激光冲击强化对304不锈钢疲劳寿命的影响
下载: 952次
1 引言
激光冲击强化处理(LSP)是一种将光能转化为机械能的先进的表面改性技术,可以提高材料的抗疲劳、耐磨损和抗应力腐蚀等性能[1-5]。与传统的加工工艺(如机械喷丸、滚压等表面强化技术)相比,激光冲击强化具有高压、高效以及超高应变率[6-7]等特点,能够精确控制待冲击处理区域的位置,并能在离试样表面更深的位置处诱导产生残余压应力[8-9]。该技术自20世纪70年代问世来便受到了国内外学者的广泛关注,并得到了快速发展[10]。
近年来,激光冲击强化的研究对象主要是钛铝合金[2-6,8-9,11]。相对于钛铝合金而言,具有良好韧性、耐腐蚀性、耐热性及优良综合力学性能[12-14]的ANSI304不锈钢具有更广泛的应用。孔德军等[15]探讨了激光冲击处理304不锈钢后残余应力产生的微观机理,认为材料表面产生的不能完全恢复的塑性变形是残余压应力产生的主要原因。柳沅汛等[16]采用短脉冲强激光对304奥氏体不锈钢表面进行冲击处理,得出了激光冲击工件表面形貌与塑性变形机制具有对应关系的结论。钟金杉等[17]系统研究了激光冲击对AISI304不锈钢拉伸性能及摩擦磨损性能的影响,发现激光冲击处理可以提高AISI304不锈钢的抗拉强度及磨损性能。李玉琴等[18]的研究表明,经激光冲击处理后,304不锈钢的比磨损率减小,显微硬度从200 HV提高到260 HV。Luo等[13-14]的研究表明,ANSI304奥氏体不锈钢的表面显微硬度、弹性模量等在激光冲击处理后均显著提高。然而,有关激光冲击处理对304不锈钢抗疲劳性能的影响鲜有报道。鉴于此,本文以304不锈钢为研究对象,探讨了激光冲击强化对其抗疲劳性能的影响。利用Rtec Up型三维形貌仪观察激光冲击试样的表面形貌,使用X350A型X射线应力仪对试样表面的残余应力进行测量;采用JSM-6490LV型扫描电子显微镜(SEM)观察试样的断口形貌,并根据疲劳裂纹扩展速率曲线验证激光冲击强化的效果。
2 强化原理及试验
2.1 激光冲击强化的原理
激光冲击强化是利用具有ns量级脉冲宽度、GW量级高功率密度的激光辐射靶材表面,使其表面的吸收层汽化产生高温高压等离子体,并在约束层的作用下形成向靶材内部传播高达GPa量级的应力波,迫使靶材表面产生不可逆的塑性变形,使靶材表层晶粒细化并形成一定深度的残余压应力层。
2.2 试样的准备及试验
304不锈钢的化学成分及室温下的力学性能见
表 1. 304不锈钢的化学成分
Table 1. Chemical composition of 304 stainless steel
|
表 2. 304不锈钢的室温力学性能
Table 2. Mechanical properties of 304 stainless steel at room temperature
|
利用激光束同时冲击试样两侧的指定区域。为了防止金属材料表面被高功率激光烧蚀,同时也为了提高激光能量的利用率,在进行激光冲击试验前,在试样两侧待冲击区域粘贴一层均匀的吸收层。选择3M公司的铝箔作为吸收层,厚度为0.1 mm;将水作为约束层,厚度约为2 mm。激光冲击设备如
采用PLN-100/500型伺服液压机进行疲劳试验,试验设备如
3 试验结果与讨论
3.1 表面形貌及残余应力
经激光双面冲击后,试样的表面形貌如
从
式中:
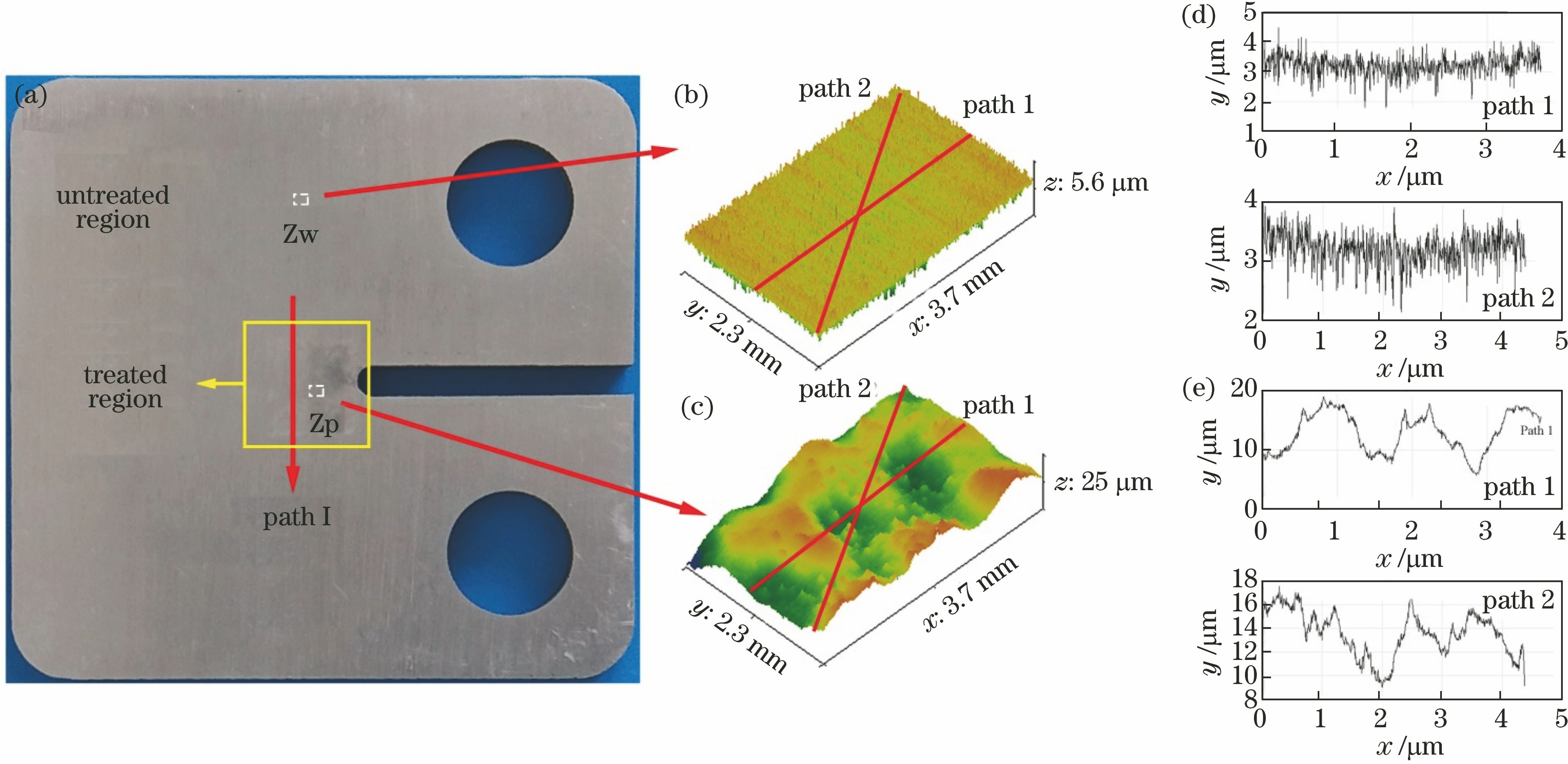
图 5. LSP试样的表面形貌及轮廓曲线。(a)表面宏观形貌;(b)未冲击区的三维形貌;(c)冲击区的三维形貌;(d)未冲击区的轮廓曲线;(e)冲击区的轮廓曲线
Fig. 5. Surface morphology and profile curves of LSP sample. (a) Macro morphology of sample surface; (b) 3D image of un-LSP region; (c) 3D image of LSP region; (d) profile curves of un-LSP region; (e) profile curves of LSP region
3.2 疲劳断口形貌
LSP试样疲劳断口的宏观形貌如
304不锈钢试样断口上疲劳裂纹萌生区域的微观形貌如
由
残余压应力对裂纹源萌生位置的影响如
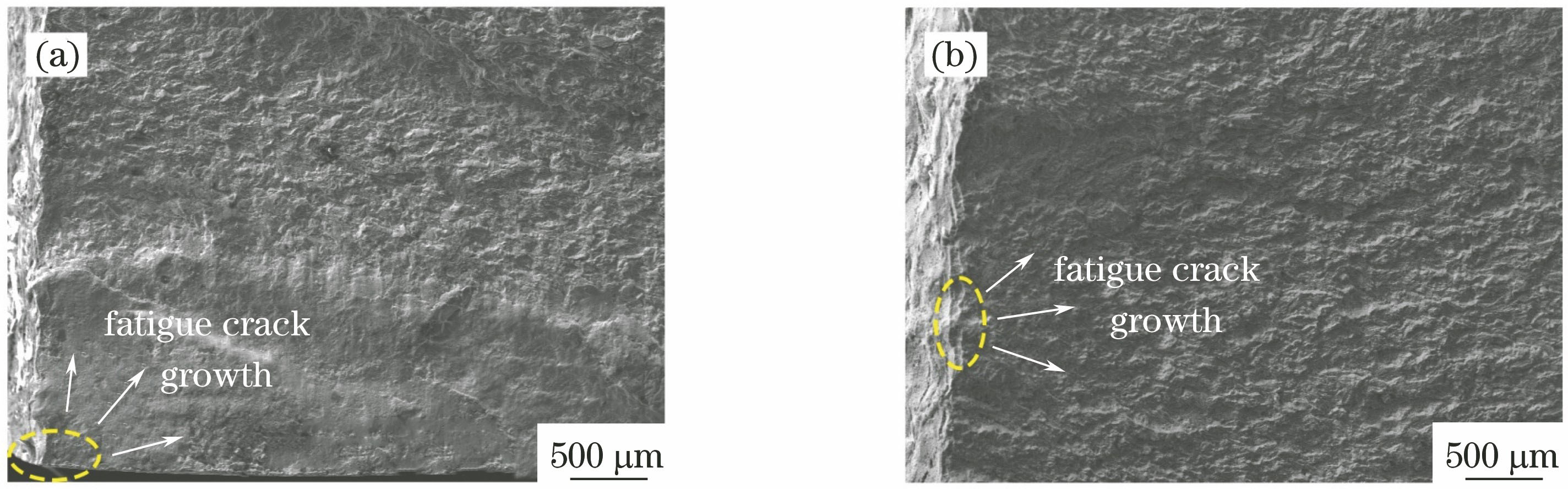
图 8. 疲劳裂纹萌生区的微观形貌。(a) un-LSP试样;(b) LSP试样
Fig. 8. Morphology of fatigue crack initiation region. (a) Sample without LSP; (b) sample with LSP
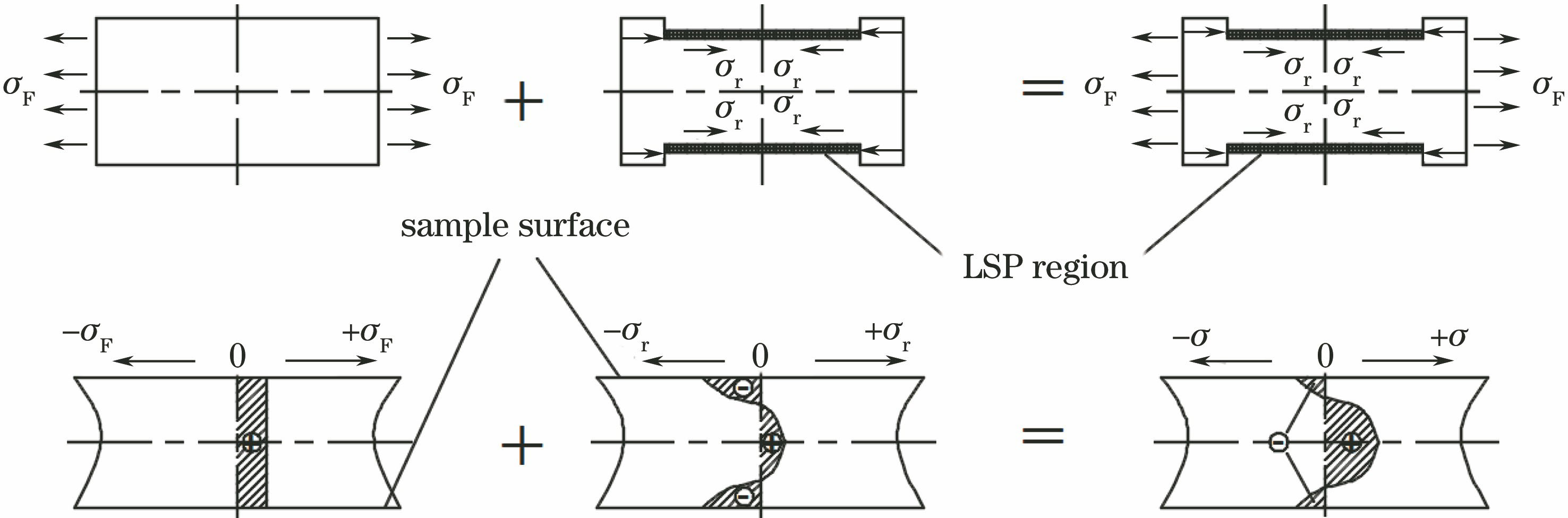
图 9. 残余压应力对裂纹源萌生位置的影响
Fig. 9. Diagram of effect of compressive residual stress on crack initiation
裂纹扩展区的微观形貌如
经过裂纹扩展阶段后,当裂纹扩展至临界尺寸时,试样将发生瞬间断裂。瞬断区的微观形貌如
3.3 疲劳寿命
试样完全断裂时的载荷循环次数见
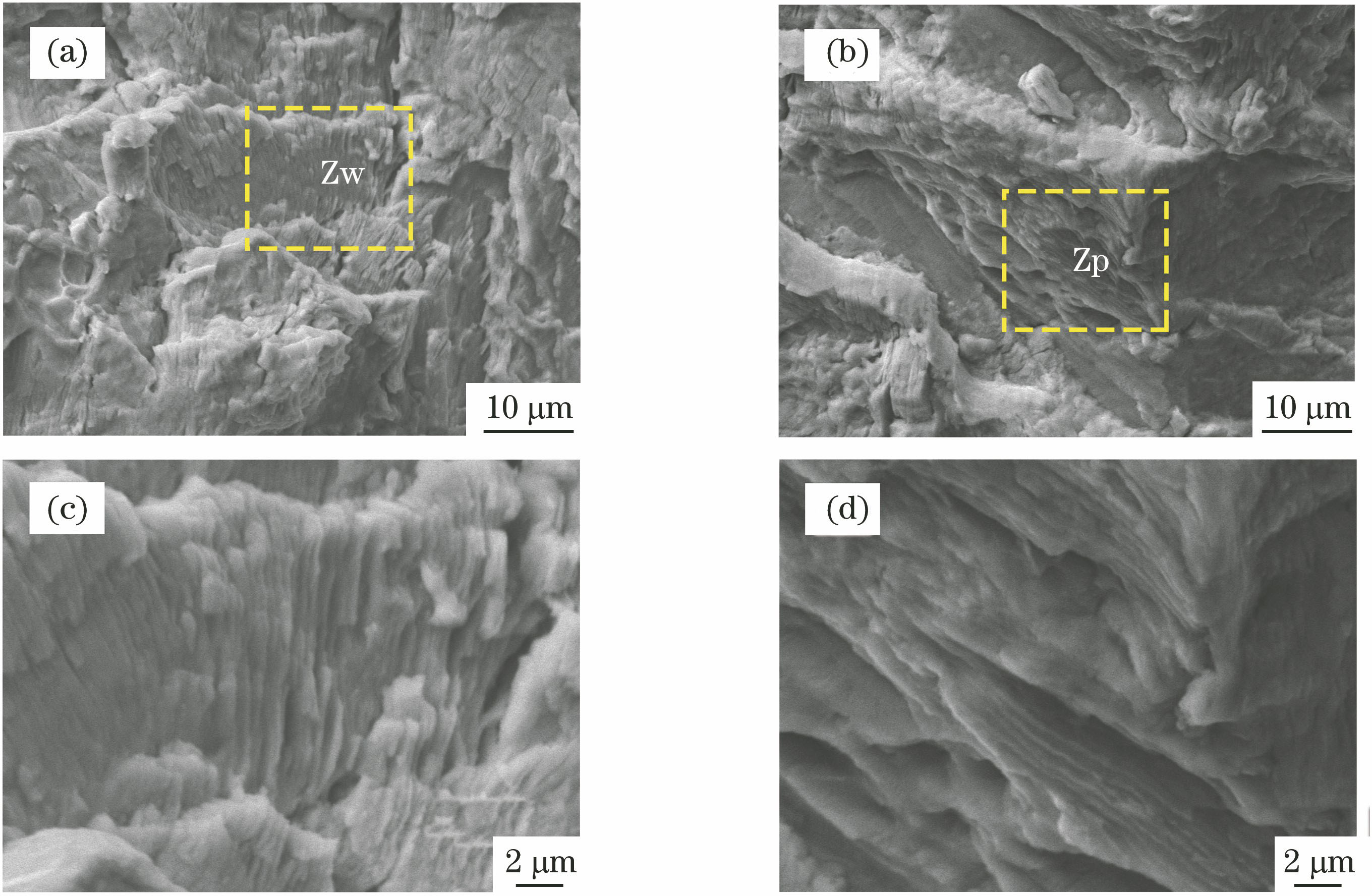
图 10. 裂纹扩展区的微观形貌。(a) un-LSP试样;(b) LSP试样;(c) Zw区的放大图;(d) Zp区的放大图
Fig. 10. Morphology of crack growth zone. (a) Sample without LSP; (b) sample with LSP; (c) enlarged image of Zw region; (d) enlarged image of Zp region
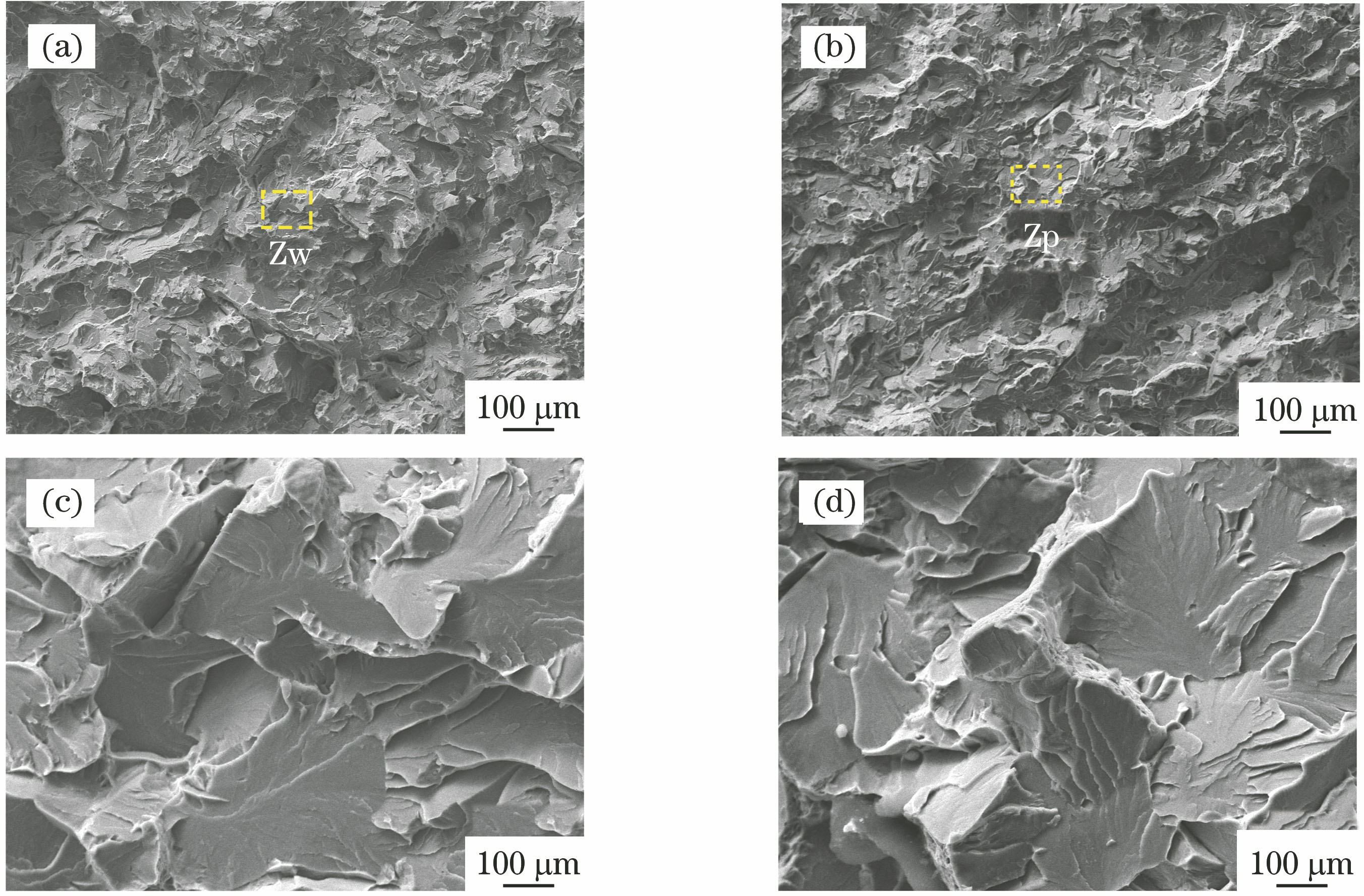
图 11. 瞬断区的微观形貌。(a) un-LSP试样;(b) LSP试样;(c) Zw区的放大图;(d) Zp区的放大图
Fig. 11. Morphology of abrupt fracture zone. (a) Sample without LSP; (b) sample with LSP; (c) enlarged image of Zw region; (d) enlarged image of Zp region
裂,此时的裂纹扩展长度约为31.6 mm;而LSP试样的裂纹扩展长度约为37 mm,对应的载荷循环次数约为356000。由此可见,激光冲击强化处理能够有效地延长304不锈钢的疲劳寿命。
4 结论
采用激光冲击强化技术对304不锈钢试样进行双面冲击强化处理,研究了激光冲击对试样断口形貌及疲劳性能的影响,得到以下结论:
表 3. 试样完全断裂时的载荷循环次数
Table 3. Loading cycle numbers of the specimens in two groups
|
1) 激光双面多点搭接冲击处理可以使304不锈钢表面产生塑性强化区域;
2) 激光冲击处理能够使裂纹源移至试样内部,并减小裂纹的扩展速率;
3) 激光冲击处理能抑制裂纹源的萌生,有效提高304不锈钢的疲劳性能。
[1] 罗开玉, 周阳, 鲁金忠, 等. 激光冲击强化对316L不锈钢熔覆层微观结构和性能的影响[J]. 中国激光, 2017, 44(4): 0402005.
[2] 杨祥伟, 周建忠, 盛杰, 等. TC6钛合金激光喷丸组织演变与表面强化机理[J]. 光学学报, 2017, 37(9): 0914001.
[3] 朱然, 张永康, 孙桂芳, 等. 三维平顶光束激光冲击2024铝合金的残余应力场数值模拟[J]. 中国激光, 2017, 44(8): 0802007.
[4] 李翔, 何卫锋, 聂祥樊, 等. 不同能量空间分布激光冲击钛合金残余应力的分布规律[J]. 激光与光电子学进展, 2018, 55(6): 061402.
[5] 张兴权, 李欢, 黄志来, 等. 7075铝合金激光多点冲击诱导残余应力的数值模拟[J]. 中国激光, 2015, 42(12): 1203002.
[6] KingA, SteuwerA, WoodwardC, et al. Effects of fatigue and fretting on residual stresses introduced by laser shock peening[J]. Materials Science and EngineeringA, 2006, 435/436: 12- 18.
[7] ScherpereelX, PeyreP, FabbroR, et al. Modifications of mechanical and electrochemical properties of stainless surfaces by laser shock processing[C]. Proceedings of SPIE, 1997, 3097: 546- 557.
[10] 吴嘉俊, 赵吉宾, 乔红超, 等. 激光冲击强化技术的应用现状与发展[J]. 光电工程, 2018, 45(2): 170690.
[11] 罗密, 罗开玉, 王庆伟, 等. 激光冲击7075-T6铝合金焊缝的残余应力场数值模拟[J]. 光学学报, 2014, 34(4): 0414003.
[15] 孔德军, 周朝政, 吴永忠. 304不锈钢激光冲击处理后的残余应力产生机理[J]. 红外与激光工程, 2010, 39(4): 736-740.
[16] 柳沅汛, 王曦, 吴先前, 等. 激光冲击处理304不锈钢表面的形貌特征及其机理分析[J]. 中国激光, 2013, 40(1): 0103004.
[17] 钟金杉, 鲁金忠, 罗开玉, 等. 激光冲击对AISI304不锈钢拉伸性能和摩擦磨损性能的影响[J]. 中国激光, 2013, 40(5): 0503002.
[18] 李玉琴, 王学德, 宋飞龙, 等. 激光冲击304不锈钢微观组织和性能研究[J]. 红外与激光工程, 2016, 45(10): 1006005.
[20] 孙汝剑, 朱颖, 郭伟, 等. 激光冲击强化对TC17表面形貌及残余应力场影响的有限元数值模拟研究[J]. 塑性工程学报, 2017, 24(1): 187-193.
汪军, 李民, 汪静雪, 张兴权, 魏伟, 戚晓利, 王会廷. 激光冲击强化对304不锈钢疲劳寿命的影响[J]. 中国激光, 2019, 46(1): 0102003. Wang Jun, Li Min, Wang Jingxue, Zhang Xingquan, Wei Wei, Qi Xiaoli, Wang Huitin. Effects of Laser Shock Processing on Fatigue Life of 304 Stainless Steel[J]. Chinese Journal of Lasers, 2019, 46(1): 0102003.