Challenges for plasma-facing components in nuclear fusion
1 I. INTRODUCTION
The plasma-facing wall of future thermonuclear fusion reactors with magnetic confinement such as ITER or DEMO must withstand harsh loading scenarios.
Today, tungsten is considered to be the most reliable material for high-heat-flux components in future fusion reactors owing to its high melting point (Tmelt = 3422 °C) and a thermal conductivity of approximately 160 W m−1 K−1. For ITER and other large-scale confinement experiments, alternative candidate materials based on beryllium and carbon-fiber composites (CFCs) show promise. A major drawback of the application of beryllium in PFM is its relatively low melting point (Tmelt = 1287 °C).
Beside beryllium, carbon (in particular, fiber-reinforced graphite) is the most frequently used PFM in today’s magnetic confinement experiments. Depending on the selected fiber type and architecture, carbon-fiber reinforced graphite can be manufactured with thermal conductivities equal to or even better than that of copper (up to about 400 W m−1 K−1). However, such an excellent thermal conductivity will degrade rapidly under the influence of energetic neutrons. In D-T-burning fusion reactors with carbon walls, tritium-containing hydrocarbon deposits are formed on all in-vessel components. This will finally result in an inacceptable tritium inventory in the fusion reactor under current licensing laws and limits. For these two reasons, carbon has been discarded as a PFM for ITER.
On the one hand, materials research for plasma-facing components (PFCs) has become of great importance owing to the construction of ITER in Cadarache, France.
2 II. LOADS ON PLASMA-FACING COMPONENTS
Materials research for magnetic confinement experiments has now been ongoing for more than 50 years; it received strong input from a number of medium-sized tokamak devices, which were operated in the 1970s quite successfully and were in urgent need of improvements in wall materials compared with bare stainless steel vessel walls. A further need for suitable materials with well-defined specifications came with the construction of the Joint European Torus (JET, at Culham, UK), which started in 1978.
Today, material specifications and loading scenarios are primarily dictated by ITER,
These extremely harsh loading conditions can only be met with very diligent component design and careful selection of the best suited material and manufacturing techniques. Meticulous risk assessment, nondestructive testing and the application of in situ diagnostics are mandatory, to validate the component lifetime and to avoid any critical deterioration of the PFM or the metallic heat sink, i.e., recrystallization of all materials and any failure of the joints due to material fatigue.
Unmitigated natural ELMs in ITER would result in serious irreversible degradation of the PFCs. Thus, thermal transients such as ELMs must remain below critical limits in terms of power density, pulse duration, and frequency.
Further serious lifetime-limiting PWI processes are caused by material irradiation with hydrogen isotope ions (D+ and T+) and impurities that—depending on their impact energy—will sputter the wall material. The eroded species will be deposited elsewhere, for example, on unshielded parts of the vacuum vessel, on blanket modules, or on less severely exposed divertor targets (outside the separatrix strike zone). Implantation of hydrogen isotopes into the surface of the PFM will result in severe embrittlement of the wall. This also has a strong impact on its cracking resistance, in particular during short transient thermal loads (i.e., ELMs). Helium will also be implanted into the surface of the wall armor or buried in redeposited surface layers. Implanted helium tends to migrate (depending on the prevailing temperature) and to form tiny bubbles that again can interact with implanted hydrogen. In several fusion-relevant PFMs (e.g., tungsten) helium can initiate rather substantial changes in surface morphology, such as the growth of tiny tendrils or “fuzz” on the surface of the PFM.
Finally, irradiation of wall materials by neutrons sourced from the fusion reaction produces collision cascades with high concentrations of interstitials, vacancies, and displacements, and will initiate transmutation processes. Tungsten, for example, the prime candidate for a PFM in ITER and DEMO, will transmute into rhenium (Re), which will transmute again under neutron bombardment into osmium (Os). These processes can amount to several percent of the newly generated elements.
The thermal wall loads that are expected for ITER in the D-T phase are envisaged to be as high as 20 MW m−2 on the separatrix strike point; the typical pulse length of plasma discharges will be 450 s. In addition, powerful ELMs will be triggered during the H-mode plasma operation. The natural, unmitigated ELM energy will be in the range of several tens of gigawatts per square meter, with a duration of 0.5 ms and a frequency of several hertz. These loading conditions—which will be even higher in a DEMO-type fusion reactor—will induce severe surface degradation by cracking and melting (even if tungsten is used as a PFM). Therefore, ELM-mitigation techniques have to be applied to keep the so-called heat flux factor FHF below the damage threshold of about 10 MW m−2 s0.5. The heat flux factor FHF represents the product of power density and the square root of pulse length Δt, which is motivated by the temperature increase of a semi-infinite body under a constant heat load.
The above-mentioned loads are visualized in
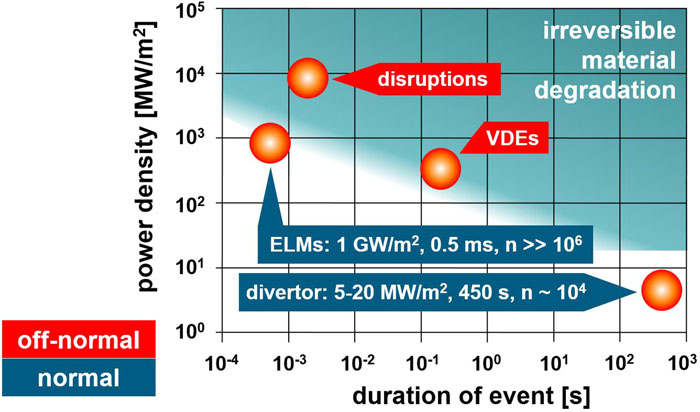
Fig. 2. Thermal loads on the divertor targets of ITER. The turquoise area represents operation conditions with irreversible material degradations during off-normal events. The irreversible damage depends on the number of pulses (for ELMs), and of course there is also degradation due to neutron and H/He loading.
In addition, off-normal plasma operation scenarios cannot be excluded completely, since ITER is an experimental plasma device that needs to explore new plasma regimes. Events such as plasma disruptions—a violent termination of the magnetically confined plasma—or vertical displacement events (VDEs)—an upward or downward motion of hot plasma due to malfunction of the plasma positioning system—may occur. The expected energy densities and pulse durations for these events depend strongly on the size of the tokamak and can be as high as 30 MJ m−2 for 2–5 ms (for disruptions) and up to 60 MJ m−2 and 100–300 ms (for VDEs) in ITER.
To illustrate the interplay between steady-state heat loads and ELMs, these two effects are shown in
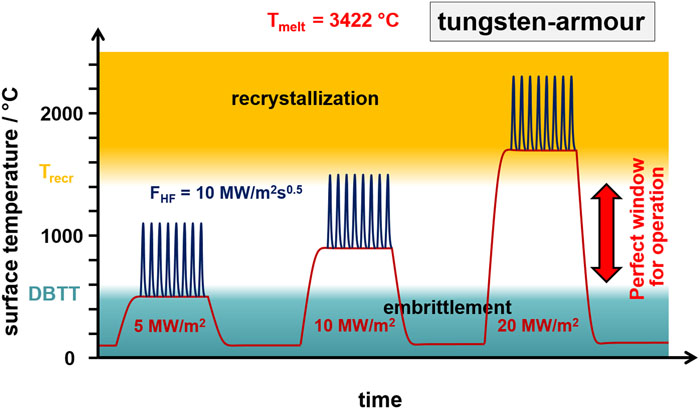
Fig. 3. Schematic presentation of the surface temperature of tungsten-armored divertor targets in ITER at three different power density levels (5, 10, and 20 MW m−2). Thermal spikes caused by mitigated ELMs with an assumed intensity of 10 MW m−2 s0.5 are shown in dark blue.16 Reproduced with permission from Rieth et al. , J. Nucl. Mater. 519 , 334-368 (2019). Copyright 2019 Elsevier.
During a standard discharge in ITER, the maximum target temperature remains far below the Tmelt of tungsten. However, the tungsten or tungsten alloy that has been selected for the manufacturing process will undergo substantial modifications due to recrystallization in all sections of the tungsten armor where the recrystallization temperature Trecr of approximately 1500 °C has been exceeded. It also should be mentioned that tungsten is brittle at temperatures below the so-called ductile–brittle transition temperature (DBTT), which varies in a range from approximately 200 to 600 °C, depending on the selected manufacturing processes, the related material microstructure, and the applied deformation rate.
The damaging effect on actively cooled divertor components for ITER is demonstrated in
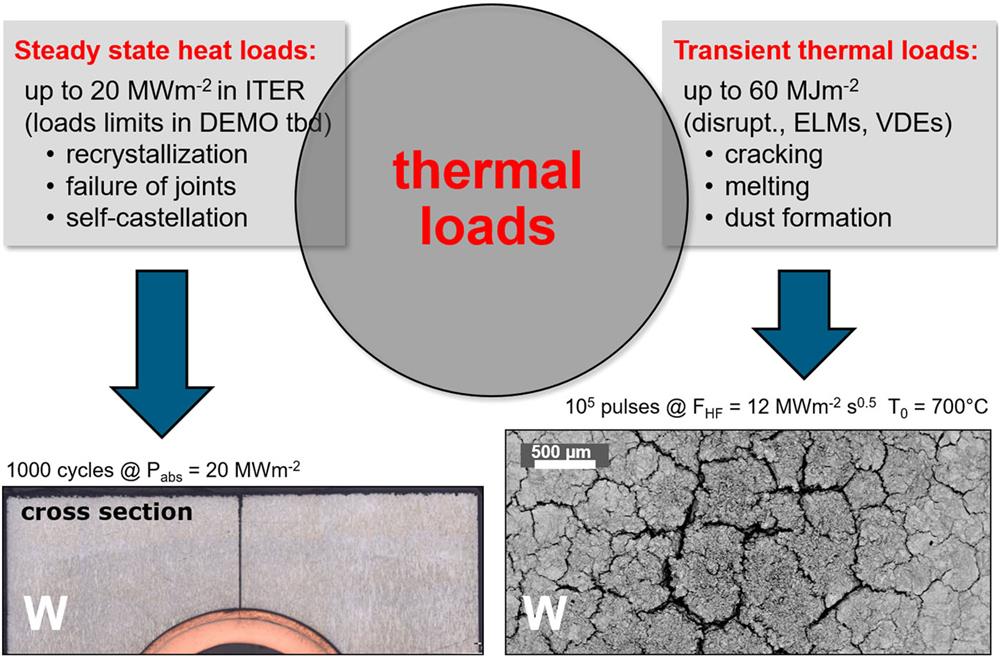
Fig. 4. Major damage to monoblock type PFCs caused by intense cyclic steady-state heat loads of 20 MW m−2 with 1000 pulses (left) and surface damage with intense crack networks induced by intense electron beam pulses simulating 105 ELM-like pulses of F HF = 12 MW m−2 s0.5 (right).17 Reprinted with permission from Pintsuk et al. , Fusion Eng. Des. 88 , 1858–1861 (2013). Copyright 2013 Elsevier.
Serious damage to the plasma-facing armor is also initiated by transient thermal loads with very high numbers of cycles: see the right-hand side of
3 III. PLASMA-FACING MATERIALS AND COMPONENTS
Several different component design options have been developed during the past few decades. The most robust and most efficient are shown schematically in
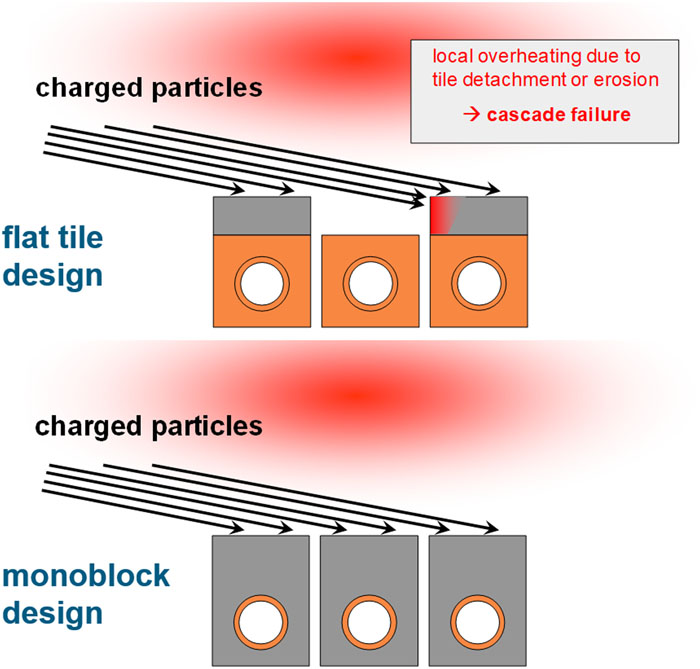
Fig. 5. Different design options for plasma-facing components in ITER. Charged particles that deposit their energy at the surface of the component are guided by the magnetic field lines at shallow angles of approximately 3° to the plasma-facing surface.
A more robust design option is the monoblock divertor. The individual tiles of the PFM are equipped with a cylindrical hole. Rather complex joining methods such as active metal casting (AMC)
The specifications for selection of suitable PFMs are manifold: first of all, the PFM needs good compatibility with the hot fusion plasma, i.e., a low atomic number Z and an excellent sputter resistance. Alternatively, tokamaks with high-Z materials such as tungsten must be operated in such a way as to guarantee that the net impurity influx into the plasma should be so low that the critical impurity concentration is not exceeded. In addition, very high thermal conductivity, high mechanical strength, good matching of the thermal expansion coefficient with the selected heat sink material, and low neutron-induced activation are the most critical material properties.
Early magnetic confinement experiments were performed with glass or steel walls. These material solutions turned out to be inadequate when plasma regimes with higher particle fluxes and thus higher thermal loads were achieved. In this transition phase, steel walls were replaced by carbon walls made from fine-grained graphite or pyrolytic carbon for special application with rather high thermal loads (see
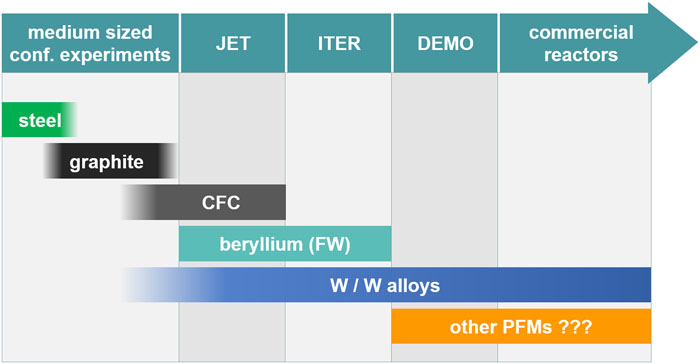
Fig. 6. Schematic summary of the implementation of new PFMs in magnetic confinement experiments. The orange bar indicates that a final decision on the use of PFMs in future fusion reactors is still pending.
As an alternative to carbon-based materials, the high-Z material tungsten and its alloys have been successfully tested in medium-sized tokamak devices (e.g., ASDEX-U
A major drawback of tungsten is the brittleness of this otherwise almost perfect PFM.
Table 1. Different tungsten grades and alloys that have been developed and investigated thoroughly as plasma-facing and structural materials for next-step magnetic confinement experiments.
|
Some of these newly developed materials and manufacturing technologies, such as powder-injection molding (PIM), 3D printing, and coating by physical vapor deposition (PVD), chemical vapor deposition (CVD), or plasma spraying, also offer another attractive feature, namely, the manufacture of net-shaped tungsten parts that can be used without additional cost-intensive and time-consuming manufacturing steps. To avoid hotspots on leading edges on a segmented (or castellated) plasma-facing surface of a divertor module, the application of shaped tiles
4 IV. TESTING OF PLASMA-FACING MATERIALS AND COMPONENTS
The selection of suitable PFMs and, in a second step, the manufacture of PFCs requires a very extensive characterization and testing procedure.
4.2 A. Test facilities
To simulate PWI processes in detail, many sophisticated test devices are being used in numerous laboratories worldwide. Thermal loads are simulated by intense laser or ion beams; depending on beam power and the size of the loaded area, either defocused beams or beam scanning are the most common procedures to expose large surface areas or even full PFCs. In addition, powerful linear plasma devices
Today, there are no adequate test devices available that would enable experiments with in situ neutron wall loads together with other load types (thermal and plasma loads). To mimic these conditions, high-heat-flux experiments using thermal heaters have been performed in situ inside the cores of nuclear fission test reactors (e.g., the HFR reactor in Petten, Netherlands,
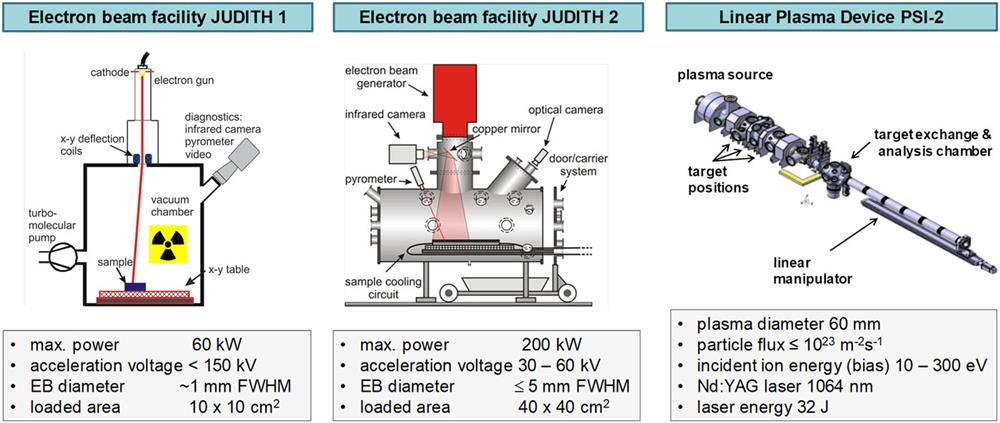
Fig. 7. Selected test facilities and layout parameters for high-heat-flux and plasma exposure of PFMs under fusion-relevant conditions that have been applied for the experiments described in this paper. A rather thin electron beam (EB) favors the simulation of transients with extreme power densities, such as plasma disruptions. Note that approximately 50% of the incident electron energy is reflected on high-Z materials such as tungsten. The electron beam facilities JUDITH 1 and JUDITH 2 are also compatible with operations with toxic materials such as beryllium, and JUDITH 1 can also handle neutron-irradiated test samples.36
4.3 B. Thermal fatigue
A major threat to actively cooled PFCs comes from the high internal stresses that occur due to the thermal gradient in these components: a surface temperature of more than 2000 °C (see
To investigate the heat load limits on different divertor designs and different armor materials, systematic high-heat-flux experiments have been performed with cyclic heat pulses at a predetermined power density level. In JUDITH 1, 1000 thermal pulses have been applied (10 s heating, 10 s cooldown). The critical parameters, namely, the surface temperature of the PFC (two-color pyrometer), the internal temperature close to the interface, and the coolant temperature (both by thermocouples) were monitored continuously to detect sudden temperature variations initiated by internal cracks or other degradation mechanisms in the PFC.
After the successful completion of such a cyclic campaign at a predefined power density level, the heat flux density was increased to the next level (with increment typically 1 MW m−2). This testing procedure was applied continuously until thermal excursions indicate the occurrence of fatigue damage.
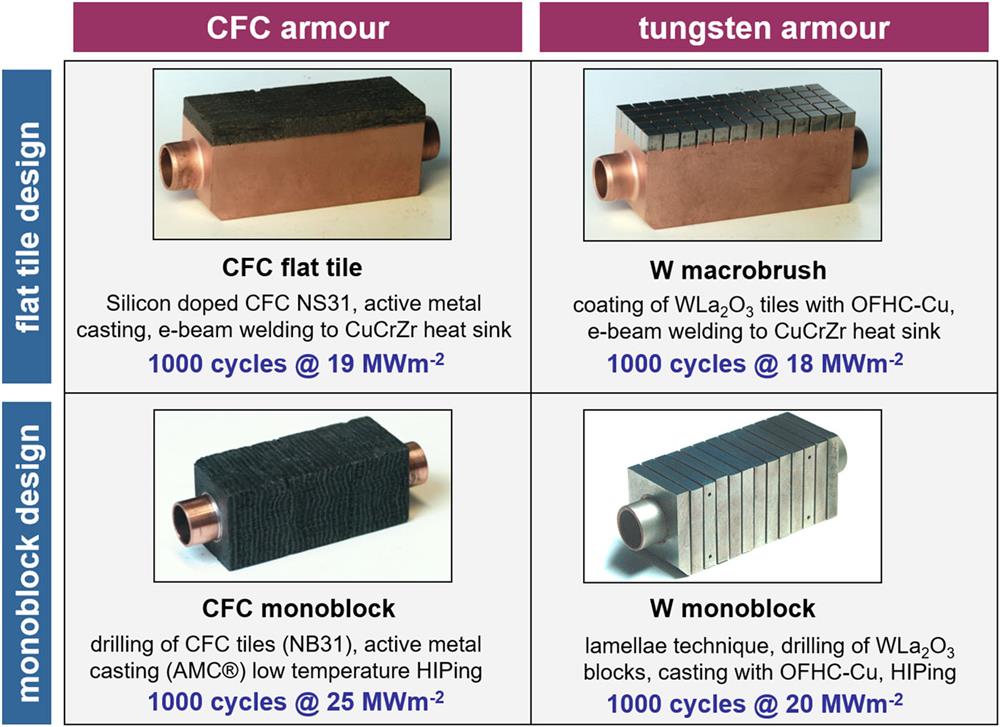
Fig. 8. Thermal fatigue experiments on CFC- and tungsten-armored PFCs with design options (flat tile and monoblock). The load limits are presented in blue.
It is important to note that the loading conditions that have been applied here are pure thermal fatigue conditions and do not consider any synergistic effects such as intense transients by ELM deposition, hydrogen or helium bombardment, or neutron-induced degradations (cf.
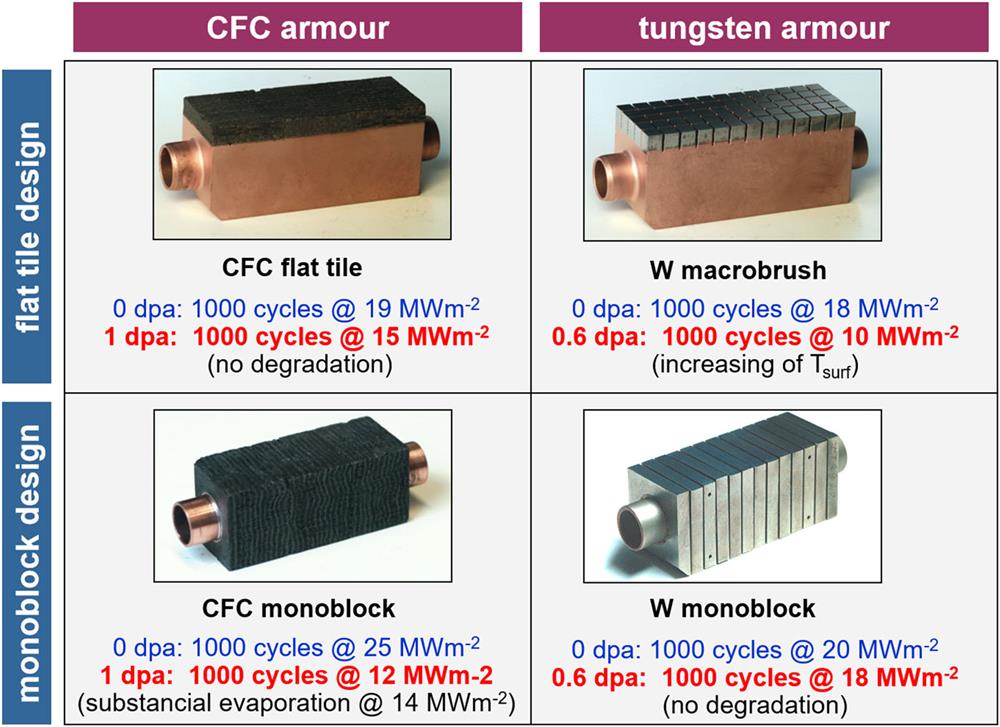
Fig. 9. Thermal fatigue experiments on CFC- and tungsten-armored PFCs with different design options (flat tile and monoblock) after neutron irradiation in the HFR materials test reactor HFR in Petten at 700 °C and neutron fluxes up to 1025n m−2. The load limits for the non-irradiated modules are shown in blue; data obtained after neutron irradiation are shown in red (see also Fig. 8 ).2 Reprinted with permission from Linke et al. , in Proceedings of Forum 2008 of the World Academy of Ceramics, Chianciano Terme, Italy, July 5–8, 2008 (Techna Group Srl, 2009), pp. 307–334. Copyright 2009 Techna Group Srl.
4.4 C. Thermal shocks
During steady-state heat loads with pulse durations of the order of several tens of seconds or longer, the temperature field inside the PFC is characterized by an almost continuous gradient that extends from the surface of the PFC down to the coolant tube. Intense transient thermal loads such as ELMs, disruptions, or VDEs with pulse durations in the millisecond range create very steep thermal gradients with a relatively shallow penetration depth that is proportional to the square root of the thermal diffusivity and the pulse duration. Hence, the damaged area during ELM-like loads will be limited to a few hundred micrometers.
Typical material damages induced by ITER-specific transient events are shown in
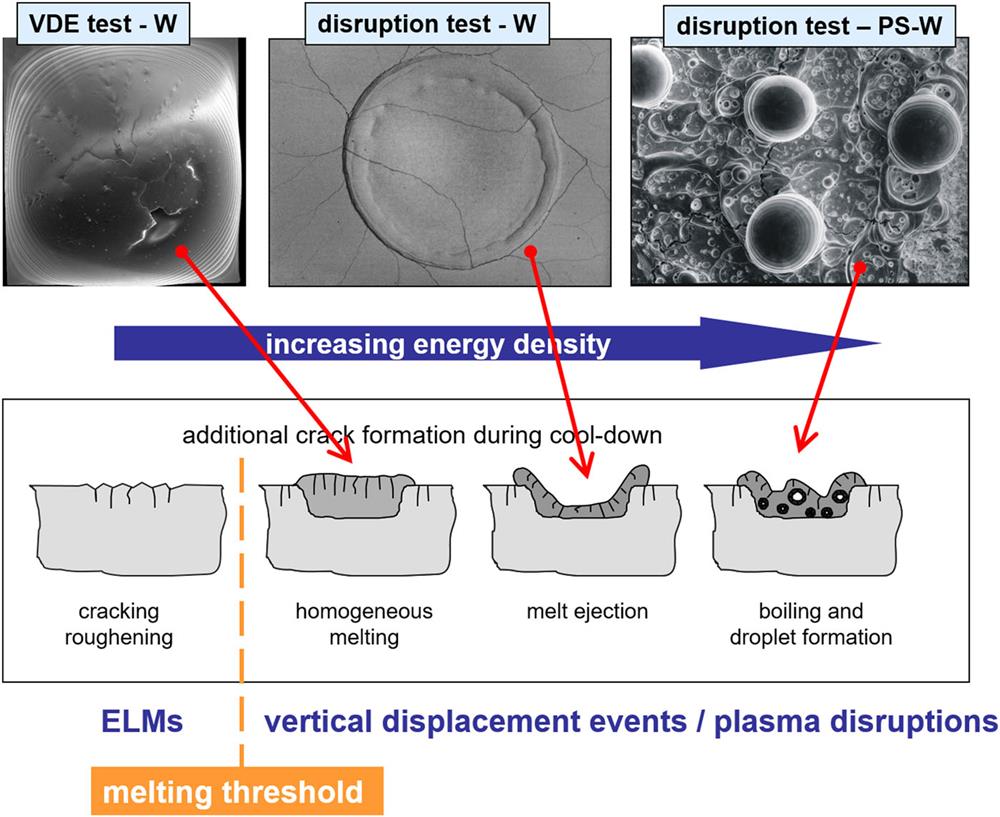
Fig. 10. Schematic presentation of the degradation of tungsten-based armor tiles with increasing transient thermal loads below and above the melting threshold.39 The top row shows photographs from test samples that have been exposed to off-normal events that might occur in ITER if suitable mitigation techniques are not applied.
To evaluate the resistance of different PFMs to ELM-like heat fluxes, systematic thermal load tests were performed in electron beam and laser beam experiments.
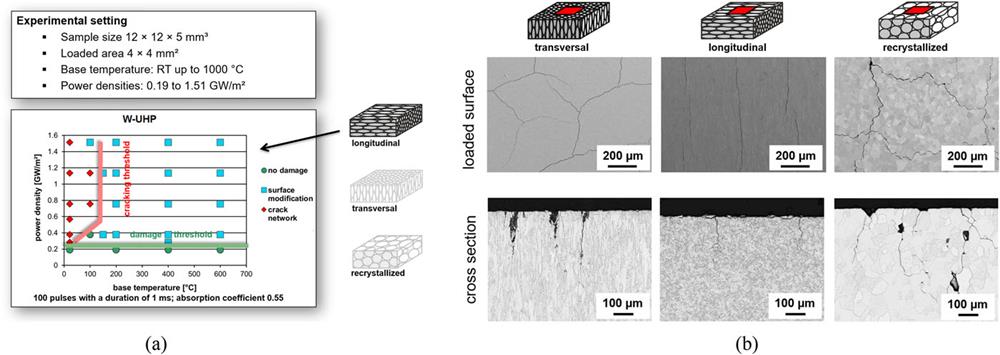
Fig. 11. (a) Generation of a typical damage map for an ultra-high-purity (UHP) tungsten grade with longitudinal grain orientation under intense transient thermal loads applied in the electron beam test facility JUDITH 1. Each data point represents a single test sample that has been exposed to 100 electron beam pulses at different base temperatures and power density levels (green circles, no damage; blue squares, surface modifications; red diamonds, crack network).44 Reprinted with permission from Wirtz et al. , Nucl. Mater. Energy 12 , 148–155 (2017). Copyright 2017 Elsevier. (b) Micrographs taken by scanning electron microscopy (top row) and after metallographic sectioning using optical microscopy (bottom row) on tungsten test samples exposed to one particular load scenario plotted in the damage map in (a). The three different test specimens (transverse, longitudinal, and recrystallized) have been exposed to 100 repeated electron beam pulses under identical conditions: a power density level L abs = 0.38 GW m−2 (F HF = 12 MW m−2 s0.5) and a base temperature T base = room temperature.44
The color coding based on the above-mentioned diagnostics in
The experimental procedure described above has been applied to a large number of metallic PFMs, primarily to tungsten- and beryllium-based materials. In addition, alloys of high-Z metals, materials with modified grain structures, and coatings made from these materials have been tested. With a beam repetition rate of 1 s to allow sample cool-down in between shots and to accommodate the large number of samples required to develop the damage mapping, this procedure turned out to be rather time-consuming in JUDITH 1 for experimental campaigns with more than 1000 pulses (namely, ∼20 min for 1000 pulses, or 280 h for 106 electron beam pulses per data point).
To overcome this problem with the low repetition rate, the more powerful electron beam device JUDITH 2 has been operated with an upgraded digital beam control system which allows the programming of rather complex beam traces on the surface of actively cooled PFCs. Active cooling is mandatory for these tests to avoid excessive heating of the loaded surface and, in addition, to combine the transient thermal loading with steady-state heat loads that provide the base temperature (e.g., 700 °C for an experiment with a steady-state heat flux of 10 MW m−2). These tests [see
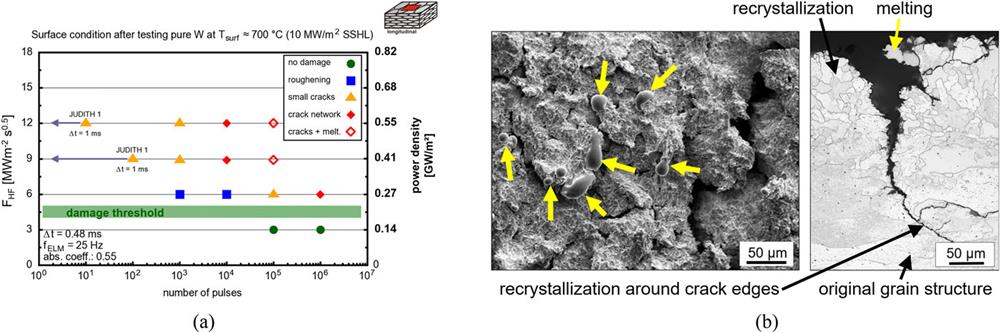
Fig. 12. (a) Damage map for actively cooled tungsten specimens under simultaneous steady-state heat loads (SSHL = 10 MW m−2) and intense transient thermal loads applied in electron beam tests with high repetition rates (25 Hz) and an absorption coefficient on tungsten targets of 0.55. The chart summarizes experimental data that have been taken at different power density levels for the transient events and pulse numbers up to n = 106 and at a constant base temperature T surf = 700 °C.46 Reprinted with permission from Loewenhoff et al. , Phys. Scr. T145 , 014057 (2011). Copyright 2011 IOP Publishing. (b) Results from post-mortem analyses on a tungsten test sample that has been exposed to 105 transient thermal load pulses in the damage map in (a). The tests were performed at a heat flux factor F HF = 9 MW m−2 s0.5 and a base temperature T surf = 700 °C. The surface is covered homogeneously with a high number of re-solidified tungsten droplets that are generated when individual tungsten grains are thermally isolated by thermal shock-induced microcracks.47 Reprinted with permission from Loewenhoff et al. , Fusion Eng. Des. 87 , 1201–1205 (2012). Copyright 2012 Elsevier.
The damage map in
This map demonstrates clearly that experiments conducted at a given heat flux factor (e.g., FHF = 9 MW m−2 s0.5) show growing damage with increasing pulse number. Small cracks (seen after 100 cycles) develop into crack networks and melting effects [visible after 105 pulses; see the micrographs in
As a conclusion for next-step tokamaks including ITER, the heat flux factor should remain below 6 MW m−2 s0.5 to avoid component failure due to high-cycle fatigue induced by frequent ELM events. It is important to note that these results do not yet include any synergistic effects induced by hydrogen, helium, or neutron bombardment.
Thermally induced cracking or opening of grain boundaries in the plasma-facing surface can be a hazard for the safe operation of a confinement device: deep cracks have a strong impact on heat removal through the PFM into the heat sink. In particular, cracks that are oriented perpendicular to the thermal gradient in the armor material show reduced capability for heat removal and end up in isolated hot-spots that even reach temperatures above the melting point of tungsten. An example of this effect is shown in
From this point of view, carbon is a much more “forgiving” material than tungsten or other metals. The absence of any liquid phase on carbon-armored PFCs and the very low atomic number of carbon eliminate the risk of large melt accidents during off-normal events such as VDEs or major plasma disruptions. Therefore, in earlier stages of the ITER design phase, CFCs were proposed as armor for the very high-heat-flux regions of the divertor, i.e., for the separatrix strike zone and adjacent targets. The very high thermal conductivity of CFCs with pitch fiber reinforcement led to excellent thermal shock resistance with almost twice the values that could be realized in high-dense tungsten grades.
Carbon-based materials are no longer PFM candidates in ITER, because of their high tritium retention. However, they excel in heat load tests and are therefore discussed in what follows. Transient heat load tests on CFCs confirmed their high resistance against erosion of the pitch fibers to intense ELM-like loads with energy densities of up to 1.0 MJ m−2 at pulse durations of 0.5 ms (FHF = 44.7 MW m−2 s0.5). However, the polyacrylonitrile (PAN) fibers and needled PAN fibers that are responsible for the mechanical properties of these three-directional composites are heavily eroded under intense heat fluxes.
A further drawback of CFC material under extreme thermal shocks is that thermally induced stresses during these thermal spikes can even destroy the fiber integrity. After 100 pulses with a heat flux factor of 31.3 MW m−2 s0.5, some of the pitch fiber bundles are completely broken; the cracks extend to a depth of 100 μm as shown in
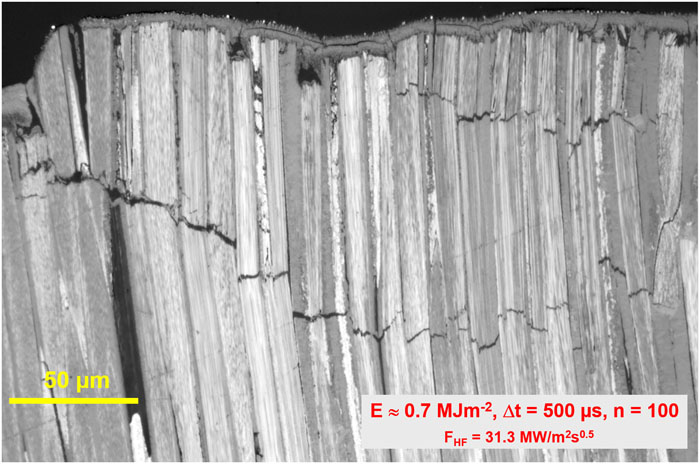
Fig. 13. Ceramographic section from a CFC sample exposed to 100 transient heat pulses with an energy density of 0.7 MJ m−2, Δt = 500 µ s show deep cracks that intersect the pitch fiber bundles owing to thermal stresses.48
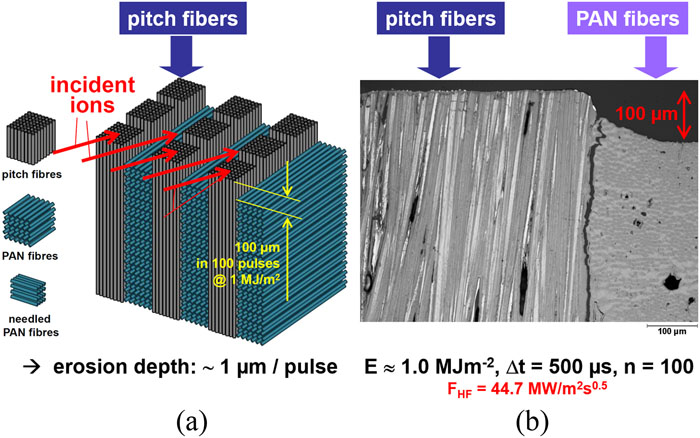
Fig. 14. View of thermal shock experiments simulating unmitigated ELMs deposited on a CFC surface: (a) schematic; (b) ceramographic section from a loaded test sample. The pitch fibers of this composite with a high thermal conductivity along the fiber axis do not show any severe thermal erosion, while the PAN fibers with an orientation parallel to the surface are strongly affected and show a total erosion of approximately 100 μ m.
Like tungsten, carbon-based materials such as isotropic fine grain graphite also show a strong increase in damage above a certain damage threshold. Test samples were subjected to disruption-like heat pulses of 2 ms duration with stepwise increasing power densities from 3.1 to 3.3 and 4.3 GW m−2 (see
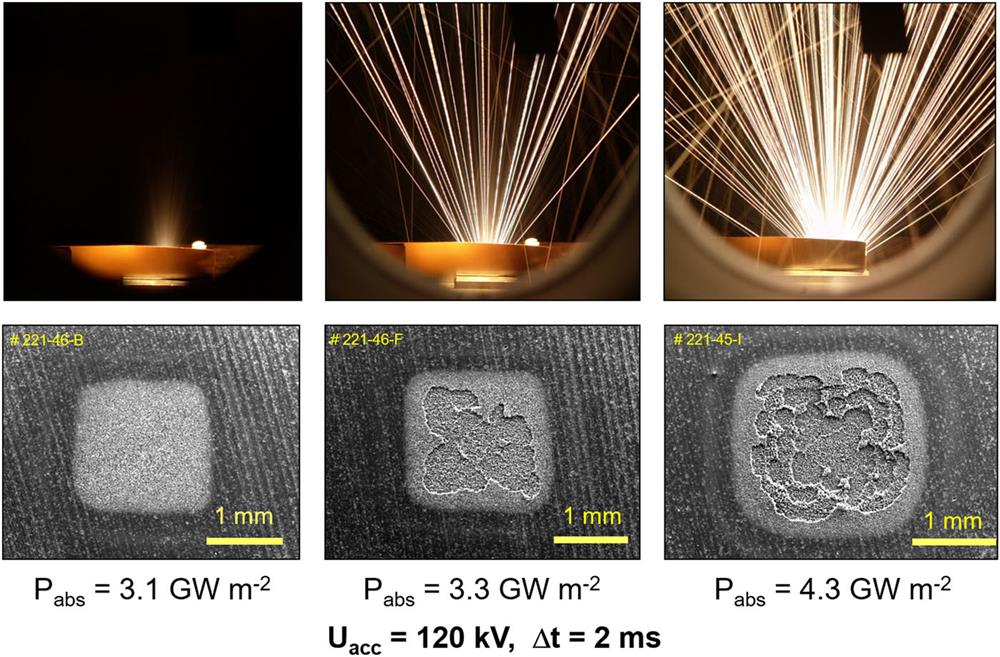
Fig. 15. Disruption simulation experiments on isotropic fine-grained graphite in the electron beam test facility JUDITH 1 with increasing power density level.50 The top row shows long-exposure photographs taken during the 2 ms beam exposure; i.e., emitted hot particles are identified from their straight trajectories. The bottom row are SEM images from the exposed surfaces. Up to a threshold value of 3.1 GW m−2, thermally induced material erosion remains marginal; above this threshold, intense emission of grains or grain clusters and intense surface erosion has been identified.51 Reprinted with permission from Linke, Trans. Fusion Sci. Technol. 53 , 278–287 (2008). Copyright 2008 Taylor and Francis.
In addition to the divertor, other components will be subject to the heat load originating from the plasma. The armor of the blanket, i.e., the first wall that protects the breeding blanket in future tritium-burning confinement experiments, must withstand less severe thermal loads compared with the divertor target. To avoid excessive neutron absorption and thus allow for a sufficiently high tritium breeding ratio in the breeding blanket, the thickness of the high-Z armor layer must be limited to a few (2–3) millimeters only, and the structural material, including the coolant tubes, must be manufactured from a less dense material (compared with tungsten) with adequate thermal conductivity and neutron resistance, for example, steel. In addition, this component requires very sophisticated engineering to guarantee a long lifetime of the blanket modules and to avoid any contaminations of the fusion plasma from wall material that might enter the core plasma owing to delamination or evaporation processes. Tungsten, with its extremely high melting point, might also be a very suitable material for the plasma-facing wall (e.g., as a plasma-sprayed coating or a plated layer).
For ITER, the tritium-breeding blanket first wall will be made from a low-oxygen vacuum hot-pressed beryllium grade that is attached to a CuCrZr heat sink. This material selection has been motivated by the relatively high thermal conductivity of beryllium and its low atomic number, which make plasma contamination by wall material (e.g., as a result of sputtering processes) less harmful. In addition, beryllium is an excellent getter for oxygen, which enables plasma discharges with low impurity levels (i.e., so-called low-Z effective discharges). However, the toxicity of beryllium and its relatively low melting point Tmelt = 1278 °C are less favorable properties that hamper the use of this rather interesting material for applications in future fusion reactors beyond ITER.
The performance of beryllium under extreme transient thermal loads has been investigated thoroughly in experiments analogous to those on tungsten described above.
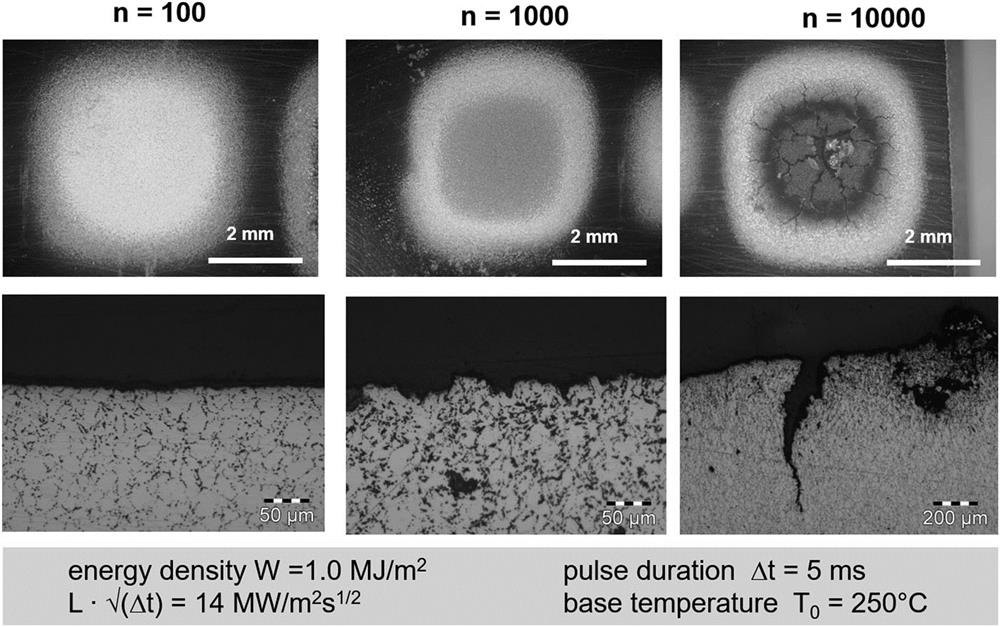
Fig. 16. Repeated disruption-like electron beam loads (Δt = 5 ms) on polished beryllium test specimens preheated to 250 °C. Up to 100 pulses, the surface (top row, SEM images; bottom row, metallographic sections) does not exhibit any erosion; intense surface roughening is evident after 1000 pulses; intense cracks with a depth of 500 μ m are detected after 10 000 pulses.52
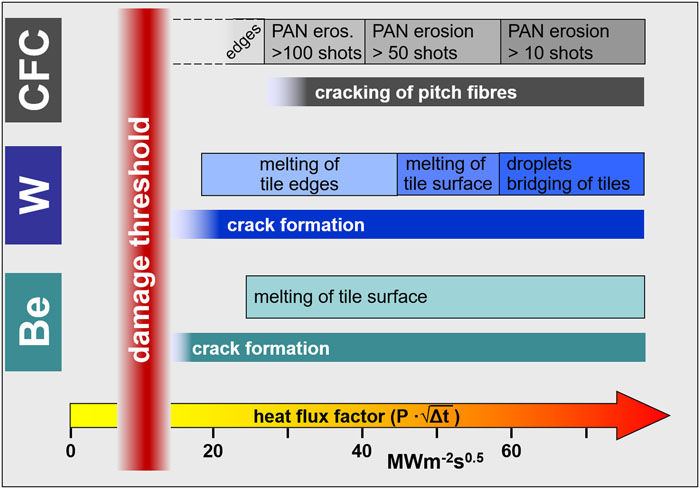
Fig. 17. Comparison of the resulting material degradation on different PFMs under repeated transient thermal loads (n ≤ 100). Tungsten and CFC data were obtained on a quasistationary plasma accelerator (QSPA), with 0.5 ms pulse duration and T 0 = 500 °C; beryllium data were from electron beam experiments on JUDITH 1, with T 0 = 300 °C. The damage threshold values for all three materials are at a level of approximately 10 MW m−2 s0.5.2,40,48,54
In addition to comprehensive and costly experimental campaigns that cover individual or synergistic effects, numerical methods are important tools to aid the synthesis of new materials with improved properties, to predict the performance of complex components, to benchmark experimental findings, and to predict material performance in very complex and harsh conditions.
5 V. IRRADIATION EFFECTS
As well as extreme thermal loads, particle bombardment from the hot fusion plasma is another serious issue for wall materials in future fusion reactors. Since charged particles such as deuterium and tritium, which are guided by the magnetic field lines, have only a very shallow penetration depth, they will primarily affect the near-surface region of the PFM. However, owing to diffusion processes on hot walls, hydrogen ions in particular can also penetrate into deeper layers. Neutrons of energy 14 MeV have a penetration depth of up to several tens of centimeters, depending on the selected materials and the coolant. This means that neutron-induced degradation must be taken into account for the plasma-facing component as well as for structural materials.
5.2 A. Hydrogen and helium effects
Extensive studies of hydrogen and helium bombardment have been performed in laboratories worldwide to investigate and quantify sputtering effects and microstructural changes of the bombarded surface layer, including recombination effects and migration of defects and defect clusters. As well as these single-load effects, combined events such as simultaneous bombardment with helium and hydrogen ions
To highlight the importance of such synergies, material degradation under simultaneous helium irradiation and intense transient thermal loading using a focused laser beam is illustrated in
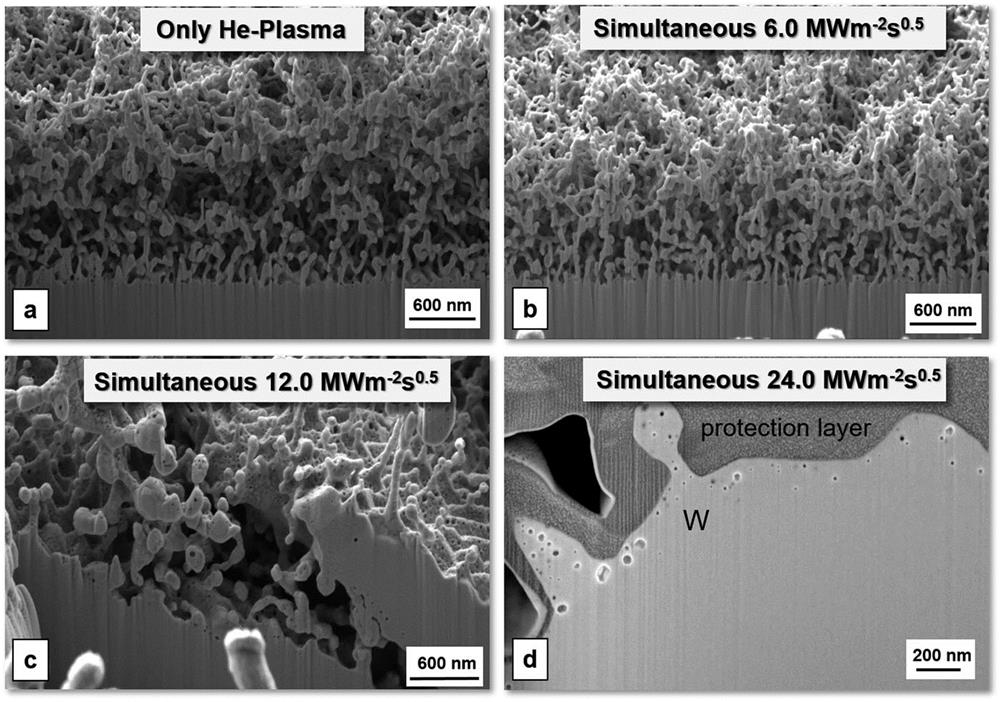
Fig. 18. Synergistic experiments with simultaneous exposure of polished tungsten specimens under helium bombardment and laser beam transient thermal loads in the PSI-2 linear plasma device.65 Helium implantation at high temperatures initiated the growth of tiny tungsten tendrils (tungsten fuzz). SEM images were taken on sections cut with focused ion beams using Ga ions.66 Reprinted with permission from Wirtz et al. , Nucl. Mater. Energy 9 , 177–180 (2016). Copyright 2016 Elsevier.
5.3 B. Material degradation by energetic neutrons
To study neutron-induced material degradation, PFMs, structural materials, and miniaturized components have been irradiated by a number of different neutron sources such as fission-type material test reactors or spallation neutron sources. Unfortunately, the neutron spectra in these devices do not fully coincide with the fusion neutrons generated in D-T fusion reactions. The International Fusion Materials Irradiation Facility (IFMIF), with an almost perfect energy spectrum, is still in an early design stage and will not be available before 2030 (IMIF-DONES).
Post-irradiation testing (PIE) following well-instrumented irradiation experiments in material test reactors has been performed on all fusion-relevant PFMs with ITER-relevant fluences up to 1.0 dpa in carbon (approximately 1025n m−2). These irradiation tests require a very diligent design and construction of the irradiation capsule, with heaters or coolant channels to guarantee the predetermined irradiation temperature.
Heat removal from plasma-facing components from the heat-affected surface to the coolant is strongly determined by the thermal conductivity λ of the PFM and the heat sink. During neutron irradiation, energetic neutrons with energies of up to 14.7 MeV generate collision cascades. During their decay process, a large fraction of point defects and interstitials are generated, which have strong impact on the thermal conductivity. The neutron-induced decrease in λ of the full PFC is a serious concern for the safe operation of a reactor, since increasing surface temperatures of the PFC surfaces will in turn affect the recrystallization of the PFM.
Cylindrical test specimens, manufactured from different grades of PFM and with different surface orientations were irradiated in material test reactors at different temperatures (200–700 °C) up to neutron damage rates of 1.0 dpa. A thermal flash apparatus installed inside a hot cell was utilized to measure the thermal diffusivity and thus (after multiplication by temperature-dependent data for density and specific heat) the thermal conductivity.
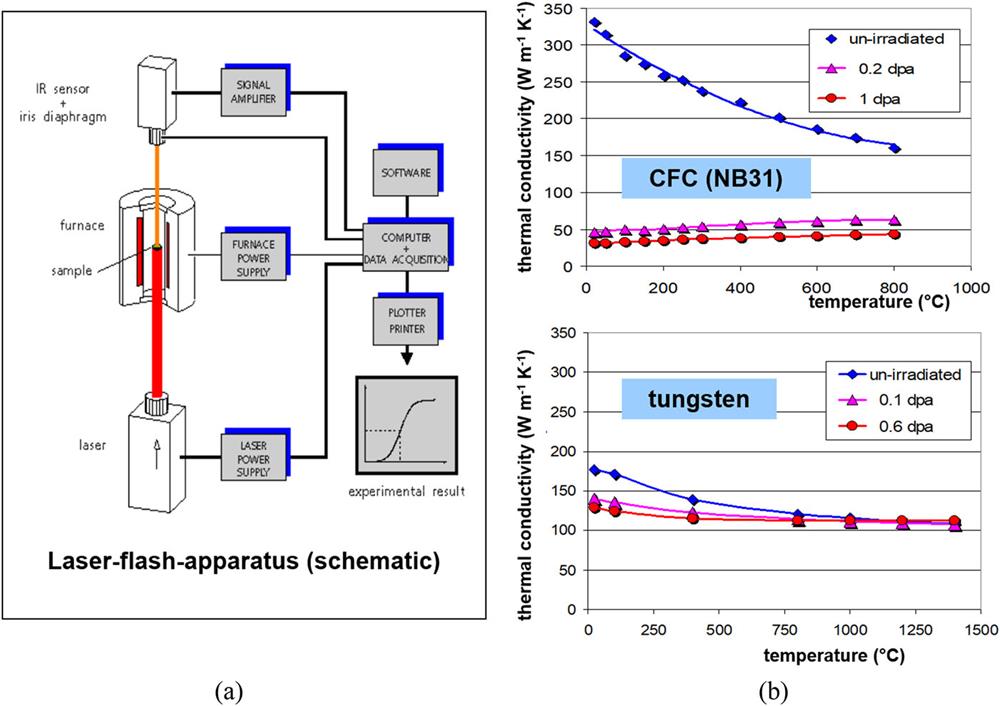
Fig. 19. (a) Schematic presentation of the laser-flash apparatus used to determine the thermal diffusivity. (b) Thermal conductivity data measured on a CFC (NB31) and a tungsten specimen without and after neutron irradiation at neutron damage rates up to 1.0 dpa for carbon and 0.6 dpa for tungsten.71 Reprinted with permission from Linke et al. , Fusion Sci. Technol. 47 (3), 678 (2005). Copyright 2005 Taylor and Francis.
CFCs show excellent thermal conductivities, one reason why they have been considered as excellent PFMs for the separatrix strike zone of next-step fusion devices with moderate neutron fluences. Nevertheless, the values of the thermal conductivity λ determined after 0.1 dpa already show a very drastic decrease, especially at low temperatures. For neutron fluences expected at the end of life of ITER (approximately 1 dpa) the effect is even stronger, and the room-temperature thermal conductivity is decreased by almost one order of magnitude.
For tungsten, the degradation of the thermal conductivity is less severe; here the neutron-induced decrease in λ is limited to about 25%–30% at low temperatures and diminishes at elevated temperatures above 1000 °C. This is a strong argument for the selection of tungsten as a PFM for ITER and especially for future fusion reactors with very high neutron fluences. However, it must be noted that reliable irradiation data for relevant neutron damages of up to 8 dpa for DEMO are not yet available.
Experiments exploring the performance of neutron-irradiated PFMs can only be done in a hot cell to protect the operators from high radioactivity of the neutron-irradiated specimens or actively cooled components.
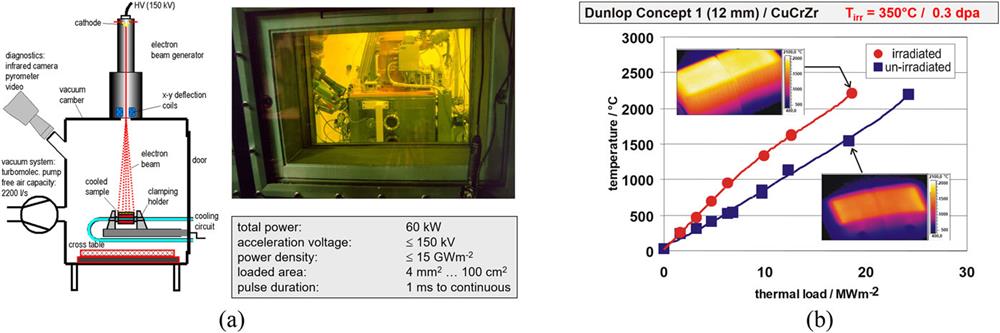
Fig. 20. (a). Schematic diagram from the electron beam test facility JUDITH 1 (left) and photograph from the test device inside the hot cell (right).36 (b) High-heat-flux screening test up to absorbed power densities of 25 MW m−2 in JUDITH 1 on an actively cooled monoblock target with CFC armor made from Dunlop Concept 1 and a CuCrZr coolant tube. The module has been tested before (blue curve) and after (red curve) neutron irradiation. The inserts are infrared images taken at the end of the 18 MW m−2 heat pulses.72 Reprinted with permission from Linke et al. , Fusion Sci. Technol. 46 (1), 142–151 (2004). Copyright 2004 Taylor and Francis.
Owing to the hexagonal lattice structure of graphite, neutron-induced defects are produced in a basal plane and/or in-between the basal planes.
The unirradiated component has been tested up to stationary heat loads of 25 MW m−2; the surface temperature increases almost linearly with increasing electron beam load with a slope of approximately 80 K per MW m−2. After neutron irradiation, this slope almost doubles, at least in the temperature range below 1000 °C, i.e., in a regime where recovery effects are less relevant. For higher heat loads (6 MW m−2 and above), some of the neutron-induced defects can be recovered, and the slope of the curve decreases considerably. Since the evaporation of carbon atoms from the heated surface increases dramatically above 2000 °C, the experiment had to be stopped at a heat load of 18 MW m−2 to avoid thermal erosion of the component and undesired contamination of the vacuum chamber and the diagnostic windows.
The thermal fatigue tests described in
The CFC monoblock component could not be tested above 12 MW m−2 without any degradation of the module. This is due to the relatively low bulk temperature of the carbon material close to the coolant tube, which prevents recovery of irradiation-induced defects. For the flat tile design, this limit was somewhat higher (15 MW m−2).
The tungsten monoblock module has demonstrated the best irradiation performance; here, the neutron-exposed PFC could tolerate ITER-like fluences of 1025n m−2 without fatigue failure up to heat flux densities of 18 MW m−2. These very promising results indicate that tungsten monoblock targets might also be a good choice for future fusion experiments with even higher neutron damage rates.
6 VI. SUMMARY AND CONCLUSIONS
The extremely harsh environment in future fusion reactors—high stationary and transient thermal loads, hydrogen and helium bombardment, 14 MeV neutrons—puts strong demands on the selection of PFMs and the manufacture of actively cooled components with a long expected lifetime. Up to now, materials research in the field of thermonuclear fusion has been done primarily in laboratories and in test facilities that have focused primarily on individual effects only, such as thermal fatigue, thermal shocks during transient events, plasma exposure, and neutron irradiation tests. Today, emphasis is also laid on synergistic effects such as high thermal loads under plasma exposure or simultaneous thermal and neutron wall loads (see
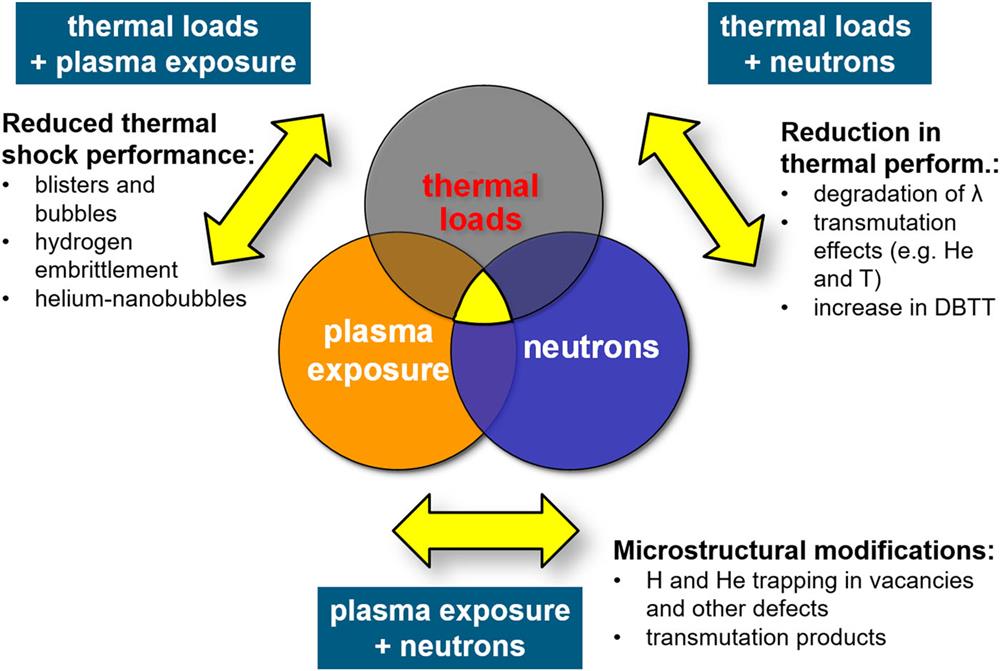
Fig. 21. Synergistic loading scenarios and important parameters with a strong impact on performance and lifetime of PFCs in future fusion reactors.
Synergies between thermal loads plus plasma exposure: Here, plasma-induced processes such as blister or bubble formation, hydrogen embrittlement, or the growth of He nanobubble layers or of fuzz on the plasma-exposed surface have a negative impact on resistance to intense thermal loads.
Synergies between thermal loads plus neutrons: Neutron-induced material degradation such as reduced thermal conductivity, transmutation effects, embrittlement, and increased ductile–brittle transition temperature have a strong impact on the high-heat-flux performance of wall components, both under steady-state conditions and under intense transients.
Synergies between plasma exposure plus neutrons: Research on this third synergism, namely, the interaction of plasma exposure with neutron-induced effects, has not been discussed here. In this area, future research should be directed toward the trapping of H and He in neutron-induced defects, the formation and influence of transmutation products, etc.
The results described in this paper indicate that material degradation is accelerated when synergistic effects are taken into consideration. Therefore, future experiments should also focus more strongly on these effects. New multipurpose test devices that enable simultaneous exposure with fusion-relevant ion fluxes and in situ thermal loading and that are well diagnosed are now available. The integration of these high-heat-flux and plasma devices into a powerful neutron source with a fusion-relevant energy spectrum would clearly go beyond current technical and financial limits. Alternatively, test specimens (including miniaturized PFCs) must be irradiated in qualified neutron sources (material test reactors, spallation neutron sources, or later in IFMIF) to allow investigation by the above-mentioned multipurpose test devices.
The ideal, comprehensive testbed that enables simultaneous thermal loads, plasma exposure, and neutron irradiation (the yellow triangle in
[10] T. E. Evans. ELM mitigation techniques. J. Nucl. Mater., 2013, 438: S11-S18.
[18]
[26]
[36]
[37]
[38]
[39] G. Pintsuk. Tungsten as a plasma-facing material. Compr. Nucl. Mater., 2012, 4: 551-581.
[46]
[47]
[52]
[54]
Article Outline
Jochen Linke, Juan Du, Thorsten Loewenhoff, Gerald Pintsuk, Benjamin Spilker, Isabel Steudel, Marius Wirtz. Challenges for plasma-facing components in nuclear fusion[J]. Matter and Radiation at Extremes, 2019, 4(5): 056201.