构技术因具有设备简易、成本低、加工速度快、加工质量好、织构形貌易控制等特点,得到更广泛的应用[5-6]。Hoppermann等[7]对比了多种表面织构技术,发现激光表面织构技术在加工效率、质量及可控性方面具有显著优势。
凹坑(槽)以及毛化凸起织构是应用最广泛的两种表面织构形貌,通过优化的排列方式,合理设计表面织构,可以有效改善接触表面的摩擦特性。微凹坑能够减小对偶副接触面积、增强流体动压效应、捕捉磨损颗粒、储存释放润滑剂,这些特性使其广泛应用于推力轴承、缸套-活塞环系统、机械密封等机械系统关键摩擦副表面[8-9]。毛化形貌具有微凸起的结构特征,可以改变两个接触面表面的摩擦特性,同时可以有效分离两接触面,降低材料之间的粘着与吸附,毛化形貌也因此广泛应用于轧辊、磁盘及模具表面[10-11]。
国内外学者针对激光表面织构的工艺可控性做了大量的研究工作。Vilhena等[12]利用Nd∶YAG激光器在100Cr6试样表面上进行凹坑加工以改善接触表面的摩擦学性能并优化激光参数,研究了激光加工参数对凹坑三维形貌的影响规律。黄志辉等[13]基于冲击强化技术在Al7075表面开展微凹坑造型研究,考察了脉冲能量、冲击次数、离焦量、约束层K9玻璃厚度对凹坑形貌的影响,设计需求的凹坑形貌。张培耘等[14]利用固体激光器在45#钢材料表面进行织构试验研究,发现通过选择合适的激光加工工艺参数,可加工出高质量的凹坑形貌。钱振华[15]对关节轴承内圈进行微凹坑和微凹槽的激光织构工艺试验,通过对不同脉冲重复次数、重叠度等条件下试验数据的分析,掌握微凹坑和微凹槽几何形状和分布的控制方法,得到表面形貌参数可控的激光微织构。Liu[16-17]利用YAG激光器对轧辊试样表面进行织构加工,通过优化激光工艺参数实现特殊毛化形貌-球冠状凸起形貌的加工,为激光毛化加工工艺参数的优化及应用提供了重要参考。靳广林等[18]研究了激光能量、脉冲个数以及辅助气体对激光表面微造型尺寸的影响,发现脉冲个数对微坑直径和凸起的影响有限,辅助气体对微造型的变化有一定的影响趋势,带有凸起的微造型试样有着更好的摩擦学性能。叶云霞等[19]利用波长1064 nm的脉冲激光在45#钢表面进行凸起造型试验,得到三种典型形貌(球冠状、墨西哥帽状和M状),提出凸起形貌是激光与材料作用过程中热、力耦合作用的结果,通过试验与数值计算指导控制凸起形貌,优化摩擦学金属表面。
在现有的研究工作中,微凹坑织构主要是利用短脉宽激光的气化作用形成,而毛化织构则主要是通过长脉宽激光的熔凝作用形成,采用同一台激光器很难同时实现凹/凸形貌加工。在工业化应用中常常需要在同一表面实现凹凸复合形貌加工,但现有技术一般通过两台激光器来实现,单一的织构形貌加工对于工业化应用非常不利,其效率低、成本高,应用受到限制。本文利用英国SPI光纤微秒激光系统功率、脉宽等参数覆盖范围较广的特点,结合自主开发的数控技术,系统研究了不同激光加工参数对织构形貌的影响规律,分析了不同形貌形成作用机理,验证了同一激光器同时实现凹/凸织构的可行性。本研究有助于激光织构技术的产业化推广,具有重要的工程应用价值。
2 试验
2.1 试验准备
试验材料选用GCr15轴承钢,试验中试样尺寸为30 mm×30 mm×10 mm,试样表面经砂纸打磨及抛光后的粗糙度
表 1. SPI光纤激光器参数
Table 1. Parameters of SPI fibre laser
|
2.2 试验方案
采用单因素轮换试验法考察功率、脉宽、重复次数等激光主要参数对织构形貌的影响,试验过程中控制激光头处于焦点位置。具体试验方案如下:
1) 采用200#、400#、600#、800#、1000#、1200#砂纸依次打磨,并进行抛光处理;
2) 将试样装夹在工作台上,依次改变功率为10,30,50,70,90 W,脉宽为500,1000,5000,10000,20000 μs,重复次数为1,5,10,15。每个参数加工5次,尺寸参数取5次平均值;
3) 将加工好的试样放入超声波清洗机中清洗15 min后取出吹干;
4) 利用德国NanoFocus共聚焦显微镜(μsurf mobile)对试样表面进行测量。
3 结果与讨论
3.1 单次作用功率和脉宽对形貌的影响
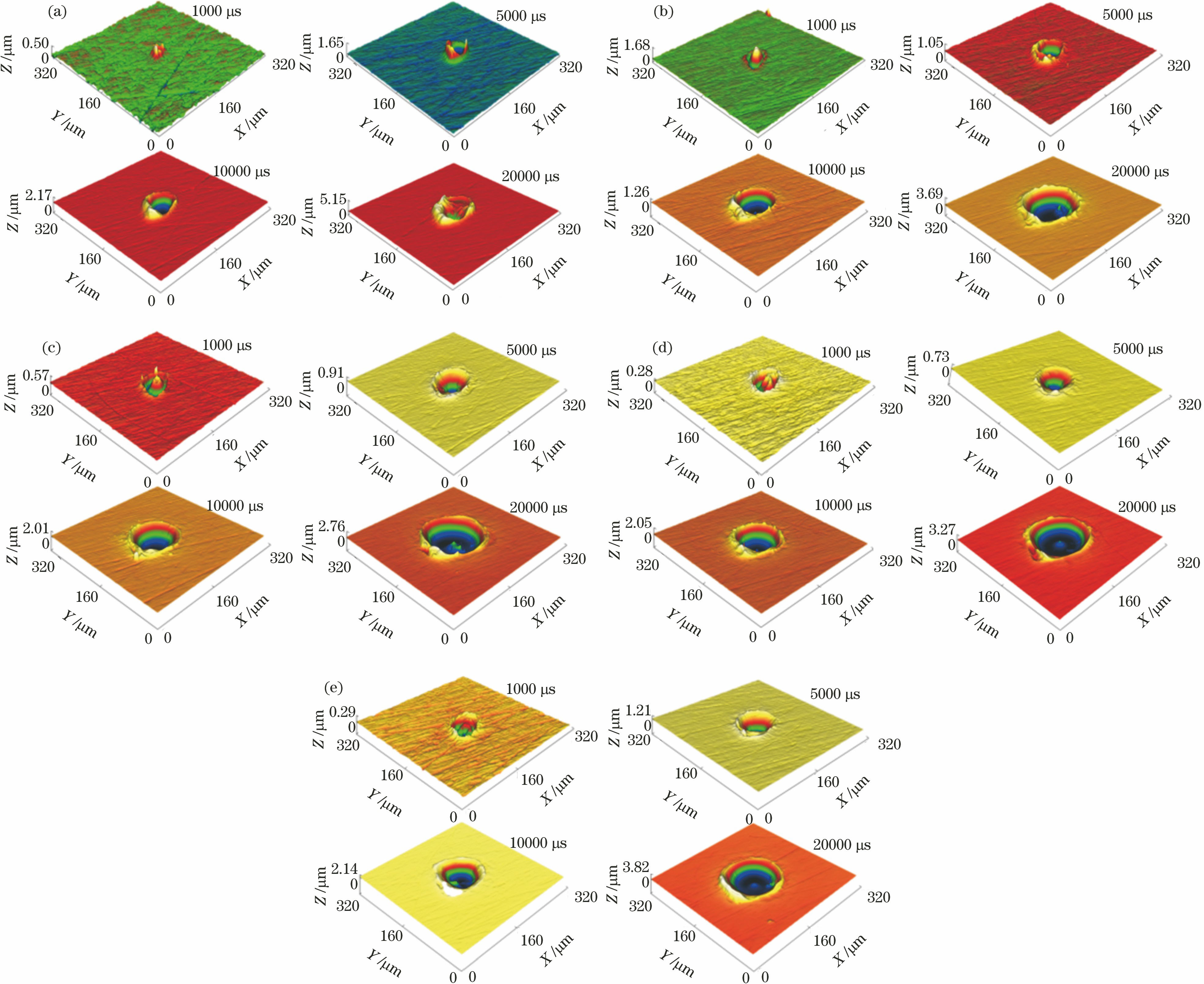
图 1. 不同功率下织构点形貌随脉宽的变化。(a) 10 W;(b) 30 W;(c) 50 W;(d) 70 W;(e) 90 W
Fig. 1. Morphology changes of textured point with pulse width at different powers. (a) 10 W; (b) 30 W; (c) 50 W; (d) 70 W; (e) 90 W
当脉宽为1000 μs时,材料快速发生重熔,重熔区表面张力发生改变,由于光斑为高斯分布,熔池中心温度最高,其表面张力大于四周,导致熔池中较强的向内Marangoni流动[20],因此材料向中心流动,中心区域形成了“微凸体”形貌。当脉宽增大至5000 μs以上时,中心部位凸起被“削平”,随着脉宽增大,逐渐形成越来越大的“凹坑”,单个脉冲作用时间增大,热量发生累积,中心部位受热最多,部分材料达到气化阈值,材料气化去除,且由于激光作用时间较长,中心表面张力逐渐与四周趋同,但中心区受热影响较大,材料不断重熔流向四周,因此最终织构点中心部位形成深度较大的凹坑,而四周部位凸起高度也逐渐增大。
为了进一步定量分析织构点形貌与功率和脉宽的关系,用NanoFocus共聚焦显微镜观测织构轮廓形貌,绘制不同功率下织构点直径、凸起高度、深度随脉宽变化关系,分别如
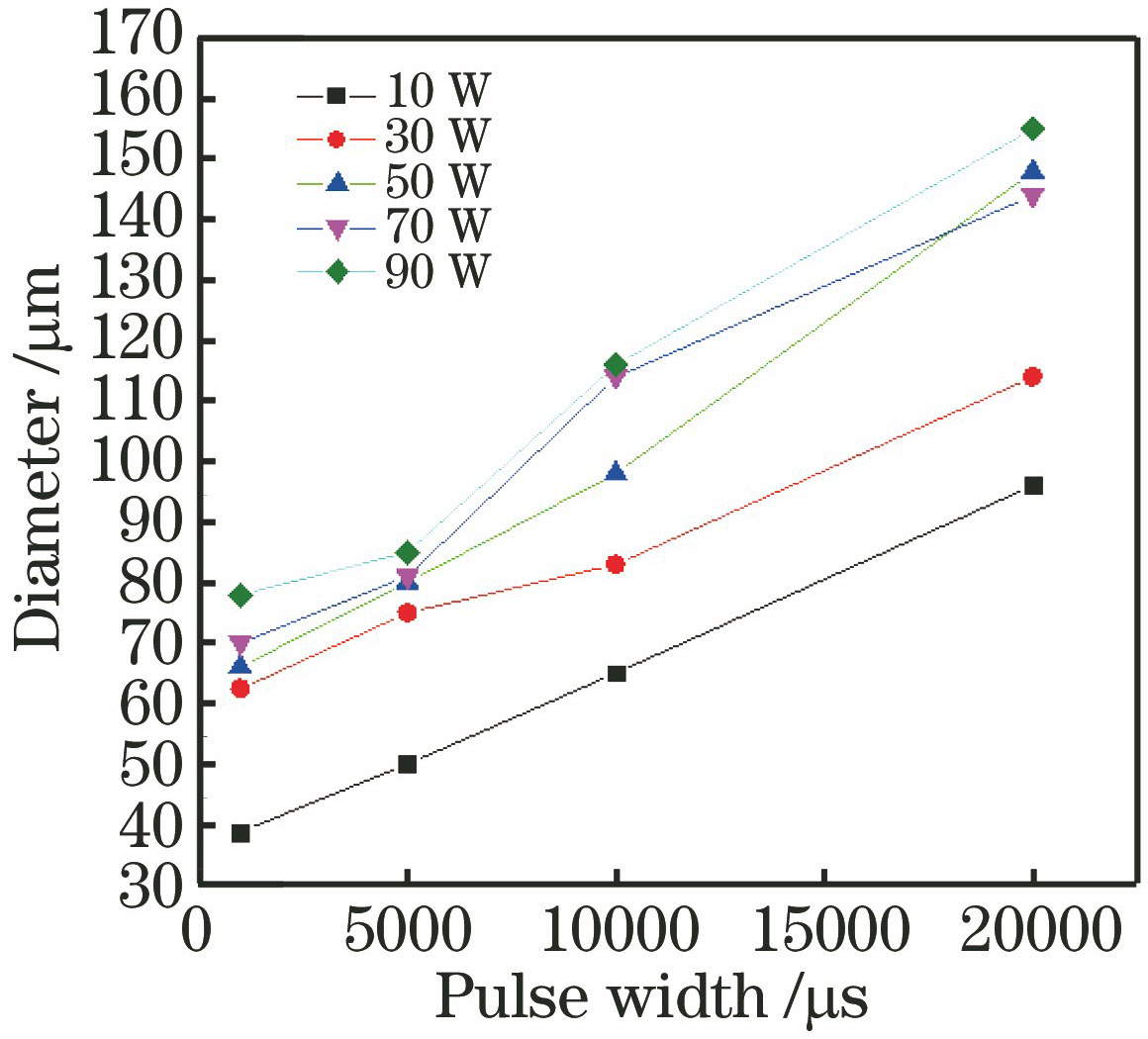
图 2. 不同功率下织构点直径随脉宽变化关系图
Fig. 2. Relationship between diameter of texturedpoint and pulse width at different powers
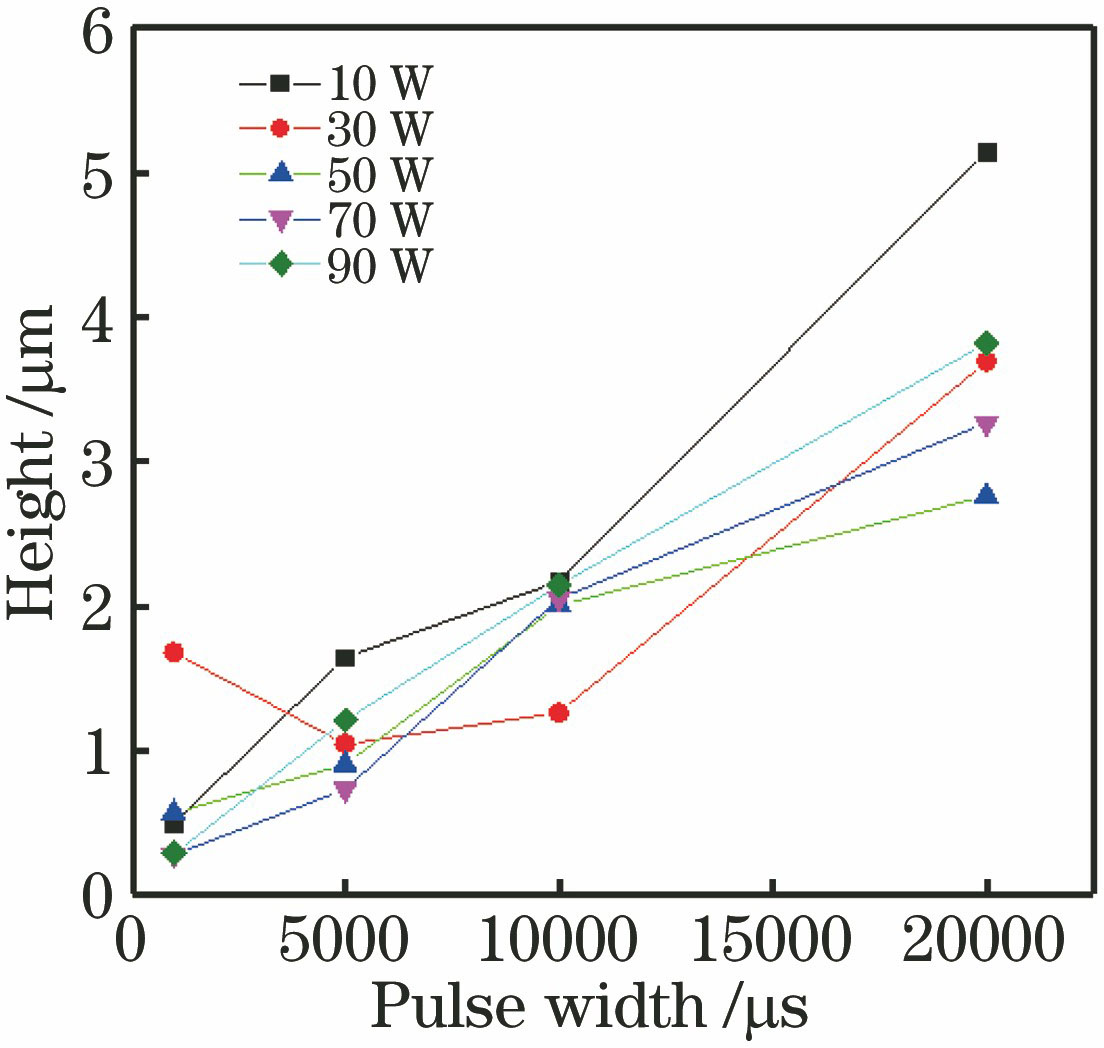
图 3. 不同功率下凸起高度随脉宽变化关系图
Fig. 3. Relationship between heightof convex profile and pulse width at different powers
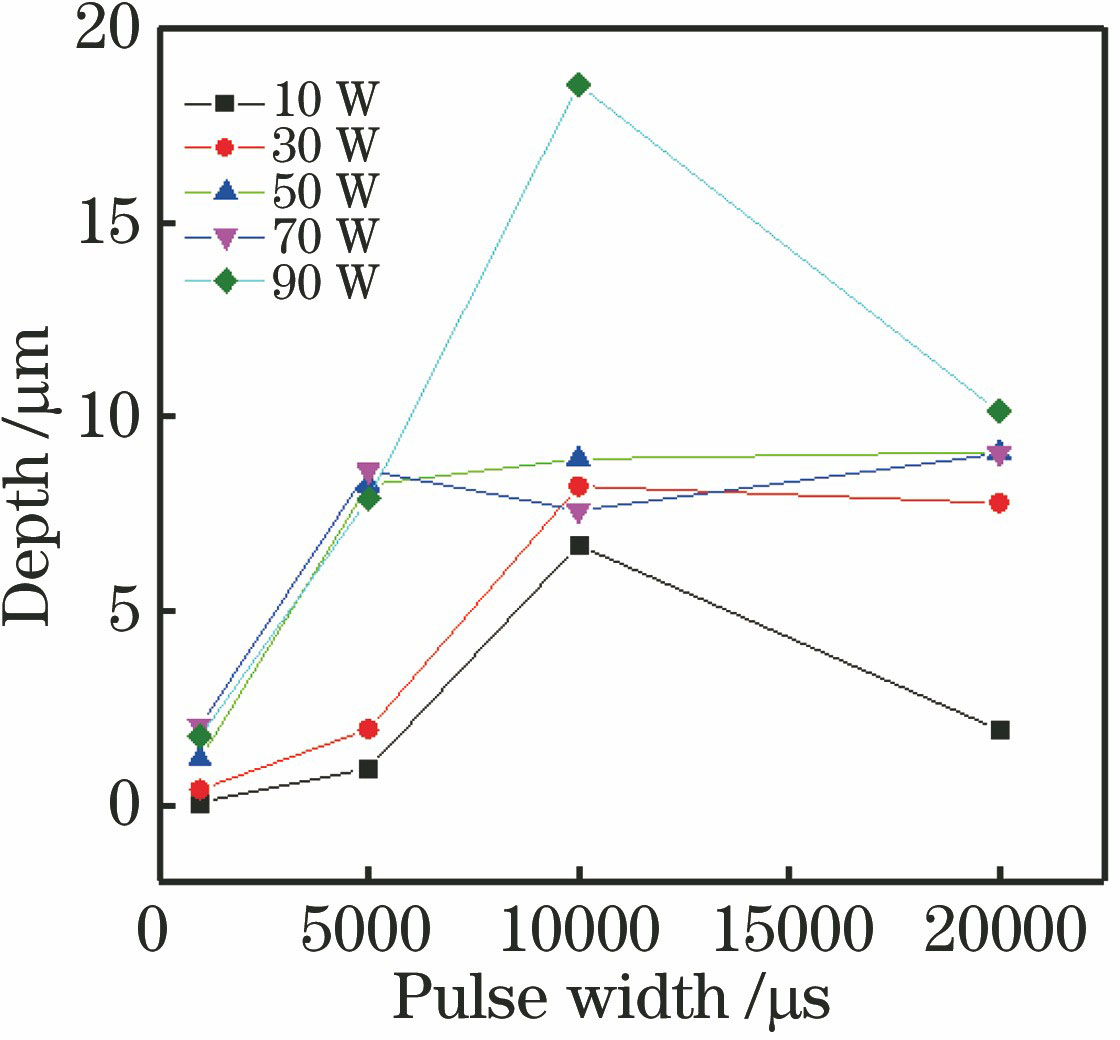
图 4. 不同功率下织构点深度随脉宽变化关系图
Fig. 4. Relationship between depth of texturedpoint and pulse width at different powers
从
从
从
当脉宽为1000 μs时,材料发生微熔形成中间凸起的毛化形貌,少量材料发生流动而在凸起部位旁形成深度较浅的凹坑。当脉宽增大,单个脉冲累积能量增大,材料流动变快,发生气化的材料也越多,因此形成的凹坑深度也越深。当脉宽大于10000 μs时,凹坑区域重熔作用明显,材料堆积在凹坑底部,凹坑深度变小。当功率增大时,能量密度增大,也会造成材料流动加快、气化的材料增多,凹坑深度随之增大,但由于脉宽较大(5000 μs以上)而导致功率对深度的影响相对脉宽较小。
3.2 重复次数对形貌的影响
采用“单脉冲同点间隔多次”加工方法具有热效应影响小、形貌质量高、加工效率高等优势[22],为了研究SPI光纤微秒激光器加工织构时不同功率和脉宽参数下激光作用重复次数对形貌的影响,本次试验分别考量功率30 W、50 W和脉宽1000,5000,10000 μs时重复次数对织构形貌的影响,重复次数变化范围为:1,5,10,15次。织构点三维形貌变化如
从
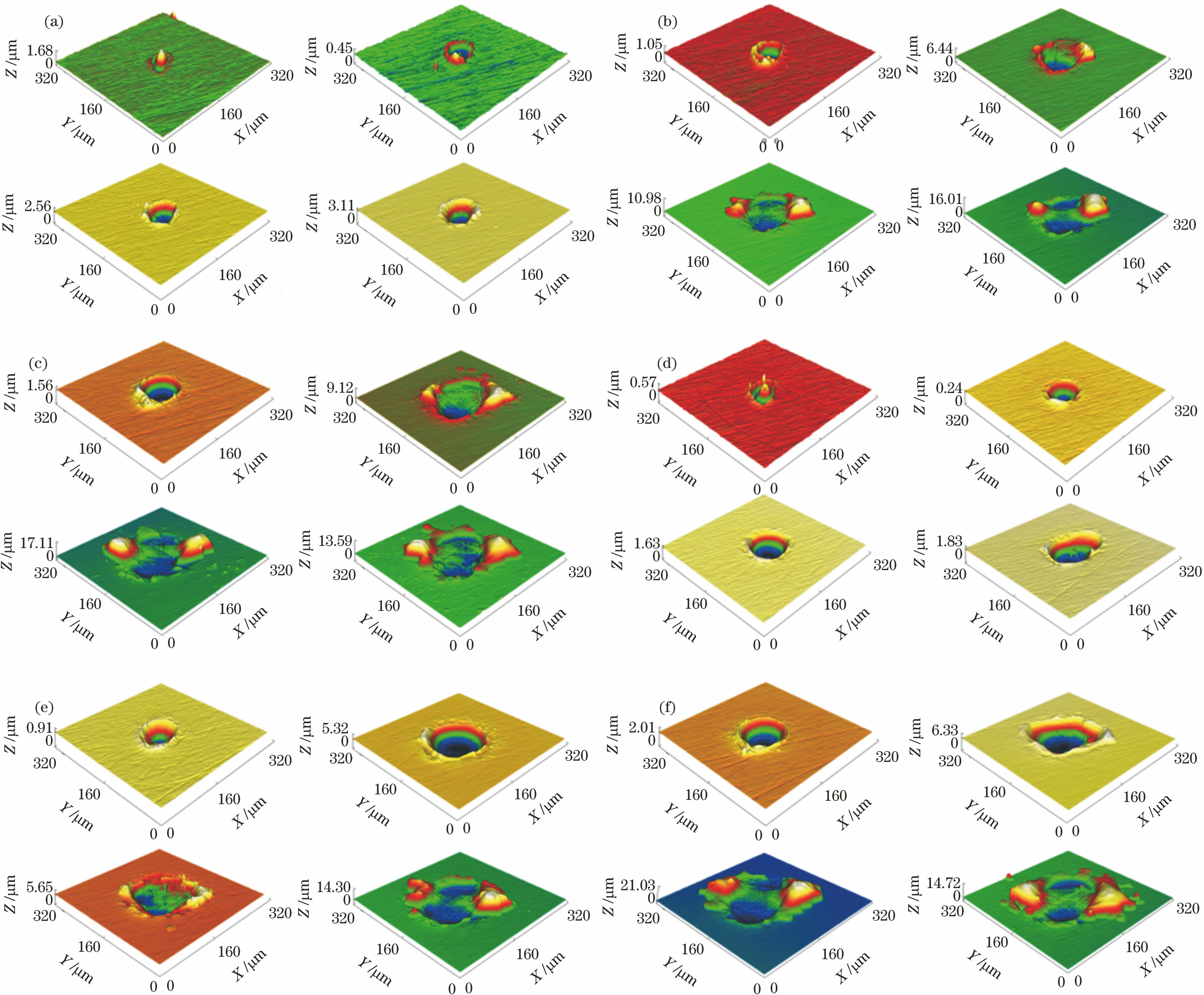
图 5. 不同功率和脉宽下织构点形貌随重复次数的变化。(a) 30 W,1000 μs;(b) 30 W,5000 μs;(c) 30 W,10000 μs;(d) 50 W,1000 μs;(e) 50 W,5000 μs;(f) 50 W,10000 μs
Fig. 5. Morphology changes of texturedpoint with repetition times at different powers and pulse widths.(a) 30 W, 1000 μs; (b) 30 W, 5000 μs; (c) 30 W, 10000 μs; (d) 50 W, 1000 μs; (e) 50 W, 5000 μs; (f) 50 W, 10000 μs
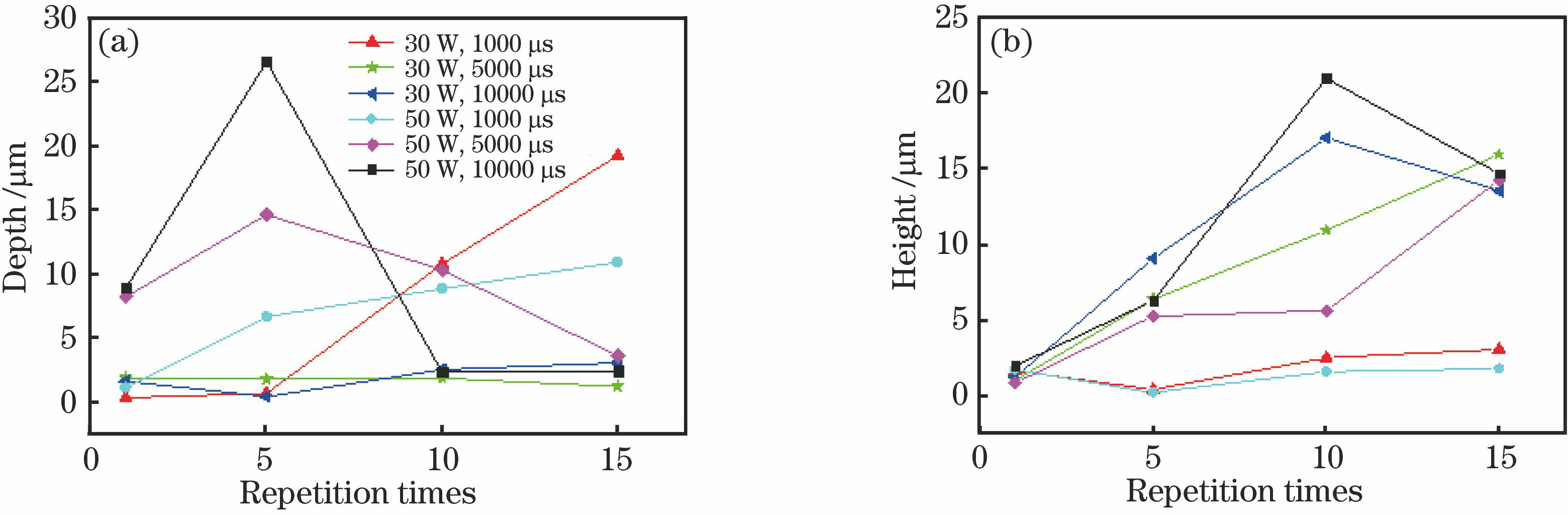
图 6. 不同功率和脉宽下重复次数对织构点深度和凸起高度的影响。(a)深度;(b)凸起高度
Fig. 6. Effects of repetition times on depth and convex profile height of textured point at different powers and pulse widths. (a) Depth; (b) height of convex profile
从
结合
4 结论
探究了SPI微秒级光纤激光器的激光功率、脉宽、重复次数等不同工艺参数对GCr15轴承钢表面织构形貌的影响。单脉冲作用时,脉宽对形貌形成影响较大,脉宽为1000 μs左右,熔凝作用明显,易形成毛化凸起型形貌,但功率过大或过小都不利于毛化形貌的形成;脉宽持续增大,熔池中心材料会发生气化,形成微凹坑形貌。脉冲重复次数会加剧熔池中心材料气化,有利于凹坑形成,但过多的脉冲重复次数会导致热效应过大,熔渣累积。
揭示了通过激光能量累积效应来控制不同织构形貌形成的基本原理和参数调控方法,成功利用一台微秒级激光器实现了凹/凸形貌织构的加工。未来有望将该项技术应用于拉伸模具、机床导轨等工业应用中。
[1] Merlo A M. The contribution of surface engineering to the product performance in the automotive industry[J]. Surface and CoatingsTechnology, 2003, 174/175: 21- 26.
[3] Kligerman Y, Etsion I, Shinkarenko A. Improving tribological performance of piston rings by partial surface texturing[J]. Journal of Tribology, 2005, 127(3): 632-638.
[4] 冯爱新, 杨润, 施芬, 等. 激光微织构硬质合金表面润湿性[J]. 强激光与粒子束, 2014, 26(2): 299-302.
[6] 万轶, 熊党生. 激光表面织构化改善摩擦学性能的研究进展[J]. 摩擦学学报, 2006, 26(6): 603-607.
[7] Hoppermann A, Kordt M. Tribological optimisation using laser-structured contact surfaces[J]. Ölhydraulik und Pneumatik, 2002, 46: 1-23.
[10] 雷泽红. 轧辊激光毛化技术的应用及发展[J]. 应用激光, 2013, 33(5): 563-566.
[13] 黄志辉, 刘会霞, 沈宗宝, 等. 工艺参数对激光冲击微造型效果的影响[J]. 中国激光, 2012, 39(5): 0503004.
[14] 张培耘, 华希俊, 符永宏, 等. 激光表面微织构工艺试验及应用研究[J]. 表面技术, 2013, 42(5): 55-58, 73.
[15] 钱振华. 关节轴承表面形貌参数可控的激光微织构技术[J]. 轴承, 2018( 2): 14- 17.
Qian ZH. Laser micro texturing with controllable surface morphology parameters of spherical plain bearings[J]. Bearing, 2018( 2): 14- 17.
[18] 靳广林, 虞宙, 胡俊. 激光表面微造型与凸起形貌摩擦性能研究[J]. 应用激光, 2015, 35(5): 536-540.
[19] 叶云霞, 贾子扬, 符昊, 等. 脉冲激光作用下45#钢表面微凸起形貌演变规律的研究[J]. 激光与光电子学进展, 2016, 53(3): 031408.
[20] Wang X S, Xu W T, Liu L, et al. Magnetic-field-assisted fabrication of micro-convex domes using long pulse laser[J]. Applied Physics A, 2017, 123(9): 592.
[21] 符永宏, 刘强宪, 叶云霞, 等. 同点间隔多次激光微织构工艺研究[J]. 中国激光, 2015, 42(12): 1203005.
[22] Vadillo J M. Fernández Romero J M, Rodríguez C, et al. Effect of plasma shielding on laser ablation rate of pure metals at reduced pressure[J]. Surface and Interface Analysis, 1999, 27(11): 1009-1015.
华希俊, 张加力, 解玄, 平国峰, 张玲慧, 尹必峰. GCr15轴承钢表面的激光凹/凸微织构工艺[J]. 中国激光, 2019, 46(3): 0302009. Xijun Hua, Jiali Zhang, Xuan Xie, Guofeng Ping, Huiling Zhang, Bifeng Yin. Laser Concave/Convex Micro-Texture Process of GCr15 Bearing Steel Surface[J]. Chinese Journal of Lasers, 2019, 46(3): 0302009.