1 上海电力大学自动化工程学院, 上海 200090
2 科廷大学计算机科学系, 澳大利亚 珀斯 6102
三维激光扫描点云在采集和处理后生成的三角化网格,由于测量设备限制或模型自身形状特点常包含孔洞,这类孔洞会给后续三维重建带来障碍。针对孔洞修补问题,提出了一种激光三角网格曲面点云孔洞修补算法。首先对封闭孔洞通过遍历三角网格确定三角面片边界,检测孔洞。其次基于最小角度法在孔洞多边形处快速生成新三角面片,形成初始网格。然后融合最小二乘网络与径向函数隐式曲面,利用最小二阶导数对曲面曲率进行最小化,并与原始网格曲率变化趋势保持相同,最终实现激光点云孔洞修补。实验结果表明,与其他点云修补方法相比,该方法降低了修补误差,适用于多种三角网格模型孔洞修补。
激光光学 三维激光扫描 三角化网格 检测孔洞 曲率 孔洞修补 激光与光电子学进展
2021, 58(20): 2014002
燕山大学先进锻压成形技术与科学教育部重点实验室, 河北 秦皇岛 066004
采用由点式锻压和激光修复组成的点式锻压激光修复(PF-LR)技术对TA15钛合金锻件进行修复。研究了PF-LR TA15钛合金锻件的组织,测试了具有不同修复体积分数(修复区体积与拉伸试样体积之比)的PF-LR TA15钛合金的拉伸力学性能。结果表明,PF-LR区内的TA15钛合金等轴晶的平均晶粒尺寸约为200 μm,等轴晶内部微观组织为网篮组织+β转变组织。PF-LR TA15钛合金修复区的屈服强度、抗拉强度及塑性比锻造退火态TA15钛合金的航空拉伸力学性能的下限标准分别提高了20.5%、23.3%及93.7%。含10%、30%及50%修复体积分数的PF-LR TA15钛合金锻件的屈服强度、抗拉强度和塑性均超过锻造退火态TA15钛合金的航空拉伸力学性能标准,且PF-LR体积分数越高,PF-LR TA15钛合金锻件的屈服强度、抗拉强度和塑性也相应越高。讨论了含不同修复体积分数的PF-LR TA15钛合金锻件拉伸力学性能提高的原因。根据拉伸断口形貌特点,分析了PF-LR TA15钛合金锻件的拉伸断裂行为。
激光技术 点式锻压 激光修复 TA15钛合金 显微组织 拉伸性能 中国激光
2021, 48(10): 1002103

安徽工业大学建筑工程学院, 安徽 马鞍山 243032
钢渣是冶金工业中产生的主要固体废弃物, 其产量约为每年粗钢产量的15%~20%。 由于技术的局限, 导致我国钢渣利用率较低, 仅为年钢渣产量的10%, 同时加之管理制度的不健全, 导致钢渣大量露天堆放, 对土地资源、 地下水源, 以及空气质量形成严重影响。 面对上述问题, 利用钢渣开发一种价格低廉的固化药剂用于重金属污染土壤的修复, 既是冶金固体废弃物可持续发展的重要途径之一, 也是大幅降低重金属污染土壤修复成本的重要途径之一。 该研究创新性是用风淬渣微粉作为固化药剂对含有Cd, Cu, Pb, Ni和Zn的重金属污染土壤进行修复。 研究了风淬渣粉磨时间、 风淬渣微粉掺量和养护时间对修复重金属污染土壤效果的影响。 利用激光粒度分析仪测试风淬渣微粉的粒度分布、 比表面积与孔隙度吸附仪测试风淬渣微粉的孔结构、 扫描电子显微镜测试风淬渣微粉-重金属污染土壤混合物的微观形貌、 X-射线衍射仪测试风淬渣微粉的矿物成分, 分析风淬渣微粉修复重金属污染土壤的机理。 结果表明, 风淬渣的性质安全, 对生态环境不存在污染, 可以用于修复重金属污染土壤的固化技术。 当风淬渣粉磨时间为100 min、 风淬渣微粉掺量为20%、 养护时间为14 d时, 风淬渣微粉对重金属污染土壤中Cu, Cd, Ni, Zn和Pb的固化效果均达到91%以上。 随着风淬渣粉磨时间的延长, 风淬渣微粉的粒径尺寸减小、 粒度分布趋向均匀。 风淬渣的多孔结构破坏、 比表面积提高, 有利于提高风淬渣微粉对重金属污染土壤的修复效果。 随着风淬渣微粉掺量的增加, 风淬渣微粉形成的水化凝胶(C—S—H)数量增加, 有利于提高风淬渣微粉包裹重金属污染土壤的效果, 以达到固化重金属污染土壤中Cd, Cu, Pb, Ni和Zn的目的。 风淬渣微粉对固化重金属污染土壤中Cu, Cd, Ni, Zn和Pb具有选择性, 在不同养护时间下, 重金属分别以Cd2SiO4, Cu(OH)2·2H2O, PbCO3, 3Ni(OH)2·2H2O, Ni2SiO4, Zn(OH)2和Zn2SiO4形式存在。
风淬渣微粉 重金属污染土壤 修复效果 固化药剂 机理 Wind quenching slag powder Heavy metal contaminated soil Repairing effect Curing agent Mechanism
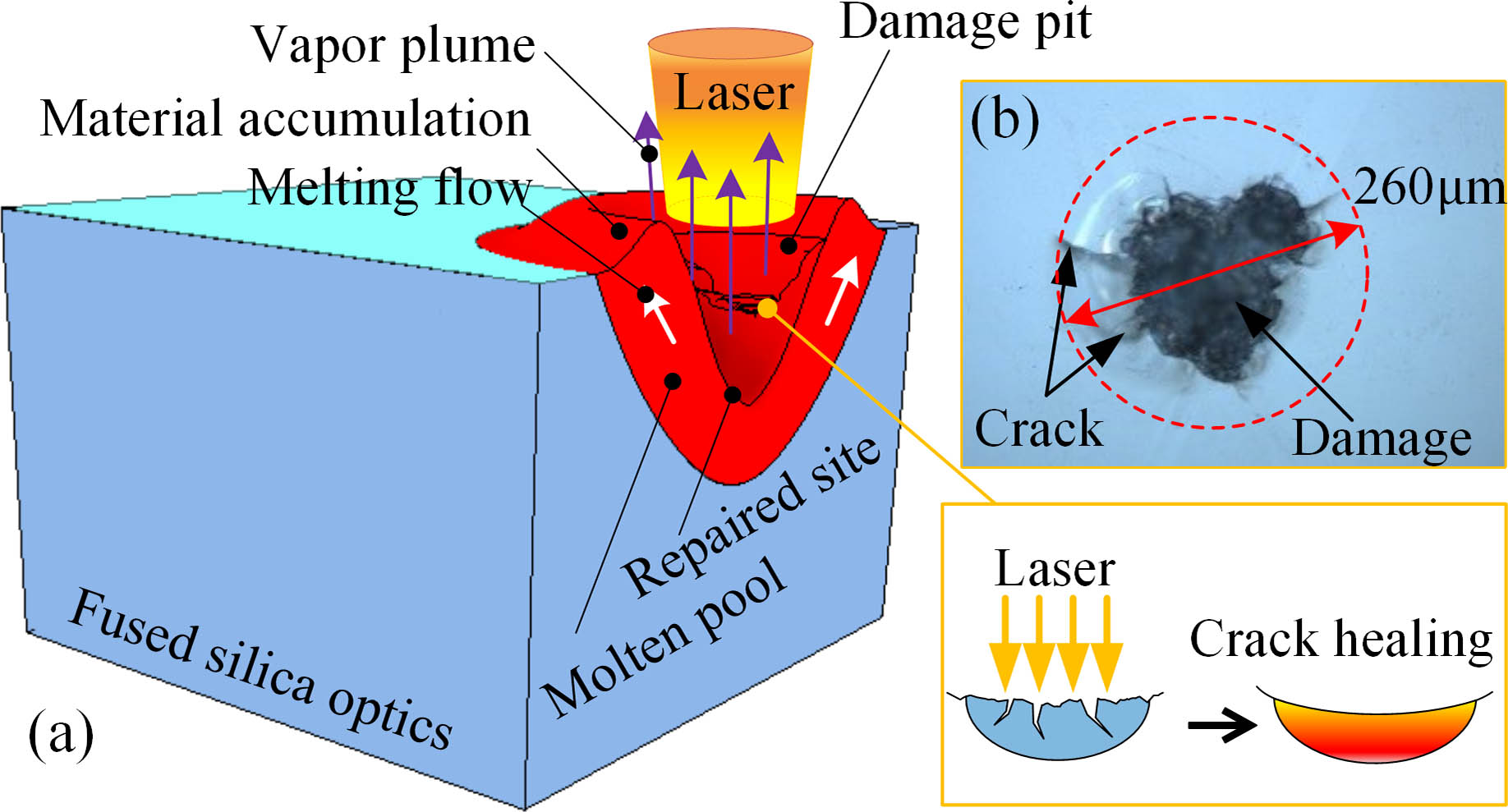
Author Affiliations
Abstract
1 State Key Laboratory of Robotics and System, Harbin Institute of Technology, Harbin 150001, China
2 Research Center of Laser Fusion, China Academy of Engineering Physics, Mianyang 621900, China
In order to reveal the evolution mechanism of repaired morphology and the material’s migration mechanism on the crack surface in the process of laser repairing surface damage of fused silica optics, two multi-physics coupling mathematical models with different scales are developed, respectively. The physical problems, such as heat and mass transfer, material phase transition, melt flow, evaporation removal, and crack healing, are analyzed. Studies show that material ablation and the gasification recoil pressure accompanying the material splash are the leading factors in forming the Gaussian crater with a raised rim feature. The use of low-power lasers for a long time can fully melt the material around the crack before healing, which can greatly reduce the size of the residual air layer. Combined with the experimental research, the methods to suppress the negative factors (e.g., raised rim, deposited debris, air bubbles) in the laser repairing process are proposed.
CO2 laser repairing fused silica crack healing surface evolution Chinese Optics Letters
2021, 19(4): 041402
1 河海大学机电工程学院, 江苏 常州 213022
2 哈尔滨工业大学先进焊接与连接国家重点实验室 黑龙江 哈尔滨 150001
利用激光熔覆修复方法修复了预置有通槽的5A06铝合金试样,通过金相显微镜和扫描电子显微镜等对修复试样的显微组织和拉伸性能进行了分析。热影响区中的β相在修复过程中受到热作用,尺寸增大,当线能量达到166.7 J/mm时,β相尺寸增大到1 μm以上。修复区的显微组织由α相、晶粒内部析出的β相及沿α相晶界分布的Al-Si共晶组织构成。当激光功率为1400 W时,未熔合缺陷得到有效抑制,气孔缺陷导致修复区强度和延伸率低于母材。
激光技术 激光熔覆修复 5A06合金 组织性能 激光与光电子学进展
2020, 57(23): 231409
1 华中科技大学材料科学与工程学院, 湖北 武汉 430073
2 湖北工业大学工程技术学院, 湖北 武汉 430064
研究了K452高温合金激光增材修复时的开裂特性及液化裂纹产生机理,采用低热输入脉冲激光工艺控制液化裂纹的产生,研究了修复区域的显微组织和力学性能。结果表明,K452高温合金在激光增材修复过程中容易产生液化裂纹,裂纹通常起源于热影响区且沿晶界向基体和修复区域扩展;拉应力作用下热影响区晶界上的液膜形成了液化裂纹。低热输入脉冲激光工艺可以有效控制液化裂纹的产生,脉冲激光修复试样修复区的平均硬度为267.9 HV;抗拉强度和屈服强度分别为814.3 MPa和685.8 MPa,略大于铸态基体的强度;延伸率为4.87%,略小于铸态基体的6.25%。低热输入脉冲激光工艺实现了无裂纹的开槽修复,铸态修复试样强度达到了铸态基体的强度标准,延伸率略低于铸态基体。
激光技术 激光修复 K452高温合金 液化裂纹 裂纹控制 力学性能
1 沈阳航空航天大学航空制造工艺数字化国防重点学科实验室, 辽宁 沈阳 110136
2 中国航发四川燃气涡轮研究院, 四川 绵阳 621700
采用激光沉积修复技术和电弧增材修复技术分别对预制损伤激光沉积制造TC4进行修复,然后对其进行不同的热处理,研究两种修复制件在热处理前后的组织和力学性能。结果表明:两种修复件的修复区均与基材形成了致密的冶金结合,无明显的热影响区;两种修复件的显微组织存在差异,激光修复区中的β柱状晶由基材延伸到修复区顶部,整体组织较为一致,而电弧修复区中出现了粗大的β等轴晶,晶内α相较基材的更细长;激光修复件的综合性能较好,其强度与塑性均高于TC4锻件标准,电弧修复件的强度与激光修复件的相当,但断面收缩率较激光修复件的低; 600 ℃退火处理对组织及性能的影响较小,而固溶时效处理能使α相明显粗化,大幅提升其塑性,且对强度的影响不大,可使制件获得较佳的强度/塑性匹配;两种热处理态修复件的拉伸断裂机制不同,激光修复件的断口表面布满大而深的韧窝,为韧性断裂,而电弧修复件断口上的颈缩不明显,韧窝较浅且起伏较小,表现为准解理断裂特征。
激光光学 激光修复 电弧修复 TC4钛合金 显微组织 力学性能 中国激光
2018, 45(12): 1202002
西北工业大学 凝固技术国家重点实验室, 陕西 西安 710072
研究了激光修复300M超高强度钢冲击韧性及断裂机理。结果表明, 激光修复300M超高强度钢沉积态的显微组织从修复区顶部到基材区发生了显著变化, 经过热处理后显微组织发生明显均匀化, 修复试样沉积态的冲击韧性为14.3 J/cm2, 远低于300M超高强度钢锻件。经过热处理后, 冲击韧性有了显著地提高, 达到28.3 J/cm2。沉积态试样的断裂方式为准解理断裂, 主裂纹在扩展的过程中横穿马氏体领域, 且在遇到下一个领域时会发生偏转。热处理态试样的断裂方式为韧性断裂。
激光修复 冲击韧性 断裂机理 300M超高强度钢 laser repairing impact toughness fracture mechanism 300M ultra-high strength steel
1 上海交通大学 电子信息与电气工程学院 薄膜与微细技术教育部重点实验室, 上海 200240
2 近地面探测与感知技术重点实验室, 江苏 无锡 214035
随着移动自组网络的快速发展, 对距离矢量按需路由协议(AODV)的服务质量提出了越来越高的要求。为了提升AODV在无线传感器网络通信中的表现, 文章提出了一种新型的基于AODV的多度量无线路由协议(MWR-AODV)。MWR-AODV综合考虑了对路由协议性能影响重大的最小跳数、剩余能量、能量流失率和网络节点密度这四个因素, 并且引入了一种低成本且高效的本地修复策略。通过Network Simulator-2仿真平台对MWR-AODV与标准AODV、DSDV协议的表现进行了仿真分析。结果表明, 所提出的MWR-AODV能为无线传感器网络提供更好的通信服务, 并且在均衡能量消耗延长网络寿命和平衡网络通信负载方面也有上佳表现。
剩余能量 能量流失率 网络密度 本地预修复 AODV AODV residual energy energy drain rate network density preemptive repairing mechanism
采用激光沉积修复方法对TC4槽损伤和面损伤试样进行了修复试验,观察了修复试样的组织和拉伸性能特点,发现修复区与基材之间形成了致密冶金结合,激光修复试样组织是由基材的双态组织经由热影响区过渡到修复区的魏氏组织。修复区组织由粗大原始β柱状晶粒及晶内细长的α针及编织细密的α+β板条组织组成。对槽修复试样进行维氏硬度测量发现,激光修复区的硬度比锻件基体区高15%,热影响区的硬度居于二者之间。修复试样的室温静拉伸结果表明,试样的抗拉强度高于同批次的工业锻件水平,但是塑性低于锻件水平。
激光沉积修复 TC4钛合金 组织 拉伸性能 laser deposition repairing TC4 alloy microstructure tensile properties