熔质流动特性对毛化凸点成形的影响
下载: 989次
1 引言
具有毛化微凸起的表面在摩擦学、流体动力学等方面具有广泛应用。目前,毛化表面制造方法主要有机械毛化、电火花毛化、激光毛化等。其中,激光毛化具有可控性好、效率高、易于实现主动设计、易于与现代智能机械设备融合等优势,近年来备受关注。激光毛化过程涉及相变、表面张力、马兰戈尼效应等物理现象,因此,毛化形貌的影响因素众多,现象丰富,可设计性强,但是形貌的控制也较复杂。鉴于此,国内外很多学者从实验、仿真和理论分析等角度研究了毛化形貌的形成机理及规律。
刘莹等[1]使用钇铝石榴石(YAG)脉冲激光器,采用合适的脉宽、功率和离焦量成功地在轧辊表面加工出了微凸体形貌。Du等[2]利用Nd∶YAG激光辅以侧吹氩气,研究了激光参数与GCr15轧辊表面凸点轮廓的关系,认为轧辊表面微凸起形貌主要受马兰戈尼对流的影响。叶云霞等[3]通过实验系统研究了激光脉宽和峰值功率密度对微凸起形貌的影响规律,认为火山口形貌是由反冲压力造成的。Zhou等[4]通过控制脉冲数和激光功率观察了凸起至凹坑的整个转变过程。在理论研究方面,采用各种数值模型模拟熔池中的传热和流体流动过程是主要的研究方法。早期的大部分模型通常将熔池表面简化为平面[5-7],导致仿真预测的熔池的几何尺寸与实际情况存在明显的偏差。因此,在激光毛化的数值模型中,应将表面设置为自由表面,以反映表面的变形情况。此后,研究人员在考虑自由表面变形的基础上,对熔池表面形貌的产生机理进行了大量的模拟研究。熔质流动是表面变形的关键,主要包含两大因素:流动方向和流动速度。Willis等[8]对脉冲激光与薄膜的作用过程进行了数值模拟,认为熔池表面形貌主要由表面张力驱动。Bennett等[9]提出了磁盘毛化形貌的成形机理,认为化学毛细管力可以逆转光斑中心区域的剪切力,从而改变熔质的流向。Chang等[10]建立了激光加工过程中熔质表面的张力模型,得出了表面张力及其温度系数随温度的变化。许伯强等[11]对激光与金属铝相互作用的温度场和流场进行了数值模拟,结果表明,表面张力温度系数的大小和正负对熔池内流体的运动起决定性作用,会对熔池形状产生很大影响。
关于熔质流向已有大量的研究,然而关于熔质流速的研究还较少。Willis等[8]对脉冲激光作用于薄膜的整个过程进行原位摄影后发现,激光脉冲辐照后,流体的流动较快,熔融区外缘流动不稳定。刘红斌等[12]建立了二维热流耦合模型,通过模拟后认为流体的流速随温度降低而减小,熔池表面附近的流速最大。王维等[13]通过建立模型发现,材料表面热源中心的温度梯度最小,因此熔池中心的速度最小,熔池中心和固液界面之间存在速度的最大值,且该值随激光功率的增大而增大。但上述仿真均预设熔池表面为平面,具有一定的局限性。Liu等[14]基于自由表面对轧辊毛化进行了数值模拟,结果发现,初始阶段熔池内的对流强烈而混乱,随着时间推移,对流形成的环流数量减少,环流中心逐渐向自由表面和熔质界面移动,最大速度位于温度梯度和表面张力较大的熔池底部以及火山口边缘凸起位置。
综上所述,尽管很多学者对熔池大小和形貌已有研究,但多数研究均采用表面张力或者表面张力温度系数来判断熔池内流体的流向,据此定性研究熔池中流体的流向对毛化点形貌的影响规律。实际上,除了流体流向,流体流速也是影响毛化点形貌的决定性因素,虽然已有人针对流速进行研究,但很少有人研究表面流速与毛化点形貌间的关系;此外,很多研究者认为马兰戈尼效应在整个毛化成形过程都起主导作用,而Shen等[15]却认为熔池冷却阶段的形貌主要受法向应力的影响,这说明激光毛化过程中尚有诸多现象和物理机制未解释清楚。为了进一步探究表面流速等规律,本文对加热和冷却过程加以区分,建立了二维轴对称有限元分析模型,研究表面流速和流向的变化情况及其对形貌的影响规律,并仿真表面轮廓的形成过程。为了验证数值模型的正确性,还进行了相应的实验,测量得到了表面轮廓,并将其与仿真预测得到的表面轮廓进行比较。
2 理论模型
毛化是一个涉及相变传热和流体流动的多物理过程。激光辐照于靶材表面,表面温度升高,温度超过靶材的熔点后形成熔池,液相在切向应力和法向应力等表面力,以及重力、浮力等体积力的作用下流动变形。表面张力梯度的存在会使液体向高表面张力区域流动,这种现象称为马兰戈尼效应。界面局部曲率引起的单位面积上的内力称为法向应力。
为了简化材料熔化和流体流动过程中自由表面的演化过程,根据以下假设建立数学模型:1)假设45钢的热物性参数与温度呈分段线性关系;2)熔池中的熔质为不可压缩的牛顿流体,熔池内的流动为层流;3)忽略产生的等离子体及其对激光的屏蔽作用;4)将固体视为黏度很大的流体。
2.1 传热方程和传热边界条件
2.1.1 传热方程
瞬态温度场由能量守恒方程控制[16],即
其中
式中:
固、液以及混合糊状区的黏度
式中:
式中:
2.1.2 传热边界条件
假设靶材各表面均存在自然对流换热、边界辐射[20],即
仅上表面存在激光辐射[20],即
式中:
式中:
2.2 对流方程和层流边界条件
2.2.1 对流方程
传热方程中的
其中
式中:
不可压缩流动的质量守恒方程(连续性方程)[22]为
2.2.2 层流边界条件
上表面为可以自由变形的开边界,毛细力(表面张力)作用于法向,而热毛细流动(马兰戈尼效应)作用于切向[19]。
法向应力为
切向应力为
式中:
式中:
式中:系数
(1)~(16)式中具体参数的数值如
表 1. 45钢的材料属性[3,24]
Table 1. Material properties of 45 steel[3,24]
|
表 2. 不同热力学温度T下45钢的比热容Cp和热导率k[25]
Table 2. Specific heat capacity Cp and thermal conductivity k of steel 45 at different temperatures[25]
|
3 计算模型
利用多物理场仿真软件COMSOL,建立传热和流体流动相耦合的瞬态二维轴对称模型,横轴为
切向力和法向力均以弱形式的方式进行添加,采用移动网格(ALE)在自由移动的变形网格上求解流体域和实体域的所有方程,用Laplace网格平滑算法模拟靶材表面的变形。
表 3. 边界条件
Table 3. Boundary conditions
|
表 4. 激光参数
Table 4. Laser parameters
|
4 结果与讨论
4.1 表面温度分布
激光辐照靶材0.80 ms后冷却0.40 ms,期间不同时刻靶材表面的热力学温度分布如
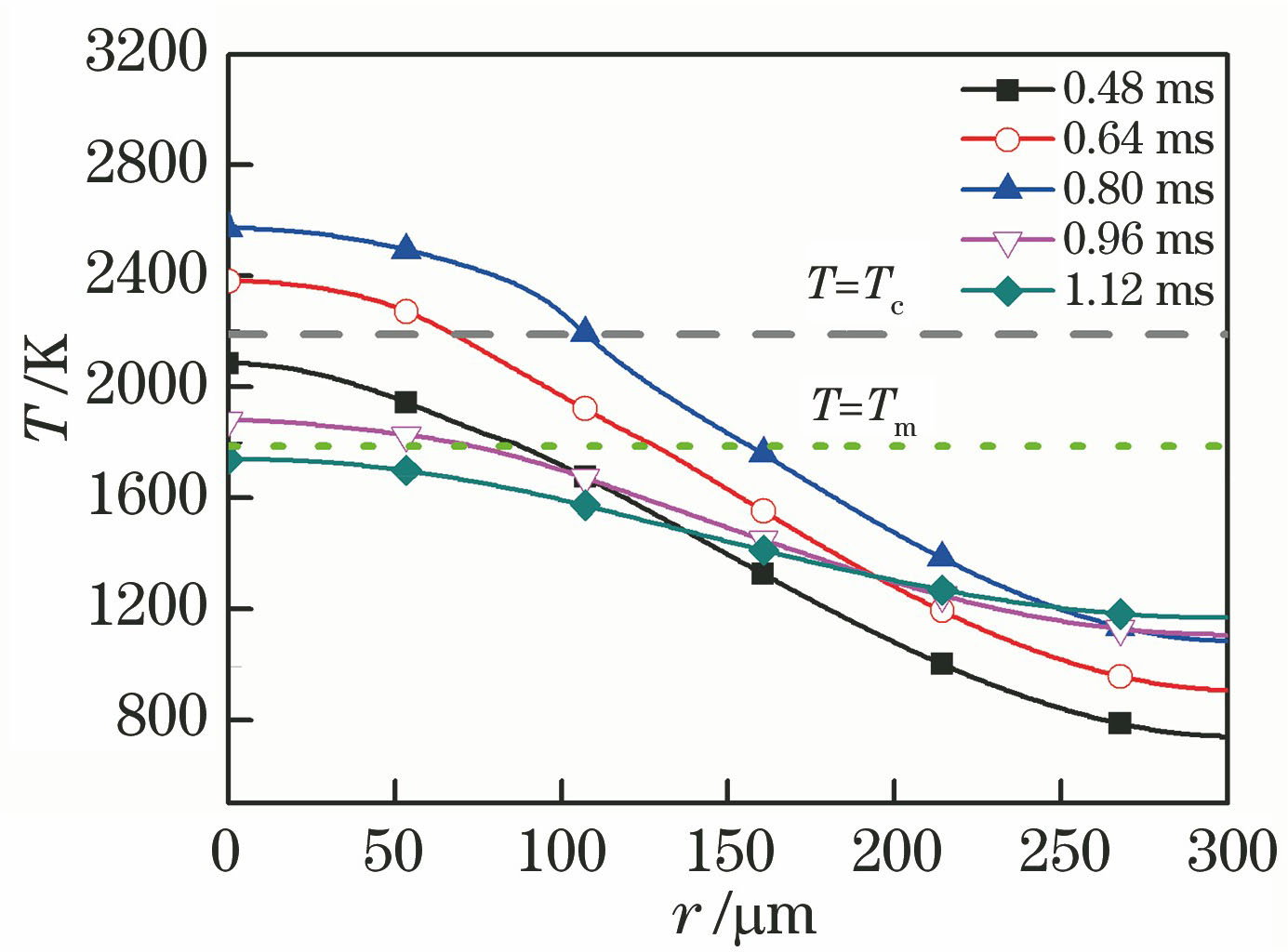
图 3. 不同时刻靶材表面的热力学温度分布
Fig. 3. Temperature distribution of target surface at different time
由(15)式和(16)式可得液态45钢的表面张力和表面张力温度系数随温度的变化情况,如

图 4. 液态45钢表面张力和表面张力温度系数随温度的变化
Fig. 4. Variations of surface tension and surface tension temperature coefficient of liquid 45 steel with temperature
4.2 熔池的流动行为
熔池中流体的流向和流速是决定毛化点形貌的直接因素。
由
由
4.3 形貌演变
根据上述规律可以得出毛化点形貌随激光加热时间的演变规律,并且可以预测毛化点的形貌。当加热时间较短(0.48 ms)时,熔池上方形成的逆时针环流会使熔池表面产生高度差,如
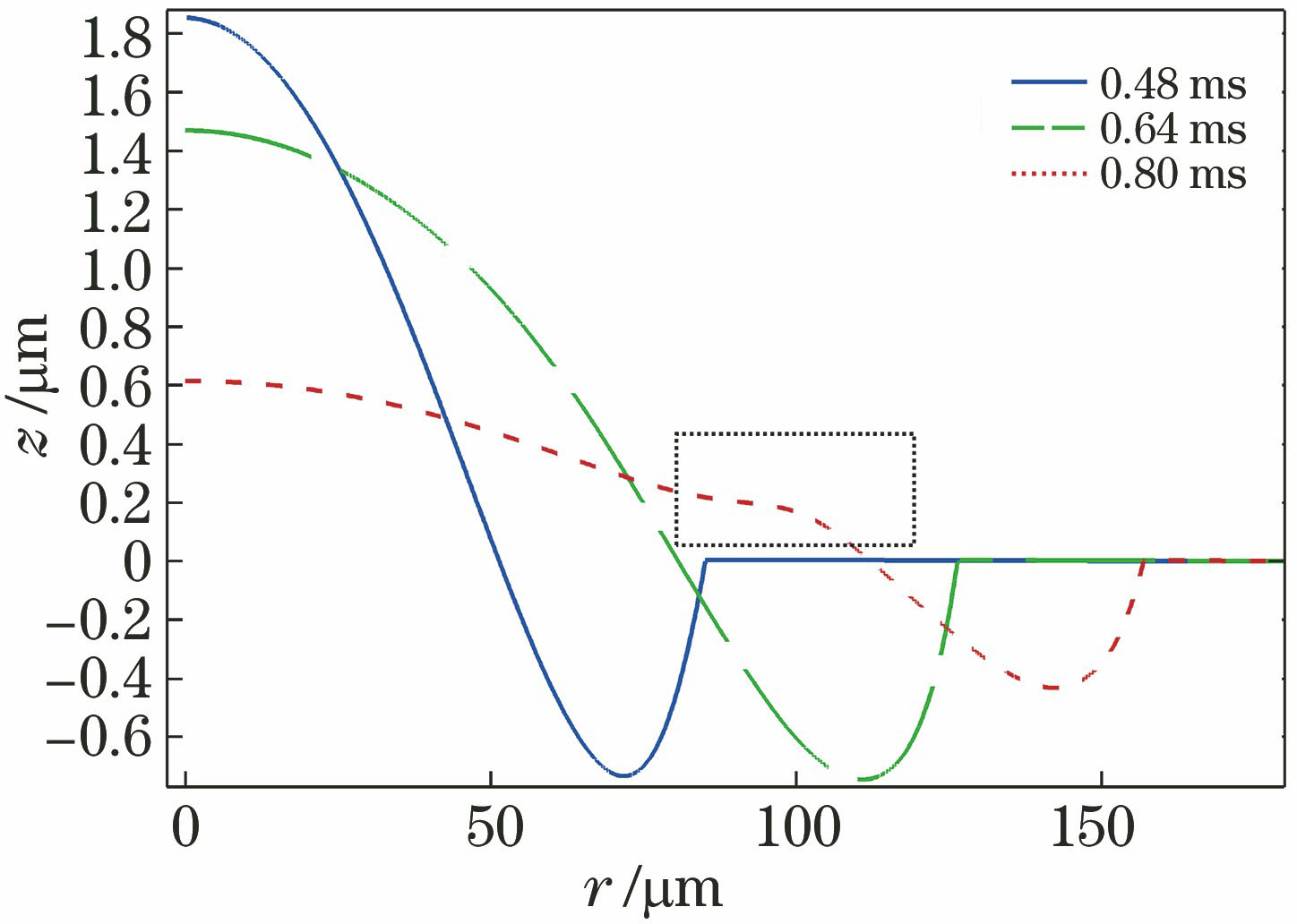
图 6. 加热过程熔池表面形貌的演变
Fig. 6. Evolution of surface morphology of molten pool during heating process
4.4 其他影响因素
选取加热0.80 ms研究光束撤离后熔池的冷却过程。通过(4)式中的
4.5 实验对比
将模拟所得的球冠状形貌与实验结果进行比较,如
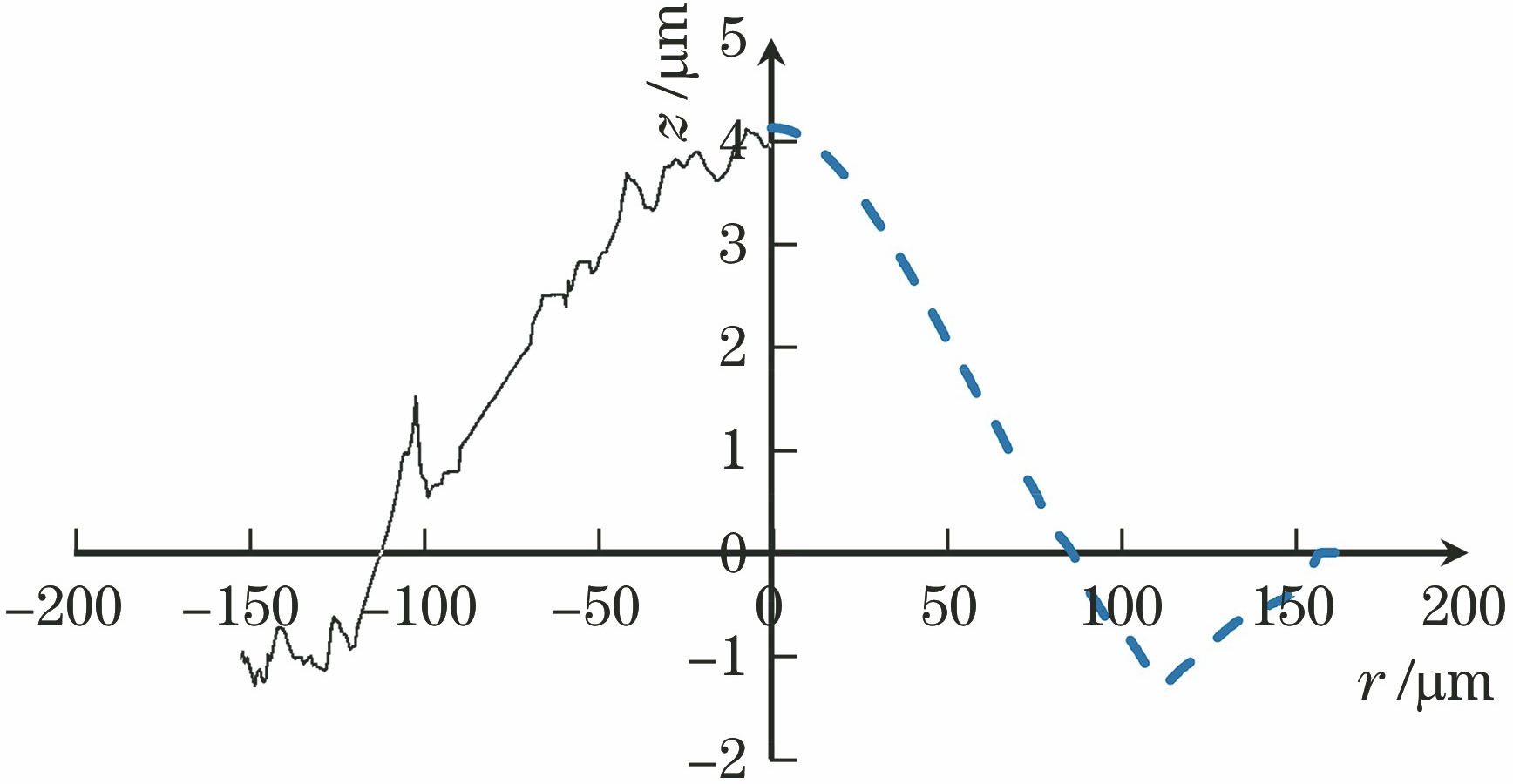
图 9. 实验形貌与仿真形貌的对比
Fig. 9. Comparison between experimental morphology and simulation morphology
表 5. 实验测量得到的宽度和高度
Table 5. Width and height measured in experiment
|
实验与仿真得到的高度和宽度的对比如
表 6. 实验测量结果与模拟结果对比
Table 6. Comparison between experimental measurement and numerical simulation results
|
5 结论
以45钢为研究对象,采用二维轴对称模型进行毛化仿真探究脉冲激光作用下熔池内的温度场、流体流向和流速的变化情况,据此研究毛化形貌形成的微观机理和动态过程。得到的主要结论如下:张力温度系数为正的含硫材料在加热过程中存在临界温度
[1] 刘莹, 陈大融, 杨文言. 轧辊表面微凸体形貌激光毛化技术的试验研究[J]. 机械工程学报, 2003, 39(7): 107-110.
[3] 叶云霞, 贾子扬, 符昊, 等. 脉冲激光作用下45#钢表面微凸起形貌演变规律的研究[J]. 激光与光电子学进展, 2016( 3): 031408.
[8] Willis D A, Xu X. Transport phenomena and droplet formation during pulsed laser interaction with thin films[J]. Journal of Heat Transfer, 2000, 122(4): 763-770.
[9] Bennett T D, Krajnovich D J, Grigoropoulos C P, et al. Marangoni mechanism in pulsed laser texturing of magnetic disk substrates[J]. Journal of Heat Transfer, 1997, 119(3): 589-596.
[11] 许伯强, 汪昊, 徐桂东, 等. 金属材料中激光产生熔池的数值模拟及应用[J]. 江苏大学学报(自然科学版), 2010, 31(3): 358-362.
[12] 刘红斌, 万大平, 胡德金. 脉冲激光表面熔凝熔池演变数值模拟[J]. 上海交通大学学报, 2008, 42(9): 1438-1442.
[13] 王维, 刘奇, 杨光, 等. 钛合金激光熔凝熔池流场及温度场的数值模拟[J]. 应用激光, 2014, 34(5): 389-394.
[15] Shen H, Pan Y Q, Zhou J, et al. Forming mechanism of bump shape in pulsed laser melting of stainless steel[J]. Journal of Heat Transfer, 2017, 139(6): 062301.
[19] Zhang C, Zhou J, Shen H. Role of capillary and thermocapillary forces in laser polishing of metals[J]. Journal of Manufacturing Science and Engineering, 2017, 139(4): 041019.
[22] 陈晓锋. 激光深熔焊接厚板细长小孔瞬态形成过程模拟研究[D]. 长沙: 湖南大学, 2014: 23- 34.
Chen XF. Study on simulation of slender keyhole transient formation process during deep penetration laser welding of thick plate[D]. Changsha: Hunan University, 2014: 23- 34.
[24] 陈家祥. 炼钢常用图表数据手册[M]. 2版. 北京: 冶金工业出版社, 2010: 213.
Chen JX. Manual of commonly used chart data for steelmaking[M]. 2nd ed. Beijing: Metallurgical Industry Press, 2010: 213.
[25] 田宗军, 王东生, 黄因慧, 等. 45钢表面激光重熔温度场数值模拟[J]. 材料热处理学报, 2008, 29(6): 173-178.
Article Outline
符永宏, 黄婷, 叶云霞, 华希俊, 李海波, 钟行涛. 熔质流动特性对毛化凸点成形的影响[J]. 中国激光, 2019, 46(7): 0702005. Yonghong Fu, Ting Huang, Yunxia Ye, Xijun Hua, Haibo Li, Xingtao Zhong. Influence of Melt Flow Characteristics on Textured Bump Forming[J]. Chinese Journal of Lasers, 2019, 46(7): 0702005.