38MnVS6钢中硫元素扩散对激光熔覆涂层形貌和组织的影响
下载: 1036次
1 引言
激光熔覆技术利用高功率密度激光束辐照基体和粉末材料,形成液态熔池,随着熔池的迅速凝固,在基体表面形成冶金结合的熔覆层[1-3]。在激光熔覆过程中,熔池的流动对熔覆层的形貌、成分分布、显微组织和性能具有重要影响[4-6]。熔池流动过程中的马兰戈尼效应对流体的流动起决定性作用[7-10],被称为活性元素的第VIA族元素对流体的流动有重要影响[11]。
Lu等[12]研究发现,在钨极稀有气体保护焊接过程中,氧含量的轻微变化显著改变了焊缝的形状,增大了熔深。Mills等[13]发现,在激光焊接过程中,焊丝中活性元素的含量对熔池流动方向的改变有着重要影响。Lienert等[14]研究发现,激光焊接硫含量差异较大的两块钢板,得到的焊缝两侧的熔池呈现不同的流动方向。上述研究集中于激光焊接过程保护气或焊丝中的活性元素对熔池马兰戈尼对流的影响,但有关激光熔覆过程中活性元素对熔覆层流动方向影响的研究鲜有报道[15-16],尤其是基体中活性元素对熔覆层形貌的影响。
硫是最常见的表面活性元素之一,广泛存在于各种材料中,特别是钢铁材料中。本文选择含硫的38MnVS6钢作为激光熔覆基体,研究了基体中硫元素对激光熔覆过程马兰戈尼对流方向、涂层形貌与组织的影响,并分析了工艺参数对涂层形貌的影响机制。研究结果为激光熔覆过程中基体材料及熔覆粉末的选择提供了参考。
2 实验材料和方法
选择硫含量(质量分数,下同)为0.04%的38MnVS6亚共析钢作为基体,自熔Co基合金作为熔覆粉末,粉末粒径为40~150 μm。基体和熔覆粉末的化学成分见
表 1. 基体和熔覆粉末的化学成分(质量分数,%)
Table 1. Chemical compositions of substrate and cladding powder (mass fraction, %)
|
激光熔覆实验使用波长为1030 nm的1 kW Nd∶YAG连续波激光器。激光通过直径为100 μm的光纤传输,由焦距为160 mm的透镜聚焦。激光熔覆实验装置如
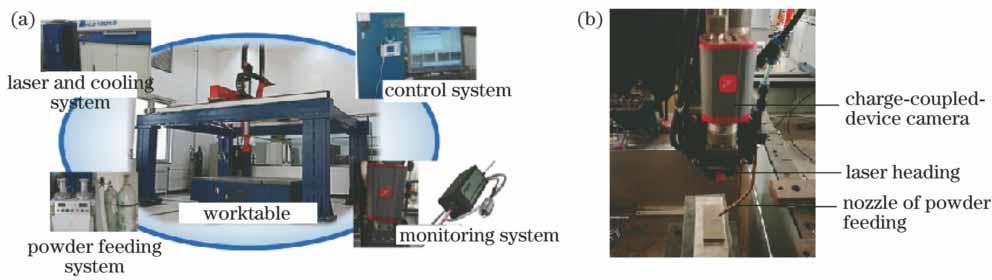
图 1. 激光熔覆实验装置。(a)加工系统;(b)加工头
Fig. 1. Experimental setup of laser cladding. (a) Processing system; (b) processing head
采用线切割方式对试样进行切割,机械研磨、抛光试样横截面后用王水进行化学腐蚀。利用能谱仪(EDS)检测涂层中主要元素的分布情况。使用俄歇电子能谱(AES)测试涂层中硫的含量。
3 实验结果与讨论
3.1 涂层形貌转变的规律和机理
不同扫描速度下涂层的横截面形貌如
不同扫描速度下涂层的稀释率如
当扫描速度为10 mm·s-1时,不同送粉率下涂层的横截面形貌如
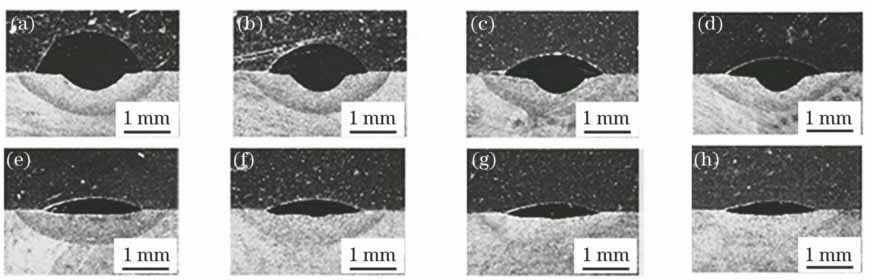
图 2. 不同扫描速度下涂层的横截面形貌。(a) 2 mm·s-1;(b) 3 mm·s-1;(c) 4 mm·s-1;(d) 5 mm·s-1;(e) 6 mm·s-1;(f) 7 mm·s-1;(g) 8 mm·s-1;(h) 9 mm·s-1
Fig. 2. Cross-sectional morphologies of cladding layers under different scanning speeds. (a) 2 mm·s-1;(b) 3 mm·s-1; (c) 4 mm·s-1; (d) 5 mm·s-1; (e) 6 mm·s-1; (f) 7 mm·s-1; (g) 8 mm·s-1; (h) 9 mm·s-1
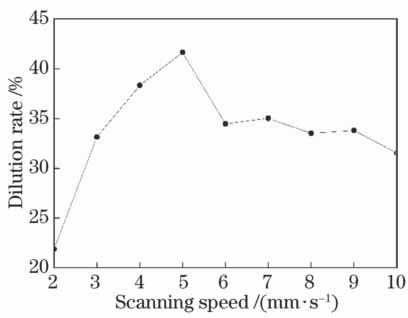
图 3. 不同扫描速度下涂层的稀释率
Fig. 3. Dilution rates of cladding layers under different scanning speeds
线呈现下凹的特征;当送粉率大于5.60 g·min-1时,涂层的熔深较小,涂层与基体结合平整光滑。
不同扫描速度下涂层中沿深度方向的硫元素检测结果如
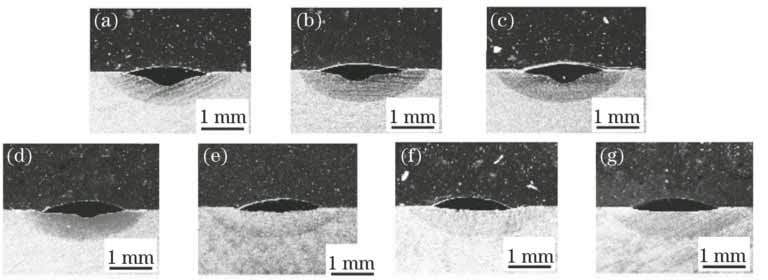
图 4. 不同送粉率下涂层的横截面形貌。(a) 1.80 g·min-1;(b) 3.13 g·min-1;(c) 4.37 g·min-1;(d) 5.60 g·min-1;(e) 6.93 g·min-1;(f) 8.17 g·min-1;(g) 9.40 g·min-1
Fig. 4. Cross-sectional morphologies of cladding layers under different powder feeding rates. (a) 1.80 g·min-1;(b) 3.13 g·min-1; (c) 4.37 g·min-1; (d) 5.60 g·min-1; (e) 6.93 g·min-1; (f) 8.17 g·min-1; (g) 9.40 g·min-1
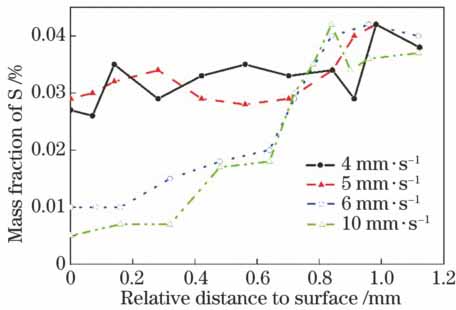
图 5. 不同扫描速度下涂层中沿深度方向的硫元素分布
Fig. 5. Content of sulfur element distribution along depth direction of cladding layer under different scanning speeds
在激光熔覆过程中,随着激光的辐照和合金粉末的添加,粉末和部分基体熔化形成熔池,熔池中的金属液体高速流动,最高可达102 mm·s-1量级[18]。表面张力梯度引起的马兰戈尼效应和浮力的综合作用决定了流体流动的形式和速度[17,19]。由Gibbs-Langmuir等温吸附理论可知,合金体系的表面张力温度系数由温度和活性元素的浓度所决定[11]。纯金属的表面张力温度系数是负值,熔池中心的表面张力较小,熔池边缘附近的表面张力大,由此引起流体向外流动,易于形成宽而浅的熔池。随着表面活性元素浓度的增大,表面张力温度系数可能由负值变为正值,表面的液态金属从温度较小的边缘区域流向温度较大的中心,然后会聚向下形成窄而深的熔池。根据Fe-S和Co-S二元合金体系的表面张力温度系数相关参数[20],采用差值法估算Fe-Co-S体系的表面张力温度系数,结果如
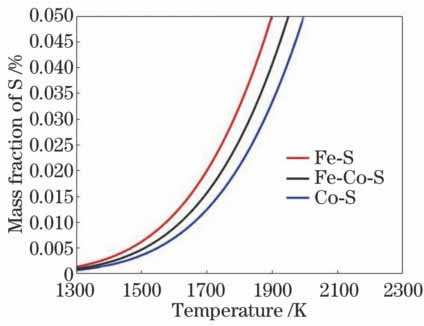
图 6. 不同合金的表面张力温度系数
Fig. 6. Temperature coefficient of surface tension for different alloys
38MnVS6钢中含有一定量的硫元素,在激光熔覆过程中,当温度增大时,基体材料熔化,硫元素进入熔池,而硫元素浓度和熔池温度会随着扫描速度的变化而变化。由
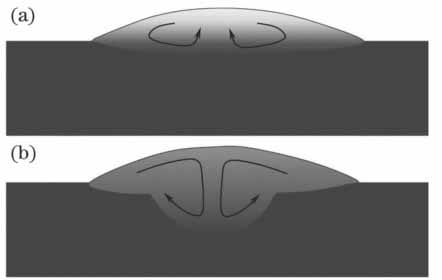
图 7. 激光熔覆中马兰戈尼对流方向示意图。(a)向外流动;(b)向内流动
Fig. 7. Schematic of direction of Marangoni convection in laser cladding. (a) Outward flow; (b) inward flow
3.2 流动方向对涂层成分和组织的影响
为了进一步考察流动方向对涂层成分及组织的影响,选取Fe和Co作为基体和熔覆粉末中的主要元素。不同扫描速度下Fe和Co沿涂层深度方向的分布如
基体中的活性元素改变了流体的流动方向,从而改变了熔池的形状,而熔池的形状对凝固过程中的温度梯度
扫描速度为5 mm·s-1和6 mm·s-1的涂层显微组织如
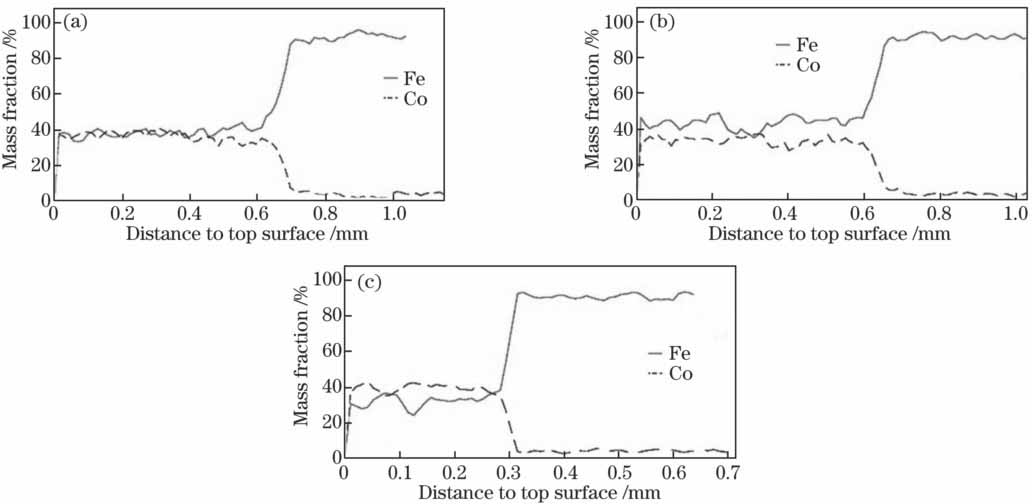
图 8. 不同扫描速度下涂层沿深度方向主要元素的分布。(a) 4 mm·s-1;(b) 5 mm·s-1;(c) 6 mm·s-1
Fig. 8. Distributions of main elements along depth direction of cladding layer under different scanning speeds. (a) 4 mm·s-1; (b) 5 mm·s-1; (c) 6 mm·s-1
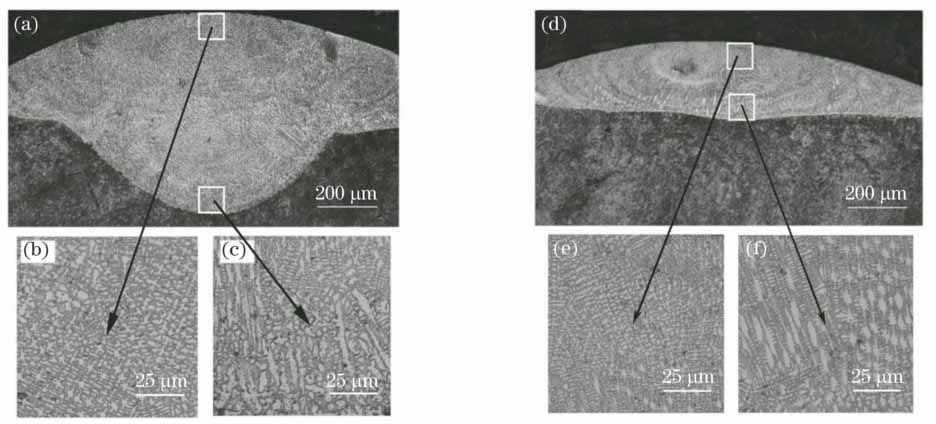
图 9. 熔池形貌和凝固前沿示意图。(a)内流型熔池;(b)外流型熔池
Fig. 9. Schematics of molten pool morphology and solidification front. (a) Molten pool with inward flow; (b) molten pool with outward flow
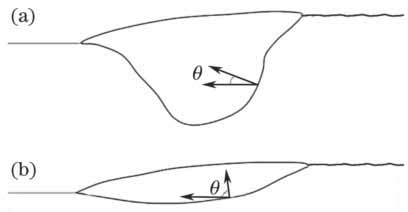
图 10. 涂层的显微组织。(a)内流型熔池,横截面;(b)内流型熔池,顶部;(c)内流型熔池,底部;(d)外流型熔池,横截面;(e)外流型熔池,顶部;(f)外流型熔池,底部
Fig. 10. Microstructures of cladding layer. (a) Molten pool with inward flow, cross-section; (b) molten pool with inward flow, top region; (c) molten pool with inward flow, bottom region; (d) molten pool with outward flow, cross-section; (e) molten pool with outward flow, top region; (f) molten pool with outward flow, bottom region
外流型熔池的
对于金属基体中含有活性元素的激光熔覆,活性元素的含量影响了熔池中流体流动的方式,从而影响了涂层的形态及稀释率,进而影响涂层最终的成分和组织。因此,在激光熔覆过程中,可以通过选择基体或熔覆粉末成分、调节工艺参数和环境等因素,控制熔池中活性金属的含量或熔池温度,最终获得所需的涂层。
4 结论
利用激光熔覆技术,在硫含量为0.04%的38MnVS6钢上制备了CoCrW涂层,得到以下结论。
1) 涂层横截面呈现两种不同的形貌特征:一种是熔深较大,涂层与基体的结合线中心部分向下凹陷;另一种是熔深较小,涂层与基体的结合线平整光滑。
2) 基体中活性元素含量的差异引起了两种不同的涂层形貌。
3) 扫描速度和送粉率对涂层的形貌、成分、组织都有重要影响。
[3] 段晓溪, 高士友, 顾勇飞, 等. 激光熔覆316L+SiC的强化机制和摩擦磨损性能研究[J]. 中国激光, 2016, 43(1): 0103004.
段晓溪, 高士友, 顾勇飞, 等. 激光熔覆316L+SiC的强化机制和摩擦磨损性能研究[J]. 中国激光, 2016, 43(1): 0103004.
[9] 彭进, 王星星, 李刚, 等. 激光填丝焊对熔池动态行为及焊缝成形的影响[J]. 中国激光, 2017, 44(11): 1102004.
彭进, 王星星, 李刚, 等. 激光填丝焊对熔池动态行为及焊缝成形的影响[J]. 中国激光, 2017, 44(11): 1102004.
[13] Mills K C, Keene B J, Brooks R F, et al. Marangoni effects in welding[J]. Philosophical Transactions of the Royal Society A, 1998, 356(1739): 911-925.
Mills K C, Keene B J, Brooks R F, et al. Marangoni effects in welding[J]. Philosophical Transactions of the Royal Society A, 1998, 356(1739): 911-925.
[19] 夏胜全, 何建军, 王巍, 等. 激光深熔焊熔池三维瞬态行为数值模拟[J]. 中国激光, 2016, 43(11): 1102004.
夏胜全, 何建军, 王巍, 等. 激光深熔焊熔池三维瞬态行为数值模拟[J]. 中国激光, 2016, 43(11): 1102004.
陈茹, 虞钢, 何秀丽, 甘政涛, 李少霞. 38MnVS6钢中硫元素扩散对激光熔覆涂层形貌和组织的影响[J]. 中国激光, 2018, 45(6): 0602005. Ru Chen, Gang Yu, Xiuli He, Zhengtao Gan, Shaoxia Li. Effect of Sulfur Diffusion in 38MnVS6 Steel on Morphology and Microstructure of Laser Cladding Layers[J]. Chinese Journal of Lasers, 2018, 45(6): 0602005.