三光束光内送丝激光熔覆温度场仿真分析与工艺优化
下载: 1013次
1 引言
激光熔覆成形技术[1]是以高能量激光束为热源熔化金属材料并进行逐层堆积,进而形成零件实体的制造技术。根据材料添加时性状的不同,熔覆成形技术可分为送粉式熔覆和送丝式熔覆两种[2]。送丝式熔覆成形技术具有极高的材料利用率及环境污染小等特点,近年来受到了人们的广泛关注。送丝式熔覆根据丝材进给位置可分为光外送丝熔覆与光内送丝熔覆两种。本文采用实验室自主研发的三光束光内送丝熔覆喷头[3]进行实验,该喷头在熔覆过程中送丝平缓,丝材受热均匀。
熔池的温度分布直接影响着熔池的对流、传质和传热过程,进而影响熔覆层的形貌与质量,因此对熔池温度场的研究至关重要。在激光熔覆成形过程中,熔池具有升温快、温度高的特点,采用实验测量的方式很难得到熔池的温度场分布。目前,国内外很多研究者都通过数值模拟对熔池的温度场进行模拟[4-5]:孙进[6]利用ANSYS仿真软件对侧向送丝熔覆成形进行了温度场和应力-应变场的有限元分析,并据此推测出熔覆层内部晶粒的生长方式以及熔道的热变形情况;戴德平等[7]利用Abaqus软件对718镍基合金的单道多层熔覆过程进行了温度场和应力场的仿真,分析了激光熔覆过程的温度场分布、热循环特征以及残余应力的分布特点;Tseng等[8]提出了一种新的激光熔覆热源模型,在综合考虑了光束波长、光束半径、透射电镜模式和聚焦条件等的条件下,预测了预置钴粉层激光熔覆过程中的温度分布和熔覆层形貌,并在与数学模型相同的条件下进行了激光熔覆实验,验证了数值计算结果的正确性。上述研究主要针对的是圆形激光光斑熔覆方式,对于三光束激光光斑熔覆温度场尚缺乏深入研究。圆形激光光斑熔覆温度场的热源大部分可视作单个的高斯热源,能量集中区域为光斑的中心,而三光束光内送丝激光熔覆温度场的热源是三个高斯热源的叠加,能量集中区域从中心变为外缘,能量分布更加均匀,同时能够改善圆形激光光斑熔覆时熔覆层边缘部分冶金结合较差的缺点。本文基于三光束光内送丝熔覆喷头建立了三光束光源的热源模型,利用ANSYS软件进行了熔池温度场的仿真,对熔覆层的形貌进行了预测与分析,优化了单道熔覆的工艺参数,为后续光内送丝熔覆成形工艺提供了实验与数据参考。
2 仿真模型的建立
三光束光内送丝熔覆喷头的光丝耦合原理如
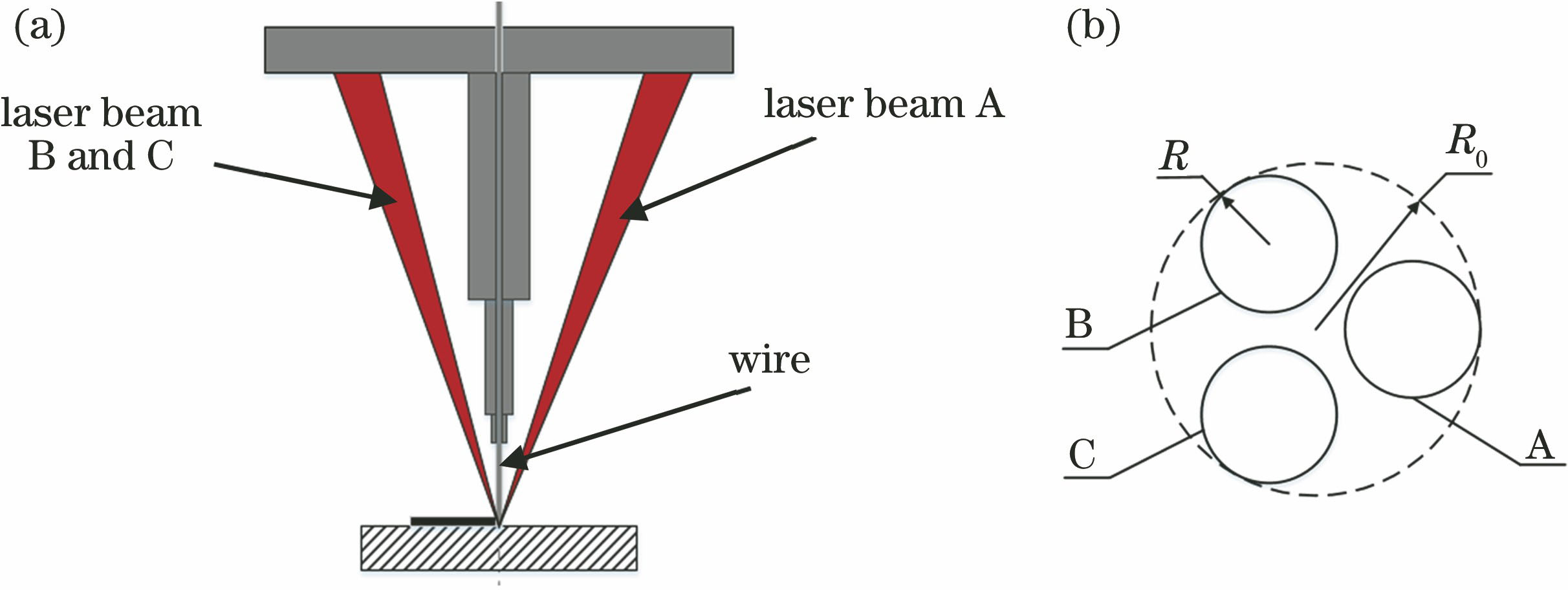
图 1. 光丝耦合原理图。(a)耦合模型;(b)光斑位置
Fig. 1. Coupling principle of light and wire. (a) Coupling model; (b) light spot location
A、B和C为3个独立的光斑,
式中:
为了减少仿真过程的计算时间,同时保证计算结果较为精确,截取基板的尺寸为20 mm×15 mm×5 mm,网格划分尺寸为0.25 mm×0.25 mm×0.5 mm,网格尺寸由熔池到基板边缘逐渐增大[9]。网格划分使用solid70单元,该单元具有8个节点,每个节点有一个温度自由度,适用于瞬态与非瞬态热分析。激光熔覆是一个极为复杂的过程,包含着熔化、凝固、对流和辐射等。为了简化模型,使仿真计算便于实现,现进行如下假设[10-12]:材料均为各向同性;材料的物理属性随温度的变化而变化;不考虑热辐射的影响;忽略熔池的流动和重力的影响。
3 实验与仿真结果分析
3.1 熔覆层形貌的预测与实验验证
采用IPG YLS-2000-TR光纤激光器进行熔覆实验,额定输出功率为2000 W。熔覆材料为碳钢实芯焊丝,其熔点约为1450 ℃,丝材直径为1.2 mm,其化学成分如
表 1. 金属丝材的化学成分
Table 1. Chemical compositions of metal wire materials
|
光斑的移动如
采用德国三铯M322双色红外测温仪测试温度,温度测量范围为800~3000 ℃。测试方法为定点测试,即温度测试仪固定不动,熔覆过程中光斑移动并经过测试点。由于温度测试仪的测试点半径较大,故只能测得
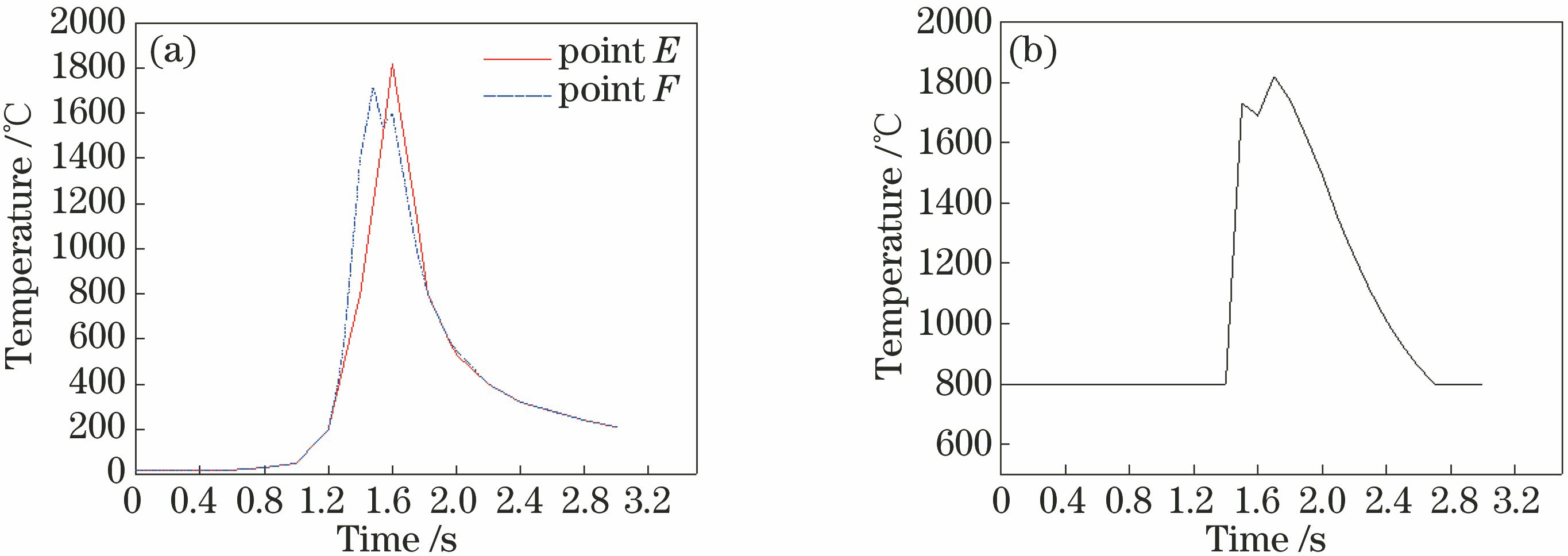
图 4. 仿真和采用温度仪测试得到的温度曲线。(a)仿真结果;(b)温度仪测试值
Fig. 4. Diagrams of temperature curves obtained by simulation and measurement with thermometer.(a) Simulation; (b) thermometer test
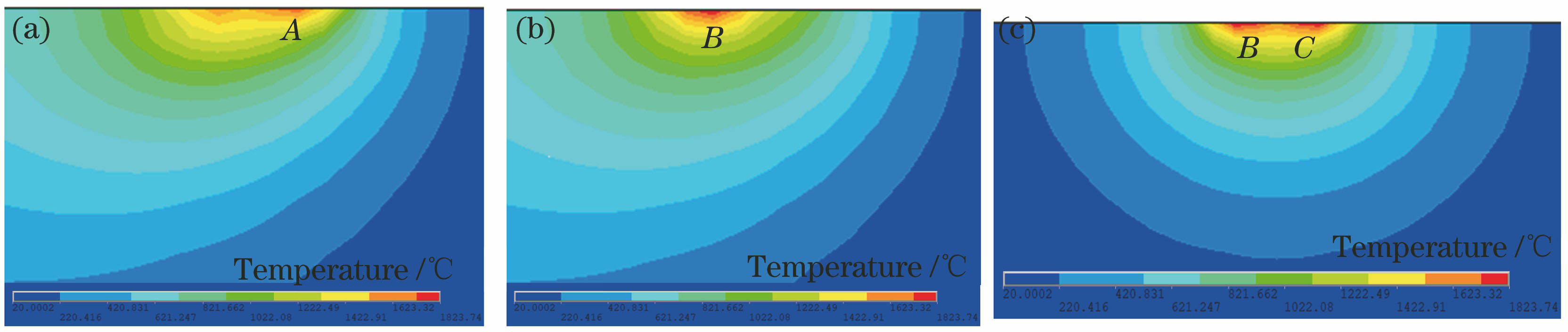
图 5. 基板纵切面及横截面上的温度分布云图。(a) DF;(b) BE;(c) BC
Fig. 5. Temperature profiles of longitudinal section and cross section of basal plate. (a) DF; (b) BE; (c) BC
3.2 离焦量的影响
离焦量是光斑焦点与熔覆层之间的距离,离焦量的大小决定了光斑的半径。实验采用负离焦,在其他参数不变的条件下,随着离焦量增大,熔覆层的宽度、高度和宽高比如
由
表 2. 不同离焦量下获得的熔覆层的宽度与高度
Table 2. Width and height of cladding layer obtained at different defocusing amounts
|
对于三光束光斑而言,离焦量直接影响到熔覆层稀释区的形貌。当离焦量分别为-2 mm与-1 mm时,熔池的温度分布如
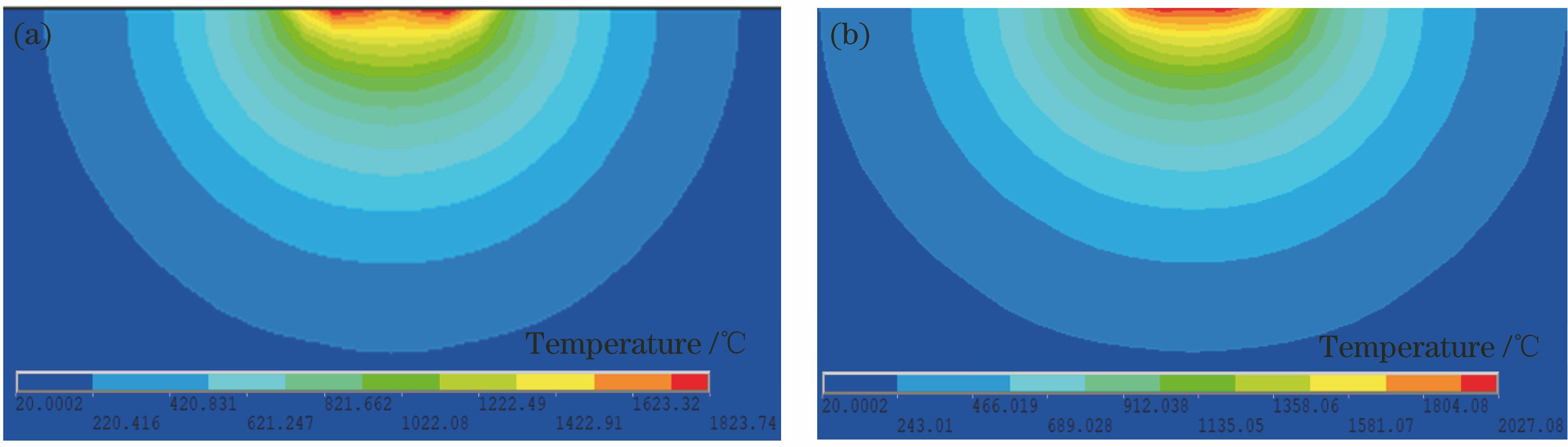
图 7. 不同离焦量下的熔池温度分布云图。(a) -2 mm;(b) -1 mm
Fig. 7. Cloud charts of temperature distributions of molten pool at different defocusing amounts. (a) -2 mm; (b) -1 mm
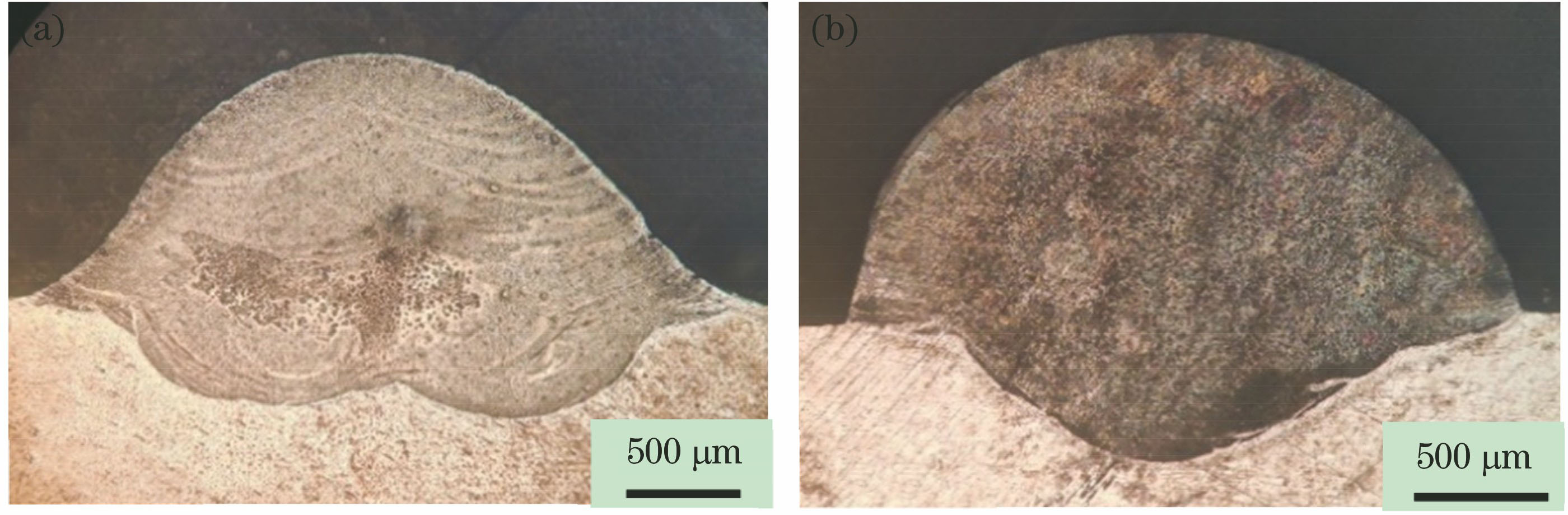
图 8. 不同离焦量下制得的熔覆层的横断面形貌。(a) -2 mm;(b) -1 mm
Fig. 8. Cross sections of cladding layer obtained at different defocusing amounts. (a) -2 mm; (b) -1 mm
3.3 激光功率的影响
激光功率决定了光源能量输入的大小。在其他参数不变的条件下,随着激光功率逐渐增大,熔覆层的宽度、高度和宽高比如
表 3. 不同激光功率下得到的熔覆层的宽度与高度
Table 3. Width and height of cladding layer obtained at different laser powers
|
随着激光功率增大,熔覆层的宽度增大,高度下降,宽高比增大。这是由于激光功率增大时,光斑的能量密度增大,熔覆层的熔宽与熔深增大,进而熔覆层的宽度和稀释率增大,但光斑尺寸未发生改变,故熔覆层的宽度变化幅度较小。稀释率是衡量熔覆层质量的另一个重要参数,在保证冶金结合的情况下,稀释率越小越好[13]。激光功率分别为1400 W与1700 W时熔池的温度分布云图和熔覆层的横断面形貌如
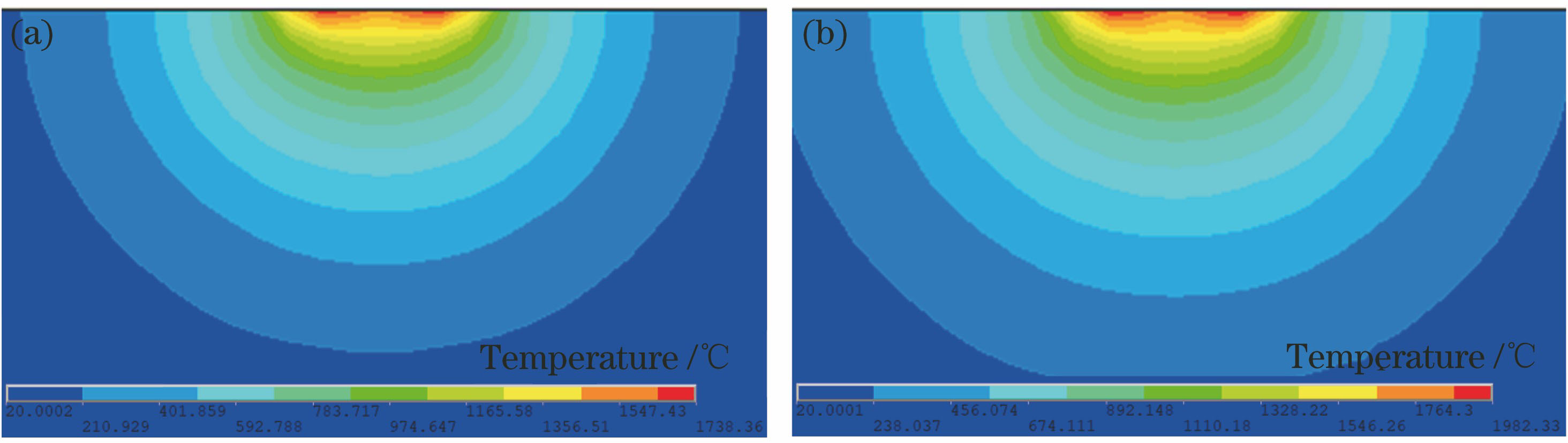
图 9. 不同激光功率下的熔池温度分布云图。(a) 1400 W;(b) 1700 W
Fig. 9. Cloud charts of temperature distributions of molten pool at different laser powers. (a) 1400 W; (b) 1700 W
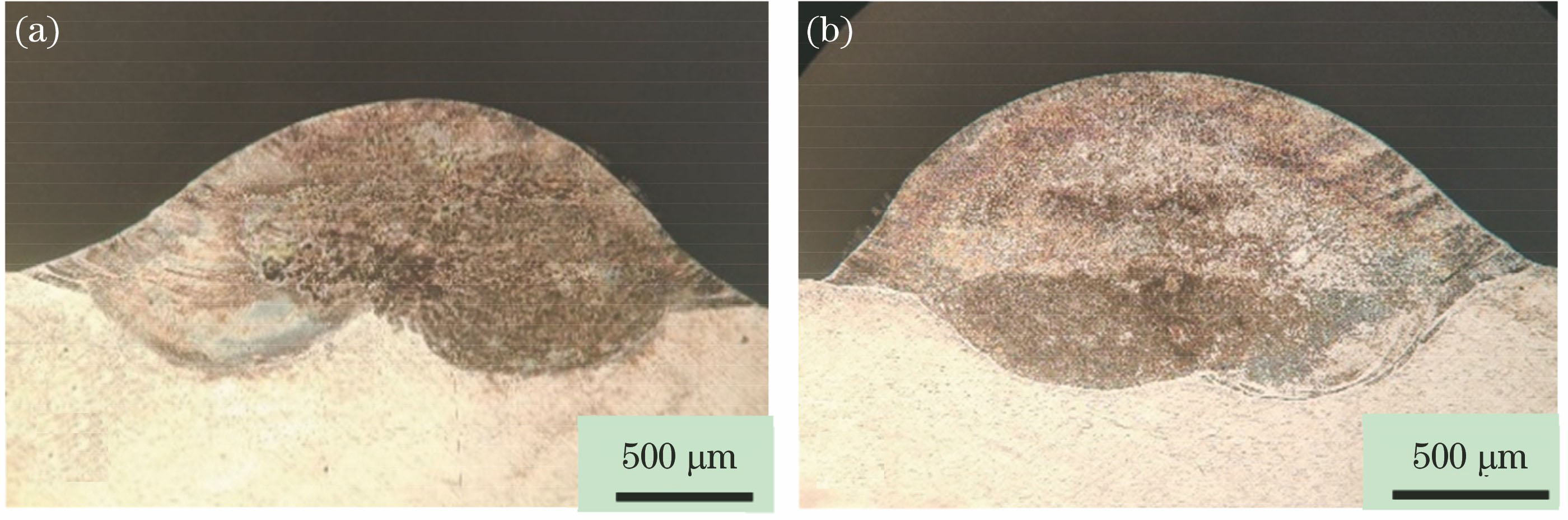
图 10. 不同激光功率下得到的熔覆层的横断面形貌。(a) 1400 W;(b) 1700 W
Fig. 10. Cross sections of cladding layer obtained at different laser powers. (a) 1400 W; (b) 1700 W
3.4 扫描速度的影响
扫描速度反映了单位时间内光斑移动的距离。在其他参数不变的情况下,随着扫描速度增大,熔覆层的宽度、高度和宽高比如
随着扫描速度增大,熔覆层的宽度减小,高度下降,宽高比增大。扫描速度直接影响单位时间内进入熔池的丝材质量,同时影响单位时间内丝材与基板对激光能量的吸收。随着扫描速度增大,单位时间内进入熔池的丝材质量减少,熔覆层高度显著下降。同时,熔覆层同一位置的熔池接受能量的时间缩短,接受的能量减少,熔覆层熔深与熔宽均减小,进而使得熔覆层的宽度减小。扫描速度分别为3 mm/s与7 mm/s时熔池的温度分布云图和熔覆层的横断面形貌如
表 4. 不同扫描速度下得到的熔覆层的宽度与高度
Table 4. Width and height of cladding layer obtained at different scanning speeds
|
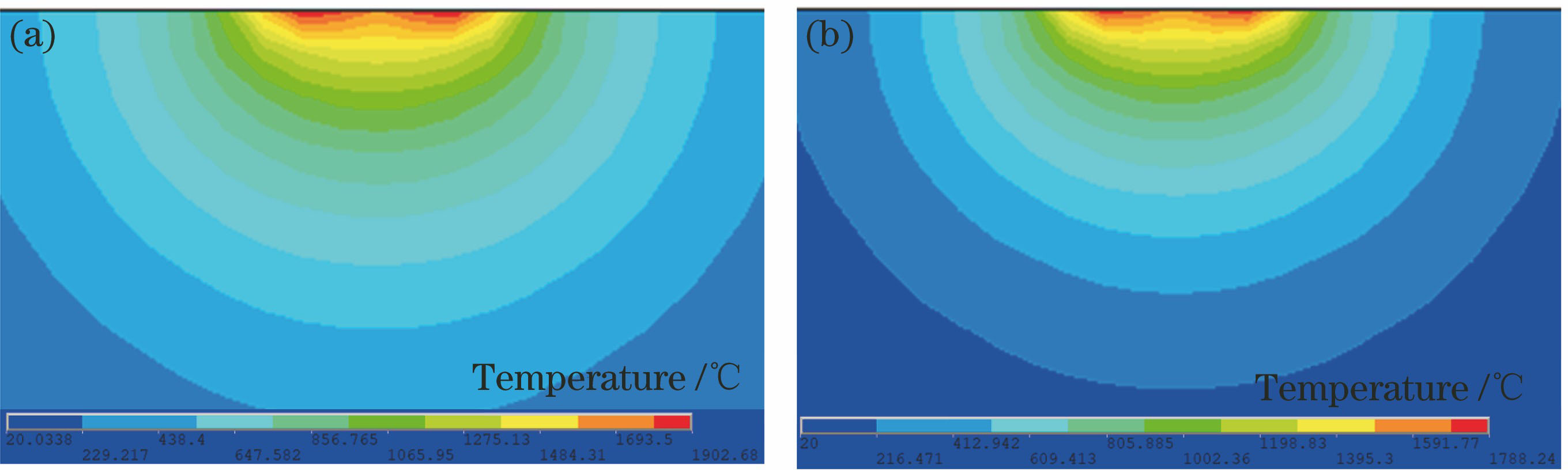
图 11. 不同扫描速度下的熔池温度分布云图。(a) 3 mm/s;(b) 7 mm/s
Fig. 11. Cloud charts of temperature distributions of molten pool at different scanning speeds. (a) 3 mm/s; (b) 7 mm/s
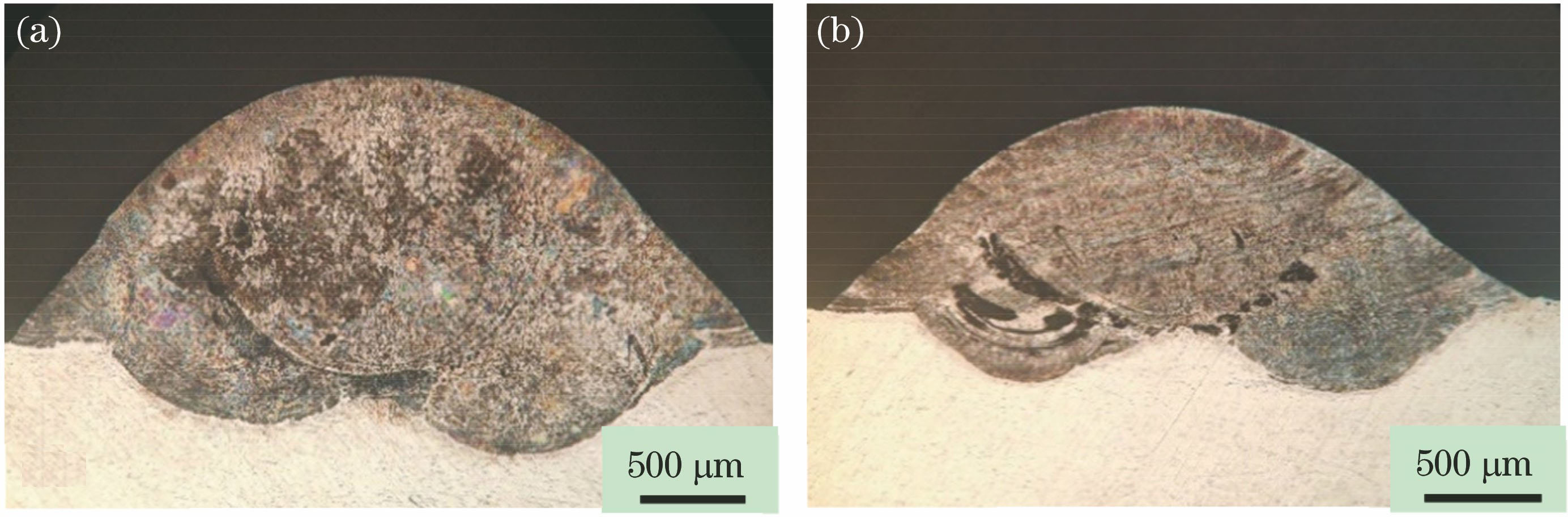
图 12. 不同扫描速度下得到的熔覆层的横断面形貌。(a) 3 mm/s;(b) 7 mm/s
Fig. 12. Cross sections of cladding layer obtained at different scanning speeds. (a) 3 mm/s; (b) 7 mm/s
3.5 扫描方向的影响
光外侧向送丝熔覆时丝材为单边受热,三光束光内同轴送丝熔覆过程中光斑围绕着丝材,丝材受热较为均匀。由于三个光斑呈正三角形分布,故在0°~60°范围进行扫描方向实验。选取离焦量为-2 mm,每隔15°进行一次激光熔覆,温度场云图及对应的熔覆层的横断面形貌如
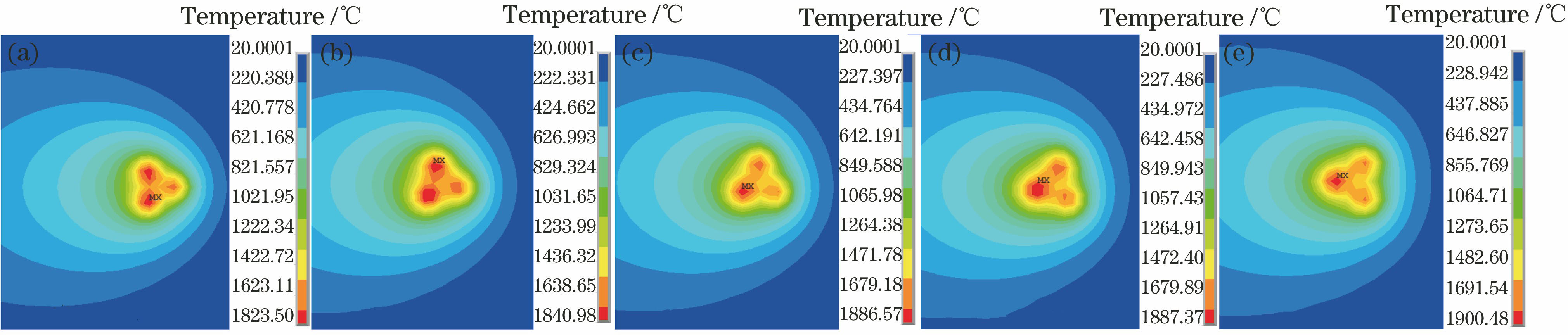
图 13. 不同扫描方向下的温度场云图。(a) 0°;(b) 15°;(c) 30°;(d) 45°;(e) 60°
Fig. 13. Cloud charts of temperature field at different scanning directions. (a) 0°; (b) 15°; (c) 30°; (d) 45°; (e) 60°

图 14. 不同扫描方向下得到的熔覆层的横断面形貌。(a) 0°;(b) 15°;(c) 30°;(d) 45°;(e) 60°
Fig. 14. Cross sections of cladding layer obtained at different scanning directions. (a) 0°; (b) 15°; (c) 30°; (d) 45°; (e) 60°
3.6 优化实验与组织分析
通过仿真与实验分析得到了能够较好地进行熔覆的工艺参数范围:离焦量为-1.5~-2.5 mm,激光功率为1400~1800 W,扫描速度为3~7 mm/s。选取离焦量为-2 mm、激光功率为1500 W、扫描速度为5 mm/s进行单道熔覆实验,得到的熔覆单道、截面及组织如
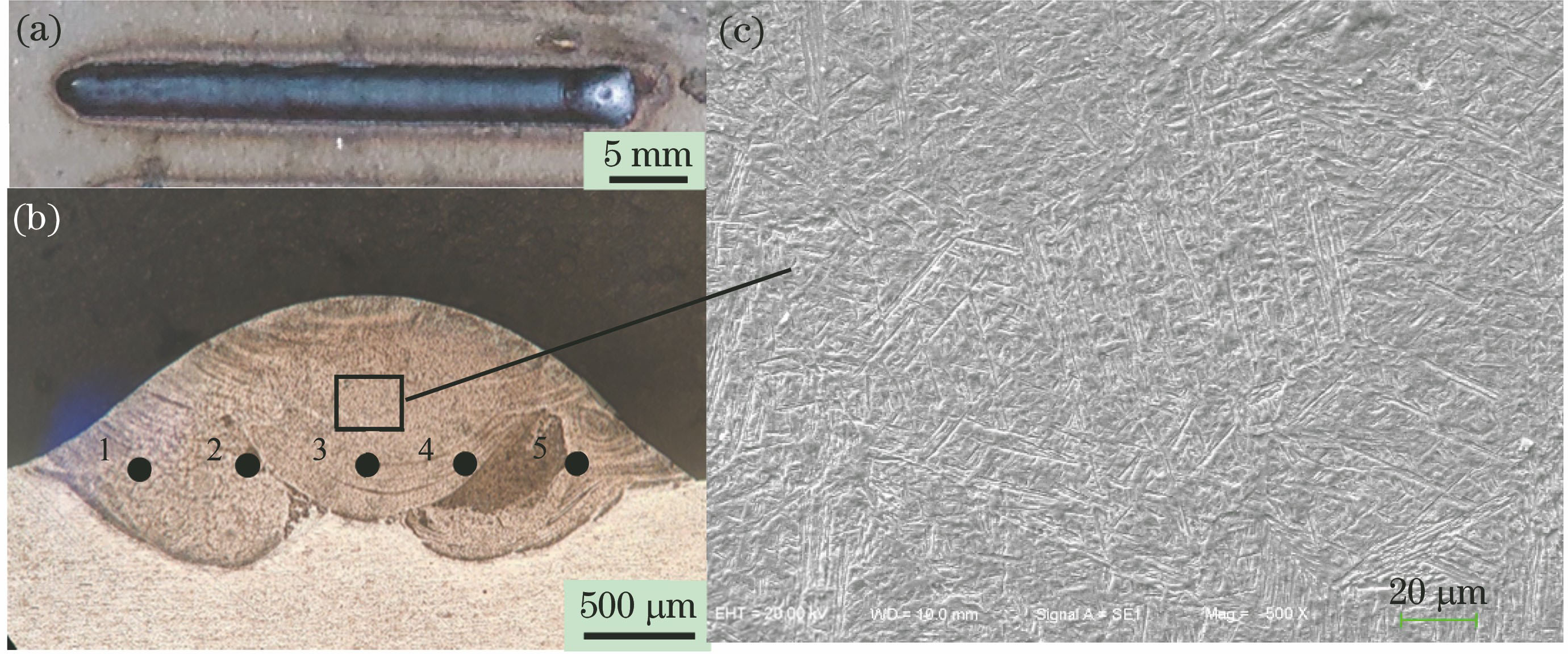
图 15. 单道熔覆层及横截面形貌。(a)单道;(b)截面;(c)组织
Fig. 15. Single cladding layer and cross section. (a) Cladding layer; (b) cross section; (c) texture
4 结论
基于三光束光内送丝熔覆喷头,采用ANSYS软件分析了熔池的温度场,并对熔覆层的形貌进行了预测和验证,得出如下结论:建立的三光束热源模型能够较为合理地反映熔池的温度场;离焦量的减小会使熔覆层稀释区形状由W形向V形转变;扫描方向对稀释区的对称性有一定的影响,应尽量选取0°与60°方向进行熔覆;在优化的工艺参数下能得到平整光滑、质量较高的单道熔覆层。
通过仿真与实验分析对单道熔覆工艺参数进行了优化,但并未对多道多层熔覆成形工艺进行研究。下一步计划进行多道多层熔覆成形实验,进一步分析样件的组织、性能与工艺参数的关系。
[1] 刘勇, 任香会, 常云龙, 等. 金属增材制造技术的研究现状[J]. 热加工工艺, 2018, 47(19): 15-24.
[2] 李凯斌, 李东, 刘东宇, 等. 光纤激光送丝熔覆修复工艺研究[J]. 中国激光, 2014, 41(11): 1103006.
[3] 吉绍山,[\s]{1}傅戈雁,[\s]{1}石世宏,[\s]{1}等.[\s]{1}激光多光束熔覆装置:[\s]{1}106583726[P].2017-04-26.[\s]{1}
Ji[\s]{1}SS,[\s]{1}Fu[\s]{1}GY,[\s]{1}Shi[\s]{1}SH,[\s]{1}et[\s]{1}al.[\s]{1}A[\s]{1}multi-beam[\s]{1}laser[\s]{1}cladding[\s]{1}apparatus:[\s]{1}106583726[P].[\s]{1}2017-04-26.[\s]{1}
[4] 党元晓, 祁文军, 芦丽丽. 激光熔覆技术数值模拟研究现状及发展趋势[J]. 热加工工艺, 2016, 45(6): 23-27.
[5] 董冬梅, 陈菊芳, 雷卫宁. 激光熔覆的研究现状[J]. 热加工工艺, 2017, 46(16): 9-13.
[6] 孙进.[\s]{1}侧向送丝激光熔覆成型技术的工艺研究及其数值模拟[D].[\s]{1}广州:[\s]{1}华南理工大学,[\s]{1}2012:[\s]{1}45-[\s]{1}79.[\s]{1}
SunJ.[\s]{1}Process[\s]{1}research[\s]{1}and[\s]{1}numerical[\s]{1}simulation[\s]{1}of[\s]{1}laser[\s]{1}cladding[\s]{1}fabrication[\s]{1}technology[\s]{1}feeding[\s]{1}by[\s]{1}side[D].[\s]{1}Guangzhou:[\s]{1}South[\s]{1}China[\s]{1}University[\s]{1}of[\s]{1}Technology,[\s]{1}2012:[\s]{1}45-[\s]{1}79.[\s]{1}
[7] 戴德平, 蒋小华, 蔡建鹏, 等. 激光熔覆Inconel718镍基合金温度场与应力场模拟[J]. 中国激光, 2015, 42(9): 0903005.
[9] 任仲贺, 武美萍, 唐又红, 等. 基于热力耦合的激光熔覆数值模拟与实验研究[J]. 激光与光电子学进展, 2019, 56(5): 051404.
[10] 王涛, 秦令超, 刘佳奇. 基于有限元的激光熔覆CoNiCrAlY温度场模拟及实验验证[J]. 热加工工艺, 2018, 47(18): 154-157, 161.
[11] 操顺森.[\s]{1}3D激光熔覆铁基合金温度场模拟与试验研究[D].[\s]{1}南昌:[\s]{1}南昌大学,[\s]{1}2017:[\s]{1}13-[\s]{1}14
Cao[\s]{1}SS.[\s]{1}Simulation[\s]{1}of[\s]{1}temperature[\s]{1}field[\s]{1}and[\s]{1}experimental[\s]{1}study[\s]{1}of[\s]{1}3D[\s]{1}laser[\s]{1}cladding[\s]{1}Fe-based[\s]{1}alloy[D].[\s]{1}Nanchang:[\s]{1}Nanchang[\s]{1}University,[\s]{1}2017:[\s]{1}13-[\s]{1}14
[12] 李俐群, 王建东, 吴潮潮, 等. Ti6Al4V激光熔化沉积熔池温度场与微观组织特性[J]. 中国激光, 2017, 44(3): 0302009.
[13] 潘浒, 赵剑峰, 刘云雷, 等. 激光熔覆修复镍基高温合金稀释率的可控性研究[J]. 中国激光, 2013, 40(4): 0403007.
Article Outline
张吉平, 石世宏, 蒋伟伟, 石拓, 吉绍山. 三光束光内送丝激光熔覆温度场仿真分析与工艺优化[J]. 中国激光, 2019, 46(10): 1002004. Jiping Zhang, Shihong Shi, Weiwei Jiang, Tuo Shi, Shaoshan Ji. Simulation Analysis of Temperature Field and Process Optimization of Laser Cladding Based on Internal Wire Feeding of Three Beams[J]. Chinese Journal of Lasers, 2019, 46(10): 1002004.