SiCp/Al复合材料纳秒脉冲光纤激光刻蚀
下载: 1046次
1 引言
SiC颗粒增强Al基(SiCp/Al)复合材料具有高比强度、低热膨胀系数以及优良的耐磨性,广泛应用于航天航空、汽车等领域[1-2]。SiC颗粒的引入使得传统机械加工存在刀具寿命短、加工成本高、表面质量差、次表层损伤等一系列问题[3-6]。电火花加工效率低、周期长[7-9],难以满足批量加工和商业化应用的需求。SiC具有较好的化学稳定性[10],但基于SiC化学反应的刻蚀加工方法的刻蚀效率很低,如反应离子刻蚀、光电化学刻蚀,以及感应耦合等离子体和电子回旋共振方法刻蚀[11]。此外,SiC颗粒和Al基体的刻蚀效率不同也造成很难用化学加工方法加工SiCp/Al复合材料。近年来,激光辅助的机械加工方法被用来加工SiC颗粒增强的A359 Al基复合材料,该方法使用连续激光作为前置热源,通过局部加热软化材料,可大大降低切削力、刀具的磨损程度、表面粗糙度及次表层损伤程度[12-13]。
脉冲激光刻蚀是利用脉宽压缩技术产生的高能量密度激光在短时间内将材料气化的一种先进加工手段,可实现金属、半导体、陶瓷等各种材料的加工[14-16]。例如,采用纳秒和飞秒激光刻蚀AISIH13工具钢,刻蚀的垂直度和表面精度都较高[17];利用飞秒激光刻蚀SiC材料可获得竖直和V型精密结构[18]等。金属基颗粒增强复合材料具有优异的物理及机械性能,逐步成为研究的热点。目前,利用激光手段已实现对SiC材料的焊接[19]、切割[20]和表面改性[21-22]。但是,关于利用脉冲激光对SiCp/Al复合材料的刻蚀加工的研究鲜有报道。
本文采用红外纳秒光纤激光器在同轴Ar气辅助下刻蚀SiCp/AA2024复合材料,探讨了SiCp/AA2024复合材料脉冲激光刻蚀的可行性,并对刻蚀机制进行了讨论。
2 实验材料及方法
2.1 实验材料
实验材料为SiCp/AA2024。机械抛光SiCp/AA2024表面后,将其放入丙酮液体中进行超声清洗,并利用压缩空气进行干燥,处理后的母材扫描电镜(SEM)照片如
2.2 实验方法
实验采用IPG公司生产的波长为1064 nm的YLPM-1-A4-20-20光纤激光器,其最大平均功率为20 W且脉宽可调。准直后的光束直径为8 mm,聚焦镜焦距为50 mm,聚焦光斑直径约为10 μm。实验时重复频率固定为3 kHz,平均脉冲光强
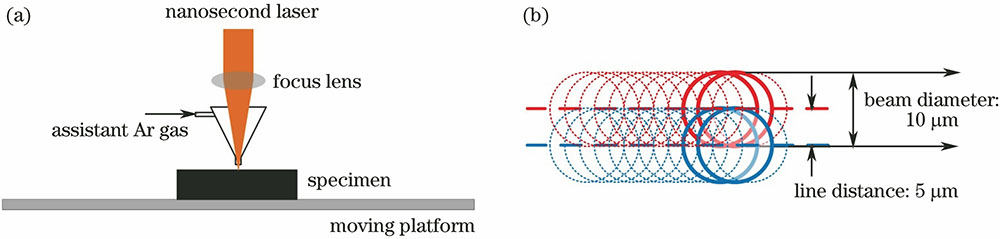
图 2. (a)实验布置示意图;(b)激光刻蚀路径示意图
Fig. 2. (a) Schematic diagram of experimental setup; (b) schematic diagram of laser ablation path
利用HITACHI公司生产的S-3400N SEM在15 kV条件下观察刻蚀表面微结构,利用BRUKER公司生产的QUANTAX能谱仪(EDS)对刻蚀表面进行元素分析,分别使用WYKO 公司生产的NT1100三维(3D)表面轮廓仪及KEYENCE 公司生产的VK-X260K 3D激光共聚焦显微镜测量刻蚀表面深度及粗糙度。
3 实验结果与讨论
3.1 刻蚀规律
当脉冲能量密度为140 J/cm2时,刻蚀表面SEM照片及3D激光共聚焦显微镜图如
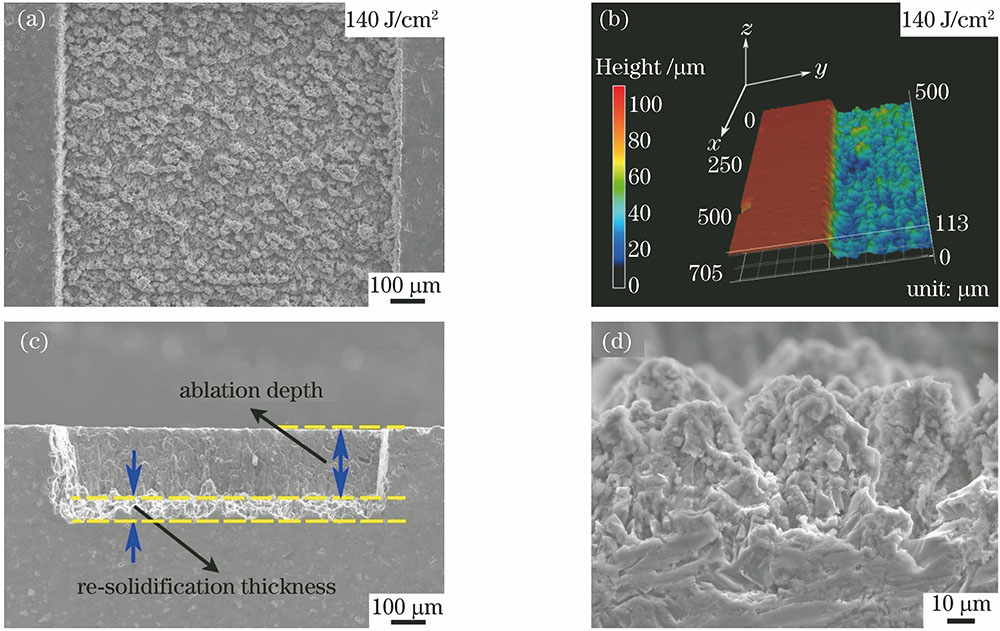
图 3. 刻蚀表面形貌图。(a)SEM; (b)3D激光共聚焦显微镜图; (c)截面SEM; (d) 表面重凝物放大图
Fig. 3. Morphology of ablated surface. (a) SEM; (b) 3D confocal laser scanning microscopy; (c) SEM of cross-section; (d) re-solidification on the surface with a high magnification
激光刻蚀深度、重凝层厚度、刻蚀表面粗糙度随激光脉宽的变化规律如

图 4. 激光刻蚀结果随脉宽变化曲线。(a)刻蚀深度及重凝层厚度;(b)表面粗糙度
Fig. 4. Variations of laser ablation results with pulse width. (a) Ablation depth and re-solidified layer thickness; (b) surface roughness
3.2 刻蚀表面成分分析
刻蚀表面重凝层SEM图及其元素分布EDS面扫描结果如
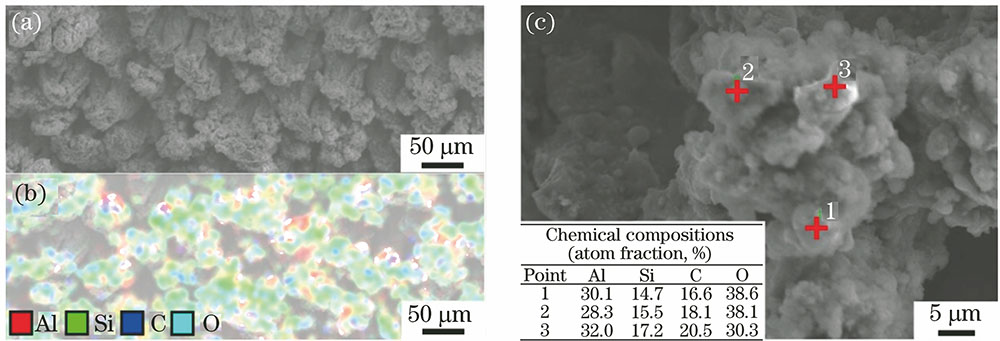
图 5. 刻蚀表面重凝层。(a)SEM;化学元素分布EDS(b)面和(c)点扫描
Fig. 5. Re-solidified layer of ablated surface. (a) SEM; EDS (b) surface and (c) point scanning analyses of chemical element distribution
利用纳秒脉冲激光刻蚀时,材料一般会经历熔化、气化等相变过程。SiC材料在不同温度阶段除了发生熔化、气化外,还会伴随一定的升华、分解。Pehrsson等[23]指出β-SiC热加工过程中,在2100~2300 K之间开始升华,但直到3000 K都不发生熔化。Gupta等[24]指出,4H-SiC和6H-SiC在1600~2400 K范围内会生成液态Si及固态C。该现象称为包晶反应,即SiC在热平衡条件下,当达到一定温度时会发生化学反应,生成液态Si(溶解部分C)及固态C。在激光的快速加热和冷却的非热平衡过程中,除了上述包晶反应外,还存在尚未熔化的SiC[25]。
综合上述,将刻蚀过程中可能出现的化学反应列举如下
式中s、g、l分别表示固体、气体、液体,
上述材料相变及冶金反应进一步说明了脉冲激光对SiCp/AA2024复合材料的刻蚀是一个复杂的过程。SiC颗粒大小不一、形状各样、位置分布随机,导致每个光脉冲辐照对象及其组分的不确定性,因此重凝层为上述可能反应产物的随机混合,重凝物元素比例及氧含量都具有一定的不确定性,但相对均匀。
3.3 刻蚀机制探讨
在纳秒脉冲激光与材料相互作用过程中,电子与晶格已达到热平衡,材料不断升温并经历熔化、气化等热相变过程[27]。据相关研究[28-29]报道,5 ns脉宽、1064 nm波长Nd∶YAG激光对Al的刻蚀阈值为5.2 J/cm2,6 ns脉宽、1064 nm波长Nd∶YAG激光对SiC的刻蚀阈值为7.8 J/cm2。实验过程中平均光强
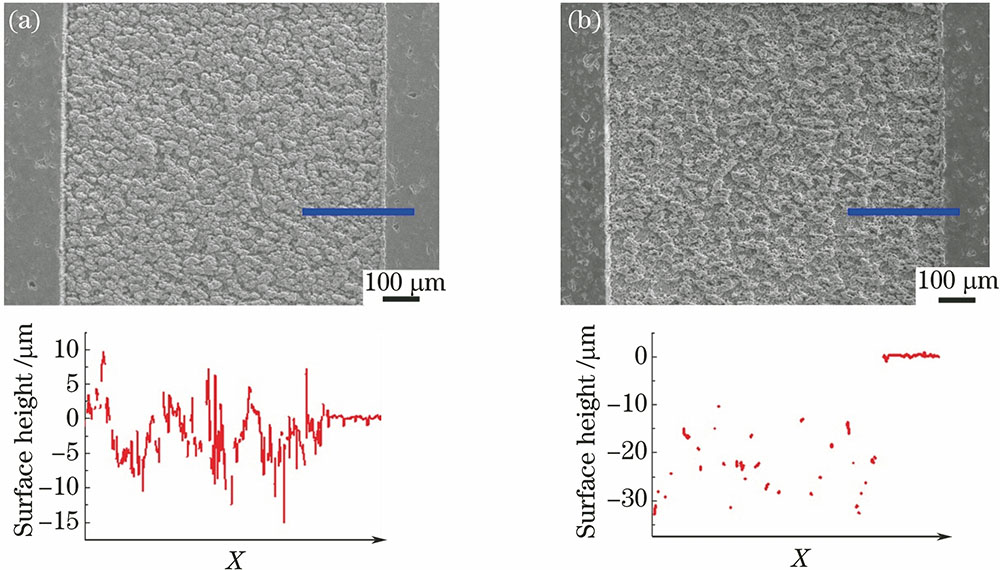
图 6. 不同气压条件下,28 J/cm2脉冲激光刻蚀效果。(a) 0.1 MPa;(b) 1 Mpa
Fig. 6. Ablation results by 28 J/cm2 laser under different gas pressures. (a) 0.1 MPa; (b) 1 MPa
在纳秒脉冲激光与材料的相互作用过程中,激光会使材料熔化形成熔池。实验中单光斑范围内脉冲数高达600,因此熔池内Al、SiC及O2有较充足的时间发生冶金反应并混合均匀,且高压Ar气可将熔融物从熔池中吹除,从而实现对复合材料的刻蚀加工。
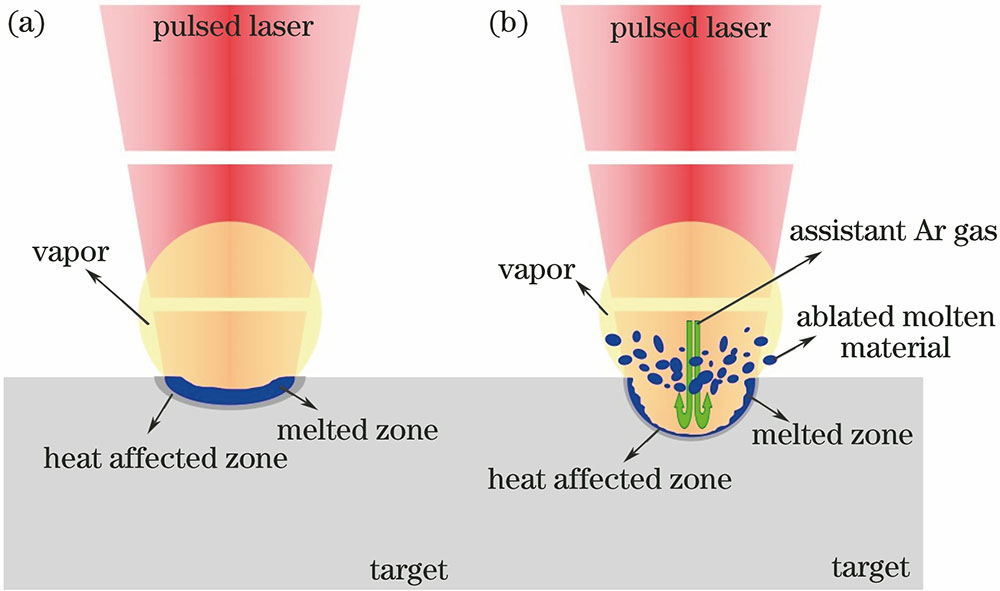
图 7. 不同气压条件下,纳秒脉冲激光刻蚀材料示意图。(a) 0.1 MPa;(b) 1 MPa
Fig. 7. Schematic diagrams of nanosecond-pulsed laser ablation of materials under different gas pressures. (a) 0.1 MPa; (b) 1 MPa
4 结论
在高压同轴气体辅助下,采用红外纳秒激光器可以实现SiCp/AA2024复合材料相对均匀的刻蚀加工,高压同轴气体的机械作用是材料蚀除的主要机制。在激光刻蚀过程中存在复杂的冶金反应,刻蚀表面粗糙度和重凝层厚度随激光能量的增加而增加,但最后均呈饱和趋势。
[3] El-Gallab M, Sklad M. Machining of Al/SiC particulate metal-matrix composites: Part I: Tool performance[J]. Journal of Materials Processing Technology, 1998, 83(1-3): 151-158.
[8] Singh P N, Raghukandan K, Rathinasabapathi M, et al. Electric discharge machining of Al-10% SiCp as-cast metal matrix composites[J]. Journal of Materials Processing Technology, 2004, 155: 1653-1657.
[10] Harris GL.Properties of silicon carbide[M]. London: Institution of Electrical Engineers, 1995: 134.
[13] Dandekar CR.Multi-scale modeling and laser-assisted machining of metal matrix composites[D]. Indiana: Purdue University, 2010.
[15] NeuenschwanderB, Bucher GF, NussbaumC, et al. Processing of metals and dielectric materials with ps-laser pulses: Results, strategies, limitations and needs[C]. SPIE, 2010, 7584: 75840R.
[16] Momma C, Nolte S, Chichkov B N. et al. Precise laser ablation with ultrashort pulses[J]. Applied Surface Science, 1997, 109: 15-19.
[18] VankoG, ZehetnerJ, CholevaP, et al. Laser ablation: A supporting technique to micromachining of SiC[C]. Ninth International Conference on Advanced Semiconductor Devices and Microsystems, 2012: 259-262.
张寰臻, 黄婷, 肖荣诗. SiCp/Al复合材料纳秒脉冲光纤激光刻蚀[J]. 中国激光, 2017, 44(1): 0102017. Zhang Huanzhen, Huang Ting, Xiao Rongshi. Nanosecond Pulsed Fiber Laser Ablation of SiCp/Al Composite Materials[J]. Chinese Journal of Lasers, 2017, 44(1): 0102017.