送粉式激光增材制造TC4钛合金熔覆层组织及电化学腐蚀行为的研究
下载: 1301次
1 引言
TC4钛合金是一种具有高比强度、高比韧性等优异综合力学性能的金属材料,具有优良的耐蚀性和耐高温性,广泛应用于航空航天、电子化工及汽车制造等工业领域[1]。但由于钛合金的硬度低、耐磨性差,且易在强酸、强碱等环境下发生严重腐蚀[2],从而在一定程度上限制了它的发展及应用。为提高钛合金的性能,扩展其在各领域的应用与发展,国内外学者研究了钛合金的制备方法,如铸造、锻造、焊接、激光熔覆、激光增材制造[3-4]等。其中,激光增材制造(LDM)技术[5-7]是一种将增材制造思想与激光熔覆原理相结合的技术,采用高功率激光熔融金属粉末,根据预设轨迹逐层自下而上沉积[8-9],在基体上形成高性能的熔覆层,可以改善材料的力学性能及耐蚀性。激光增材制造技术具有低成本、低耗材、高效率等特点,发展及应用前景十分广阔。Wang等[10]研究了激光增材制造钛合金零件晶粒形貌的演化行为,认为工艺参数对非均质成核的等轴晶及外延生长的柱状晶均有很大影响。Zhu等[11]发现激光增材制造钛合金相比传统铸造钛合金表现出了高强度和低延展性。刘金等[12]发现激光增材制造沉积态Ti60A钛合金比锻态钛合金表面的氧化膜更致密,高温抗氧化性更高。所查资料显示,多数研究[13-16]是针对激光增材制造钛合金显微组织及力学性能开展的,而对其抗电化学腐蚀性能方面的研究则鲜有报道。
本课题组采用激光增材制造技术在TC4钛合金基体上制备了TC4钛合金熔覆层,通过X射线衍射(XRD)分析、扫描电镜(SEM)观察、能谱(EDS)分析、显微硬度测试、电化学腐蚀实验研究了熔覆层的显微组织及电化学腐蚀行为,并与基体试样进行对比,期望能为扩展LDM TC4钛合金熔覆层在相关领域中的发展及应用提供参考。
2 实验
2.1 实验材料与设备
以尺寸为60 mm×60 mm×20 mm的TC4钛合金(Ti-6Al-4V)板作为基体,以TC4钛合金粉末作为熔覆材料进行实验。TC4钛合金粉末的成分列于
表 1. TC4钛合金粉末的化学成分
Table 1. Chemical composition of TC4 alloy powders
|
试验采用南京中科煜宸公司LDM-8060送粉式金属3D打印设备,其配有德国Laserline公司的Laserline-4000型高功率半导体激光器。在钛合金板上采用激光增材制造技术制备多道单层TC4钛合金熔覆层,
2.2 显微结构表征
用Rigaku D/Max 2550型(日本理学公司)X射线衍射仪分析熔覆层的物相结构,扫描角度范围为10°~80°,然后用X' Pert HighScore和Jade 6软件对检测结果进行分析,并标定出其物相成分。采用由氢氟酸、硝酸、蒸馏水按体积比为1∶2∶59配制而成的混合溶液腐蚀试样表面30 s,然后用德国ZEISS公司的Sigma300场发射扫描电镜观察熔覆层的微观形貌,并用其自带的能谱仪对元素分布及含量进行分析,其中扫描电镜的加速电压为5 kV。
2.3 性能测试
采用上海比目仪器有限公司的HXDG1000T型数字显微硬度计测试熔覆层的显微硬度,加载载荷为1.96 N,保载时间为10 s,从接近熔覆层表面向下每隔50 μm测试一个点,测试点均在同一直线上,显微硬度取三次测试的平均值。采用武汉科思特仪器股份有限公司的CS350型电化学工作站测试熔覆层的抗电化学腐蚀性能。电解液选择浓度为0.5 mol/L的H2SO4溶液,采用三电极测量系统,辅助电极为铂电极,参考电极(RE)为饱和甘汞电极,工作电极(WE)为制备的熔覆层试样,工作电极的表面积为1 cm2。电化学阻抗测试频率范围为10-2~105 Hz,测试前先将熔覆层试样在电解液中浸泡1 h,所有测试均在稳定的开路电位下测试完成;然后测试其电化学阻抗谱和动电位极化曲线,以20 V/min的扫描速率从腐蚀电位-1.2 V扫描至1.2 V。用CS Studio 5软件计算自腐蚀电位和腐蚀电流密度,分析电化学交流阻抗谱,并建立对应的等效电路。每个试样均至少测试三次,并取平均值,以尽量避免测试过程中的误差。
3 实验结果分析
3.1 显微组织
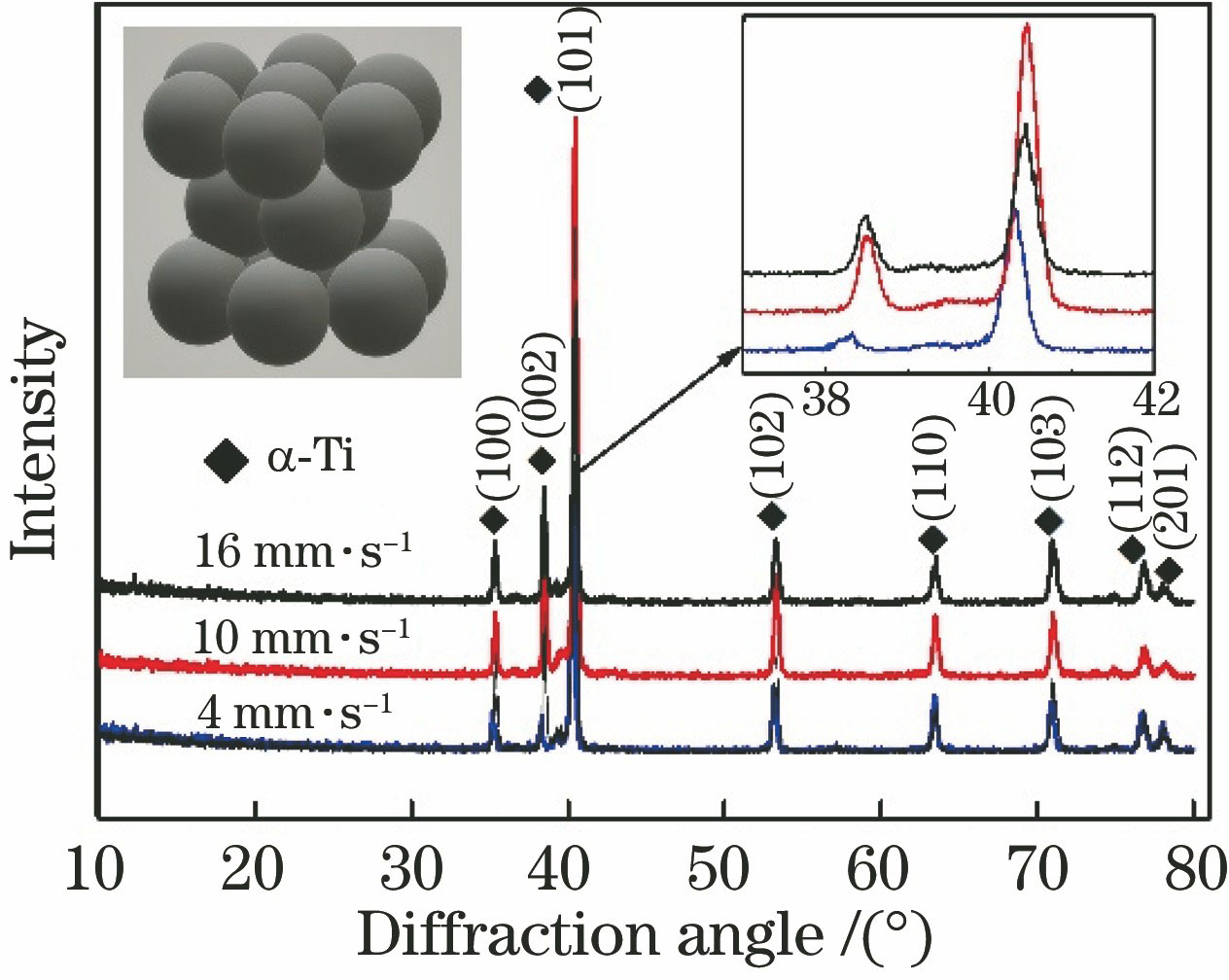
图 2. 不同扫描速率下制备的熔覆层的XRD衍射图谱
Fig. 2. XRD diffraction spectra of cladding layers prepared at different scanning speeds
激光增材制造技术的冷却速率极高,所形成的熔覆层的组织、性能与基体截然不同,
另外,如

图 3. 不同扫描速率下制备的试样的横截面形貌。(a) 4 mm/s,基体/熔覆层结合区;(b) 10 mm/s,基体/熔覆层结合区;(c) 16 mm/s,基体/熔覆层结合区;(d) β晶界;(e) 4 mm/s,熔覆层中部;(f) 10 mm/s,熔覆层中部;(g) 16 mm/s熔覆层中部;(h)基体
Fig. 3. Cross-section of samples prepared at different scanning speeds. (a) 4 mm/s, bonding zone of the substrate and cladding layer; (b) 10 mm/s, bonding zone of the substrate and cladding layer; (c) 16 mm/s, bonding zone of the substrate and cladding layer; (d) β-grain boundary; (e) 4 mm/s, middle of cladding layer; (f) 10 mm/s, middle of cladding layer; (g) 16 mm/s, cladding layer; (h) substrate
对熔覆层中的β晶界进行EDS能谱分析,测定熔池凝固组织晶粒内部及晶界上Al、V合金元素的分布及含量,选取
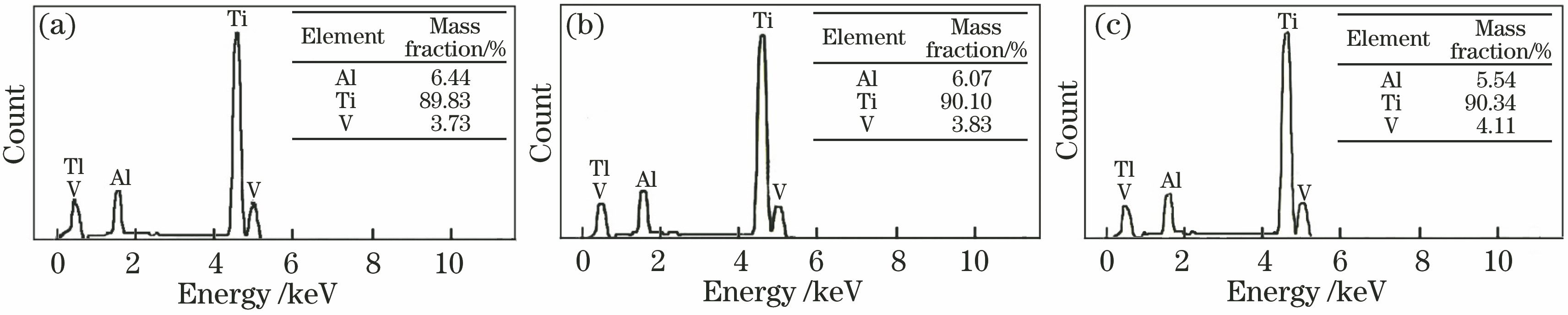
图 4. 元素含量的EDS分析结果。(a)点D;(b)点E;(c)点F
Fig. 4. EDS analysis of element content. (a) Point D; (b) point E; (c) point F
3.2 显微硬度
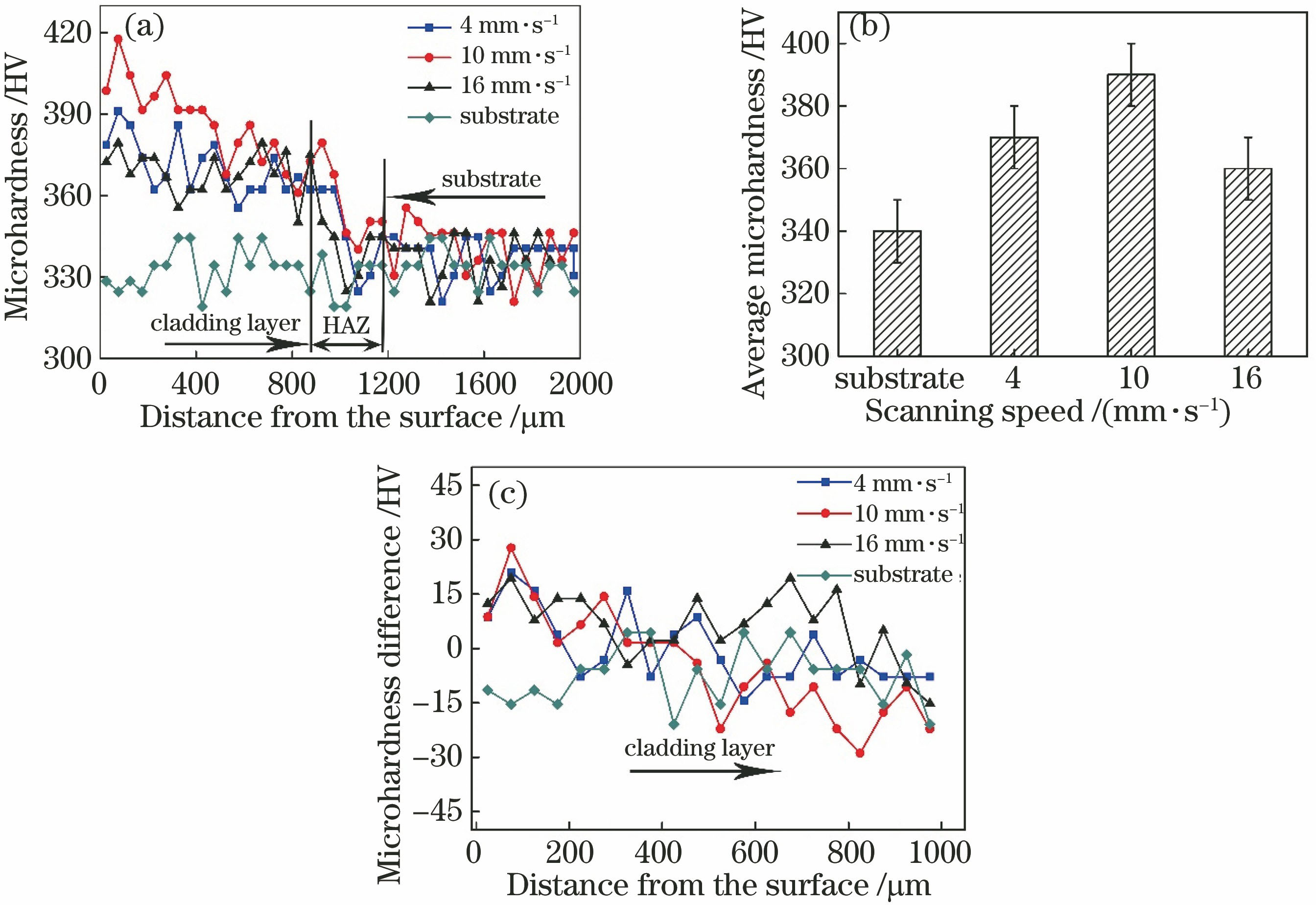
图 5. 不同扫描速率下制备的熔覆层的显微硬度测试结果。(a)显微硬度分布;(b)平均显微硬度;(c)偏差值
Fig. 5. Tested microhardness of cladding layer prepared at different scanning speeds. (a) Microhardness distribution; (b) average microhardness; (c) microhardness difference
结合之前的分析可知,基体的晶粒尺寸为1~1.2 μm,熔覆层内的晶粒尺寸为0.3~0.5 μm。根据Hall-Petch公式可知[24],屈服极限
式中:
3.3 电化学腐蚀行为
3.3.1 动电位极化曲线
表 2. 极化曲线的标准腐蚀参数
Table 2. Standard corrosion parameters of polarization curve
|
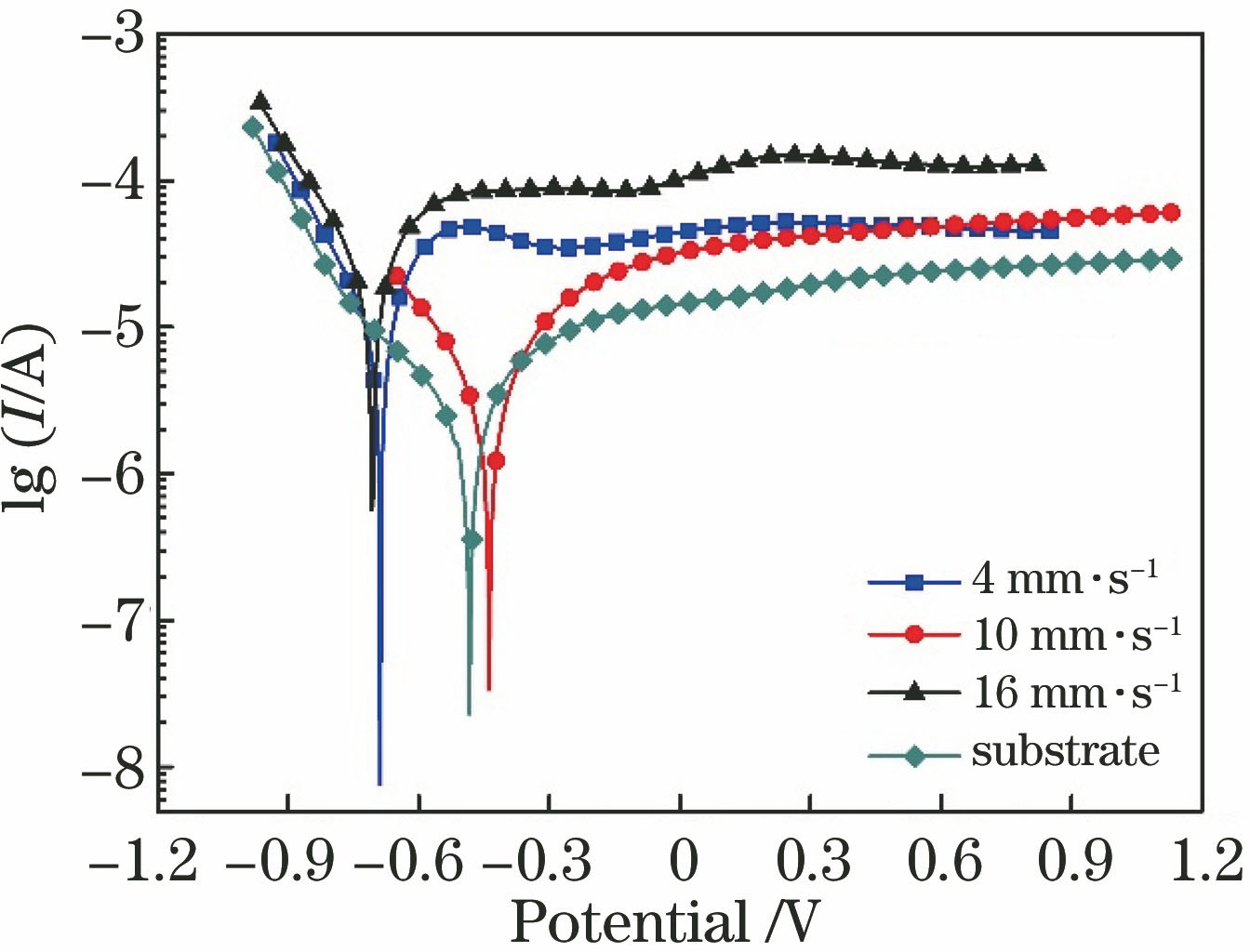
图 6. 不同扫描速率下制备的熔覆层的动电位极化曲线
Fig. 6. Polarization curves of dynamic potential of cladding layers prepared at different scanning speeds
另外,极化电阻是腐蚀电化学中重要的动力学参数之一。随着扫描速率增大,熔覆层的极化电阻呈先增大后减小的趋势,表明其耐蚀性先增强后减弱;与4 mm/s和16 mm/s相比,扫描速率为10 mm/s时制备的熔覆层具有最大的极化电阻(98966 Ω),约为基体(145800 Ω)的68%,具有优异的耐蚀性,但略低于基体的耐蚀性。在阳极区域,随着腐蚀电压缓慢增大,自腐蚀电流均明显增大,熔覆层表面处于活性溶解状态,且都具有明显的钝化行为。从
3.3.2 交流阻抗谱
为了进一步论证熔覆层与基体的电化学腐蚀行为特征,
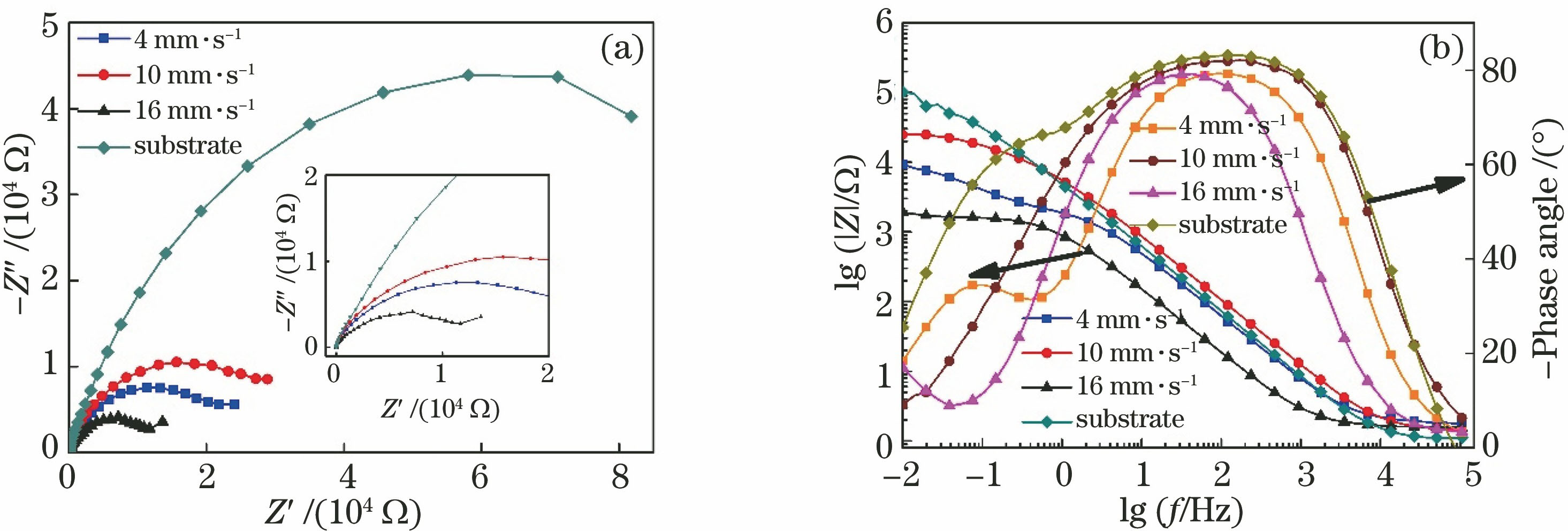
图 7. 不同扫描速率下制备的熔覆层的EIS结果。(a) Nyquist曲线;(b)波特图
Fig. 7. EIS results of cladding layers prepared at different scanning speeds. (a) Nyquist curves; (b) bode diagram
熔覆层和基体具有相同的等效电路模型,如
表 3. 等效模拟电路的电气参数
Table 3. Electrical parameters of equivalent simulated circuit
|
3.3.3 腐蚀机理
金属材料发生点蚀的难易程度一般由点蚀电位
表 4. 不同扫描速率下制备的熔覆层的点蚀参数
Table 4. Pitting parameters of cladding layers prepared at different scanning speeds
|
钛合金的腐蚀行为及腐蚀程度受其化学成分、显微组织、晶粒度、晶体缺陷、性能、热处理工艺以及表面状态的影响[33]。
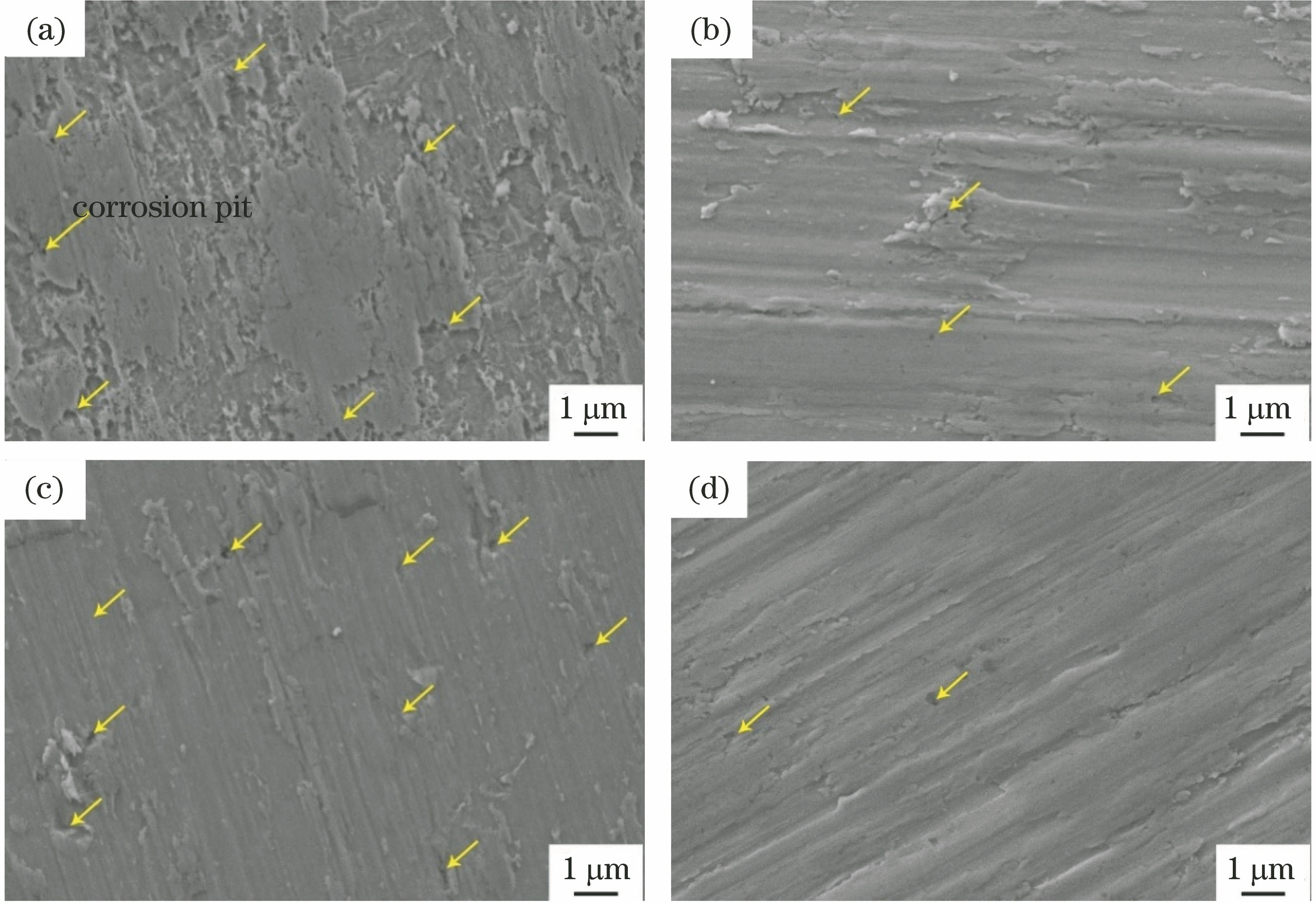
图 9. 不同扫描速率下制备的熔覆层在电化学腐蚀后的SEM照片。(a) 4 mm/s;(b) 10 mm/s;(c) 16 mm/s;(d)基体
Fig. 9. SEM images of cladding layers prepared at different scanning speeds. (a) 4 mm/s; (b) 10 mm/s; (c) 16 mm/s; (d) substrate
综上可知,随着扫描速率增大,熔覆层在0.5 mol/L H2SO4溶液中的耐蚀性先增大后减小。在激光增材制造过程中,扫描速率过大或过小都会对熔覆层组织的形成及性能有不利的影响。在本实验条件下,当描速率为10 mm/s时,制备得到的熔覆层具有较好的耐蚀性。
4 结论
研究分析了不同扫描速率下制备的TC4熔覆层的显微组织,并采用电化学腐蚀测试方法研究了其在H2SO4溶液中的电化学腐蚀行为,得到如下结论:1) 熔覆层的β晶界附近生成了α-Ti固溶体及细针状α'马氏体,在10 mm/s扫描速率下得到的熔覆层的组织更加均匀致密,组织呈正交状网篮;2) 随着扫描速率增大,熔覆层的显微硬度先增大后减小,当扫描速率为10 mm/s时,熔覆层的显微硬度最高,约为390 HV,比基体提高了约14.71%,这是由于激光熔融金属粉末过程中发生了固溶强化、晶粒细化及马氏体切变;3) 随着扫描速率增大,熔覆层的自腐蚀电位
尽管通过激光增材制造技术得到了组织和性能较优的熔覆层,但其在H2SO4溶液中的抗电化学腐蚀性能还有待提高。在激光增材制造过程中应选取适当的工艺参数,因为其对所制备的熔覆层的组织、性能都有很大影响。
[1] 原国森, 兖利鹏, 韩艳艳. 钛合金的应用进展[J]. 热加工工艺, 2017, 46(4): 13-16.
[2] Cao S, Zhu S M. Lim C V S, et al. The mechanism of aqueous stress-corrosion cracking of α+β titanium alloys[J]. Corrosion Science, 2017, 125: 29-39.
[4] 王科. 钛合金制备方法的研究进展[J]. 材料导报, 2014, 28(S2): 143-146,158.
Wang K. Progress in manufacture of titaniumalloy[J]. Materials Review, 2014, 28(S2): 143-146,158.
[5] 王舒, 程序, 田象军, 等. TiC添加量对激光增材制造MC碳化物增强Inconel625复合材料组织及性能的影响[J]. 中国激光, 2018, 45(6): 0602002.
[6] 王志会, 王华明, 刘栋. 激光增材制造AF1410超高强度钢组织与力学性能研究[J]. 中国激光, 2016, 43(4): 0403001.
[9] Gasser A, Backes G, Kelbassa I, et al. Laser additive manufacturing[J]. Laser Technik Journal, 2010, 7(2): 58-63.
[12] 刘金, 王薇茜, 程序, 等. 激光增材制造Ti60A钛合金的氧化行为[J]. 中国激光, 2018, 45(7): 0702007.
[13] Wang P, Huang Z H, Qi W J, et al. Application and research progress on titanium alloy printed by 3D technology[J]. Material Sciences, 2017, 7(3): 275-282.
[17] PolmearI, StjohnD, Nie JF, et al. Titanium alloys[M] ∥Polmear I, Stjohn D, Nie J F, et al. Light alloys. Netherlands: Elsevier, 2017: 369- 460.
[19] 张霜银, 林鑫, 陈静, 等. 工艺参数对激光快速成形TC4钛合金组织及成形质量的影响[J]. 稀有金属材料与工程, 2007, 36(10): 1839-1843.
[20] 张启良. TC4钛合金激光焊接工艺优化及接头组织性能研究[D]. 呼和浩特: 内蒙古工业大学, 2014.
Zhang QL. Welding process optimization and research on microstructure and properties FNR laser weld joints of TC4 Titanium alloy[D]. Hohhot: Inner Mongolia University of Technology, 2014.
[21] 姚化山, 史玉升, 章文献, 等. 金属粉末选区激光熔化成形过程温度场模拟[J]. 应用激光, 2007, 27(6): 456-460.
[22] 崔忠圻, 覃耀春. 金属学与热处理[M]. 2版. 北京: 机械工业出版社, 1989.
Cui ZY, Yan YC. Metallurgy and heat treatment[M]. 2nd ed. Beijing: Mechanical Industry Press, 2009.
[25] 曹楚南. 腐蚀电化学原理[M]. 3版. 北京: 化学工业出版社, 2008.
Cao CN. Principles of electrochemistry of corrosion[M]. 3rd ed. Beijing: Chemical Industry Press, 2008.
[28] 曹楚南, 张鉴清. 电化学阻抗谱导论[M]. 北京: 科学出版社, 2002.
Cao CN, Zhang JQ. An introduction to electrochemical impedance spectroscopy[M]. Beijing: Science Press, 2002.
[29] SatoN. Basics of corrosion chemistry[M] ∥Sato N. Green corrosion chemistry and engineering. Weinheim, Germany: Wiley-VCH Verlag GmbH & Co. KGaA, 2011: 1- 32.
[30] Newman R. Pitting corrosion of metals[J]. The Electrochemical Society Interface, 2010, 19(1): 33-38.
[31] 王海杰, 王佳, 彭欣, 等. 钛合金在3.5%NaCl溶液中的腐蚀行为[J]. 中国腐蚀与防护学报, 2015, 35(1): 75-80.
Wang H J, Wang J, Peng X, et al. Corrosion behavior of three titanium alloys in 3.5%NaCl solution[J]. Journal of Chinese Society for Corrosion and Protection, 2015, 35(1): 75-80.
[32] PedeferriP. Pitting corrosion[M] ∥Pedeferri P. Corrosion science and engineering. Cham: Springer, 2018: 207- 230.
[34] Shoesmith DW, Noël JJ. Corrosion of titanium and its alloys[M] ∥Shoesmith D W, Noël J J. Shreir's corrosion. Netherlands: Elsevier, 2010: 2042- 2052.
[35] PourbaixM, Staehle RW. Lectures on electrochemical corrosion[M]. Boston, MA: Springer US, 1973.
[36] Schmuckler J S. Oxidation reduction electrochemistry[J]. Journal of Chemical Education, 1981, 58(5): 404.
冯晓甜, 顾宏, 周圣丰, 雷剑波. 送粉式激光增材制造TC4钛合金熔覆层组织及电化学腐蚀行为的研究[J]. 中国激光, 2019, 46(3): 0302003. Xiaotian Feng, Hong Gu, Shengfeng Zhou, Jianbo Lei. Microstructure and Electrochemical Corrosion Behavior of TC4 Titanium Alloy Cladding Layer Prepared with Powder Feeding Laser Additive Manufacturing[J]. Chinese Journal of Lasers, 2019, 46(3): 0302003.