不同粒径粉末搭配对激光选区熔化IN738合金成形件表面粗糙度及内部缺陷的影响
下载: 1000次
1 引言
激光选区熔化技术(SLM)能够自动、快速、准确地将数字模型直接或间接转化成有一定功能的零件,因而在全球得到迅速的发展[1]。长期以来,研究人员在探讨SLM工艺参数对成形件质量的影响及优化成形件的后处理工艺参数等方面做了大量的工作[2-3]。Carter等[4]和Catchpole-Smith等[5]研究了扫描策略与裂纹的形成和分布之间的关系,并通过改变激光扫描策略降低了裂纹密度,提高了CM247LC成形件的致密度;Perevoshchikova等[6]使用Doehlert设计,经过14次实验,优化了IN738LC合金SLM成形参数,成形出致密度接近100%且无裂纹的IN738LC合金试样;Wang等[7]在IN738LC合金的SLM成形中,通过前期粉末筛分处理及工艺参数优化,成功打印出几乎完全致密的合金试样,经过后期的热等静压和双重时效热处理,试样具有优良的强度和延展性。
研究表明,SLM成形零件的性能不仅与打印工艺参数有关,而且与原材料粉末特性密切相关[8-9],粉末的特性主要包括粉末成分、粉末形态、粉末氧含量等,其中由不同粒径粉末搭配所造成的成形粉末的粒径分布、松装密度、流动性等对于SLM加工过程及成形零件的性能有很大的影响[10-12]。Nguyen等[13]研究了镍铬铁合金的原始粉末和循环使用10次后回收粉末的SLM成形性能,结果表明,适合SLM工艺的粒径分布范围为15~63 μm,原始粉末相较于回收粉末具有更好的流动性,但二者成形零件均具有良好的力学性能;魏青松等[14]对比了不同粒径分布的316L不锈钢SLM成形件,研究发现,粉末粒径越小,成形件致密度越高,但粒径过小时,粉末颗粒容易发生团聚,使得粉末流动性变差,反而影响成形质量;Spierings等[15]通过对不同粒径的316L不锈钢粉末成形件研究发现,粉末粒度分布越窄、松装密度越高,成形时球化现象越少,且成形件致密度和表面质量更好;Gu等[16]研究了粉末粒径分布对SLM成形Ti-6Al-4V合金性能的影响,结果表明,在相同范围内粒径分布具有双峰特征的金属粉末,成形件具有较高的致密度和力学性能;王黎等[17]研究了316L不锈钢粉末粒径和松装密度对成型性能的影响,发现在一定范围内,粉末粒径越小,成形过程中颗粒飞溅现象越少,熔池越稳定,成形件表面粗糙度越小,而粒度分布较宽的粉末在成形时容易发生球化现象。此外,粉末松装密度越高,成形件致密度越大。
IN738合金是一种沉淀强化型镍基高温合金,其工作温度约为980 ℃[18]。由于该合金具有优异的高温蠕变性能和耐热腐蚀性能而被广泛应用于航空发动机、燃气轮机等热端部件[19]。虽然采用SLM技术成形这类复杂结构零件具有独特优势,但是相较于其他镍基高温合金而言,IN738合金化学成分更加复杂,Al、Ti含量更高(约6.8%),具有较高的裂纹敏感性而被称为“难焊合金”[20-23]。目前对于SLM成形IN738合金的工艺优化及缺陷控制已有广泛研究[24-27],但高品质的SLM用IN738合金粉末的选择和评定标准还有待完善,特别是不同粒径粉末搭配对于成形粉末特性及打印件质量影响的相关研究还很欠缺。因此,本文系统研究了同批次不同粒度粉末搭配形成成形粉末的物理特性及其对成形件致密度、表面粗糙度和内部缺陷的影响。该研究工作将为后续制备高质量、全致密的打印件,原材料的选择和制定SLM技术用粉末标准提供参考依据。
2 试验材料与方法
试验原材料为通过气雾化技术制备的商用IN738合金粉末。为了保持粉末特性(包括粉末的形态和成分)的一致性,选用同一批粉末预先筛分成细粉(粒径为15~30 μm)和粗粉(粒径为30~53 μm),随后将粗细粉末按照一定的比例进行充分混合,并进行编号。成形粉末具体如下:1#代
采用EOS公司INT M280型SLM成形设备完成试块制备。具体打印参数如下:粉末层厚为0.04 mm、激光功率为270 W、扫描速度为1150 mm/s、扫描间距为0.09 mm。试验采用316L不锈钢基板并预热至100 ℃,激光扫描策略如
采用蔡司LSM 800型激光扫描共聚焦显微镜对试样上表面以及侧表面粗糙度进行测量,每个试样测量3次并取平均值;采用DH-200M型高精度密度测试仪检测SLM成形件密度;对抛光的试样截面选取5张相同倍数的光学显微照片,采用Image pro plus分析计算每张图片中孔洞面积占该图片面积的百分比并求其平均值得到孔隙率;对抛光的XOY面和XOZ面分别选取5张相同倍数的光学显微照片,采用Image pro plus分析计算每张图片中裂纹面积占该图片面积的百分比并求其平均值得到裂纹密度;采用Quanta 450 FEG场发射扫描电镜及电子背散射衍射(EBSD)对试样微观组织及晶粒取向进行表征分析。
3 试验结果与讨论
3.1 不同粒度粉末搭配对粉末特性的影响
同一生产批次的合金粉末经筛分后以不同比例混合得到三种不同粒径分布的粉末,三种粉末的化学成分保持一致,如
表 1. IN738合金粉末元素含量(质量分数,%)
Table 1. IN738 alloy powder element content (mass fraction, %)
|
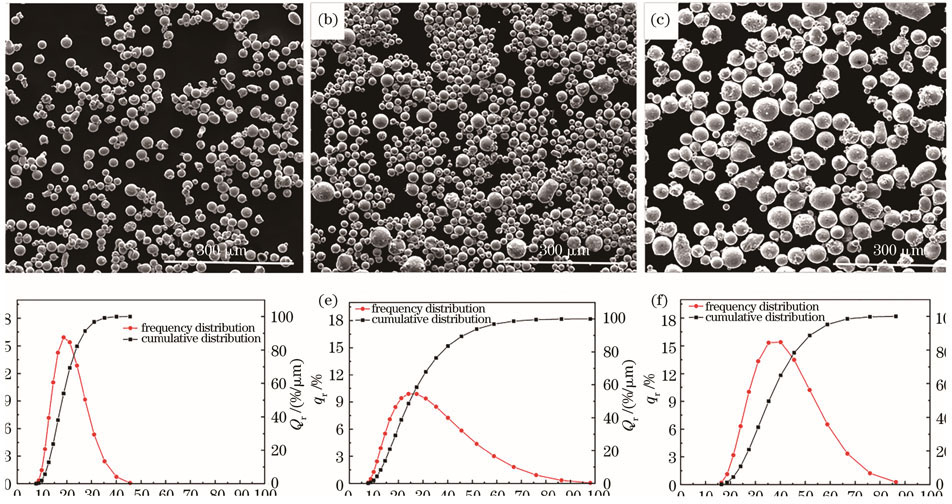
图 2. 不同粒径分布的IN738合金粉末形貌和粒度分布图。(a)~(c)1#粉末、2#粉末、3#粉末颗粒形貌;(d)~(f)1#粉末、2#粉末、3#粉末粒度分布图
Fig. 2. Morphology and particle size distribution of IN738 alloy powder with different particle sizes. (a)?(c) Particle morphology of 1 # powder, 2 # powder, and 3 # powder; (d)?(f) particle size distribution of 1 # powder, 2 # powder, and 3 # powder
表 2. IN738合金粉末粒度分布特征量和物理性能
Table 2. IN738 alloy powder particle size distribution characteristics and physical properties
|
3.2 不同粒度粉末搭配对成形件表面粗糙度和致密度的影响
虽然三种粉末的XOZ面粗糙度值和XOY面粗糙度值具有相同的变化趋势,但很明显,XOZ面比XOY面粗糙度值高。
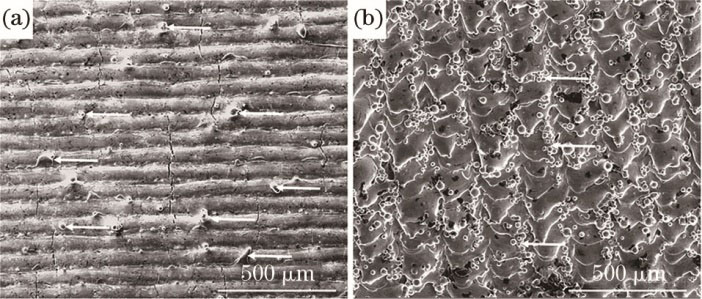
图 4. 2#粉末SLM成形件表面形貌。(a)XOY面;(b)XOZ面
Fig. 4. Surface morphology of 2 # powder SLM forming parts. (a) XOY plane; (b) XOZ plane
由
式中:
3.3 不同粒度粉末搭配对孔隙率和裂纹密度的影响

图 5. 不同粒径粉末制备的SLM成形件的孔隙率和裂纹密度
Fig. 5. Porosity and crack density of SLM shaped parts prepared with powders of different particle sizes
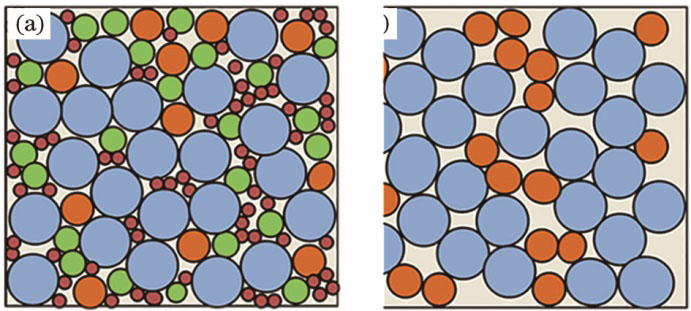
图 6. 不同粒径粉末铺粉的示意图。(a)粉末粒径配比均匀;(b)粉末粒径单一
Fig. 6. Schematic of powder spreading with different particle sizes. (a) Powder particle size ratio is uniform; (b) single powder size
3.4 成形件内部组织及裂纹形态
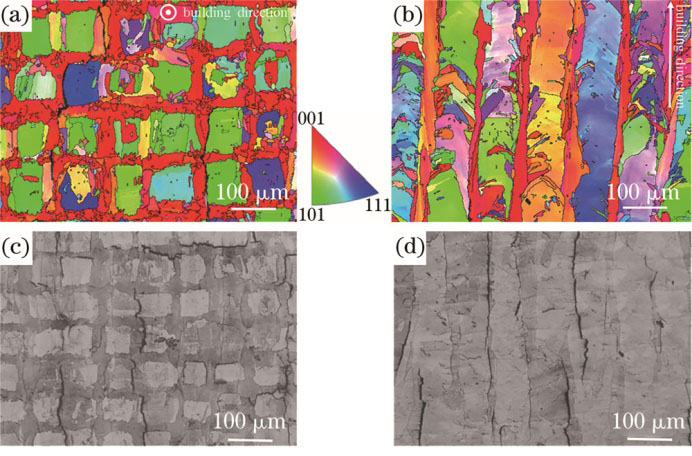
图 7. 2#粉末SLM成形件XOY和XOZ面IPF晶粒结构图及显微组织。(a)XOY面IPF;(b)XOZ面IPF;(c)XOY面微观形貌;(d)XOZ面微观形貌
Fig. 7. 2 # powder SLM formed parts XOY and XOZ plane IPF grain structure diagram and microstructure. (a) XOY plane IPF; (b) XOZ plane IPF; (c) XOY plane microtopography; (d) XOZ plane microtopography
根据熔池内部组织及晶粒生长方向,建立单熔池内部组织生长模型如
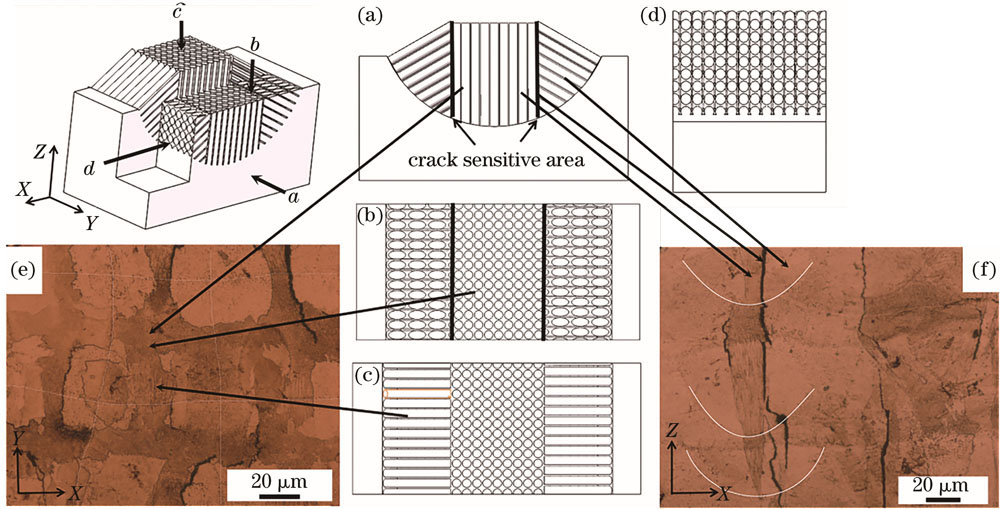
图 8. XOY面和XOZ面熔池组织模型示意图。(a)单个熔池模型;(b)(c)图(a)的俯视图;(d)切割位置示意图;(e)XOY 面熔池;(f)XOZ 面熔池
Fig. 8. Schematic of molten pool organization model on XOY plane and XOZ plane. (a) Single molten pool model; (b) (c) top view of Fig. (a); (d) schematic of cutting position; (e) molten pool on XOY plane; (f) molten pool on XOZ plane
4 结论
不同粒度粉末搭配是决定成形粉末物性参数及影响成形件性能的至关重要因素。本研究通过对三种不同搭配比例成形粉末的粉末特性、成形件表面质量及内部缺陷研究发现:
1)当粉末为100%粗粉或细粉时,松装密度和振实密度较小,但粗粉的流动性最好,细粉流动性最差;
2)单一粗粉或细粉所对应的打印成形件的表面粗糙度及内部缺陷相较于粗细颗粒搭配的粉末差;
3)粗细粉末颗粒相互搭配时,流动性和松装密度都较好,成形件表面粗糙度最小,致密度可以达到99.3%,内部孔隙密度和裂纹密度相应最小。IN738合金SLM成形件内部的裂纹主要为凝固裂纹,分布在熔池中心,裂纹沿着外延生长的〈001〉取向的柱状晶晶界扩展。
[2] 马英怡, 刘玉德, 石文天, 等. 扫描速度对选区激光熔化316L不锈钢粉末成形缺陷及性能的影响[J]. 激光与光电子学进展, 2019, 56(10): 101403.
[3] 万乐, 王思琦, 张晓伟, 等. 基于分区扫描的选区激光熔化钛合金的成形质量[J]. 激光与光电子学进展, 2018, 55(9): 091401.
[5] Catchpole-Smith S, Aboulkhair N, Parry L, et al. Fractal scan strategies for selective laser melting of ‘unweldable’ nickel superalloys[J]. Additive Manufacturing, 2017, 15: 113-122.
[6] Perevoshchikova N, Rigaud J, Sha Y, et al. Optimisation of selective laser melting parameters for the Ni-based superalloy IN-738 LC using Doehlert’s design[J]. Rapid Prototyping Journal, 2017, 23(5): 881-892.
[8] 周燕, 段隆臣, 吴雪良, 等. 粉末粒径对激光选区熔化成形S136模具钢的磨损与抗腐蚀性能的影响[J]. 激光与光电子学进展, 2018, 55(10): 101403.
[9] 吴伟辉, 杨永强, 卫国强. 激光选区熔化快速成型制造精密金属零件技术[J]. 中国激光, 2007, 34(s1): 175-179.
[11] 杨倩, 胡勇, 丁雨田, 等. 选区激光熔化所用IN738合金粉末的特性与成形性[J]. 激光与光电子学进展, 2019, 56(10): 101402.
[12] 孙健峰, 杨永强, 杨洲. 基于粉末特性的选区激光熔化Ti6Al4V表面粗糙度研究[J]. 中国激光, 2016, 43(7): 0702004.
[13] Nguyen Q B. Nai M L S, Zhu Z G, et al. Characteristics of inconel powders for powder-bed additive manufacturing[J]. Engineering, 2017, 3(5): 695-700.
[14] 魏青松, 王黎, 张升, 等. 粉末特性对选择性激光熔化成形不锈钢零件性能的影响研究[J]. 电加工与模具, 2011( 4): 52- 56, 69.
Wei QS, WangL, ZhangS, et al. Study on the effects of powder properties on the performance of stainless steel parts produced by selective laser melting[J]. Electromachining & Mould, 2011( 4): 52- 56, 69.
[16] Gu HF, Gong HJ, Dilip J J S, et al. Effects of powder variationon the microstructure and tensile strength of Ti6Al4V parts fabricated by selective laser melting[C]//International Solid Freeform Fabrication Symposium. Aug. 2014, Austin, USA: FFS, 2014: 39, 470- 483.
[17] 王黎, 魏青松, 贺文婷, 等. 粉末特性与工艺参数对SLM成形的影响[J]. 华中科技大学学报(自然科学版), 2012, 40(6): 20-23.
Wang L, Wei Q S, He W T, et al. Influence of powder characteristic and process parameters on SLM formability[J]. Journal of Huazhong University of Science and Technology (Natural Science Edition), 2012, 40(6): 20-23.
[18] Egbewande A T, Zhang H R, Sidhu R K, et al. Improvement in laser weldability of INCONEL 738 superalloy through microstructural modification[J]. Metallurgical & Materials Transactions A, 2009, 40(11): 2694-2704.
[19] Campo E, Lupinc V. High temperature structural materials for gas turbines[J]. Metallurgical Science & Technology, 2013, 11(1): 31-45.
[22] Sames W J, Unocic K A, Helmreich G W, et al. Feasibility of in situ controlled heat treatment (ISHT) of Inconel 718 during electron beam melting additive manufacturing[J]. Additive Manufacturing, 2017, 13: 156-165.
[23] Slotwinski J A, Garboczi E J. Metrology needs for metal additive manufacturing powders[J]. JOM, 2015, 67(3): 538-543.
[28] 李瑞迪. 金属粉末选择性激光熔化成形的关键基础问题研究[D]. 武汉: 华中科技大学, 2010.
Li RD. Research on the key basic issues in selective laser melting of metallic powder[D]. Wuhan: Huazhong University of Science and Technology, 2010.
[29] Akram J, Chalavadi P, Pal D, et al. Understanding grain evolution in additive manufacturing through modeling[J]. Additive Manufacturing, 2018, 21: 255-268.
[32] Wang N, Mokadem S, Rappaz M, et al. Solidification cracking of superalloy single- and bi-crystals[J]. Acta Materialia, 2004, 52(11): 3173-3182.
Article Outline
胡勇, 杨小康, 康文江, 丁雨田, 许佳玉, 张会莹. 不同粒径粉末搭配对激光选区熔化IN738合金成形件表面粗糙度及内部缺陷的影响[J]. 激光与光电子学进展, 2021, 58(1): 0114003. Hu Yong, Yang Xiaokang, Kang Wenjiang, Ding Yutian, Xu Jiayu, Zhang Huiying. Effects of Combination of Powders with Different Particle Sizes on Surface Roughness and Internal Defects of IN738 Alloy Formed by Selective Laser Melting[J]. Laser & Optoelectronics Progress, 2021, 58(1): 0114003.