基于ROI-RSICP算法的车轮廓形动态检测
下载: 948次
1 引言
车轮的质量对列车的运行速度有着重要的影响,随着重型铁路运输的增加,服役车轮的磨耗加剧,车轮磨耗的加剧严重影响到列车行驶的安全性、稳定性和舒适性。因此,定期在线检测车轮廓形对铁路安全具有极其重要的意义,它不仅保证了列车运行的安全,对车轮的日常维护和镟修也起着指导作用。
车轮廓形测量分为静态测量和动态测量。静态测量是采用专用机械卡尺(第四种检查器)或者自动测量设备进行测量的方法。采用第四种检查器测量的方法具有携带和操作方便等优点,目前仍广泛应用于铁路车轮测量,但测量效率低,且只能测量部分车轮廓形几何参数,无法获取车轮廓形完整的磨耗形态。静态自动测量采用便携式光学设备实现对车轮的静态非接触式测量[1-5],该方法具有较高的精度,但通常只能在车辆段进行测量,且通常需将车轮从车身拆离,占用的列车周转时间较长,效率较低。随着传感器和计算机信息技术的发展,动态测量方法由于具有实时测量的能力且不影响铁路正常运行的优势,在车轮廓形检测中得到了广泛的应用[6-11]。Chen等[8]采用两个结构光视觉传感器获取车轮内外侧廓形,并通过ICP算法将两个廓形拼接成完整的廓形以获取车轮的踏面磨耗。然而,该方法未对动态获取的车轮廓形畸变进行校正,因此检测结果存在一定的误差。Xing等[9]采用四个二维激光传感器动态获取完整车轮廓形,并从中选取畸变最小的廓形来计算轮缘厚度、轮缘高度与车轮直径。该方法虽然精度较高,但成本高且传感器的安装精度对实验结果的影响较大。因此,使用单线激光准确地检测车轮廓形仍是一个挑战。
车轮廓形检测的重要步骤之一是利用标准车轮廓形来精确校正测量车轮廓形。这一过程涉及到点云配准问题,最常用的一种点云配准算法是ICP算法,它通过最小化距离平方差和,迭代匹配两个点集[12-13]。但是,由于动态测量的车轮廓形产生了仿射变形,因此传统ICP算法无法对车轮廓形进行精确校正。近年来,针对仿射变换的问题,研究者提出了加入缩放系数的迭代最近邻 (Scaling ICP, SICP)算法[14-16]。然而,它不能有效且准确地将测量车轮廓形的未磨耗部分和磨耗部分与标准车轮廓形进行配准。因此,本文提出了一种校正畸变车轮廓形的方法。首先,通过安装在钢轨外侧的线激光传感器动态获取车轮廓形。然后通过PointNet深度学习网络将激光传感器动态获取的车轮廓形点集分割成两部分:磨耗感兴趣区域(region of interest,ROI)与非磨耗部分,并将权重函数引入到SICP算法中,实现了仿射变形的磨耗车轮廓形与标准车轮廓形的精确配准。
2 问题概述
2.1 车轮廓形的拉伸变形
当激光平面与车轮表面的交线不过轮心时,车轮廓形产生畸变,如
假设采集的畸变车轮廓形点集中任意一点为pi'(
式中: 旋转矩阵R=
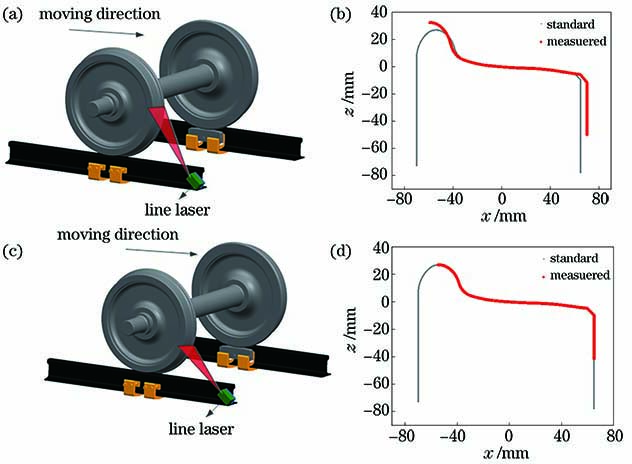
图 1. 不同情况下的测量车轮廓形示意图。(a)激光平面与车轮表面的交线不过轮心;(b)畸变车轮廓形;(c)激光平面与车轮表面的交线过轮心;(d)无畸变车轮廓形
Fig. 1. Measured wheel profiles under different situations. (a) Intersection line of laser plane and wheel surface not crossing wheel axis; (b) wheel profile with distortion; (c) intersection line of laser plane and wheel surface crossing wheel axis; (d) wheel profile without distortion
2.2 车轮廓形磨耗演变
轨道车辆车轮廓形主要由踏面(tread)、轮缘(flange)以及踏面内外侧基线(inner/outer baseline)组成,车轮与钢轨接触部分称为踏面,车轮踏面内侧的圆周凸缘称为轮缘[17]。列车在直线行驶的路段,只有车轮踏面与钢轨接触;在曲线行驶的路段,部分轮缘也与钢轨发生接触[18]。
3 车轮廓形动态配准算法
3.1 Scaling ICP算法简介
我们的目标是准确地解决涉及仿射变换的车轮廓形点云配准问题,最常用的仿射变换点云配准算法是SICP算法。假设测量点集为P={pi,i=1,2,3,…},参考模型点集Q={qj,j=1,2,3,…}。SICP配准算法的目标函数[19-20]可以表示为
式中:det(·)为行列式;diag(·)为对角矩阵;s1,s2,…,sj为j个维度上的缩放比例;pi 、qj为点向量;I为单位矩阵。SICP算法处理涉及仿射变换的点集配准问题主要有两步。
第一步,根据(Rk,Sk,Tk)变换后的待配准点云,构建最近邻点对集为
式中:Rk为第k次迭代对应的旋转矩阵;Sk为第k次迭代对应的缩放矩阵;Tk为第k次迭代对应的平移矩阵。
第二步,根据第一步得到的近邻点集,通过最小平方距离法计算新的变换矩阵:
式中:qc(i)为经过第k次迭代后的参考模型点集中的第i个点向量。
3.2 ROI-reweighted scaling ICP算法
SICP算法虽能解决点集的仿射变换问题,却无法解决磨耗车轮廓形ROI与标准车轮廓形不同导致的配准不精确的问题。因此,需要对车轮廓形ROI与非磨耗区域分别赋予不同的权重,以保证磨耗车轮廓形与标准车轮廓形的精确配准。调整车轮廓形ROI与非磨耗区域权重的前提是先提取ROI,本文采用PointNet[21]点云分割网络实现车轮廓形ROI的提取,该网络是美国斯坦福大学于2016年提出的一种新型的用于点云分类和分割的神经网络,具体网络结构图如
对于ROI内的点对,由于其形状与标准车轮廓形对应部分相差大,因此对其赋予较小的权值。对于非磨耗部分的点对,引入柯西权函数[22],进行迭代重加权,以提高算法鲁棒性,并确保当非磨耗部分点集中包含离群点时,算法依然能够有效运行。具体权重函数定义为
式中:RROI为感兴趣区;ri为pi与最邻近点qi的欧氏距离;kca为柯西函数调优常数值。
将权函数引入SICP算法以提高算法的准确度,并提出感兴趣域的加权尺度迭代最近邻 (ROI-Reweighted Scaling ICP,ROI-RSICP) 算法 ,该算法的目标函数可表示为
令
显然,(8)式中变量只剩下S和R,令
则
对S求偏导并求极值得
得到S为
化简(10)式为
当S是定值时,
式中:tr(·)为矩阵的迹;W为权重矩阵;Y为以yi为矩阵元的矩阵;X为以xi为矩阵元的矩阵。
计算协方差矩阵H=SXWYT,并对H进行奇异阵分解,即可得到旋转矩阵R,奇异阵分解的详细步骤参考文献[ 23]。
4 车轮廓形动态检测流程
5 实验与分析
5.1 ROI提取效果分析
为了验证ROI提取效果,实验分别采集了无磨耗轮对、轻微磨耗轮对以及严重磨耗轮对三种不同磨耗程度轮对的数据,其中包含无磨耗车轮廓形1997个,轻微磨耗车轮廓形2995个,严重磨耗车轮廓形3000个。为了对PointNet神经网络进行训练,首先对获取的磨耗车轮廓形数据进行手动分割标记,将磨耗区域点云数据标记为0,将非磨耗区域点云数据标记为1。在进行神经网络训练时,将获取的7992个轮对磨耗数据中的70%(5594个)作为训练数据,30%(2198个)作为测试数据。PointNet神经网络训练总损失如
PointNet的分割准确度通常采用基于点的平均交并比(mIoU)作为评价指标[13],交并比(IoU)即模型提取的ROI结果与标记结果的交叠率[27]。我们将100次训练的mIoU进行可视化处理,结果如
选取了部分不同旋转角度下不同磨耗程度的车轮廓形,其ROI提取结果如
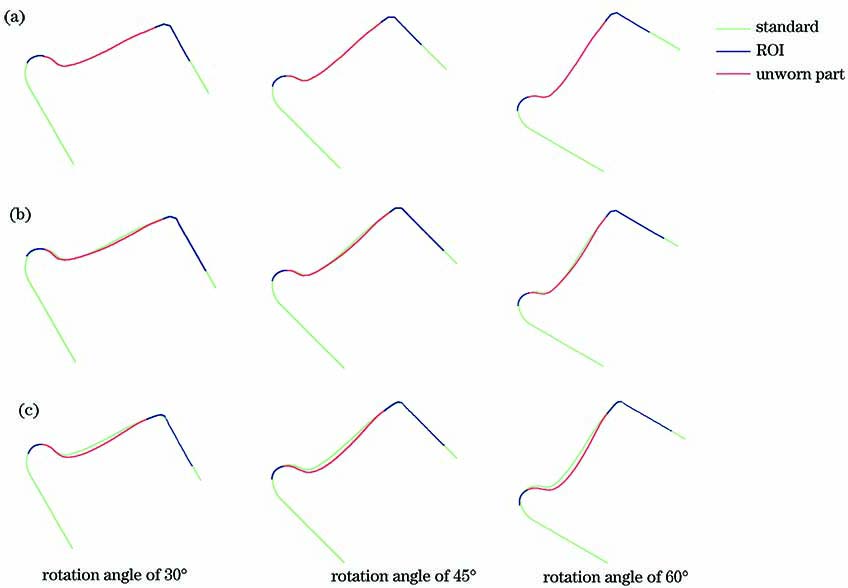
图 7. 基于PointNet提取的ROI部分结果图。(a)无磨耗;(b)轻度磨耗;(c)重度磨耗
Fig. 7. Partial results of extracted ROI based on PointNet. (a) Standard; (b) slightly worn; (c) badly worn
5.2 ROI-RSICP算法的配准精度分析
为了分析ROI-RSICP算法的精度,提取了标准车轮廓形的部分廓形,并对其进行各向同尺度缩放处理,然后将车轮廓形旋转30°,以模拟激光传感器动态获取的畸变无磨耗车轮廓形。最后,同时采用ICP、SICP和ROI-RSICP算法配准模拟的车轮廓形,并用Hausdorff距离算法对配准结果进行可视化处理,如
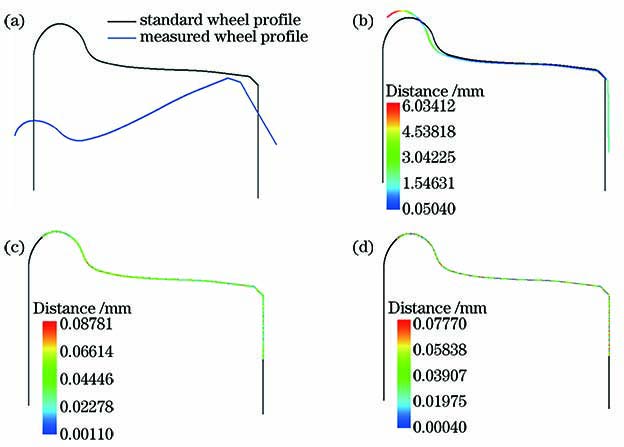
图 8. ICP、SICP与本文算法的配准精度对比。(a) 原始模型;(b) ICP;(c) SICP;(d) ROI-RSICP
Fig. 8. Accuraccy comparison among ICP, SICP and proposed methods. (a) Original model; (b) ICP; (c) SICP; (d) ROI-RSICP
由于经典的ICP算法只考虑点集间的旋转与平移,不能计算点集间的仿射系数,因此车轮轮缘部分廓形严重偏离标准车轮,如
5.3 ROI提取精度对车轮廓形配准结果的影响分析
为了分析ROI的提取精度对本文算法配准结果的影响,实验采用不同磨耗程度的车轮廓形并模拟IoU值为65%~100%时配准的结果的变化,如
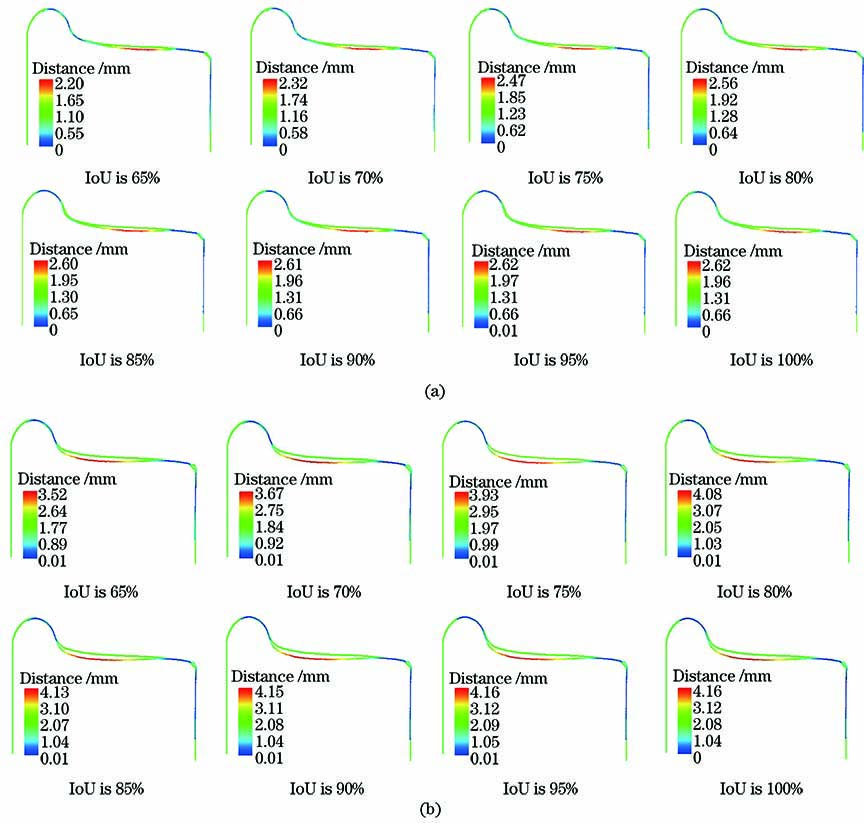
图 9. 不同IoU值下的车轮廓形配准结果图。(a)轻微磨耗;(b)严重磨耗
Fig. 9. Registration results of wheel profile under different IoU values. (a) Slightly worn; (b) badly worn
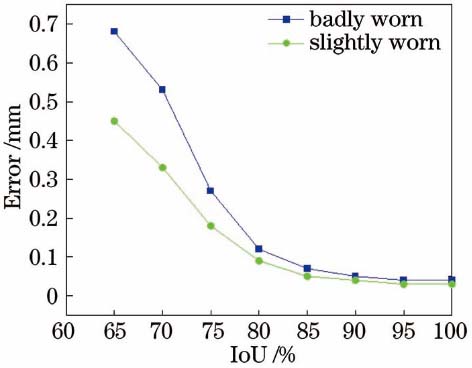
图 10. 本文方法检测结果与第四种检查器检测结果的差值随IoU的变化
Fig. 10. Difference between inspection result by proposed method and that by the 4th kind of inspector versus IoU
5.4 ROI-RSICP算法的稳定性分析
由于动态检测过程中,激光平面与车轮表面交线处法线的夹角不断变化,并且随着夹角的变大,车轮廓形产生的仿射变形也越大。为了验证本文算法的稳定性,在30°~60°角度下获取重度磨耗车轮某一位置处的车轮廓形,用ICP、SICP和ROI-RSICP算法分别对车轮廓形进行配准,并通过Hausdorff距离算法对配准结果进行可视化处理,配准结果如
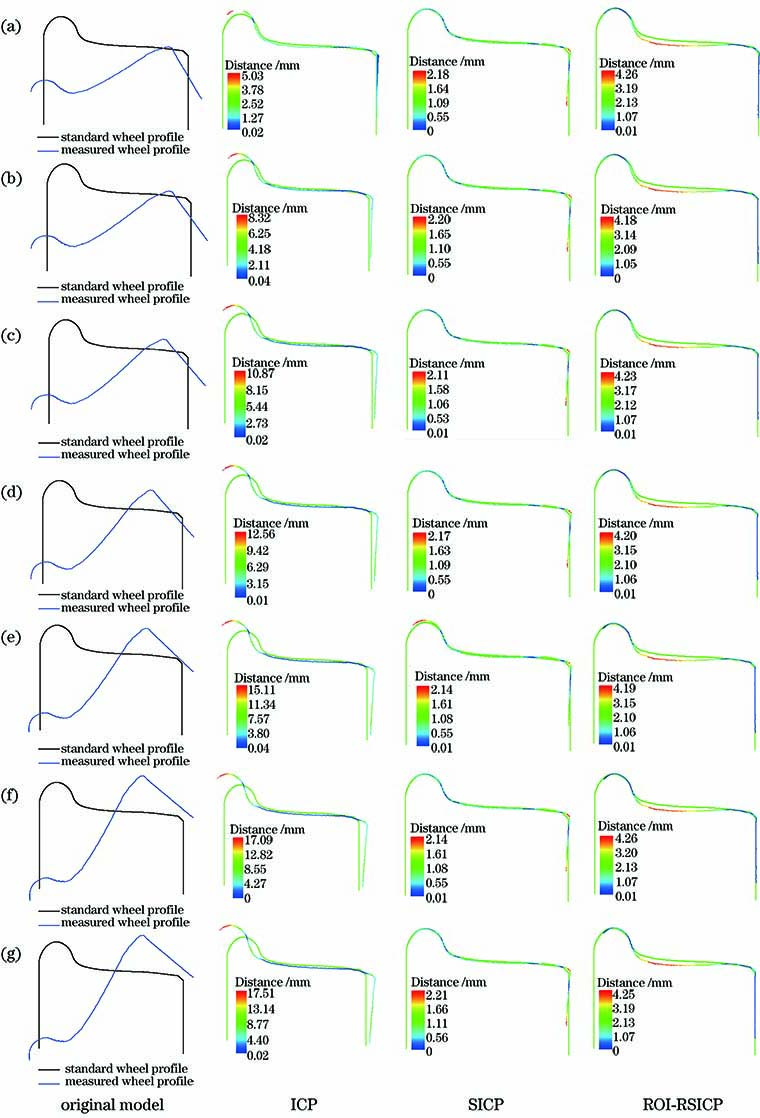
图 11. 不同夹角下 ICP、SICP与本文算法的稳定性比较。(a) 30°;(b) 35°;(c) 40°;(d) 45°;(e) 50°;(f) 55°;(g) 60°
Fig. 11. Stability comparison of ICP, SICP and proposed methods under different included angles. (a) 30°; (b) 35°; (c) 40°; (d) 45°; (e) 50°; (f) 55°; (g) 60°
从
5.5 不同磨损程度对测量精度的影响
为了分析不同磨损程度对测量精度的影响,将ROI-RSICP算法获取的车轮踏面磨耗(tread wear)与人工检测值进行对比。 ICP、SICP、ROI-RSICP算法与第四种检查器检测的轻微磨耗和严重磨耗车轮的6个位置(Position 1~6)处的踏面磨耗值如
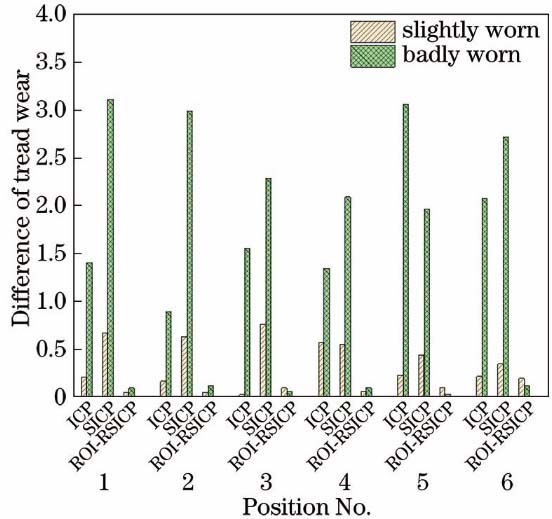
图 12. 各算法计算的踏面磨耗值与第四种检查器检测结果的差值
Fig. 12. Difference between tread wear calculated by each method and result measured by the 4th kind of inspector
表 1. ICP、RSICP、ROI-RSICP算法与人工方法检测的踏面磨耗值
Table 1. Tread wear detected by ICP, SICP, ROI-RSICP and artificial methods unit: mm
|
5.6 测量不确定度分析
由于车轮轮缘内侧面几乎没有磨耗,因此,可以将配准后的车轮廓形与标准车轮廓形轮缘内侧部分进行数据融合,以获取完整的车轮廓形,从而计算车轮轮缘高度(flange height)、轮缘厚度(flange thickness)以及踏面磨耗。
为了分析本文所提方法检测结果的不确定度,将严重磨耗车轮置于钢轨上,人工推动严重磨耗车轮通过检测装置,实验重复6次,以验证本文所提方法检测结果的可重复性。实验采用的轮对踏面为严重磨损的LM型踏面。
从
表 2. 严重磨耗车轮的重复检测结果
Table 2. Repeated detection results of badly worn wheel unit: mm
|
5.7 动态车轮几何参数的检测实验
为验证本文方法在动态检测中的应用情况,选取试验车磨耗较为均匀的车轮进行列车进站的动态检测模拟实验。实验标记车轮磨耗均匀的部分作为检测目标区域,设计传感器与试验车目标车轮区域的位置,使试验车通过传感器检测装置时,检测区域与目标区域重合。选取车轮检测区域内不同截面处的6组车轮廓形,通过ROI-RSICP算法配准后计算这6组车轮廓形的轮缘高度、轮缘厚度和踏面磨耗,同时采用第四种检查器检测该范围内6个位置处车轮的几何参数值。由于检测范围内的车轮表面磨耗较为均匀,不同位置处的车轮廓形几何参数值相差极小,可近似认为第四种检查器与ROI-RSICP算法检测的是同一个廓形,实验所获取数据如
表 3. 车轮几何参数的动态检测结果
Table 3. Dynamic inspection results of wheel geometric parameters unit: mm
|
6 结论
提出了一种基于感兴趣域的加权尺度迭代最近邻算法,实现了带有仿射畸变的磨耗车轮廓形的动态检测。该算法通过PointNet深度学习神经网络,实现了磨耗车轮廓形数据中磨耗感兴趣域部分的提取,并通过对车轮磨耗部分和非磨耗部分赋予不同权值,实现了带有仿射畸变的车轮廓形的校正。对于带有仿射畸变的非磨耗车轮廓形和磨耗车轮廓形的配准,通过对比ICP、Scaling ICP以及本文算法的结果,分析验证了本算法的准确性和稳定性。同时,对于带有仿射畸变的磨耗车轮廓形与标准廓形的匹配,将动态检测结果与人工检测结果进行对比,验证了本文方法的准确性和鲁棒性。因此所提算法能够满足车轮廓形动态检测的精度要求,对车轮镟修具有重要意义。
[1] 张红波, 叶海建. 基于图像处理的轮对磨耗值检测方法的研究[J]. 机械, 2004, 31(8): 51-53.
[2] Feng Q B, Chen S. New method for automatically measuring geometric parameters of wheel sets by laser[J]. Proceedings of SPIE, 2003, 5253: 110-113.
[3] Torabi M. Mousavi S G M, Younesian D. A high accuracy imaging and measurement system for wheel diameter inspection of railroad vehicles[J]. IEEE Transactions on Industrial Electronics, 2018, 65(10): 8239-8249.
[4] 陈瀚, 张思瑾, 高见, 等. 基于多个线激光传感器旋转扫描的铸钢车轮在线三维测量技术[J]. 中国激光, 2019, 46(7): 0704006.
[5] 李淼成, 杨岳, 易兵, 等. RC-IRLSCF方法及其服役车轮踏面线激光检测应用[J]. 中国激光, 2020, 47(9): 0904005.
[8] Chen X M, Sun J H, Liu Z, et al. Dynamic tread wear measurement method for train wheels against vibrations[J]. Applied Optics, 2015, 54(17): 5270-5280.
[9] Xing Z Y, Chen Y J, Wang X H, et al. Online detection system for wheel-set size of rail vehicle based on 2D laser displacement sensors[J]. Optik, 2016, 127(4): 1695-1702.
[10] Gao Y, Feng Q B, Cui J Y. A simple method for dynamically measuring the diameters of train wheels using a one-dimensional laser displacement transducer[J]. Optics and Lasers in Engineering, 2014, 53: 158-163.
[11] Cheng X Q, Chen Y J, Xing Z Y, et al. A novel online detection system for wheelset size in railway transportation[J]. Journal of Sensors, 2016, 2016: 9507213.
[12] Besl P J. McKay N D. A method for registration of 3-D shapes[J]. IEEE Transactions on Pattern Analysis and Machine Intelligence, 1992, 14(2): 239-256.
[13] 侯彬, 金尚忠, 王赟, 等. 点云配准方法在粗配准中的比较[J]. 激光与光电子学进展, 2020, 57(8): 081502.
[14] 王畅, 舒勤, 杨赟秀, 等. 带方差补偿的多向仿射变换点云配准算法[J]. 光学学报, 2019, 39(2): 0215002.
[15] Du S Y, Zheng N N, Xiong L, et al. Scaling iterative closest point algorithm for registration of m-D point sets[J]. Journal of Visual Communication and Image Representation, 2010, 21(5/6): 442-452.
[16] 唐志荣, 刘明哲, 蒋悦, 等. 基于典型相关分析的点云配准算法[J]. 中国激光, 2019, 46(4): 0404006.
[17] 高岩, 邵双运, 冯其波. 一种激光扫描自动测量轮对几何参数的方法[J]. 中国激光, 2013, 40(7): 0708005.
[18] 严隽耄, 傅茂海. 车辆工程[M]. 3版. 北京: 中国铁道出版社, 2008: 37- 50.
Yan JM, Fu MH. Vehicle engineering[M]. 3rd ed. Beijing: China Railway Publishing House, 2008: 37- 50.
[19] Yang Y, Liu L, Yi B, et al. Dynamic inspection of a rail profile under affine distortion based on the reweighted-scaling iterative closest point method[J]. Measurement Science and Technology, 2019, 30(11): 115202.
[20] Yang Y, Liu L, Li M C, et al. Sparse scaling iterative closest point for rail profile inspection[J]. Journal of Computing and Information Science in Engineering, 2019, 20(1): 011003.
[21] Charles RQ, SuH, Mo KC, et al. PointNet: deep learning on point sets for 3D classification and segmentation[C]∥2017 IEEE Conference on Computer Vision and Pattern Recognition (CVPR), July 21-26, 2017, Honolulu, HI, USA. New York: IEEE, 2017: 77- 85.
[23] SorkineO, AlexaM. As-rigid-as-possible surface modeling[C]∥Proceedings of the Fifth Eurographics Symposium on Geometry Processing (SGP), July 4-6, 2007, Barcelona, Spain. Demark: ACM, 2007: 109- 116.
[24] Arun KS, Huang TS, Blostein S D. Least-squares fitting of two 3-D point sets[J]. IEEE Transactions on Pattern Analysis and MachineIntelligence, 1987, PAMI-9( 5): 698- 700.
[25] Yang Y, Liu L, Yi B, et al. An accurate and fast method to inspect rail wear based on revised global registration[J]. IEEE Access, 2018, 6: 57267-57278.
[26] Huttenlocher D P, Klanderman G A, Rucklidge W J. Comparing images using the Hausdorff distance[J]. IEEE Transactions on Pattern Analysis and Machine Intelligence, 1993, 15(9): 850-863.
[27] Alberto GG, Sergio OE, SergiuO, et al. ( 2017-08-22) [2020-05-29]. https:∥arxiv.org/pdf/1704.06857.pdf.
Article Outline
易倩, 钟浩宇, 刘龙, 刘文龙, 易兵. 基于ROI-RSICP算法的车轮廓形动态检测[J]. 中国激光, 2020, 47(11): 1104006. Yi Qian, Zhong Haoyu, Liu Long, Liu Wenlong, Yi Bing. Dynamic Inspection of Wheel Profile Based on ROI-RSICP Algorithm[J]. Chinese Journal of Lasers, 2020, 47(11): 1104006.