基于非接触测量的搭接激光焊缝表面质量评估
下载: 1024次
1 引言
激光焊具有热量集中、焊接变形小等优势,在轨道交通及汽车行业得到了广泛应用[1-2]。目前,因对于不锈钢城轨车车体侧墙的外观要求较高,通常采用半熔透搭接激光焊接头(内侧母材全熔透,外侧母材半熔透)[3-5],其特殊的接头形式使得难以进行对焊接质量的非破坏性检测。有研究表明,激光脉冲的能量、激光束的光斑直径、母材钢板的装配间隙等焊接过程参数不仅影响激光焊的熔深[6-7],还会对接头的表面质量造成一定影响[8-11]。搭接激光焊缝的表面质量(一般指表面余高/下塌量)能够在一定程度上反映焊接过程参数的变化[12-15],因而可用于焊接质量的辅助评估。轨道车辆焊接常用标准EN15083对激光焊接质量的评价也涉及到了对焊缝余高的要求,因此,对激光焊缝表面质量的检测具有较为重要的意义。
不锈钢城轨车体的激光焊接头一般为薄板窄焊缝结构,其焊缝表面余高/下塌量尺度微小(一般小于1 mm)。目前的焊缝表面检测主要依靠肉眼观察或百分表等简单的测量方法实现,检测过程的精确性既难以满足测量精度的要求,也无法适应生产节奏。非接触式激光测距技术具有精度高、测量速度快等优势,在表面质量检测、工件装配间隙测量等领域应用较为广泛[16-17]。本文采用非接触式激光测距技术对激光焊接头的表面进行定位扫描式检测,并通过对检测结果的图像进行处理及修正,实现了激光焊接头表面余高/下塌量的智能计算,为激光焊接头的质量评估提供了技术支持。
2 试验方法
2.1 样件制备
本试验采用轨道车辆不锈钢车体常用的SUS304奥氏体不锈钢板材,其化学成分和力学性能分别如
表 1. SUS304不锈钢的化学成分
Table 1. Chemical compositions of SUS304 stainless steel
|
表 2. SUS304不锈钢的力学性能
Table 2. Mechanical properties of SUS304 stainless steel
|
采用两块长宽组合为150 mm×50 mm的钢板进行焊接,焊缝接头形式为搭接半熔透焊,即上板全熔透,下板半熔透的焊接方式,如
表 3. 母材及垫片厚度组合
Table 3. Thickness combinations of base metal and gasket plate
|
2.2 非接触式激光检测原理及检测方法
本文采用单点式三角激光测距传感器对激光焊缝的表面进行检测,检测原理如
通过计算机控制,采用步进电机驱动激光测距传感器,实现在激光焊缝表面的步进式扫描,激光测距传感器在每个步进点发射/接收激光信号,计算当前点的高度,所有检测节点的高度信息组成扫查线上的激光焊缝表面状态。检测方式如
为验证激光焊缝表面质量检测的结果,沿着如
3 检测结果及讨论
3.1 激光焊接头的金相连接状态分析
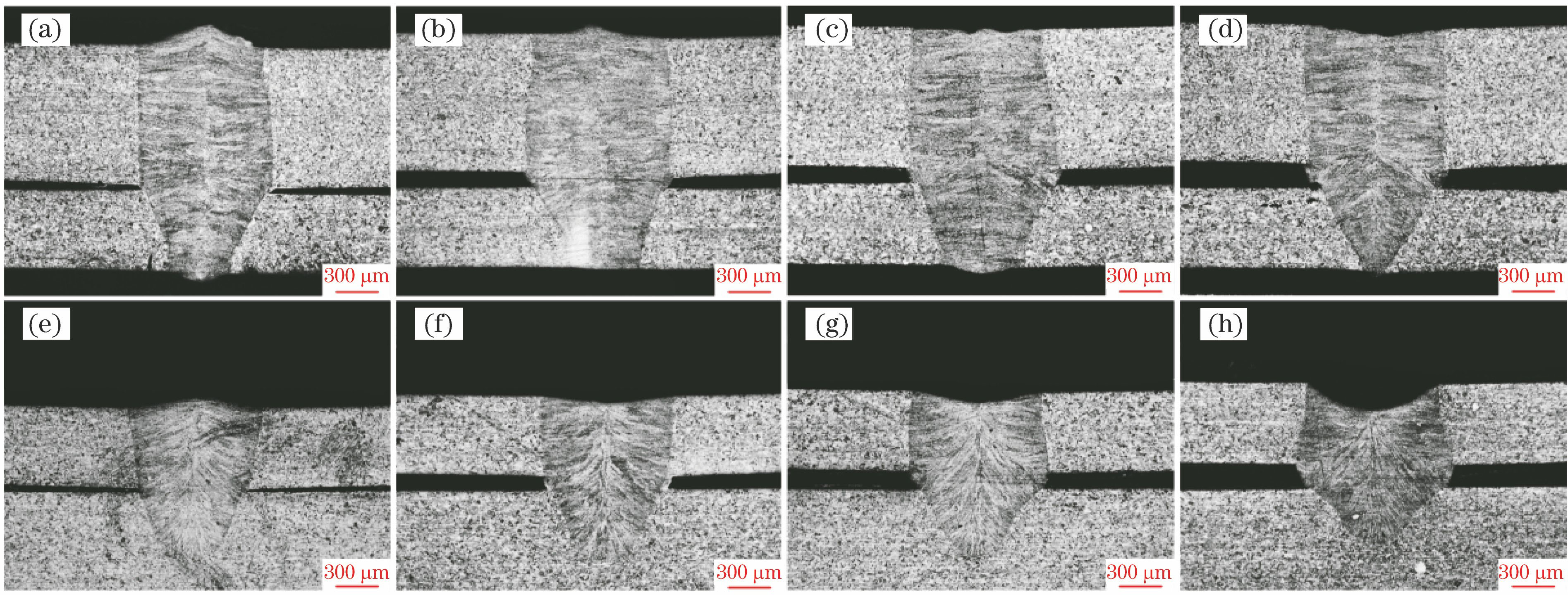
图 5. 激光焊缝横截面的金相形貌。(a)~(d)上下板厚组合为1 mm+0.6 mm,垫片厚度分别为0.04,0.08,0.12,0.2 mm;(e)~(h)上下板厚组合为0.6 mm+2 mm,垫片厚度分别为0.04,0.08,0.1,0.12 mm
Fig. 5. Metallographic morphologies of laser welding joint sections. (a)-(d) Base metal thickness combination is 1 mm+0.6 mm, and gasket thicknesses are 0.04 mm, 0.08 mm, 0.12 mm, and 0.2 mm, respectively; (e)-(h) base metal thickness combination is 0.6 mm+2 mm, and gasket thicknesses are 0.04 mm, 0.08 mm, 0.1 mm, and 0.12 mm, respectively
当焊接方向改为薄板侧施焊时,由于需要完全熔透的上板厚度较小,在施焊时焊接热输入量通常较小,因此上下板间隙的变化对接头表面轮廓的影响更为明显,在
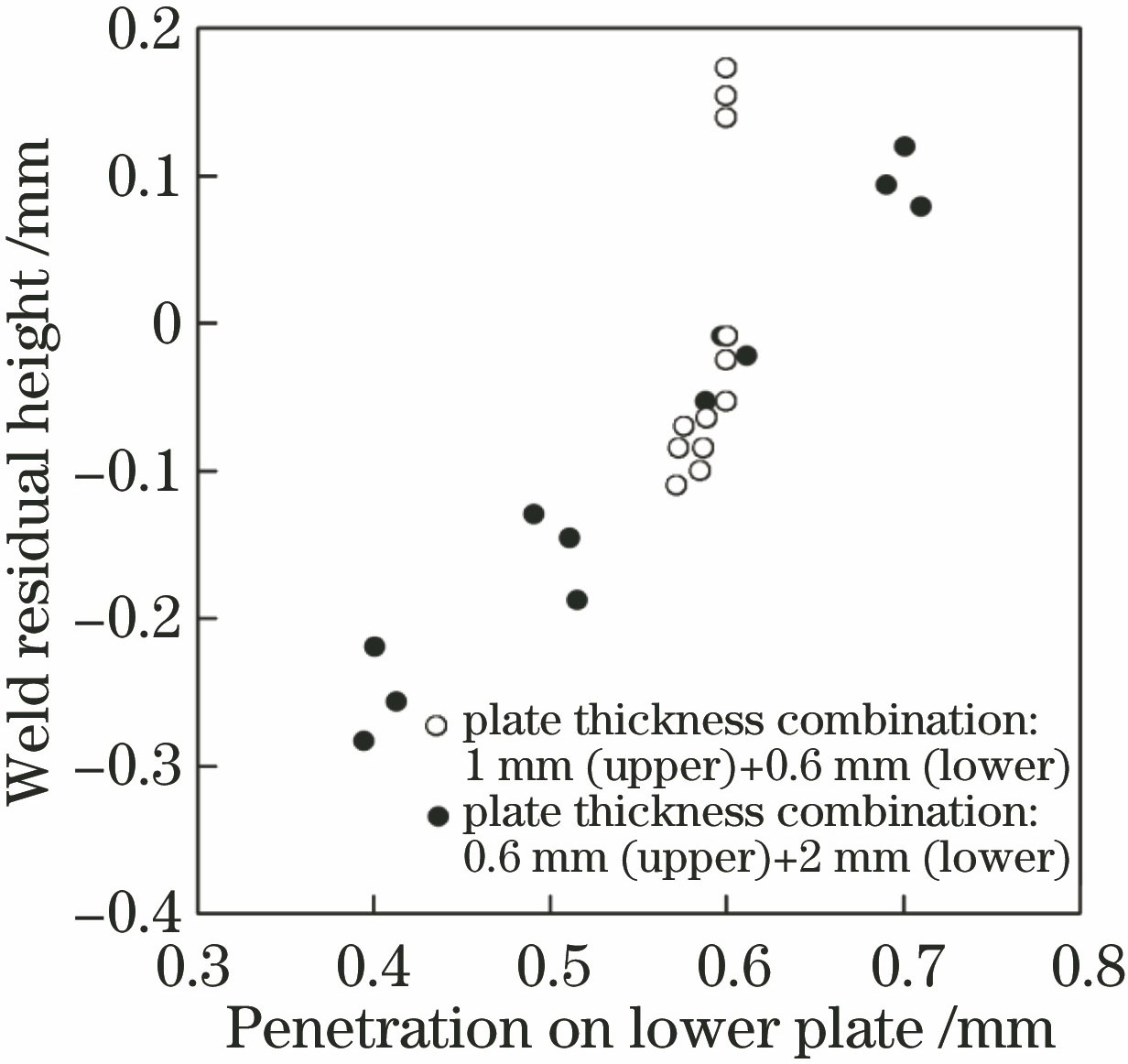
图 6. 激光搭接接头表面余高与下板熔深的对应关系
Fig. 6. Relationship between residual height of laser lap joint and penetration on lower plate
3.2 激光焊接头表面轮廓检测成像及图像处理
对
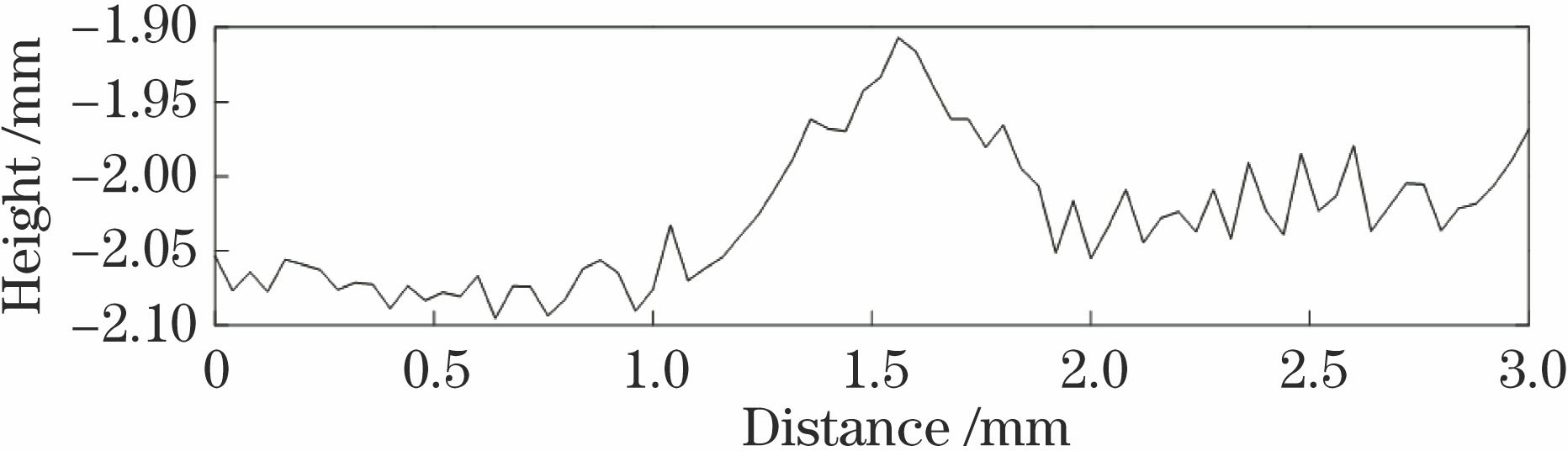
图 7. 对应图5(a)的激光焊接头金相截面的表面轮廓扫查结果
Fig. 7. Surface profile scanning result corresponding to laser weld joint metallographic section in Fig. 5(a)
为了减小测量随机因素对表面轮廓检测结果的影响,采用移动均值滤波法对
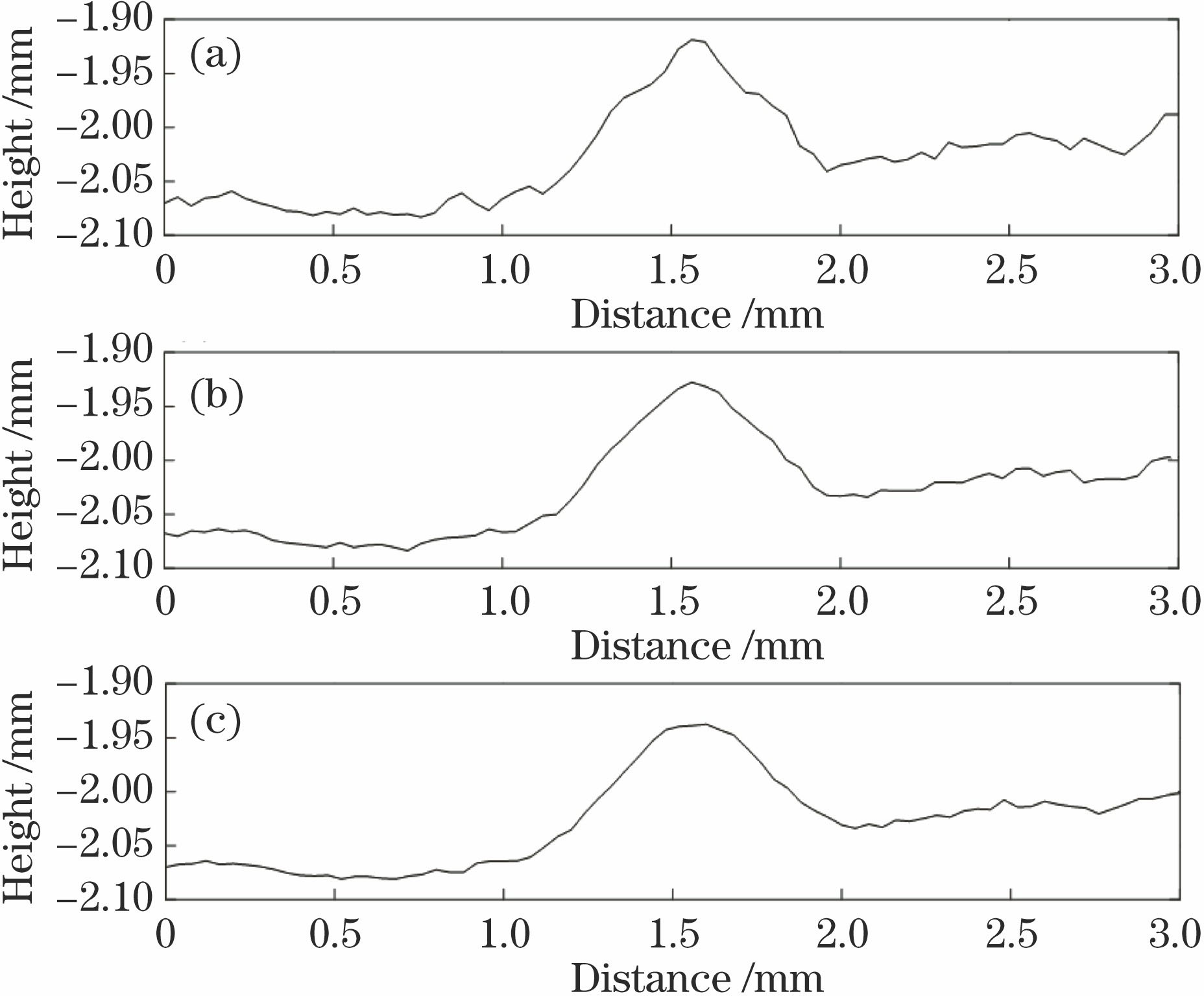
图 8. 不同滤波窗口数据量的表面轮廓曲线移动均值滤波结果。(a) 3;(b) 5;(c) 7
Fig. 8. Moving mean filtering results of surface profile curves with different numbers of filtering windows. (a) 3; (b) 5; (c) 7
在对激光焊缝表面轮廓进行检测的过程中,工件在焊接过程中的变形及扫查驱动器倾斜放置等因素,导致检测区域的图像发生倾斜,如
式中拟合直线的参数
根据拟合直线的倾斜角度,依次计算出每个数据点需要上升/下降的高度,即可完成对轮廓线的倾斜修正补偿,其中,每个数据点倾斜修正后的高度值计算公式为
式中:
根据(3)式修正所得的激光焊缝表面轮廓如
为了验证在不同的焊缝余高下,激光焊缝表面轮廓的检测及图像修正结果与金相结构的吻合程度,对4种具有代表性的金相截面形貌的表面轮廓检测曲线进行滤波及图像修正处理,其对比结果如
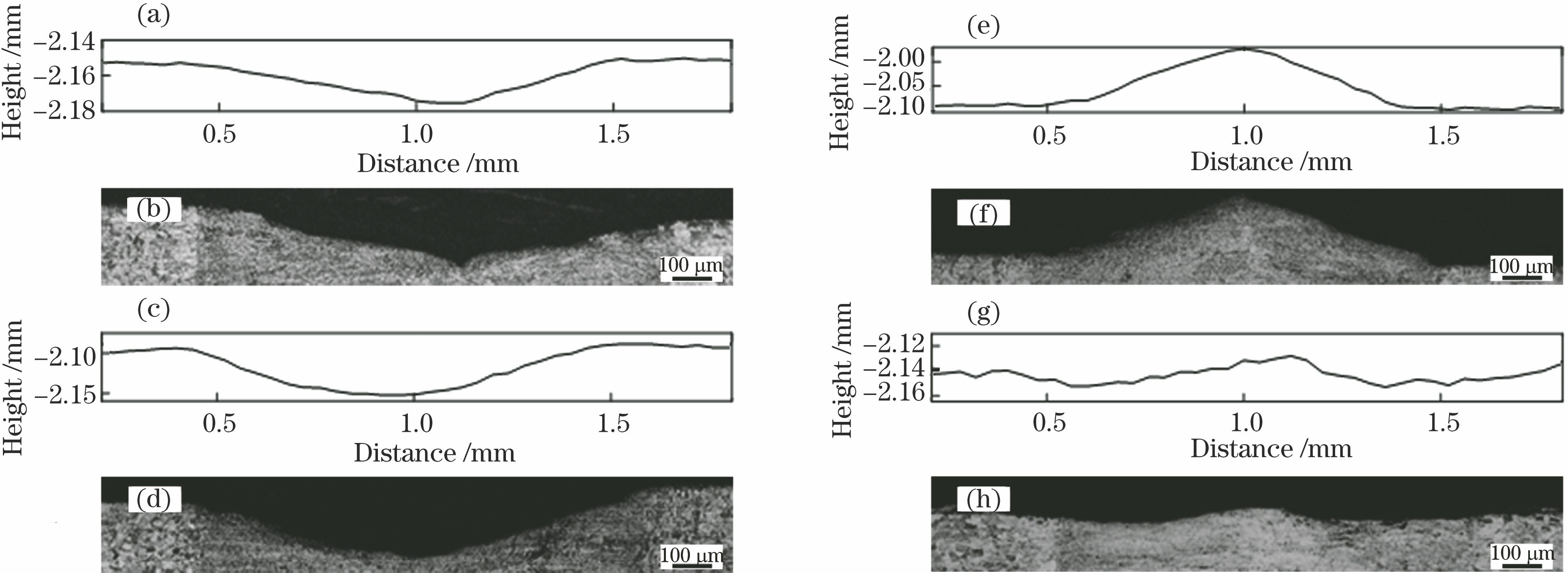
图 11. 4种典型表面轮廓检测结果的对比。(a)表面检测轮廓线1;(b)与图11(a)对应的接头的金相形貌;(c)表面检测轮廓线2;(d)与图11(c)对应的接头的金相形貌;(e)表面检测轮廓线3;(f)与图11(e)对应的接头的金相形貌;(g)表面检测轮廓线4;(h)与图11(g)对应的接头的金相形貌
Fig. 11. Comparison of four typical profile detection results. (a) Profile detection curve 1; (b) metallographic morphology corresponding to profile detection curve shown in Fig. 11(a); (c) profile detection curve 2; (d) metallographic morphology corresponding to profile detection curve shown in Fig. 11(c); (e) profile detection curve 3; (f) metallographic morphology corresponding to profile detection curve shown in Fig. 11(e); (g) profile detection curve 4; (h) metallographic morphology corresponding to
3.3 激光焊接头表面轮廓余高的计算
为了准确评估激光焊缝的表面质量,需要对轮廓的余高/下塌量等进行智能计算,以便于对激光焊缝的接头质量进行评估,余高/下塌量的智能计算方法如
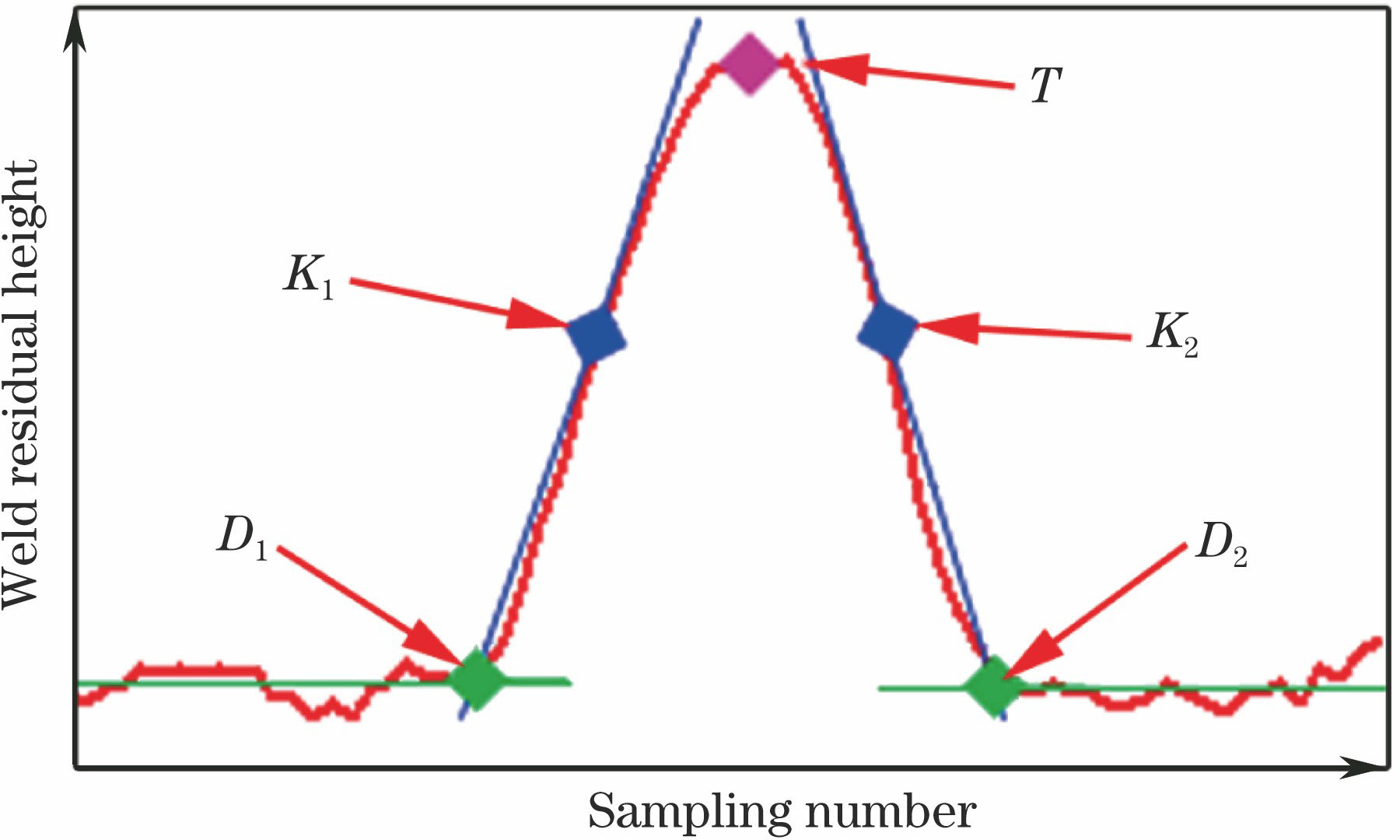
图 12. 轮廓特征点自动识别算法示意图
Fig. 12. Auto-recognition method for feature points on profile curve
为了验证激光非接触式测量结果的准确性,本文对
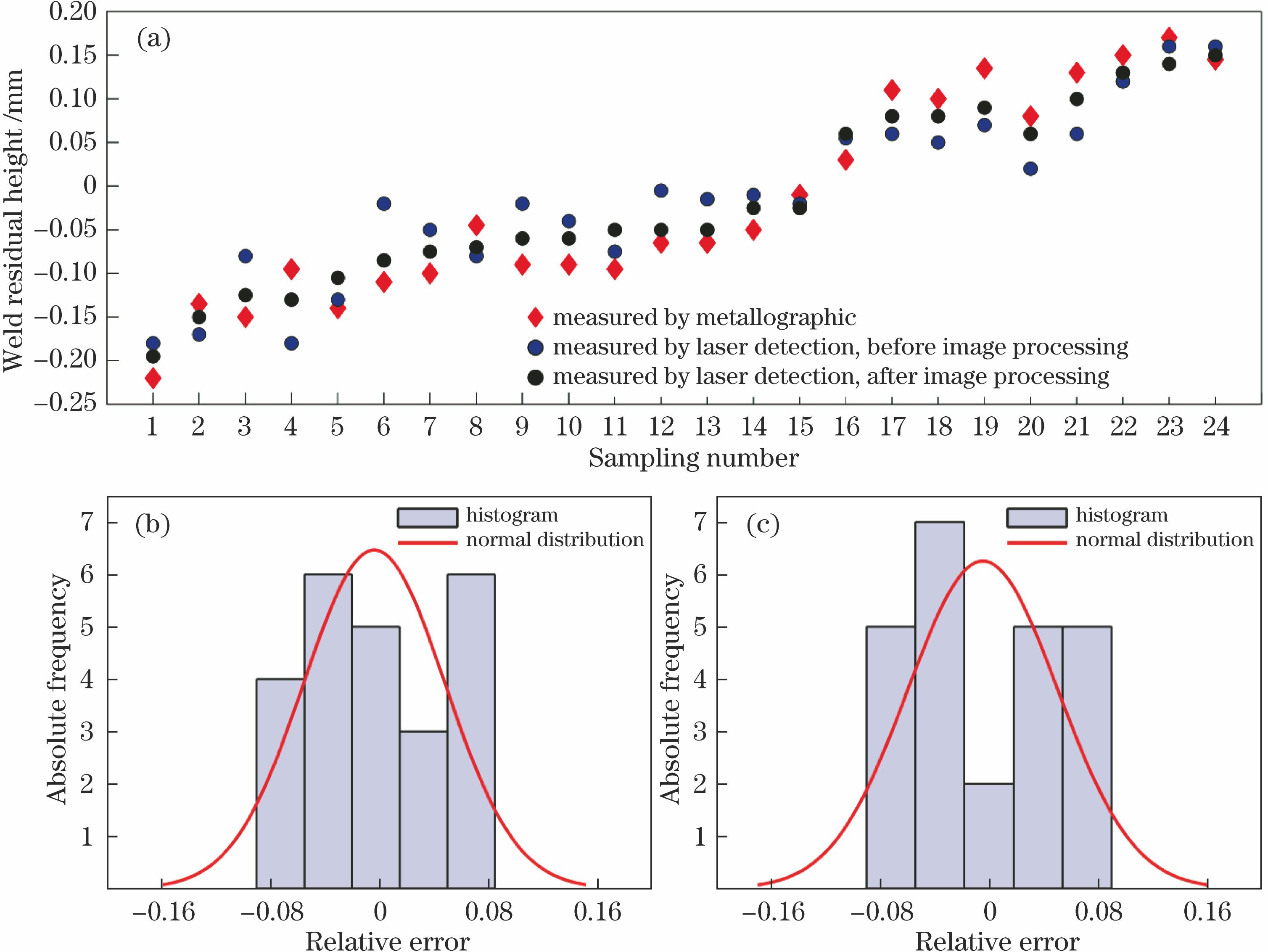
图 13. 激光非接触式测量焊缝余高与金相测量结果。 (a) 测量结果的对比;(b)原始轮廓曲线测量结果的误差分布;(c)图像处理后测量结果的误差分布
Fig. 13. Comparison of residual height and metallographic measurement result obtained by laser noncontact measurement. (a) Detection result comparison; (b) error distribution of detection result obtained from original image; (c) error distribution of detection result after image processing
4 结论
采用非接触式激光测距传感技术,并利用移动均值滤波处理及倾斜补偿修正算法,可以有效去除检测过程中的随机干扰以及传感器与工件倾斜角度对检测数据的影响,实现了对激光焊缝表面状态的高精度检测。
工件装卡间隙量对激光焊缝的熔深及焊缝表面状态具有显著影响,为通过检测激光焊缝表面状态对激光焊缝质量进行评估提供了依据。
通过研究激光焊缝表面状态的表征量——余高、下塌量等的智能算法,实现激光焊缝表面状态的高精度、定量化智能检测,为激光焊缝质量评估技术的工程化提供了参考。
[1] 林基安.[\s]{1}动车组奥氏体不锈钢激光焊接工艺及性能基础研究[D].[\s]{1}北京:[\s]{1}北京交通大学,[\s]{1}2012:[\s]{1}15-[\s]{1}26.[\s]{1}
Lin[\s]{1}JA.[\s]{1}The[\s]{1}basic[\s]{1}study[\s]{1}on[\s]{1}laser[\s]{1}welding[\s]{1}technology[\s]{1}and[\s]{1}performance[\s]{1}of[\s]{1}CRH[\s]{1}austenitic[\s]{1}stainless[\s]{1}steel[D].[\s]{1}Beijing:[\s]{1}Beijing[\s]{1}Jiaotong[\s]{1}University,[\s]{1}2012:[\s]{1}15-[\s]{1}26.[\s]{1}
[2] 李亚江,[\s]{1}吴娜,[\s]{1}Puchkov[\s]{1}PU.[\s]{1}先进焊接技术在航空航天领域中的应用[J].[\s]{1}航空制造技术,[\s]{1}2010([\s]{1}9):[\s]{1}43-[\s]{1}47.[\s]{1}
Li[\s]{1}YJ,[\s]{1}WuN,[\s]{1}Puchkov[\s]{1}PU.[\s]{1}Application[\s]{1}of[\s]{1}advanced[\s]{1}welding[\s]{1}technology[\s]{1}in[\s]{1}aviation[\s]{1}and[\s]{1}aerospace[\s]{1}industry[J].[\s]{1}Aeronautical[\s]{1}Manufacturing[\s]{1}Technology,[\s]{1}2010([\s]{1}9):[\s]{1}43-[\s]{1}47.[\s]{1}
[3] 黄治轶.[\s]{1}城市轨道客车不锈钢车顶钢结构制造工艺研究[D].[\s]{1}长春:[\s]{1}吉林大学,[\s]{1}2005:[\s]{1}12-[\s]{1}28.[\s]{1}
Huang[\s]{1}ZY.[\s]{1}Study[\s]{1}on[\s]{1}the[\s]{1}welding[\s]{1}technology[\s]{1}for[\s]{1}the[\s]{1}stainless[\s]{1}steel[\s]{1}roof[\s]{1}structure[\s]{1}of[\s]{1}the[\s]{1}urban[\s]{1}railway[\s]{1}carriage[D].[\s]{1}Changchun:[\s]{1}Jilin[\s]{1}University,[\s]{1}2005:[\s]{1}12-[\s]{1}28.[\s]{1}
[4] 段珍珍, 张雪红, 谷晓鹏. 轨道车辆焊接制造工艺现状及发展趋势[J]. 焊接技术, 2011, 40(11): 1-5.
[5] 韩晓辉, 陈静, 阚盈, 等. 不锈钢薄板非熔透激光搭接焊热源模型[J]. 中国激光, 2017, 44(5): 0502002.
[6] 彭进, 李俐群, 张瑞珠, 等. 铝合金电弧预熔丝激光焊工艺特性研究[J]. 激光与光电子学进展, 2017, 54(6): 061404.
[7] 黄怡洁, 高向东, 林少铎. 激光焊接参数对有机玻璃与不锈钢接头力学性能的影响[J]. 中国激光, 2017, 44(12): 1202006.
[10] 梁行, 阚盈, 姜云禄, 等. 不锈钢薄板激光搭接焊接头的力学性能[J]. 中国激光, 2018, 45(6): 0602001.
[14] 高世一, 杨凯珍, 刘师田, 等. 基于数据拟合的激光焊接焊缝图像表面缺陷检测[J]. 现代电子技术, 2011, 34(14): 188-190, 198.
[15] 刘恩泽, 姚成武, 谢雨凌, 等. 非熔透激光搭接焊SUS304奥氏体不锈钢无焊缝侧变形机理[J]. 中国激光, 2019, 46(4): 0402004.
[17] 孙向伟, 殷咸青, 王江超, 等. 采用三维光学测量技术对薄板焊接失稳变形的分析[J]. 焊接学报, 2013, 34(6): 109-112, 118.
[19] 刘维, 韩旭东, 艾华. 激光三角法在位移测量中的应用[J]. 光学精密工程, 2004, 12(s2): 104-107.
[20] 韩庆瑶, 肖强, 乐英. 空间离散点最小二乘法分段直线拟合的研究[J]. 工业仪表与自动化装置, 2012, 4: 107-109.
Article Outline
叶结和, 刘勇, 徐国成, 谷晓鹏, 董娟, 彭博, 魏凌波. 基于非接触测量的搭接激光焊缝表面质量评估[J]. 中国激光, 2019, 46(10): 1002008. Jiehe Ye, Yong Liu, Guocheng Xu, Xiaopeng Gu, Juan Dong, Bo Peng, Lingbo Wei. Evaluation of Surface Quality of Lap Laser Weld Joints Based on Noncontact Measurement[J]. Chinese Journal of Lasers, 2019, 46(10): 1002008.