铝箔的激光温冲击压印工艺及机理研究
下载: 881次
Objective Laser shock imprinting (LSI) is a manufacturing technique for material strengthening and forming using high-pressure plasma shock waves induced by laser pulses. It has been widely used in many fields. Warm laser shock peening (WLSP) combines the advantages of laser shock peening, dynamic strain aging, and dynamic precipitation and can produce microstructures with high stability. The LSI technology can produce regular large-area periodic microstructures with different shapes from hundreds of microns to nanometers on a metal foil surface. Corresponding to WLSP, the temperature-assisted LSI technology changes the forming process, forming quality, and forming mechanism of an aluminum foil. Therefore, it is important to conduct a detailed investigation on warm laser shock imprinting (WLSI) and reveal the mechanism of high strain rate plastic deformation hardening and dynamic recovery softening during multiple WLSI.
Methods WLSI of an aluminum foil at different imprinting temperatures and imprinting times was conducted using the WLSI experimental devices. The imprinting temperature was controlled using an electric heating plate. We tested the forming height, surface quality, surface hardness, and microstructure of the aluminum foil using an optical profilometer, scanning electron microscope, nano-indenter, and transmission electron microscope, respectively. The ABAQUS/Explicit module was used to analyze the transient mechanical effect of the aluminum foil during the WLSI process, in which the residual stress and deformation speed of the forming parts were also analyzed.
Results and Discussions For WLSI at different temperatures, when the imprinting temperature was 25 ℃, the forming height was about 8.2 μm. When the imprinting temperatures were 150 ℃ and 225 ℃, the forming height was increased to 9.3 μm, and the microstructure on the aluminum foil surface had a good forming quality. When the imprinting temperature was 300 ℃, the forming height was dropped to about 8.35 μm, and the formed part surface had a poor oxidation phenomenon (Fig. 3). The simulation results by the ABAQUS/Explicit module showed that the maximum deformation speed of the aluminum foil at 300 ℃ was about 41.8 m/s, 10.6% higher than that at 25 ℃ (37.8 m/s). Furthermore, the WLSI introduced high residual stress at the top of the microstructure. With the increase of imprinting temperature, the area of the high residual stress was increased, the maximum residual stress was decreased, and the difference between the maximum and the minimum internal stresses was decreased gradually (Fig. 5). In the WLSI at different imprinting times, compared with the forming height after single imprinting (3.8 μm), those after two (5.8 μm) and three (7.4 μm) successive imprintings were increased by 52.6% and 94.7%, respectively (Fig. 6). It should be noted that slip and twinning are the main deformation mechanisms of materials. Aluminum is a high-fault-energy metal with a small expansion dislocation width but does not easily form twin. In this study, the laser-induced shock pressure was 3.8 GPa, and the strain rate was greater than 10 4s -1 during the WLSI shock hardening and softening process. The WLSI process triggered dislocation slip in different slip planes and formed dense dislocation. The grains’ dislocation entanglement and chaotic dislocation entanglement separated the high- and low-density dislocations to form cellular substructure and sub-grains. The high-density dislocation, small cellular substructure, and sub-grains made the strength and hardness of the aluminum foil increased, which led to the second and third WLSI deformation increments. We divided the softening process at multiple WLSI into two processes, namely, dynamic recovery and dynamic recrystallization, based on the deformation conditions. Furthermore, we compared the refinement methods for high- and low-fault-energy materials with that for the medium-fault-energy materials. Our results show that the refinement methods for high- and low-fault-energy materials are more simple than that for the medium-fault-energy materials. Owing to the high-fault-energy material of the aluminum foil, dislocation slip and dynamic recrystallization result in grain refinement. However, owing to the low temperature, short deformation time, small deformation degree, and high-fault-energy, only dynamic recovery occurred in our experiment. Moreover, no dynamic recrystallization and grain refinement occurred, and a large number of cellular substructures and high-density dislocation were retained in the grains (Fig. 9). Therefore, compared with dynamic recovery softening, shock hardening plays a dominant role in multiple WLSI.
Conclusions This study demonstrates that an increase in imprinting temperature reduces the flow stress of aluminum foil and makes its formation easy. WLSI leads to a high forming height and good surface quality at 150 ℃ when the imprinting temperature is 300 ℃. Furthermore, the springback and shrinkage of the aluminum foil lead to a small forming height, whereas the oxidation leads to bad surface quality. With the increase of imprinting times, the forming height of the aluminum foil gradually increases, whereas that of each imprinting decreases. After three imprinting times at 200 ℃, the forming part surfaces maintain good oxidation state and surface quality. Multiple WLSI can enhance the deformation resistance of the formed parts and strengthen the mechanical properties of the aluminum foil. Thus, the foil is subjected to the dual effects of shock hardening and recovery softening. The shock hardening plays an important role in the experiment, which ultimately leads to the successive increment of the hardness and decrement of the forming height of the aluminum foil.
1 引言
激光冲击技术是利用激光脉冲诱导的高压等离子冲击波实现材料强化与成形的制造技术,其在多个领域中已获得广泛应用。激光冲击喷丸(LSP)以实现金属材料表面性能强化为目的,材料表面性能主要包括硬度、耐磨性、抗拉强度、耐腐蚀性和抗疲劳强度等[1-4]。为了获得更佳的强化效果,2010年,Liao等[5]提出了激光温冲击喷丸(WLSP)技术,该技术基于LSP,具有动态应变时效和动态析出的优点,能够在材料内部制备具有高稳定性的微观结构。江苏大学周建忠课题组在WLSP方面也开展了广泛的研究工作[6]。
2006年,Cheng 等[7] 首次提出激光冲击压印(LSI)技术,并成功制造出周期为300 μm的微结构。随后,江苏大学的王霄课题组初步建立了LSI技术的理论模型和实验系统,并分析了该工艺的成形特点[8]。山东大学的季忠课题组在该领域也进行了深入的研究[9]。Gao等[10]通过实验和仿真发现,该技术能够有效改善微结构的力学性能。Ehrhardt [11]在铜箔上实现了亚微米结构的制造,并探讨了微结构的微观组织。2014年,Gao等[12]在铝箔表面制造出特征尺寸小于10 nm的微结构,并分析了成形过程中纳米晶粒的微观演化过程以及铝箔的形变机理。国内外在LSI领域已开展了大量的研究工作,但WLSI的冲击硬化与回复/再结晶软化的机理还有待进一步研究。
本文以铝箔为研究对象,研究了冲击温度和连续多次冲击对WLSI铝箔微结构成形高度和成形质量的影响,分析了WLSI高应变率塑性变形硬化和动态回复软化之间的关系,揭示了WLSI的成形和强化机理。
2 实验原理与方法
2.1 WLSI原理
WLSI的实验装置如
2.2 显微结构的表征与测量
为了对比不同参数下WLSI后的微结构,采用三维光学轮廓仪进行三次测量并将平均值作为成形高度;采用扫描电子显微镜和透射电子显微镜(TEM)对成形件的表面形貌和显微组织进行表征;采用能量色散谱仪(EDS)和纳米压痕仪对成形件的表面元素含量和分布、纳米硬度和弹性模量进行测量。
2.3 数值模拟
选用ABAQUS/Explicit模块对WLSI过程进行瞬态力学效应分析。选择Johnson-Cook应变敏感塑性模型,该模型适用于高应变率条件下的材料变形,考虑了应变和温度对等效屈服强度的影响、金属材料弹性特性和流动应力的温度依赖性。该模型的表达式[13]为
式中:σe是等效屈服强度;εpl是真实塑性应变;
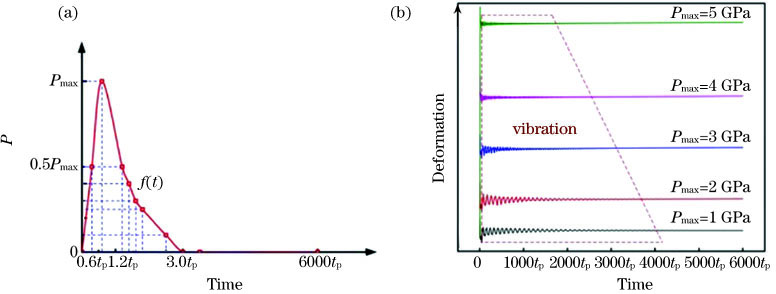
图 2. 加载曲线及时间步的确定。(a)加载曲线;(b)变形量-时间曲线
Fig. 2. Loading curve and determination of time steps. (a) Loading curve; (b) deformation versus time
3 结果与讨论
3.1 温度对WLSI的影响
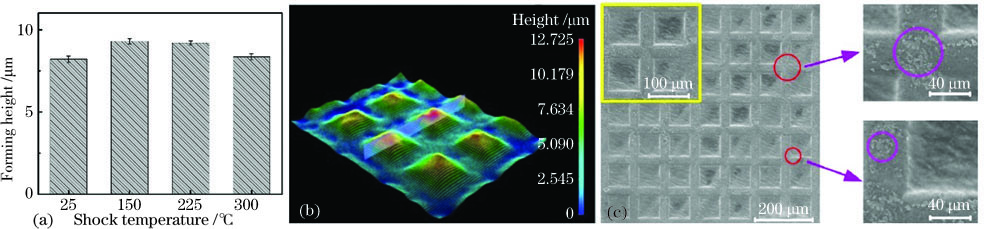
图 3. 不同温度下的WLSI成形高度及形貌。(a)成形高度;(b)150 ℃下的形貌;(c)300 ℃下的形貌
Fig. 3. Forming heights and morphologies of WLSI at different temperatures. (a) Formation height ; (b) morphology at 150 ℃;(c) morphology at 300 ℃
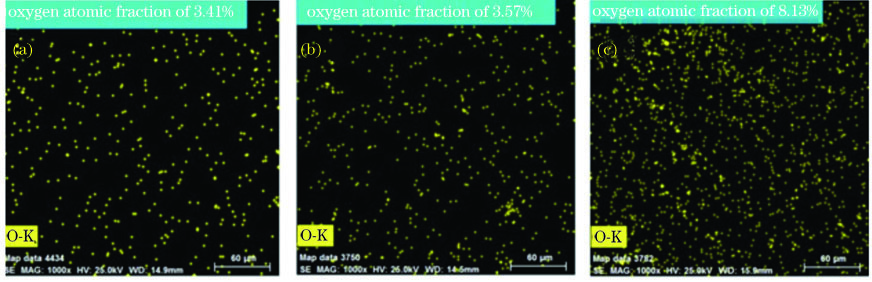
图 4. 不同冲击温度下成形件表面氧的原子数分数及分布。(a)25 ℃;(b)150 ℃;(c)300 ℃
Fig. 4. Atomic fractions and distributions of surface oxygen element of formed part at different impact temperatures. (a) 25 ℃; (b) 150 ℃; (c) 300 ℃
为了研究冲击温度对成形件内部残余应力的影响,本文对压印温度为25,150,225,300 ℃时的WLSI进行了数值分析,仿真结果如
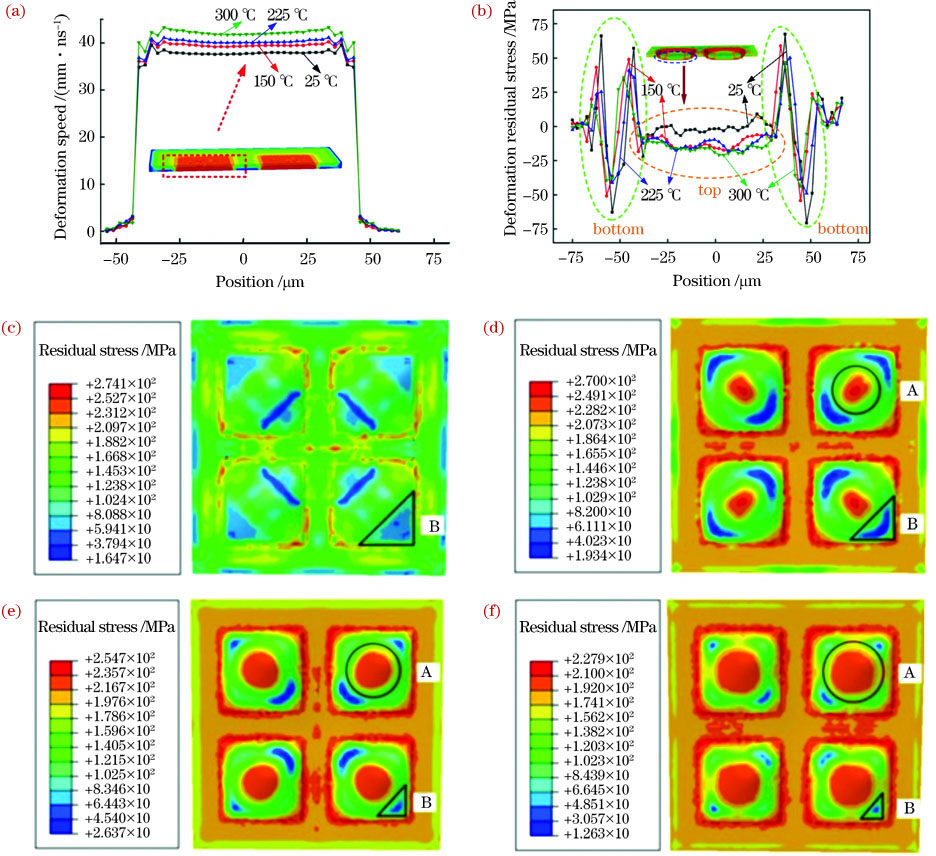
图 5. 不同压印温度下成形件的变形速度和应力图。(a)变形速度; (b)横截面的S33应力曲线;(c)25 ℃下的应力图;(d)150 ℃下的应力图;(e)225 ℃下的应力图;(f)300 ℃下的应力图
Fig. 5. Deformation speeds and stress maps at different imprinting temperatures. (a) Deformation speed; (b) stress curves of cross section (S33); (c) stress map at 25 ℃; (d) stress map at 150 ℃; (e) stress map at 225 ℃; (f) stress map at 300 ℃
表 1. 不同压印温度下成形件的残余应力值
Table 1. Residual stress values of formed parts at different imprinting temperatures
|
3.2 冲击次数对WLSI的影响
为了研究冲击次数对WLSI的影响,根据150 ℃和225 ℃时的WLSI成形高度实验,选择在200 ℃的压印温度下分别进行单次、连续两次与连续三次的WLSI实验。
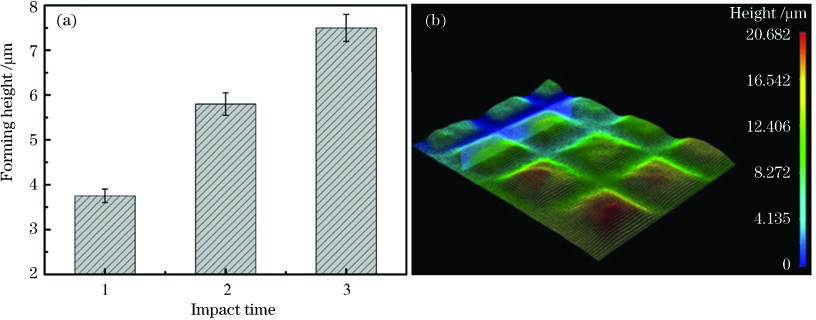
图 6. 成形高度和轮廓图。(a)不同冲击次数下的成形高度;(b)连续三次冲击后的轮廓图
Fig. 6. Forming height and contour map. (a) Forming heights at different impact times; (b) contour map after three consecutive impacts
然而,在多次冲击过程中,每一次压印后成形高度的增加量(下一次压印后的成形高度与上一次压印后的成形高度之差)逐渐减小。造成该结果的原因可归结为三点:第一,根据金属氧化物激光清洗机理的研究结果[18-19]可知,激光烧蚀作用会在吸收层表面上形成氧化铝(Al2O3), 吸收层纯铝和表面形成的氧化铝的熔点分别为660 ℃和2054 ℃,再次压印时,氧化铝和铝共同作为吸收层吸收激光能量并产生等离子体,等离子体高速膨胀产生的冲击波使下一次压印的深度继续增加,但氧化铝的高熔点使得冲击波的强度有所减小;第二,上一次压印时,由于冲击波和光的吸收作用,K9玻璃表面产生了轻微的损伤和光致变色,因此下一次冲击时激光能量发生损失;第三,在上一次压印过程中,吸收层和金属层在冲击波的作用下发生塑性变形,这在一定程度上引起了加工硬化现象,从而加剧了下一次压印过程中变形的困难程度,对成形高度的继续增加有一定的限制作用。为了验证WLSI导致加工硬化的推论,在200 ℃下对多次WLSI制备的成形件进行了纳米压痕测试,结果如
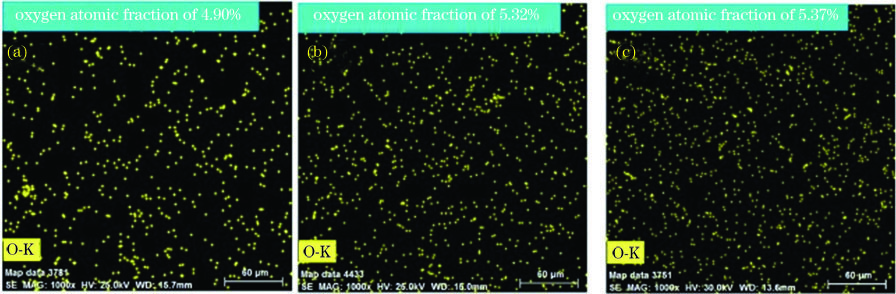
图 7. 多次WLSI后表面氧的原子数分数与分布。(a)1次;(b)2次;(c)3次
Fig. 7. Atomic fractions and distributions of surface oxygen element after multiple WLSI. (a) One time; (b) two times; (c) three times
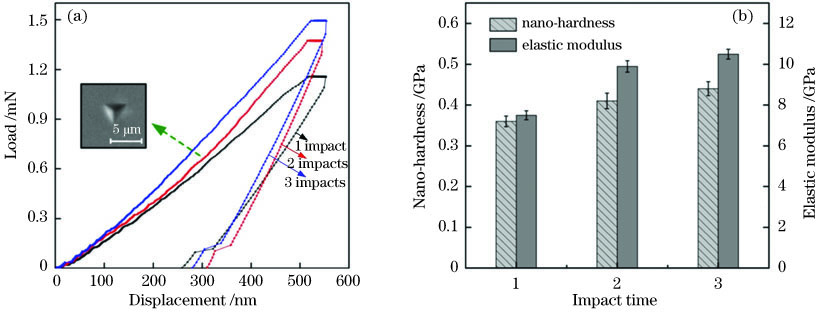
图 8. WLSI的纳米压痕测试结果。(a)载荷-位移曲线;(b)纳米硬度和弹性模量
Fig. 8. Nano-indentation test results of WLSI. (a) Load-displacement curves; (b) nano-hardness and elastic modulus
3.3 WLSI过程中的硬化与软化机制
在多次WLSI过程中,硬度逐次增加,成形高度的增加量逐次减小,这说明硬化过程占主导作用,软化过程起次要作用。因此,利用TEM和ABAQUS仿真软件对冲击后的显微组织及瞬态过程进行研究。
首先,对于高应变率塑性变形硬化过程而言,滑移和孪晶是材料的主要变形机理,如本课题组对铜箔进行激光冲击处理,处理过程中同时存在位错引起的滑移和孪生引起的孪晶[14];江苏大学的鲁金忠团队对不锈钢进行激光冲击时发现,孪生是其主要的变形方式[20]。而在本文中,铝是高层错能金属,其扩展位错宽度较小,不易形成孪晶。根据Fabbro模型和Johnson-Cook (J-C)[21],本实验中WLSI的冲击波峰值压力高达3.8 GPa,应变率大于104 s-1,WLSI过程触发了不同滑移面上的位错滑移,在晶粒内形成了密集的位错和位错缠结,如
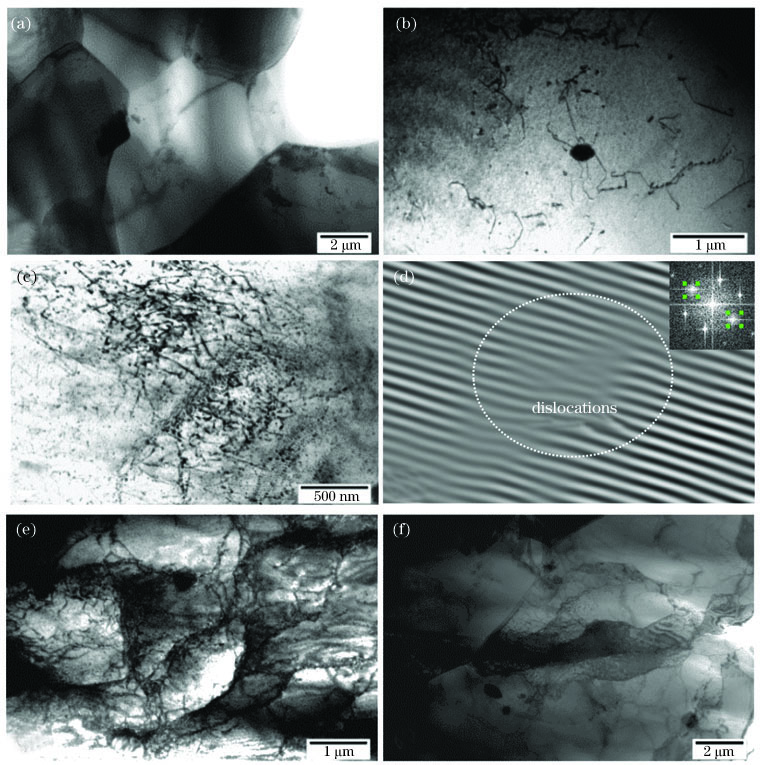
图 9. 单次WLSI前后铝箔的TEM显微结构。(a) WLSI前的晶粒形态; (b) WLSI前的低密度位错; (c) WLSI后的高密度位错;(d) WLSI后高密度位错的傅里叶逆变换图;(e) WLSI后的位错胞;(f) WLSI后的亚晶结构
Fig. 9. TEM microstructures of aluminum foil before and after single WLSI. (a) Grain shape before WLSI; (b) low density dislocations before WLSI; (c) high density dislocations after WLSI; (d) inverse Fourier transform graph of high density dislocations after WLSI; (e) dislocation cells after WLSI; (f) sub-grains after WLSI
高密度位错、胞状亚结构和亚晶对材料的性能有很大影响。前人的研究表明,位错交互作用产生的阻力与材料的屈服强度有关,塑性变形抗力σ与晶粒内部位错密度的关系为
式中:σ0是材料初始的塑性变形抗力;α0是强化系数;G是材料的切变模量;b是柏氏矢量大小;ρd是材料内部的位错密度。位错密度的增加增大了材料位错滑移所需要的剪应力,即位错起动力,因此靶材将产生附加强化效应。
另外,当晶粒组织由大角度晶粒和亚晶粒的混合组织构成时,其屈服应力也在一定程度上有所增加,表达式为
式中:σs是材料的屈服应力;ky是组织仅由大倾角晶粒构成时σs与晶粒直径的关系;ks是全部组织由亚晶粒构成时与亚晶粒尺寸相关的系数;ds为亚晶粒直径;fs为亚晶粒的体积率。这也进一步证实了,本实验中高密度位错[
根据变形条件的不同,WLSI中的软化过程分为动态回复过程和动态再结晶过程。相对于中等层错能材料而言,高等和低等层错能材料的细化方式更为单一[23]。铝箔属于高层错能材料,位错滑移与动态再结晶的共同作用造成晶粒细化。但在本实验中,并没有观察到晶粒细化现象,仅仅发现了大量的位错胞和亚晶。可能的原因主要包括以下四点:第一,铝的再结晶温度一般在250~300 ℃之间,本实验中WLSI的温度为200 ℃,不足以达到再结晶温度;第二,由文献[ 12]可知,LSI过程属于绝热过程,材料内部的温度可达300 ℃,但温度持续时间非常短;第三,铝的扩展位错很窄,容易发生交滑移和攀移,异号位错相互抵消,使得亚晶组织中的位错密度下降,储存能下降,不足以引起动态再结晶;第四,材料的变形量也将影响动态再结晶过程。文献[ 20]表明,大的塑性变形量将触发动态再结晶从而细化晶粒,反之,将不会发生动态再结晶。因此,在本实验中,由于温度低、变形时间短、变形程度小、层错能高,仅发生了动态回复而无动态再结晶,没有发生晶粒细化,晶粒中仍保留有大量的胞状亚结构和高密度位错。
通过TEM分析发现,WLSI中存在着材料冲击硬化和回复软化双重作用。下面通过ABAQUS数值仿真进一步说明硬化和软化在WLSI过程中所起的作用。当压印温度为200 ℃,冲击次数分别为1、2、3时,通过ABAQUS对铝箔进行仿真分析,结果如
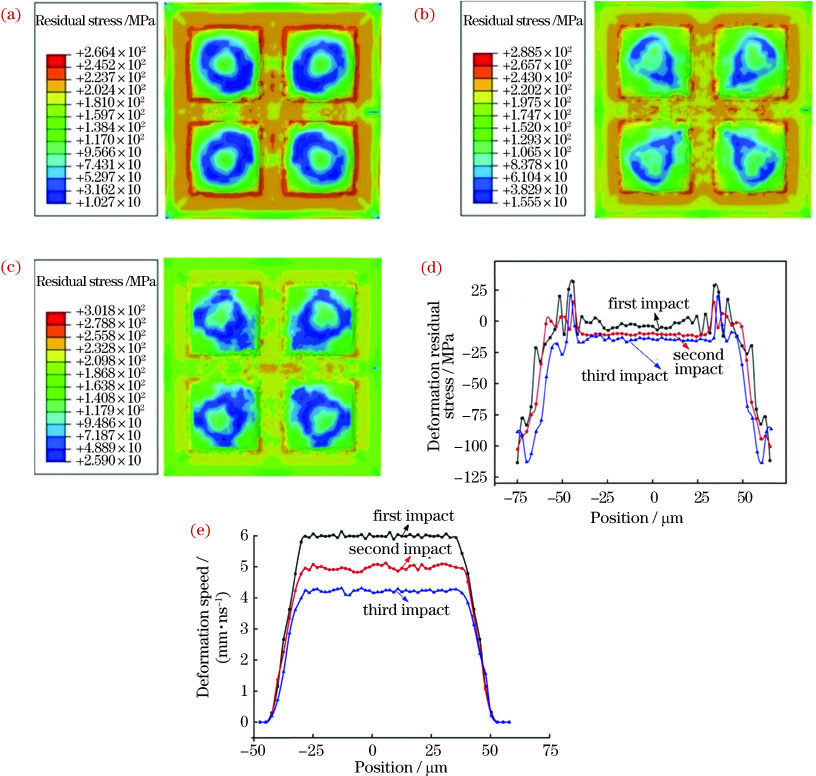
图 10. 不同冲击次数下的变形速度与应力。(a)一次冲击下的应力图;(b)二次冲击下的应力图;(c)三次冲击下的应力图;(d)横截面的S33应力曲线;(e)变形速度
Fig. 10. Deformation speeds and stresses at different impact times. (a) Stress map after one impact; (b) stress map after two impacts; (c) stress map after three impacts; (d) stress curves of cross section (S33); (e) deformation speed
表 2. 不同冲击次数下成形件的残余应力值
Table 2. Residual stress values of formed parts at different impact times
|
综上所述,残余内应力的提高增加了成形件的强度和硬度,但降低了塑性,从而导致在下一阶段的冲击成形过程中,铝箔的动态屈服强度升高,其塑性变形需要更高的冲击波压力。冲击次数提高了微凸起的残余内应力,这很好地解释了多次冲击过程中冲击次数对成形高度变化量以及机械性能的影响规律。
4 结论
研究了多次WLSI时冲击温度和冲击次数对铝箔微结构成形高度、成形质量的影响,并结合数值仿真和TEM显微组织,分析了多次WLSI过程中冲击硬化和回复软化的机理,得出以下结论。
1)随着冲击温度的升高,铝箔塑性变好,流变应力变小,成形更加容易;当压印温度为150 ℃时,成形件具有较大的成形高度和较好的表面质量;当压印温度为300 ℃时,由于回弹和收缩的影响,成形高度下降,同时氧化导致表面质量变差;温度的升高增加了成形件残余应力分布的均匀性。
2)随着压印次数的增加,成形件的成形高度逐渐增大,但每一次压印时成形高度的增加量逐次减小;在200 ℃下多次冲击后,成形件的表面没有出现过度氧化的情况,表面质量较好;多次WLSI能够增强成形件的抗变形能力,对铝箔的机械性能具有强化作用。
3)在多次WLSI过程中,铝箔受冲击硬化和回复软化的双重作用,其中冲击硬化起主导作用,最终导致晶粒内有大量残余的位错和胞状亚结构,残余应力逐次增加,变形速度逐次减小,硬度逐次增加,成形高度的增加量逐次减小。
[1] 刘亚鹏, 史志俊, 赵一昭, 等. 激光冲击与喷丸复合强化对TC4钛合金细节疲劳额定强度截止值的影响[J]. 中国激光, 2020, 47(5): 0502006.
[2] Zhou J Z, Yang J C, Zhang Y K, et al. A study on super-speed forming of metal sheet by laser shock waves[J]. Journal of Materials Processing Technology, 2002, 129(1/2/3): 241-244.
[3] 汪军, 李民, 汪静雪, 等. 激光冲击强化对304不锈钢疲劳寿命的影响[J]. 中国激光, 2019, 46(1): 0102003.
[4] 田绪亮, 周建忠, 李京, 等. 深冷激光喷丸强化对2024-T351铝合金微观组织的影响[J]. 中国激光, 2019, 46(9): 0902004.
[5] Liao Y L, Ye C, Kim B J, et al. Nucleation of highly dense nanoscale precipitates based on warm laser shock peening[J]. Journal of Applied Physics, 2010, 108(6): 063518.
[6] Zhou J Z, Meng X K, Huang S, et al. Effects of warm laser peening at elevated temperature on the low-cycle fatigue behavior of Ti6Al4V alloy[J]. Materials Science and Engineering: A, 2015, 643: 86-95.
[7] Cheng GJ, PirzadaD. Characterizations on microscale laser dynamic forming of metal foil[EB/OL] (2008-10-02)[2020-04-25] https://appliedmechanics.asmedigitalcollection.asme.org/MSEC/proceedings-abstract/MSEC2006/47624/29/319862.
[8] Liu H X, Shen Z B, Wang X, et al. Micromould based laser shock embossing of thin metal sheets for MEMS applications[J]. Applied Surface Science, 2010, 256(14): 4687-4691.
[9] Zheng C, Zhang X, Zhang Y L, et al. Effects of laser power density and initial grain size in laser shock punching of pure copper foil[J]. Optics and Lasers in Engineering, 2018, 105: 35-42.
[10] Gao H, Cheng G J. Laser-induced high-strain-rate superplastic 3-D microforming of metallic thin films[J]. Journal of Microelectromechanical Systems, 2010, 19(2): 273-281.
[11] Ehrhardt M. Processes at multi-pulse laser embossing of submicron surface structures[J]. Journal of Laser Micro, 2014, 9(3): 252-256.
[12] Gao H, Hu Y, Xuan Y, et al. Large-scale nanoshaping of ultrasmooth 3D crystalline metallic structures[J]. Science, 2014, 346(6215): 1352-1356.
[13] Yang H F, Xiong F, Liu K, et al. Research on temperature-assisted laser shock imprinting and forming stability[J]. Optics and Lasers in Engineering, 2019, 114: 95-103.
[14] Yang H F, Xiong F, Wang Y, et al. Manufacturing profile-free copper foil using laser shock flattening[J]. International Journal of Machine Tools and Manufacture, 2020, 152: 103542.
[15] Yang H F, Jia L, Liu K, et al. High precision complete forming process of metal microstructure induced by laser shock imprinting[J]. The International Journal of Advanced Manufacturing Technology, 2020, 108(1/2): 143-155.
[16] 李应红, 何卫锋, 周留成. 激光冲击复合强化机理及在航空发动机部件上的应用研究[J]. 中国科学:技术科学, 2015, 45(1): 1-8.
Li Y H, He W F, Zhou L C. The strengthening mechanism of laser shock processing and its application on the aero-engine components[J]. Scientia Sinica (Technologica), 2015, 45(1): 1-8.
[17] Wang Y, Xu J X, Zhang J, et al. Tribochemical reactions and graphitization of diamond-like carbon against alumina give volcano-type temperature dependence of friction coefficients: a tight-binding quantum chemical molecular dynamics simulation[J]. Carbon, 2018, 133: 350-357.
[18] 佟艳群. 激光去除金属氧化物的机理与应用基础研究[D]. 镇江: 江苏大学, 2014.
Tong YQ. Study on mechanism and application fundamentals of laser removal of metal oxides[D]. Zhenjiang: Jiangsu University, 2014.
[19] 佟艳群, 陆勤慧, 周建忠, 等. 铝合金焊前激光清洗的等离子体光谱在线检测[J]. 光谱学与光谱分析, 2020, 40(1): 255-260.
[20] Lu J Z, Deng W W, Luo K Y, et al. Surface EBSD analysis and strengthening mechanism of AISI304 stainless steel subjected to massive LSP treatment with different pulse energies[J]. Materials Characterization, 2017, 125: 99-107.
[21] Fabbro R, Fournier J, Ballard P, et al. Physical study of laser-produced plasma in confined geometry[J]. Journal of Applied Physics, 1990, 68(2): 775-784.
[22] Nagarajan B, Castagne S, Wang Z K, et al. EBSD analysis of plastic deformation of copper foils by flexible pad laser shock forming[J]. Applied Physics A, 2015, 121(2): 695-706.
[23] An X H, Lin Q Y, Wu S D, et al. Significance of stacking fault energy on microstructural evolution in Cu and Cu-Al alloys processed by high-pressure torsion[J]. Philosophical Magazine, 2011, 91(25): 3307-3326.
Article Outline
杨海峰, 满家祥, 熊飞, 时明天. 铝箔的激光温冲击压印工艺及机理研究[J]. 中国激光, 2021, 48(6): 0602118. Haifeng Yang, Jiaxiang Man, Fei Xiong, Mingtian Shi. Technology and Mechanism on Warm Laser Shock Imprinting of Aluminum Foils[J]. Chinese Journal of Lasers, 2021, 48(6): 0602118.