基于投影条纹级次识别的发动机叶片三维测量方法
下载: 878次
ing at the precision measurement problem of the profile of aero-engine blades, a measurement method based on projected fringe order identification is presented. Firstly, a three-dimensional measurement system with composite structured light is designed and the rotation axis of the system is calibrated by the method of center circle fitting. Then, the aero-engine blades are measured by the digital fringe projection method. In the process of phase unwrapping, the projected fringe order is recognized by projecting two-dimensional code pattern combined with binocular vision, and the front and back surfaces of the blade are reconstructed respectively. In the process of point cloud data stitching, a three-dimensional stitching method combining rotating axis with iterative closest point algorithm is proposed. The experimental results show that the method does not rely on feature extraction and effectively solves the problem of insufficient surface features on aero-engine blades. Which can realize fast and accurate three-dimensional reconstruction of aero-engine blades.
1 引言
航空发动机是民航客机重要的组成部件,其加工精密程度直接影响着民航客机的飞行性能、安全性和经济性。航空发动机叶片在航空发动机中分布广泛且数量和种类很多,包括压气机静子叶片、压气机转子叶片、涡轮静子叶片和涡轮转子叶片等。航空发动机叶片的工作环境恶劣、叶片型面复杂、尺寸跨度大且需要在复杂的应力负载和微振动状态下工作[1-2]。随着对民航安全运行要求的日益提升,建立精确的叶片三维模型对发动机维修及相应的质量监控过程均变得极为重要。
对航空发动机叶片的测量从方法上可以分为接触式测量和非接触式测量[3]。接触式测量(如三坐标测量机等)通过探头与物体直接接触进行逐点式测量,测量精度高但测量效率低,且可能对被测表面产生损坏。非接触式测量主要通过采集经由被测表面调制的物理信号对被测表面进行还原,其中基于光学原理的结构光三维测量方法越来越受到重视。相比于传统测量方法,非接触式测量不接触被测物体的表面,避免了对所测物体的损伤,且极大地缩短了测量时间,提高了检测效率[4]。因而在工业检测中得到了广泛的应用。
从国外来看,Ukida等[3]提出了采用彩色光立体扫描的三维轮廓测量技术;Barone等[5]提出了一种基于光学扫描仪的多视图三维形貌测量方法;Hu等[6]提出了一种基于投影条纹模式偏移估计的三维轮廓术;Kawasaki等[7]提出了一种采用单一结构光模式的动态场景形状重建方法。从国内来看,针对航空发动机叶片三维信息的测量,很多重点实验室都进行了深入的研究。陆军等[8]通过基于格雷码和线移编码的结构光系统进行三维测量,并提出了此系统较高精度的标定方法;戴士杰等[9]提出了纵向分段非均匀正弦条纹生成算法,通过生成非均匀条纹改善了像素-相位的非线性关系;赵磊[10]提出一种基于测杆姿态的运动学反解算法,通过采用Revo测头对整体叶盘进行测量;于霞等[11]设计研制了一种尺寸小、灵敏度高的差激励涡流检测探头,利用总体平均模态经验模态分解技术和小波变换相结合的方法来有效抑制背景噪声,提取信号特征,并结合支持向量机方法实现裂纹缺陷的分类;孔玮琦等[12]提出的基于一般成像模型的标定方法,可以实现微小物体的三维重构。
表 1. 两种模型拟合结果误差比较
Table 1. Error comparison of fitting results of two models
|
2 结构光三维重建系统
2.1 系统整体设计
设计所搭建的结构光三维重建系统主要包括三个模块:运动控制模块、图像采集模块以及上位机系统。
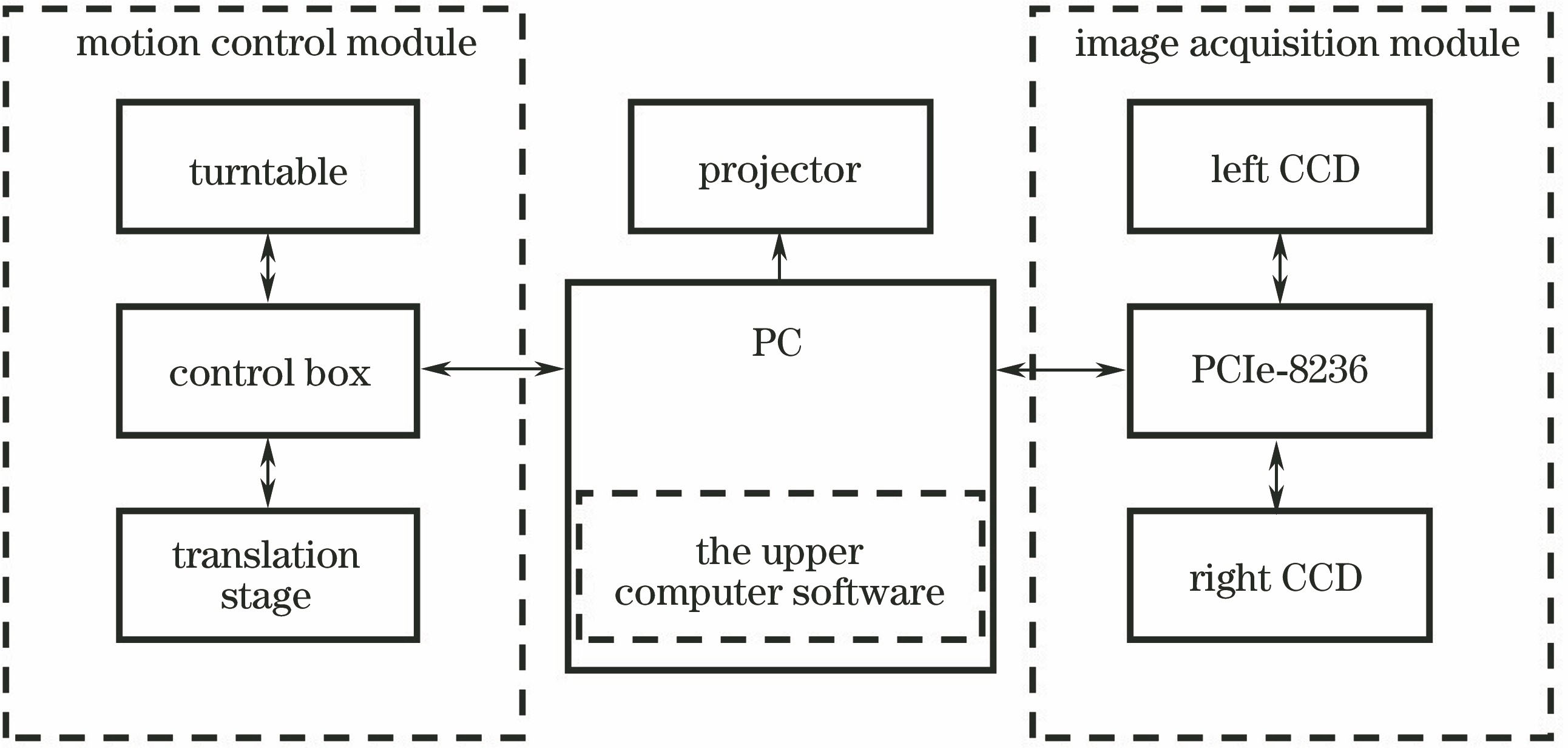
图 1. 结构光三维重构系统结构图
Fig. 1. Structure diagram of structured light three-dimensional reconstruction system
由
运动控制模块的设备包括由北京卓立汉光仪器有限公司生产的型号为MC600的电动控制箱一台、型号为KSA400-12-X的电动平移台一台和型号为RAuK100的电动旋转台一台。为了避免外界震动对实验的影响,整个系统放置于由北京卓立汉光仪器有限公司生产的型号为ZVB15-10的气浮隔振台上,以实现对待测物体运动的精确控制。
图像采集模块包括德国Basler公司生产的型号为acA1300-30gm的以太网相机两个,型号为PCIe-8236(NI 公司)的图像采集卡一张,型号为M115HD(DELL公司)的数码光处理(DLP)投影仪一台,该模块可实现对相机的控制及图像采集的过程。
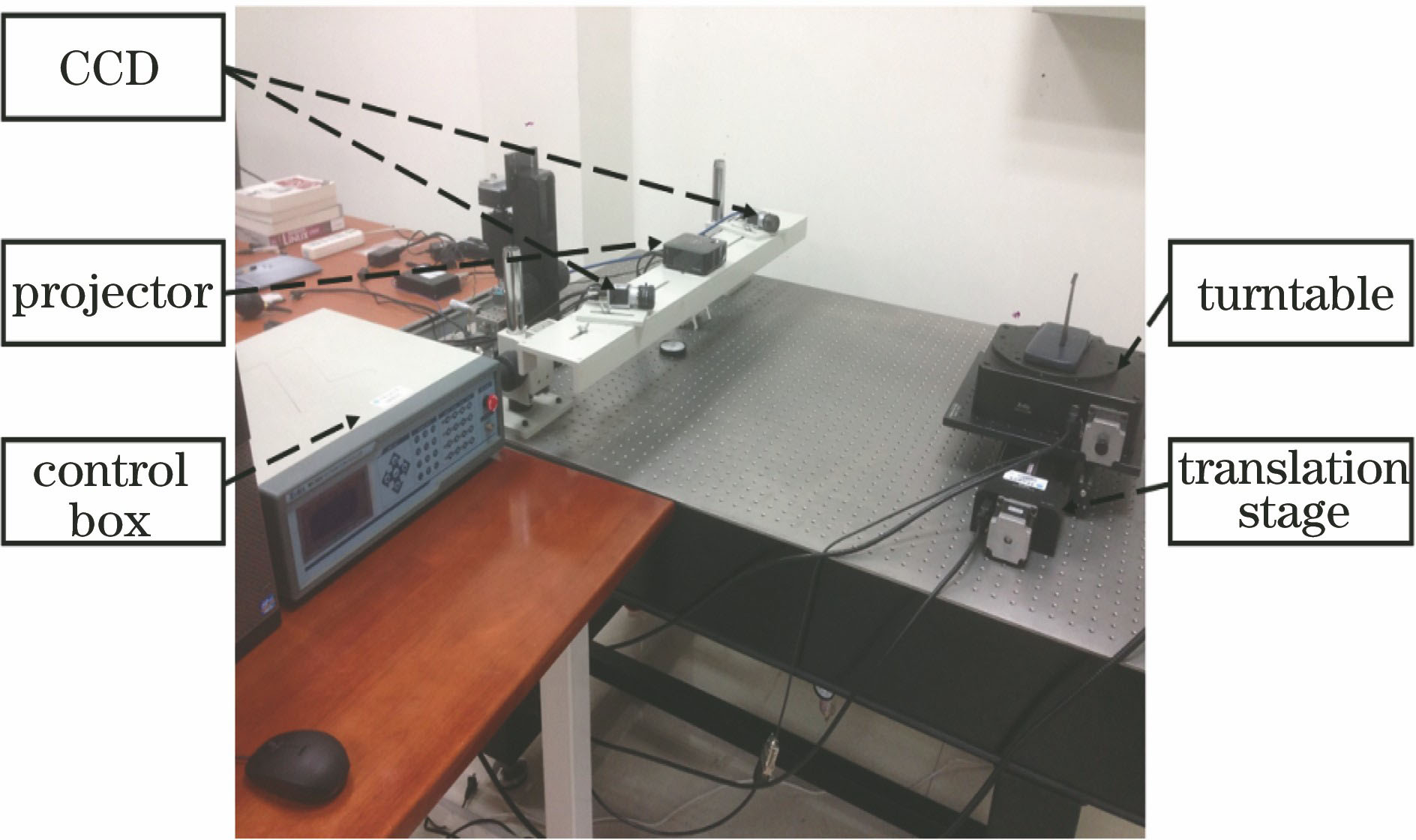
图 2. 结构光三维重构系统实物图
Fig. 2. Object graph of structured light three-dimensional reconstruction system
的上位机软件包括三个模块:图像采集模块、运动控制模块和数据处理模块。整个上位机系统基于LabVIEW进行编写,其中数据处理模块中的数据处理算法在Matlab中实现,该模块由LabVIEW与Matlab混合编程。结构光三维重建系统的上位机软件主要实现两个部分的功能:一是对标定和测量图像采集过程的控制,使得图像采集过程更为方便;二是对所采集到的图像进行处理并显示结果。
2.2 结构光三维重构系统标定
2.2.1 摄像机参数标定
摄像机的参数标定主要是标定单个摄像机的内外参数。摄像机的基本成像模型为小孔成像模型,该模型主要包含4个坐标系:图像坐标系(
式中
实验采用的标定方法为张正友棋盘标定法[14],假设棋盘所在平面处于世界坐标系下
由(2)式可知,通过采集图像可以得到像素坐标系下加点坐标(
2.2.2 条纹投影系统标定
条纹投影三维测量方法通过同一像素点相位变化值得到该点高度信息[15]。实验投射均匀条纹投影,需要对图像上所有点进行标定,标定目的是为了建立物体的高度信息和图片上相位差之间的关系。由于透视投影矩阵
实验选用的是一种不要求系统满足光心连接线平行于参考面的约束条件,对投影仪与摄像机位置没有特定要求,只需确保投射至参考平面的光栅条纹之间相互平行,简化了系统校准过程[15]。由于摄像机和投影仪之间的距离和摄像机到标准平面的距离这两个结构参数会对三维测量系统的测量精度造成影响,因此为了得到较高的测量精度,系统硬件的摆放需要满足一定要求:标准平面处于摄像机对焦良好的范围内以保证采集图像的有效性,且保证投射到标准平面的光栅条纹节距大小合适;摄像机与投影仪距离不可过远,两光轴夹角不可过大,以保证投射到待测物表面光栅条纹节距相近,防止部分过宽影响细节测量,也防止部分过窄降低信号采样率和信噪比。在实验中,摄像机和投影仪之间的距离约为0.3 m,摄像机到标准平面的距离约为0.9 m,保证了测量系统对图片采集质量的要求。
如
根据几何关系,高度
(4)式表明高度
(4)与(5)式均为理论关系式,但由于实际测量中摄像机和投影仪的聚焦均处于一定参考范围内,参考面以外的地方会出现不同程度的离焦现象。距离参考面越远,离焦现象越明显,此时高度的倒数和相位差的倒数的关系并非线性关系,可用二次曲线(称为多项式模型[16])表示为:
分别用(4)式和(6)式进行标定。标定过程为:选定初始面为标准平面,将白板沿着摄像机
分别以三角光路模型进行非线性拟合和以多项式模型进行多项式拟合,以采集图像上坐标为(125,134)的点为例,
2.2.3 旋转轴标定
基于组合结构光的三维测量方法一次只能获得被测物体某一个视角的三维信息,要想获取其360°
表 1. 两种模型拟合结果误差比较
Table 1. Error comparison of fitting results of two models
|
面形信息,必须采集不同视角的信息,并对结果进行拼接融合[17]。
为了进行完整表面的测量,实验选择通过旋转平台控制叶片进行精确旋转,以得到前一次测量中未能测到的点云数据。因此,除了需要标定光学成像系统的基本参数外,还必须对旋转台的旋转轴进行标定[18]。
对旋转轴的标定主要思路为:让棋盘标定板随着电动旋转台转动,电动旋转台每次旋转相同的角度,用通过摄像机拍摄每个位置的图片。通过这些图片对张正友标定法,可以得到棋盘标定板上角点的三维坐标。通过对每个角点拟合圆心,则可以得到一系列在旋转轴上的点。通过对这些点拟合直线,则可以得到旋转轴方程。实验将棋盘标定板放置于旋转台上,旋转台每次逆时针旋转15°。
旋转轴的初始法向量通过对每张图片的角点进行平面拟合,将其各自法向量再进行平面拟合,所得到的法向量即为旋转轴初始法向量。为了对圆心进行拟合,先将相机坐标系下各角点坐标转换为
3 基于条纹识别的叶片三维测量
3.1 连续相位图的获取
连续相位图的获取主要包括两个步骤:四步相移法解相位和相位解包裹。相移法通过向物体投射多幅具有固定相位差的条纹图片,对同一像素点处进行解相位获得该点相位值。相移法需要投影三张或三张以上的条纹图像,为时间编码,采集速度慢,但测量精度高,因此广泛应用于物体的三维形貌测量[19]。本研究中条纹投影三维测量方法采用的是四步相移法进行包裹相位的提取。投射条纹的光强分布满足:
式中
通过对同一包裹相位进行解包裹比较两者结果。
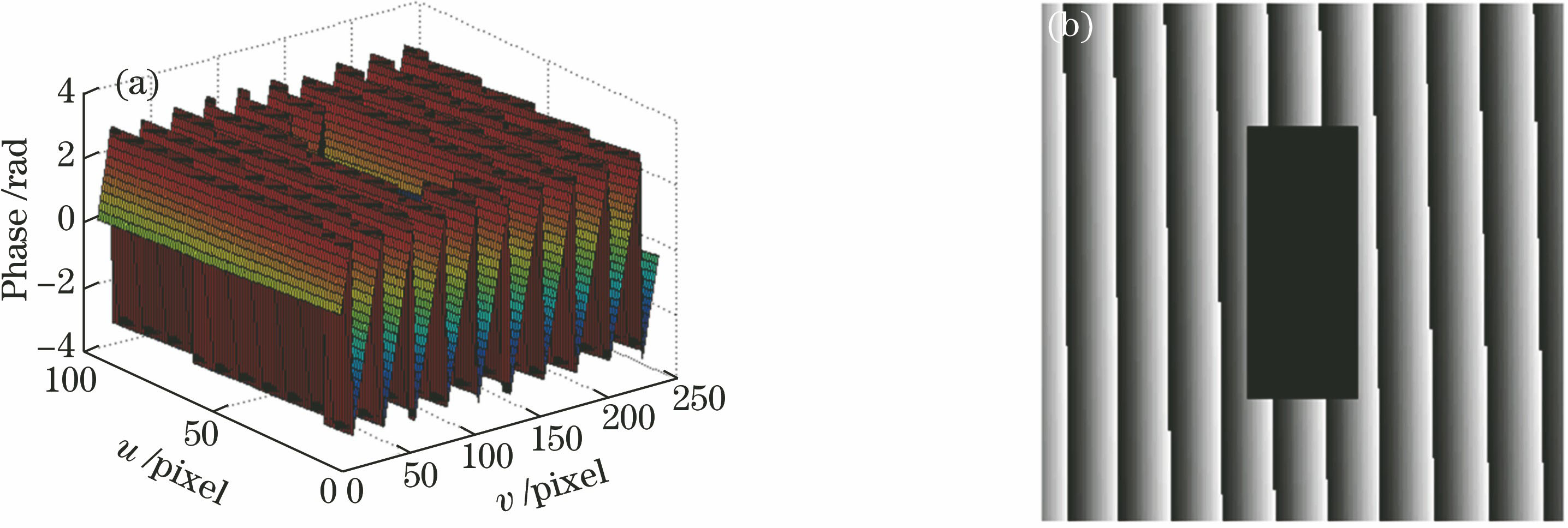
图 10. 非连续包裹相位的(a)像素点三维图像及(b)灰度图像
Fig. 10. (a) Three-dimensional form and (b) gray-scale form of discontinuous wrapping phase
3.2 基于双目视觉条纹识别的相位解包裹
由条纹投影系统的标定过程可知,还原高度信息需要每个像素点处相位差值,该相位差值为解包裹连续相位值与标准相位值的差值。选取的相位解包裹初始点的位置不同,则得到的解包裹连续相位值也会不同。为了与标准相位值采用相同的标准,需要对解包裹连续相位值进行修正。
基于主动双目视觉的条纹识别的相位解包裹方法基本思路为:在对摄像机、投影仪和系统进行标定后,由于叶片表面特征不明显,故向其投影二维码图样,增加其表面特征。通过左右相机双目视觉还原特征点处三维坐标,转化到投影仪坐标系下,则可得到该特征点处对应的条纹级次。
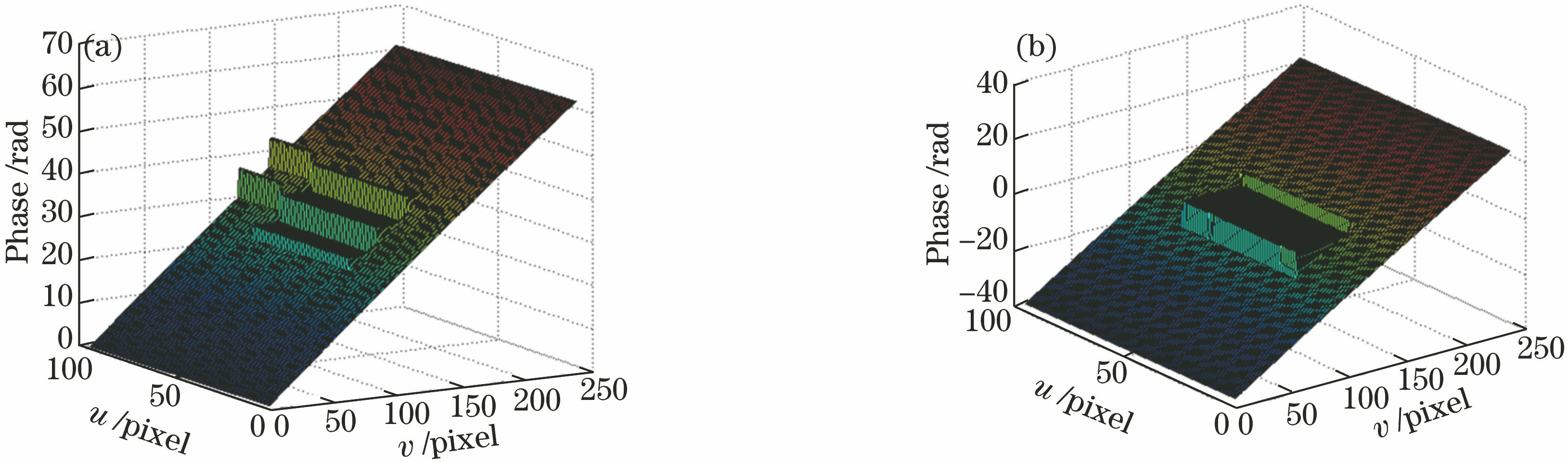
图 11. (a)使用行列逐点法的解包裹相位图;(b)使用基于质量图引导的非连续路径积分算法的解包裹相位图
Fig. 11. (a) Unwrapping phase diagram with the method of point by point; (b) unwrapping phase diagram with discontinuous path integral algorithm based on quality graph guidance
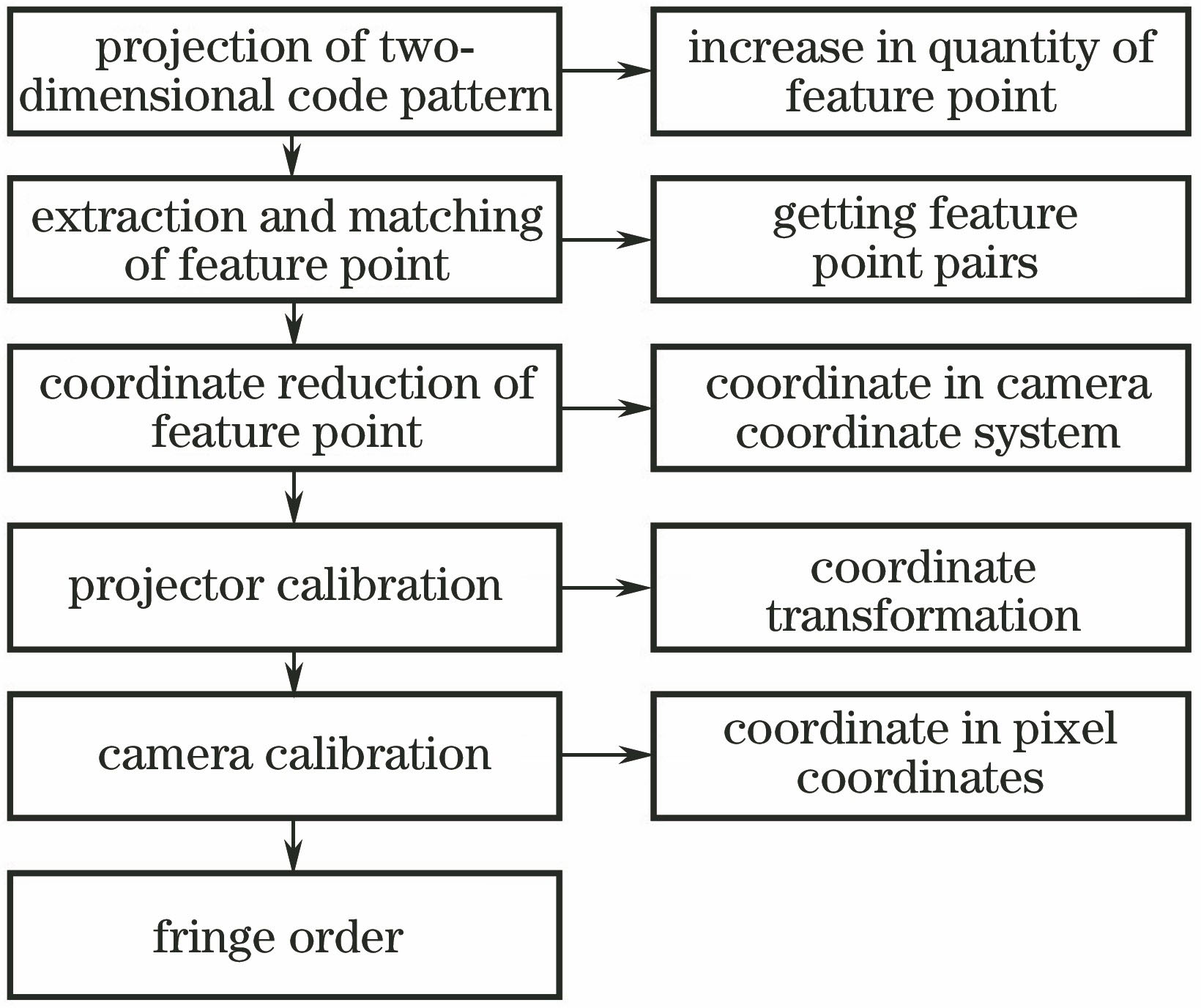
图 13. 基于主动双目视觉的条纹识别方法流程图
Fig. 13. Flow chart of stripe recognition method basedon active binocular vision
假设像素点
通过基于主动双目视觉的条纹识别方法,可以获得特征点
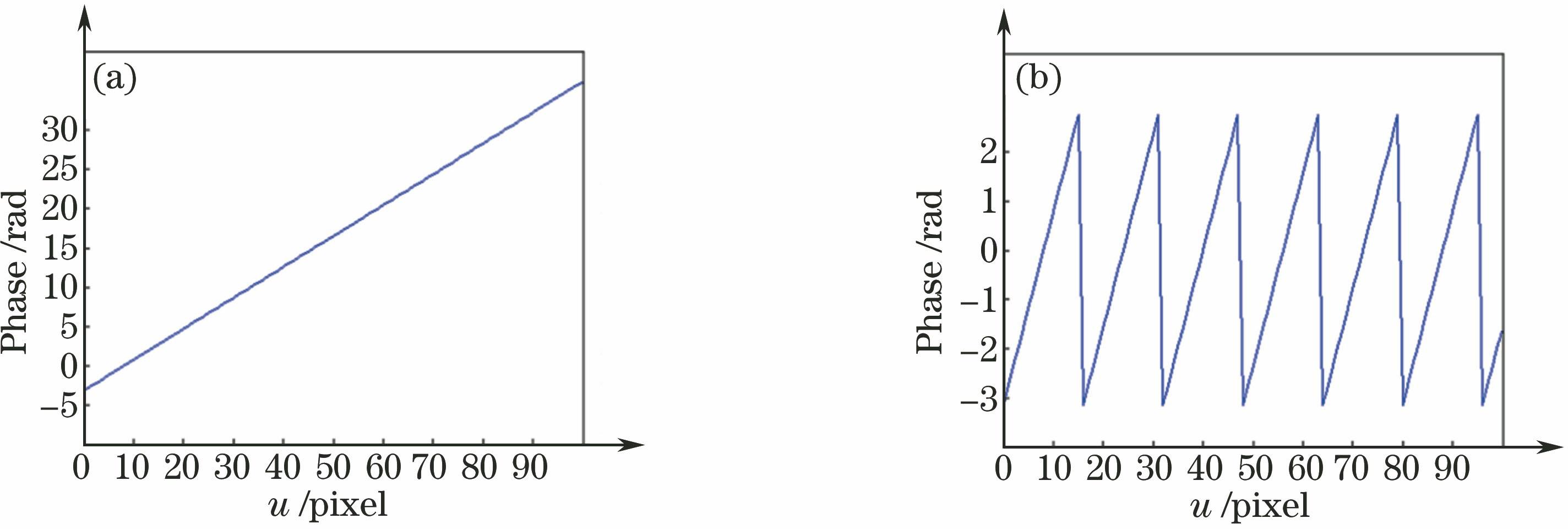
图 14. P点相位随u的变化趋势图。(a)真实相位的变化规律;(b)包裹相位的变化规律
Fig. 14. Trend of the phase of point P with the change of u. (a) Change law of real phase; (b) change law of wrapped phase
假设
假设与
假设
可得到
由(15)式可知,与
3.3 叶片点云数据拼接
由于条纹投影三维测量方法为面结构光测量方法,只能获得物体单侧表面的点云数据。为了得到叶片的三维形貌,需要通过旋转台控制叶片进行旋转,分别获取两面的叶片数据,需要对两面的叶片点云数据进行拼接。为了解决点云数据拼接的问题,实验采用旋转轴旋转与迭代最近点算法相结合的方法。
2.2.3节对旋转轴进行了标定由旋转轴方程可以将一组点云数据与另外一组点云数据进行初步拼接。迭代最近点算法以欧氏距离为迭代判据,通过多次迭代获取最优解,进行精确拼接。设两组具有
寻找旋转矩阵
对平移向量
该问题可以转化为求解使
迭代最近点算法所进行拼接的点集为叶片前后两面相连接的轮廓线,通过连通区域提取算法对其轮廓线进行提取。
4 实验结果及分析
4.1 系统测量精度标定
实验对标准量块进行测量,得到了组合结构光三维测量系统的精度。标准量块是通过两个平行的工作面之间的距离作为基准,来验证测量方法的精密程度。实验所用标准量块由哈尔滨量具刀具集团有限责任公司生产,规格为75 mm×35 mm×1 mm,其中工作平面相距75 mm,将量块紧贴在标准平面上进行测量,比较量块高度与标准长度75 mm的差别。实验一共进行了10次测量。
实验采用四步相移法获取待测物体表面点的包裹相位,投影条纹图片是在Matlab软件中编制而成,图片尺寸为 1024 pixel×960 pixel,每幅图片包含64条条纹,
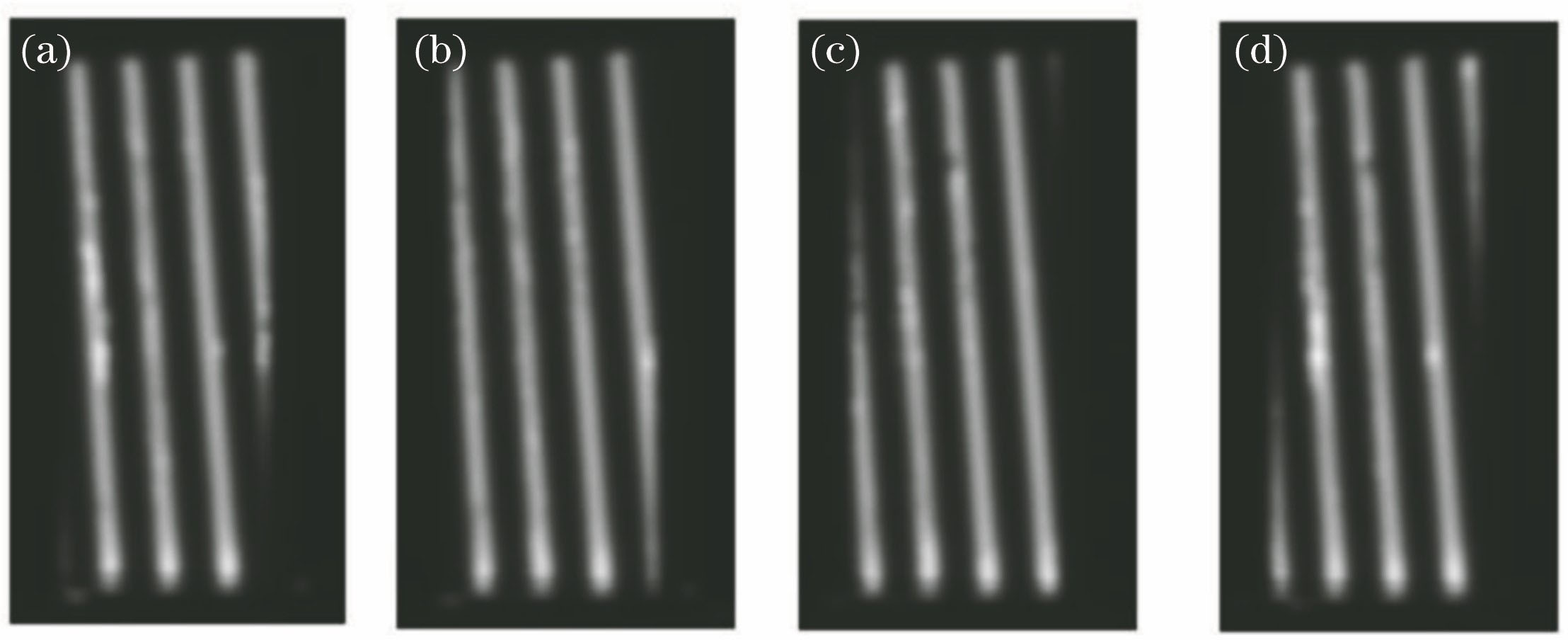
图 16. 标准量块表面投影条纹后所采图像。(a) 0相移;(b) π/2相移;(c) π相移;(d) 3π/2相移
Fig. 16. Images of standard measured mass surface with projected fringe. (a) 0 phase shift; (b) π/2 phase shift; (c) π phase shift; (d) 3π/2 phase shift
由双目识别获取的图像上特征点在初步解包裹相位中的解包裹相位值之差,可以得到各匹配点之间条纹级数差。
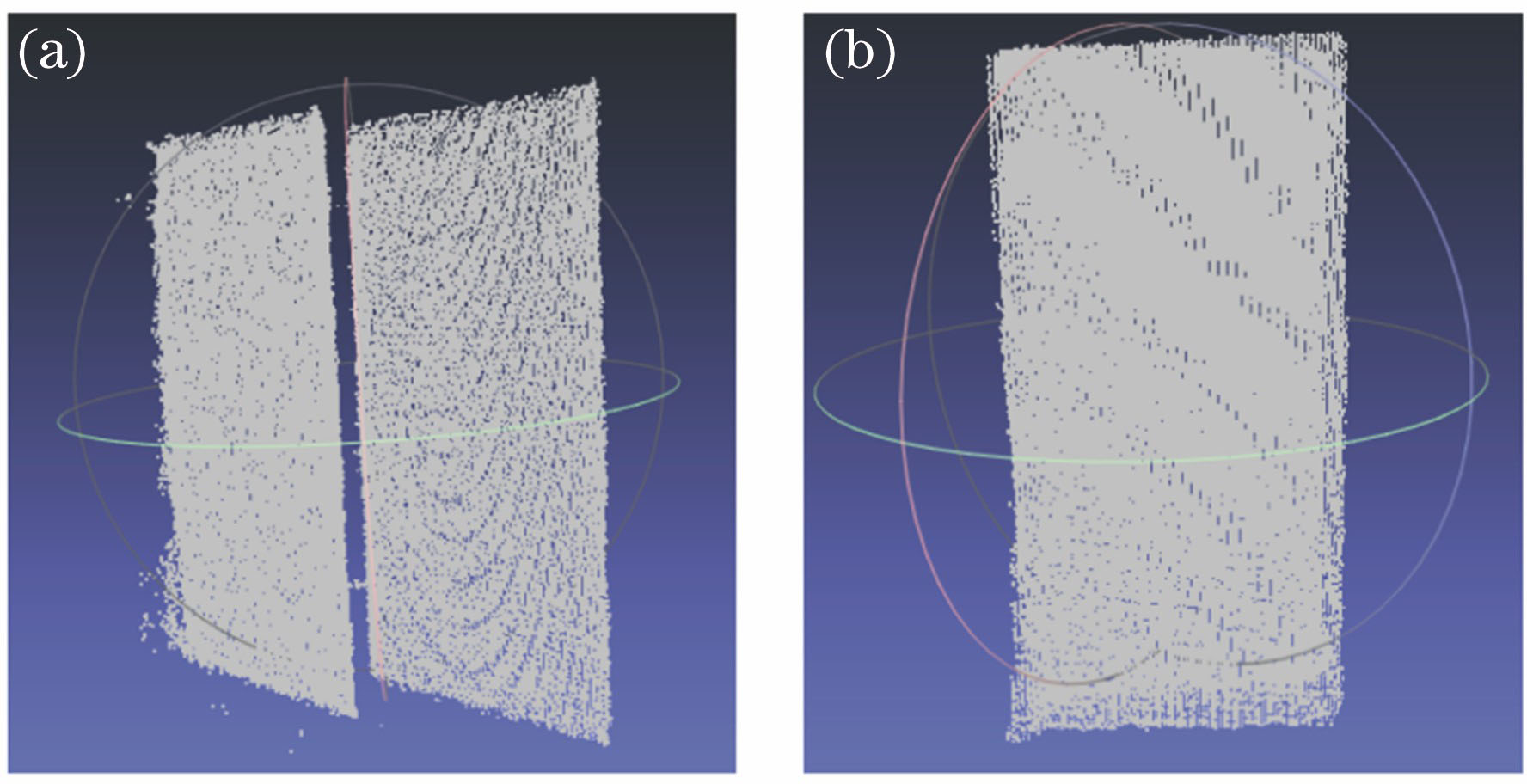
图 17. 标准量块(a)初始还原结果和(b)拼接还原结果
Fig. 17. (a) Initial restoration result and (b) stitching restoration result of standard measured mass
4.2 发动机进口导向叶片测量
实验对航空发动机进口导向叶片进行了测量,
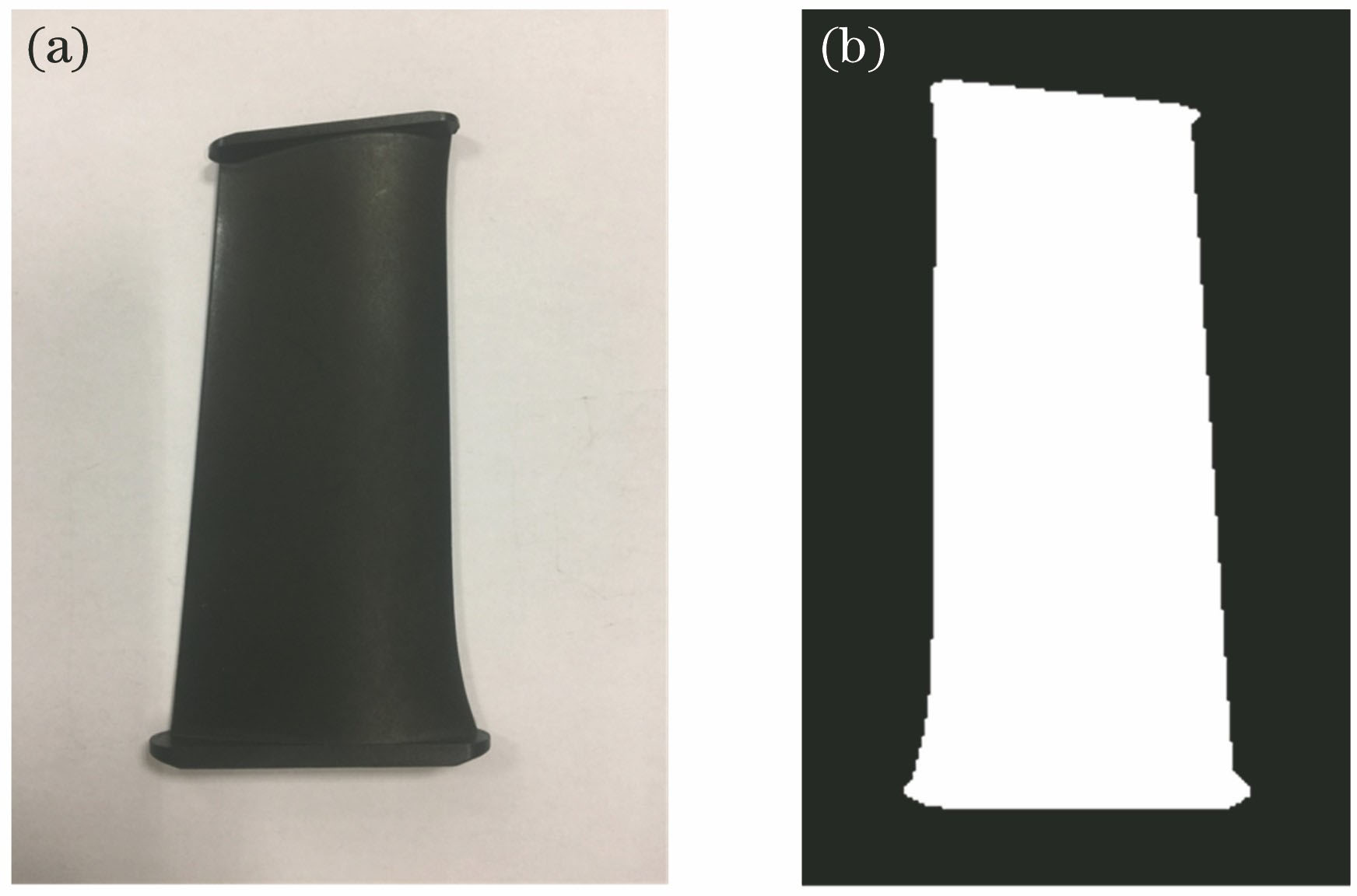
图 18. (a)进口导向叶片实物图;(b)叶片区域提取结果
Fig. 18. (a) Physical map of inlet guide vane; (b) extraction result of the area of vane
通过双目视觉对条纹级次进行判断后,对
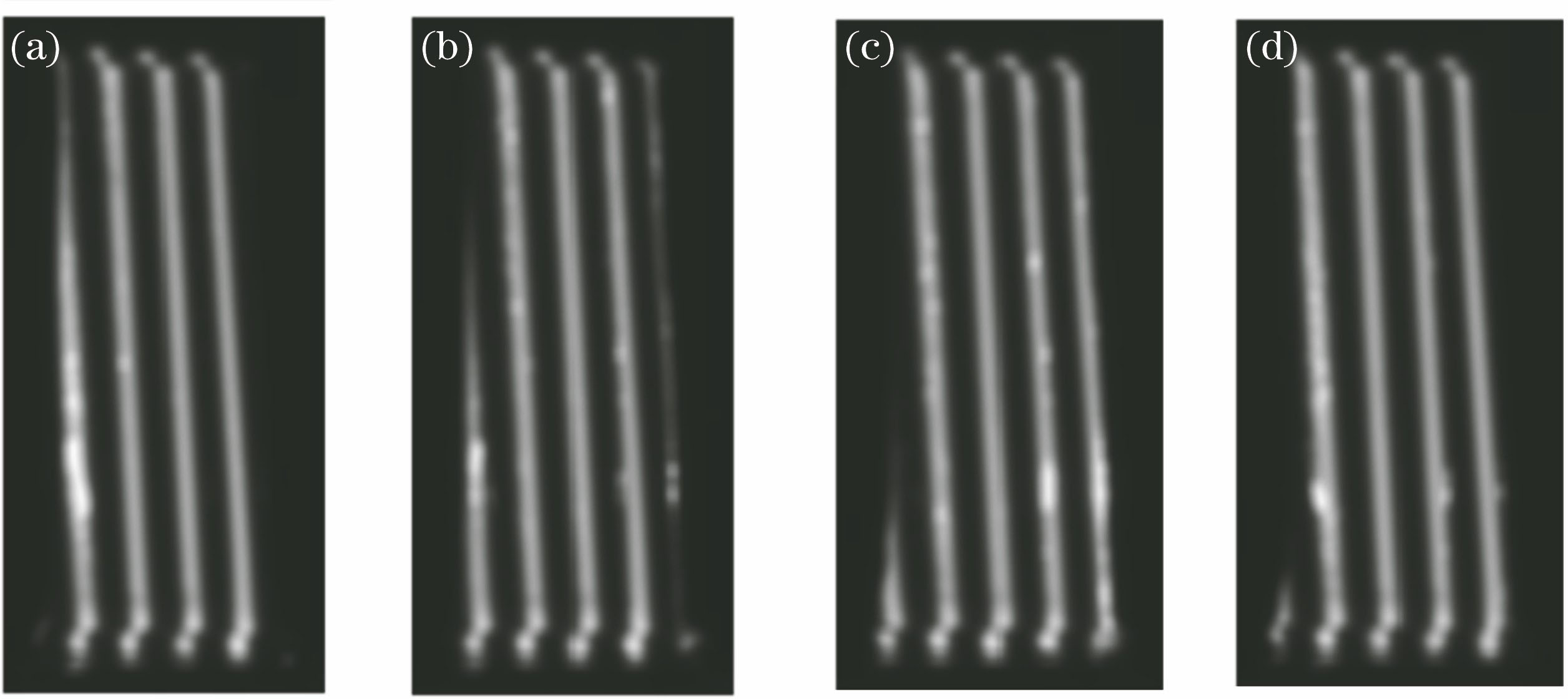
图 19. 进口导向叶片表面投影条纹后所采图像。(a) 0相移;(b) π/2相移;(c) π相移;(d) 3π/2相移
Fig. 19. Images of inlet guide vane surface with projected fringe. (a) 0 phase shift; (b) π/2 phase shift; (c) π phase shift; (d) 3π/2 phase shift
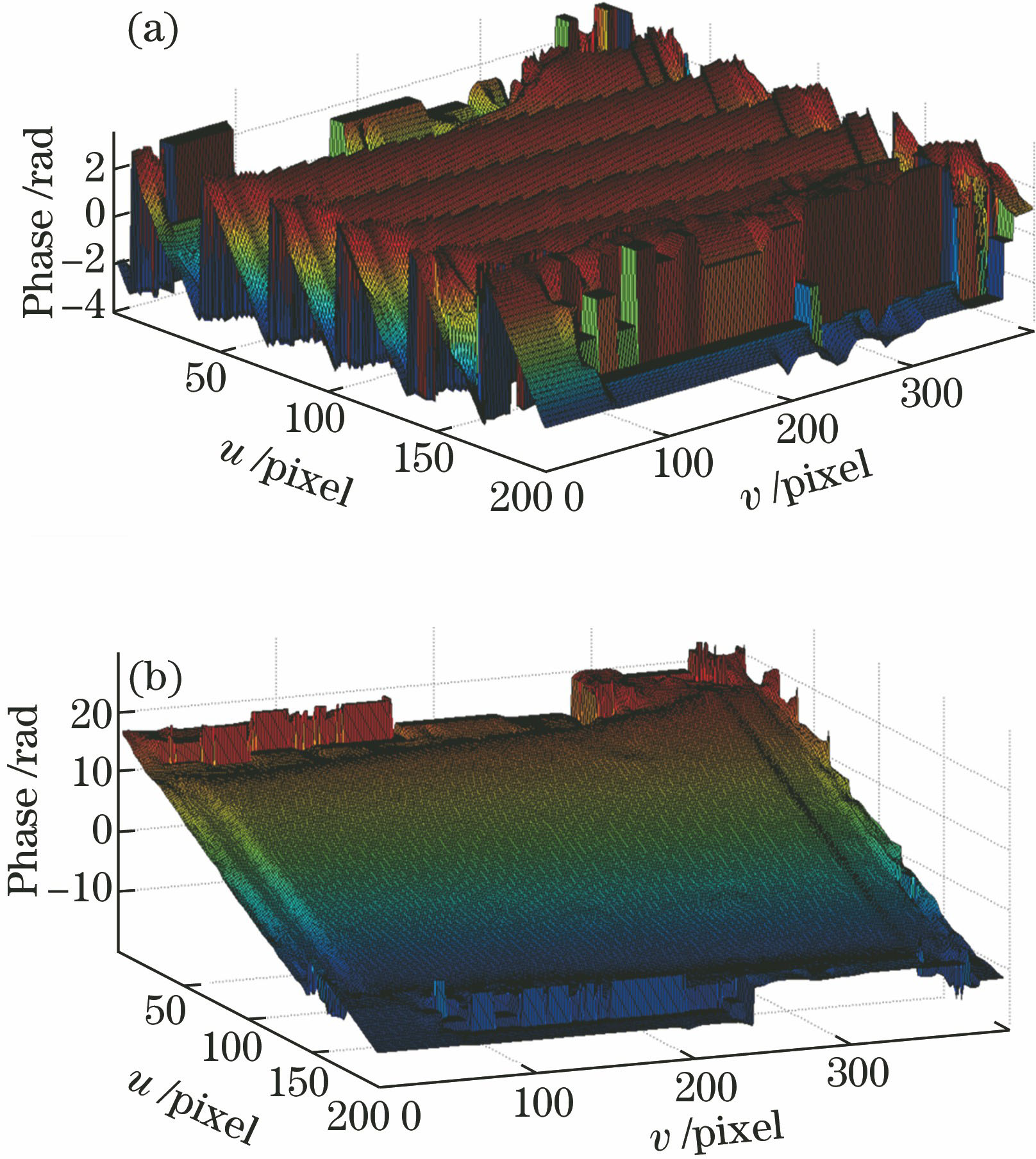
图 20. 进口导向叶片表面的(a)包裹相位值和(b)解包裹相位值
Fig. 20. (a) Wrapped phase and (b) unwrapped phase on inlet guide vane surface
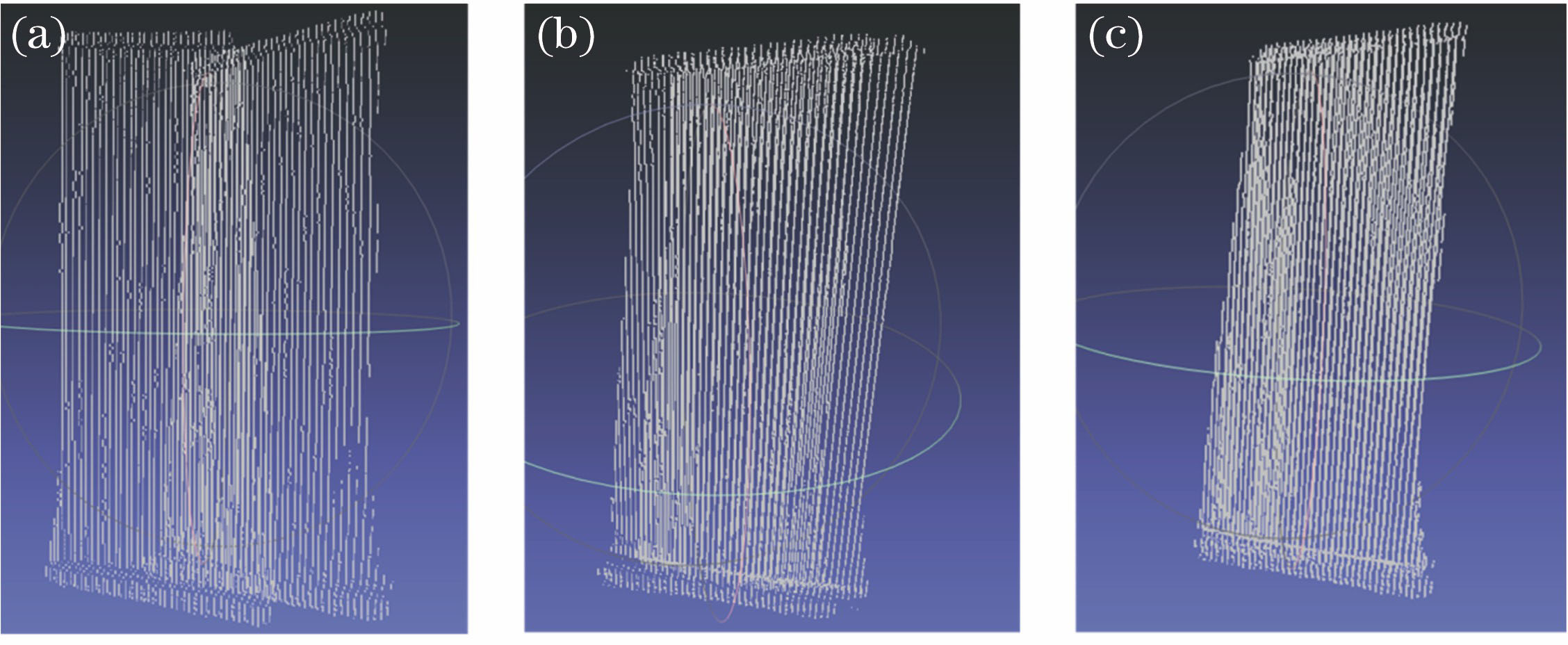
图 22. 进口导向叶片的(a)初始还原结果、(b)初步拼接还原结果和(c)迭代最近点算法拼接结果
Fig. 22. (a) Initial restoration result, (b) preliminary stitching restoration result and (c) stitching result using the iterative nearest point algorithm of inlet guide vane
5 结论
针对发动机叶片的三维测量与拼接问题,提出了一种基于条纹投影级次识别的发动机叶片三维测量方法。通过投射二维码与主动双目视觉的方法,实现投影条纹级次的判别,并对获取的解包裹相位进行周期校正;对获取的面形信息通过旋转轴标定与迭代最近点算法相结合的方式,实现了精度高于0.08 mm的三维测量,将其运用到叶片三维形貌的获取,得到了较好的结果,实验证明了本方法的可行性。但是由于航空发动机叶片对精度要求较高,通常需达到0.01 mm以上,因此尚存在不足。本方法为发动机叶片快速有效的检测做出了探索,后期工作将围绕进一步提高测量系统精度展开。
[1] 李妙玲, 朱春熙, 尤惠媛. 航空发动机叶片叶身型面测具设计及精度分析[J]. 制造技术与机床, 2011( 1): 113- 116.
Li ML, Zhu CX, You HY. Design and precise analysis of measuring tool for profiles of an aircraft engine blade working[J]. Manufacturing Technology & Machine Tool, 2011( 1): 113- 116.
[2] 陈志强, 张定华, 金炎芳, 等. 基于测量数据的叶片截面特征参数提取[J]. 科学技术与工程, 2007, 7(9): 1972-1975.
Chen Z Q, Zhang D H, Jin Y F, et al. Cross-sectional feature parameter extraction of blade based on measurement data[J]. Science Technology and Engineering, 2007, 7(9): 1972-1975.
[3] UkidaH, TakamatsuS. 3D shape measurements using stereo image scanner with three color light sources[C]. IEEE Instrumentation and Measurement Technology Conference, 2004, 1: 639- 644.
[4] 欧攀, 王婷, 李瑞祥. 一种基于结构光的牙齿三维测量系统[J]. 激光与光电子学进展, 2016, 53(1): 011102.
[7] KawasakiH, FurukawaR, SagawaR, et al. Dynamic scene shape reconstruction using a single structured light pattern[C]. IEEE Conference on Computer Vision and Pattern Recognition, 2008: 1- 8.
[8] 陆军, 宋成业. 基于格雷码和线移编码的结构光系统标定[J]. 光电子·激光, 2012, 23(6): 1146-1151.
Lu J, Song C Y. Structured light system calibration based on Gray code combined with line-shift[J]. Journal of Optoelectronics·Laser, 2012, 23(6): 1146-1151.
[9] 戴士杰, 易丹, 李伟超, 等. 分段非均匀条纹生成方法及其在双频解相位中的应用[J]. 红外与激光工程, 2015, 44(9): 2849-2853.
[10] 赵磊. 航空发动机整体叶盘的测量[D]. 天津: 天津大学, 2012.
ZhaoL. The measurement of aero engine blisk[D]. Tianjin: Tianjin University, 2012.
[11] 于霞, 张卫民, 邱忠超, 等. 基于涡流检测信号的航空发动机叶片缺陷分类与评估方法[J]. 测试技术学报, 2016, 30(2): 99-105.
Yu X, Zhang W M, Qiu Z C, et al. Study on classifying and evaluating defects of the aviation engine blade based on eddy current detection signals[J]. Journal of Test and Measurement Technology, 2016, 30(2): 99-105.
[12] 孔玮琦, 刘京南, 达飞鹏, 等. 基于一般成像模型的微小物体测量系统标定方法[J]. 光学学报, 2016, 36(9): 0912003.
[13] 达飞鹏. 光栅投影三维精密测量[M]. 北京: 科学出版社, 2011.
Da FP. Grating projection three-dimensional precision measurement[M]. Beijing: Science Press, 2011.
[14] Zhang Z. A flexible new technique for camera calibration[J]. IEEE Transactions on Pattern Analysis & Machine Intelligence, 2000, 22(11): 1330-1334.
[15] 安冬, 达飞鹏, 盖绍彦, 等. 新的基于条纹投影轮廓测量的系统标定方法[J]. 应用光学, 2014, 35(1): 81-84.
[16] 李健兵, 雷志辉. 位相测量轮廓术中的相位修正及系统标定的新方法[J]. 光学技术, 2006, 32(3): 422-424.
[17] 吴庆阳, 曾增, 张佰春, 等. 一种新的360°三维测量系统及标定技术[J]. 中国激光, 2017, 44(4): 0404002.
[18] 吴庆阳, 李景镇, 苏显渝, 等. 线结构光三维测量系统中旋转轴的标定方法[J]. 中国激光, 2008, 35(8): 1224-1227.
[20] 刘景峰, 李艳秋, 刘克. 一种新的质量图导引路径积分相位展开算法[J]. 光电工程, 2007, 34(12): 104-107.
Article Outline
马龙, 徐泓悦, 胡艳敏, 王建春, 黄超, 裴昕. 基于投影条纹级次识别的发动机叶片三维测量方法[J]. 激光与光电子学进展, 2018, 55(4): 041201. Long Ma, Hongyue Xu, Yanmin Hu, Jianchun Wang, Chao Huang, Xin Pei. Three-Dimensional Measurement Method of Aero-Engine Blades Based on Projected Fringe Order Identification[J]. Laser & Optoelectronics Progress, 2018, 55(4): 041201.