利用FBG传感信号诊断滚动轴承故障的检测方法
下载: 702次
1 引言
轴承的性能状态直接影响着机械设备能否长期安全可靠地运行,若发生故障,会影响机械设备的正常工作,轻则导致经济损失,重则引起生产安全事故[1]。因此,对轴承故障进行诊断有助于降低设备使用风险,减小不必要的设备维修成本,利于维修人员对设备进行维护和保养[2]。
通常轴承的故障诊断是通过传感器测量应力变化,计算每个故障的特征频率并对其和真实故障频率进行对比进行的,所得到的频谱会受噪声的影响,若对信号进行傅里叶变换[3],复杂的频谱分量又会增加准确获取故障信息的难度。文献[ 4]提出一种基于变分模态分解(VMD)的故障特征提取方法,该方法对信号进行VMD并提取特征,分类的准确性得到了提高,然而该方法需要通过K值优化[5]来确定VMD分量的个数,算法复杂度较高。文献[ 6]提出一种基于卷积神经网络(CNN)和振动图像的滚动轴承故障诊断方法,该方法利用归一化幅度与信号像素之间的关系将一维信号转换为二维图像,并利用卷积神经网络进行故障分类。文献[ 7]提出一种基于一维卷积神经网络的轴承自适应诊断方法,该方法通过一维卷积神经网络对不同的轴承故障信号进行分类。以上方法虽可以有效地诊断轴承单点故障,但针对复合故障的识别还有待进一步提高。
本文提出一种经验模态分解(EMD)与改进卷积神经网络结合的轴承故障诊断方法,通过光纤布拉格光栅(FBG)获取轴承的振动信号(其振动是由应力变化引起的,其实质反映轴承的应力变化)。利用EMD将信号分解为多个本征模态函数(IMF)分量[8],并采用Pearson相关系数[9]与峭度值所构成的综合评价指标筛选出有效IMF分量。根据IMF分量的结构特性,将有效IMF分量组合为矩阵形式,并输入至卷积神经网络进行特征训练,最后经解耦分类完成对轴承的单点及复合故障的分类与识别。
2 轴承故障诊断方法
2.1 振动信号的获取
FBG传感器具有体积小、质量轻、不受电磁干扰等优点[10],相较于传统电学传感器、加速度传感器等,其材质为绝缘体,具有被动性电学特性,并且不受电磁感应和噪声的影响,安装简便。在工业环境条件下,FBG可以有效地避免厂房噪声或外界复杂环境的干扰,且能精确地提取轴承振动信号[11-12]。根据FBG工作原理,它是由中心波长的漂移量来实现传感的,中心波长的表达式为
式中:neff为光纤的有效折射率;Λ为光栅周期。当外界发生振动(或形变)时,neff和Λ会发生改变,从而导致FBG中心波长发生漂移,通过中心波长漂移量Δλ可确定外界应变大小。中心波长漂移量Δλ与应变之间的关系表达式为
式中:pe为光纤的弹光系数;ε为FBG传感器受到的应变大小。
根据上述测量原理,轴承在运行时产生的机械振动会对安装在箱体表面的FBG传感器产生应力作用,通过测量FBG传感器的波长偏移量,能采集到轴承齿轮的振动信号。对振动信号中的频率分量进行分析,并提取瞬变、调幅或调频等非平稳、非线性的特征是轴承故障识别的关键[13]。
2.2 经验模态分解算法
EMD可将FBG获取的轴承振动信号即非平稳信号分解为具有不同频率的IMF分量,其算法步骤[14]如下。
1)首先对数据进行初始化处理,确定原始信号x(t)的所有极大值点和极小值点,t为时间。利用三次样条插值法,将极大值点和极小值点分别拟合成上包络线emax(t)与下包络线emin(t),并求出上下包络线的平均曲线m1(t):
2) 计算信号的剩余分量
3) 判断h1(t)是否满足IMF条件,若不满足,则将h1(t)作为原始数据返回步骤1);若满足,则第一个IMF分量c1(t)确定。并从原始信号中分离出c1(t)。
4) 进行多次迭代,直到不满足EMD条件,最终可以分解出所有的IMF分量。但并非所有分量都包含有用信号,为此需要寻求确定有效IMF分量的方法。
2.3 有效IMF分量的确定
为了确定IMF分量的有效性,采用Pearson相关系数[15]与峭度值的综合评价指标来筛选IMF分量。
1) 相关系数
Pearson相关系数的表达式为
式中:x为原始信号;y为IMF分量;xs和ys分别为原始信号与IMF分量第s个采样点;
2) 峭度
峭度对冲激信号较为敏感,当轴承正常运转时,振动信号呈正态分布,峭度值通常为常量(一般为3)[16]。当轴承出现故障时,信号冲激成分增强,幅值会偏离正态分布,峭度值增大。峭度K的计算公式为
式中:n为采样点数。
3) 综合指标
上述两指标仅从不同的角度反映IMF分量的特性,为了更全面反映IMF分量包含的有用信息,采用综合评价指标来衡量IMF分量的有效性,将其定义为
式中:Cindex为一致性指标。当Cindex值越大,说明所包含故障信息越多,即相关性越强。在选择Cindex阈值时,将各个IMF分量的Cindex值的平均值作为筛选条件,即
式中:
2.4 故障诊断算法的设计
CNN的结构一般为输入层、卷积层、池化层、全连接层、Softmax函数、输出层[17]。目前,Softmax函数在故障诊断中主要应用于单点故障识别,在复合故障中的识别效果并不理想。受文献[
18]的启发,将解耦分类器与CNN中卷积层、池化层相结合,提出一种关于轴承的复合故障诊断方法。对此所设计的网络结构为2个卷积层和2个池化层。将经验模态分解并计算确定得到的有效IMF分量矩阵输入至CNN后,通过卷积层和池化层进行特征提取,并由最后的池化层输出高维特征向量,每个卷积层的激活函数均为ReLU函数。
式中:dj为解耦分类器的第j个输出张量,j=1,2,3,…,C,C为故障类的数量;cqj为耦合系数;
式中:bqj为初始耦合系数。初始时刻bqj趋近于0。
当得到解耦分类器的输出张量d后,采用Squash函数作为激活函数,将短矢量转换为趋于0的长度,将长矢量转换为接近1的长度,即
并对初始耦合系数进行迭代,其迭代方式如
(13)式中,
再利用L2范数将vj转换为最终预测矢量ypre=[y1,y2,…,yC],其中,ypre中的元素代表输入样本属于第j类故障的概率。最后,选用故障概率阈值φ并对其与
另外,将边缘损失函数作为损失函数时可有效扩大类间差异并减少类内变化[19]。其函数表达式为
式中:Tc为指标函数,若存在c类故障对象,Tc=1,否则Tc=0;m+为‖vc‖的上边界,m-为‖vc‖的下边界。
根据上述步骤,对EMD分解出的IMF分量进行筛选,利用IMF分量的结构特性将各个分量转换为二维矩阵并输入至所提算法中,故障诊断流程如
3 实验与分析
3.1 实验平台构建
根据传感系统设计原理,搭建的轴承故障实验平台如
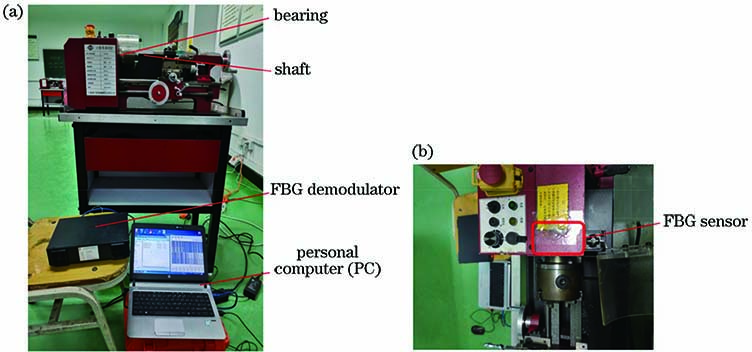
图 4. FBG轴承故障检测实验平台。(a)轴承故障检测平台;(b) FBG安装位置
Fig. 4. FBG bearing failure detection experimental platform. (a) Bearing fault detection platform; (b) FBG installation location
小型车床主轴为轴承型号为6203深沟球轴承,其参数如
表 1. 6203轴承参数
Table 1. Parameters of 6203 bearing
|
3.2 实验设计
实验中,选择具有代表性的6种故障类型的轴承:外圈故障、内圈故障、滚体故障、外圈与内圈故障、外圈与滚体故障、内圈与滚体故障,如

图 5. 不同故障轴承。(a)外圈故障;(b)内圈故障;(c)滚体故障;(d)外圈和内圈故障;(e)外圈和滚体故障;(f)内圈和滚体故障
Fig. 5. Different faulty bearings. (a) Outer fault; (b) inner fault; (c) roller fault; (d) outer & inner fault; (e) outer & roller fault; (f) inner & roller fault
3.3 振动信号采集
实验中采集振动信号时,运行时间均为1 min,转速大小为1500 r/min。
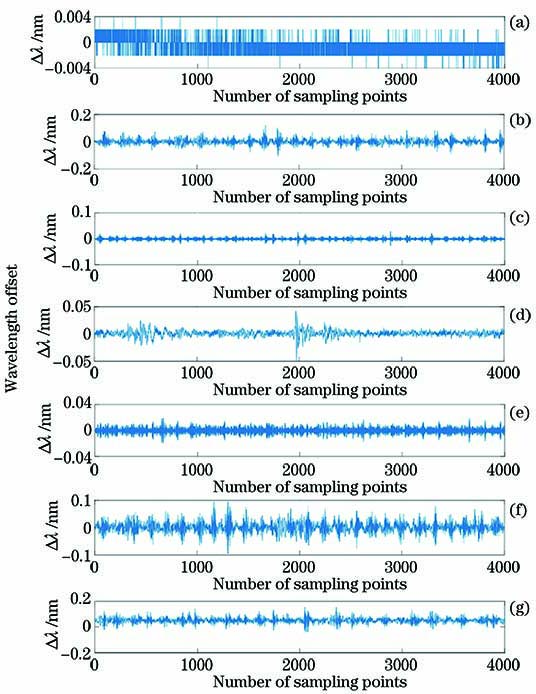
图 7. 不同故障轴承的时域信号图。(a)正常;(b)外圈故障;(c)内圈故障;(d)滚体故障;(e)外圈和内圈故障;(f)外圈和滚体故障;(g)内圈和滚体故障
Fig. 7. Time-domain signal diagrams of different faulty bearings. (a) Normal; (b) outer fault; (c) inner fault; (d) roller fault; (e) outer & inner fault; (f) outer & roller fault; (g) inner & roller fault
进一步分析可知:正常工况下,信号趋于平稳,且幅值(Δλ/nm)仅仅在-0.004~0.004内波动,如
3.4 信号分解
实验中所采用的解调仪的解调频率为2000 Hz,即1 min之内采集1.2×105个采样点,数据量过大会增加数据处理难度和时间。对此,将长信号平均分为2560个信号段,在每个信号段中选择局部极小点与极大点并保留下来,最后形成5120个样本点的信号,然后采用EMD生成多个IMF分量。如
现以外圈故障为例,通过(5)~(7)式计算得到的外圈故障下三项评价指标数值如
同时,采用相同方法,计算得到的其他故障的综合评价指标如
表 2. 外圈故障下评价指标数值表
Table 2. Numerical table of evaluation indicators under outer fault
|
表 3. 其他故障下各分量综合评价指标数值表
Table 3. Numerical table of comprehensive evaluation indicator of each components under other faults
|
3.5 特征训练与测试
根据IMF分量的结构特性,将有效IMF分量组成矩阵形式,并以采样点的形式展开,再提取各个数据点的幅值,构成二维矩阵的形式。
表 4. 改进卷积神经网络的各层尺寸
Table 4. Size of each layer of improved convolutional neural network
|
由最后的池化层(第2层)输出高维向量,并将结果作为解耦分类算法的输入。在解耦算法中,参考文献[ 18],迭代次数r选为3,将阈值φ设为0.6。为了最小化损失函数,采用默认参数设置的Adam优化器[22]来对模型进行训练和优化。经实验和信号分解得到5120个样本点,其中80%的样本用于训练,20%的样本用于测试。
3.6 实验结果与分析
为证明所提方法在故障诊断上的优越性,对传统卷积神经网络和所提方法进行对比。由于所提方法的损失函数和分类器分别是余量损失函数和解耦分类器,而传统卷积神经网络的损失函数和分类器分别是交叉熵函数和Softmax分类器,为了保证公平起见,其参数均设为相同。
采用多分类混淆矩阵来展示故障分类的状况,其横轴代表样本的输出标签,纵轴代表样本的真实标签,右侧色度条表示颜色与识别准确率的对应关系[23-24]。
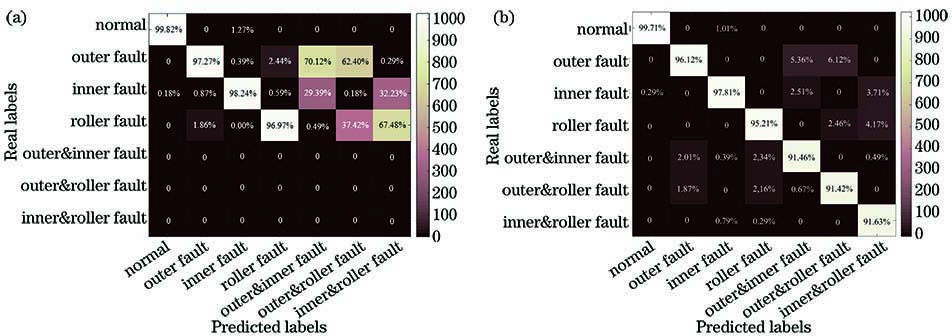
图 10. 不同方法的多类混淆矩阵。(a)传统卷积神经网络;(b)所提方法
Fig. 10. Multi-class confusion matrix of different methods. (a) Traditional convolutional neural network; (b) proposed method
4 结论
提出一种经验模态分解与改进卷积神经网络结合的轴承故障诊断方法,解决了传统卷积神经网络难以检测复合故障的问题。为了使分解出来的IMF分量具有有效性,利用Pearson相关系数对IMF分量进行筛选,依靠IMF的结构特性,将IMF分量变换为二维矩阵并输入至网络中。为了有效地诊断出轴承的复合故障,在网络中的最后池化层后连接解耦分类器,将复合故障解耦为两个单点故障进行识别。实验结果表明,所提方法可有效地对轴承的单点故障、复合故障进行诊断,诊断准确率均在91%以上,为准确地识别轴承故障提供了参考。
[2] JiaF, Lei YG, LinJ, et al. and intelligent diagnosis of rotating machinery with massive data[J]. Mechanical Systems and SignalProcessing, 2016, 72/73: 303- 315.
[3] 周围, 梁琦. 非平稳信号实时谱分析算法及其FPGA实现[J]. 重庆邮电大学学报(自然科学版), 2018, 30(5): 633-641.
[4] 任学平, 李攀, 王朝阁, 等. 基于改进VMD与包络导数能量算子的滚动轴承早期故障诊断[J]. 振动与冲击, 2018, 37(15): 6-13.
[5] 王奉涛, 柳晨曦, 张涛, 等. 基于k值优化VMD的滚动轴承故障诊断方法[J]. 振动、测试与诊断, 2018, 38(3): 540-547.
Wang F T, Liu C X, Zhang T, et al. Rolling bearing fault diagnosis method based on k-value optimized VMD[J]. Journal of Vibration, Measurement & Diagnosis, 2018, 38(3): 540-547.
[6] Hoang D T, Kang H J. Rolling element bearing fault diagnosis using convolutional neural network and vibration image[J]. Cognitive Systems Research, 2019, 53: 42-50.
[7] 刘星辰, 周奇才. 一维卷积神经网络实时抗噪故障诊断算法[J]. 哈尔滨工业大学学报, 2019, 51(7): 89-95.
[8] 陈勇, 安汪悦, 刘焕淋, 等. 改进经验模态分解算法在光纤布拉格光栅周界入侵行为分类中的应用[J]. 中国激光, 2019, 46(3): 0304003.
[9] 陈勇, 陈亚武, 刘志强, 等. 基于光纤布拉格光栅传感的齿轮故障检测方法[J]. 中国激光, 2020, 47(3): 0304007.
[10] Nguyen D, Kang M, Kim C H, et al. Highly reliable state monitoring system for induction motors using dominant features in a two-dimension vibration signal[J]. New Review of Hypermedia and Multimedia, 2013, 19(3/4): 248-258.
[11] 赵呈锐, 金晓峰, 倪大成, 等. 基于塑料光纤和棱镜结构的光纤式转速传感器[J]. 重庆邮电大学学报(自然科学版), 2016, 28(3): 383-388.
Zhao C R, Jin X F, Ni D C, et al. Optical fiber rotational speed sensor based on plastic optical fiber and optical prism[J]. Journal of Chongqing University of Posts and Telecommunications (Nature Science Edition), 2016, 28(3): 383-388.
[12] Liu H L, Wang C J, Chen Y. An improved genetic algorithm for increasing the addressing accuracy of encoding fiber Bragg grating sensor network[J]. Optical Fiber Technology, 2018, 40: 28-35.
[13] Rauber T W, de Assis Boldt F, Varejão F M. Heterogeneous feature models and feature selection applied to bearing fault diagnosis[J]. IEEE Transactions on Industrial Electronics, 2015, 62(1): 637-646.
[14] 郭翠娟, 李德冲, 荣锋, 等. 基于最大相关波形延拓改进的EEMD方法[J]. 重庆邮电大学学报(自然科学版), 2017, 29(6): 768-775.
Guo C J, Li D C, Rong F, et al. An improved EEMD method based on maximal correlation waveform extension[J]. Journal of Chongqing University of Posts and Telecommunications (Nature Science Edition), 2017, 29(6): 768-775.
[15] Lee D S, Chang C S, Chang H N. Analyses of the clustering coefficient and the Pearson degree correlation coefficient of chung's duplication model[J]. IEEE Transactions on Network Science and Engineering, 2016, 3(3): 117-131.
[16] 张龙, 毛志德, 杨世锡, 等. 基于包络谱带通峭度的改进谱峭度方法及在轴承诊断中的应用[J]. 振动与冲击, 37( 23): 179- 187.
ZhangL, Mao ZD, Yang SX, et al. Improved spectral kurtosis method based on envelope bandpass kurtosis and its application in bearing diagnosis[J]. Journal of Vibration and Shock, 37( 23): 179- 187.
[17] Sun J H, Xiao Z W, Xie Y X. Automatic multi-fault recognition in TFDS based on convolutional neural network[J]. Neurocomputing, 2017, 222: 127-136.
[18] SabourS, FrosstN, Hinton GE. Dynamic routing between capsules[C]∥31st Annual Conference on Neural Information Processing Systems, December 3-8, 2018, Long Beach, CA, USA. New York: Curran Associates, 2017: 3857- 3867.
[19] Gao R Q, Yang F W, Yang W M, et al. Margin loss: making faces more separable[J]. IEEE Signal Processing Letters, 2018, 25(2): 308-312.
[20] Smith W A, Fan Z Q, Peng Z X, et al. Optimised spectral kurtosis for bearing diagnostics under electromagnetic interference[J]. Mechanical Systems and Signal Processing, 2016, 75: 371-394.
[21] 龚华平, 杨效, 屠于梦, 等. FBG传感器和电阻应变仪的振动监测特性[J]. 红外与激光工程, 2013, 42(3): 810-813.
Gong H P, Yang X, Tu Y M, et al. Vibration detection characteristics of FBG sensor and resistance strain gauge[J]. Infrared and Laser Engineering, 2013, 42(3): 810-813.
[22] Kingma DP, Ba J. Adam: a method for stochastic optimization[EB/OL]. ( 2017-01-30)[2020-05-13]. https:∥arxiv.org/abs/1412. 6980.
[23] Huang R Y, Liao Y X, Zhang S H, et al. Deep decoupling convolutional neural network for intelligent compound fault diagnosis[J]. IEEE Access, 2019, 7: 1848-1858.
[24] Zhang H, Huang Q, Li F W, et al. A network security situation prediction model based on wavelet neural network with optimized parameters[J]. Digital Communications and Networks, 2016, 3: 139-144.
Article Outline
陈勇, 安汪悦, 刘焕淋, 陈亚武. 利用FBG传感信号诊断滚动轴承故障的检测方法[J]. 中国激光, 2020, 47(11): 1104004. Chen Yong, An Wangyue, Liu Huanlin, Chen Yawu. Detection Method Using FBG Sensing Signal to Diagnose Rolling Bearing Fault[J]. Chinese Journal of Lasers, 2020, 47(11): 1104004.