不等高弯曲弧形薄壁结构激光熔覆成形
下载: 766次
1 引言
薄壁部件具有质量轻、生产成本低等优势,被广泛应用于各工程领域。但薄壁部件一般稳定性较差且刚度较低[1],解决这类问题的方法有两种 :一种是通过布置加强筋板实现部件局部加厚,另一种是在特定位置沿特定的受力方向布置加强筋,通常第二种方法效果更好[2-4]。复合加筋薄壁结构具有相接或相交贯穿等结构特征,加工较为复杂,传统的加工方法一般为焊接、轧制或铸造。
激光熔覆成形是在20世纪90年代初提出的一项新型制造技术[5-6],具有一次成形、短流程、无模、组织性能优良等优点,被应用于复杂薄壁零构件和大型承力结构件的制造[7-8]。钟敏霖等[9]运用激光技术,制造了等高太空望远镜准直器结构件;方琴琴等[10]运用激光直接成形技术,加工了等高带连接筋双层薄壁件;美国GE公司采用选择性激光熔化(SLM)技术,制备了不等高相交薄壁夹嘴[11]。采用激光熔覆成形技术加工等高薄壁件的工艺较为成熟,一般不等高薄壁件加工采用SLM技术,但受到粉床尺寸限制不宜加工体积较大的零件。本文以不等高弯曲弧形工字结构件作为薄壁零件,采用激光加载防塌陷法解决了成形件可能出现的塌陷问题,利用不等高自适应原理实现了成形件的高度变化,并对结构件进行了成形研究与性能分析。
2 实验设备及材料
实验所用基板为304不锈钢,粉末为Fe313,其具体化学成分见
表 1. Fe313合金粉末的化学成分(质量分数,%)
Table 1. Chemical compositions of Fe313 alloy powder (mass fraction, %)
|
3 实验方法
3.1 实验工艺参数与零件建模
实验的激光功率为800 W,扫描速度为8 mm·s-1,送粉量为8 g·min-1,离焦量为-3.5 mm。在此工艺参数条件下,熔覆单道的形貌特征见
表 2. 熔覆单道特征
Table 2. Features of single cladding track
|
不等高弯曲弧形工字结构模型由内外两个弯曲弧形部分以及中间连接扇形部分组成,如
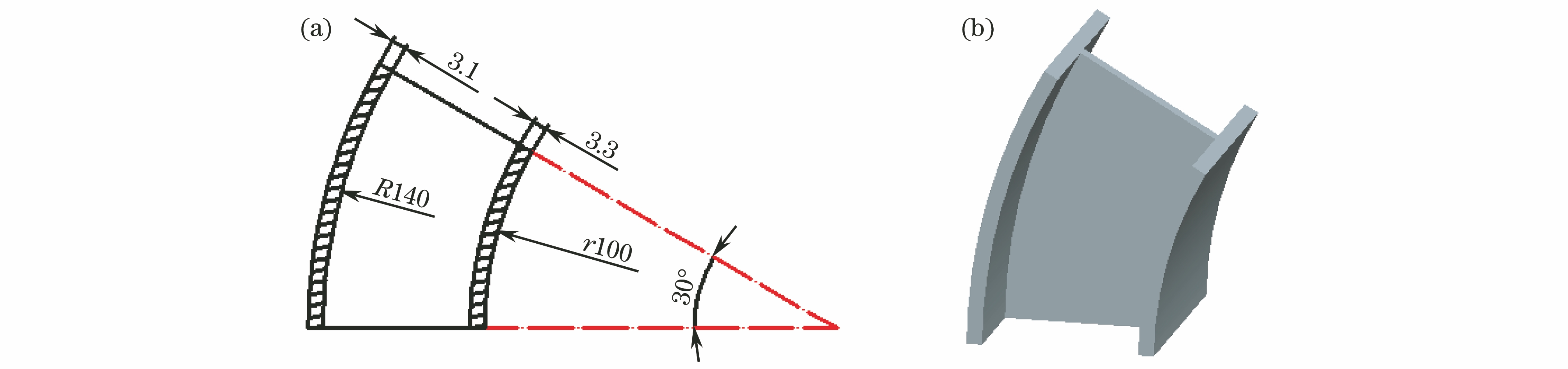
图 1. 设计模型的(a)二维图和(b)三维图
Fig. 1. (a) Two-dimensional and (b) three-dimensional diagrams of designed model
3.2 激光加载防塌陷法
基于中空环形激光特征,加工平面上的大部分粉末位于环形激光内,如
激光加载是指机器人运动到预定轨迹的端点时,保持空间姿态及位置不变,待激光停滞一定时间后再关闭激光执行下一条指令。为求得激光加载的具体时间,通过
直墙堆积采用单向扫描方式避免开光端塌陷的影响,直墙堆积

图 4. 直墙。(a)塌陷后的直墙;(b)导入AutoCAD的直墙
Fig. 4. Thin wall. (a) Thin wall after collapse; (b) thin wall after AutoCAD introduction
采用线切割方式,沿扫描垂直方向切割相同工艺参数条件下成形的熔覆单道,用砂纸打磨后,利用金相电镜拍取熔覆单道横截面的轮廓照片,如

图 5. 熔覆单道横截面。(a)横截面轮廓;(b)横截面拟合曲线
Fig. 5. Cross section of single cladding track. (a) Profile of cross section; (b) fitting curve of cross section
为获得激光加载时间,现建立如下假设:零件关光末端的塌陷全由熔道关光点处不够饱满导致;堆积的每一层熔道具有相同的形状特征;塌陷部分的体积等于堆积
式中
在上述工艺条件下堆积50层后,将图形导入AutoCAD软件,测得
为验证理论的正确性,在同样的工艺参数下,使用激光加载的方法进行熔覆单道与直墙堆积实验,加载时间为0.1 s,得到的熔覆单道与直墙分别如
3.3 不等高自适应原理
在不改变其他工艺参数条件下,通过改变离焦量进行单道熔覆实验,得到的熔覆单道高度随离焦量的变化曲线如
当离焦量在-5.5~-2.5 mm时,熔覆单道高度随离焦量的变化呈线性变化。对其线性拟合,得到方程为
式中
3.4 轨迹规划
不等高弯曲弧形工字薄壁的结构模型由内侧半径分别为140 mm和100 mm的弧形结构1, 2以及介于两者之间的扇形结构组成,如
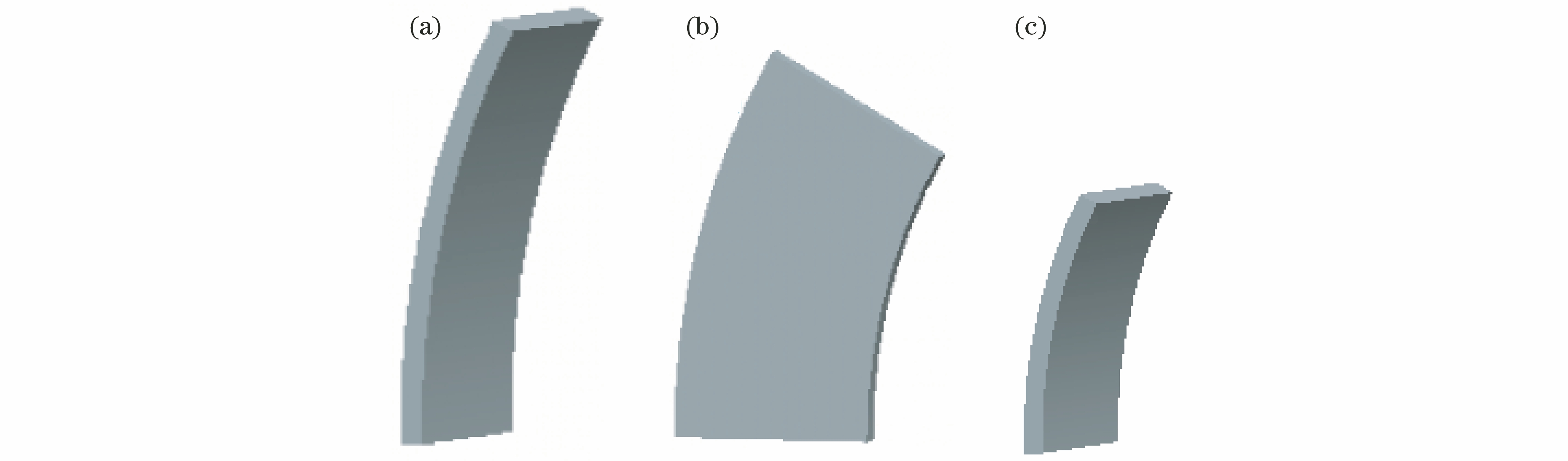
图 9. 模型结构。(a)弧形结构1; (b)扇形结构;(c)弧形结构2
Fig. 9. Model structure. (a) Arc-shaped structure 1; (b) fan-shaped structure; (c) arc-shaped structure 2
采用法向分层的方法,将每个弧形结构划分为若干小的扇形单元。如
式中
弧形结构件成形条件需满足扇形实体单元任意半径处的弧长与该处工作点位置的生长高度一致的条件,即
由于扇形实体单元的熔层高度沿径向线性增加,因此,针对弧形结构件成形提出了一种变姿态熔覆、周向扫描的方法。在变姿态熔覆过程中,激光轴线与已成形表面成一定夹角
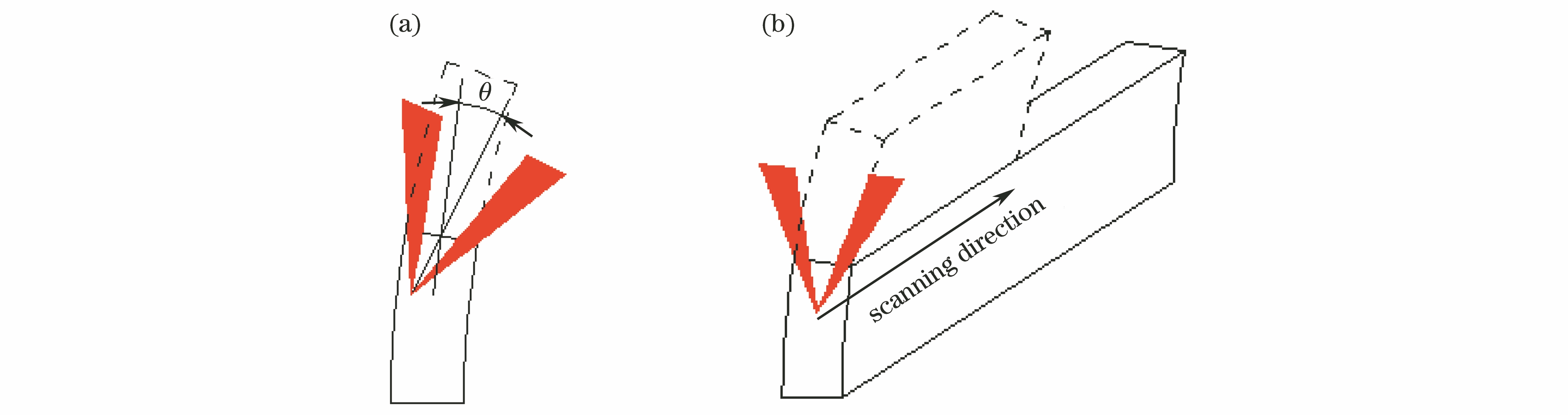
图 11. 弧形结构件熔覆扫描。(a)变姿态熔覆;(b)周向扫描
Fig. 11. Cladding and scanning of arc-shaped structural parts. (a) Variable-attitude cladding; (b) circular scanning
采用法向分层的方法,同样可以将每个扇形结构划分为若干小的扇形单元。由于扇形结构与弧形结构的圆心相同,因此,在任意半径处的弧长仍然满足(6)式,且该处所需的生长高度也满足(5)式。
针对扇形结构件的成形,提出了一种变姿态熔覆、径向扫描的实验方法,如
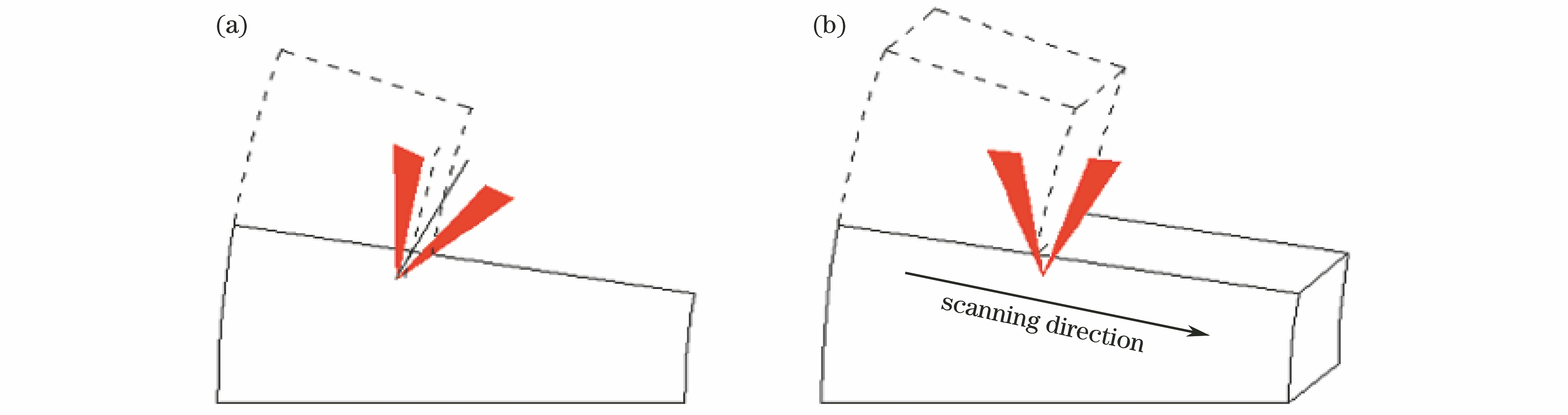
图 12. 扇形结构件熔覆扫描。(a)变姿态熔覆;(b)径向扫描
Fig. 12. Cladding and scanning of fan-shaped structural parts. (a) Variable-attitude cladding; (b) radial scanning
采用变姿态熔覆、周向扫描的方法成形弧形结构,并使激光束在弧形关光端停留0.1 s,以防止端部塌陷;采用变姿态熔覆、径向扫描的方法成形扇形结构。逐层扫描内侧弧形、外侧弧形以及中间连接扇形,进而堆积成形。
4 实验及检测
4.1 实验
在其他工艺参数不变的条件下,选用激光离焦量为-3.5 mm进行实验,熔覆单道的生长高度为0.49 mm,代入(6)式得,半径
采用上述规划轨迹与实验参数进行熔覆成形,实验过程中熔覆喷头光粉耦合性良好,即使在大倾角时也没有火花飞溅,如
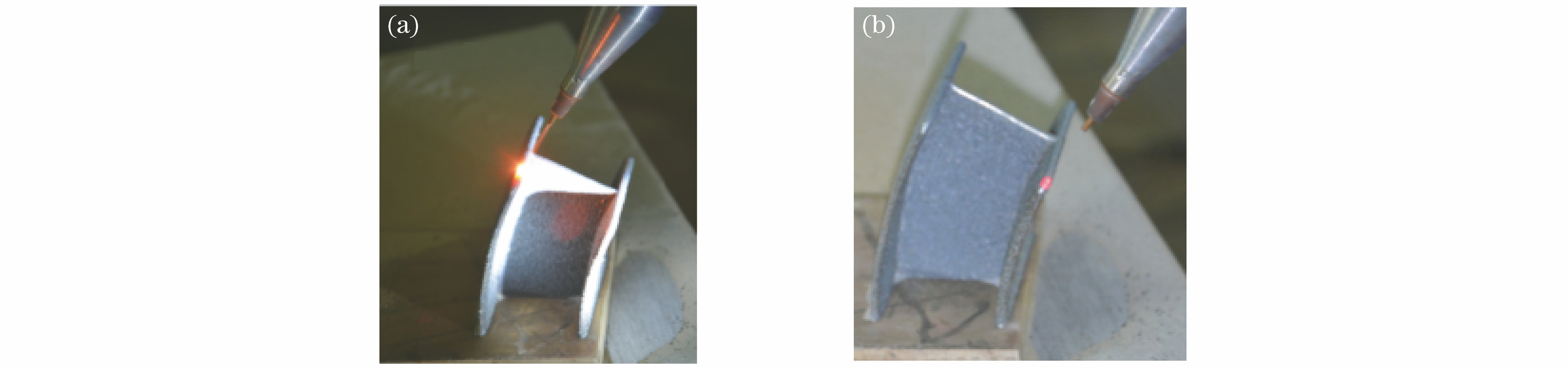
图 13. 成形过程。(a)激光熔覆;(b)调整姿态
Fig. 13. Forming process. (a) Laser cladding; (b) adjusting attitude
4.2 成形件检测
4.2.1 尺寸误差分析
不等高弯曲弧形工字薄壁结构成形件如
在距离端面15 mm处,利用线切割方法将成形件沿曲线1,2,3剖开,如
4.2.2 硬度分析
采用显微硬度计测得弧形1、扇形、弧形2处硬度随角度的变化关系,如
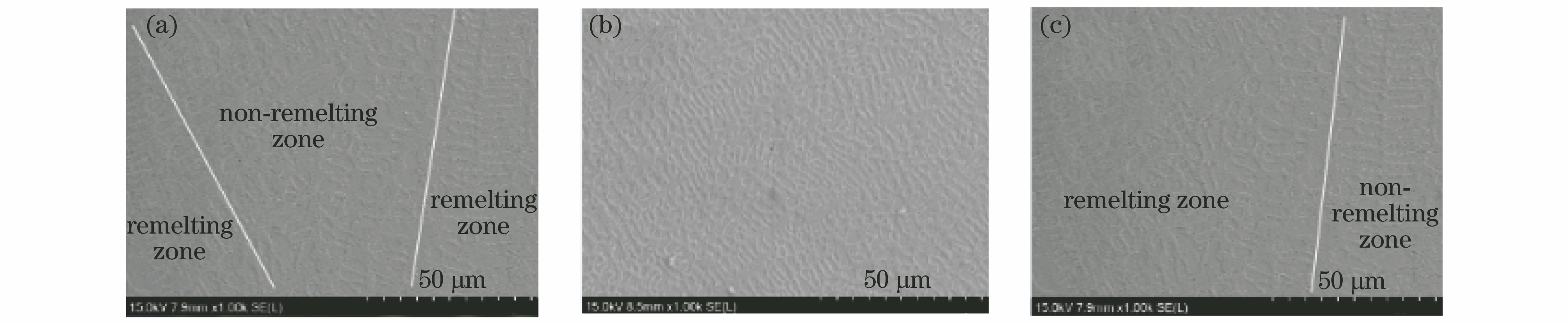
图 18. 成形件显微组织。(a) A处;(b) B处;(c) C处
Fig. 18. Microstructures of formed parts. (a) Location A; (b) location B; (c) location C
4.2.3 组织分析
利用线切割方式,获取
5 结论
针对熔覆层扫描末端的塌陷现象,提出了激光加载防塌陷方法,实现了端部堆积的平整化。当聚焦光束离焦量为-5.5~-2.5 mm时,通过线性拟合,得到了熔道生长高度与离焦量的线性回归方程,成功堆积出了由不等高熔道组成的扇形结构。对成形件进行检测,得到成形件尺寸高度的相对误差最大值为-5.9%,且不同半径处的厚度略有不同,但相同半径处厚度相对均匀;成形件组织致密均匀、无气孔、无裂纹。
[1] 季学荣, 丁晓红. 板壳结构加强筋优化设计方法[J]. 机械强度, 2012, 34(5): 692-698.
[2] MorelloL, Rossini LR, PiaG, et al. The automotive body[M]. Heidelberg: Springer Verlag, 2011: 275- 310.
[3] 陈冬民, 王丽娟, 陈宗渝, 等. 基于等效原理的板壳结构加强筋设计方法[J]. 机械科学与技术, 2015, 34(12): 1841-1845.
[4] 宋建丽, 李永堂, 邓琦林, 等. 激光熔覆成形技术的研究进展[J]. 机械工程学报, 2010, 46(14): 29-39.
[7] 王斌修, 田新国. 浅析激光熔覆成形技术的应用及其发展方向[J]. 制造技术与机床, 2011( 11): 57- 59.
WangBinxiu, TianXinguo. The application and development direction of laser cladding forming technology[J]. Manufacturing Technology and Machine Tool, 2011( 11): 57- 59.
[9] 钟敏霖, 杨林, 刘文今, 等. 激光快速直接制造W/Ni合金太空望远镜准直器[J]. 中国激光, 2004, 31(4): 482-486.
[10] 方琴琴, 傅戈雁, 王聪, 等. 带连接筋双层薄壁件激光直接成形[J]. 中国激光, 2017, 44(2): 0202005.
[11] 董鹏, 陈济轮. 国外选区激光熔化成形技术在航空航天领域应用现状[J]. 航天制造技术, 2014( 1): 1- 5.
DongPeng, ChenJilun. Current status of selective laser melting for aerospace applications abroad[J]. Aerospace Manufacturing Technology, 2014( 1): 1- 5.
Article Outline
邓志强, 石世宏, 周斌, 傅戈雁, 王聪. 不等高弯曲弧形薄壁结构激光熔覆成形[J]. 中国激光, 2017, 44(9): 0902005. Deng Zhiqiang, Shi Shihong, Zhou Bin, Fu Geyan, Wang Cong. Laser Cladding Forming of Unequal-Height Curved Arc-Shaped Thin-Wall Structures[J]. Chinese Journal of Lasers, 2017, 44(9): 0902005.