激光复合焊接7020铝合金的疲劳性能及损伤行为
下载: 704次
1 引言
7020铝合金属于热处理强化Al-Zn-Mg系合金,具有比强度高和焊接性优良的特性,室温下拥有极强的时效强化能力,被广泛应用于高速列车的关键部件[1-2]。激光-电弧复合焊接可以获得质量优异的铝合金焊接接头,焊接效率高,在车辆构件方面具有广阔的发展潜力和应用前景[3-5]。车辆构件在服役中会承受交变载荷,疲劳断裂是威胁构件长期服役的主要问题之一[6]。因此,研究焊接接头的疲劳性能和开裂机制至关重要。
目前,国内外学者主要从疲劳损伤机制和数值仿真两方面开展了铝合金焊接接头疲劳行为的研究[6]。气孔是铝合金熔焊过程中最常见的体缺陷之一,气孔致疲劳损伤是铝合金焊接结构研究的热点之一。气孔的存在减小了构件的有效承载面积,造成材料局部应力集中,使材料的动载性能降低[7]。Buffière等[8]指出,体积分数为1%的气孔会使材料的疲劳寿命降低50%,疲劳极限下降20%,疲劳强度及其离散性取决于萌生裂纹的气孔尺寸。McDowell等[9]发现,当诱发裂纹的气孔直径为50 μm时,裂纹萌生寿命为疲劳总寿命的50%~70%;当气孔直径为200 μm或400 μm时,裂纹萌生寿命为疲劳总寿命的20%~30%。韧性材料的疲劳损伤过程分为裂纹萌生、短裂纹扩展和长裂纹扩展三个阶段[10],裂纹萌生阶段主要受微气孔影响[11],表面或近表面处较大的气孔易诱导裂纹萌生[12]。大部分铸造铝合金的疲劳断裂源于试样表面或近表面[13]。当气孔刚好位于自由表面之下,萌生裂纹的可能性最大[14]。Serrano等[15]发现,即使表面气孔尺寸仅为内部气孔的十分之一,同样会引起最终失效断裂,高周疲劳几乎不存在内部气孔致损伤断裂现象。Zhang等[16]认为,直径为80 μm的气孔是铸造铝合金诱导裂纹萌生的临界尺寸。Toda等[13]发现,距离自由表面20~30 μm处,平均尺寸为4~5 μm的聚集型小气孔是裂纹萌生的危险点。
裂纹萌生后,材料进入短裂纹扩展阶段,短裂纹扩展在微结构与裂纹耦合作用下存在局部加速或减速现象。应力集中系数较高的气孔会促进裂纹连通前沿气孔而加速扩展;当裂纹穿越前沿气孔后,会出现缺口钝化效应,同时,裂纹扩展方向发生偏折致裂纹闭合,使得扩展速率减小[10]。Buffière等[8]指出,当主裂纹长度达400 μm以上时,裂纹扩展行为对微观缺陷的敏感程度显著降低。何超等[17]发现,当裂纹长度大于气孔半径的3.5倍时,气孔对裂尖应力强度因子的影响可以忽略。有关气孔致疲劳损伤行为的研究主要集中于铸造铝合金,而焊接气孔的大小、形态和位置分布均不同于铸造孔洞的,因此,有必要开展焊接接头内部气孔与裂纹萌生寿命和扩展行为的研究。
随着对材料疲劳损伤机制的深入研究,表征手段得到不断改进。2006年,Buffière等[18]利用集成于同步辐射光源的微型疲劳试验机对材料疲劳损伤行为开展了实时原位可视化研究。通过计算机断层切片图(CT)的三维重构仅能捕捉到试样裂纹萌生和扩展阶段的状态信息,而基于裂纹和焊接缺陷真实形貌、大小和分布的有限元模拟可以获取材料连续变形过程及相应的应力应变场信息,这是目前材料疲劳损伤机制研究的热点之一[19]。
本文通过激光-熔化极稀有气体保护电弧(MIG)复合焊得到了7020铝合金接头,分析了焊接接头的微观组织、力学性能、疲劳性能和裂纹扩展行为。该研究为激光复合焊接技术在高铁车辆构件中的应用提供了试验依据。
2 试验材料与方法
试验材料为2 mm厚的7020-T651铝合金板材;填充材料采用直径为1.2 mm的ER5356焊丝,铝合金板材和焊丝的化学组成见
表 1. 7020-T651铝合金和ER5356焊丝的化学组成(质量分数,%)
Table 1. Chemical compositions of 7020-T651 aluminum alloy and ER5356 filler (mass fraction, %)
|
表 2. 激光-MIG复合焊接工艺参数
Table 2. Process parameters for hybrid laser-MIG hybrid welding
|
取焊缝形貌光滑连续的焊接试板沿焊缝横截面制备电子背散射衍射(EBSD)样品。采用金刚石抛光液和硅溶胶对样品表面进行精细抛光和离子刻蚀。采用双束聚焦离子束扫描电镜(SEM,LYRA 3,泰思肯公司,捷克)进行焊接接头的织构检测和Mg元素线分布测定。Zn元素的面分布在上海同步辐射光源(SSRF)BL15U1线站测试获得,X射线光子能量为18 keV,步长为0.05 mm,扫描时间为2.7 s。
试验前需去除焊缝上下表面余高和其他几何不连续处,试样的厚度为1.9 mm。采用材料试验机(MTS809,MTS公司,美国)进行拉伸试验,加载速率为1 mm·min-1。采用疲劳试验机(Amsler HFP 5000,Amsler公司,德国)进行高周疲劳试验,选用轴向拉-拉加载方式,载荷波形为恒幅正弦波,加载频率为50 Hz,应力比为0.1。室温疲劳裂纹扩展速率试验在疲劳试验机(MTS809,MTS公司,美国)上进行,加载方式为循环正弦波,最大工作载荷为25 kN,试验频率为10 Hz,应力比为0.1;利用线切割制备标准紧凑拉伸试样,缺口尖端位于焊缝区域。
结合三维X射线成像技术,利用微型疲劳试验机,对复合焊接头进行疲劳加载并实时观测裂纹萌生和扩展行为。试验参数是试验机频率为8 Hz,应力比为0.2,最大力为230 N;X射线光子能量为26 keV,试样距探测器18 cm,像素尺寸为3.25 μm,曝光时间为500 ms。试样尺寸和试验原理如
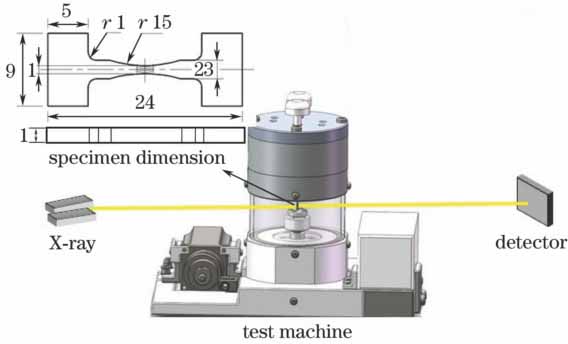
图 2. 复合焊接头各区域微观织构与晶粒尺寸分布。(a)焊缝;(b)细晶区;(c)母材
Fig. 2. Microstructure and grain diameter distribution in different zones of hybrid welded joints. (a) Weld zone; (b) fine grain zone; (c) as-received base metal
3 试验结果与分析
3.1 织构特征与元素分布
复合焊接头各区域的微观织构和晶粒尺寸如
在高能量密度的复合焊热源作用下,接头组织的成分变化情况如
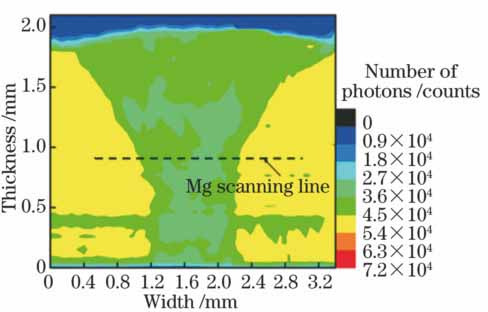
图 3. 复合焊接头Zn面分布和Mg线分布
Fig. 3. Zn plane-distribution and Mg line-distribution of hybrid welded joint
3.2 拉伸性能
7020铝合金母材和3个月自然时效下复合焊接头室温拉伸曲线如
式中
3.3 应力-寿命(S-N)曲线
焊接接头的疲劳性能由疲劳
疲劳载荷名义应力范围Δ
(2)式两边取对数为
式中
将各组疲劳结果Δ
式中
当
对铝合金母材和复合焊接头的疲劳数据进行整理,得到名义应力中值
由
规弧焊对接接头的疲劳强度,复合焊接头的疲劳性能满足现行的设计标准,可应用于实际工程。此外,对应于2×106循环周次下的复合焊接头的疲劳强度约为母材的63.14%,焊接过程降低了材料的疲劳性能。焊接是一个快速加热与冷却的过程,焊后接头成为一个成分复杂的不均匀体,接头局部区域的抗疲劳性能决定了焊接结构的安全性和可靠性。接头各区域的焊接热循环差异较大,且母材和填充金属成分不完全相同,这会导致接头的成分、组织分布不均匀,存在变化梯度较大的薄弱环节[24];焊后伴随着强化元素的蒸发烧损以及强化相大量溶解、分解与长大的现象,接头焊缝区域软化严重,裂纹扩展阻力降低,不均匀性对焊接结构的抗疲劳断裂行为具有重要影响[20]。此外,熔焊过程会产生气孔和夹杂等焊接缺陷,导致接头几何形状不连续和有效承载面积减小,材料的疲劳强度降低。
表 3. 疲劳性能参数
Table 3. Fatigue parameters
|
3.4 原位同步辐射X射线成像
由Amira三维图像重构软件获取的垂直于加载方向上的裂纹萌生和部分扩展阶段的三维形貌如
疲劳裂纹萌生于接头熔合区表面深约103 μm的缺口处,裂纹萌生寿命
疲劳裂纹扩展路径的表征结果如
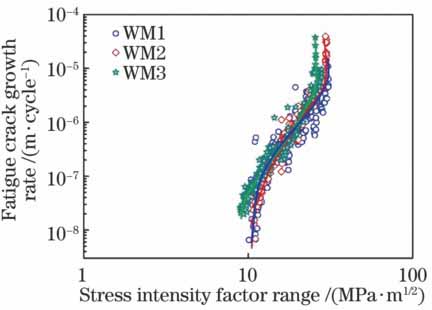
图 8. 3组复合焊接头的疲劳裂纹扩展速率与应力强度因子幅间的关系
Fig. 8. Relationship between fatigue crack growth rate and stress intensity factor range for three groups of hybrid welded joints
为进一步说明气孔对稳定扩展阶段裂纹速率的影响,进行了室温下疲劳裂纹扩展速率试验,
基于同步辐射X射线成像得到了同一焊接接头3个不同取样位置的气孔分布图,如
结合同步辐射X射线三维成像和扫描电镜对疲劳损伤机理开展了研究,复合焊接头疲劳断口形貌的SEM图如
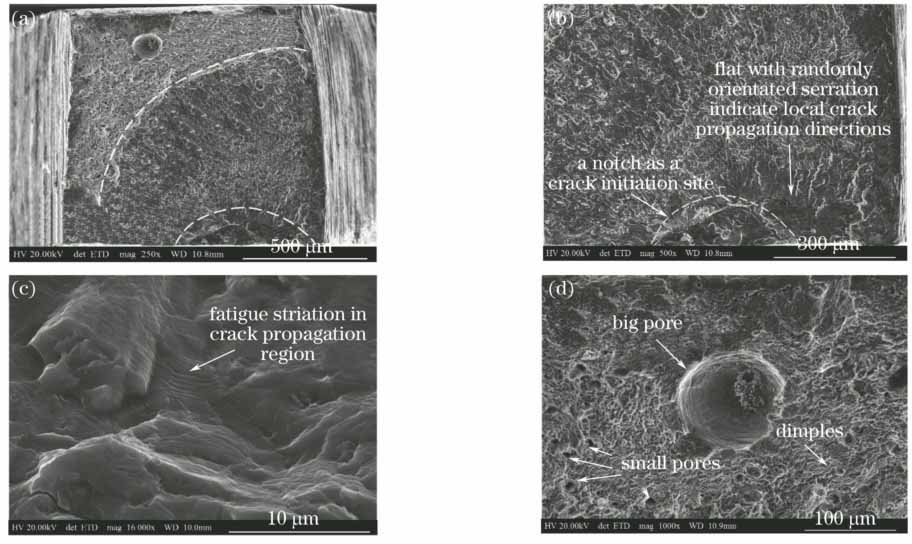
图 10. 复合焊接头疲劳断口形貌。(a)宏观形貌;(b)疲劳源区;(c)稳定扩展区的疲劳辉纹;(d)瞬断区
Fig. 10. Fracture morphology of hybrid welded joints. (a) Overall morphology; (b) fracture origin; (c) fatigue striation in crack extension region; (d) rupture region
为探究裂纹尖端塑性区分布及气孔对疲劳强度的影响,结合同步辐射X射线得到的真实缺陷,利用有限元对裂纹扩展最后一阶段即
将Mimics软件得到的真实气孔和裂纹形貌导入SolidWorks软件中,建立含缺陷的实体模型,如
当
对于即将失稳断裂的接头试样,裂纹长度达0.85 mm,占试样厚度的77.98%,裂纹所在截面材料厚度显著减小,在裂纹扩展最后阶段,裂纹附近100 μm的大气孔和密集分布的小气孔会显著减小裂纹尖端区域的有效承载面积,裂尖产生更为明显的应力集中,导致裂纹更易向薄弱部位扩展直至试样破坏。基于真实缺陷裂尖力学行为的有限元模拟更清晰地反映出7020铝合金复合焊接头在疲劳加载过程中的力学响应。
![N=77300循环周次时的应力分布。(a)裂纹尖端的理论应力分布[29];(b) 裂纹尖端应力分布;(c)裂纹与气孔周围应力分布;(d)裂纹周围应力分布](/richHtml/zgjg/2018/45/3/0302003/img_12.jpg)
图 12. N=77300循环周次时的应力分布。(a)裂纹尖端的理论应力分布[29];(b) 裂纹尖端应力分布;(c)裂纹与气孔周围应力分布;(d)裂纹周围应力分布
Fig. 12. Stress distributions when N is 77300 cycles. (a) Theoretical stress distribution of crack tip[29]; (b) stress distribution around crack tip; (c) stress distribution around crack and pores; (d) stress distribution around crack
4 结论
通过试验对激光-MIG复合焊接7020铝合金的微结构特性、力学性能、疲劳性能和断裂行为进行了研究分析,得到以下结论。
1) 焊缝区由平均晶粒直径约为33 μm的铸态等轴枝晶组成,母材为纤维状轧制态组织,平均晶粒宽度约为28 μm。焊缝区强化元素Zn发生了严重的蒸发烧损。
2) 复合焊接头的静载抗拉强度和屈服强度分别为265.34 MPa和218.85 MPa,接头强度系数为0.74。
3) 在50%存活率下,当疲劳寿命为2×106循环周次时,对应的接头疲劳强度为96.13 MPa,约为母材的63.14%。复合焊接头拉伸和疲劳性能均满足工程设计要求。
4) 疲劳裂纹萌生于复合焊接头熔合区,呈现典型的I型四分之一椭圆裂纹扩展形貌,气孔对疲劳裂纹稳定扩展阶段的速率影响较小。
[1] 彭小燕, 曹晓武, 段雨露, 等. 7020铝合金MIG焊焊接接头的组织与性能[J]. 中国有色金属学报, 2014, 24(4): 912-918.
[2] 胡雅楠, 吴圣川, 张思齐, 等. 基于三维X射线成像的激光复合焊接7020铝合金的组织与力学特性演变[J]. 中国激光, 2016, 43(1): 0103007.
[3] 赵琳, 塚本进, 荒金吾郎, 等. 激光-电弧复合焊焊缝合金元素分布的研究[J]. 中国激光, 2015, 42(4): 0406006.
[4] 乔俊楠, 王启明, 邹江林, 等. 光纤激光-变极性TIG复合填丝焊接A7N01铝合金接头的组织与力学性能[J]. 中国激光, 2016, 43(9): 0902001.
[5] 杨晓益, 陈辉, 王秋影, 等. A7N01P-T4铝合金激光-MIG复合焊接头微区性能[J]. 焊接学报, 2016, 37(8): 114-118.
[6] 季凯, 张静, 徐玉松. 新型高铜的6005A铝合金焊接接头疲劳性能[J]. 焊接学报, 2017, 38(1): 95-98.
[7] 吴圣川, 朱宗涛, 李向伟. 铝合金的激光焊接及性能评价[M]. 北京: 国防工业出版社, 2014.
Wu SC, Zhu ZT, Li XW.Laser welding of aluminum alloys and the performance evaluation[M]. Beijing: National Defense Industry Press, 2014.
[15] Serrano-Munoz I, Buffiere J Y, Mokso R, et al. Location, location & size: Defects close to surfaces dominate fatigue crack initiation[J]. Scientific Reports, 2017, 7: 45239.
[17] 何超, 崔仕明, 刘永杰, 等. 气孔对铝合金焊接接头超长疲劳寿命的影响[J]. 焊接学报, 2014, 35(11): 18-22.
[21] 佟建华, 张坤, 林松, 等. 搅拌摩擦焊和熔化极气体保护焊6082铝合金疲劳性能分析[J]. 焊接学报, 2015, 36(7): 105-108.
[22] 李晋永, 王文先, 慕伟, 等. AZ31镁合金TIG焊横向十字接头疲劳性能研究[J]. 太原理工大学学报, 2008, 39(S1): 8-10.
[23] Hobbacher AF.Recommendations for fatigue design of welded joints and components: XIII-1539-96/XV-845-96[S]. Paris: Internation Institute of Welding, 2002.
[24] 张亮, 方洪渊, 王林森, 等. A7N01铝合金焊接接头的不均匀特性[J]. 焊接学报, 2012, 33(11): 97-100.
[25] 喻程, 吴圣川, 胡雅楠, 等. 铝合金熔焊微气孔的三维同步辐射X射线成像[J]. 金属学报, 2015, 51(2): 159-168.
胡雅楠, 吴圣川, 宋哲, 付亚楠, 袁清习. 激光复合焊接7020铝合金的疲劳性能及损伤行为[J]. 中国激光, 2018, 45(3): 0302003. Hu Yanan, Wu Shengchuan, Song Zhe, Fu Yanan, Yuan qingxi. Fatigue Property and Fracture Behavior of 7020 Aluminum Alloys Welded by Laser-MIG Hybrid Welding[J]. Chinese Journal of Lasers, 2018, 45(3): 0302003.