锂离子电池内温度场健康状态分布式光纤原位监测技术研究
下载: 1944次
1 引言
与其他化学电源相比,锂离子电池因其具有储存和循环寿命长、大倍率、高能量密度、环境污染低、工作范围广等显著优势,在新能源电动汽车、船舶、飞机、智能手机等领域拥有非常广阔的应用前景[1-3],已成为发展最为迅速的二次电池。但当锂离子电池应用于电动汽车等要求高容量和大体积电池的动力领域时,软包装锂电池高倍率充放电必然会连续释放出大量的焦耳热与化学反应热,在电池组集成系统中,大量热量在狭小空间内累积会引起热失控,此时工作过程中的产热和自身内部温度分布不均衡性的问题就不容忽略,因此研究锂电池在不同条件下充放电过程中的温度场分布十分重要[4-6]。
目前,国内外各研究团队大多采用电池热模型,结合数值仿真有限元技术对电池模块热效应进行研究。该模型由1980年代的Bernardi等根据电池内部实际电量,基于能量和物质的守恒定律建立,为后来电池模块热效应模拟提供了根本依据。电池充电放电过程包括各种电化学反应[7],即使是最好的理论模型也无法捕捉和预测由不可预测的操作、环境应力和制造缺陷等导致的退化和故障。目前电池管理系统(BMS)通常通过外部测量电压、电流、温度等参数,来估计电池的充电(SOC)状态和健康(SOH)状态,而由于电池物理和电化学变化的高度复杂性,物理模型在BMS中的应用受限。
当今动力电池的温度通常可通过热电偶、热敏电阻、光纤传感、红外热成像等检测方法进行实时监测,相关温度数据将被送入汽车的BMS进行处理及阈值判断,当发生热异常时BMS能够及时采取相应措施,如切断电源、启动冷却系统等。对于电池外部温度检测,Warwick大学的Fleming等[8]利用热电偶对大尺寸方形软包锂离子电池表面的16个不同温度点位置进行温度监测。Tesla作为当今世界电动汽车产业的领军者,其汽车电池组采用热敏电阻和光纤相结合的电池智能温度监测系统,每个电池单体电极都连接着一个热敏电阻(http:∥old.sensorexpert.com.cn/article/tesilaqichedianchizu_1.html.),各电池侧壁或附近都布设有一系列的监测光纤,同时将热敏电阻连接到电池监控器,将监测光纤连接到光敏感应器。当某个电池单体温度超过安全标准时,热敏电阻将产生一个电信号传至电池监控器,启动电池冷凝系统,以保证电池安全性能(https:∥www.ofweek.com/auto/2014-06/ART-70105-11000-28986810_3.html)[9]。当电池发生热逃逸等现象时,将导致光纤中光束的传输发生强度衰减或频移,激发光敏感应器发出相应信号,进行热度调节[10]。基于实验室数值模拟仿真得到的结果[11-12]可知,电池内外部差异可能相当大,故当前采用热模型与外部温度检测相结合的BMS存在局限性。
光纤传感器具有轻巧、外形薄、电绝缘性、抗静电放电、抗电磁干扰以及能高灵敏度分布式测试多参数(如温度、应变、压力和化学成分)的优点。光纤传感器已被证明对多种恶劣环境的稳健性[13],某些材料的光纤传感器根据之前的实验证明可以在各种酸性条件下发挥功效,如锂电池中的氟化氢溶液(HF)[14]。光纤传感器最常用的材料是耐腐蚀的二氧化硅,可工作于-200~800 ℃下[15],可长期承受拉应力高达1 GPa[16],其介电击穿强度>470 kV/mm[17],因此它非常适合用作嵌入锂离子电池的传感器。2017年,美国阿尔托研究中心Ganguli等[18]提出了一种利用热密封材料填充间隙来密封嵌入软包电池中光纤布拉格光栅(FBG)的方法,并对电池的内应力、温度进行监测,估计了电池的SOC状态。2018年,英国Warwick大学的Torres等[19]利用在光纤和铝表面涂覆氟化乙烯-丙烯热收缩膜,并将裸纤穿过作为应变保护层的铝管的方法,对圆柱锂电池进行内部热传感。2019年,武汉理工大学的徐一旻等[20]将密集型光纤光栅贴合在圆柱状汽车动力电池的正极上进行温度监测,并反馈给BMS。为了能更好地实时表征电池组件运行的健康状态,需要采取更直接的原位检测方法来对每个电池单体组件内温度场进行全面的测量和表征。
本文面向未来汽车、航空航天等先进制造领域对大尺度锂离子电池集成组件健康状态原位监测的重大应用需求,提出和设计了一种锂离子电池内温度场健康状态的分布式光纤原位监测方法。采用合理的密封埋入方法将光纤FBG温度传感器埋入锂电池内部,在理论和实验上实现了不同运行环境下锂离子电池内温度场的分布状态和演化规律的分布式实时监测。为实现高精度监测电池内每点的温度变化,一般需要集成上百个光纤传感器,而本研究结合热模型仿真选取3个特征温度点优化了传感器的布设位置与传感器使用量,在准确实现各种情况下温度场准确测量表征的同时,降低了前期传感器布设工艺的难度与后期海量数据解调的成本,获得最高性价比。该方法克服了当前锂离子电池组外表面温度检测的局限性,具有分布式多点同时监测、成本低的优点,可为未来大尺度锂离子电池集成组件健康状态的预警和评估提供参考。
2 原理和分析
2.1 锂离子电池结构及产热原理
2.2.1 锂离子电池结构及工作原理
如
2.2.2 锂离子电池单体温度场模型分析
由锂离子电池工作原理可知,电池在锂离子动力电池充放电过程中的温度变化主要是由充放电过程中产生的热量所致。实际生热量主要是由化学反应热Qr、极化反应热Qp、欧姆热Qj和电解质分解产生的副反应热Qs组成,表达式为
采用美国伯克利大学Bernadi等[21]提出的Bernadi生热率计算模型对电池生热量和温度的变化进行分析,计算模型为
式中,I为电流,V为电池体积,Eoc为电池的平衡电动势,U为电池工作电压,T为电池温度。将电流密度J=I/V代入(2)式得
由于在安全的充放电范围内,实际使用中自放电和电解质分解产生的热量很小,故可认为Qs=0。另外,以等效极化内阻产生的焦耳热替代极化热。结合Bernadi生热率计算模型,建立生热速率计算模型,为
式中Rp为等效极化内阻。
基于能量守恒定律和傅里叶变换,综合考虑电池电势和电流密度模型,建立单体电池热耦合模型,表达式为
式中:ρp、ρn、ρr分别为正极片集流体、负极片集流体和电池极板密度,kg·m-3;Cp、Cn、Cr分别为正极片集流体、负极片集流体和电池极板比热容,J·kg-1·K-1;qfp、qfn、qfr分别为正极片集流体、负极片集流体和电池极板的散热速率,W·m-3;正负极片的散热率
2.2.3 锂离子电池温度场仿真
实验采用的5500 mA·h(1 mA·h=1 C)锂电池单体的规格参数及基本工作性能如
表 1. 5500 mA·h锂离子电池规格及性能参数
Table 1. Specifications and performance parameters of the 5500 mA·h lithium-ion battery
|
表 2. 5500 mA·h锂离子电池各部分的热物性参数
Table 2. Thermal physical parameters of each part of 5500 mA·h lithium-ion battery
|
通过有限元软件(UG)热分析模块对锂电池进行建模,分析锂电池内部温度场,给出初始状态、放电过程中间时刻、放电结束时刻三个时间点的仿真结果,如
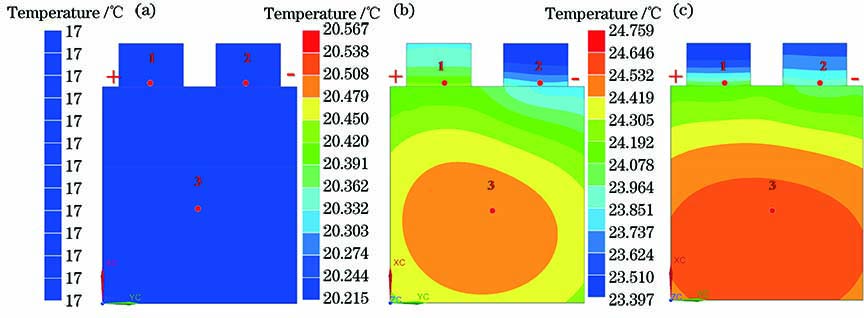
图 2. 常温下软包锂离子电池温度场仿真结果。(a)初始状态;(b)放电过程中间时刻;(c)放电结束时刻
Fig. 2. Simulation results of temperature field of the battery pouch at normal temperature. (a) Initial state; (b) middle moment of discharge process; (c) end moment of discharge process
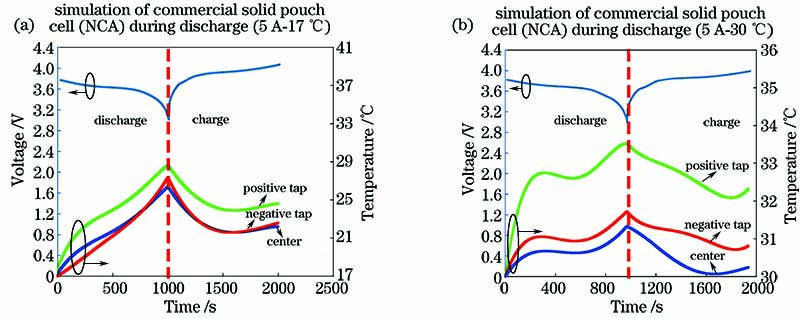
图 3. 一个充放电周期内电池温度随工作电压变化的仿真图。(a)常温17 ℃;(b) 30 ℃
Fig. 3. Simulation diagram of the temperature change of the battery with the operating voltage during one cycle. (a) Normal temperature 17 ℃; (b) 30 ℃
3 实验验证与分析
3.1 实验装置介绍
根据上述的理论分析,在实验中搭建了锂离子电池内温度场分布式光纤原位监测实验装置,如
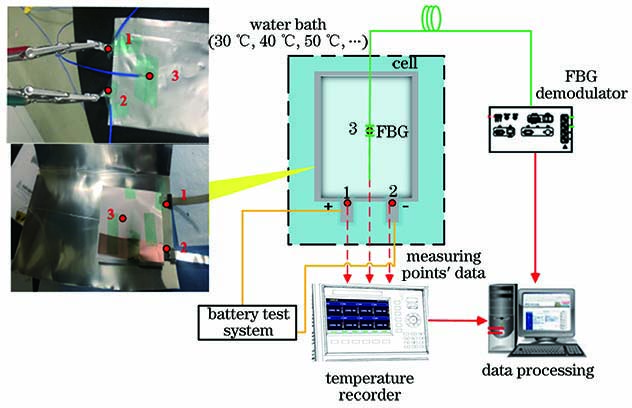
图 4. 实验装置图(内含FBG传感器埋入的软包电池实物图)
Fig. 4. Experimental setup diagram (including photograph of a battery pouch with the embedded FBG sensors)
3.2 分布式光纤光栅传感器测温原理
光纤光栅传感器测温原理如
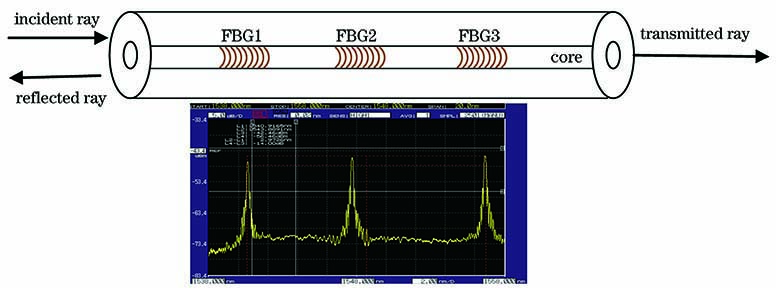
图 5. 光纤光栅传感器测温原理图
Fig. 5. Schematic diagram of fiber grating sensor temperature measurement
光纤光栅温度传感器分布式传感系统如
3.3 光纤传感器的埋入方法
在锂离子制备过程中,采取由本实验室制作的分布式光纤光栅传感器埋入锂离子电池的内部,埋入位置的选取是本实验的关键。3.2节中基于电池热模型仿真确定了3个特征区域(正极耳、负极耳、电池中心位置)。锂电池的正负极耳均是通过高温或超声波设备焊接至正负极片上,焊接过程中会产生焊点,这些点由于电阻率高会成为电池运行时易发热的区域。因此结合理论仿真及焊点因素,本节选择了以上3个特征区域进行传感器的埋入。由于所采用的RT2000/L FBG传感系统内集成的宽带光源的带宽为1520~1570 nm,功率为10 mW,故选用中心波长为1540.9199,1547.7101,1556.7247 nm的三段光栅进行埋入,各光栅之间的间距为36~42 mm,以保证布设在3个相应的特征区域上。光栅埋入前先对分布式光纤的传感栅区使用丙烯酸酯材料进行涂覆保护,以防止电池内部电解液的腐蚀对传感器性能以及电池本身转化效率产生影响。对于本文所使用的软包锂离子电池,将3个栅区分别贴于电池电芯中心位置和正负极耳焊点附近,并用常用的高温胶带固定于隔膜与7层正负极片之间,尽可能地保证光纤松弛垂直,以规避光纤弯曲应力的影响,保证解调仪能测得更精确的电芯内温度场数据。为方便后期铝塑膜的封装以及光纤分析仪的数据采集,光纤末端从与极耳方向相反的一端穿出。传感器埋入固定方法及封装后电池实物图如
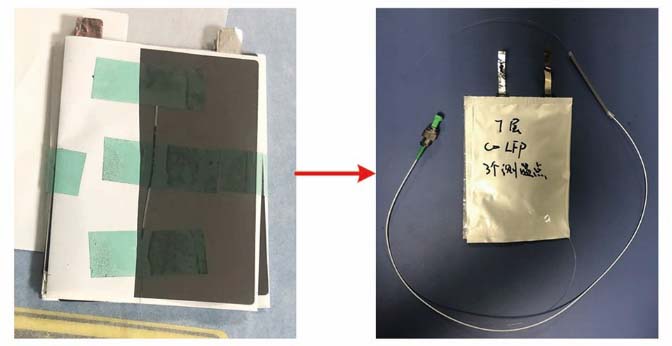
图 7. 传感器埋入固定方式及封装后电池实物图
Fig. 7. Embedded method of the sensors & physical picture of battery embedded with FBGs
在传感器埋入方法方面,经研究可在纽扣电池壳底部穿上略大于光纤直径尺寸的不锈钢管(ϕ0.6 mm)[22],或在栅区镀金[23]或涂覆防腐蚀保护涂层来保证传感器在电池内部的工作稳定性。
3.4 实验结果验证与分析
在室温条件(17 ℃)下通过埋入的FBG测得所用锂电池在三个充放电循环内的温度数据如
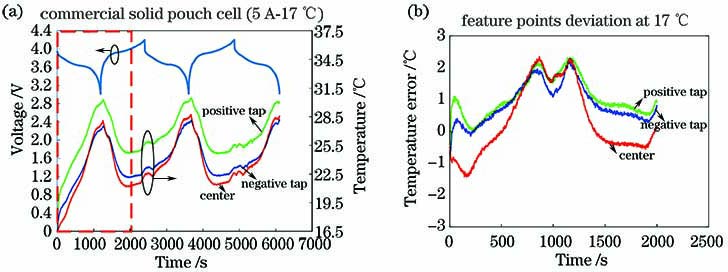
图 8. 常温(17 ℃)下3个充放电循环锂电池特征点温度变化及误差。(a)实测数据;(b)理论与实际误差
Fig. 8. Characteristic temperature change and errors of the battery during 3 cycles at room temperature (17 ℃). (a) Actual measured data; (b) error between theoretical data and actual data
通过以上实验装置,将锂电池经过外部防短路保护措施后置于恒温水浴箱中,以在实验电池允许的工作温度范围内模拟不同外部环境温度条件下的变温实验。
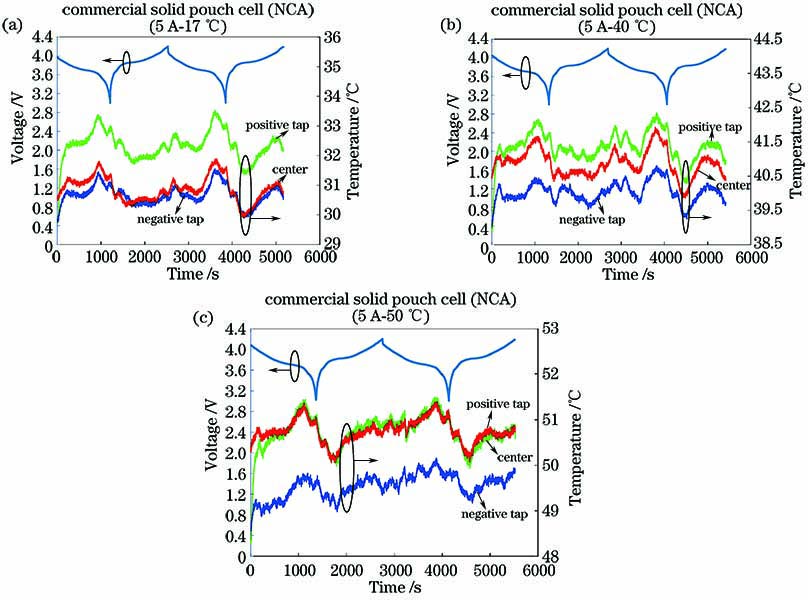
图 9. 不同环境温度下软包电池三个测温点温度变化趋势。(a) 30 ℃;(b) 40 ℃;(c) 50 ℃
Fig. 9. Trend of temperature change of three measuring points of the battery pouch under different ambient temperatures. (a) 30 ℃; (b) 40 ℃; (c) 50 ℃
从图中可发现,各个工作周期内的温度最高点均出现在放电过程结束的时刻,与仿真曲线相符。对比3个特征区域的放电阶段的温度变化趋势,正极耳在放电初始阶段的温升相比中心、负极耳都要快,这也与仿真曲线的趋势相符。在30,40,50 ℃条件下,电池的最高温升分别为3.66,3.22,2.84 ℃,验证了仿真结果中相同工作电压条件下,外界环境温度越高,锂电池各点温升越低的变化规律。另外,随着环境温度的升高,中心温度的温升相比其他正极耳、负极耳更明显:30 ℃时一个充放电周期内中心点的最高温升为1.32 ℃,正极耳的温升为3.66 ℃;40 ℃时一个充放电周期内中心点的最高温升为1.64 ℃,正极耳的温升为3.22 ℃;50 ℃时一个充放电周期内中心点的最高温升为1.82 ℃,正极耳的温升为2.84 ℃。由此说明外界环境温度越高,中心温度温升越快。为了防止电池热失控,对于电池内部的原位温度检测尤为重要。
3.5 大尺度锂离子电池组件综合集成监测方案讨论
目前新能源汽车动力电池应用以锂离子动力电池系统为主,为了提供汽车行驶所需要的足够功率,新能源汽车动力电池是通过多个电池单体组件串联来实现。不同电动汽车动力电池由于规格不同,所需的电池组件数量也不同,如Tesla Model S通常由8142节松下提供的18650型电池组件构成[24],每一个电池组件都连接有一个热敏电阻,当某个电池单体温度超过安全标准时,热敏电阻将产生一个电信号,传达至电池监控器,以便启动电池冷凝系统,保证电池安全性能,如
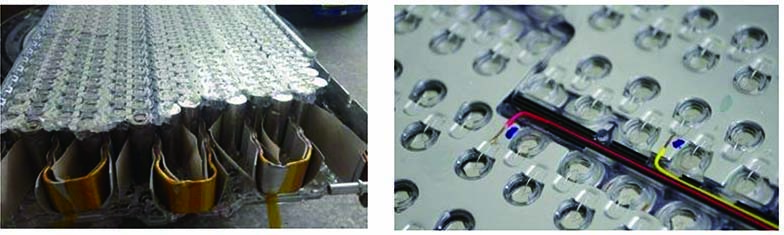
图 10. 特斯拉Model 3电池组局部排列及电池组上的热敏电阻感温元件
Fig. 10. Local arrangement of battery pack and thermistor temperature sensor on battery pack for Tesla Model 3
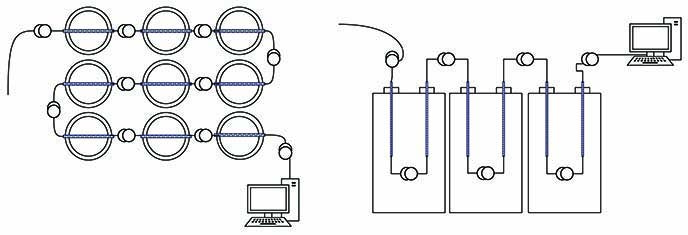
图 11. 多电池阵列分布式光纤传感器级联示意图
Fig. 11. Schematic diagram of concatenation of distributed optical fiber sensors in multi-battery array
4 结论
根据锂离子电池结构模型,利用有限元软件(UG)对电池单体温度场进行建模分析,模拟了不同环境温度条件下的内温度场演化规律。在此基础上,通过选取特征温度点,对分布式级联的光纤光栅温度传感器的性能及埋入方法进行了研究,验证了模拟分析结果,实验与理论结果相符。最后,对大尺度锂离子电池组件综合集成监测方案进行了讨论和分析,为未来智能新能源功能的发展提供了参考。
[2] Xie G, Zhu H J, Liu X M, et al. A core-shell LiFePO4/C nanocomposite prepared via a sol-gel method assisted by citric acid[J]. Journal of Alloys and Compounds, 2013, 574: 155-160.
[5] Fathollahi F, Javanbakht M, Omidvar H, et al. Improved electrochemical properties of LiFePO4/graphene cathode nanocomposite prepared by one-step hydrothermal method[J]. Journal of Alloys and Compounds, 2015, 627: 146-152.
[6] Talebi-Esfandarani M, Savadogo O. Enhancement of electrochemical properties of platinum doped LiFePO4/C cathode material synthesized using hydrothermal method[J]. Solid State Ionics, 2014, 261: 81-86.
[7] Raghavan A, Kiesel P, Sommer L W, et al. Embedded fiber-optic sensing for accurate internal monitoring of cell state in advanced battery management systems part 1: cell embedding method and performance[J]. Journal of Power Sources, 2017, 341: 466-473.
[8] Fleming J, Amietszajew T, Mcturk E, et al. Development and evaluation of in-situ instrumentation for cylindrical Li-ion cells using fibre optic sensors[J]. HardwareX, 2018, 3: 100-109.
[9] 郭晓际. 特斯拉纯电动汽车技术分析[J]. 科技导报, 2016, 34(6): 98-104.
Guo X J. Tesla electric vehicle technology analysis[J]. Science & Technology Review, 2016, 34(6): 98-104.
[10] Weston AH, Paul BK, DorianW, et al. 2010-06-03.
[12] Bandhauer T M, Garimella S, Fuller T F. A Critical Review of Thermal Issues in Lithium-Ion Batteries[J]. Journal of the Electrochemical Society, 2011, 158(3): R1-R25.
[13] Udd E, Shulz W L, Seim J M, et al. Fiber optic distributed sensing systems for harsh aerospace environments[J]. Proceedings of SPIE, 1999, 3674: 136-147.
[16] Nellen P M, Mauron P, Frank A, et al. Reliability of fiber Bragg grating based sensors for downhole applications[J]. Sensors and Actuators A: Physical, 2003, 103(3): 364-376.
[17] BanaszczykJ, AdamczykB. Investigation of dielectric strength of solid insulating materials[C]∥2017 Progress in Applied Electrical Engineering (PAEE), June 25-30, 2017, Koscielisko, Poland.New York: IEEE Press, 2017: 1- 7.
[18] Ganguli A, Saha B, Raghavan A, et al. Embedded fiber-optic sensing for accurate internal monitoring of cell state in advanced battery management systems part 2: internal cell signals and utility for state estimation[J]. Journal of Power Sources, 2017, 341: 474-482.
[20] 徐一旻, 丁宏军, 王剑, 等. 基于密集型光纤光栅温度传感器的电池温度监测系统: CN109580039A[P].2019-04-05.
Xu YM, Ding HJ, WangJ, et al. 2019-04-05.
[21] Bernardi D, Pawlikowski E M, Newman J. A general energy balance for battery systems[J]. Journal of the Electrochemical Society, 1985, 132(1): 5-12.
[22] 周炜航, 叶青, 叶蕾, 等. 基于锂电池的光纤温度传感器埋入方法: CN201910840056.0[P].2019-09-06.
Zhou WH, YeQ, YeQ, et al. 2019-09-06.
[23] 刘延超, 方进, 徐翀, 等. 镀金光纤布拉格光栅传感器用于锂离子电池原位检测的可行性[J]. 激光与光电子学进展, 2017, 54(7): 040602.
Liu Y C, Fang J, Xu C, et al. Feasibility of gold-plated fiber Bragg grating sensors used in lithium-ion battery in-situ detection[J]. Laser & Optoelectronics Progress, 2017, 54(7): 040602.
[24] 刘春娜. 特斯拉汽车电池技术及策略[J]. 电源技术, 2014, 38(7): 1201-1202.
Liu C N. Tesla car battery technology and strategy[J]. Chinese Journal of Power Sources, 2014, 38(7): 1201-1202.
[25] Bao X Y, Chen L. Recent progress in distributed fiber optic sensors[J]. Sensors, 2012, 12(7): 8601-8639.
[26] 杨颖. 分布式大容量光纤光栅传感网络的组网技术[J]. 光学技术, 2019, 45(6): 712-717, 736.
[27] 陶渊, 张翠, 童杏林, 等. 用低反射率光栅阵列实现智能复合电力电缆温度监测[J]. 光电子·激光, 2019, 30(2): 134-139.
Tao Y, Zhang C, Tong X L, et al. Temperature monitoring for intelligent composite electric cable by weak reflective fiber Bragg grating array[J]. Journal of Optoelectronics·Laser, 2019, 30(2): 134-139.
[28] 娄辛灿, 郝凤欢, 刘鹏飞, 等. 一种光纤光栅阵列波长解调系统[J]. 激光与光电子学进展, 2019, 56(3): 030604.
Article Outline
周炜航, 叶青, 叶蕾, 李璇, 曾朝智, 黄淳, 蔡海文, 瞿荣辉. 锂离子电池内温度场健康状态分布式光纤原位监测技术研究[J]. 中国激光, 2020, 47(12): 1204002. Zhou Weihang, Ye Qing, Ye Lei, Li Xuan, Zeng Chaozhi, Huang Chun, Cai Haiwen, Qu Ronghui. Distributed Optical Fiber In-Situ Monitoring Technology for a Healthy Temperature Field in Lithium Ion Batteries[J]. Chinese Journal of Lasers, 2020, 47(12): 1204002.