喷流冷却复合陶瓷薄片激光器的热特性仿真分析及实验研究
0 Introduction
High-powered Laser Diode (LD)-pumped solid-state lasers are very important light sources for many applications such as material processing, industrial cleaning, and national defense, etc[1-4]. However, there are some disadvantages of a LD-pumped solid-state laser such as relatively unsatisfied beam quality at even higher output power, which mainly results from the serious thermally-induced birefringence and thermally-induced lens of a laser medium[5-7].
LD-pumped thin-disk solid-state lasers offer a large ratio of diameter to thickness of a laser medium. The laser beam transfers along the axial direction, which is vertical to the surface of the laser disk. An end surface cooling configuration of a thin-disk solid-state laser offers the short distance of heat conduction and a large ratio of the cooling area to the heat generation volume, which can enormously reduce the operation temperature of a laser medium. If the pumping and cooling distributions of a thin-disk solid-state laser are uniform, the heat flux will only exist along the axial direction and the temperature gradient will not exist along the radial and tangential directions. The thermally-induced optical distortion can be therefore deduced of a laser medium[8-9]. Thus, a high-performance and uniform cooling configuration is required for a thin-disk solid-state laser with the high output power and good beam quality.
In the jet cooling scheme, the flowing coolant is assumed to directly contact with a laser medium in order to generate the turbulent heat transfer, which offers some advantages of simple technique and less installed stress. There are several research works about the jet cooling thin-disk laser. In 2011, VRETENAR N et al. investigated the thermal effects of a jet impingement cooling capped YAG/Yb:YAG thin-disk laser[10]. In 2012, SARAVANI M et al. investigated the impact of the substrate thickness and material thermal conductivity effects on temperature distribution and thermal stress of thin disk laser through analyzing heat flow in jet impingement cooling system[11]. In 2014, GUO J et al. used a simulated heat source to analyze the performance of the jet cooling technology on a thin-disk laser[12]. In 2016, SHAO N et al. analyzed the core factor of cooling effect of jet array impingement unit of disk-laser crystal module[13]. In addition, there is almost no intermediate thermal resistance between the coolant and the heat medium, and the optical films cannot be directly destroyed [14-15].
As a novel lasing material, the transparent ceramic has numerous advantages compared with laser crystals for high power solid-state lasers. The physical features of pure ceramic, doped ceramic, and composite ceramic are very close to laser crystals[16-18]. A high-performance and uniform cooling for a composite ceramic can be achieved by the design optimization of the jet cooling configuration.
In this paper, we carried out the theoretical analyses, schematic design, simulation, and experiment for a jet cooling thin-disk composite ceramic laser. The structure of a jet cooling device for a thin-disk composite ceramic laser is designed, and a systematic simulation model is developed by using the turbulent heat transfer theory and Computational Fluid Dynamics (CFD) method. Two evaluation parameters for cooling capacity and uniformity of the jet cooling device are defined. The structural parameters of a jet cooling device are optimized by the simulation, and a verification experiment for thermal and power Input-Output (I-O) characteristics has been carried out afterward. At last, we compare the simulated and experimental temperatures of the upper surface of a thin-disk composite ceramic, and give some conclusions.
1 Configuration and theory
The configuration diagram of a jet cooling thin-disk composite ceramic laser is shown in
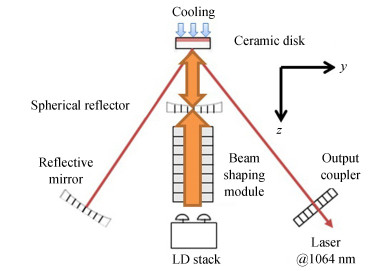
图 1. Configuration diagram of a jet cooling thin-disk composite ceramic laser
Fig. 1. Configuration diagram of a jet cooling thin-disk composite ceramic laser
The composite ceramic YAG/Nd:YAG disk consists of 4 mm-thick pure YAG and 2 mm-thick Nd:YAG with the doping concentration of 1.0 at.%. The configuration of a ceramic disk is shown in
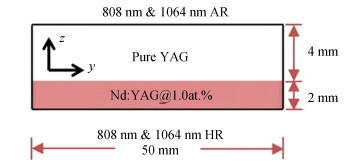
图 2. Schematic illustration of a large diameter composite ceramic
Fig. 2. Schematic illustration of a large diameter composite ceramic
The jet cooling configuration of a thin-disk composite ceramic laser is shown in
The Convective Heat Transfer Coefficient (CHTC) is adopted to quantitatively represent the cooling performance of coolant on the heat transfer surface[19]. A CHTC (W/m2/℃) is defined as the ratio of the heat flux, which is perpendicular to the heat transfer surface, to the difference between the temperatures of the heat transfer surface and coolant as expressed by
where hinterface is the CHTC of the heat transfer surface, Фq_interface is the heat flux (W/m2) perpendicular to the heat transfer surface, Tinterface and Tcoolant (℃) are the temperatures of the heat transfer surface and coolant, respectively.
According to Fourier heat conduction law, the steady-state heat conduction equation with constant physical property of solid material with internal heat source can be expressed by Poisson equation
where ▽2 is the Laplace operator, T (℃) is the temperature of solid material, Φ (W/m3) is the generated heat density of solid material, k (W/m/℃) is the thermal conductivity of solid material, respectively.
If Φ, k, and Tcoolant are acquired, and all surfaces except the heat transfer surface are assumed to be adiabatic, the temperature distribution of a thin-disk composite ceramic Tceramic(x, y, z) will be evaluated by Eq. (2) with the Robin boundary condition which is the CHTC distribution on the heat transfer surface. Thus, the evaluation of the CHTC distribution on the heat transfer surface is the key point in analyzing the thermal characteristics of a jet cooling thin-disk composite ceramic laser.
2 Simulation model and discussions
2.1 Simulation model
In this subsection, a systematic simulation model is established to explore the thermal characteristics of a jet cooling thin-disk composite ceramic laser by using a CFD software of ANSYS-CFX as shown in
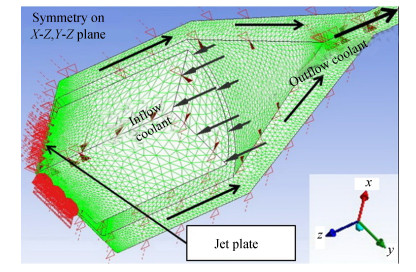
图 4. Schematic illustration of the thermal simulation of a jet cooling thin-disk composite ceramic laser
Fig. 4. Schematic illustration of the thermal simulation of a jet cooling thin-disk composite ceramic laser
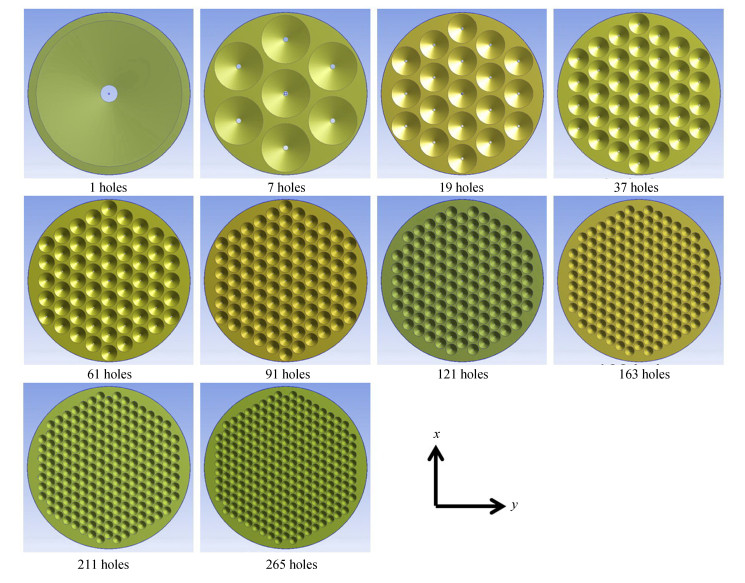
图 5. Geometric configurations of 10 kinds of jet plates with different holes
Fig. 5. Geometric configurations of 10 kinds of jet plates with different holes
Shear-Stress Transport (SST) turbulence model is adopted to calculate the turbulence and boundary layer characteristics near the heat transfer surface precisely[20].
The distribution of the CHTC on the heat transfer surface is not uniform. The area weighted average convective heat transfer coefficient (hAVE_interface) is defined to evaluate the cooling capacity of a jet cooling device on the heat transfer surface as expressed by
where A is the area of the heat transfer surface.
To evaluate the cooling uniformity of a jet cooling device on the heat transfer surface, the coefficient of variation of CHTC (CV_CHTC) is defined by the ratio of the standard deviation of the CHTC distribution to the hAVE_interface, as expressed by
The cooling capacity increases with the hAVE_interface, and the cooling uniformity decreases as the CV_CHTC increases.
2.2 Results and discussions
In this subsection, the cooling capacity and uniformity of a jet cooling device are evaluated by a simulation model as described in subsection 2.1. We consider that the equal flow resistance standard is relatively suitable for the comparison of 10 kinds of jet plates with different number of holes. The outlet diameters of 10 kinds of jet plates have been carefully adjusted to ensure that the coolant pressure differences for all jet plates are the same. Note that the flow rate of coolant passing through the jet plates are assumed to be the same value of 0.2 kg/s. Pure water is adopted as the coolant with the temperature of 20 ℃. The coolant pressure difference are therefore calculated as about 2.1 atm.
表 1. Outlet diameters of holes on 10 different jet plates
Table 1. Outlet diameters of holes on 10 different jet plates
|
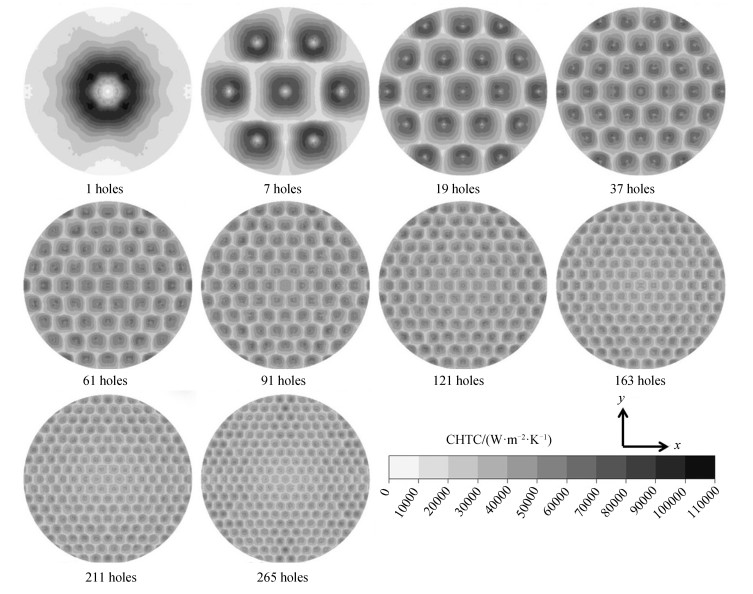
图 6. CHTC distributions for 10 kinds of jet plates with different holes
Fig. 6. CHTC distributions for 10 kinds of jet plates with different holes
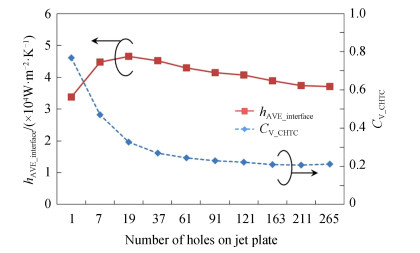
图 7. h AVE_interface and C V_CHTC for 10 kinds of jet plates with different holes
Fig. 7. h AVE_interface and C V_CHTC for 10 kinds of jet plates with different holes
FromTable 1, the outlet diameters of 163 and 211 holes are respectively 0.300 mm and 0.263 mm. According to the machining experiences, it is extremely difficult to drill a lot of holes with the diameter less than 0.3 mm on a 2 mm-thick stainless steel jet plate with the tolerance of 0.001 mm. Moreover, the CV_CHTC for 211 holes is merely 1.49% lower than that for 163 holes. Therefore, it is wise to adopt a configuration with 163 holes rather than one with 211 holes. The value of hAVE_interface for 163 holes is 83.58% of that for 19 holes, and the value of CV_CHTC for 163 holes is 64.51% of that at 19 holes. The configuration with 19 holes is the best with the highest cooling capacity among 10 cases. On the other hand, the configuration with 163 holes is the best with the best cooling uniformity. Thus, the jet plate with 163 holes, whose relatively low cooling capacity can be accepted from the viewpoint of engineering, is thought to be optimal for a high-powered jet cooling thin-disk composite ceramic laser.
3 Experiments and results
An experiment for verifying the jet cooling thin-disk composite ceramic laser has been carried out with the configuration and parameters discussed in Sections 1 and 2.
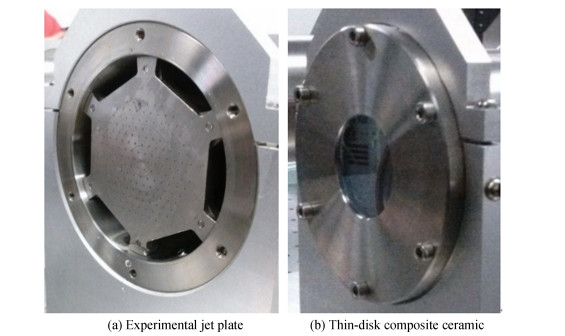
图 8. Photographs of an experimental jet plate and a thin-disk composite ceramic
Fig. 8. Photographs of an experimental jet plate and a thin-disk composite ceramic
In
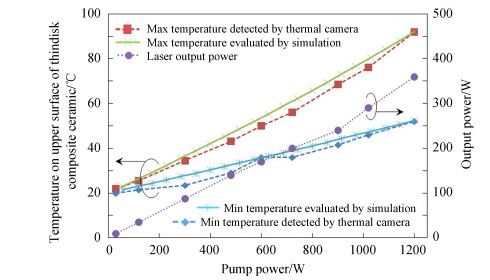
图 9. The maximal and minimal temperatures on the upper surface of a jet cooling thin-disk composite ceramic and the output power versus the pump power
Fig. 9. The maximal and minimal temperatures on the upper surface of a jet cooling thin-disk composite ceramic and the output power versus the pump power
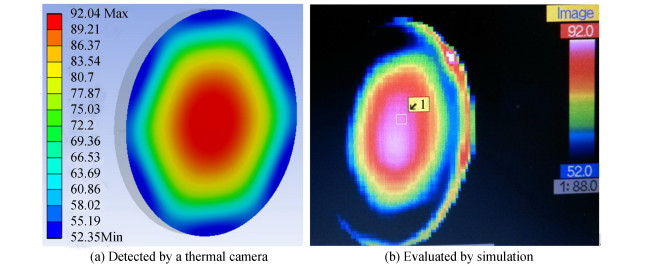
图 10. The temperature distributions on the upper surface of a 1200 W pumped composite ceramic thin-disk
Fig. 10. The temperature distributions on the upper surface of a 1200 W pumped composite ceramic thin-disk
The patterns of the temperature distributions as shown in
We find that there are some high temperature zones on the edge of a composite ceramic thin-disk in
4 Conclusion
In this study, a jet cooling device for a composite ceramic thin-disk laser has been designed, and a systematic simulation model has been developed by using the turbulent heat transfer theory and CFD method. The optimal parameters of a jet cooling device have been obtained with the simulation, and a verification experiment for thermal and I-O power characteristics has been carried out afterward. In the experiment, when the pump power is raised to 1 200 W, the output power of 359 W has been achieved, and the maximal temperature on the upper surface of the composite ceramic thin-disk detected by a thermal camera reaches 92 ℃. The temperature distributions detected by a thermal camera and evaluated by the simulation on the upper surface of a composite ceramic thin-disk are very similar to each other. It has been demonstrated that the simulation model can be employed to precisely evaluate the thermal characteristics of a jet cooling thin-disk composite ceramic laser. It has also been proved that there have been approximate positive linear relationships between the pump power and both the output power and the temperature on the upper surface of the composite ceramic thin-disk. The study is thought to be valuable for the design of a jet cooling composite ceramic thin-disk laser.
[1] JUNG M, RIESBECK T, SCHMITZ J, et al. High energy laser demonstrats f defense applications[C]. SPIE, 2016, 10254: 1025416.
[10] VRETENAR N, CARSON T, PETERSON P, et al. Thermal stress acterization of various thindisk laser configurations at room temperature[C]. SPIE, 2011, 7912: 79120B.
[12] GUO J, JIA K, YANG F. Study of jet cooling in disk laser[J]. High Power Laser and Particle Beams, 2014, 26(1): 22-26.
[14] YANG J, WANG X, YANG Q. Advances in jet impinging heattransfer[J]. Vacuum & Cryogenics, 2018, 24(4): 217-222.
[19] YANG S, TAO W. Heat transfer[M]. Beijing: Higher Education Press, 2006: 1315, 4345, 206211.
[20] WANG F. Analysis of compute fluid dynamics-CFD software theory andapplication[M]. Beijing:Qinghua University Press, 2004:12, 203.
Article Outline
郭嘉伟, 贾凯, 杨峰, 彭春, 汪晓聪, 刘晓旭, 韩聚洪, 荣克鹏, 安国斐, 蔡和, 王浟. 喷流冷却复合陶瓷薄片激光器的热特性仿真分析及实验研究[J]. 光子学报, 2020, 49(3): 0314001. Jia-wei GUO, Kai JIA, Feng YANG, Chun PENG, Xiao-cong WANG, Xiao-xu LIU, Ju-hong HAN, Ke-peng RONG, Guo-fei AN, He CAI, You WANG. Simulation and Experiment of Thermal Characteristics of a Jet Cooling Composite Ceramic Thin-disk Laser[J]. ACTA PHOTONICA SINICA, 2020, 49(3): 0314001.