Demodulation method combining virtual reference interferometry and minimum mean square error for fiber-optic Fabry–Perot sensors
Download: 815次
Fiber-optic sensors have been widely employed for the advantages of simple structure, high sensitivity, freedom from electromagnetic interference, and suitability for harsh environments[1,2]. In recent years, fiber-optic high temperature sensors have received widespread attention. Various high temperature sensors based on long period fiber gratings (LPFG)[3], Fabry–Perot interferometers (FPI)[4,5], and fiber Bragg gratings (FBG)[2] are demonstrated. Because sapphire fibers have a very high melting point, which is the most important performance for the sensing applications at a very high temperature, a lot of Letters presented the sensors combined with Fabry–Perot (F-P) and sapphire fibers. But, the fringe contrast of the sensor output depended on many factors, such as the quality of the silica-to-sapphire fiber splice, the surface roughness of the fiber end, and the F-P surface, which are hard to control.
For obtaining the high precision and resolution of the measurement, a variety of demodulation methods have been developed to extract the cavity length of the F-P sensors accurately through different algorithms. The wavelength tracking method offers high sensitivity. However, it is limited to measuring only relative changes in the F-P cavity length, and the dynamic range is limited as well[6]. The fast Fourier transform (FFT) method is a classic method for cavity length demodulation and is widely used as the first step to obtain raw cavity length estimation. It transforms the signal from an optical wavelength domain to a cavity length domain and gives the raw absolute cavity length. The FFT method is fast, has a wide dynamic range, and is less affected by noise. However, the resolution is much lower than that of the wavelength tracking method[7], and the demodulating precision is limited by the optical frequency range. To circumvent these disadvantages, researchers have to find other algorithms for different experimental environments. Wang
However, the MMSE signal processing method has a serious drawback because there is a problem of “mode jumping” as the demodulated range becomes larger. The demodulated range of the MMSE signal processing method must be limited in one mode (240 nm in our system) to avoid the “mode jumping” problem. This requires that the resolution of the algorithm for obtaining the estimated cavity length be less than half of one mode (120 nm)[12]. Since the resolution of the FFT (over 1 μm) does not meet the requirement, because FFT does not take into account the chromatic dispersion of the F-P cavity, the result of the combined FFT-MMSE method has to be corrected manually.
In this Letter, we propose the use of virtual reference interferometry (VRI) for initial estimation of the cavity length, because it takes the dispersion into account. VRI has been used to measure chromatic dispersion in short fibers and components[13,14] and is capable of extracting first- and second-order dispersion directly from spectral interference (SI) patterns[13]. Our novel demodulating method combines VRI and MMSE for optical fiber F-P sensors. Furthermore, we fabricated an optical fiber F-P high temperature sensor based on a sapphire wafer and obtained the cavity length through the proposed method. The results show that the proposed method can effectively avoid the “mode jumping” problem and achieve the same high precision of MMSE.
The combined VRI-MMSE method includes two parts, i.e., the VRI and the MMSE algorithm. The former is used to obtain an approximate cavity length, and the latter is used to achieve a more exact cavity length.
The principle of VRI is shown in detail in Ref. [13]. A summary of the steps of the demodulating method of the combined VRI-MMSE is now presented. First, a SI pattern is obtained from an FPI. Second, a simulated interference pattern is generated numerically using a virtual reference path. Third, the simulated interference pattern is multiplied (point-by-point) with the real interference pattern to produce a second-order interference pattern. Fourth, the amplitude modulation of the second-order interference pattern is extracted and used it calculate the group delay
The schematic of our experimental system is shown in Fig.
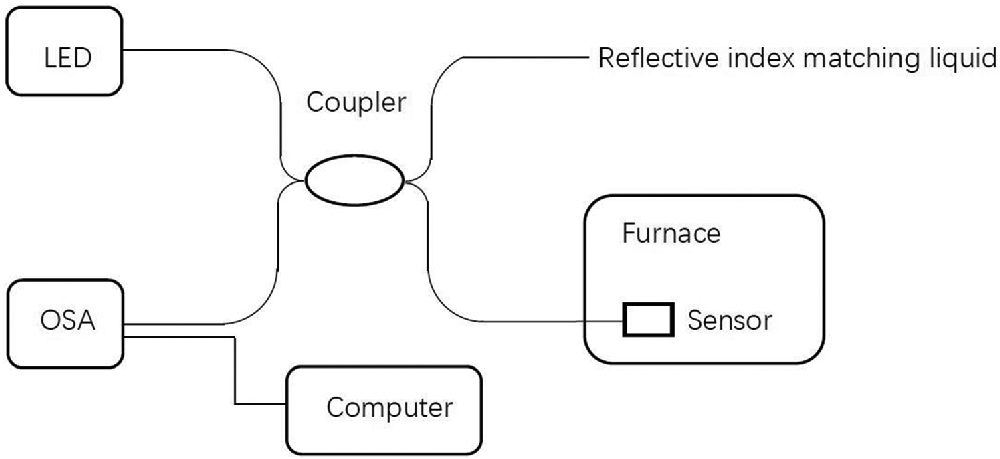
Fig. 1. Fiber-optic F-P high temperature sensing experimental system based on a sapphire wafer.
In order to evaluate the performance of the VRI-MMSE demodulating method, the system was tested for high temperature sensing. The F-P sensor was placed in the high temperature furnace, and its temperature was set to cover the range of from 28°C to 1000°C at an increment of 100°C. Each temperature was kept for half an hour to ensure a uniform temperature distribution. The measured interference spectra at 28°C, 100°C, and 200°C are shown in Fig.
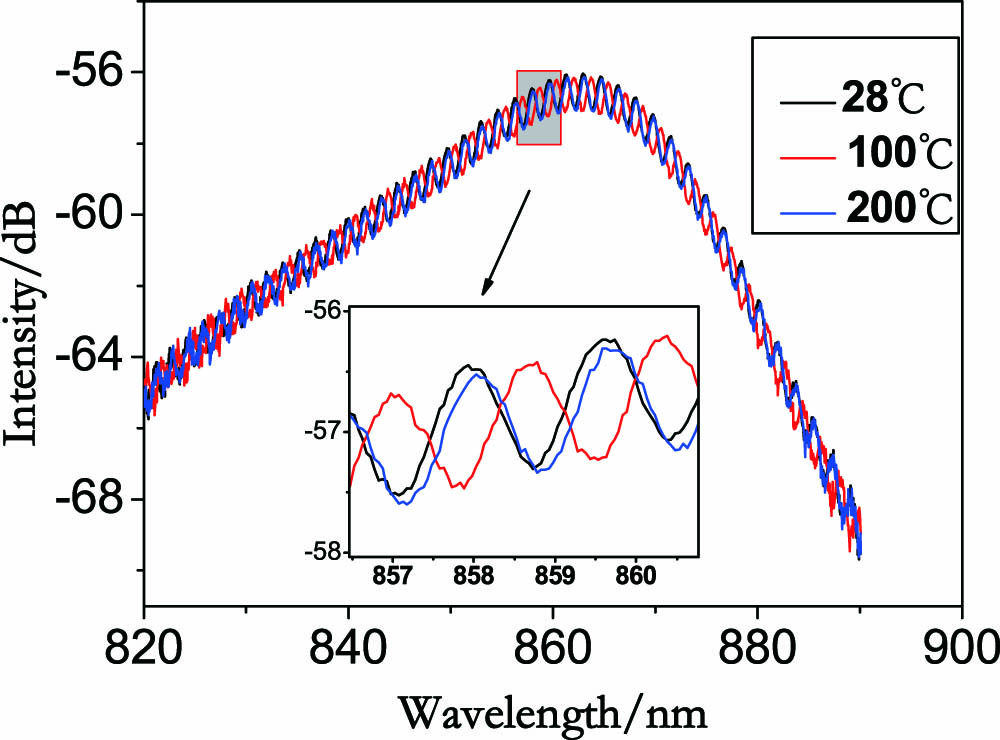
Fig. 2. (Color online) Interference spectra at the temperatures of 28°C, 100°C, and 200°C, respectively.
Figure

Fig. 4. (Color online) Group delay as a function of temperature at different wavelengths.
Figure

Fig. 5. (Color online) Corresponding cavity lengths decoded by the methods of VRI, MMSE, and VRI-MMSE.
The cavity length was measured experimentally at several temperature levels from 28°C to 1000°C. During the test, 44 spectra were recorded, and the standard deviation at each temperature step was calculated, as shown in Fig.
In conclusion, a demodulation method combining VRI and MMSE for a fiber FPI is proposed and demonstrated. By the high temperature testing experiment, the obtained resolution of the demodulating method is 4.2 nm. Integrating advantages of VRI and the MMSE-based signal processing method, this method achieves a high demodulation resolution and absolute measurement of the cavity length, while it uses VRI instead of FFT to eliminate the mode jump phenomenon of FFT-MMSE at the same time. The proposed method is a novel alternative technology of conventional F-P demodulation based on FFT.
[1]
[2]
[3]
[4]
[5]
[6]
[7]
[8]
[9]
[10]
[11]
[12]
[13]
[14]
Xinwang Gui, Michael Anthony Galle, Li Qian, Weilong Liang, Ciming Zhou, Yiwen Ou, Dian Fan. Demodulation method combining virtual reference interferometry and minimum mean square error for fiber-optic Fabry–Perot sensors[J]. Chinese Optics Letters, 2018, 16(1): 010606.