基于稀疏矩阵的光学元件表面疵病检测
下载: 1130次
1 引言
随着光学产业的蓬勃发展,光滑光学元件在各个领域的应用越来越广泛,同时,对光学元件表面质量也提出了越来越高的要求,尤其在天文学、医学和航空航天领域对光学元件表面质量的要求更为苛刻[1-3]。目前光学元件表面质量的评价主要包括面形偏差、表面粗糙度及表面疵病三个方面。相较于其他缺陷而言,光学元件表面疵病的存在范围小、分布区域广且随机[4-5],但其对整个元件工作的影响却很集中且破坏力强。此外,大多数光学系统都选用激光作为光源,这时表面疵病的存在就会引起激光损伤,进一步对光学元件造成损伤,影响光学系统的整体性能。表面疵病是指光学表面有效孔径内的局部缺陷,是由制造流程和处理不当造成的。目前,最为常见的光学表面疵病是划痕、麻点和开口气泡[6-8]。因此通过对光学元件表面疵病的检测,尽可能地减少光学元件加工过程中的损伤是非常重要的。
自20世纪90年代初开始,基于机器视觉的光学元件表面缺陷检测技术就已经逐步发展起来。1996年Raafat等[9]基于机器视觉系统对玻璃和塑料表面质量进行检测,检测目标主要是表面划痕、气泡、裂纹等;1999年Kim等[10]提出了一种基于机器视觉的快速检测方法,实现对液晶显示器和等离子体显示面板的在线质量检测;2006年孙丹丹[11]对光学表面缺陷检测散射成像理论进行了建模及系统分析研究;2007年杨甬英等[12]基于显微散射暗场成像原理及机器视觉对光学表面疵病进行检测,并建立了数字化的评价系统;2015年王世通[13]对光学表面缺陷的特性进行了研究,并提出全新的标准比对板设计和制作方法,建立了疵病检测量化的标定系统,实现对疵病的正确度量;同年,Zhang等[14]针对大孔径光学元件表面缺陷的检测,提出了一种包含两种成像系统的高效精密仪器,一种是由分辨率为10 μm的线扫描相机构成的暗场成像系统,另一种是由分辨率为1 μm的显微镜构成的亮场成像系统;2016年孙佳明[15]对激光陀螺反射镜基片表面疵病进行了测量,采用旋转多次测量来避免疵病信息的丢失;2016年李阳[16]提出基于同轴反射光与散射光干涉的光学掩模版微米级疵病检测系统;2017年罗茂等[17]根据光学元件材料性质的不同对表面疵病进行了多光谱测量。在前人的基础上,本文针对大口径光学元件表面疵病检测时拼接图像过多、图像数据量过大造成的拼接速度慢等问题,提出了利用稀疏矩阵原理来减少图像数据量以缩短拼接时间的方法,完成对大口径光学元件的快速检测。
2 显微散射暗场成像原理及系统
2.1 显微散射暗场成像原理
理想状态下,当一束平行光入射到光学元件表面上时会发生透射与反射现象。在表面疵病存在的情况下,这种不均匀性引起光束偏离理想的传播方向而向四周散开,即产生了散射。如
显微散射暗场成像原理图如
2.2 显微散射暗场成像测量系统
根据显微散射暗场成像原理,建立光学元件表面疵病显微散射暗场成像系统,如
要实现对大口径光学元件表面疵病的检测,检测精度需达到微米级,因此需要利用光学系统将子孔径图像进行放大,以得到清晰的疵病图像。由于被检元件的表面口径可达几百毫米,因此必须利用
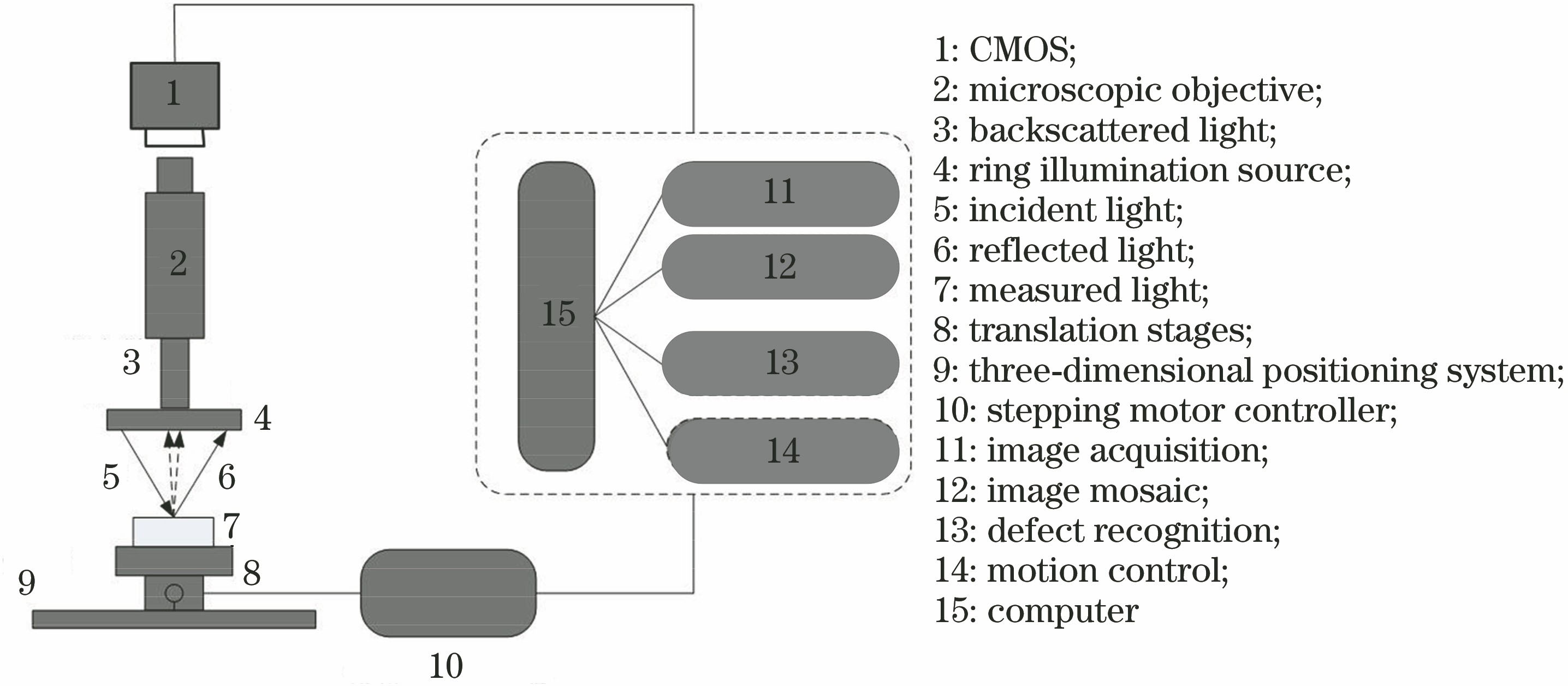
图 3. 表面疵病显微散射暗场成像系统
Fig. 3. Microscopic scattering dark field imaging system for surface defects
对全孔径疵病图像中的疵病进行识别、提取和分类。光学元件表面疵病检测的步骤为:1)对单个疵病图像进行滤波处理,消除图像中的系统噪声和背景噪声;2)对图像进行二值化处理,并利用数学形态学中的腐蚀和膨胀算法对图像中的孔洞进行填充;3)利用稀疏矩阵原理和图像拼接原理对图像进行拼接;4)基于区域识别算法及最小外接矩形对图像中的疵病进行识别,计算图像中疵病的长、宽、面积等信息,并据此对疵病种类进行区分。
3 疵病图像的采集及处理
3.1 全孔径疵病图像扫描采集
对大口径光学元件表面疵病进行采集时,通过电控平移台控制元件沿
3.2 子孔径疵病图像的滤波去噪
在图像采集过程中,由于环境、仪器自身的精度以及实验人员操作等的影响,不可避免地会在最终采集到的疵病图像上形成噪声。在该测量系统中,图像噪声主要来源于空气中的灰尘和系统中光学元件自身的缺陷。在图像处理中,如果图像中有较大的噪声,则会影响疵病检测的结果。预处理是图像处理的首要阶段,是在目标识别之前对采集到的图像进行改善处理,其主要目的是最大限度地消除各类噪声对图像中目标区域的影响、衰减图像不需要的特征,而将其中重要的特征有选择地突出。有效的图像预处理将大大提高后续图像分析识别的效果。因此,在对疵病图像进行识别之前,先要对图像进行预处理。
图像去噪是图像处理中的第一步,去噪效果的好坏直接影响后续的图像处理工作。目前比较经典的图像去噪算法主要有包括:均值滤波、中值滤波、维纳滤波和高斯滤波[18]。本文选用疵病图像最中间的图像为例,用以上4种滤波方法对疵病图像进行处理,结果如
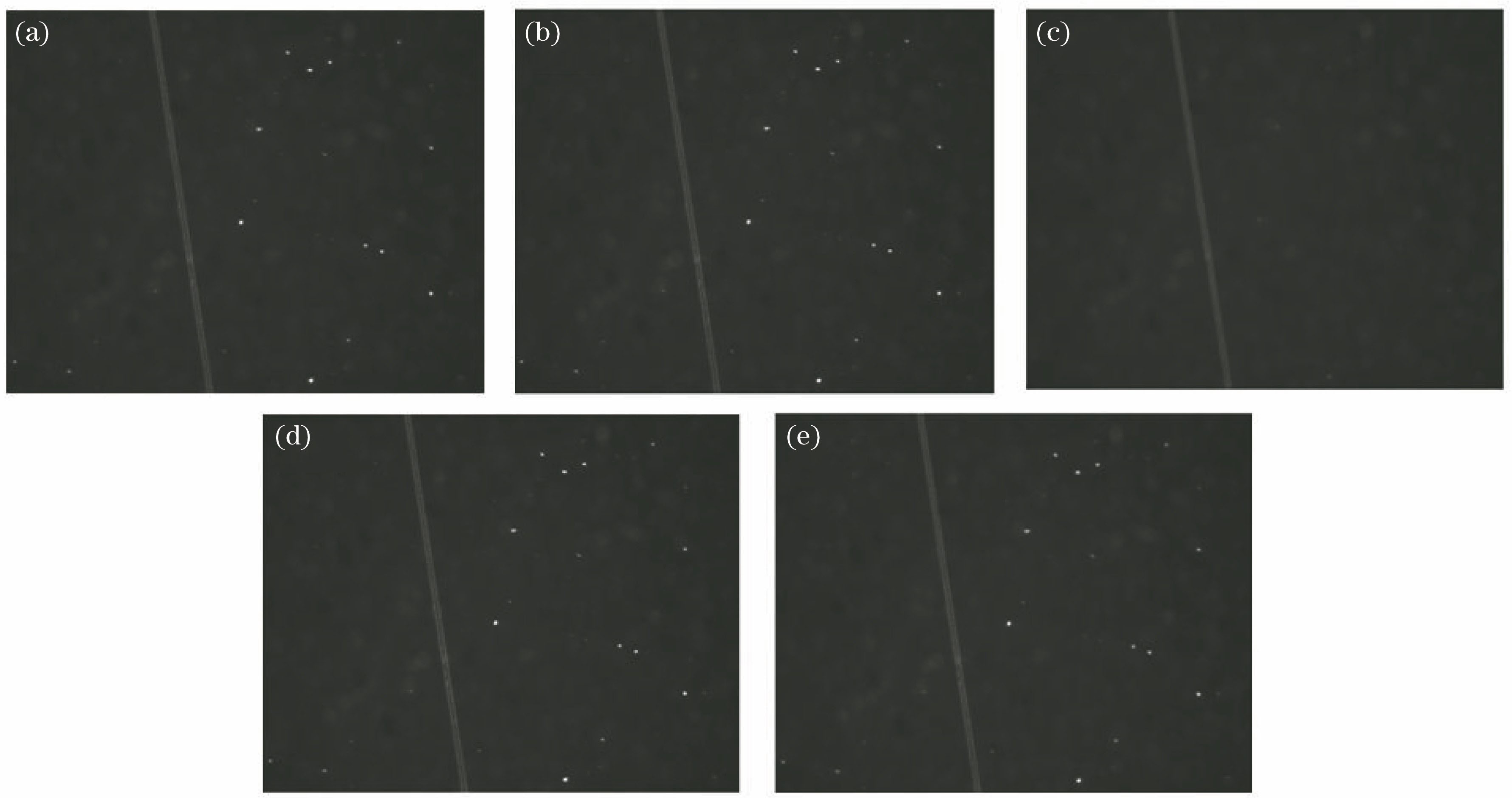
图 6. 滤波处理后的图像。(a)原始图像;(b)均值滤波;(c)中值滤波;(d)维纳滤波;(e)高斯滤波
Fig. 6. Images after filtering. (a) Original image; (b) mean filtering; (c) median filtering; (d) Wiener filtering; (e) Gaussian filtering
从原始图像中可以看出图中有很多细小的亮点,这是由灰尘造成的,在进行疵病识别时应将这些噪声滤掉。使用4种滤波方法对图像进行处理,从
3.3 图像的二值化
在图像的预处理过程中,图像二值化的目的是将图像中的特征目标从图像背景中提取出来。其原理是通过合适的方法选取合适的阈值,然后遍历整个图像,比较图像中的灰度值与阈值,将像素值大于阈值的像素点的值设为1,否则设为0,这时图像中就只有0和1两种像素,称为二值图像。例如输入图像为
在测量时,光学元件底部灰尘的不均匀性造成测量图像灰度值分布不均匀。在进行图像二值化时,当灰度值等于或大于疵病灰度值时,将噪声视为目标提取出来。图像二值化结果如
3.4 图像的数字形态学操作
数学形态学是一门建立在格论和拓扑学基础之上的图像分析学科,是数学形态学图像处理的基本理论。在图像的采集过程中,环境、光照不均匀等因素会造成采集到的划痕、麻点亮度分布不均匀。在图像二值化的过程中,划痕、麻点会出现空洞或将噪声视为目标提取出来,这些空洞和噪声会影响疵病检测的种类和数量。因此,需要对图像进行数学形态学操作,以填充图像中的空洞并消除图像中的噪声。本文主要使用腐蚀和膨胀、开运算和闭运算。
腐蚀是一种最基本的数学形态学运算,其作用是消除图像的边界点,使得边界向内部收缩。通过腐蚀可以消除较小且没有意义的干扰物。假设
式中:
膨胀是腐蚀的反操作,是将背景点中与目标区域所接触的部分合并到目标区域中,使得目标区域的边界向外扩张的一个过程。膨胀可以消除目标区域中的一些小颗粒噪声,但主要是用来填补目标区域中的空白。图像中的
式中:⌀为空集;
在叙述膨胀、腐蚀的原理时,可以明显地看到腐蚀运算和膨胀运算都存在缺陷。经过膨胀处理的图像,目标区域的面积会大于原来的面积;而经过腐蚀处理后的图像,目标物的面积会小于原来的面积。因此,在数学形态学的操作中提出了开运算和闭运算。开运算的实质是用同一个结构元素对图像先进行腐蚀、再进行膨胀的运算,其定义式为
式中:
式中:•表示闭运算。开运算可以基本保持疵病目标的原有大小不变,而且可以去除小颗粒噪声,使图像中只留下疵病特征目标的相关像素。闭运算通常用来连接断开的邻近目标和填充目标区域内的细小空洞,同时具有不明显改变目标区域大小的优点,这对后续利用最小外接矩形对块状疵病区域进行定位和评价有着巨大作用。因此,利用闭运算对图像进行形态学处理,处理后的图像如
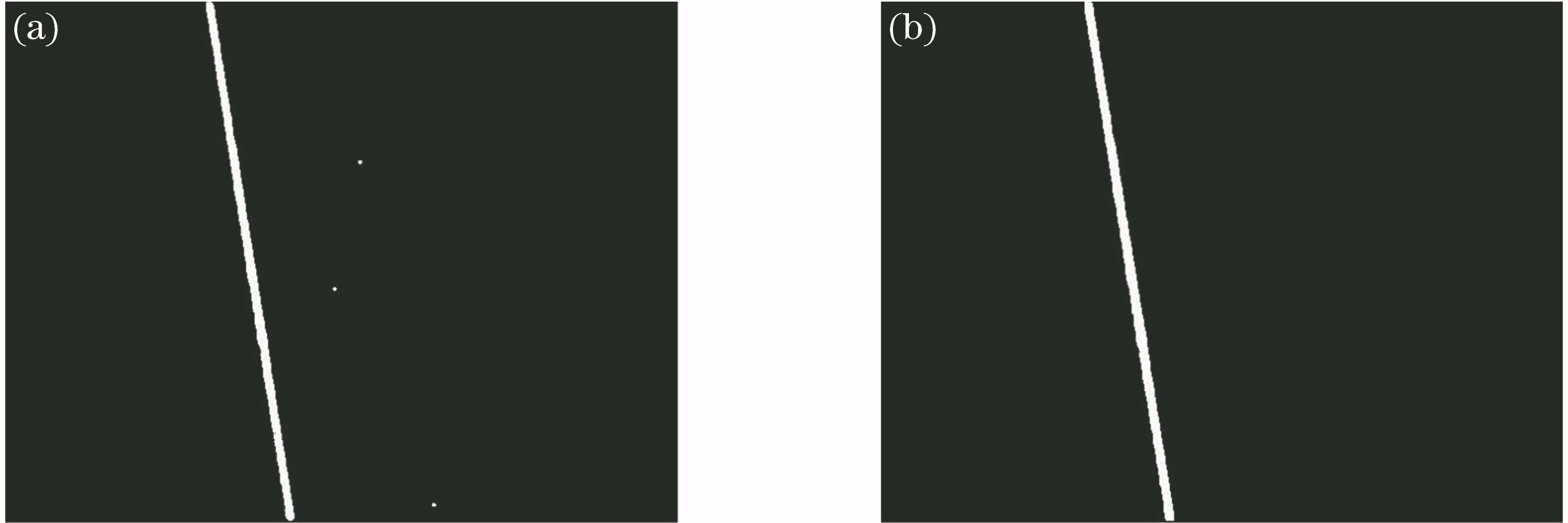
图 7. 预处理图像。(a)二值化图像;(b)形态学处理后的图像
Fig. 7. Preprocessed images. (a) Binary image; (b) morphologically processed image
4 子孔径疵病图像拼接及识别
4.1 子孔径图像拼接
图像拼接是大口径光学元件表面疵病检测最关键的一步。在大口径光学元件检测中,由于光源照射范围、显微成像系统的口径、CCD视场的限制,无法经过一次成像就完成对大口径光学元件表面疵病的检测。在本系统中,采用多幅图像拼接的技术来完成对大口径光学元件表面疵病的检测。为了实现快速拼接,将稀疏矩阵原理与图像拼接原理相结合,完成对大口径光学元件表面疵病的检测。
在大口径光学元件的检测中,由于口径较大、拼接图像太多、拼接的数据量太大,造成图像拼接时速度缓慢,拼接出的图像数据量过大,导致后续疵病识别速度缓慢,影响整个疵病检测过程。疵病在整个光学元件表面只占一小部分,疵病呈亮像,其余为暗,这时可以用稀疏矩阵的方式来保存疵病图像,大大降低图像的数据量,在进行图像运算时更加快速,从而提高图像拼接和图像处理的速度。
本文利用平移拼接和稀疏矩阵拼接两种拼接方法对图像进行拼接。平移拼接是将疵病图像按照其位置关系进行拼接,拼接图像如
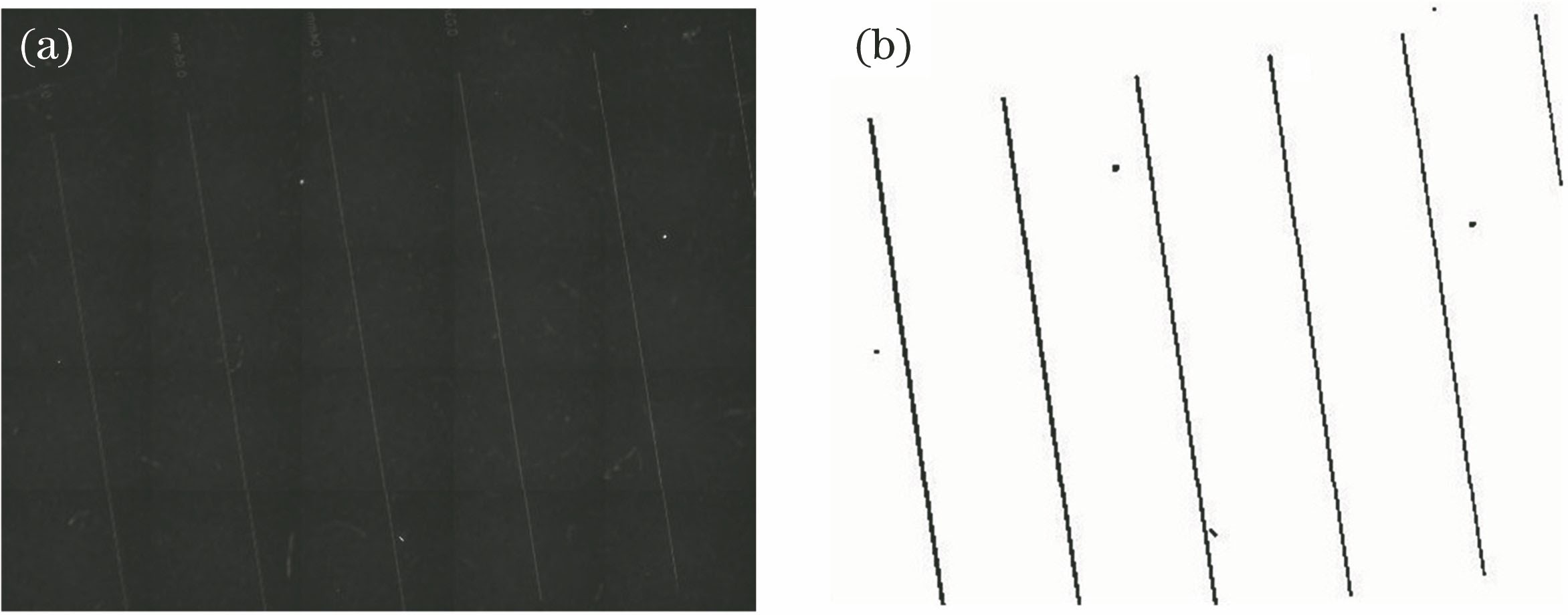
图 8. 拼接图像。(a)平移拼接图像;(b)稀疏矩阵拼接图像
Fig. 8. Mosaic images. (a) Translation mosaic image; (b) sparse matrix mosaic image
4.2 全孔径疵病图像的识别及评价
要对疵病进行评价,首先要对图像像素进行标定,然后再识别疵病的尺寸信息。在前面的工作中,已经提取出了一个完整的、轮廓清晰的疵病图像。从
计算最小外接矩形的长、宽、面积,即为图像中疵病的长、宽、面积,再利用疵病的长宽比,判断疵病类型。美国的表面疵病标准(美军标MIL-PRP-13830及MIL-O-13830)规定疵病横向长宽比小于4∶1的为麻点,反之为划痕。由此对疵病的类型进行了区分。检测结果如
表 1. 疵病结果统计表
Table 1. Statistical table of defect results
|
4.3 误差分析
标准值是指采用多种可靠的分析方法,由具有丰富经验的分析人员经过多次测定得出的比较准确的结果。测量值指使用测量仪器和工具,通过测量和计算得到一系列测量数据。采用标准划痕板作为被测件,经过显微散射暗场成像系统及计算机处理得到划痕的测量结果。测量仪器及计算过程中的误差,造成测量值与真实值之间存在误差。由于标准板只给出了划痕宽度的标准值,因此只对划痕的宽度误差进行计算,误差大小如
表 2. 划痕宽度误差
Table 2. Scratch width errors
|
上述是对标准划痕板进行处理后得到表面疵病的信息。在此基础上,对光学元件表面疵病也进行了检测。采用30 mm×30 mm的光学元件,按照上述的扫描路径采集16幅子孔径图像。以其中两幅图像为例,如
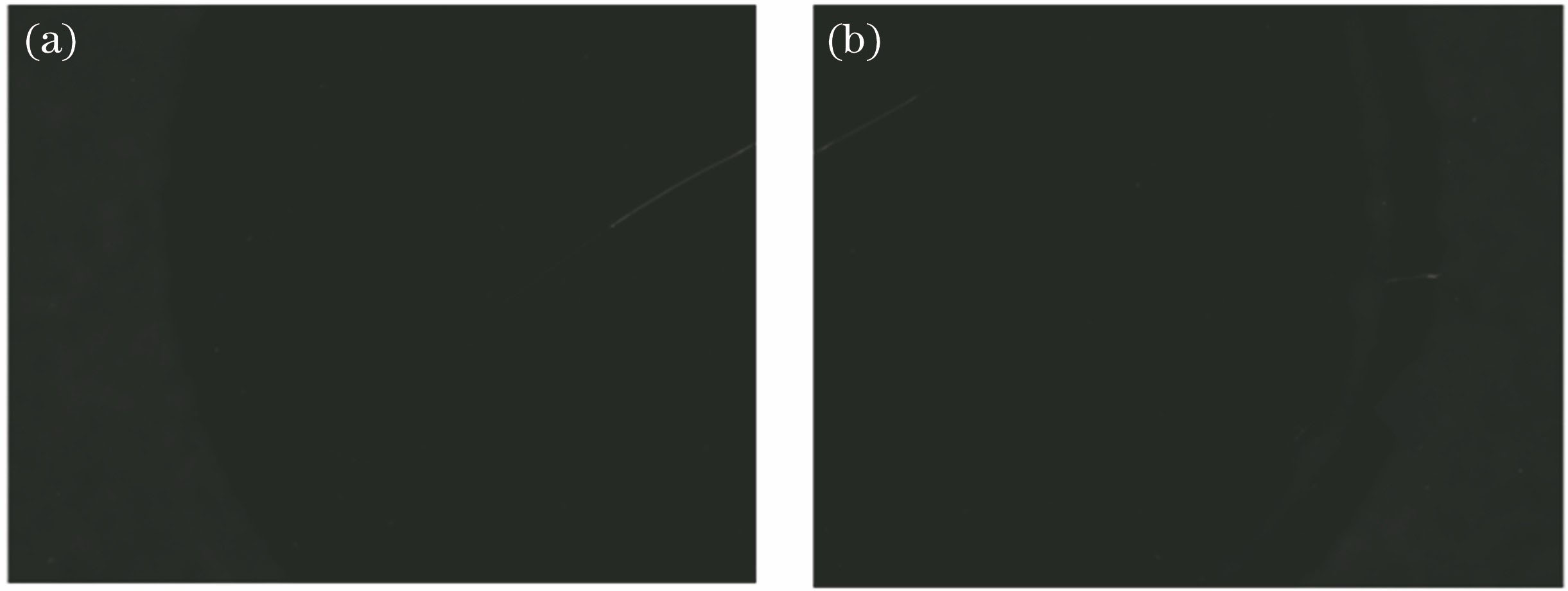
图 10. 光学元件子孔径疵病图像。(a)图像1;(b)图像2
Fig. 10. Sub-aperture defect images of optical element. (a) Image No. 1; (b) image No. 2
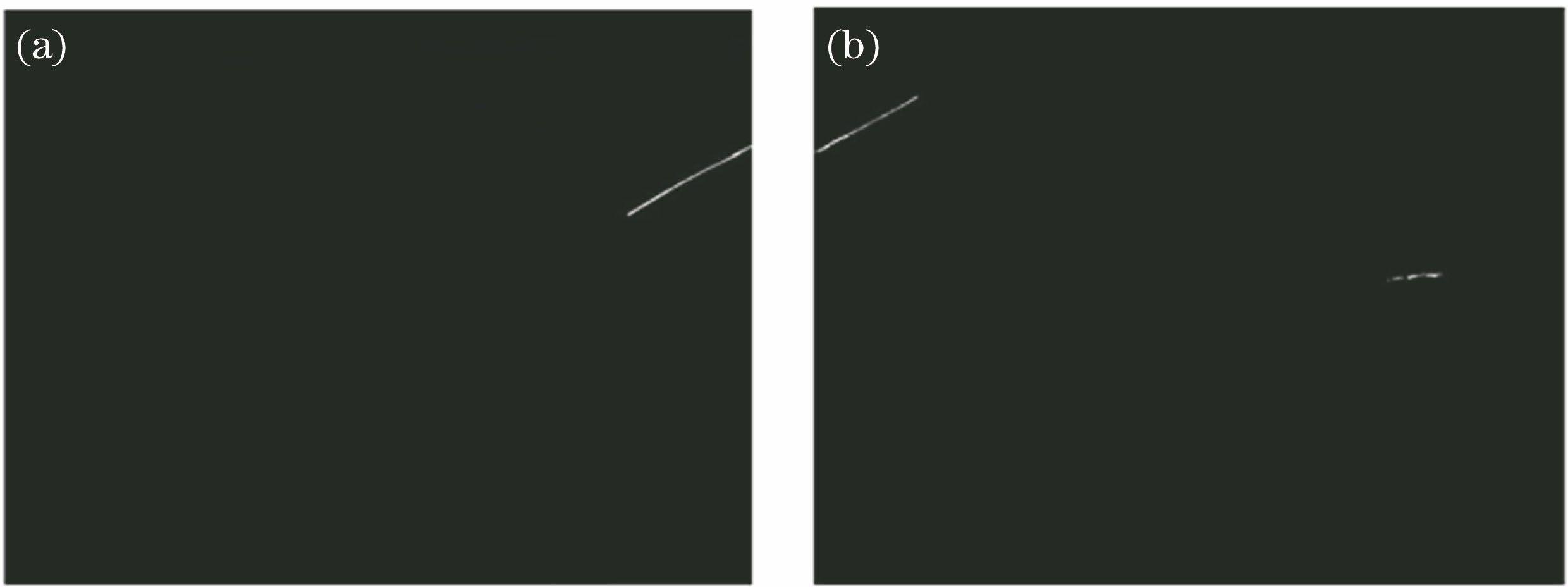
图 11. 处理后的光学元件的子孔径图像。(a)图像1;(b)图像2
Fig. 11. Sub-aperture images of processed optical elements. (a) Image No. 1; (b) image No. 2
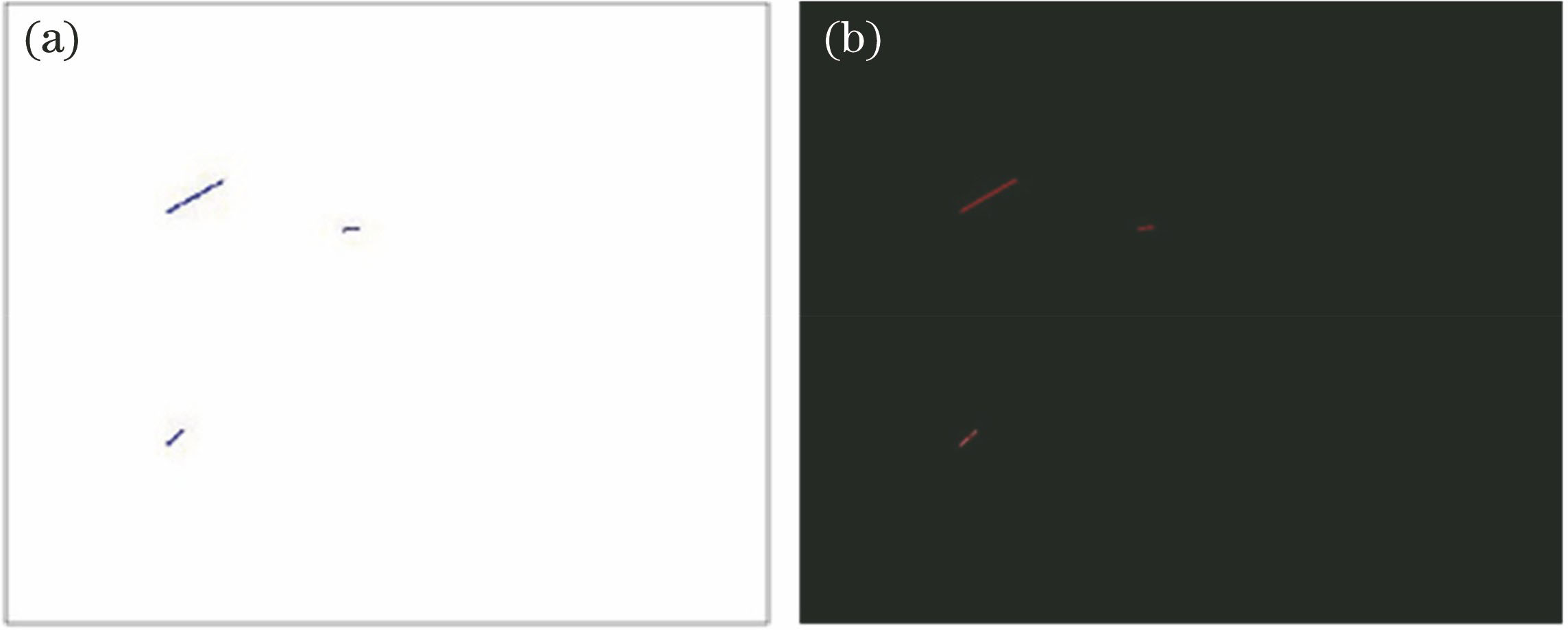
图 12. 拼接图像及疵病识别图像。(a)稀疏矩阵拼接图像;(b)疵病识别图像
Fig. 12. Mosaic image and defect recognition images. (a) Sparse matrix mosaic image; (b) defect recognition image
表 3. 光学元件检测结果统计表
Table 3. Statistical table of test results of optical elements
|
从
5 结论
光学元件因其检测口径大、检测精度高、检测速度要求高等特点,一直是光学元件检测的难点,本文采用了显微散射暗场成像系统,通过高精度、高速度的图像采集得到光学元件子孔径拼接图像;利用稀疏矩阵和图像拼接原理对获得的
[1] 杨星宇. 超光滑表面疵病的显微散射检测方法[D]. 南京: 南京理工大学, 2015.
Yang XY. Microscopic scattering detection method for super smooth surface defects[D]. Nanjing: Nanjing University of Science and Technology, 2015.
[2] 张彬. 散射扫描法光学元件表面疵病检测技术研究[D]. 西安: 西安工业大学, 2014.
ZhangB. Scattering scanning method for surface defect detection of optical components[D]. Xi'an: Xi'an University ofTechnology, 2014.
[3] 张家伟. 光学表面疵病检测系统及图像处理技术研究[D]. 南京: 南京理工大学, 2016.
Zhang JW. Research on optical surface defect detection system and image processing technology[D]. Nanjing: Nanjing University of Technology, 2016.
[4] 向弋川, 林有希, 任志英. 光学元件表面缺陷检测方法研究现状[J]. 光学仪器, 2018, 40(1): 79-87.
[8] 冈萨雷斯, 伍兹. 数字图像处理[M]. 阮秋琦, 译. 北京: 电子工业出版社, 2011.
Gonzalez RC, Woods RE. Digital image processing[M]. Ruan Q Q, Transl. Beijing: Electronic Industry Press, 2011.
[11] 孙丹丹. 精密表面缺陷特性及光学显微散射成像系统的研究[D]. 杭州: 浙江大学, 2006.
Sun DD. Study on the characteristics of precise surface defects and optical microscopic scattering imaging system[D]. Hangzhou: Zhejiang University, 2006.
[12] 杨甬英, 陆春华, 梁蛟, 等. 光学元件表面缺陷的显微散射暗场成像及数字化评价系统[J]. 光学学报, 2007, 27(6): 1031-1038.
[13] 王世通. 精密表面缺陷检测散射成像理论建模及系统分析研究[D]. 杭州: 浙江大学, 2015.
Wang ST. Theoretical modeling and systematic analysis of scattering imaging for precision surface defect detection[D]. Hangzhou: Zhejiang University, 2015.
[14] Zhang ZT, TaoX, XuD, et al. Surface flaws detection algorithms for large aperture optical element[C]∥ International Conference on Advanced Mechatronic Systems (ICAMechS), 2015: 485- 490.
[15] 孙佳明. 激光陀螺反射镜基片表面疵病暗场散射显微检测系统研究[D]. 南京: 南京理工大学, 2016.
Sun JM. Research on the dark field scattering microscopic detection system for surface defects of laser gyro reflector substrate[D]. Nanjing: Nanjing University of Technology, 2016.
[16] 李阳. 超光滑球面光学元件表面缺陷检测及定量化评价研究[D]. 杭州: 浙江大学, 2016.
LiY. Detection and quantitative evaluation of surface defects of super smooth spherical optical elements[D]. Hangzhou: Zhejiang University, 2016.
[17] 罗茂, 步扬, 徐静浩, 等. 基于多光谱技术的光学元件表面疵病检测[J]. 中国激光, 2017, 44(1): 0104001.
[18] 邵珺, 叶景峰, 王晟, 等. 基于燃烧场羟基示踪测速的噪声去除方法[J]. 中国激光, 2019, 46(3): 0309001.
Article Outline
陈晨, 王红军, 王大森, 田爱玲, 刘丙才, 朱学亮, 刘卫国. 基于稀疏矩阵的光学元件表面疵病检测[J]. 中国激光, 2019, 46(4): 0404007. Chen Chen, Hongjun Wang, Dasen Wang, Ailing Tian, Bingcai Liu, Xueliang Zhu, Weiguo Liu. Surface Defect Detection of Optical Components Based on Sparse Matrix[J]. Chinese Journal of Lasers, 2019, 46(4): 0404007.