陶瓷材料激光增材制造的研究现状及展望
下载: 2442次封面文章
1 引言
陶瓷材料常用的成型方法包括挤出成型、干压成型、等静压成型、热压成型、热压铸成型、轧膜成型、流延成型、注浆成型、凝胶注膜成型等[1]。用这些传统方法制备陶瓷构件时,需要根据构件的形状制作模具,构件坯体在烧结成型后还需要进行切割和研磨加工等,整个工艺流程时间长,成本高。此外,这些传统方法不能够用来制造形状比较复杂(比如带有内孔)和高尺寸精度的构件[2]。因此,需要开发一个更有效、更经济的高技术陶瓷制造工艺。近年来,增材制造技术受到学者们的广泛关注。增材制造技术又称为快速成型工艺,其首先利用计算机软件设计出拟构建的三维实体模型,然后将三维模型按一定厚度分割成一系列二维截面,将二维截面信息传输到数控成型系统,利用成型机通过激光束或热熔喷嘴等将打印材料(如陶瓷粉末、金属粉、塑料微球、组织细胞等)按照截面信息进行逐层添加,制造出三维实体构件[1]。金属和塑料材料的增材制造技术已相对成熟,而陶瓷材料的增材制造技术仍面临众多技术难题:一方面,现有的特定技术无法对具有不同形态和特性的各种材料进行三维(3D)打印,如金属和塑料材料的打印技术不适合陶瓷材料打印;另一方面,3D打印用陶瓷原材料稀缺。目前,陶瓷材料3D打印成本高,效率低,精度有限。陶瓷材料增材制造技术近年已成为研究热点之一[3-4]。
2 陶瓷材料激光增材制造技术
陶瓷材料增材制造可以分为以下几种:粉基三维打印成型(P-3DP)、粉基激光选区熔融(P-SLM)、粉基激光选区烧结(P-SLS)、浆料基三维打印成型(S-3DP)、浆料基激光选区烧结(S-SLS)、立体光刻成型(SLA)、分层实体成型(LOM)、直接喷墨打印(DIP)、直写式自由成型(DIW)、熔化沉积成型(FDM)和直接打印(DP)。激光在P-SLM、P-SLS、S-SLS、SLA和LOM技术中起到了熔化、烧结、光固化等作用。
表 1. 利用不同激光增材制造技术制造的陶瓷构件的精度
Table 1. Precisions of ceramic parts processed by different kinds of LAM techniques
|
2.1 P-SLM
P-SLM作为无需任何黏结剂和后续烧结步骤的技术,提供了利用松散粉体直接制造复杂形状陶瓷的可能性[5-7]。如
P-SLM系统使用刮刀将粉末散布到基板平台或粉床上。粉末颗粒良好的流动性是获得薄且均匀的粉末层的必要条件[9]。粉末床密度也对最终构件质量产生直接影响,故必须精确控制粉末参数,如粒度、分布、颗粒形状和流动性。粉末粒度和分布是P-SLM中粉末沉积的关键,较小的粒度有利于得到高粉末床密度和构件密度,粉末粒度为粉床厚度1/10的陶瓷粉末适合激光制造工艺[10]。但小粉末容易产生团聚,导致流动性差。由于存在静电电荷,小的粉末颗粒容易附聚并粘附在印刷平台的表面和刮刀上,难以形成均匀的粉末层。由于颗粒的聚集,陶瓷粉末层(如SiO2)在基板上铺设不均,从粉末原料中除去较小的颗粒能提高流动性,但会对粉末床的密度产生负面影响,进而影响构件密度[11]。
粉末形状对粉末的扩散和粉末床的密度也有影响[12]。Wilkes等[13]认为,球形粉末有利于改善P-SLM构件密度。由于没有专门为P-SLM工艺设计的陶瓷粉末,因此选择P-SLM的最佳粉末并不容易。市场上可以买到利用不同方法(如粉碎法和喷雾干燥法)制备的粉末。一般通过粉碎法制备的粉末有棱角且体积密度较高。通过喷雾干燥技术可获得尺寸在1 μm到几十微米之间的球形陶瓷颗粒,与粉碎法获得的陶瓷粉末相比具有更好的流动性。尽管如此,由于喷雾干燥颗粒具有多孔结构,此技术获得的粉末密度相对较小[14]。高温等离子体技术可用于制造球形且致密度高的微米级陶瓷颗粒,将原料颗粒进料到等离子火焰中,颗粒熔化,在凝固过程中形成具有高表面积与体积比的微球[15]。高温等离子体技术处理的陶瓷原料粉成为适合P-SLM工艺的候选粉末。
粉料在特定激光波长的吸收率是激光制备工艺需考虑的重要参数之一[16]。P-SLM工艺常使用波长约为1.06 μm的掺Nd的YAG激光器或光纤激光器作为光源。实验测得的陶瓷粉末吸收率如
表 2. 陶瓷粉末对Nd∶YAG激光和CO2激光的吸收率
Table 2. Absorptivity of Nd∶YAG and CO2 aser by ceramic powder
|
由
利用P-SLM/P-SLS制备的陶瓷构件在高温度梯度下容易发生开裂,因此需要研究热和残余应力对开裂的影响。Wilkes等[13]将Al2O3/ZrO2陶瓷粉末预热后进行激光选区熔融,制备的构件具有近100%的密度和500 MPa以上的抗弯强度。构件表面质量差(表面粗糙度Rz为60 μm,尺寸精度为150 μm),这是因为在高温预热处理下,形成的大尺寸熔池和低黏度熔体流入了周围的粉末床。不需要预热可以实现较好的表面质量,但制备的构件机械强度较小。张凯等[22]将粉末和水按1∶1的质量比混合,配制出具有较高流动性的浆料。预热基板,将浆料升温至110 ℃后进行P-SLM操作。大部分水在预热中蒸发,少量的薄膜水因表面张力仍吸附在陶瓷的表面,对颗粒起到聚集的作用。在激光选区扫描时,先形成有助于热量传递的高温热蒸汽,陶瓷粉末获得足够的能量后快速熔化,构件成型效果较好。激光的功率越高,构件表面质量越好。当激光功率提高到200 W时,构件表面的扫描轨迹连续,没有明显的气孔和裂纹,相邻扫描线结合情况较好。
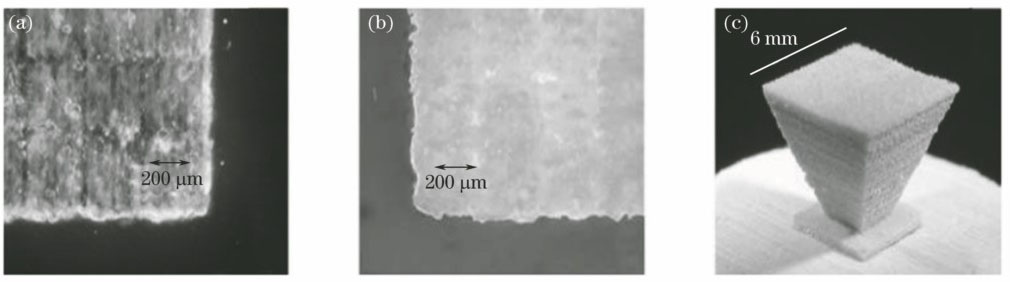
图 2. (a)(b)具有高相对密度和高分辨率的氧化物陶瓷截面;(c)倒立的金字塔
Fig. 2. (a)(b) Cross sections of oxide ceramics with high relative density and high resolution; (c) inverted pyramid
未来P-SLM研究需要解决冷粉沉积问题,同时提高构件的表面质量和机械强度,并实现该技术的工业化应用。
2.2 P-SLS
早在1989年,Deckard[23]申请了《通过选择性烧结制备构件的方法及设备》的专利,开启了激光选区烧结技术的大门。通过激光束扫描使陶瓷粉末熔结或陶瓷粉末与黏结剂(无机或聚合物)形成的粉末烧结,产生局部致密化。由于陶瓷材料对热冲击的耐受性差,直接进行激光熔接较困难。而利用激光束扫描陶瓷粉末与黏结剂形成的复合粉末时,黏结剂可以被很好地热激活,有助于粉末的局部致密化,其技术原理如
制备生物工程应用支架的另一种方法是使用生物相容性聚合物作为黏结剂。Simpson等[28]研究了95/5聚(L-丙交酯-共-乙交酯,PLG)在生物多孔支架中的应用,含有质量分数为40%的羟基磷灰石的PLG基复合材料经过激光烧结加工后,可以获得类似于人体小梁骨的支架。Tan等[29]将聚醚醚酮(PEEK)与羟基磷灰石复合,利用激光烧结得到一种不需要后续烧结的聚合物-陶瓷生物构件。
采用P-SLS方法烧结后得到的是相对密度较小的多孔陶瓷构件,仍然无法制备形状复杂的传统陶瓷。Liu等[30]将P-SLS工艺与冷等静压工艺(CIP)相结合,制备出具有较少孔隙的个性化传统高岭土陶瓷构件。将质量比为9∶1的高岭土颗粒与环氧树脂E06粉末均匀混合24 h,得到流动性佳、适合P-SLS加工的原料。调整激光参数,发现激光能量密度在0.2750~0.4125 J/mm2之间时,可以完成激光的选区烧结并形成坯体。当激光能量密度太小时,激光的能量甚至不能熔化环氧树脂,故不能粘结高岭土颗粒;当激光能量密度太大时,过大的能量使环氧树脂挥发或碳化,得到的坯体会变黑。将液态天然橡胶胶乳作为软膜涂覆在P-SLS坯体的表面,并在85 ℃下固化,当激光能量密度在0.3300~0.3763 J/mm2之间时,可以成功地完成涂覆。当激光能量密度相对较小时,尽管可以形成P-SLS坯体,但黏结剂没有完全被熔化,一些环氧树脂不能发挥黏结的作用,而当激光强度较大时,一部分黏结剂挥发或碳化,削弱了环氧树脂的黏结作用。这两种情况下P-SLS得到的构件强度都较小,无法完成CIP过程。成功完成CIP过程的坯体烧结后,可得到类似传统工艺制备的高岭土陶瓷构件。
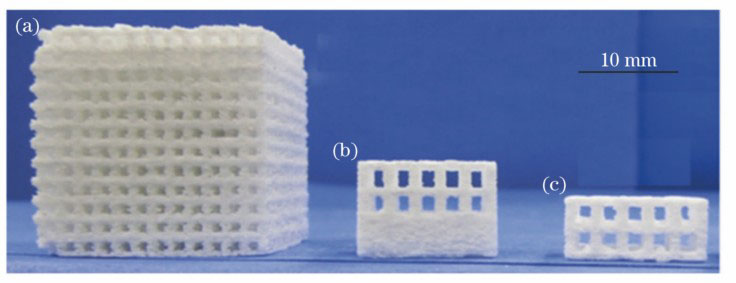
图 4. (a)孔径为1 mm的立方多孔构件;(b)有基底结构孔径为2 mm的支架;(c)没有基底结构的支架
Fig. 4. (a) Cubic porous part with pore size of 1 mm; (b) scaffold with base structure and pore size of 2 mm; (c) scaffold without base structure
2.3 SLA
SLA利用光聚合含有陶瓷粉体颗粒的液体树脂,因此不需要高能量的激光即可进行光刻,其技术原理如
SLA浆料的典型组合物包括体积分数为40%~60%的单体溶液、光引发剂和用于分散陶瓷粉末的添加剂。与基于粉末的增材制造技术不同的是,在SLA中,构件周围是不能提供支撑的液体材料,故在光刻过程中需要根据构件的具体几何形状形成一定的支撑结构。在市场上,SLA流程有不同的技术方案。奥地利Lithoz公司采用了一种将光固化层倒置的方法[33],该方法的优点是打印构件所需的浆料少,可打印高精度、高纯度陶瓷零部件,而且打印的高纯氧化铝、氧化锆陶瓷构件的四点弯曲强度可达430~650 MPa[31]。利用立体光刻技术还可制备各种多孔陶瓷组件。Kirihara[34]研制了具有有序孔隙度的功能构件。带有钇稳定氧化锆微晶格结构的固体电解质枝晶可用于新型陶瓷电极,具有金刚石结构的Al2O3构件有望作为光子晶体,具有渐变孔隙度的羟基磷灰石树枝状构件可用于生物组织支架。
一般来说,SLA可以利用粉末填充密度高于55%的坯体制备致密的陶瓷构件。存在的一个难点是:需要精密控制后续生坯的脱脂过程。在热脱脂过程中,解离和燃烧产物必须通过扩散离开坯体,因为要让构件内部的压力低于临界阈值以避免形成裂缝和空隙,所以加热过程必须缓慢进行。缓慢的脱脂过程限制了SLA陶瓷坯体的最大体积或壁厚[35-36],1 cm壁厚的坯体就需要数天以上的脱脂时间。聚合物衍生陶瓷材料在20世纪60代被制备出[37],它在一定程度上解决了脱脂的耗时问题。在稀有气体下热处理聚合物衍生陶瓷材料,材料将被热解成SiC、Si3N4、BN、AlN、SiOC、SiCN、BCN及其他成分(如挥发性物质CH4、H2、CO2、H2O和碳氢化合物)。Eckel等[38]将(巯基丙基)甲基硅氧烷与乙烯基甲氧基硅氧烷混合,并加入紫外(UV)自由基光引发剂、自由基抑制剂和UV吸收剂,对形成的硅氧烷树脂体系进行光固化,形成具有
2.4 S-SLS
S-SLS是粉末技术的一种延伸,利用陶瓷浆料或滑动剂代替干粉来增加粉末床中粉末的填充密度。Sachs等[39]提出用液体载体中粉末的分散体来实现所需速率和密度的方法。2003年,Sachs等[40]又提出使用粉末材料的液体分散体来逐层建立粉末床。现在已实现了适用于S-SLS且能够反复沉积薄层陶瓷浆料的致密粉末床技术[7,41-42]。2002年,德国克劳斯塔尔理工大学获得浆料沉积技术结合激光烧结的专利,即S-SLS技术[43]。

图 6. (a)紫外光可固化的单体和光引发剂;(b)树脂;(c)预陶瓷聚合物构件;(d)聚合物热解后得到的陶瓷构件;(e)软木塞样品;(f)(g)微晶格;(h)蜂窝
Fig. 6. (a) UV-curable monomers and UV photo initiator; (b) resin ; (c) preceramic polymer part; (d) ceramic converted from polymer; (e) cork screw; (f)(g) micro-lattice; (h) honeycomb
在S-SLS中,粉末床的生坯密度和机械强度与传统的注浆成型是相当的,故S-SLS中粉末床可以层层堆叠而不需要任何支撑结构。在使用松散粉末作为材料时,激光烧结构件容易从粉末床上释放,但是在使用S-SLS技术时,激光烧结构件嵌入在密实粉末床中,粉末床必须溶解在溶剂中才能释放构件。S-SLS选择水性浆料时,可以把水作为粉末床的溶剂。
2.5 LOM
LOM技术由美国的Lone Peak Engineering公司和Helisis公司同时开发,并实现了商业化。
Klosterman等[47]研究了LOM带与带之间的界面问题。采用具有双峰分布的SiC粉体、炭黑和石墨粉末及高分子黏合剂混合制成了陶瓷薄片。调节CO2激光器的功率,使激光器能以可接受的精度和最小的损伤切割陶瓷带。利用加热至180 ℃(足以熔化黏结剂)的辊轮层压陶瓷带,层层叠加得到坯体。坯体于600 ℃脱胶后在1600 ℃下烧结,实现了致密化。但是,这样得到的SiC构件的四点弯曲强度比预期要小很多,其主要原因如下。1) 虽然层间黏结强度足以形成构件,但是辊轮施加的瞬态压力不足以实现具有无缝层界面的紧密接触。2) 由于带铸造工艺制成的陶瓷带本身是不均匀的,陶瓷带的底表面富含聚合物。如果聚合物黏结剂无法从结合线迁移到本体粉末中,则在层界面处会存在一层厚的聚合物;黏结剂除尽时,黏合线上将出现明显的分层和弱结构。针对上述问题,有两种改进方法:1) 将聚合物的溶剂溶液在层压前均匀分散到陶瓷带底部,将聚合物溶解在叠层上,再进行层压;2) 坯体在低压(0.069~0.103 MPa)、80 ℃加热平板上压制60 min,再进行后续的烧结。得到的构件层间界限被明显消除,只存在极少量的孔隙。
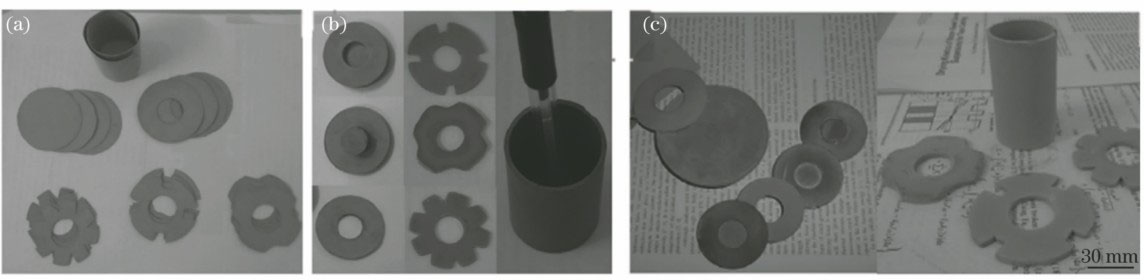
图 10. 烧结前后的坯带和Si3N4的样品。(a)坯带;(b)坯体;(c)烧结后的构件
Fig. 10. Green tapes and Si3N4 samples before and after sintering. (a) Green pieces; (b) green bodies; (c) sintered components
LOM在低介质温度和压力下层压纸张、胶带或类似的片材得到3D实体构件,被认为是将陶瓷带层压成3D密实或半密实构件的替代方案。它的优点是可以直接加工通过挤出、带状铸造等技术得到的片材。另外,LOM的加工还具有以下特点:1) 与SLA技术相比,在热处理过程中不会引入额外的有机成分;2) 与低温层压工艺相比,LOM施加的压力和温度更低,防止了复杂形状时不均匀的压力分布引起的分层;3) 在热处理过程中不需要更大的毛细作用力来促进相邻带之间的连接。
相比于传统的制造工艺如注塑、挤出、辊压, LOM制品能在相对较大的孔隙率时得到适中的弯曲强度。如
3 结束语
目前,市场上几乎没有能够生产完全致密陶瓷构件的激光增材制造技术。粉末基技术具有原材料的成本低、可并行处理多个构件、设计的灵活性高、可直接制造具有低含量有机添加剂的陶瓷生坯体等优点,将成为最经济的陶瓷增材制造技术之一。未来希望市场能够提供具有粒度分布均匀、颗粒堆积密度高的粉末,并具有很大的选择自由度。对于浆料,需要解决其流动性控制以及后续的快速脱脂等问题。需要对激光增材制造系统进一步优化和升级,对激光光源的聚焦光束质量和稳定性、振镜系统的扫描稳定性、粉体或浆料刮刀平整性、基座平台精度、腔体以及基底的温度、切片软件控制和补偿等进行精密控制。相信在不久的将来,利用增材制造技术能够制造出从微米量级尺寸到纳米量级尺寸且结构致密的复杂陶瓷结构。
[1] 夏雪. 浅谈我国3D打印陶瓷材料及产业化发展[J]. 陶瓷, 2017( 5): 9- 12.
XiaX. Introduction to 3D printing ceramics and industrialiazation development in China[J]. Ceramics, 2017( 5): 9- 12.
[3] 贲玥, 张乐, 魏帅, 等. 3D打印陶瓷材料研究进展[J]. 材料导报, 2016, 30(21): 109-118.
[15] Garcia E, Mesquita-Guimarães J, Miranzo P, et al. Mullite and mullite/ZrO2-7wt.%Y2O3 powders for thermal spraying of environmental barrier coatings[J]. Journal of Thermal Spray Technology, 2009, 19(1): 286-293.
[19] 佚名. CO2激光器缩短了陶瓷品的制作时间[J]. 激光与光子学进展, 1970, 7(12): 37-37.
[20] ExnerH, RegenfussP, HartwigL, et al. Selective laser micro sintering with a novel process[C]. SPIE, 2003, 5063: 145- 151.
[22] 张凯, 刘婷婷, 廖文和, 等. 氧化铝陶瓷激光选区熔化成形实验[J]. 中国激光, 2016, 43(10): 1002007.
[23] Deckard C R.Method and apparatus for producing parts by selective sintering: US4863538[P].1989-09-05.
[27] 关泰红, 高勃, 吕晓卫, 等. 激光快速成形工艺参数对生物陶瓷复合涂层物相组成的影响[J]. 中国激光, 2009, 36(10): 2717-2721.
[31] 李伶, 高勇, 王重海, 等. 陶瓷部件3D 打印技术的研究进展[J]. 硅酸盐通报, 2016, 35(9): 2892-2897.
[37] Wroblewska GH. Structural ceramics with complex shape——forming methods[C]. 25th Annual Conference on Composites, Advanced Ceramics, Materials and Structures, 2001, 22( 3): 43- 50.
[39] Sachs EM, Somerville JS, Cima MJ, et al. Three dimensional printing techniques: US5340656[P]. 1994-08-23.
[40] Sachs EM, Cima MJ, Caradonna MA, et al. Jetting layers of powder and the formation of fine powder beds thereby: US6596224[P].2003-07-22.
[43] KrauseT, EnglerS, GünsterJ, et al. Process and a device for producing ceramic molds: US6827988[P].2004-12-07.
倪荣萍, 钱滨, 刘畅, 邱建荣. 陶瓷材料激光增材制造的研究现状及展望[J]. 激光与光电子学进展, 2018, 55(1): 011408. Ni Rongping, Qian Bin, Liu Chang, Qiu Jianrong. Status and Prospect of Laser Additive Manufacturing of Ceramic Materials[J]. Laser & Optoelectronics Progress, 2018, 55(1): 011408.