基于反射云纹的抛光曲面表面缺陷检测研究
下载: 1074次
1 引言
为实现“中国制造2025”,机器视觉成为工厂自动化向智能化发展的关键性技术。随着工业产业升级,产品质量要求日益提高,工件表面检测成为必不可少的一环,利用视觉进行工件表面缺陷检测逐渐成为制造业的重要研究课题。目前大部分精加工厂仍采用人工检测的方法对工件表面缺陷进行检测,工人在对高反射曲面的表面缺陷进行检测时需要在强光下从不同的角度进行观察,不仅效率低,而且长期强光下作业对视力伤害也很大。视觉检测与人眼检测相比具有非接触式测量、严格的一致性、更小的空间分辨率、更高的时间分辨率以及更高的工作效率等特点[1]。高反射曲面常见于打磨抛光工件、汽车车身、光学元件等场合,因此,研究一种利用机器视觉对高反射曲面工件表面缺陷进行检测的方法具有很高的经济价值。
陈松赟等[2]设计了一种利用穹顶漫射光源进行高亮异形曲面缺陷检测的装置,该装置利用穹顶光源的漫反射光进行缺陷检测,但该方法只适用于缺陷较大的场合。刘元坤等[3]利用薄膜晶体管向被测物投射结构光,通过对比标准面与待测面中条纹的相位偏移实现了对镜面物体的检测,该方法中标准面的选取对检测结果的影响比较大,只适用于静态平面待测物的检测。赵文川等[4]提出一种基于相位偏折技术的光学表面疵病检测方法,利用水平和垂直两个方向上的正弦条纹,采用移相技术提取相位分布图,此方法需要采集多个相位的图像,操作复杂,且在非理想镜面下相位解析达不到理论精度。目前行业内对工件表面缺陷进行检测的方法各异,但是对于高反射曲面的缺陷目前尚没有一种在检测分辨率、可拓展性与普适性方面表现优异的方法。
本文在以实现高反射曲面缺陷检测为实际需求的背景下,以抛光曲面工件为研究对象,利用高反射曲面的镜面反射特性,提出了一种基于反射云纹的高反射曲面工件表面缺陷检测方法,并设计了基于本方法的图像采集装置,分析高反射曲面光照模型,针对采集的云纹图像设计了缺陷提取算法。实验结果表明本方法采集一次图像即可完成缺陷检测,对不同的缺陷有较好的普适性,并且实现了检测分辨率可调。
2 检测的原理及装置
2.1 高反射曲面反射模型
高反射曲面缺陷检测的部分难点在于图像采集系统的光源光路设计,需要根据物体表面的反射特性设计合适的照明系统[5]。高反射曲面光照模型如
其中
2.2 检测原理及图像采集装置
缺陷检测系统的装置示意图如
在
在上述检测装置中,云纹面光源通过计算机控制薄膜晶体管(TFT)液晶屏显示产生的云纹图像,液晶显示屏发出的光为漫反射光,因此采集的图像不会产生眩光。云纹图像通过MATLAB生成,生成的云纹图像可表示为
式中:
实验检测对象为经抛光处理后的圆柱形不锈钢工件,其曲率影响了单次有效检测面积,
在圆柱形工件截面上,
3 实验图像采集结果及分析
3.1 图像采集结果
目前打磨抛光曲面工件表面缺陷的检测都是通过人工在强光下从不同角度观察完成检测标注的。在工厂利用所提方法采集了标准面以及含有几种主要缺陷的样本图像,不同类型的缺陷样片如
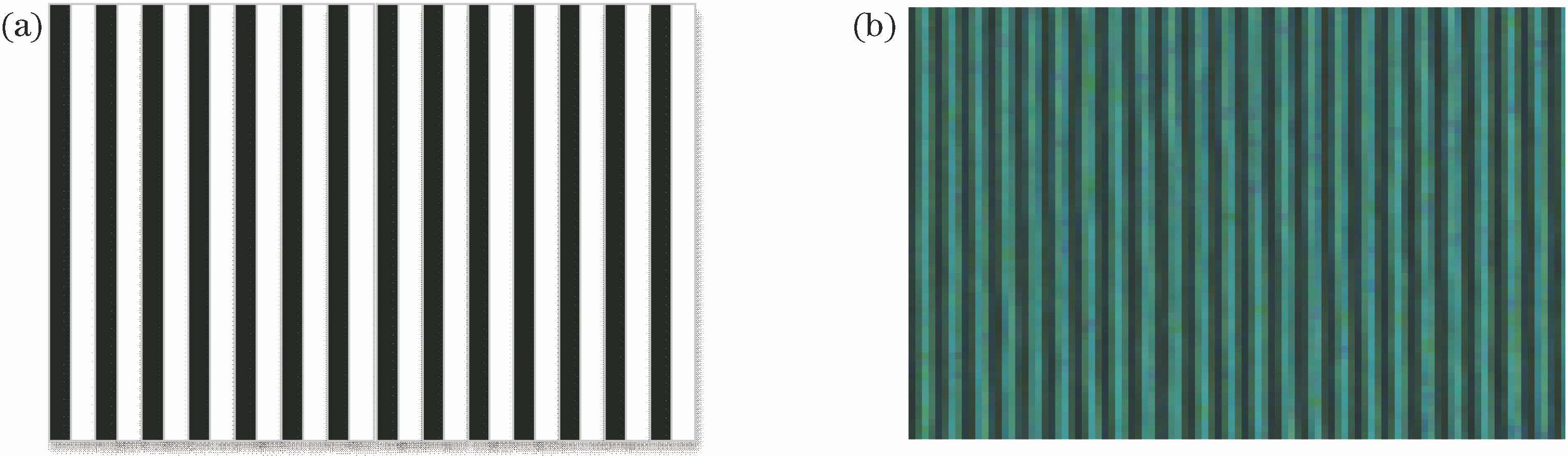
图 5. 标准云纹图像。(a) MATLAB生成的条纹图像;(b)相机采集的云纹图像
Fig. 5. Images of standard stripe. (a) Stripe image generated by MATLAB; (b) moiré image taken by camera
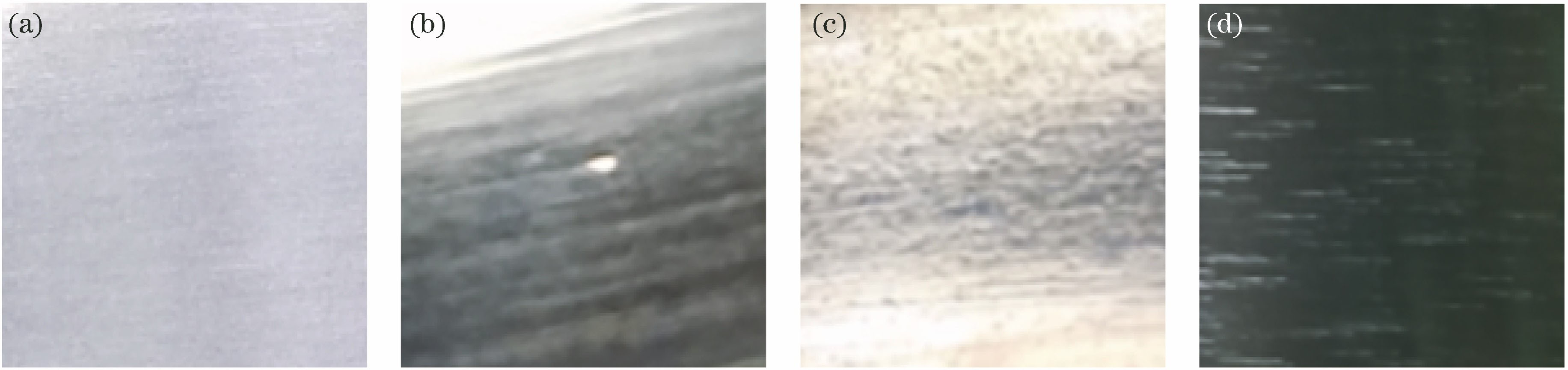
图 6. 不同类型的缺陷样片。(a)标准表面;(b)砂眼;(c)橘皮;(d)砂带痕
Fig. 6. Different types of defect samples. (a) Standard surface; (b) sand hole; (c) orange skin; (d) belt marks
上述样品的缺陷类型能覆盖94%的样本图像,不同的缺陷因为其反射特性差异,需要从不同的角度打光才能采集到清晰的样本图像。利用所提的检测方法,不同类型的缺陷都能较好地显现出来,采集的不同缺陷在云纹图像上的表征效果如
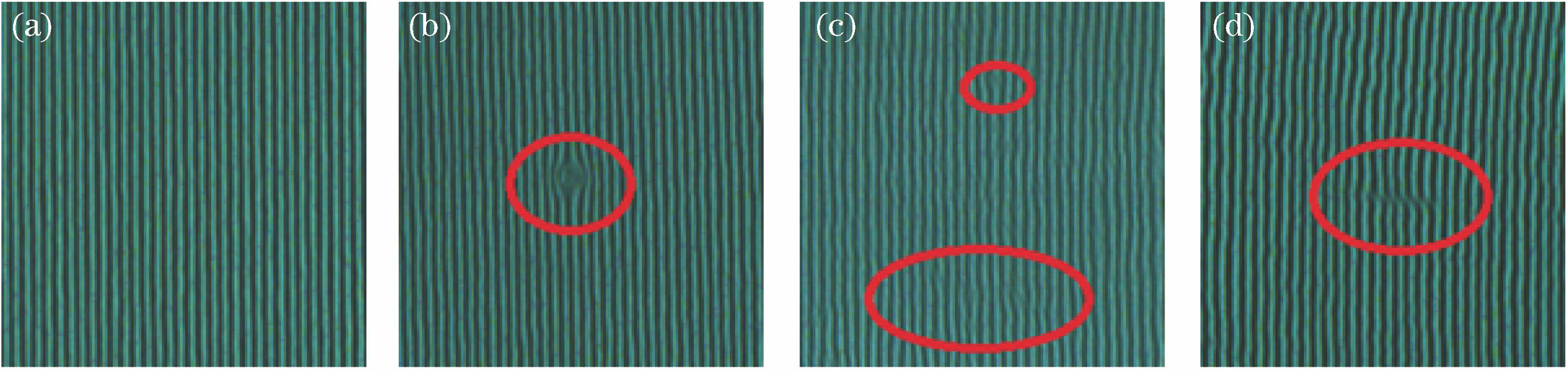
图 7. 不同缺陷在云纹图像上的表征效果。 (a)标准表面;(b)砂眼;(c)橘皮;(d)砂带痕
Fig. 7. Characterizations of different defects on moiré image. (a) Standard surface; (b) sand hole; (c) orange skin; (d) belt marks
3.2 缺陷特征分析
通过观察可以发现,受环境光、散射及相机噪声的影响,采集的条纹图像存在阶梯效应。
基于所提方法采集的图像,云纹图像纹理清晰,条纹互不干扰。缺陷存在时,云纹图像发生了弯曲或者偏折,从而能够对缺陷信息进行表征。在缺陷附近受光线散射的影响,缺陷位置的反射率
3.3 条纹间距对检测分辨率的影响
云纹图像中的明暗条纹可以作为一种参考对象。根据采样定理,条纹的间距会影响检测的分辨率。检测的分辨率
通过更改亮条纹的间距,可以在设备层面上设定系统检测的分辨率,从而适应不同场合的要求。
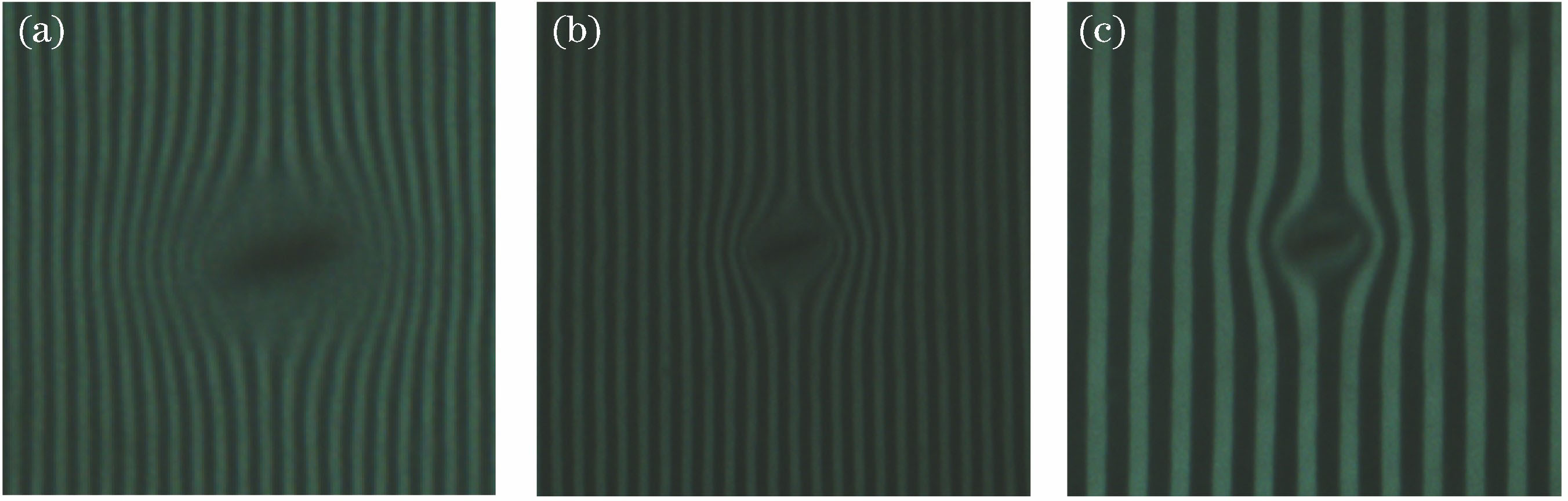
图 9. 不同条纹间距下采集的缺陷云纹图像。(a) 0.25 mm条纹间距;(b) 0.50 mm条纹间距;(c) 2.00 mm条纹间距
Fig. 9. Defect stripe images in different stripe distances. (a) Stripe spacing of 0.25 mm; (b) stripe spacing of 0.50 mm; (c) stripe spacing of 2.00 mm
3.4 云纹图像质量改善
对于标准的平面,理想条纹图像的条纹足够清晰,而实际采集的图像上,条纹的边缘灰度分布呈阶梯状,其原因是:1) 图像的采样不可能使得边缘刚好落在像素边界内,可以认为边缘的实际位置位于明暗条纹中间,在图像采样后呈现出阶梯锯齿状;2) 由于缺陷处光的散射使得缺陷处图像变得模糊;3) 环境光对条纹图像的影响。
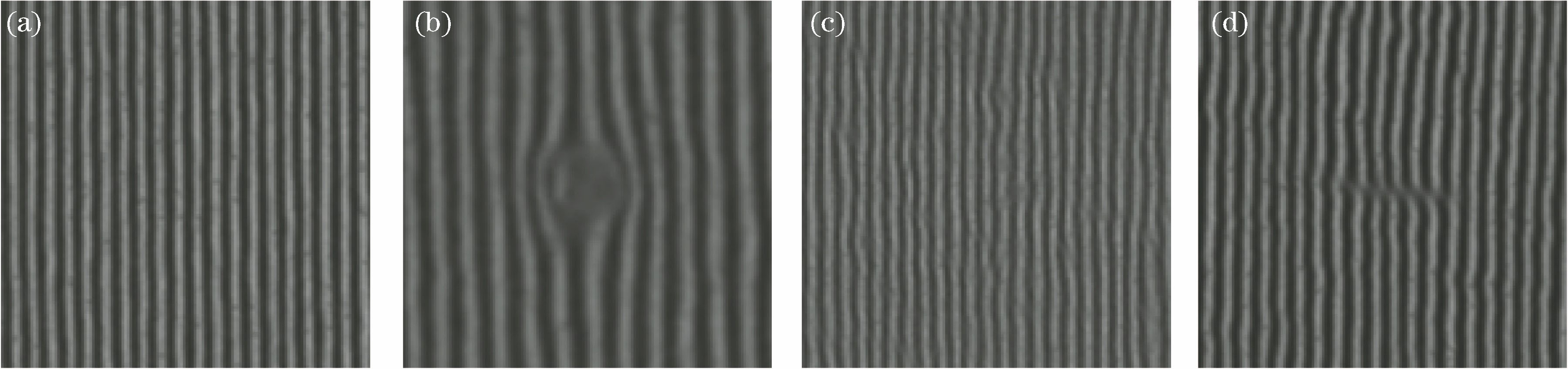
图 10. 不同缺陷的灰度图。 (a)标准表面;(b)砂眼;(c)橘皮;(d)砂带痕
Fig. 10. Gray distributions of different defects. (a) Standard surface; (b) sand hole; (c) orange skin; (d) belt marks
为了消除上述因素带来的阶梯边缘效应,引入了SHEN-Castan算法[9],利用平滑核进行卷积,然后搜索边缘像素,使用一种最小化(维度)优化。经过云纹质量改善后的灰度值分布如11所示。通过观察可以发现,改进后,图像边缘的灰度过渡变少了,使得条纹图像的对比度增加。
4 云纹图像缺陷检测算法
4.1 Gabor数学理论
采用基于图像实部的Gabor变换和最大熵分割对缺陷进行提取。二维Gabor滤波函数
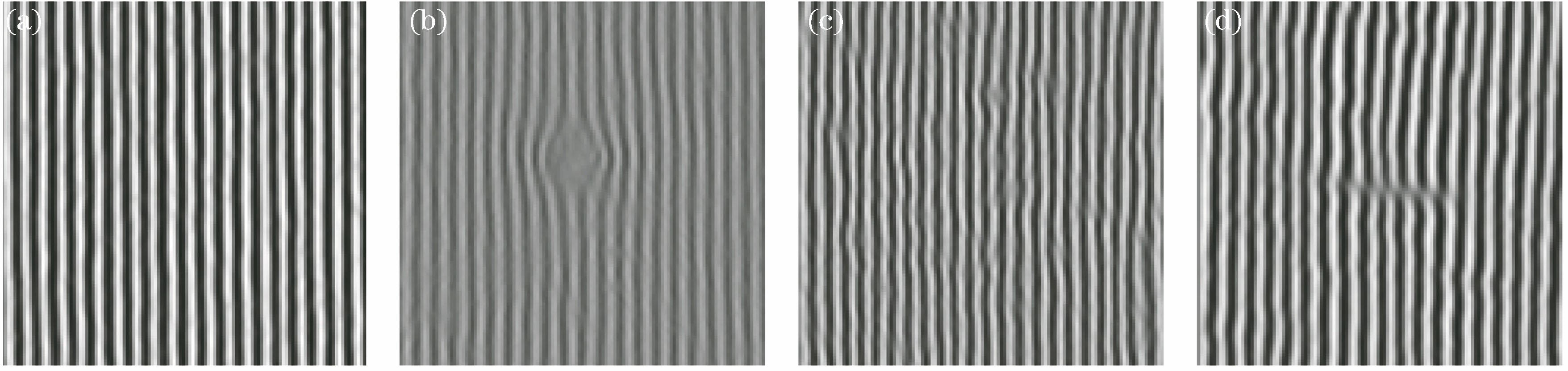
图 11. 云纹质量改善后的灰度值分布。 (a)标准表面;(b)砂眼;(c)橘皮;(d)砂带痕
Fig. 11. Gray distributions of improved fringe images. (a) Standard surface; (b) sand hole; (c) orange skin; (d) belt marks
式中:(
Gabor函数可以分解为实部
式中:
以
式中:
4.2 最大熵分割数学理论
最大熵分割是一种统计测量方法,反映随机数据源中信息的数量。将有缺陷的条纹图像作为一种随机信号处理,图像的不确定性越大,系统的信息熵就越大;系统的确定性越高,整个系统的信息熵就越小。对于窗口大小为
式中:
利用所提出的算法对图像进行分割时,可以自动选择最合适的阈值,避免光照等环境扰动对结果造成影响。
4.3 缺陷检测算法及结果
根据云纹图案的特征,缺陷检测算法流程图如
为了简化算法设计,提高系统的检测效率,对采集的图像进行旋转变换。由于缺少参照物,无法对图像的倾斜角度直接进行计算,因此提取纹图像中的条纹中心线作为参考标准。采用zhang骨架[12]提取条纹中心线,并进行hough直线拟合,通过计算间接得到直线的旋转角度
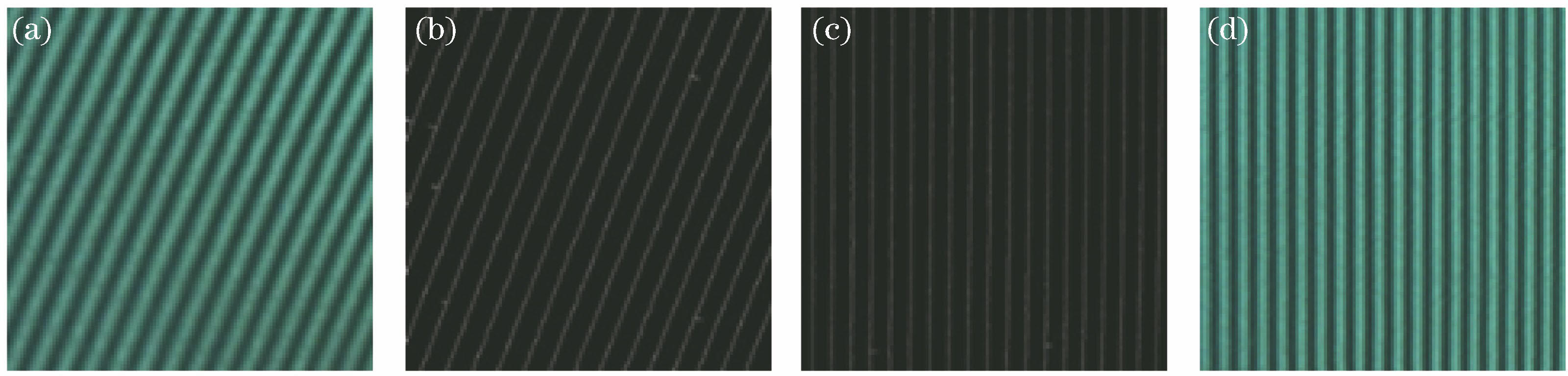
图 13. 图像预处理模块。(a)原始图片;(b)细化图片;(c)校正后的细化图像;(d)校正后的图像
Fig. 13. Image preprocessing module. (a) Original image; (b) image centerline; (c) corrected image centerline; (d) corrected image
对图像进行旋转变换并设定ROI后,条纹在不同的缺陷处表现出了不同形态的变化。对标准图像及缺陷图像在缺陷位置的灰度纹理进行分析,可以发现其梯度信息存在明显的变化。拷贝两份云纹图像,一份进行梯度变换,另一份进行频域高斯变换。
高斯函数的傅里叶变换仍然是高斯函数,但是其标准差已经发生改变,频域标准差越大,高斯函数越宽。在空域上,高斯函数表示为
式中:
对图像进行快速傅里叶变换(FFT)后,图像已经转换到频域,此时的高斯函数在频域上可表示为
式中:
式中:
在获取到缺陷信息增强的图像后,利用实验调试法,得到Gabor滤波器的最佳参数。抛光打磨过程中,磨轮的方向都是水平方向,因此在图像采集时,将云纹方向设置为竖直方向,如
在实际生产中,工厂内会存在一些灰尘。对处理后的缺陷信息进行对比后发现,灰尘的特征在处理后所占的像素面积非常小。利用面积特征对缺陷进行初步去伪。由于缺陷在表面造成了形变,因此缺陷周围的梯度比灰尘的梯度大。据此,在云纹图像上对缺陷的梯度信息进行计算,结合面积特征与梯度特征,进行伪缺陷剔除,并获取了缺陷的轮廓与坐标,在原图上进行标注并输出缺陷信息,控制执行机构进行相应的缺陷工件剔除。
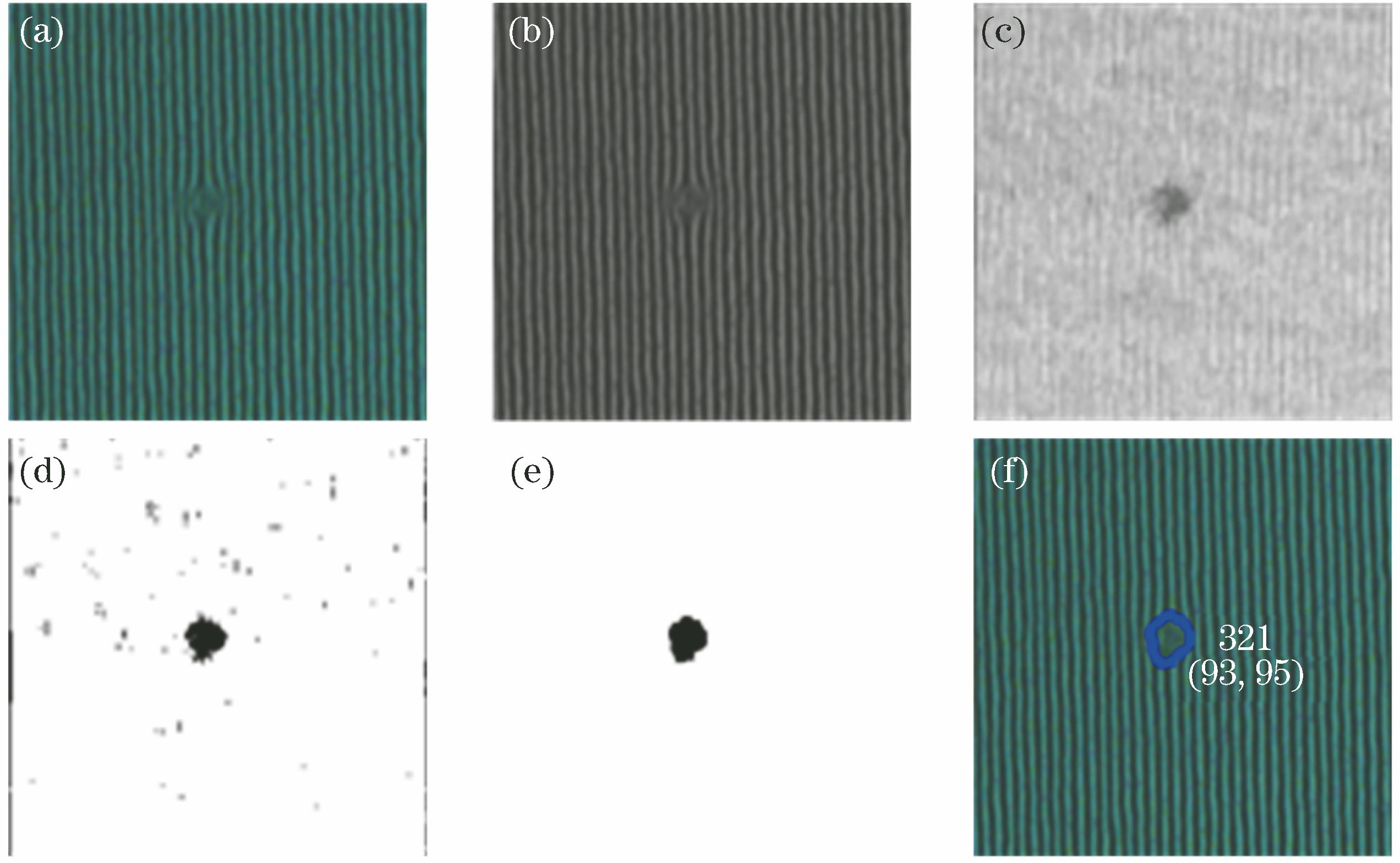
图 14. 算法对砂眼缺陷的处理结果。(a)原始图像;(b) ROI灰度图像;(c)缺陷增强后的图像;(d)缺陷特征提取后的图像;(e)形态学处理后的图像;(f)识别结果
Fig. 14. Processing results of sand hole defect by algorithm. (a) Original image; (b) ROI grayscale image;(c) image after defect enhancement;(d) image after defect feature extraction; (e) morphologically processed image; (f) identification result
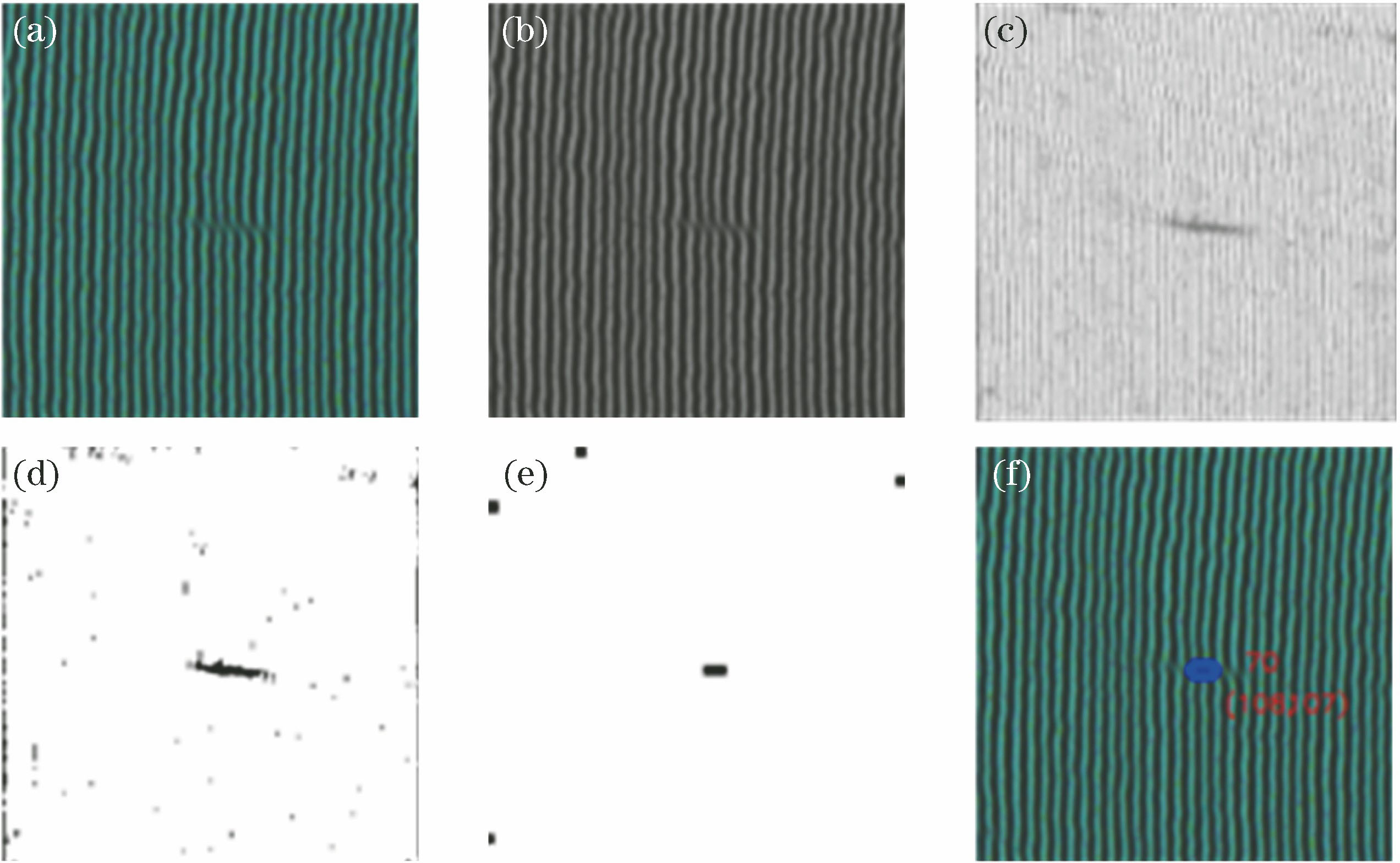
图 15. 算法对砂带痕缺陷的处理结果。 (a)原始图像;(b) ROI灰度图像;(c)缺陷增强后的图像;(d)缺陷特征提取后的图像;(e)形态学处理后的图像;(f)识别结果
Fig. 15. Processing results of belt mark defect by algorithm. (a) Original image; (b) ROI grayscale image;(c) image after defect enhancement;(d) image after defect feature extraction; (e) morphologically processed image; (f) identification result
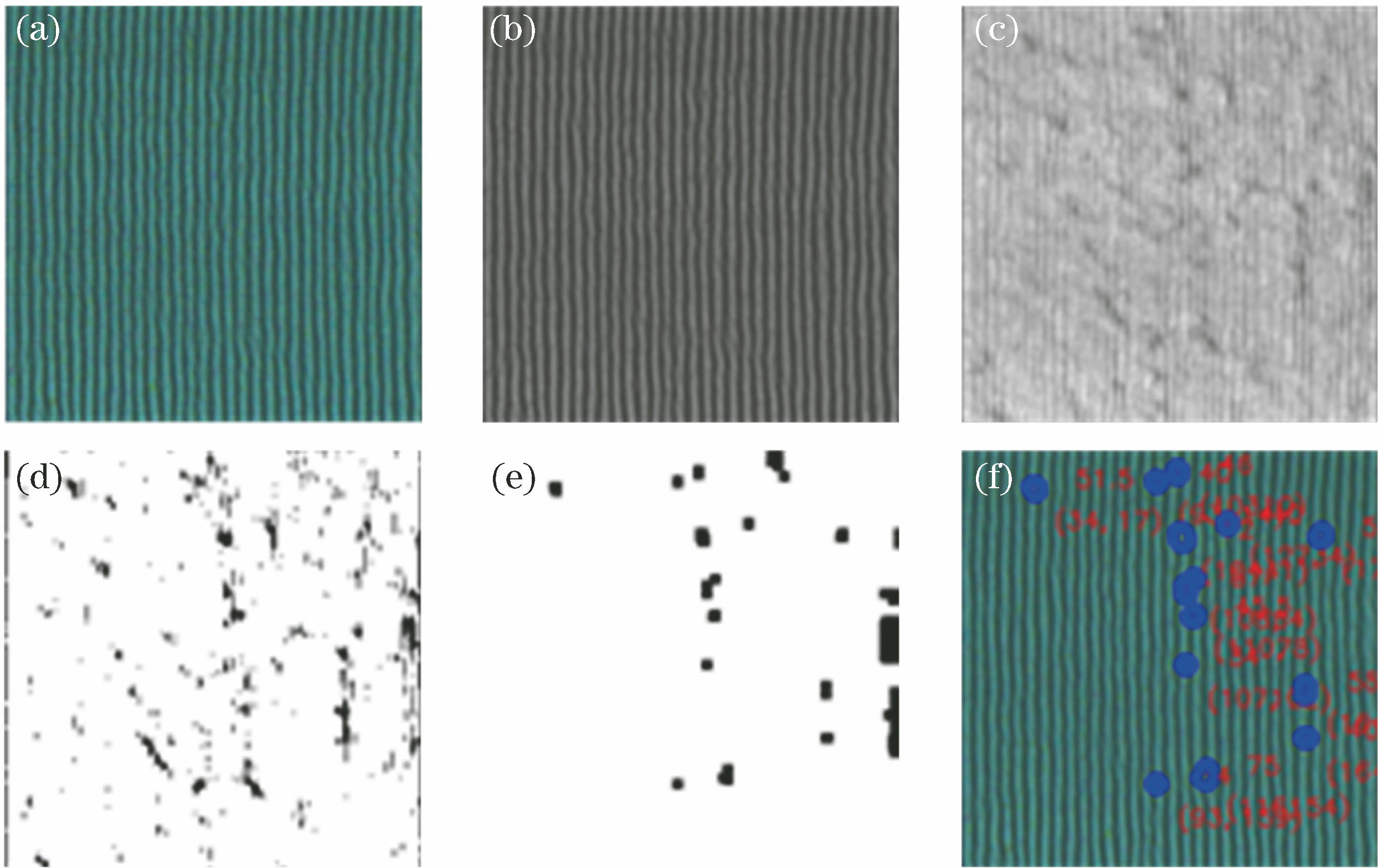
图 16. 算法对橘皮缺陷的处理结果。 (a)原始图像;(b) ROI灰度图像;(c)缺陷增强后的图像; (d)缺陷特征提取后的图像;(e)形态学处理后的图像;(f)识别结果
Fig. 16. Processing results of orange skin defect by algorithm. (a) Original image; (b) ROI grayscale image;(c) image after defect enhancement;(d) image after defect feature extraction; (e) morphologically processed image; (f) identification results
通过采集样本进行重复实验并统计结果,得到了本文方法对几种典型缺陷的检测效果,如
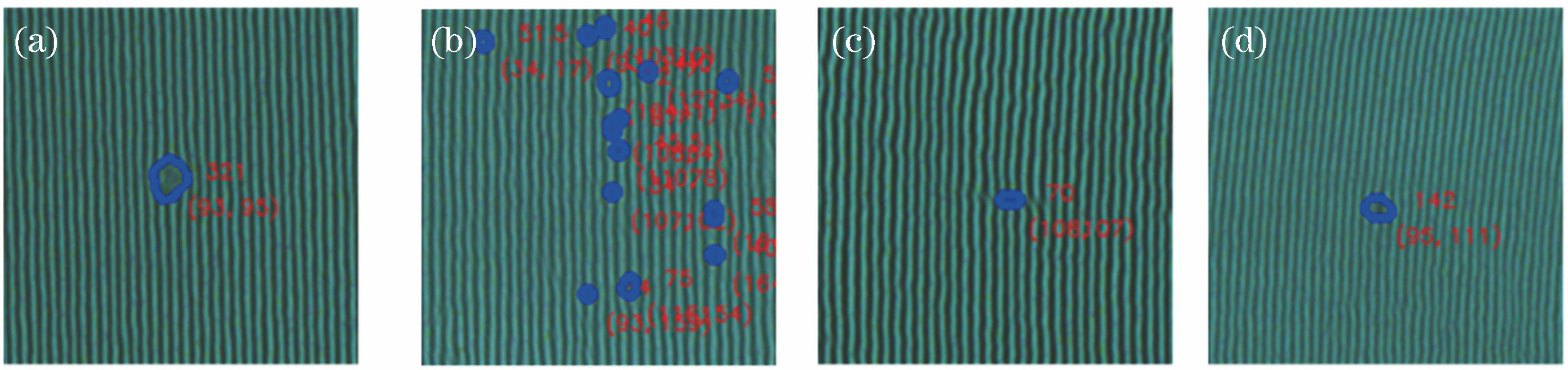
图 17. 缺陷检测与标注结果。(a)砂眼;(b)橘皮;(c)砂带痕;(d)凹坑
Fig. 17. Defect detection and labeling results. (a) Sand hole; (b) orange skin; (c) belt mark; (d) pit
利用所提高反射曲面工件检测装置,采集大量样品进行实验,对实验结果进行统计,得到了不同缺陷检测识别统计结果,如
表 1. 不同缺陷的检测识别统计结果
Table 1. Different defect detection results and identifying statistical results
|
5 结论
利用云纹面光源经高反射曲面反射差异设计了一种针对打磨抛光等具有高反射特性工件的表面缺陷检测方法,实验结果表明,该方法能克服高反射曲面图像采集的难点,对砂眼、砂带痕、橘皮等具有形变特征的缺陷有较好的检测效果。通过设置条纹间距可以实现分辨率可调,增加了系统的可拓展性。与相位偏折技术[4]相比,所提方法只需要采集一次样本图像,即可完成缺陷检测,减小了计算量,提高了设备的检测效率。本方法适用于具有高反射特性工件表面中具有形变特征的缺陷检测,而脏污等非形变特征不属于缺陷,因此不在讨论范围。
本文采用传统的图像算法来实现缺陷检测,下一步将尝试使用深度学习来解决工业缺陷检测问题,通过样本训练,避免人工特征提取,使检测结果更加精准,避免环境光干扰带来的误差。通过实验统计,所提方法对不同的形变缺陷均有较好的适应性与拓展性,有效地解决了工业高反射曲面工件缺陷检测的难点,具有较高的理论价值与经济价值。
[1] 伯特霍尔德·霍恩. 机器视觉[M]. 王亮, 蒋欣兰, 译. 北京: 中国青年出版社, 2014: 1- 14.
Berthold K PH. Robot vision[M]. Wang L, Jiang X Y, Transl. Beijing: China Youth Publishing Group, 2014: 1- 14.
[2] 陈松赟. 高亮异型曲面表面缺陷检测系统研究[D]. 哈尔滨: 哈尔滨工业大学, 2017: 1- 8.
Chen SY. A research of defect visual inspection system for specular and irregular surfaces[D]. Harbin: Harbin Institute of Technology, 2017: 1- 8.
[3] 刘元坤, 苏显渝, 吴庆阳. 基于条纹反射的类镜面三维面形测量方法[J]. 光学学报, 2006, 26(11): 1636-1640.
[4] 赵文川, 钟显云, 刘彬. 基于条纹反射的光学表面疵病检测法[J]. 光子学报, 2014, 43(9): 0912007.
[5] 郝勇, 赵翔, 温钦华, 等. 基于机器视觉的深沟球轴承滚珠遗漏检测[J]. 激光与光电子学进展, 2018, 55(2): 021502.
[6] Nayar S K, Ikeuchi K, Kanade T. Determining shape and reflectance of hybrid surfaces by photometric sampling[J]. IEEE Transactions on Robotics and Automation, 1990, 6(4): 418-431.
[7] 刘东, 严天亮, 王道档, 等. 条纹投影与相位偏折测量技术研究进展[J]. 红外与激光工程, 2017, 46(9): 0917001.
[8] 刘钦晓, 王方, 王渊承. 长景深阵列光学组件缺陷检测系统设计[J]. 光学学报, 2017, 37(3): 0322002.
[9] Shen J, Castan S. An optimal linear operator for step edge detection[J]. CVGIP: Graphical Models and Image Processing, 1992, 54(2): 112-133.
[10] 王清晨, 景军锋, 张蕾, 等. 基于最优Gabor滤波器的牛仔布缺陷检测[J]. 激光与光电子学进展, 2018, 55(7): 071501.
[11] 张刚, 马宗民. 一种采用Gabor小波的纹理特征提取方法[J]. 中国图象图形学报, 2010, 15(2): 247-254.
Zhang G, Ma Z M. An approach of using Gabor wavelets for texture feature extraction[J]. Journal of Image and Graphics, 2010, 15(2): 247-254.
[12] Zhang T Y, Suen C Y. A fast parallel algorithm for thinning digital patterns[J]. Communications of the ACM, 1984, 27(3): 236-239.
Article Outline
熊显名, 石红强, 曾星宇. 基于反射云纹的抛光曲面表面缺陷检测研究[J]. 激光与光电子学进展, 2019, 56(14): 141501. Xianming Xiong, Hongqiang Shi, Xingyu Zeng. Surface Defect Detectionon Polished Surface Based on Reflection Moiré[J]. Laser & Optoelectronics Progress, 2019, 56(14): 141501.