纳秒脉冲激光铣削Al2O3陶瓷工艺参数的优化
下载: 876次
1 引言
陶瓷材料因具有高比强度、高耐热性和电绝缘性能而被广泛应用于电子电气、化工机械和****等行业[1-3]。陶瓷具有硬度高、脆性大的特点,采用传统机械加工方法时,刀具磨损很大,且材料的去除率较低,从而使得陶瓷材料的加工具有极大的挑战性。
近年来,利用高能束实现陶瓷材料加工的先进制造技术得到了发展,例如,电子束打孔、等离子弧切割、激光铣削等[4-5]。其中,激光铣削具有高能量密度、高效率以及精确可控等优点,已成为加工陶瓷材料的重要技术。Samant等[6]建立了激光铣削深度与陶瓷材料热物理性质的关系;Karnakis等[7]采用飞秒激光器对硅片进行微铣削后发现,铣削深度和激光能量密度之间呈对数关系;徐强等[8]研究了强激光下陶瓷材料的铣削机理,主要包括材料的烧蚀氧化以及瞬时热应力破坏。确定合适的激光工艺参数是获得理想的陶瓷加工质量的关键。
李健等[9]揭示了短脉激光工艺参数对钇稳定四方多晶氧化锆陶瓷(Y-TZP)铣削量和表面质量的影响规律;许兆美等[10]采用模拟与实验方法研究了氧化铝(Al2O3)陶瓷激光铣削深度随工艺参数的变化规律;Wang等[11]研究了激光辅助水射流微铣削氮化硅(Si3N4)陶瓷技术,并利用响应面法获取了最优的工艺参数窗口;Pham等[12]对Al2O3与Si3N4陶瓷的激光铣削过程进行研究后获得了工艺参数对铣削深度及表面质量的影响规律;Umer等[13]利用多目标遗传算法得到了Al2O3陶瓷理想的铣削质量;Kibria等[14]研究了圆柱形Al2O3陶瓷的激光微车削工艺,重点探讨了连续点重叠率和周向重叠率对表面粗糙度的影响;Campanelli等[15]采用纳秒Nd∶YAG激光器对5754铝合金进行烧蚀,分析了激光参数对烧蚀深度、表面粗糙度的影响,并进行了多目标优化。
上述研究大多数侧重于单一工艺参数对单一输出变量的影响规律,但是影响铣削质量的因素众多,导致工艺参数优化具有较大的难度。本文采用纳秒脉冲激光对Al2O3陶瓷进行铣削实验,利用灵敏度分析方法确定了对铣削质量影响较大的工艺参数,并采用多目标遗传算法获得了最优的工艺参数解集。
2 实验设备及实验方法
2.1 实验材料及设备
实验材料为Al2O3陶瓷片,其尺寸为30 mm×15 mm×4 mm,铣削表面的尺寸为5 mm×5 mm。激光铣削实验系统如
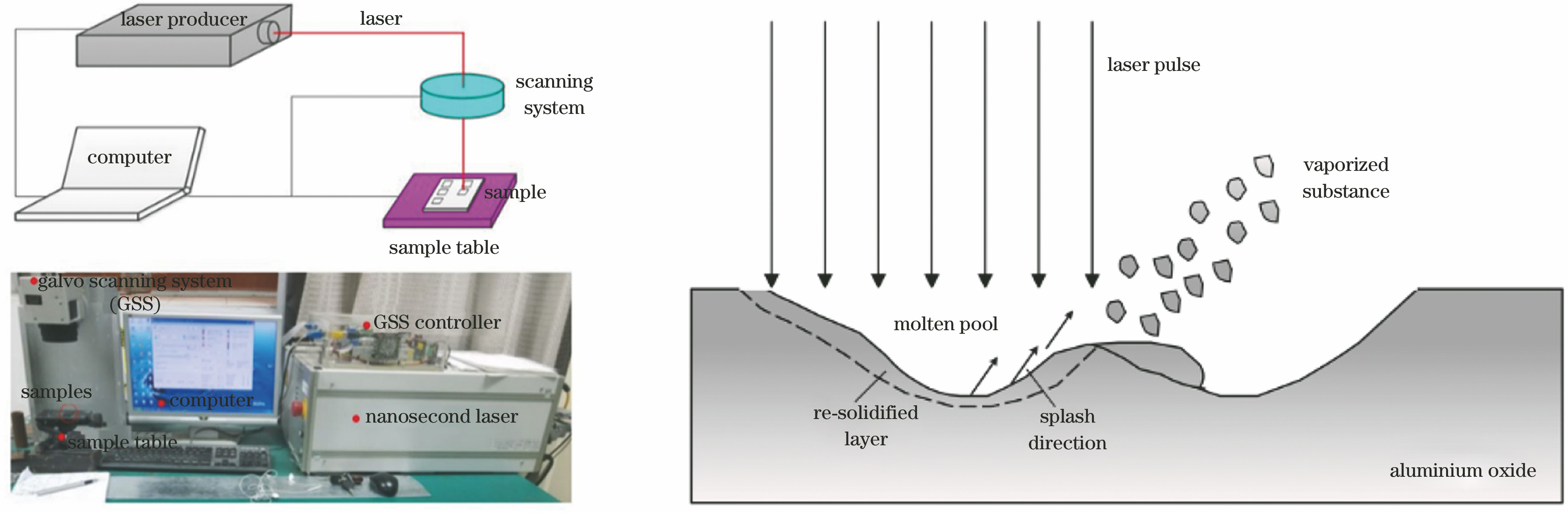
图 1. 激光铣削实验系统及激光铣削原理示意图。(a)实验系统;(b)铣削原理示意图
Fig. 1. Experimental system of laser milling and principle of laser milling. (a) Experimental system; (b) milling schematic
2.2 实验方法
铣削深度与表面质量都是通过激光功率、光斑搭接率等激光加工参数进行控制的。采用中心复合设计(CCD)方法进行实验规划。激光铣削的主要工艺参数包括搭接率、激光功率、铣削次数和重复频率,每个工艺参数取5个水平。在单因素实验的基础上,确定如
表 1. 工艺参数及其取值范围
Table 1. Process parameters and their value ranges
|
首先,使用VK-X160型激光共聚焦显微镜观察铣削表面的三维形貌、表面粗糙度(
表 2. 实验设计矩阵及结果
Table 2. Experimental design matrix and results
|
3 实验结果与讨论
3.1 激光铣削工艺数学模型的建立与分析
将搭接率、激光功率、铣削次数和重复频率视为输入变量,将表面粗糙度和铣削深度视为输出响应,使用响应面二次多项式拟合输入变量与输出响应的近似函数关系。响应面二阶回归模型[17-18]为
式中:
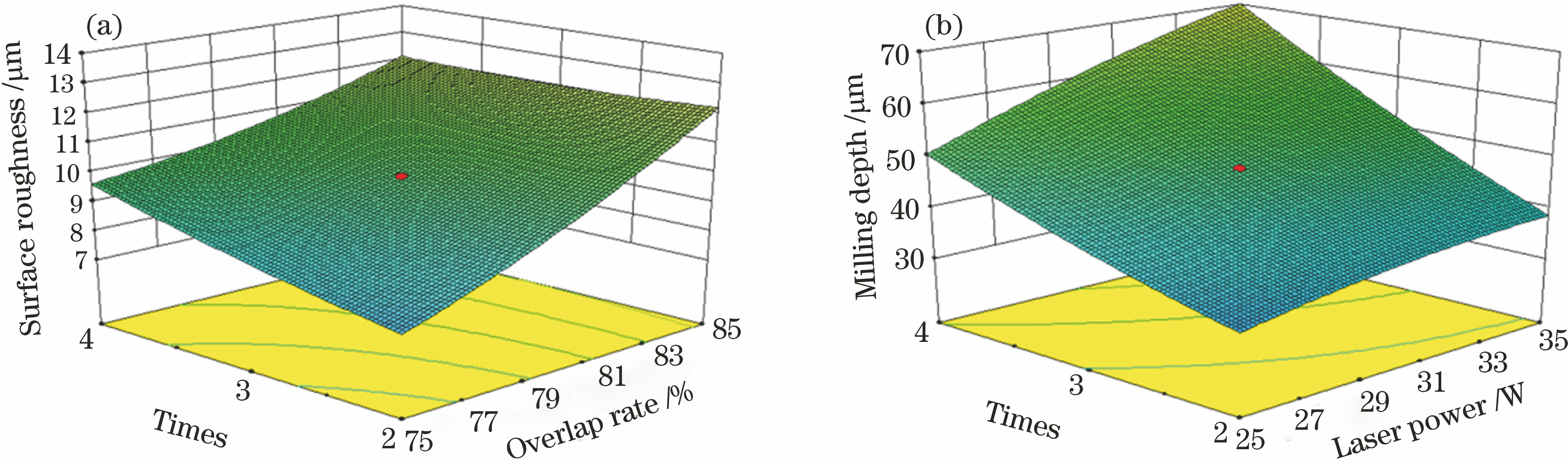
图 2. 工艺参数对铣削质量的交互式影响。(a)对表面粗糙度的影响;(b)对铣削深度的影响
Fig. 2. Interactive effects of process parameters on milling quality. (a) Effect on surface roughness; (b) effect on milling depth
表 3. 响应面模型的统计学评价
Table 3. Statistical evaluation of response surface model
|
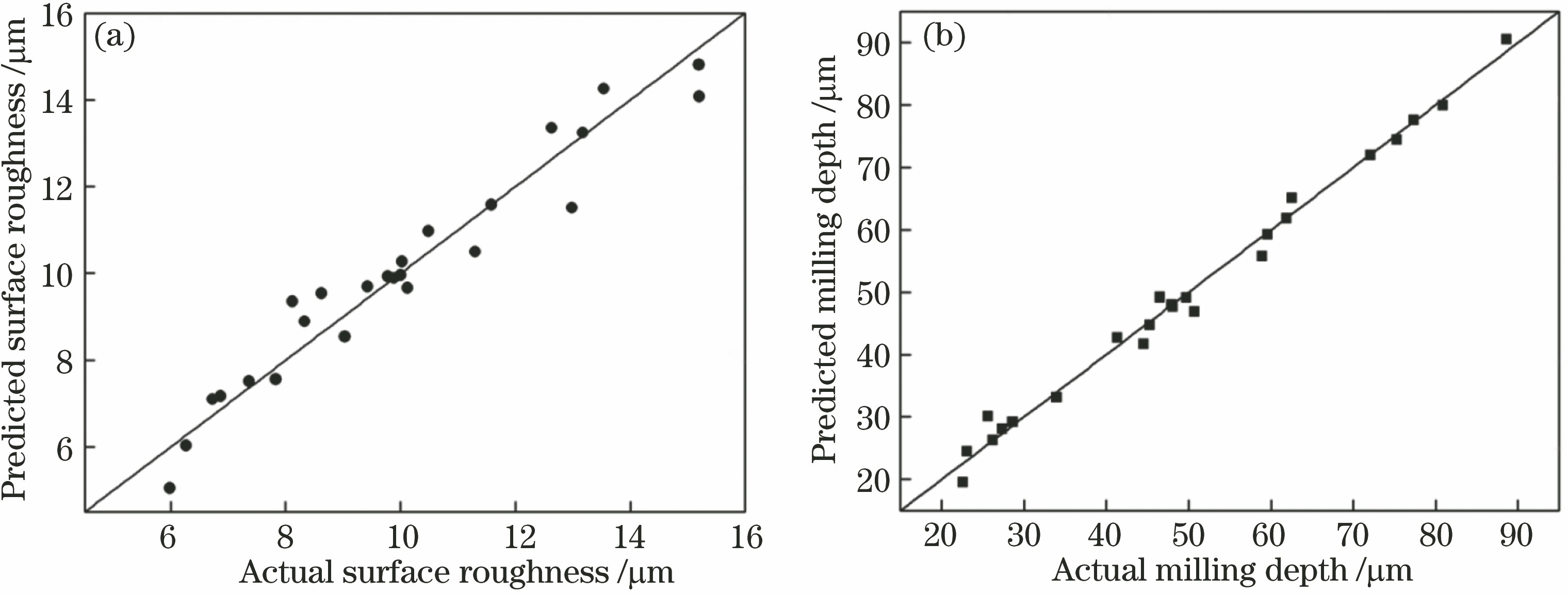
图 3. 预测值与实际值的对比。(a)表面粗糙度;(b)铣削深度
Fig. 3. Comparison of predicted and actual values. (a) Surface roughness; (b) milling depth
3.2 灵敏度分析
3.2.1 灵敏度方程的推导
目标函数对输入变量的灵敏度是该函数相对于其变量的偏导数[20-21]。为了获得搭接率对铣削质量的灵敏度方程,分别对(2)、(3)式以搭接率
同理,激光功率、铣削次数和重复频率对铣削质量的灵敏度方程如下:
3.2.2 灵敏度结果分析
灵敏度为正值说明输出响应随输入变量的增大而增大,灵敏度为负值说明输出响应随输入变量的增大而减小。同时,灵敏度绝对值越大,贡献率越高[22]。

图 4. 搭接率对铣削质量的灵敏度分析结果(激光功率为30 W,铣削次数为3,重复频率为40 kHz)
Fig. 4. Analysis results of sensitivity of overlap rate to milling quality (laser power is 30 W, milling times is 3, and laser repetition rate is 40 kHz)
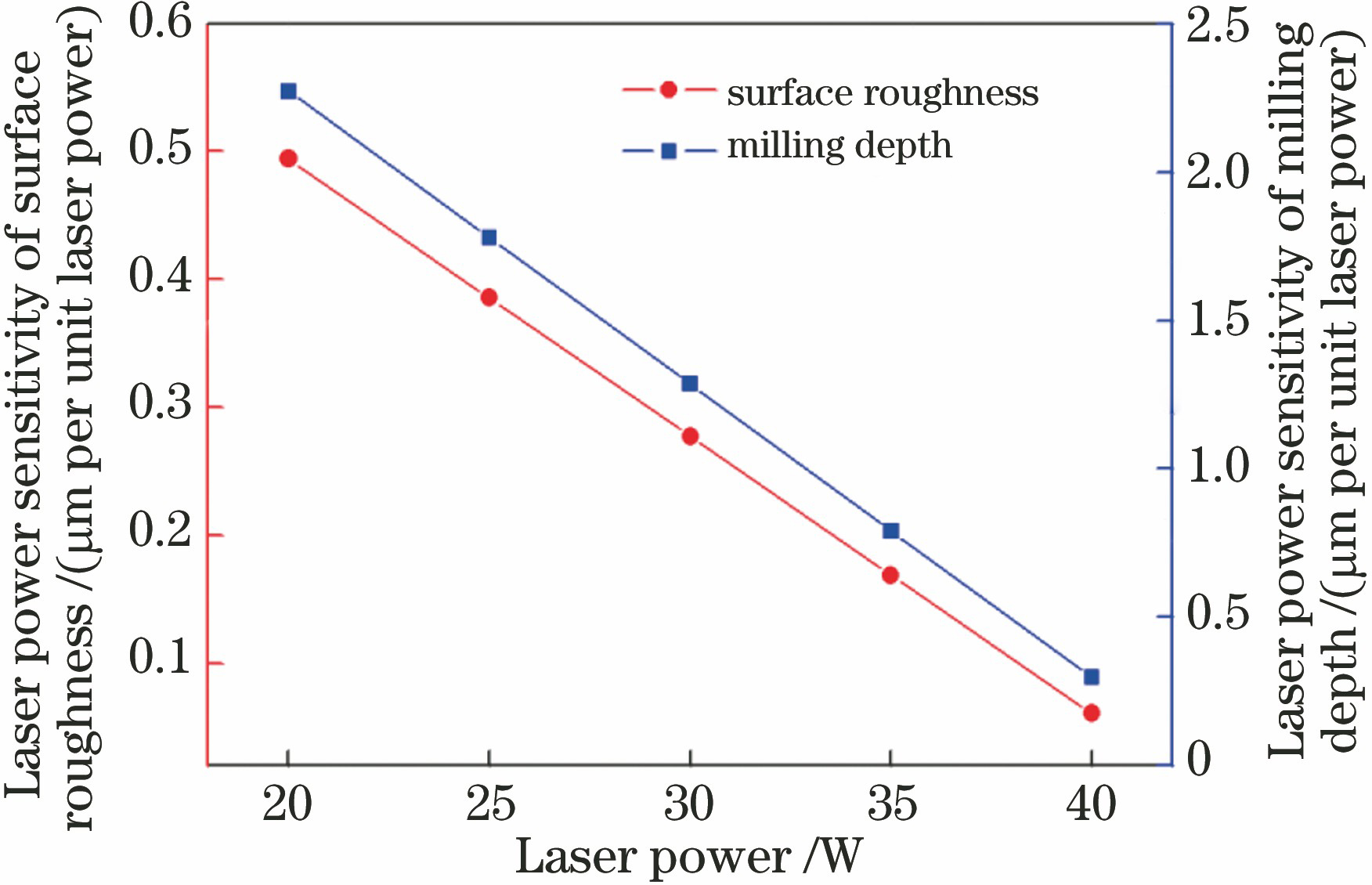
图 5. 激光功率对铣削质量的灵敏度分析结果(搭接率为80%,铣削次数为3,重复频率为40 kHz)
Fig. 5. Analysis results of sensitivity of laser power to milling quality (overlap rate is 80%, milling times is 3, and laser frequency is 40 kHz)
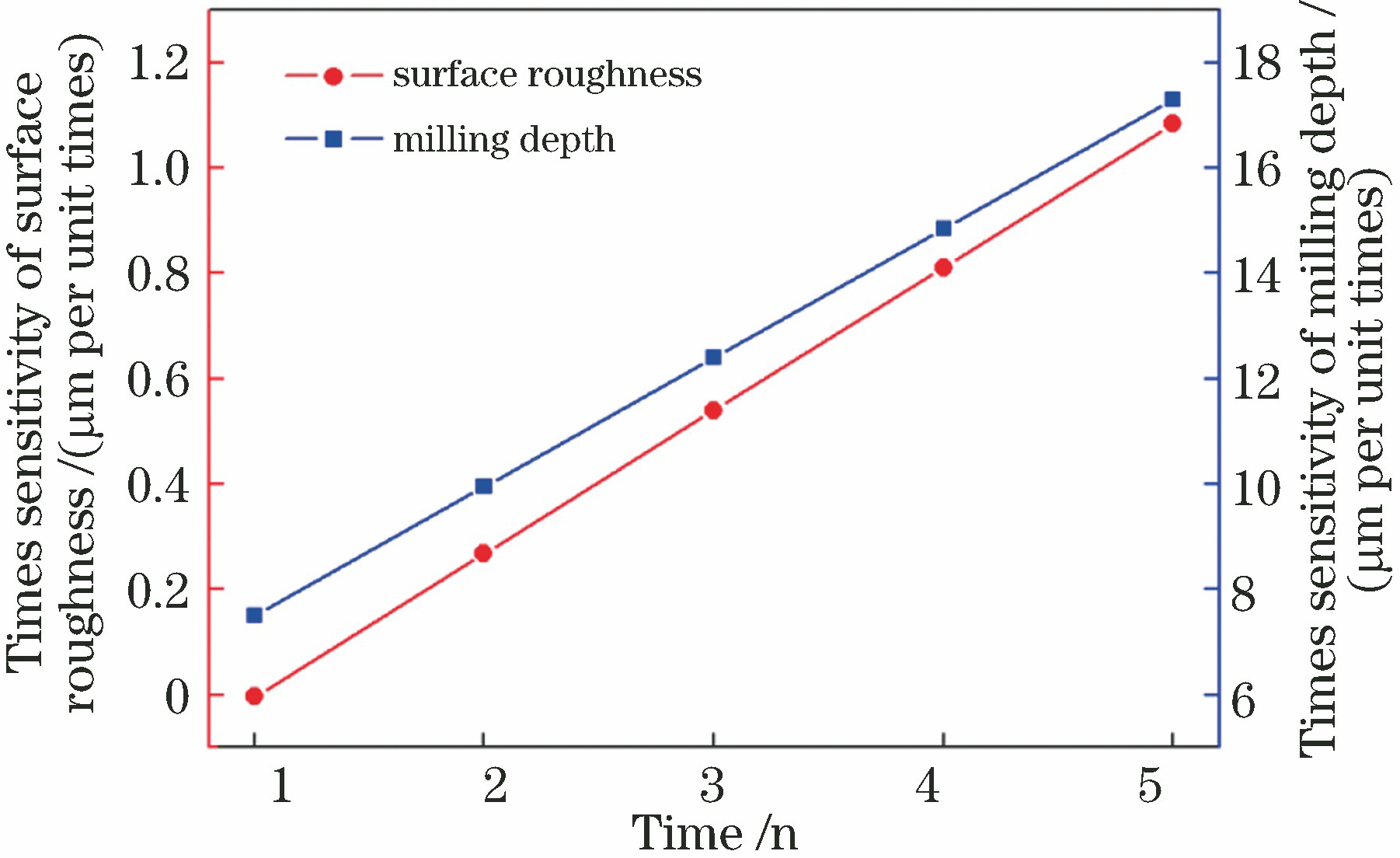
图 6. 铣削次数对铣削质量的灵敏度分析结果(搭接率为80%,激光功率为30 W,重复频率为40 kHz)
Fig. 6. Analysis results of sensitivity of laser milling times to milling quality (overlap rate is 80%, laser power is 30 W, and laser repetition rate is 40 kHz)
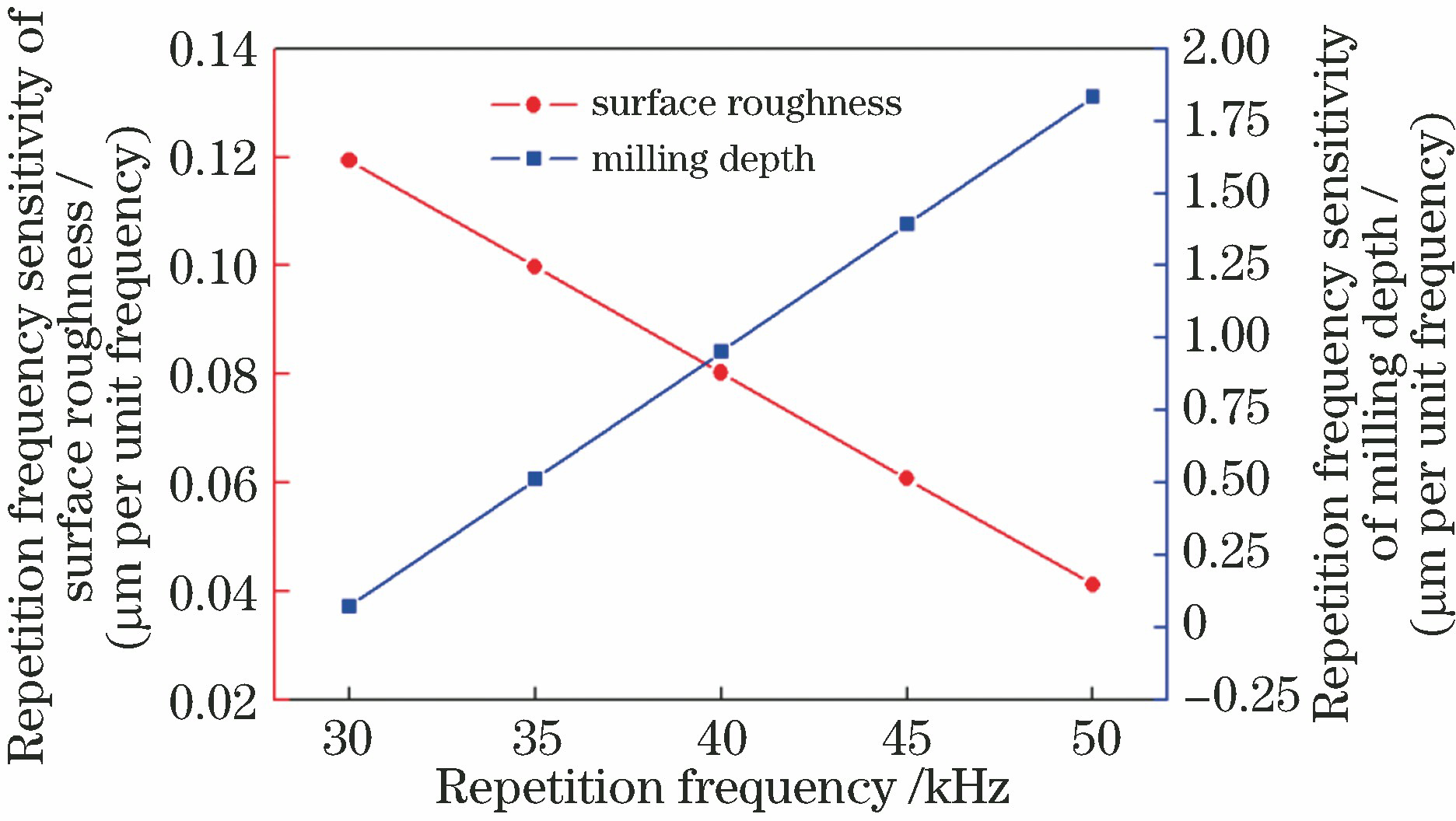
图 7. 重复频率对铣削质量的灵敏度分析结果(搭接率为80%,激光功率为30 W,铣削次数为3)
Fig. 7. Analysis results of sensitivity of laser frequency to milling quality (overlap rate is 80%, laser power is 30 W, and milling times is 3)
由
3.3 多目标参数优化及实验验证
本文以获得最大铣削深度和最小表面粗糙度为优化目标,利用多目标遗传算法进行工艺参数的优选[23]。该多目标优化问题可表示如下:
优化目标为最大化铣削深度和最小化表面粗糙度;取值范围为70 ≤
在优化过程中采用遗传算法搜寻目标函数的最小值,因此将多目标优化函数设定为-
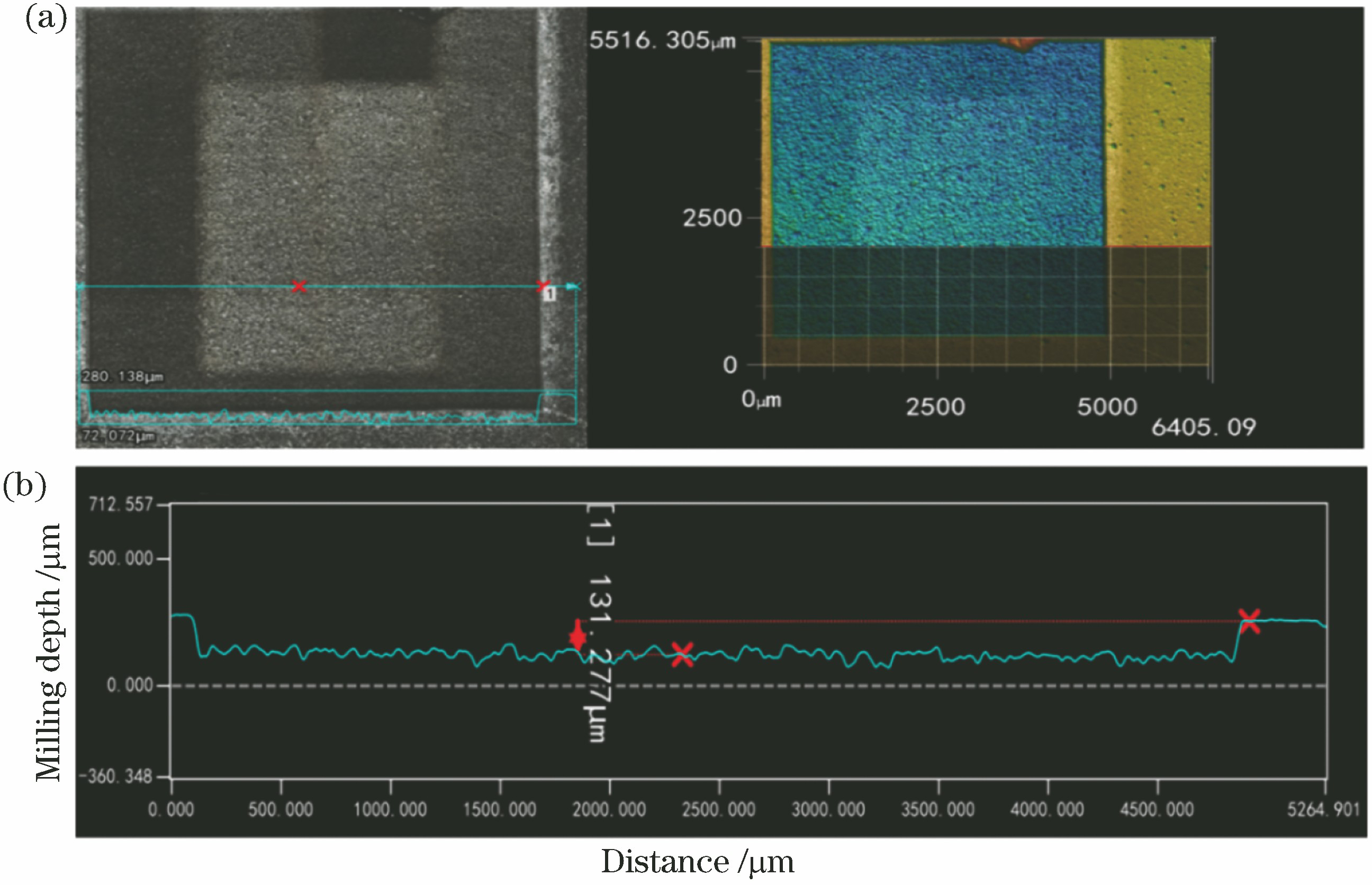
图 10. 激光铣削的三维形貌和截面轮廓。(a)三维形貌;(b)截面轮廓(搭接率为90%,激光功率为25.6 W,铣削次数为5,重复频率为50 kHz)
Fig. 10. Three-dimensional topography and sectional profile after laser milling. (a) Three-dimensional topography; (b) sectional profile (overlap rate is 90%, laser power is 25.6 W, milling times is 5, and laser repetition rate is 50 kHz)
激光铣削后的表面形貌如
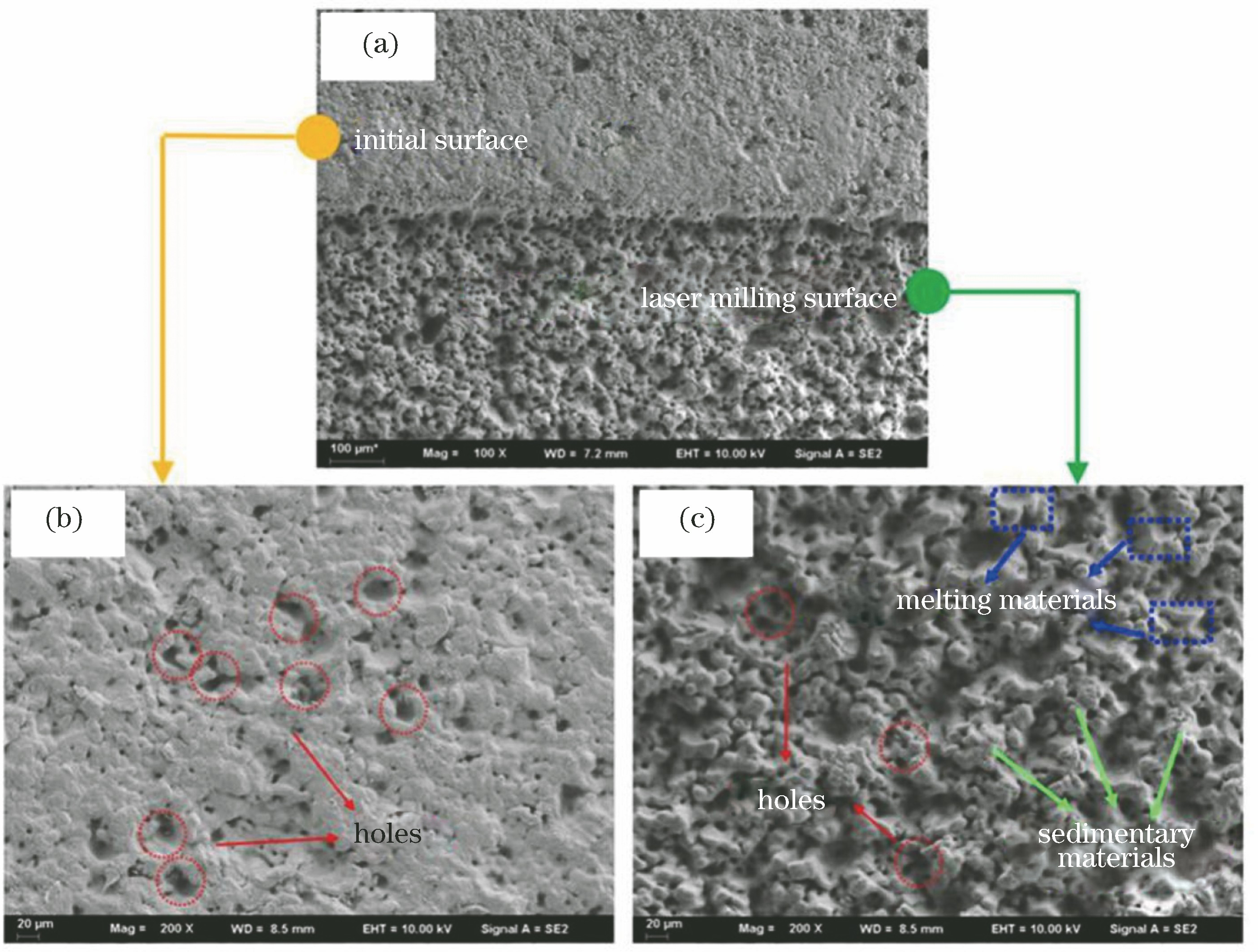
图 11. 激光铣削前后陶瓷表面的微观组织。(a)初始表面与铣削表面;(b)初始表面放大图;(c)铣削表面放大图(搭接率为90%,激光功率为25.6 W,铣削次数为5,重复频率为50 kHz)
Fig. 11. Microstructures of ceramic surface before and after laser milling. (a) Initial surface and milled surface; (b) partial enlargement of initial surface; (c) partial enlargement of milled surface (overlap rate is 90%, laser power is 25.6 W, milling times is 5, and laser repetition rate is 50 kHz).
4 结论
采用灵敏度分析方法研究了Al2O3陶瓷激光铣削过程中工艺参数的变化规律,确定了影响激光铣削表面粗糙度和铣削深度的关键参数,利用多目标遗传算法获得了理想铣削质量下的最优工艺参数解集。主要的主要结论如下:1)利用响应面二阶回归模型建立了激光铣削输入工艺参数与表面粗糙度、铣削深度之间的变化关系,该模型的拟合偏差小,预测激光铣削质量能力的稳定性较强。2)灵敏度分析结果表明,铣削次数和搭接率对表面粗糙度和铣削深度的影响最大,其次为激光功率和重复频率;另外,可以通过降低激光功率和光斑搭接率、增大重复频率等措施来降低铣削表面粗糙度,但铣削深度会明显降低。3)对优化参数进行了实验验证,结果表明激光铣削后的表面粗糙度和铣削深度的实验值及预测值的相对误差分别为3.36%和8.19%。
[1] Leone C, Genna S, Tagliaferri F, et al. Experimental investigation on laser milling of aluminium oxide using a 30 W Q-switched Yb∶YAG fiber laser[J]. Optics & Laser Technology, 2016, 76: 127-137.
[2] Kibria G, Doloi B, Bhattacharyya B. Experimental investigation and multi-objective optimization of Nd∶YAG laser micro-turning process of alumina ceramic using orthogonal array and grey relational analysis[J]. Optics & Laser Technology, 2013, 48: 16-27.
[3] 姚燕生, 陈庆波, 汪俊, 等. 氮化硅陶瓷水射流辅助激光精密加工[J]. 光学精密工程, 2018, 26(11): 2723-2731.
[4] Biswas R, Kuar A S, Mitra S. Process optimization in Nd∶YAG laser microdrilling of alumina-aluminium interpenetrating phase composite[J]. Journal of Materials Research and Technology, 2015, 4(3): 323-332.
[5] 卢芳, 田欣利, 吴志远. 等离子弧加热切削工程陶瓷试验[J]. 装甲兵工程学院学报, 2007, 21(1): 81-83.
Lu F, Tian X L, Wu Z Y. Experiment on plasma arc thermal cutting of the engineering ceramics[J]. Journal of Academy of Armored Force Engineering, 2007, 21(1): 81-83.
[6] Samant A N, Dahotre N B. Differences in physical phenomena governing laser machining of structural ceramics[J]. Ceramics International, 2009, 35(5): 2093-2097.
[7] Karnakis D, Rutterford G, Knowles M, et al. Laser micro-milling of ceramics, dielectrics and metals using nanosecond and picosecond lasers[J]. Proceedings of SPIE-The International Society for Optical Engineering, 2006, 6106: 6106131-6106134.
[8] 徐强, 邵正山, 朱时珍, 等. ZrB2-ZrC超高温陶瓷激光烧蚀行为研究[J]. 稀有金属材料与工程, 2015, 44(S1): 533-536.
Xu Q, Shao Z S, Zhu S Z, et al. Laser ablation behavior of ZrB2-ZrC ultra high temperature ceramics[J]. Rare Metal Materials and Engineering, 2015, 44(S1): 533-536.
[9] 李健, 季凌飞, 胡炎, 等. 532 nm激光铣削Y-TZP陶瓷实验研究[J]. 中国激光, 2015, 42(8): 0806002.
[10] 许兆美, 洪宗海, 蒋素琴, 等. Al2O3陶瓷激光铣削有限元模拟与实验研究[J]. 光学学报, 2014, 34(s2): s214009.
[11] Wang L, Huang C Z, Wang J, et al. An experimental investigation on laser assisted waterjet micro-milling of silicon nitride ceramics[J]. Ceramics International, 2018, 44(5): 5636-5645.
[12] Pham D T, Dimov S S, Petkov P V. Laser milling of ceramic components[J]. International Journal of Machine Tools and Manufacture, 2007, 47(3/4): 618-626.
[13] Umer U, Mohammed M K, Al-Ahmari A. Multi-response optimization of machining parameters in micro milling of alumina ceramics using Nd∶YAG laser[J]. Measurement, 2017, 95: 181-192.
[14] Kibria G, Doloi B, Bhattacharyya B. Investigation into the effect of overlap factors and process parameters on surface roughness and machined depth during micro-turning process with Nd∶YAG laser[J]. Optics & Laser Technology, 2014, 60: 90-98.
[15] Campanelli S L, Casalino G, Contuzzi N. Multi-objective optimization of laser milling of 5754 aluminum alloy[J]. Optics & Laser Technology, 2013, 52: 48-56.
[16] 袁根福, 曾晓雁. Al2O3陶瓷激光铣削试验研究[J]. 中国激光, 2003, 30(5): 467-470.
[17] 周建忠, 佘杰, 黄舒, 等. 基于RSM的铝/钢异种金属激光熔钎焊工艺研究与参数优化[J]. 中国激光, 2015, 42(s1): s103004.
[18] Liu Y, Zhang J, Pang Z C, et al. Investigation into the influence of laser energy input on selective laser melted thin-walled parts by response surface method[J]. Optics and Lasers in Engineering, 2018, 103: 34-45.
[19] 褚振涛, 于治水, 张培磊, 等. 基于响应面分析的T型接头激光深熔焊焊缝形貌预测及工艺参数优化[J]. 中国激光, 2015, 42(2): 0203006.
[20] Senthilkumar B, Kannan T. Sensitivity analysis of flux cored arc welding process variables in super duplex stainless steel claddings[J]. Procedia Engineering, 2013, 64: 1030-1039.
[21] Cheng Q, Zhao H W, Zhang G J, et al. An analytical approach for crucial geometric errors identification of multi-axis machine tool based on global sensitivity analysis[J]. The International Journal of Advanced Manufacturing Technology, 2014, 75: 107-121.
[22] Tian X J, Liu Y H, Deng W, et al. Sensitivity analysis for process parameters influencing electric arc cutting[J]. The International Journal of Advanced Manufacturing Technology, 2015, 78: 481-492.
[23] 黄俊, 陈子博, 刘其蒙, 等. 基于NSGA-Ⅱ的离体皮肤组织激光融合工艺参数的多目标优化[J]. 中国激光, 2019, 46(2): 0207001.
Article Outline
许兆美, 孟宪凯, 屈彦荣, 朱为国, 郭召恒. 纳秒脉冲激光铣削Al2O3陶瓷工艺参数的优化[J]. 激光与光电子学进展, 2019, 56(23): 231404. Zhaomei Xu, Xiankai Meng, Yanrong Qu, Weiguo Zhu, Zhaoheng Guo. Process Parameter Optimization of Al2O3 Ceramics Milled with Nanosecond Pulsed Laser[J]. Laser & Optoelectronics Progress, 2019, 56(23): 231404.