机器视觉技术在现代汽车制造中的应用综述
下载: 2960次特邀综述
1 引言
早在20世纪80年代美国国家标准局就预计,检测任务的80%乃至90%将由视觉测量系统来完成,该预测至今已基本变成现实。近年来,随着机器视觉的迅速发展,机器视觉技术的快速性、精确性、智能化特性已广泛应用到现代工业的各行各业中[1-4]。而且,在当前以智能制造为核心的工业4.0时代背景下,中国制造2025战略部署逐步深入,工业机器人产业市场呈现爆炸式增长势头[5],而充当工业机器人“慧眼”的机器视觉系统也功不可没。
机器视觉系统是一种非接触式的光学传感系统,其同时集成软硬件,能够自动地从所采集到的图像中获取信息或产生控制动作[6]。简言之,就是用计算机模拟人眼的视觉功能,从图像或图像序列中提取信息,进行处理并加以理解,最终用于检测、测量和控制[7]。典型的工业机器视觉系统使用摄像机采集被测目标的图像信息,然后将模拟图像信息转换为数字图像信号传送给上位机的数字图像处理系统,处理系统中会根据图片的像素分布、亮度、标志点和颜色等信息,运算出被测目标的位姿和形态等信息,最后根据测试得到的信息控制驱动执行器进行响应的操作。目前机器视觉已经应用在农产品分选[8]、医疗影像[9]、产品包装检测[10]和工业[11-13]等领域中。
机器视觉在工业领域中的应用广泛,主要有三个功能:视觉测量、视觉引导和视觉检测。视觉测量针对的是精度要求较高的一些零部件,精度要求为毫米级甚至为微米级[14],使用人的肉眼无法完成必须使用机器完成,如对高精度螺纹螺孔的尺寸需要通过机器视觉的方式进行测量,保证连接的间隙和精度[15];视觉引导是要求机器视觉能够快速准确的找到被测零件,并确认其位置,引导机器人机械臂准确抓取[16],如视觉引导随机抓件,通过扫描工具箱内随机分布的零件得到三维图像,采用模式识别的方式,在三维图像中获取机械臂抓取工件的最佳点,引导抓取实现自动化生产;视觉检测是使用机器视觉系统检测生产线上的产品有无质量问题,对其美观度、舒适度和使用性能进行检测[17],是取代人工最多的环节,如国内外都实现了使用机器视觉对马铃薯的几何形状检测、表面缺陷检测,从根据这些特征对马铃薯进行分级[18]。机器视觉极大的提高了工业生产中的柔性和自动化程度[19],并且能够在危险作业环境中完成一些人工难以完成的工作,在大批量的生产中极大地减少了人工的使用,并提高和保证了生产的质量。
值得指出的是,机器视觉技术在现代工业典型代表的汽车工业中的应用已十分广泛,本文也将以汽车制造业为例,重点讲述机器视觉技术在现代汽车制造中的典型应用。作为世界上规模最大和最重要的产业之一的汽车制造业已有100多年的发展历史[20]。相比于其他制造业,汽车制造业具有几个典型的特点:产量巨大且仍保持快速增长;车型更新换代速度快;制造工艺流程非常复杂。机器视觉技术在汽车制造业中的应用,极大地提高了工艺的操作质量和效率,降低了劳动强度。其已成功地应用于国内外许多汽车主机厂,包括车辆及零部件自动检测、零件三维定位、车身组装/加工,零件追溯等[21-25]。机器视觉技术的应用已贯穿了整个汽车车身制造过程,包括从初始原料质量检测发展到汽车零部件100%在线测量,再对制造过程中的焊接、涂胶、冲孔等工艺过程进行把控,最后对车身总成、出厂的整车质量进行把关。
目前,机器视觉已在现代工业各个领域被广泛应用,在未来的发展空间将更加广阔,机器视觉技术必成为引导更高、更快、更稳定的自动化工业时代的“慧眼”。但不得不指出,机器视觉技术在现代工业应用中也受到一定因素的制约,需要未来进行针对性的改进和提升。获取一个良好的图像需要受到光源、镜头选择、传感器选型、节拍考虑、安装布置、工件状态变化等一系列因素的制约,因此某一个部分发生变化都有可能影响图片质量,从而影响算法的正常工作,所以机器视觉算法的稳健性还需要进一步提高。另外,目前计算机软件的智能程度也还远远不够,在计算机视觉领域大热的深度学习神经网络目前在机器视觉领域的成功应用较少,当目标对象多变、特征复杂、样本数不够的时候,深度学习无法使用,还是要回到传统的老路上来,再考虑实时性的严格要求,机器视觉特别需要一种新的智能的普遍应用于大部分领域的方法出来。工业界基本都是三维的部件,而二维成像毕竟是三维空间的实际情况的一种病态数据采集,围绕三维机器视觉检测、测量、机器人导引等项目和应用将会越来越多,三维视觉检测将更多的应用到工业生产领域。在其他众多民用领域也会迎来机器视觉发展的高潮,现代制造、医疗、电子、仓储等各个领域都会有各种各样的新应用,促进新时代智能化的发展;机器视觉硬件系统也会朝着嵌入式方向发展,运算效率和智能化程度越来越高。
2 视觉测量
最初,汽车制造质量主要依靠三坐标机测量完成[26],如
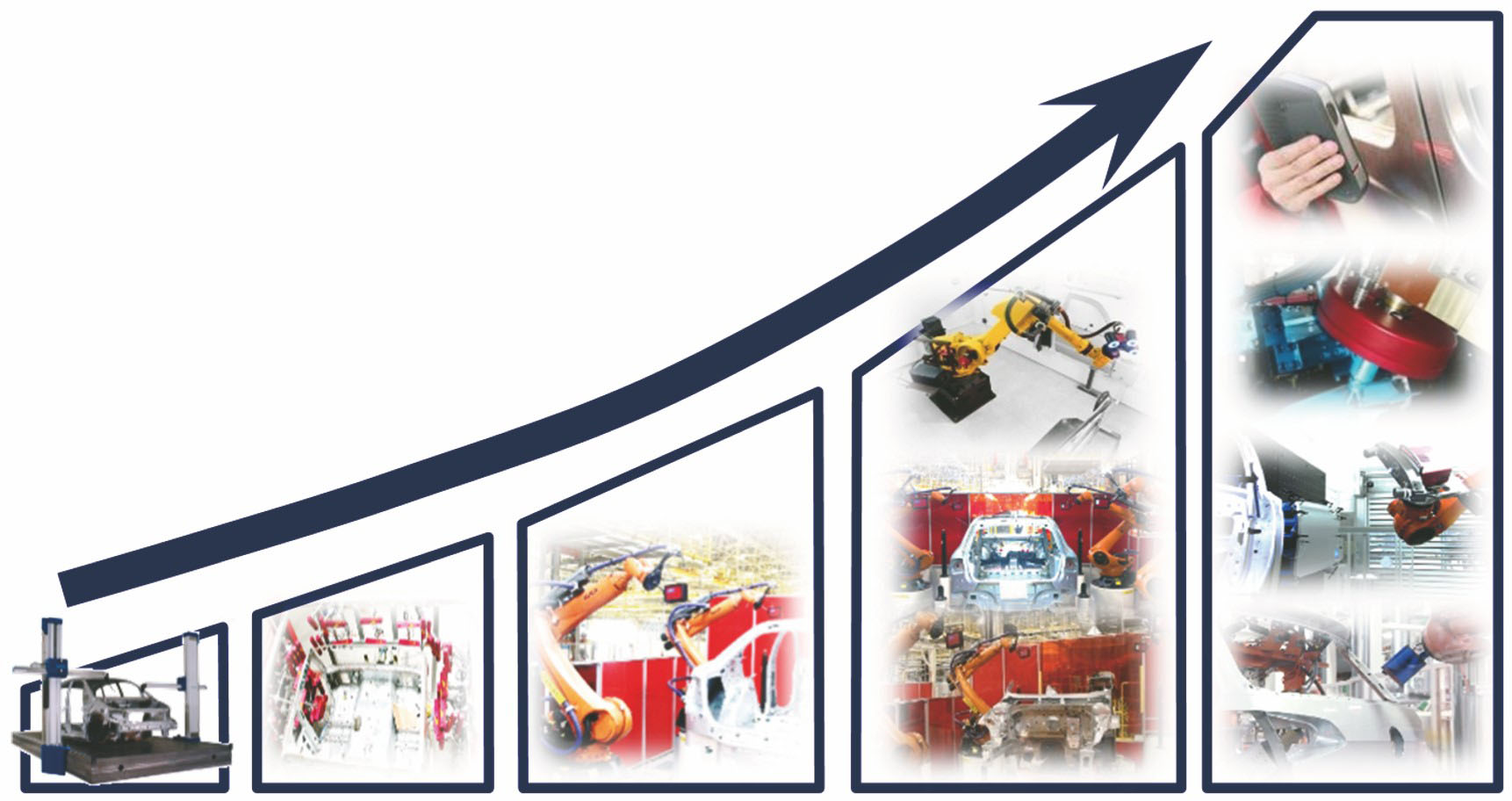
图 1. 视觉测量技术在汽车质量检测中的发展
Fig. 1. Development of visual measurement technology in automobile quality inspection
2.1 激光在线测量
汽车白车身是轿车所有零部件的基本载体,白车身的制造尺寸精度直接影响汽车车身外形、气动性能,以及制造成本等,因此,对尺寸控制机构的制造是提高车身质量的必要条件之一,车身尺寸的先进检测方法是控制汽车制造尺寸精度的关键手段[27]。目前在汽车制造企业中广泛应用的车身测量系统主要包括三坐标机和激光在线测量系统。在焊装车间质量控制过程中,三坐标测量系统广泛应用于车身尺寸的测量,以监测尺寸波动,具有测量精度高、可靠性好等优点。但存在测量效率低、响应周期长等问题,无法实现白车身生产过程的实时监控。激光在线测量系统对环境要求低,测量效率高,可以实现对车身进行100%实时三维测量[28],计算机可以根据测量数据输出报表,自动分析生产线的运行状况,及时地显示尺寸偏差及趋势,更有利于车身制造过程中的质量控制,具有良好的应用前景。
激光在线测量技术基于三角测量原理,其利用线状激光构造被测特征,结合有效的照明,获得被测特征的表面信息,相机拍摄特征图像,通过图像处理技术得到被测特征在图像上的二维(2D)坐标,再通过三角测量模型将2D坐标转换为传感器坐标系下的三维(3D)空间坐标。在线测量技术根据不同的应用场景可分为固定式在线测量系统与机器人柔性在线测量系统,如
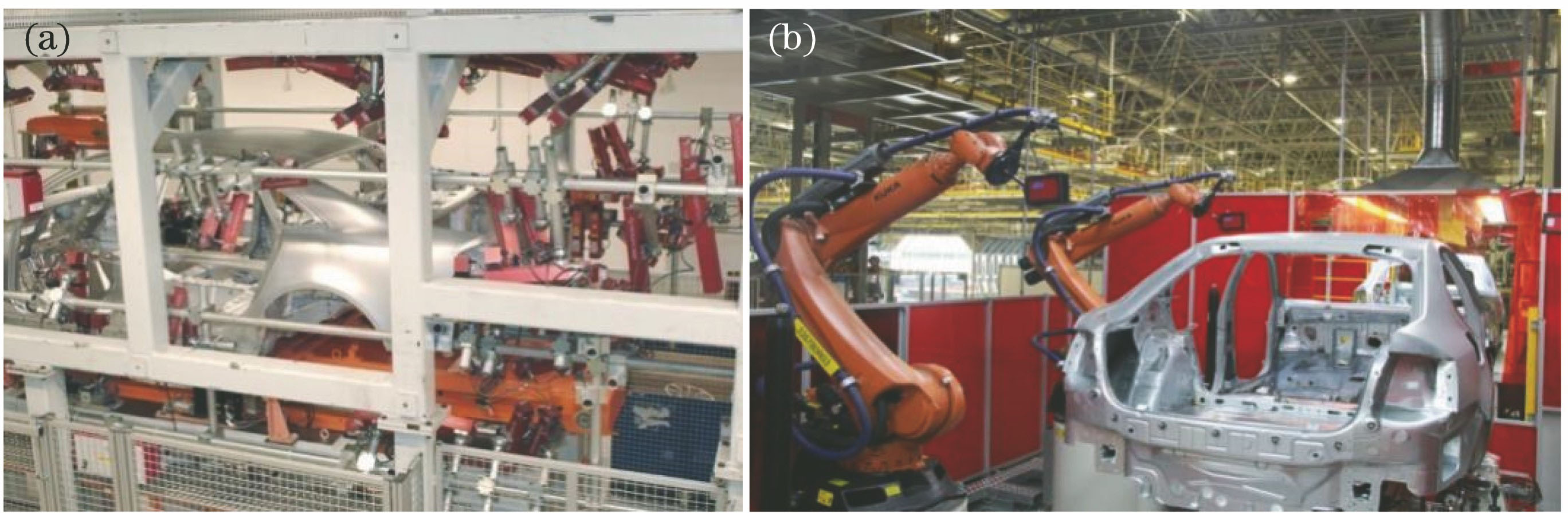
图 2. 激光在线测量。(a)固定式测量站;(b)机器人柔性测量站
Fig. 2. Laser on-line measurement. (a) Fixed measuring station; (b) robot flexible measuring station
近年来,上海大众、一汽大众、上海通用,以及东风汽车等公司纷纷引进了在线测量系统,进行尺寸波动的监控和工艺能力的研究[27]。总体上,在线检测技术在中国汽车行业中正处于普及、发展和进步的阶段,通常一条焊装生产线都会配置底板在线测量工位和车身总成在线测量工位,分别用来监控底板总成和车身总拼的制造质量。但是当前在线测量设备在大部分主机厂中的应用尚处于起步阶段,如何合理的推广并使用在线测量系统,是车间生产亟待解决的重要问题。对于汽车白车身中产生的质量,在紧凑型生产节拍中,如何优化在线测量频率,测量更多的特征点,最大限度地提高测量设备的效率,保证对车身质量准确、及时的控制,成为白车身制造质量控制中的关键技术问题[27]。白车身在线测量系统主要在测量位置分布优化、测量频次优化等领域尚有上升空间。但由于激光在线测量系统使用线激光传感器进行测量,适用于细节化数据指标比较少的测量场合,当被测特征表面信息需求量变大时,激光在线测量系统的效率不能满足测量的需求,这时蓝光扫描测量系统便展现出极大地优势。
2.2 蓝光扫描测量
汽车等高端先进装备制造高速发展,对产品几何尺寸测量提出更多需求,产品结构形式和检测功能需求更加多样化,局部细节检测要求更加精细化,对测量效率、数字化及自动化程度要求更高。在汽车生产中,形貌测量是产品质量控制中的重要部分。汽车车身外覆盖件的形貌精度直接影响了汽车部件可装配性和气密性,及时发现车身外覆盖件的尺寸与形貌异常可以大大降低出厂产品的缺陷率,对车身外覆盖件的精密获取还能反映冲压工序中模具的工作状态和寿命。
蓝光扫描测量技术摆脱了传统三坐标机单特征测量的局限性,可实现整体形貌尺寸测量与分析,具有更高的测量效率,更全面的特征评价,且安装调试方便。蓝光扫描技术可获得高密度的测量数据应对复杂曲面多变的形貌特征与曲率变化,有效实现复杂曲面的精细化测量,其扫描测量精度可以达到±0.02 mm,在单幅0.5 m范围内可以获得上千万个高密度点云数据。通过采用高精度拼接技术,蓝光扫描测量可以有效统一局部测量数据至全局坐标系下,满足大型构件测量范围的要求,与此同时,通过结合机器人运动平台,可以提高测量效率与自动化水平,实现无人干预工作,基于这些特点,可以对车身零部件及整车进行非常细致的质量评价,包括表面形貌评价和局部特征评价。
由于蓝光扫描测量系统测量数据丰富、数据分析方法多样化等特点,奔驰、宝马、大众、通用等的高端汽车厂已引入蓝光扫描测量系统对车身总成和四门两盖总成进行测量,同时东风汽车、长安汽车等国产汽车厂也纷纷引进了蓝光扫描测量系统。蓝光扫描系统可实现全自动测量,且在覆盖传统三坐标测量数据的基础上能提供更丰富的数据,因此目前越来越多的主机厂采用蓝光测量设备来替代三坐标机进行零部件及整车测量。但为了保证测量精度,目前蓝光测量系统需要采用贴点方式实现点云数据拼接,影响整体测量效率,如何实现在无贴点场景下的高精度数据拼接是蓝光测量系统后续发展的一个重要方向。另外蓝光扫描系统采用多相机和投影机共同构成测量系统,系统成本较其他测量成本高。
2.3 表面质量检测
汽车涂装是汽车生产制造过程中一个重要的环节,车身喷涂不仅可以提供外观装饰,而且可以对车身表面进行保护。然而,在实际的涂装生产中,由于涂装车间环境的影响,油漆的质量和涂装工艺的不同,使得涂膜的车体很容易产生不同类型的缺陷[31],比如杂质、喷涂污染等典型表面瑕疵,如何准确地实现汽车表面涂装质量自动化测量极其关键。
目前,汽车表面质量测量主要通过人工视觉的方法完成,其效率低,易受人为因素的影响,已成为制约涂装车身质量监控效率的关键因素之一[32]。为提升效率、减少人工,基于机器视觉的汽车表面质量测量已开始应用在汽车涂装检测领域,如
由于汽车涂装表面较光滑,且为大范围不规则自由曲面,因此汽车涂装表面质量测量具有一定难度,在众多自由曲面面形测量方法中,反射式条纹偏折法分辨率高、曲率测量范围大、结构简单、对环境变化不敏感,具有重要的应用前景,目前汽车生产厂商主流表面质量测量系统均基于反射式条纹偏折法。表面质量测量系统主要包括机器人、显示器、计算机与相机。测量时首先通过计算机控制显示器投影正弦条纹到被测曲面上,经反射后由相机采集。被测曲面上的面形变化会使条纹发生变形,利用相位提取算法对条纹的相位信息进行提取,即可实现对被测曲面面形的测量。该方法结构简单、成本低,测量分辨率可达到纳米级别,曲率测量范围大。同时,将显示器、相机等设备搭载在示教后的机器人上,通过机器人的大范围运动可实现全车身大范围表面质量测量。
汽车漆膜缺陷自动检测系统目前已经在几个汽车公司中开始测试和使用,主要应用地区是欧美和日本等汽车技术发达的区域,国内还没有在生产中应用的实例。福特汽车在全世界的3个工厂涂装线上已经采用自己开发的漆膜3D缺陷检测系统[32];德国宝马汽车公司与梅赛德斯奔驰汽车公司也纷纷将漆膜缺陷检测系统应用于生产中,该系统能保证高于99.5%的缺陷识别率和低于5%的错误率,4个传感器检测一台车的时间仅为60 s。使用反射式条纹偏折测量车身表面质量能够实现自动化检测和质量监督,但是反射式条纹偏折测量方法光路调整有一定的复杂性,在国内还有一定的技术难度,需要进行新一步的研发和应用推广。
3 视觉引导
视觉引导技术结合了多种视觉检测技术与机器人运动学原理,旨在为工业现场的每台机器人安装“眼睛”。视觉引导系统将突破机器人只能单纯地重复示教轨迹的限制,使其能根据被操作工件的变化实时调整工作轨迹,提升机器人智能水平,促进生产效率,提高生产质量,比如通过引导机器人自动上下料和引导物流及输送设备定位等。后来,视觉引导技术逐渐渗透到汽车制造的全过程,比如引导机器人进行最佳匹配安装、精确制孔、焊缝引导及跟踪、喷涂引导、风挡玻璃装载引导等,如
3.1 视觉引导抓取
汽车制造中的焊装工艺主要是将各类零部件通过焊接、胶粘等连接工艺组装成各类分总成,再将各分总成装配成一个白车身总成。目前,零部件主要是利用料箱从冲压车间转运至焊装车间,各类分总成也是通过料箱或EMS等机运装置在车间内流转,如何实现机器人自动从料箱、EMS等装置上取件一直是白车身制造过程中亟待解决的问题。由于汽车一般都是金属材质,重量较重,传统人工运输搬运不仅占用了大量的劳动力,生产成本高,而且拿取搬运堆放效率低,搬运期间易造成一定的危险安全事故,实现高效率低成本的机器人自动上件已成为众多主机厂的迫切需求。
车身车间的上件模式主要分为人工上件,超高精度料箱上件,视觉引导抓取上件。目前绝大部分国内车厂上下料主要采用人工上件,即通过现场工人将车门等配件从料箱中搬运至车身上,此种方式占用了大量的人力且引入人为干扰因素;为了减少人员成本并提高安装精度,超高精度料箱上件方式应运而生,其通过机器人与高精度料箱配合,机器人事先规划好运行轨迹,机械式抓取料箱内的汽车配件,此方法摆脱了人员操作,但是流程相对死板,需要机器人、料箱位置及内部配件保持固定的位姿关系;而大众、通用等主流合资工厂已大规模采用视觉引导上件,视觉引导抓取方法将机器人与视觉测量相结合,突破机器人只能单纯地重复示教轨迹的限制,使其能根据被操作工件的位置变化实时调整其工作轨迹,准确抓取工件,直接提升整个车身制造过程的自动化效率,如
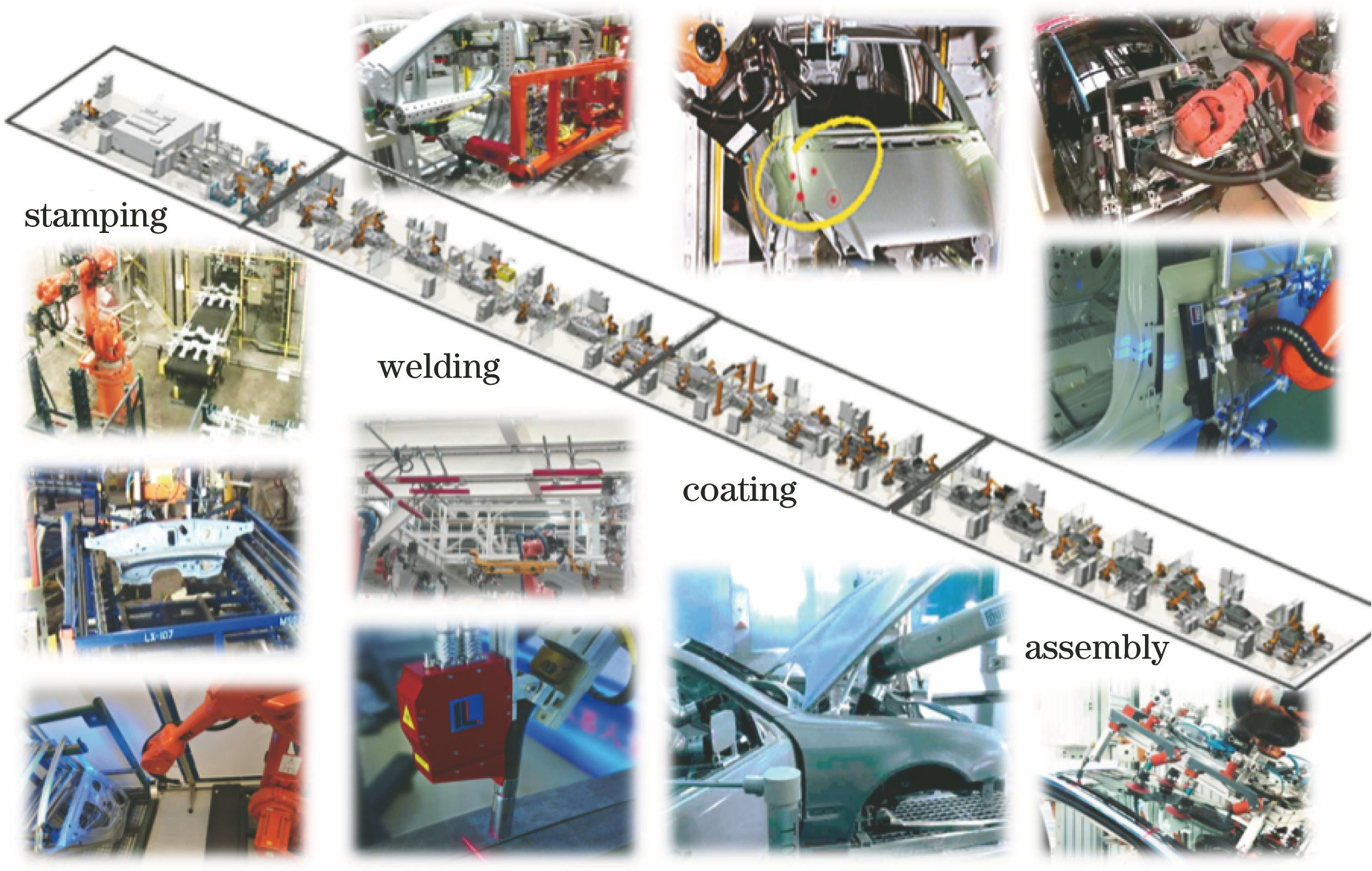
图 5. 视觉引导技术在车身制造过程中的应用
Fig. 5. Application of visual guidance technology in car body manufacturing process
视觉引导抓取方法中,需要在机器人上分别集成测距传感器与视觉传感器并标定,抓取时首先读取测距仪数值实时感知零件与机器人相对位置,引导机器人接近料箱;其次通过视觉传感器对料箱内配件拍照,结合零件自身特征(例如孔、角点等)的三维信息,实现零件相对于初始状态的6自由度(3方向位置及3方向旋转角度)精确定位,继而计算工件位置及角度的偏移,反馈修正取件机器人的抓取轨迹。
目前,视觉引导抓件已在通用、大众等主机厂大量使用,长安、广汽、东风汽车等也纷纷尝试引入该技术。但视觉引导抓件主要还是应用于如四门内外板、侧围内外板、底板等中大型零件,而如车门铰链、前纵梁挡板等众多小型零件任无法实现自动抓取。车身小型零件通常是随机散乱堆放的,散件抓取面临零件高精度定位、机器人轨迹规划、机器人碰撞规避等众多难题需要突破。
3.2 视觉引导装配
基于视觉引导的机器人自动装配已成为车身装配的主流发展方向,其将机器视觉技术与工业机器人结合起来,通过视觉引导机器人,实现汽车配件高精度安装,极大地提高了环境适应能力以及智能化程度。在机器人装配过程中,只有考虑到视觉导引和定位技术的装配要求,才能充分发挥技术优势,提高机器人抓取和放置的精度[33],如
视觉引导装配与视觉引导抓取不同,其需要高精度保证配件与车身相对位姿的一致性,故视觉引导装配系统需要配置多个激光视觉传感器。
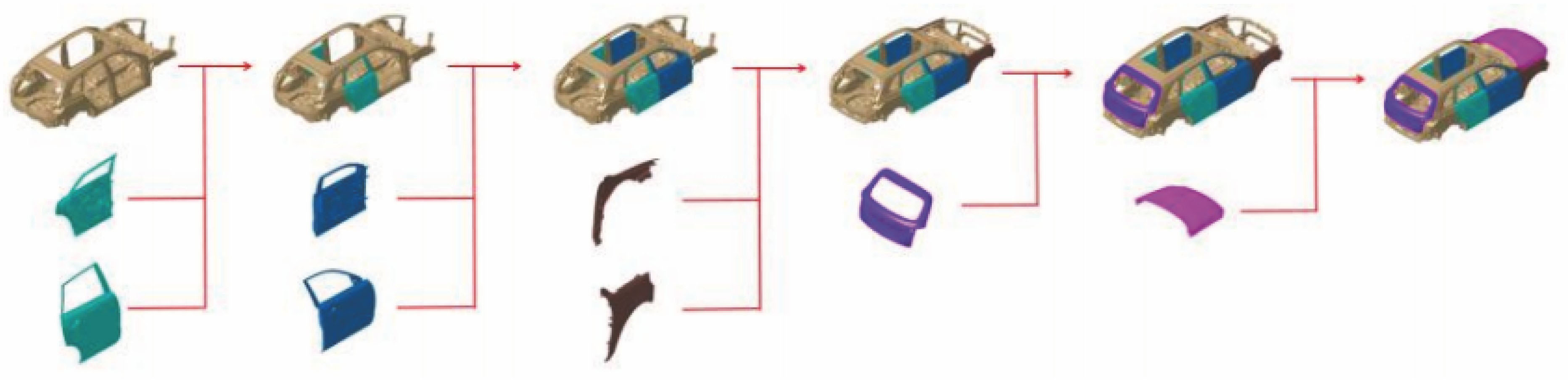
图 8. 视觉引导机器人实现四门两盖自动安装
Fig. 8. Vision guided robot for automatic installation of four doors and two covers
除了顶盖引导装载之外,视觉引导装配同样应用于四门两盖最佳匹配安装、风挡自动装载等场合,
3.3 视觉引导加工
视觉引导加工是指利用视觉测量技术测量每台车的特定区域尺寸信息,并根据其实际状态引导机器人进行精确切割、制孔、打磨等。激光加工技术具有先进、快速、灵活,以及准确的特点,如激光焊接、激光切割等技术在汽车制造中应用越来越广泛,将机器人、激光加工技术,以及机器视觉技术结合在一起可以充分利用各自的优势,实现自动化的高精度加工,如
传统的切割方式均要依赖模版刀具,由于待加工零件形状可能是不规则的,并且边缘的形状是复杂的,模具刀版的制造非常困难,一些特殊形状的切削无法完成[34]。若采用机器视觉技术引导方式替代传统的模板,并引入激光方式实现切割,使得切割加工更加灵活,极大地提高了切割系统的柔性。
加工切割过程中,首先要对机器人、激光器,以及视觉传感器之间的关系进行标定,计算机中载入待加工配件的尺寸与加工位置,通过视觉传感器实现待加工配件特征的准确测量,自动提取待切割边缘,建立智能化切削路径,机器人基于已设计路线进行引导,同时采用自适应算法避免了切削目标柔性变形引起的切削不准确问题[35]。
4 视觉检测
如今的产品生产、检测与机器视觉紧密相关[5],通过机器视觉检测还可以对产品进行制造工艺检测、自动化跟踪、追溯与控制等。其中具体包括通过光学字符识别(OCR)技术获取车身零件编码以保证零件在整个制造过程中的可追溯性,通过识别零件的存在或缺失以保证部件装配的完整性,以及通过视觉技术识别产品表面缺陷或加工工具是否存在缺陷以保证生产质量。
4.1 制造工艺检测
车身制造过程中大量使用了焊接、胶粘等连接工艺,胶粘工艺可以起到增强结构、紧固隔振、密封保护等作用。涂胶环节由于其工作环境恶劣、工作强度高、运动精度高,以及稳定性好,涂胶工艺逐渐由手工涂胶改为机器人涂胶,涂胶自动化已逐渐成为一种趋势[36]。传统的涂胶质量检测方法包括人工检测和离线视觉检测。人工检测是由质检工作人员凭借自身的经验,使用专用工具进行检验,此方法具有不确定性且占用人员劳动成本;离线视觉检测则是在涂胶完成后通过相机进行拍摄,后期图像处理得到最终涂胶质量评价,这种方法浪费大量时间成本。
当前基于机器视觉实现自动化检测的涂胶检测工艺,已经可以实现边涂边检,最高检测速度可以达到500 mm·s-1,甚至更高,其中涂胶质量的把控通过视觉检测来实现。如
焊接在结构件成形中扮演了非常重要的角色,对焊后的焊缝进行抛磨是消除焊接材料内部应力,生成光滑的焊接表面的关键技术。然而,工业现场主要依靠人工通过肉眼观察焊缝外观,劳动效率低且检测会引入人眼误差。视觉检测的出现有助于实现机器人自主抛磨焊缝质量的评价,其良好的稳定性、高效率等特性必将取代传统的人工视觉探测方法。
焊缝余高以及熔宽是评价焊接质量的关键要素,目前应用最广泛的是线结构光视觉与工业机器人的组合,线结构光视觉传感器安装在机器人上,通过示教后的机器人跟踪整条焊缝并用视觉传感器拍摄焊缝信息。但由于焊接过程中的飞溅、弧光、甚至高温等干扰因素的存在,焊缝引导及焊缝跟踪对视觉系统的防护功能提出很高的要求,通过图像处理算法对拍摄的图片进行特征分析提取,准确获取焊缝余高以及熔宽,如
在焊缝检测过程中,首先为机器人自动抛磨焊缝提供有关参数,规划机器人磨抛路径,带动焊枪与视觉传感器协同运动,与此同时通过线结构光传感器基于三角测量法计算得到相应位置的焊缝余高以及熔宽信息,高速处理拍摄的图像,提取焊缝余高以及熔宽信息,对焊接质量进行评价,实现焊接过程的智能化和柔性化。但由于焊接过程中的外界干扰问题,视觉传感器需要增加防护功能,满足一定防护等级,并能够防飞溅和自我冷却。
4.2 存在/缺失检测
机器视觉同样可应用于汽车零部件质量检测、相关标志识别等,其有助于提高生产效率、增强自动化程度以及提高作业过程的可靠性与可追溯性。具体应用包括类型识别与防错,例如顶盖类型识别、横梁、前盖类型防错;存在/缺失检测以保证零件的完整性,例如螺柱完整性检测;视觉读码以保证零件在整个制造过程中或整个生命周期内的可追溯性。
汽车内部具有多达数百个螺柱,而焊接螺柱不同于常规的螺柱,常常由于焊枪导向夹套疲劳磨损、设定伸出长度(预压量)和提升距离不合理,间接影响电弧熔化—熔池成型凝固—焊缝成形过程,导致质量缺陷进而脱焊,从而影响螺柱的完整性[37]。
机器视觉技术可以应用于汽车视觉读码技术,通过视觉传感器读取或校验字符码[39],可以实现零件在生产过程中的可追溯,避免出现生产差错,如
5 结束语
机器视觉已被广泛应用于现代工业的各个领域,尤其是汽车制造业。未来视觉检测技术及各类视觉产品将分布于整条汽车制造流水线,护航整个车身的制造过程,并向汽车产业链的各个环节迅速拓展。与此同时,随着增强现实、虚拟现实、云服务,以及人工智能等技术的发展与成熟,未来视觉检测获取的信息将与人工实现多方面、多维度的互动反馈,检测将以多种形式与用户实现交互。而且,随着视觉检测系统在制造现场的广泛应用,测量数据将越来越庞大,将测量数据与汽车制造工艺进行关联与分析,可以形成制造工艺改进的指导性意见。当前视觉技术已经在汽车制造中起到了至关重要的作用,未来的发展空间将更加广阔,机器视觉技术将成为引导更高、更快、更稳定的自动化工业时代的“慧眼”。
[1] 梁燕飞, 潘琳. 浅谈计算机视觉图像精密测量基础下的关键技术[J]. 数码世界, 2017( 3): 44.
梁燕飞, 潘琳. 浅谈计算机视觉图像精密测量基础下的关键技术[J]. 数码世界, 2017( 3): 44.
Liang YF, PanL. Key technologies of computer vision and image precision measurement[J]. Digital World, 2017( 3): 44.
Liang YF, PanL. Key technologies of computer vision and image precision measurement[J]. Digital World, 2017( 3): 44.
[2] 李毅萱. 基于计算机视觉图像精密测量的关键技术研究[J]. 工程技术: 全文版, 2016(11): 276.
李毅萱. 基于计算机视觉图像精密测量的关键技术研究[J]. 工程技术: 全文版, 2016(11): 276.
Li Y X. Research on key technology of image precision measurement based on computer vision[J]. Engineering Technology:Full Text Edition, 2016(11): 276.
[3] 吴文荣. 基于机器视觉的柔性制造岛在线零件识别系统研究[D]. 成都: 电子科技大学, 2006.
吴文荣. 基于机器视觉的柔性制造岛在线零件识别系统研究[D]. 成都: 电子科技大学, 2006.
Wu WR. Research on machine vision based online parts recognition system for flexible manufacturing island[D]. Chengdu: University of Electronic Science and Technology of China, 2006.
Wu WR. Research on machine vision based online parts recognition system for flexible manufacturing island[D]. Chengdu: University of Electronic Science and Technology of China, 2006.
[4] 王富治. 视觉检测的几个关键问题研究[D]. 成都: 电子科技大学, 2011.
王富治. 视觉检测的几个关键问题研究[D]. 成都: 电子科技大学, 2011.
Wang FZ. Study on several key questions in visual inspection[D]. Chengdu: University of Electronic Science and Technology of China, 2011.
Wang FZ. Study on several key questions in visual inspection[D]. Chengdu: University of Electronic Science and Technology of China, 2011.
[5] . 阮晋蒙. 机器视觉, [J]. 让中国制造2025“看”得更远 新经济导刊, 2017(z1): 80-83.
. 阮晋蒙. 机器视觉, [J]. 让中国制造2025“看”得更远 新经济导刊, 2017(z1): 80-83.
Ruan J M. Machine vision: making China manufacture 2025 "see" further[J]. New Economy Guide, 2017(z1): 80-83.
Ruan J M. Machine vision: making China manufacture 2025 "see" further[J]. New Economy Guide, 2017(z1): 80-83.
[6] 刘金桥, 吴金强. 机器视觉系统发展及其应用[J]. 机械工程与自动化, 2010(1): 215-216.
刘金桥, 吴金强. 机器视觉系统发展及其应用[J]. 机械工程与自动化, 2010(1): 215-216.
Liu J Q, Wu J Q. Development and application of machine vision system[J]. Mechanical Engineering & Automation, 2010(1): 215-216.
[7] 唐向阳, 张勇, 李江有, 等. 机器视觉关键技术的现状及应用展望[J]. 昆明理工大学学报(自然科学版), 2004, 29(2): 36-39.
唐向阳, 张勇, 李江有, 等. 机器视觉关键技术的现状及应用展望[J]. 昆明理工大学学报(自然科学版), 2004, 29(2): 36-39.
Tang X Y, Zhang Y, Li J Y, et al. Present situation and applications of machine vision’s key techniques[J]. Journal of Kunming University of Science and Technology(Natural Science Edition), 2004, 29(2): 36-39.
[8] 应义斌, 饶秀勤, 赵匀, 等. 机器视觉技术在农产品品质自动识别中的应用(Ⅰ)[J]. 农业工程学报, 2000, 16(1): 103-108.
应义斌, 饶秀勤, 赵匀, 等. 机器视觉技术在农产品品质自动识别中的应用(Ⅰ)[J]. 农业工程学报, 2000, 16(1): 103-108.
Ying Y F, Rao X Q, Zhao Y, et al. Application of machine vision technique to quality automatic identification of agricultural products(I)[J]. Transactions of the Chinese Society of Agricultural Engineering, 2000, 16(1): 103-108.
[9] 余冬, 冯云浩, 李根池, 等. 机器视觉在医疗器械检测中的应用与展望[J]. 中国医疗器械信息, 2015(8): 57-59, 63.
余冬, 冯云浩, 李根池, 等. 机器视觉在医疗器械检测中的应用与展望[J]. 中国医疗器械信息, 2015(8): 57-59, 63.
Yu D, Feng Y H, Li G C, et al. Application and Prospect of medical instrument inspection based on machine vision technology[J]. China Medical Device Information, 2015(8): 57-59,63.
[10] 王健. 机器视觉系统在现代包装行业中的应用[J]. 包装与食品机械, 2004, 22(5): 46-49.
王健. 机器视觉系统在现代包装行业中的应用[J]. 包装与食品机械, 2004, 22(5): 46-49.
Wang J. Introduction to machine vision system and its applications in modern packaging industry[J]. Packaging and Food Machinery, 2004, 22(5): 46-49.
[11] 张业鹏, 何涛, 文昌俊, 等. 机器视觉在工业测量中的应用与研究[J]. 光学精密工程, 2001, 9(4): 324-329.
张业鹏, 何涛, 文昌俊, 等. 机器视觉在工业测量中的应用与研究[J]. 光学精密工程, 2001, 9(4): 324-329.
Zhang Y P, He T, Wen C J, et al. Application and research of machine vision in industrial measurement[J]. Optics and Precision Engineering, 2001, 9(4): 324-329.
[12] 范祥, 卢道华, 王佳. 机器视觉在工业领域中的研究应用[J]. 现代制造工程, 2007( 6): 129- 133.
范祥, 卢道华, 王佳. 机器视觉在工业领域中的研究应用[J]. 现代制造工程, 2007( 6): 129- 133.
FanX, Lu DH, WangJ. Research and application of machine vision in industry[J]. Modern Manufacturing Engineering, 2007( 6): 129- 133.
FanX, Lu DH, WangJ. Research and application of machine vision in industry[J]. Modern Manufacturing Engineering, 2007( 6): 129- 133.
[13] 范祥, 卢道华, 王佳. 仪器仪表技术: 机器视觉在工业领域中的研究应用[J]. 中国学术期刊文摘, 2007, 13(22): 5.
范祥, 卢道华, 王佳. 仪器仪表技术: 机器视觉在工业领域中的研究应用[J]. 中国学术期刊文摘, 2007, 13(22): 5.
Fan X, Lu D H, Wang J. Instrument technology: research and application of machine vision in industrial field[J]. China Academic Journal Abstracts, 2007, 13(22): 5.
[14] 赵文辉, 段振云, 赵文珍, 等. 基于机器视觉的微米级2D零件自动检测系统[J]. 组合机床与自动化加工技术, 2012(9): 52-55.
赵文辉, 段振云, 赵文珍, 等. 基于机器视觉的微米级2D零件自动检测系统[J]. 组合机床与自动化加工技术, 2012(9): 52-55.
Zhao W H, Duan Z Y, Zhao W Z, et al. Research on Micron-sized 2D measurement system based on machine vision[J]. Modular Machine Tool & Automatic Machining Technology, 2012(9): 52-55.
[15] 周策策. 基于机器视觉的螺纹参数测量系统[D]. 天津: 天津大学, 2016.
周策策. 基于机器视觉的螺纹参数测量系统[D]. 天津: 天津大学, 2016.
Zhou CC. Thread parameter measurement system based on machine vision[D]. Tianjin: Tianjin University, 2016.
Zhou CC. Thread parameter measurement system based on machine vision[D]. Tianjin: Tianjin University, 2016.
[16] 党希超. 基于视觉导向的机械手抓取定位技术研究[D]. 广州: 华南理工大学, 2013.
党希超. 基于视觉导向的机械手抓取定位技术研究[D]. 广州: 华南理工大学, 2013.
Dang XC. Research on grasping and positioning technology of manipulator based on vision guided[D]. Guangzhou: South China University of Technology, 2013.
Dang XC. Research on grasping and positioning technology of manipulator based on vision guided[D]. Guangzhou: South China University of Technology, 2013.
[17] 汤勃, 孔建益, 伍世虔. 机器视觉表面缺陷检测综述[J]. 中国图象图形学报, 2017, 22(12): 1640-1663.
汤勃, 孔建益, 伍世虔. 机器视觉表面缺陷检测综述[J]. 中国图象图形学报, 2017, 22(12): 1640-1663.
Tang B, Kong J Y, Wu S Q. Review of surface defect detection based on machine vision[J]. Journal of Image and Graphics, 2017, 22(12): 1640-1663.
[18] 赵军, 田海韬. 利用机器视觉检测马铃薯外部品质方法综述[J]. 图学学报, 2017, 38(3): 382-387.
赵军, 田海韬. 利用机器视觉检测马铃薯外部品质方法综述[J]. 图学学报, 2017, 38(3): 382-387.
Zhao J, Tian H T. The applications of potato external quality detection using machine vision[J]. Journal of Graphics, 2017, 38(3): 382-387.
[19] 朱正德, 杨虹, 方琳, 等. 质量监控的第三只眼[J]. 汽车工艺师, 2010(10): 51-58.
朱正德, 杨虹, 方琳, 等. 质量监控的第三只眼[J]. 汽车工艺师, 2010(10): 51-58.
Zhu Z D, Yang H, Fang L, et al. Machine vision: the third eye of quality control[J]. Auto Manufacturing Engineer, 2010(10): 51-58.
Zhu Z D, Yang H, Fang L, et al. Machine vision: the third eye of quality control[J]. Auto Manufacturing Engineer, 2010(10): 51-58.
[20] Song G. New trend of auto parts market management[N]. Southern Network, 2017-04-21.
Song G. New trend of auto parts market management[N]. Southern Network, 2017-04-21.
宋鸽. 汽车零部件市场管理新趋势[N]. 南方网, 2017-04-21.
宋鸽. 汽车零部件市场管理新趋势[N]. 南方网, 2017-04-21.
[21] 朱阳芬, 银冬平, 邹舜章, 等. 机器视觉在汽车行业中的发展与应用[J]. 汽车实用技术, 2017(22): 8-11.
朱阳芬, 银冬平, 邹舜章, 等. 机器视觉在汽车行业中的发展与应用[J]. 汽车实用技术, 2017(22): 8-11.
Zhu Y F, Yin D P, Zou S Z, et al. The development and application of machine vision in the automotive industry[J]. Automobile Applied Technology, 2017(22): 8-11.
[22] . 机器视觉检测汽车零部件OCR有/无和读取DPM[J]. 自动化博览, 2012(1): 46-47.
. 机器视觉检测汽车零部件OCR有/无和读取DPM[J]. 自动化博览, 2012(1): 46-47.
Microscan Systems. Machine vision testing automotive parts OCR with/without and reading DPM[J]. Automation Panorama, 2012(1): 46-47.
[23] 梁炳春. 基于机器视觉的辅助驾驶系统中车辆检测与测距研究[D]. 上海: 东华大学, 2016.
梁炳春. 基于机器视觉的辅助驾驶系统中车辆检测与测距研究[D]. 上海: 东华大学, 2016.
Liang BC. Vehicle detection and ranging in auxiliary driving system based on machine vision[D]. Shanghai: Donghua University, 2016.
Liang BC. Vehicle detection and ranging in auxiliary driving system based on machine vision[D]. Shanghai: Donghua University, 2016.
[24] 宋海斌. 基于单目机器视觉的人体头颅捕捉技术研究[D]. 洛阳: 河南科技大学, 2014.
宋海斌. 基于单目机器视觉的人体头颅捕捉技术研究[D]. 洛阳: 河南科技大学, 2014.
Song HB. Technology research to capture the monocular machine vision based human shull[D]. Luoyang: Henan University of Science and Technology, 2014.
Song HB. Technology research to capture the monocular machine vision based human shull[D]. Luoyang: Henan University of Science and Technology, 2014.
[25] 徐中辉, 汪峰, 陈妍, 等. 光电信息专业校内模块化实习实训平台的建设与探讨[J]. 教育教学论坛, 2017(35): 223-227.
徐中辉, 汪峰, 陈妍, 等. 光电信息专业校内模块化实习实训平台的建设与探讨[J]. 教育教学论坛, 2017(35): 223-227.
Xu Z H, Wang F, Chen Y, et al. The construction and discussion of the campus modularization practice training platform for optoelectronic information engineering[J]. Education Teaching Forum, 2017(35): 223-227.
[26] 李洪全. 三坐标测量技术在汽车制造业的应用[D]. 天津: 天津大学, 2004.
李洪全. 三坐标测量技术在汽车制造业的应用[D]. 天津: 天津大学, 2004.
Li HQ. Application of three-coordinate measuring technology in automobile manufacturing[D]. Tianjin: Tianjin University, 2004.
Li HQ. Application of three-coordinate measuring technology in automobile manufacturing[D]. Tianjin: Tianjin University, 2004.
[27] 余文超, 齐二石. 在线测量技术应用于白车身的生产尺寸监控[J]. 机械设计与研究, 2014(2): 96-98.
余文超, 齐二石. 在线测量技术应用于白车身的生产尺寸监控[J]. 机械设计与研究, 2014(2): 96-98.
Yu W C, Qi E S. Study theonline measurement technology during monitoring the dimension quality of the body-in-white production[J]. Journal of Machine Design and Research, 2014(2): 96-98.
[28] 刘庆坤. 白车身装焊误差人机交互识别技术的研究[D]. 沈阳: 沈阳理工大学, 2015.
刘庆坤. 白车身装焊误差人机交互识别技术的研究[D]. 沈阳: 沈阳理工大学, 2015.
Liu QK. Research on HCI recognition technology of BIW welding error[D]. Shenyang: Shenyang Ligong University, 2015.
Liu QK. Research on HCI recognition technology of BIW welding error[D]. Shenyang: Shenyang Ligong University, 2015.
[29] 刘常杰, 杨学友, 邾继贵, 等. 基于工业机器人白车身柔性坐标测量系统研究[J]. 光电子·激光, 2006, 17(2): 207-210.
刘常杰, 杨学友, 邾继贵, 等. 基于工业机器人白车身柔性坐标测量系统研究[J]. 光电子·激光, 2006, 17(2): 207-210.
Liu C J, Yang X Y, Zhu J G, et al. Flexible coordinate measurement system based on industrial robot for car body-in-white[J]. Journal of Optoelectronics·Laser, 2006, 17(2): 207-210.
[30] 任永杰, 邾继贵, 杨学友, 等. 白车身柔性测量机器人本体补偿方法[J]. 光电工程, 2009, 36(2): 79-84.
任永杰, 邾继贵, 杨学友, 等. 白车身柔性测量机器人本体补偿方法[J]. 光电工程, 2009, 36(2): 79-84.
[31] 骆亚微. 基于图像处理的车身漆膜缺陷识别与分类研究[D]. 长春: 吉林大学, 2016.
骆亚微. 基于图像处理的车身漆膜缺陷识别与分类研究[D]. 长春: 吉林大学, 2016.
Luo YW. Recognition and classification of car body lacquer defects based on image processing[D]. Changchun: Jilin University, 2016.
Luo YW. Recognition and classification of car body lacquer defects based on image processing[D]. Changchun: Jilin University, 2016.
[32] 孔飞, 张川, 冯日华, 等. 汽车车身漆膜缺陷自动检测系统[J]. 现代涂料与涂装, 2017, 20(3): 57-61.
孔飞, 张川, 冯日华, 等. 汽车车身漆膜缺陷自动检测系统[J]. 现代涂料与涂装, 2017, 20(3): 57-61.
Kong F, Zhang C, Feng R H, et al. Automatic inspection system for car body paint defect[J]. Modern Paint & Finishing, 2017, 20(3): 57-61.
[33] 袁文礼. 机器人装配中的视觉引导定位技术分析[J]. 科技与创新, 2017(10): 55.
袁文礼. 机器人装配中的视觉引导定位技术分析[J]. 科技与创新, 2017(10): 55.
Yuan W L. Analysis of vision guided positioning technology in robot assembly[J]. Science and Technology & Innovation, 2017(10): 55.
[34] 王卫翼, 张秋菊. 机器视觉和激光切割技术在异形吸塑包装中的应用研究[J]. 包装工程, 2013(23): 116-120.
王卫翼, 张秋菊. 机器视觉和激光切割技术在异形吸塑包装中的应用研究[J]. 包装工程, 2013(23): 116-120.
Wang W Y, Zhang Q J. Application of machine vision and laser cutting technology in special-shaped blister packaging[J]. Packaging Engineering, 2013(23): 116-120.
[35] 彭斐. 探寻机器视觉与激光加工的未来之路 2011慕尼黑上海激光、光电展参观记[J]. 汽车与配件, 2011(19): 42-43.
彭斐. 探寻机器视觉与激光加工的未来之路 2011慕尼黑上海激光、光电展参观记[J]. 汽车与配件, 2011(19): 42-43.
Peng F. Explore the future road of machine vision and laser processing. 2011 Munich Shanghai laser and Optoelectronics exhibition[J]. Automobile & Parts Technology, 2011(19): 42-43.
[36] 王亚运. 基于机器视觉的机器人涂胶质量在线检测技术研究[D]. 哈尔滨: 哈尔滨工业大学, 2015.
王亚运. 基于机器视觉的机器人涂胶质量在线检测技术研究[D]. 哈尔滨: 哈尔滨工业大学, 2015.
Wang YY. Research on online inspection technology for robot glue spreading quality based on machine vision[D]. Harbin: Harbin Institute of Technology, 2015.
Wang YY. Research on online inspection technology for robot glue spreading quality based on machine vision[D]. Harbin: Harbin Institute of Technology, 2015.
[37] 王海龙, 赵继成, 靳立昆, 等. 一起汽车短周期螺柱焊接质量事故分析[J]. 汽车科技, 2014(2): 48-53.
王海龙, 赵继成, 靳立昆, 等. 一起汽车短周期螺柱焊接质量事故分析[J]. 汽车科技, 2014(2): 48-53.
Wang H L, Zhao J C, Jin L K, et al. Sample analysis of quality control for automotive short cycle stud welding[J]. Automobile Technology, 2014(2): 48-53.
[38] 李博, 李仕奇, 谭振豪. 基于机器视觉的封印产品字符编码检测系统[J]. 现代制造工程, 2013(6): 88-91.
李博, 李仕奇, 谭振豪. 基于机器视觉的封印产品字符编码检测系统[J]. 现代制造工程, 2013(6): 88-91.
Li B, Li S Q, Tan Z H. Seal character encoding inspection system based on machine vision[J]. Modern Manufacturing Engineering, 2013(6): 88-91.
[39] . 追溯读码,康耐视使命必达[J]. 汽车工艺师, 2014(11): 26-27.
. 追溯读码,康耐视使命必达[J]. 汽车工艺师, 2014(11): 26-27.
Conway Vision Company. Traceability code, Condon mission[J]. Auto Manufacturing Engineer, 2014(11): 26-27.
Article Outline
尹仕斌, 任永杰, 刘涛, 郭思阳, 赵进, 邾继贵. 机器视觉技术在现代汽车制造中的应用综述[J]. 光学学报, 2018, 38(8): 0815001. Shibin Yin, Yongjie Ren, Tao Liu, Siyang Guo, Jin Zhao, Jigui Zhu. Review on Application of Machine Vision in Modern Automobile Manufacturing[J]. Acta Optica Sinica, 2018, 38(8): 0815001.