激光超声结合电磁超声在铝板无损检测中的应用研究
下载: 1219次
1 引言
人类文明的发展和社会的进步与金属材料的使用密切相关。火车钢轨、航空航天、汽车制造等领域对生产加工的机械零件的厚度精准度有较高要求,同时随着长时间的反复循环使用,零件上也会产生细小裂痕甚至断裂,造成一定的经济损失甚至危害人身安全,因此需要对金属材料加工及使用过程中的厚度及裂痕损伤进行实时检测[1-2]。激光超声技术是利用脉冲激光在样品中激励出较好方向性的超声波,再通过样品内部激光超声的检测实现对样品材料的无损检测及特性评价[3-4]。相比于空气耦合超声、电磁超声,激光超声技术可以实现超声波的非接触产生和非接触接收,以及快速、实时、高精度探测分析[5-6]。
传统激光超声技术采用激光干涉仪接收激光超声波信号,可实现金属样品的厚度测量及裂痕缺陷检测[7-8]。但激光干涉仪内部结构复杂,对检测环境稳定性要求较高,一定程度上限制了激光超声技术的应用[9]。采用电磁超声换能器(EMAT)的超声信号接收部分接收脉冲激光激励样品产生的超声波,可降低激光超声技术光路的复杂性,降低检测费用[10-11]。目前,电磁超声技术已被较为广泛地应用于多种金属材料的质量检测中[12-14]。Finkel等[15]利用激光超声技术对薄金属板进行了裂痕缺陷检测,验证了电磁超声对金属薄板缺陷的检测能力。Ribichini等[16]利用多种电磁超声换能器分析了超声波在钢材中的传输方式,建立了不同换能器的有限元传输模型,并利用仿真结果验证了模型的准确性。杨理践等[17]研究了电磁超声在铝板裂痕缺陷检测中的应用,为超声波接收的优化提供了理论依据。
本文采用脉冲激光激励铝板样品产生激光超声波,再采用激光干涉仪和EMAT两种信号接收方式搭建铝板样品激光超声接收系统,优化激光超声接收参数,对比分析激光干涉仪和EMAT两种信号接收方式下的铝板厚度及表面损伤的检测精度,探索在复杂环境下基于激光超声的样品厚度及损伤等性能在线检测的最佳方法。
2 实验系统
高功率的脉冲激光垂直入射至样品表面,部分脉冲激光能量被样品材料表面吸收并转化为其内部热能,样品表面的温度迅速升高,受到热膨胀的影响样品中会产生对应的应变场和应力场,进而激发产生超声波,通过分析超声波波速与传播时间来反演超声波传播距离,反演测量样品厚度及表面损伤位置。本文实验采用的激光超声激励源为1064 nm脉冲激光,能量为80 mJ,脉冲宽度为15 ns,聚焦透镜焦距为100 mm,聚焦光斑直径约为1 mm。当脉冲激光入射至待测样品表面时,样品中将产生激光超声表面波及纵波信号,实验对比分析激光干涉仪和EMAT两种激光超声信号接收方式下,激光超声对铝板厚度及表面损伤的检测精度。
3 结果与讨论
3.1 激光干涉仪接收激光超声信号
为了提高激光超声信号的稳定性和信噪比,本文实验测量的激光超声信号数据为64次激光脉冲信号的平均数据。
激光干涉仪物光聚焦点的位置会影响表面波信号的幅值大小,
实验采用激光干涉仪探测了厚度分别为16,20,23,25,30 mm的5种铝板样品的激光超声信号。测量得表面波在铝板中的传播速度v1相对固定为3000 m/s,纵波在铝板中的传播速度v2为6460 m/s。通过第一个表面波峰值信号的探测时间t1可以计算出激光干涉仪与脉冲激光的间隔l0,纵波信号在底部界面反射后被接收为第二个峰值信号,对应时间t2,铝板厚度d的计算式为
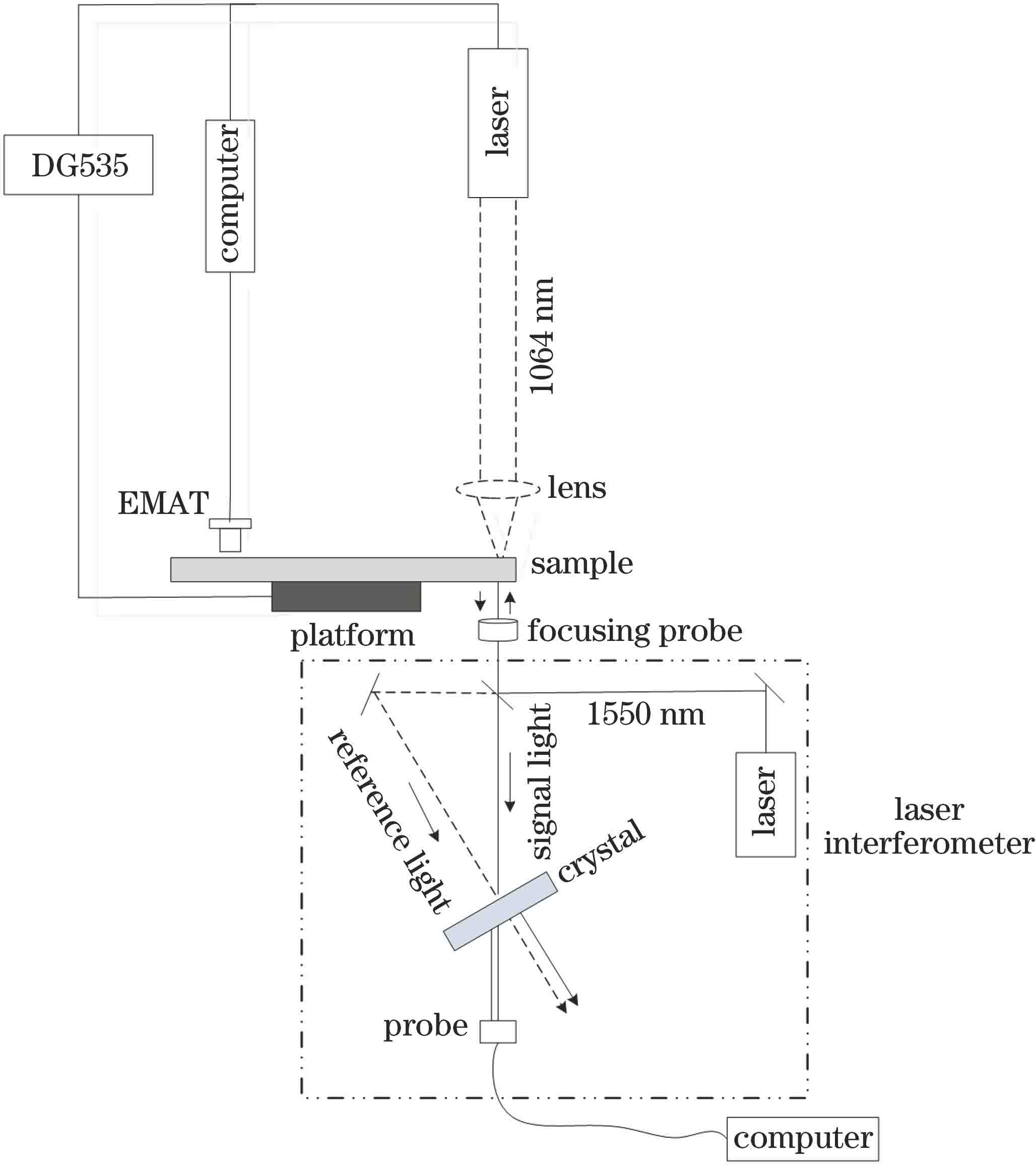
图 1. 两种不同激光超声信号接收方式的实验装置示意图
Fig. 1. Schematic of experimental setup with two different laser ultrasonic receiving methods
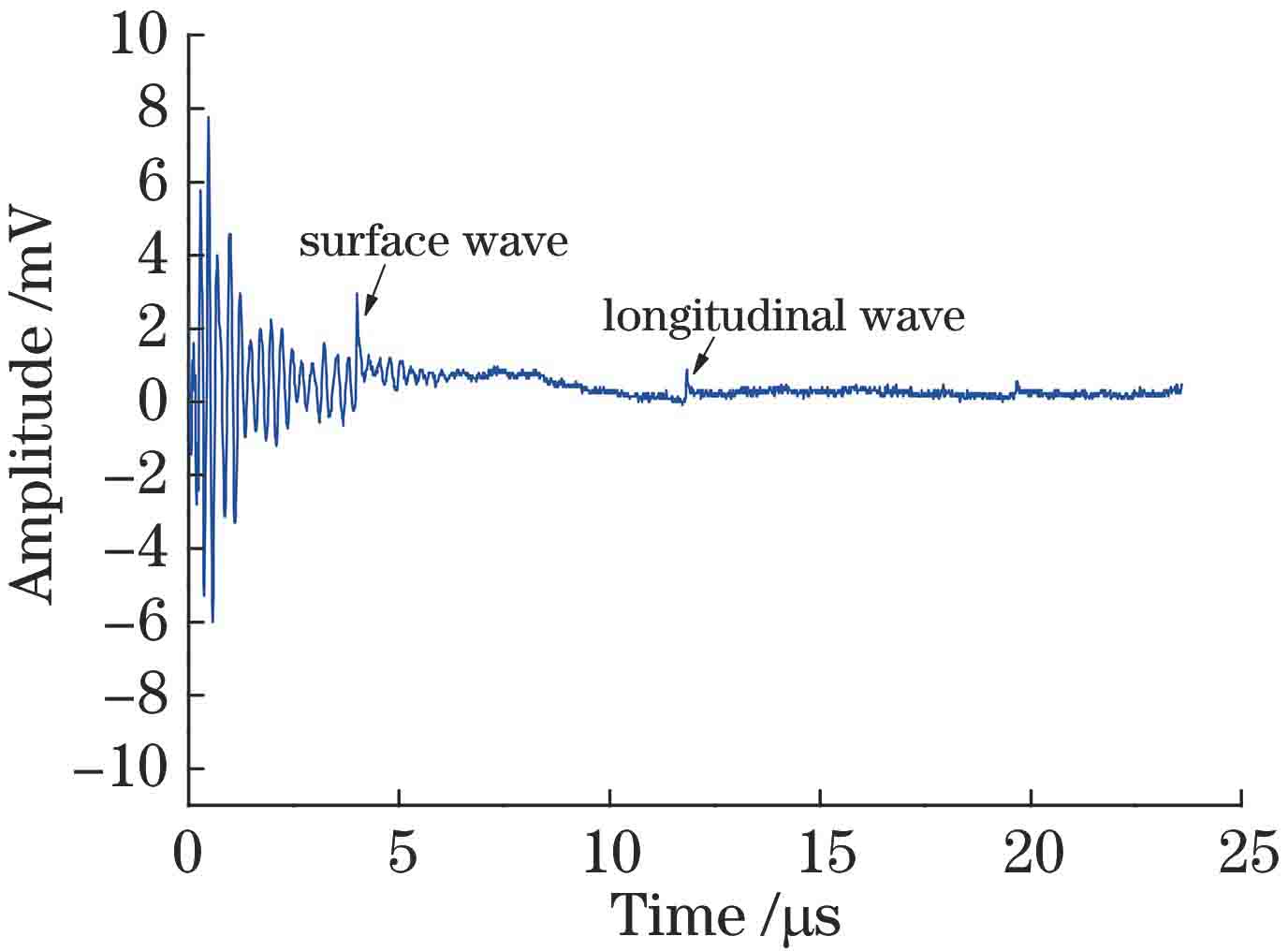
图 2. 激光干涉仪接收到的典型铝板测厚激光超声信号
Fig. 2. Typical laser ultrasonic signal of aluminum plate thickness measurement by laser interferometer
表 1. 激光干涉仪铝板厚度测量结果
Table 1. Thickness measurement results for the aluminum plates by laser interferometer
|
为了研究激光超声在样品损伤探测中的应用,实验探测了具有3个人工缺陷铝板样品的激光超声信号,其中铝板样品为100 mm×100 mm×36 mm的立方体,人工缺陷均位于铝板样品表面,分别距离左边缘22 mm、50 mm和88 mm,三个人工缺陷分别是16 mm×16 mm×6 mm、12 mm×12 mm×4 mm及6 mm×6 mm×2 mm的立方空心槽,缺陷实际位置如
为了更直观探测人工缺陷的激光超声信号,采用激光干涉仪背面探测铝板激光超声纵波信号。
式中:d表示待测样品厚度;v表示激光超声纵波传播速度;t表示纵波信号探测时间。根据所测得的激光超声纵波信号,采用(2)式计算得到人工缺陷深度,结果如
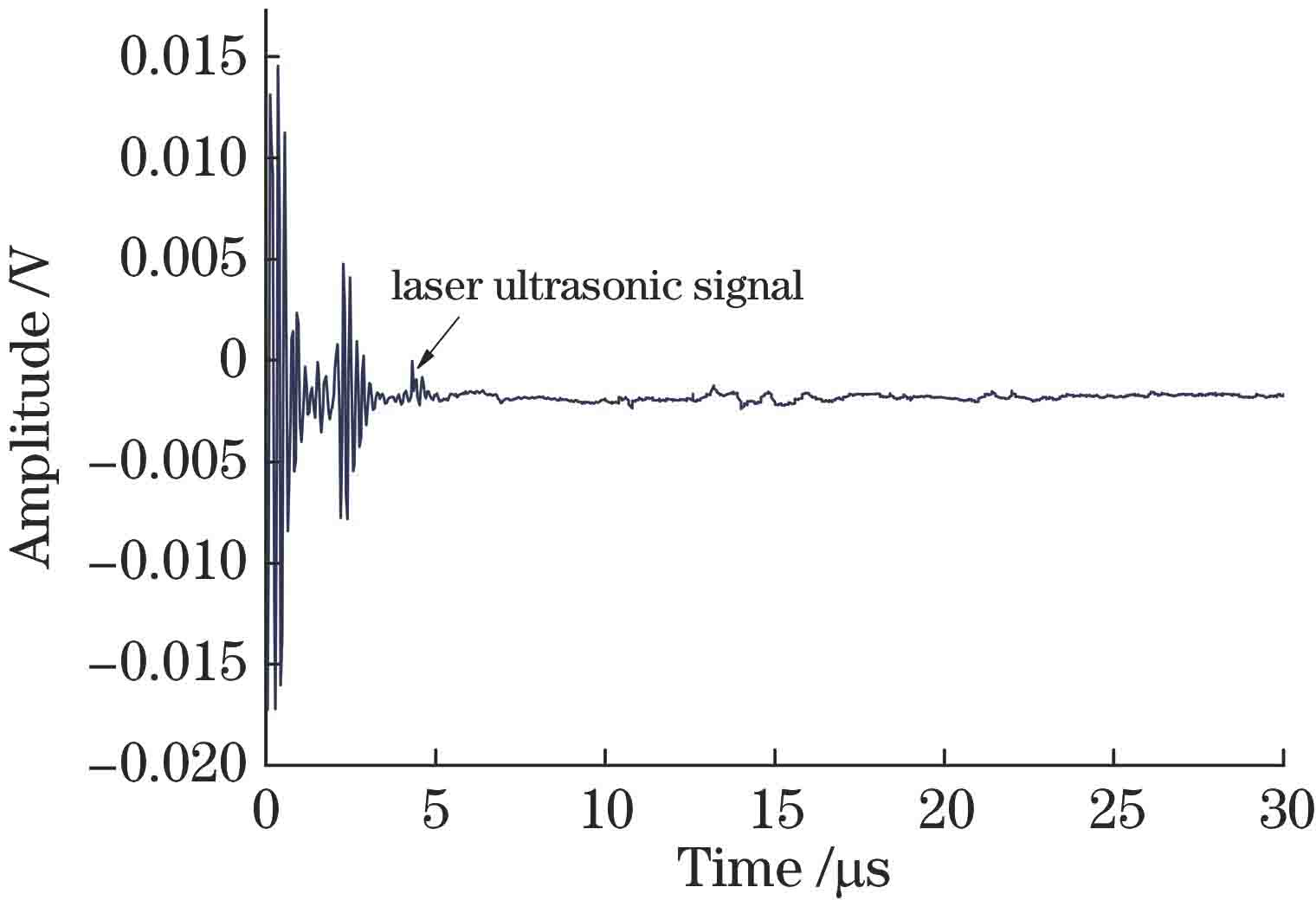
图 5. 16 mm×16 mm×6 mm人工缺陷的激光超声纵波信号
Fig. 5. Laser ultrasonic longitudinal wave signal of 16 mm×16 mm×6 mm artificial defect
表 2. 激光干涉仪测得的铝板表面裂痕缺陷深度结果
Table 2. Depth of cracks on aluminum plate by laser interferometer
|
3.2 EMAT接收激光超声信号
由于激光干涉仪对光路稳定性以及检测环境的稳定性要求较高,因此在实际工业生产环境应用中具有局限性。EMAT由高频线圈、永磁铁等较为稳固的器件组成,高频线圈被置于永磁体磁场中,区别于EMAT自发自收的小范围区域信号检测方式,本文利用脉冲激光作为激发源,待测样品表面质点在有超声信号传送时发生振动,高频线圈感应出与超声波信号对应的电压,通过探测激光超声纵波信号检测待测样品的厚度,通过探测激光超声表面波信号检测待测样品的缺陷。
对于25 mm厚的铝板样品,由EMAT接收的典型测厚激光超声纵波信号及纵波信号幅值随着EMAT与样品提离距离(EMAT探测模块与样品之间的距离)变化的趋势图如
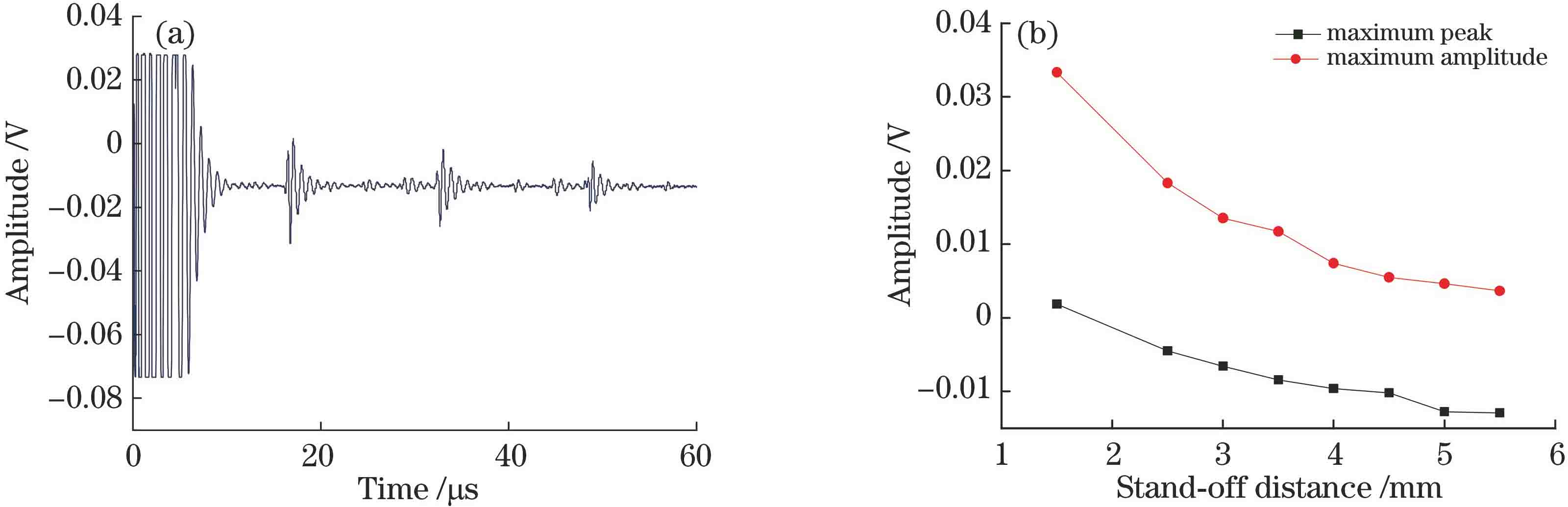
图 6. EMAT探测方式的结果。(a)典型铝板测厚激光超声信号;(b)纵波幅值与提离距离的关系曲线
Fig. 6. Results of EMAT detection method. (a) Typical laser ultrasonic signal of aluminum plate thickness measurement; (b) longitudinal wave amplitude versus stand-off distance
采用EMAT接收激光超声纵波信号测量待测样品厚度时,待测铝板样品厚度的计算式为
式中:d表示待测铝板的厚度;v表示激光超声纵波在铝板中的传播速度;Ds表示EMAT与激发脉冲激光的距离;t表示纵波信号探测时间。
激光超声在待测样品中的传播距离随着Ds的增加而增加,传播距离的远近影响样品厚度测量的精度。为了提高样品厚度测量的精度,
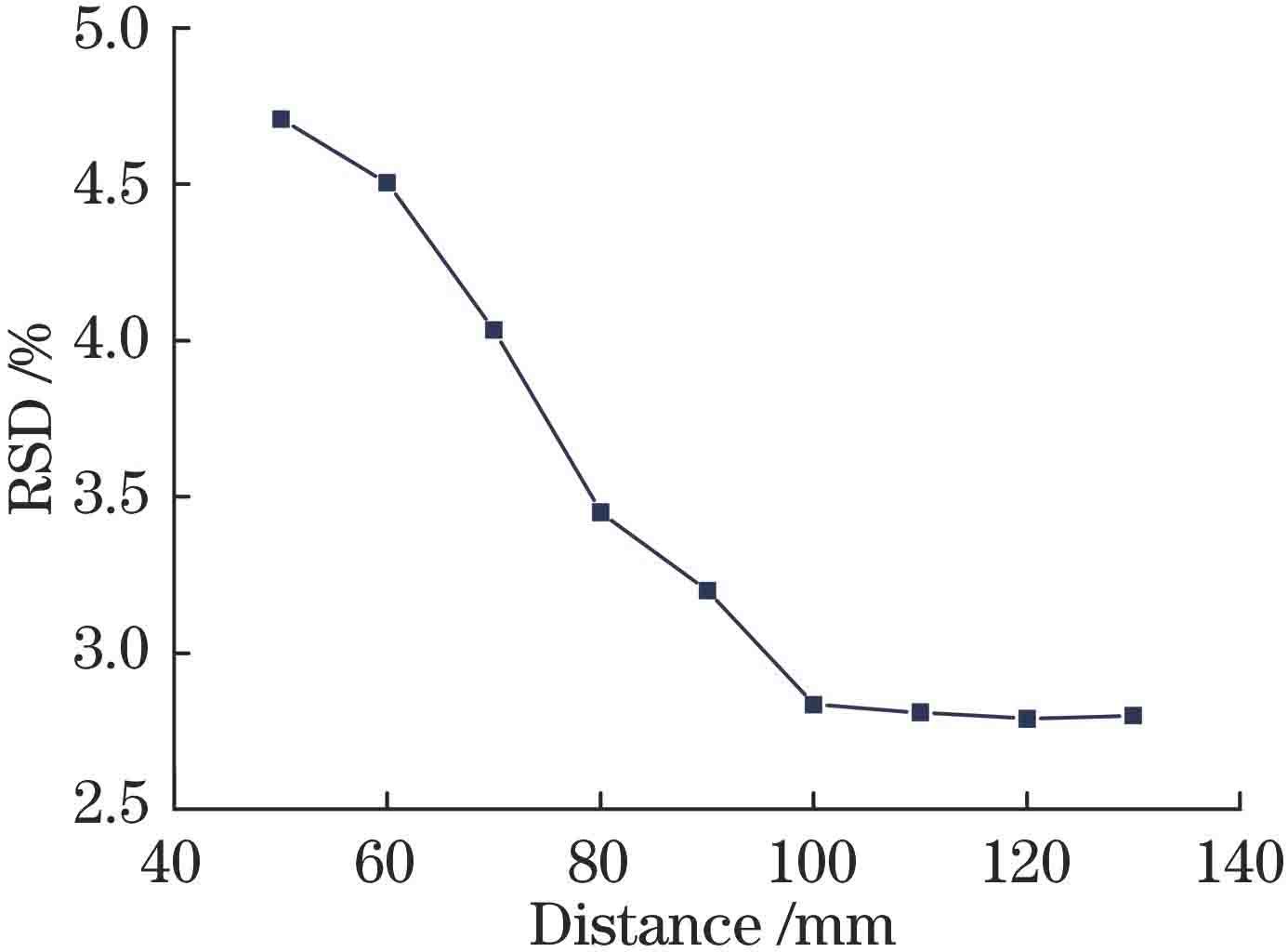
图 7. 铝板厚度测量精度与EMAT探测距离的关系曲线
Fig. 7. Measurement accuracy for aluminum plate thickness versus EMAT measurement distance
实验采用EMAT探测了厚度为16,20,23,25,30 mm的5种铝板样品的激光超声纵波信号,提取2个纵波峰值信号时间,利用(3)式计算出的5种铝板样品的厚度如
表 3. EMAT方式的铝板厚度测量结果
Table 3. Thickness measurement results for the aluminum plates by EMAT
|
同样,实验采用EMAT正面探测了人工缺陷铝板样品的激光超声表面波信号,其中触发激光光源距离铝板边缘1 mm。
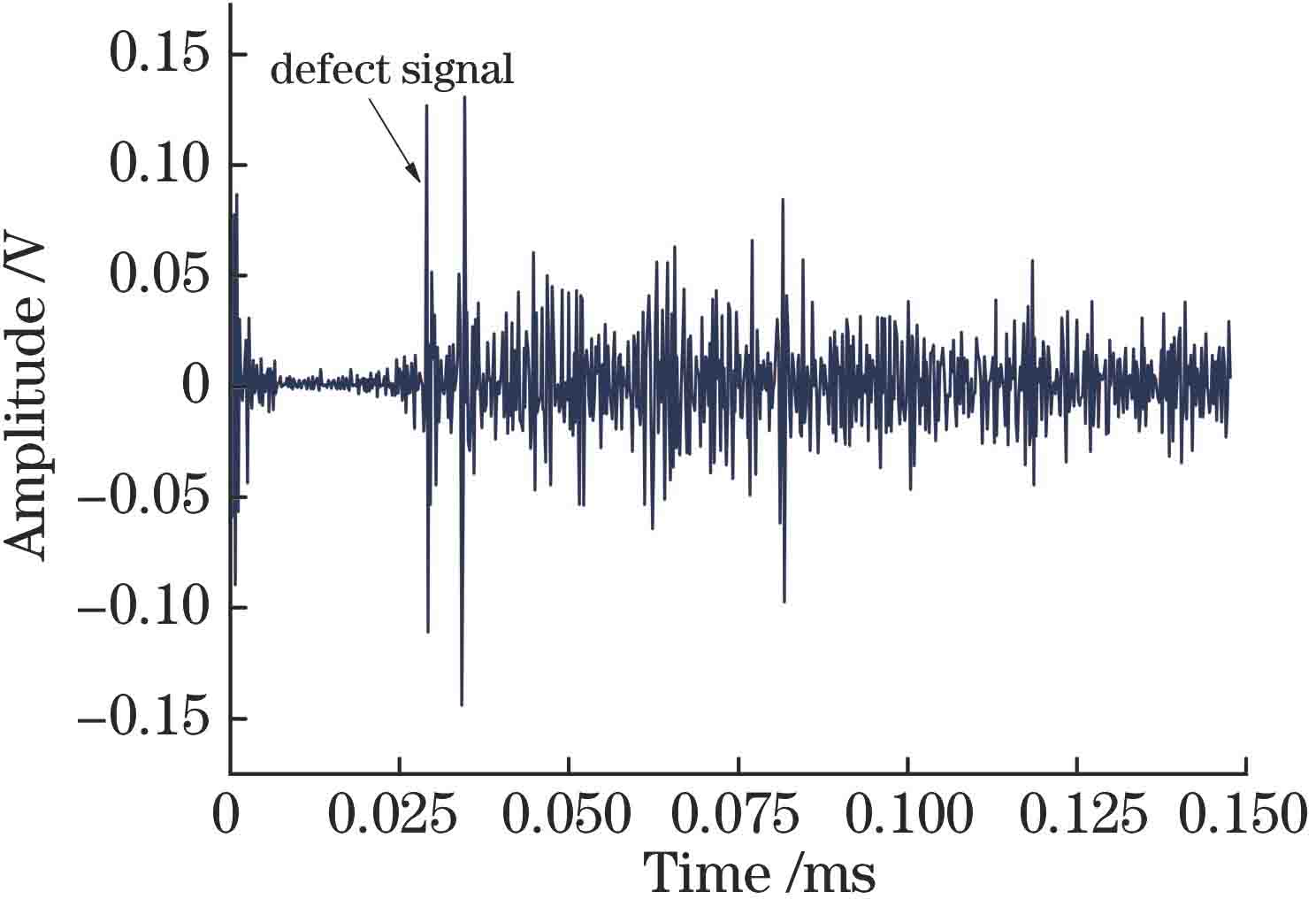
图 8. EMAT测得的人工缺陷激光超声表面波信号
Fig. 8. Laser ultrasonic surface wave signal of artificial defect detected by EMAT
由(2)式可得:
3个缺陷距离铝板边缘的预测值分别为21.73,51.49,85.33 mm,测量相对误差分别为3.32%、2.98%、3.03%,EMAT测量误差产生的主要原因是EMAT测量一定范围区间内的超声波信号时产生了一定的误差,但误差在测量误差允许范围内,因此该方式可用于铝板缺陷位置检测,当缺陷较小时也可以实现缺陷位置较为准确的预估。
4 结论
本文采用脉冲激光作为激光超声信号激励源,对比分析了激光干涉仪和EMAT两种超声波信号探测方式在铝板无损检测中的准确度和实用性。通过优化实验确定了不同信号接收方式下的最佳探测参数,在最佳实验参数条件下:激光干涉仪对铝板厚度测量的预测相对误差均小于4.31%,在对铝板表面裂痕缺陷深度进行预测时,预测结果的相对误差随着铝板表面裂痕缺陷深度的减小而增大;采用EMAT预测铝板样品厚度时,预测相对误差均小于3.1%,采用EMAT预测铝板裂痕缺陷位置时,预测相对误差均小于3.4%。由结果可知,在铝板样品的无损检测中,采用激光超声与电磁超声相结合的方法可以提高铝板测厚及表面裂痕检测的精度,同时EMAT检测方式的系统结构简单,对检测条件的稳定性要求较低,可作为金属在线无损检测的备选方法。
[1] Lee E, Kim T, Suh H, et al. Effect of metal thickness on the sensitivity of crack-based sensors[J]. Sensors, 2018, 18(9): 2872.
[2] Zhao L, Li C J, Duan Z X, et al. The metal thickness detection using pulsed eddy-current computation and detection method[J]. Cluster Computing, 2019, 22: 6551-6562.
[3] Kravcov A, Shibaev I A, Blokhin D I, et al. Examination of structural members of aerial vehicles by laser ultrasonic structuroscopy[J]. International Journal of Civil Engineering and Technology, 2018, 9(11): 2258-2265.
[4] Kusano M, Hatano H, Watanabe M, et al. Mid-infrared pulsed laser ultrasonic testing for carbon fiber reinforced plastics[J]. Ultrasonics, 2018, 84: 310-318.
[5] Yan G Q, Raetz S, Chigarev N, et al. Characterization of progressive fatigue damage in solid plates by laser ultrasonic monitoring of zero-group-velocity lamb modes[J]. Physical Review Applied, 2018, 9(6): 061001.
[6] Zarubin V, Bychkov A, Zhigarkov V, et al. Model-based measurement of internal geometry of solid parts with sub-PSF accuracy using laser-ultrasonic imaging[J]. NDT & E International, 2019, 105: 56-63.
[7] Zhou Z G, Zhang K S, Zhou J H, et al. Application of laser ultrasonic technique for non-contact detection of structural surface-breaking cracks[J]. Optics & Laser Technology, 2015, 73: 173-178.
[8] 睢晓乐, 肖夏, 戚海洋, 等. 残余应力对激光激发超声表面波技术检测二氧化硅体材料杨氏模量的影响[J]. 激光与光电子学进展, 2017, 54(12): 121202.
[9] Sun G K, Zhou Z G, Li G H, et al. Development of an optical fiber-guided robotic laser ultrasonic system for aeronautical composite structure testing[J]. Optik, 2016, 127(12): 5135-5140.
[10] 张闯, 刘成立, 刘素贞, 等. 基于电磁加载的铝板应力超声检测[J]. 仪器仪表学报, 2018, 39(8): 169-177.
Zhang C, Liu C L, Liu S Z, et al. Ultrasonic detection of aluminumstress based on electromagnetic loading[J]. Chinese Journal of Scientific Instrument, 2018, 39(8): 169-177.
[11] He J P, Dixon S, Hill S, et al. A new electromagnetic acoustic transducer design for generating and receiving S0 lamb waves in ferromagnetic steel plate[J]. Sensors, 2017, 17(5): 1023.
[12] Murav'eva O V, Len'kov S V, Murashov S A. Torsional waves excited by electromagnetic-acoustic transducers during guided-wave acoustic inspection of pipelines[J]. Acoustical Physics, 2016, 62(1): 117-124.
[13] Zhang Y, Huang S L, Wang S, et al. Direction-controllable electromagnetic acoustic transducer for SH waves in steel plate based on magnetostriction[J]. Progress In Electromagnetics Research M, 2016, 50: 151-160.
[14] Huang S L, Zhang Y, Wang S, et al. Multi-mode electromagnetic ultrasonic lamb wave tomography imaging for variable-depth defects in metal plates[J]. Sensors, 2016, 16(5): 628.
[15] Finkel P, Godinez V. Electromagnetic stimulation of the ultrasonic signal for nondestructive detection of ferromagnetic inclusions and flaws[J]. IEEE Transactions on Magnetics, 2004, 40(4): 2179-2181.
[16] Ribichini R, Cegla F, Nagy P, et al. Study and comparison of different EMAT configurations for SH wave inspection[J]. IEEE Transactions on Ultrasonics, Ferroelectrics and Frequency Control, 2011, 58(12): 2571-2581.
[17] 杨理践, 邢燕好, 张佳, 等. 基于电磁超声导波的铝板裂纹缺陷检测方法[J]. 仪器仪表学报, 2018, 39(4): 150-160.
Yang L J, Xing Y H, Zhang J, et al. Crack defect detection of aluminum plate based on electromagnetic ultrasonic guided wave[J]. Chinese Journal of Scientific Instrument, 2018, 39(4): 150-160.
Article Outline
谷艳红, 张振振, 高先和, 石朝毅, 卢军, 张胜, 周泽华. 激光超声结合电磁超声在铝板无损检测中的应用研究[J]. 中国激光, 2020, 47(5): 0504002. Yanhong Gu, Zhenzhen Zhang, Xianhe Gao, Chaoyi Shi, Jun Lu, Sheng Zhang, Zehua Zhou. Application of Nondestructive Detection of Aluminum Using Laser Ultrasonic Technology and EMAT Method[J]. Chinese Journal of Lasers, 2020, 47(5): 0504002.