超高速激光熔覆与常规激光熔覆431不锈钢涂层微观组织和耐蚀性的对比
下载: 1722次
1 引言
煤机的液压支架、海洋平台立柱等轴类构件长期服役于恶劣的工况环境,表面会受到环境的腐蚀破坏,导致整个轴类构件报废失效,极大地浪费了材料,使生产成本增加。为了降低生产成本,工业中常在零件表面制备耐蚀涂层,以提高零件的耐蚀性。目前耐蚀涂层的制备工艺多以电镀和激光熔覆为主,电镀工艺虽然成本低廉,涂层的耐蚀性强,但对环境的污染非常严重,并且涂层与基体的结合强度低,涂层容易剥落。而采用激光熔覆技术制备的耐蚀涂层与基体为冶金结合,既能保证结合强度,又能达到耐蚀性能要求,因而近年来,激光熔覆技术在耐蚀涂层的制备中受到了很多关注:瑞士洛桑联邦理工学院的Fouquet等[1]以0.7 m/min的扫描速度,在低碳钢基体上制备了单层厚度约为600 μm的304不锈钢涂层,其中元素过渡区宽度约为30 μm,该涂层的腐蚀电位较低碳钢基体高0.6 V,耐蚀性能得以提高;葡萄牙里斯本大学化学工程系的Li等[2]以0.3 m/min的扫描速度制备了厚度为1300 μm的S31254奥氏体不锈钢涂层,元素过渡区的宽度达到100 μm,通过FeCl3腐蚀浸泡试验发现该涂层中的点蚀孔尺寸明显小于商用S31254不锈钢;上海交通大学的任超等[3]对激光熔覆Stellite6涂层的性能进行研究后发现,涂层的耐蚀性能得到了提高,但搭接区存在软化现象;朱红梅等[4]对马氏体/铁素体双相不锈钢涂层的性能进行研究后发现,涂层的硬度和耐蚀性能都显著提高;湖北汽车工业学院的叶四友等[5]以1.35 m/min的扫描速度制备厚度为700 μm的单层316L不锈钢涂层,其稀释率达到了25%,该涂层的耐蚀性能较45钢基体明显提高;中国北方大学的张美美等[6]制备了厚度约为220 μm的316L不锈钢涂层,其稀释率达到了20%,该涂层的耐蚀性能较基体20钢显著提高。
如上所述,通过常规激光熔覆技术得到的涂层,稀释率均在10%以上,元素过渡区较宽(30~100 μm),涂层需要达到一定的厚度才能有效提高基体的耐蚀性。由于常规激光熔覆涂层的表面粗糙度较大,需进行车削和磨削加工处理后才可以投入使用,既增加工时又浪费材料。此外,由于常规激光熔覆过程中的激光能量主要作用于工件表面,存在较大的热输入,可能会使涂层因存在过大的残余应力而产生裂纹,甚至剥落,在进行大面积激光熔覆以及对薄壁或小尺寸零件进行熔覆时易使工件发生变形[7]。
近年来,德国弗朗恩霍夫激光技术研究所发明了一种超高速激光熔覆技术[8-9],其熔覆速度可达25~200 m/min,加工过程中激光聚焦于工件上方,使能量大部分作用于工件上方的粉末上。采用这种技术进行熔覆时,基体的热输入虽然极小,但却能保证粉末与基体发生充分的冶金结合,涂层的稀释率一般仅为2%~4%。因此,采用该技术可以制备超薄且质量很高的涂层。根据熔覆速度的不同,涂层厚度基本在25~400 μm范围内,且涂层的表面粗糙度较好,进行简单的磨削与抛光后即可投入使用,被誉为替代传统电镀工艺的先进绿色制造技术,具有广阔的应用前景。弗朗恩霍夫激光技术研究所的Schopphoven等[9]系统研究了工艺参数对涂层厚度的影响规律,发现在扫描速度为250 m/min时可以获得25 μm厚的超薄涂层;随扫描速度降低到25 m/min,涂层厚度的最大值约为300 μm;送粉量、保护气流量都会对涂层厚度有影响。
因工作原理、传热模式与常规激光熔覆技术有较大差异,超高速激光熔覆技术制备的涂层的宏观特征、微观组织结构及耐蚀性能都表现出其独特性。本文以煤机行业液压支架常用的27SiMn钢管为基体材料,采用超高速激光熔覆技术在其表面制备了431不锈钢耐蚀涂层,先对涂层的组织进行了系统分析,然后通过电化学腐蚀试验对涂层的耐腐蚀性能进行了测试与评估,并深入探讨了超高速激光熔覆涂层宏观、微观结构与耐蚀性能的相关性。为了充分说明超高速激光熔覆涂层的组织和性能,将其与常规激光熔覆涂层进行了对比分析。
2 试验方法
试验系统包括IPG公司的YLS-10000型10 kW光纤激光器、GTV双筒送粉器、同轴环形送粉喷嘴及管件高速旋转变位机。基体材料为经调质处理的27SiMn管材,其外径为102 mm,壁厚为15 mm,长度为1000 mm。
试验前,对钢管表面进行机械打磨至消除表面的车削条纹,然后用酒精擦拭除去油污;431不锈钢熔覆粉末置于干燥箱中进行干燥处理(保温温度为100 ℃,保温时间为2 h),以除去其中的水分。熔覆用431不锈钢粉末是利用等离子旋转电极法在真空环境下制备的,粉末颗粒度为25~105 μm,粉末的化学成分如
表 1. 27SiMn钢和431不锈钢粉末的化学成分(原子数分数,%)
Table 1. Chemical composition of 27SiMn steel and 431 stainless steel powder (atomic number fraction, %)
|
超高速激光熔覆(EHLA)的工作原理图与实际加工过程如
常规激光熔覆(CLA)一般采用的线速度为0.3~1.8 m/min,本文中常规激光熔覆选用1.5 m/min的线速度,激光功率为1 kW。常规熔覆过程示意图如
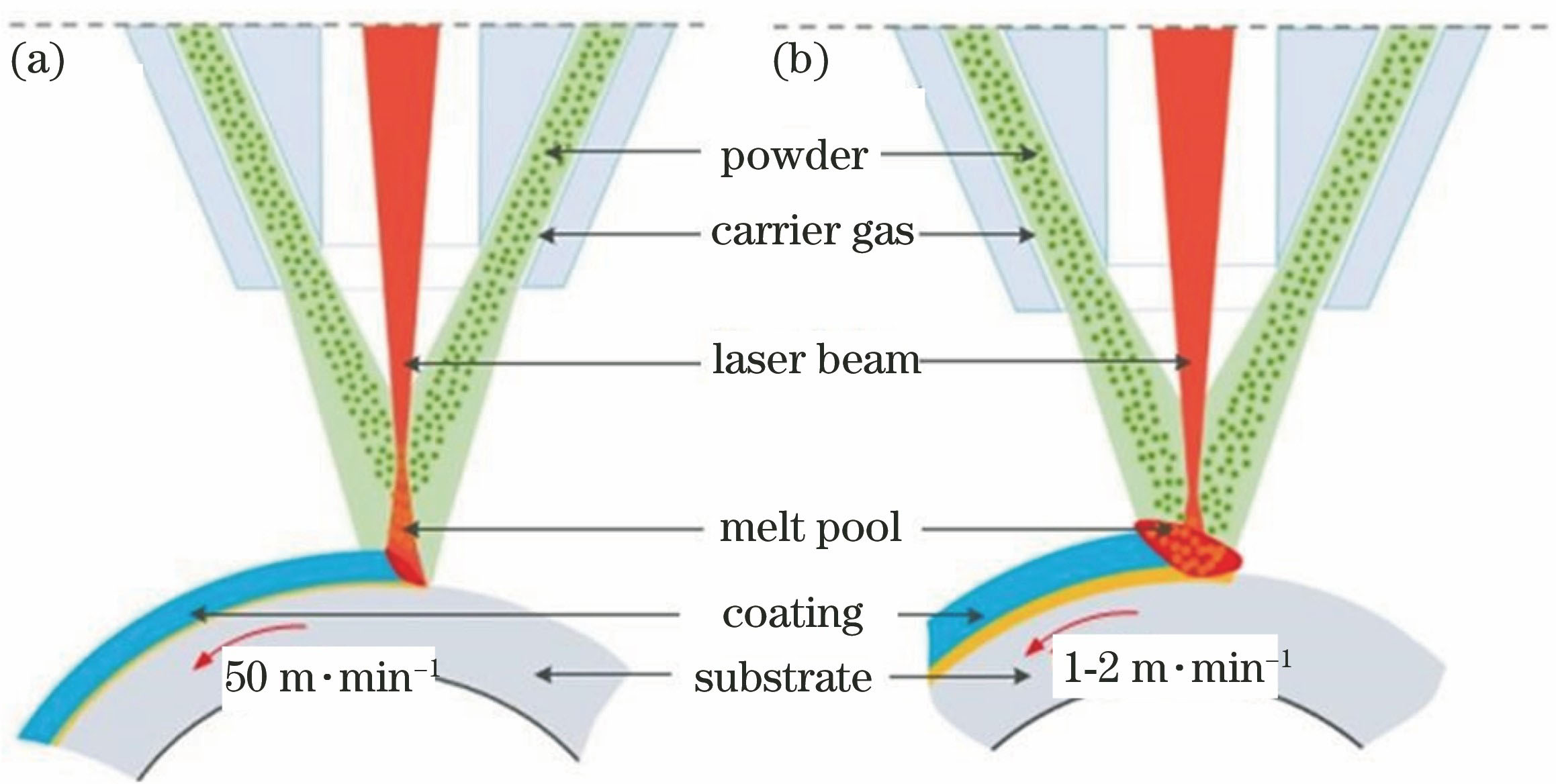
图 1. 熔覆原理图。 (a)超高速激光熔覆过程原理;(b)常规激光熔覆过程原理
Fig. 1. Principles of two laser claddings. (a) EHLA; (b) CLA
使用线切割机将激光熔覆试样制成8 mm×8 mm×12 mm的金相试样,经打磨、抛光后采用王水溶液[
2 试验结果与分析
2.1 涂层的宏观特征
为了获得致密且足够厚度的涂层,超高速激光熔覆的搭接率一般在80%~90%,相比常规激光熔覆(搭接率为20%~30%)提高很大,因此对于超高速激光熔覆技术,即使是单层熔覆,也可以获得类似“多层”熔覆的效果。
超高速激光熔覆的热影响区宽度约为50 μm,如
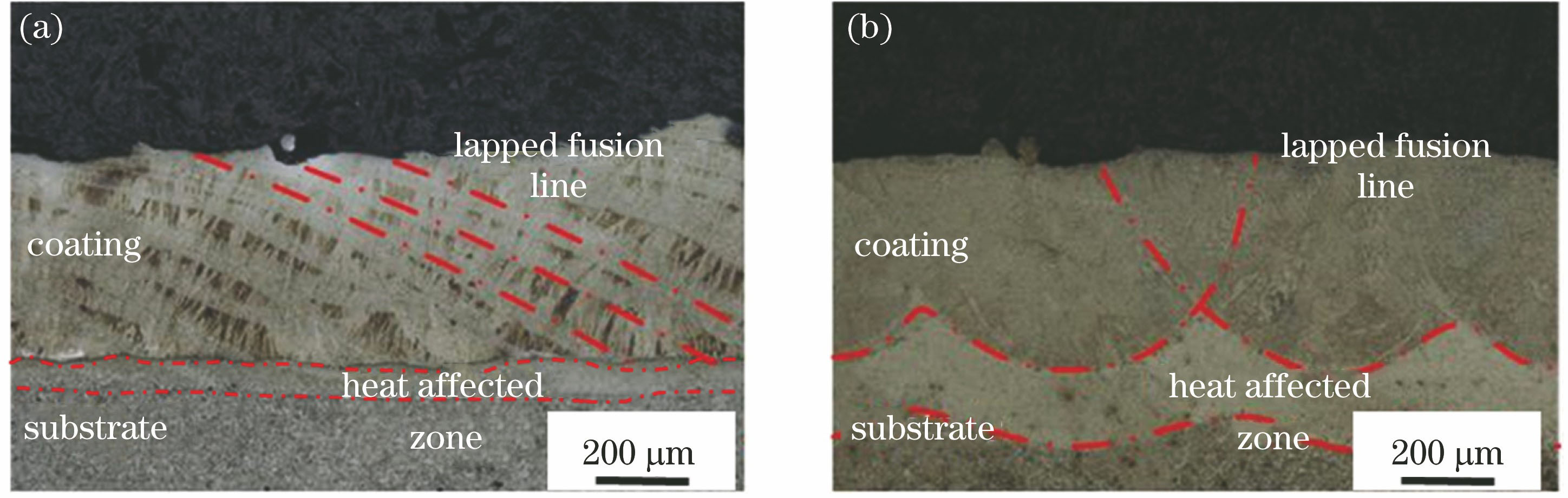
图 2. 单层不锈钢涂层截面的宏观形貌。(a)超高速激光熔覆;(b)常规激光熔覆
Fig. 2. Macroscopic morphologies of single-layer stainless steel coating prepared by two methods. (a) EHLA; (b) CLA
从
此外,超高速激光熔覆表面相对平整,涂层的表面粗糙度
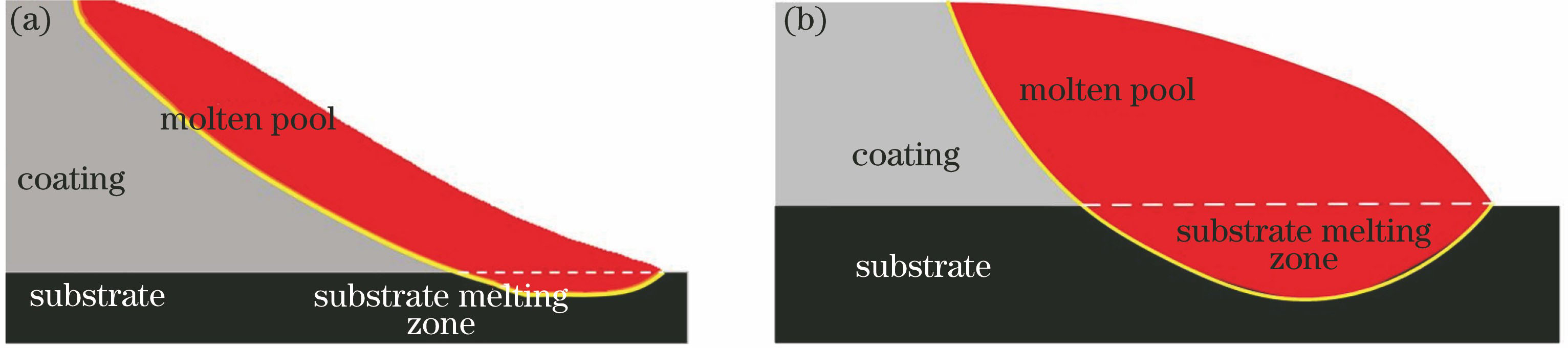
图 3. 超高速和常规激光熔覆过程的熔池形态。(a)超高速激光熔覆;(b)常规激光熔覆
Fig. 3. Molten pool morphologies of EHLA and CLA. (a) EHLA; (b) CLA
2.2 涂层的微观组织特征
由于超高速激光熔覆涂层为多层搭接结构,且熔池尺寸很小,因此总体上涂层的微观组织非常均匀。针对涂层表面、中部多层搭接区及底部/基体界面结合区这三个重点区域进行微观组织特征分析,具体取样位置与对应微区的组织形貌如
涂层表面的组织如
涂层中部的组织如
涂层底部/基体界面结合区的组织如
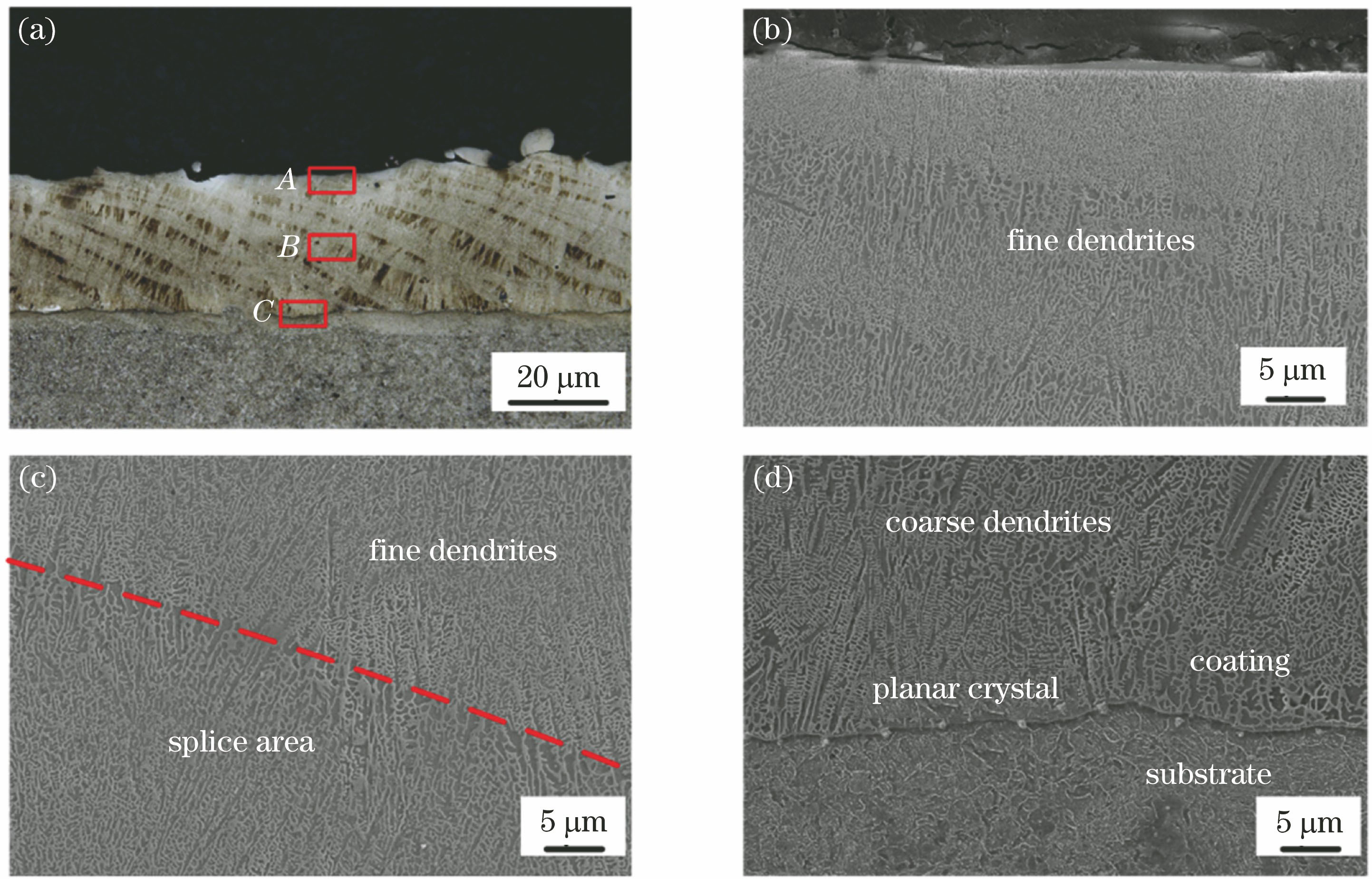
图 4. 超高速激光熔覆单层多道搭接涂层的形貌。(a)涂层整体形貌; (b)涂层表面(A区域)形貌;(c)涂层中部(B区域)形貌; (d)底部/基体界面结合区(C区域)形貌
Fig. 4. Morphologies of single-layer multi-lap coatings by EHLA. (a) Macroscopic morphology of coating; (b) micro-morphology of surface of coating (zone A); (c) micro-morphology of middle part of coating (zone B); (d) micro-morphology of coating/substrate interface (zone C)
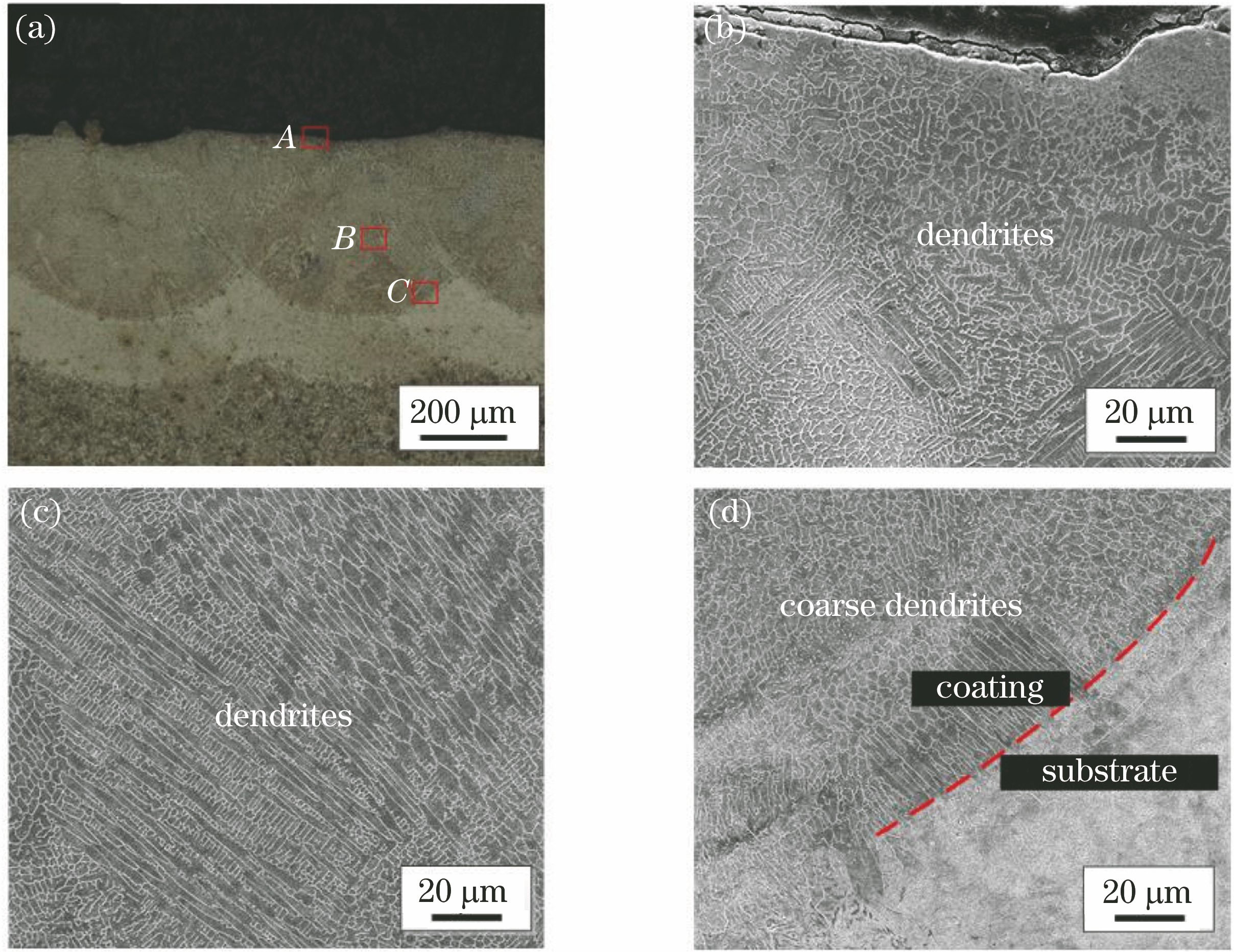
图 5. 常规激光熔覆单层多道搭接涂层的形貌。 (a) 涂层整体形貌; (b)涂层表面(A区域)形貌;(c)涂层中部(B区域)形貌; (d)底部/基体界面结合区(C区域)形貌
Fig. 5. Morphologies of single-layer multi-lap coatings by CLA. (a) Macroscopic morphology of coating; (b) micro-morphology of surface of coating (zone A); (c) micro-morphology of middle part of coating (zone B); (d) micro-morphology of coating/substrate interface (zone C)

图 6. 超高速激光熔覆涂层与常规激光熔覆涂层的组织对比。(a)超高速激光熔覆涂层的顶部组织;(b)超高速激光熔覆涂层的截面组织;(c)常规激光熔覆涂层的顶部组织;(d)常规激光熔覆涂层的截面组织
Fig. 6. Comparison of microstructures of coatings prepared by EHLA and CLA. (a) Top microstructure of coating prepared by EHLA; (b) cross-sectional microstructure of coating prepared by EHLA; (c) top microstructure of coating prepared by CLA; (d) cross-sectional microstructure of coating prepared by CLA
2.3 涂层元素的分布特点
采用线扫描能谱的方法对两种工艺下的涂层与基体中的Cr、Fe元素的分布特征进行分析,结果如
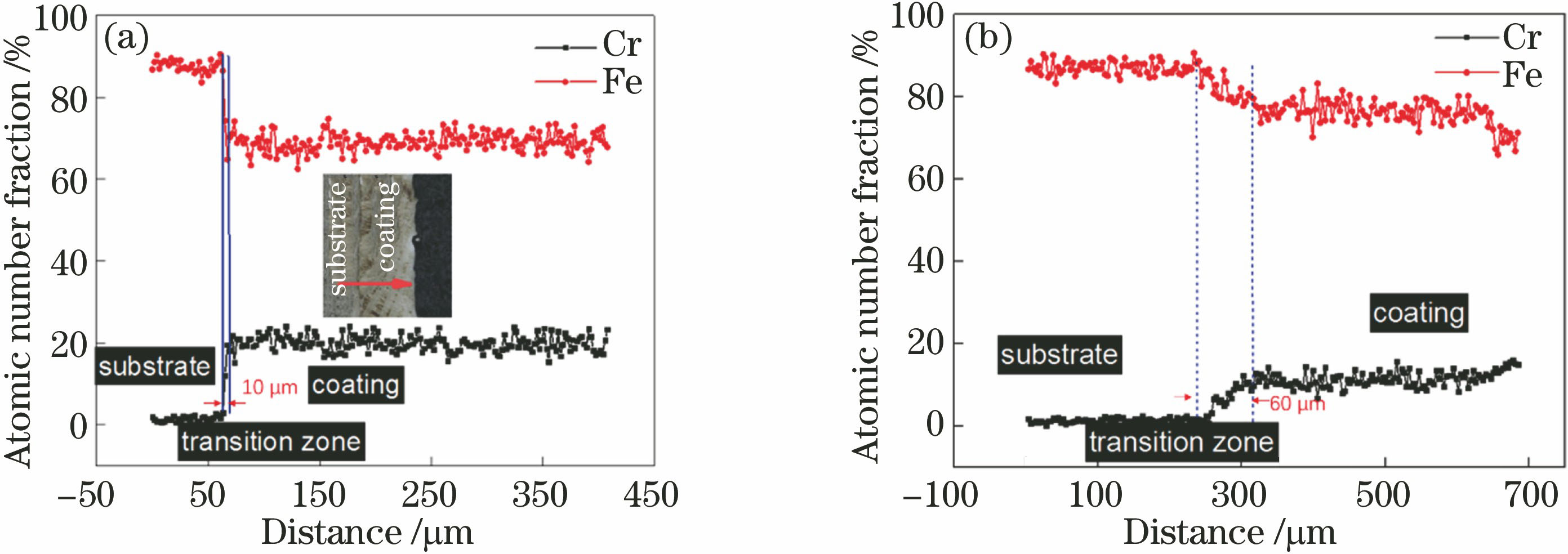
图 7. 涂层中的元素分布。(a)超高速激光熔覆涂层;(b)常规激光熔覆涂层
Fig. 7. Elemental distributions of coatings. (a) Coating prepared by EHLA; (b) coating prepared by CLA
超高速激光熔覆涂层之所以形成了极窄的元素过渡区,主要是因为超高速激光熔覆的热输入很小,形成的熔池也很小,仅有很薄一层的基体发生熔化,与填充材料实现冶金结合。此外,涂层间的高搭接率形成的多层结构也有效阻碍了基体与涂层成分的混合,使得熔池只有在接触基体的非常小的范围内存在稀释区。
2.4 涂层的硬度分析
从
2.5 涂层的XRD分析
从
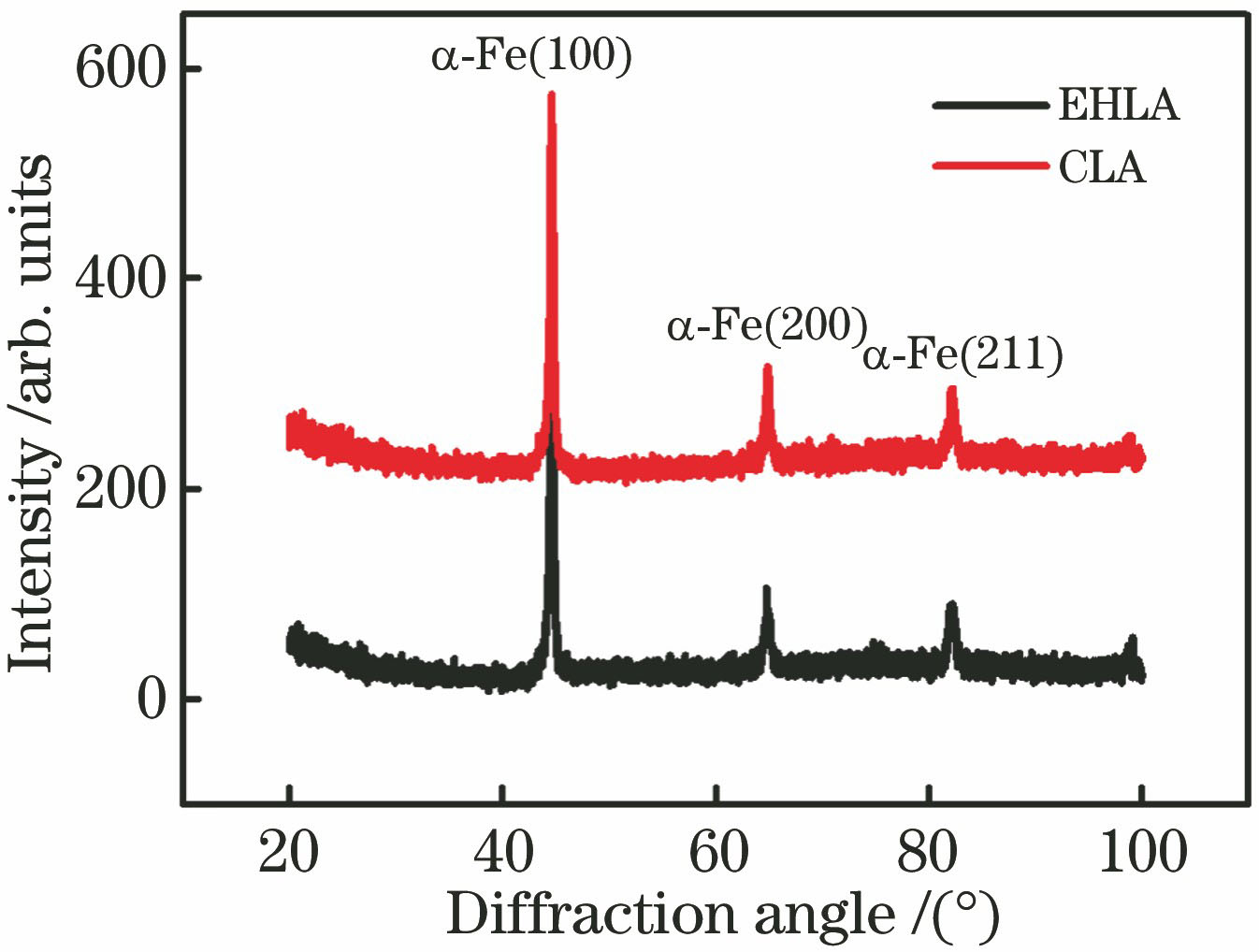
图 9. 超高速激光熔覆突出和常规激光熔覆涂层表面的XRD分析
Fig. 9. XRD analyses for surfaces of coatings prepared by EHLA and CLA
2.6 涂层的耐蚀性分析
采用电化学腐蚀方法对超高速激光熔覆涂层与常规激光熔覆涂层的耐蚀性进行测试与分析。首先,对涂层表面进行打磨抛光处理,保留涂层剩余厚度约为150 μm。
从
由
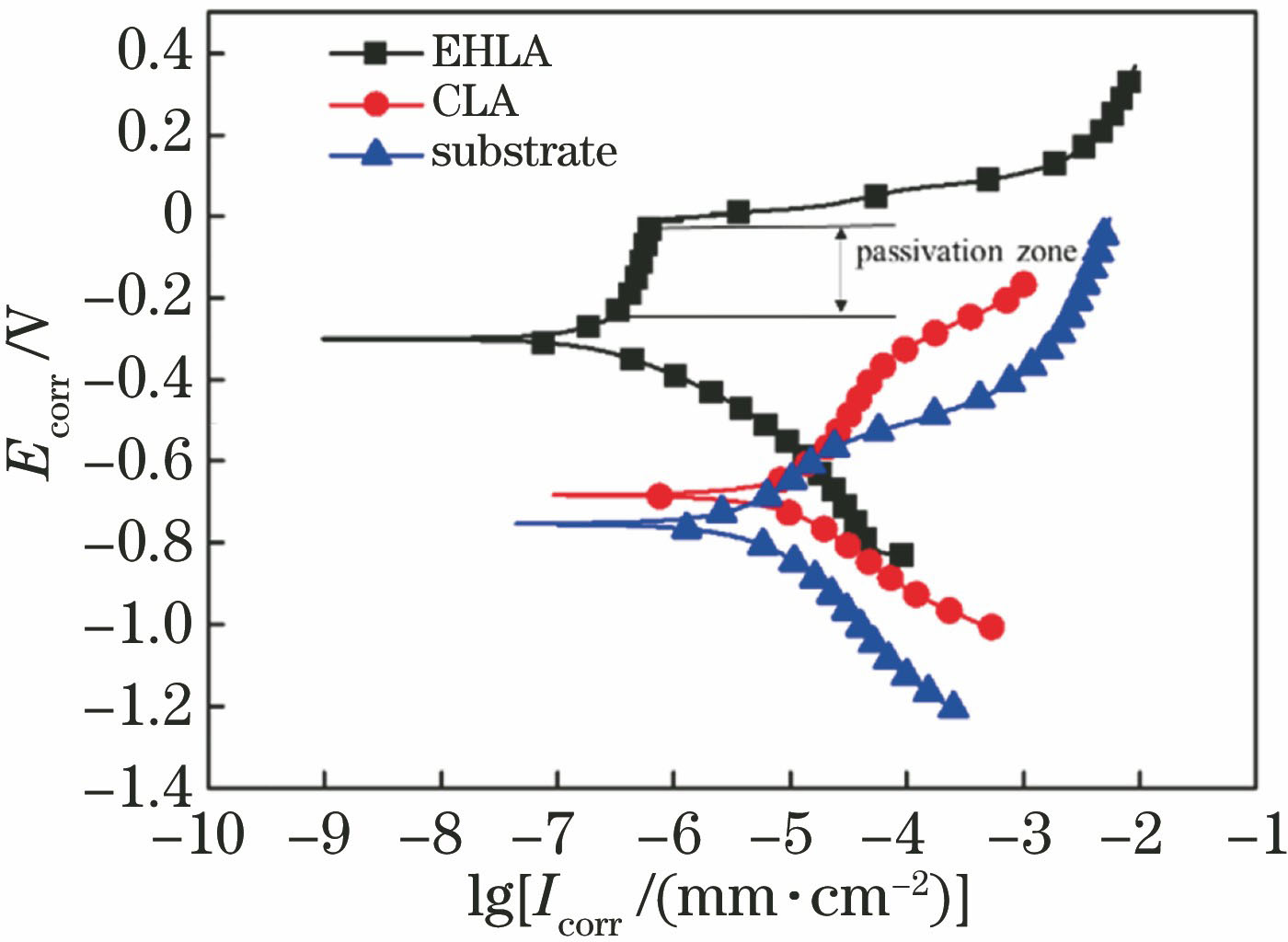
图 10. 超高速激光熔覆涂层、常规激光熔覆涂层和基体在3.5%NaCl溶液中的极化曲线
Fig. 10. Polarization curves of substrate and coatings prepared by EHLA and CLA in 3.5% NaCl solution
表 2. 涂层与基体的腐蚀电位、腐蚀电流密度
Table 2. Corrosion potentials and current densities of substrate and coatings prepared by EHLA and CLA
|
1) 超高速激光熔覆具有更高的Cr含量,有助于形成更加致密的钝化膜。
2) 均匀、细小的微观组织能够使钝化膜形核的位点增加,在表面越容易形成致密的钝化膜,钝化膜破裂后的“自愈”能力越强,因此更有利于提高耐蚀性能[20-23]。此外,均匀的组织有效减少了因组织结构不均而引起的电偶腐蚀程度。
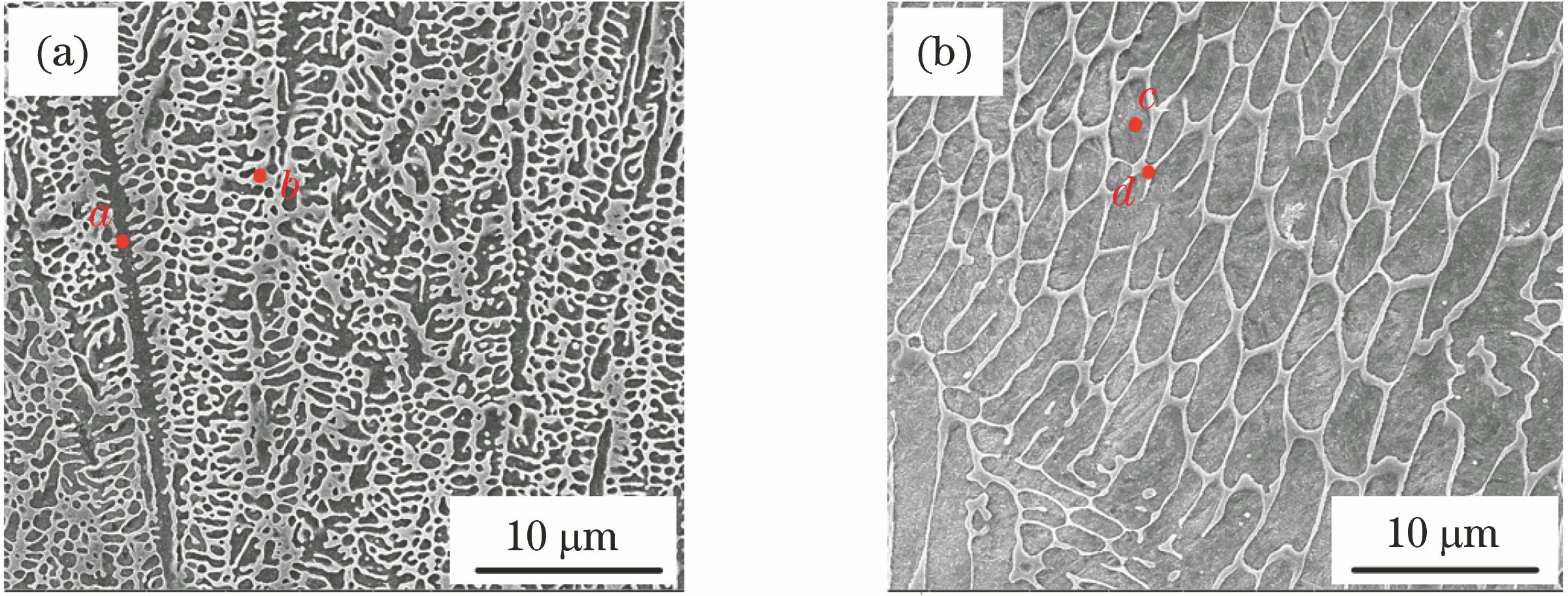
图 11. 涂层枝晶的显微组织。(a)超高速激光熔覆涂层;(b)常规激光熔覆涂层
Fig. 11. Microstructures of dendrites in coatings. (a) Coating prepared by EHLA; (b) coating prepared by CLA
表 3. 超高速激光熔覆涂层和常规激光熔覆涂层的枝晶内部和晶间成分差异
Table 3. Difference in chemical composition inside and between dendrites for coatings prepared by EHLA and CLA
|
由于Cr也是影响涂层耐蚀性的主要因素之一,本研究对超高速激光熔覆涂层表面耐蚀性测试区的Cr含量进行了面扫描测试,得到超高速激光熔覆涂层表面与液体接触处涂层中Cr的原子数分数为19%,与原始粉末中Cr的原子数分数基本相当,而常规熔覆涂层表面与液体接触位置中Cr的原子数分数约为14%。Cr元素能在涂层表面形成Cr2O3膜层,可以有效地阻碍腐蚀的继续,减缓腐蚀速率[24-25];同时Cr元素还有利于合金在较低的电位时进入钝化态,使表层形成完整的钝化膜,并在较低的电位维钝[26],因而使得涂层具有优良的耐蚀性能。
3 结论
采用超高速激光熔覆和常规激光熔覆的方法在27SiMn基体上成功制备出致密、无缺陷,并且具有良好冶金结合的431不锈钢耐蚀涂层。超高速激光熔覆具有较高的熔覆速度,比常规激光熔覆具有更高的熔覆效率。超高速激光熔覆涂层具有特殊的“多米诺骨牌”搭接形式,使得母材仅有小部分稀释到了涂层中,从而获得了不超过4%的稀释率。超高速激光熔覆涂层组织以细密的树枝晶为主,相较于常规激光熔覆组织更加细密均匀。超高速激光熔覆涂层中的Cr含量在枝晶内部和枝晶间的分布更加均匀。组织和成分的均匀性提高了涂层的耐蚀性能,使得涂层即使在300 μm左右的厚度下也可较好地保护基体。
超高速激光熔覆技术耐蚀性能的研究对超高速激光熔覆技术在工业中的应用具有重要意义。关于超高速激光熔覆涂层的耐蚀性能需要进一步研究,涂层内部存在的夹渣等缺陷对涂层的耐蚀性能的影响也需进一步明确。
[1] Fouquet F, Sallamand P, Millet J P, et al. Microstructural and electrochemical characterization of laser deposited 18-10 austenitic stainless steel clad layers[J]. Journal de Physique IV, 1993, 3(C7): 991-994.
[2] Li R. Ferreira M G S, Anjos M A, et al. Localized corrosion of laser surface cladded UNS S31254 superaustenitic stainless steel on mild steel[J]. Surface and Coatings Technology, 1997, 88(1/2/3): 90-95.
[3] 任超, 李铸国, 疏达, 等. 17-4PH不锈钢表面激光熔覆Stellite6涂层组织及耐水蚀性能[J]. 中国激光, 2017, 44(4): 0402010.
[4] 朱红梅, 李勇作, 张振远, 等. 激光熔覆制备马氏体/铁素体双相不锈钢层的力学与腐蚀性能研究[J]. 中国激光, 2018, 45(12): 1202012.
[5] 叶四友, 刘建永, 杨伟. 激光熔覆316L不锈钢涂层组织和性能的研究[J]. 表面技术, 2018, 47(3): 48-53.
[6] 张美美, 刘斌, 白培康. 液压支架管激光熔覆316L不锈钢涂层组织与性能研究[J]. 测试科学与仪器, 2017, 8(2): 154-161.
[7] 袁庆龙, 冯旭东, 曹晶晶, 等. 激光熔覆技术研究进展[J]. 材料导报, 2010, 24(3): 112-116.
[8] KelbassaI,[\s]{1}GasserA,[\s]{1}MeinersW,[\s]{1}et[\s]{1}al.[\s]{1}High[\s]{1}speed[\s]{1}LAM[M][\s]{1}∥Hinduja[\s]{1}S,[\s]{1}Li[\s]{1}L.[\s]{1}Laser[\s]{1}technology:[\s]{1}additive[\s]{1}manufacturing.[\s]{1}London:[\s]{1}Springer,[\s]{1}2012:[\s]{1}381-[\s]{1}385.[\s]{1}
[11] 达则晓丽, 朱彦彦, 李铸国. 激光功率对激光熔覆Fe-Co-B-Si-Nb涂层组织和性能的影响[J]. 中国表面工程, 2012, 25(3): 52-56.
[14] 何骅波, 杨梦梦, 黄晓波, 等. 螺杆钢表面不同激光熔覆层的耐磨与耐腐蚀性能[J]. 机械工程材料, 2017, 41(10): 11-14, 19.
[15] 李泽邦.[\s]{1}Ni基复合粉末激光熔覆层组织与性能的研究[D].[\s]{1}济南:[\s]{1}山东大学,[\s]{1}2013.[\s]{1}
Li[\s]{1}ZB.[\s]{1}Study[\s]{1}on[\s]{1}microstructure[\s]{1}and[\s]{1}properties[\s]{1}of[\s]{1}Ni-based[\s]{1}composite[\s]{1}laser[\s]{1}cladding[\s]{1}layers[D].[\s]{1}Jinan:[\s]{1}Shandong[\s]{1}University,[\s]{1}2013.[\s]{1}
[17] 郭振, 温永红, 胡水平, 等. 针状铁素体钢的组织类型及对性能的影响[J]. 材料开发与应用, 2007, 22(6): 5-8.
[18] 张郁彬, 苏长伟, 张长科, 等. 镍铁合金的微观结构及其在3.5%氯化钠溶液中的腐蚀行为[J]. 电镀与涂饰, 2009, 28(12): 1-4, 17.
Zhang Y B, Su C W, Zhang C K, et al. Microstructure of Ni-Fe alloy and its corrosion behavior in 3.5% NaCl solution[J]. Electroplating & Finishing, 2009, 28(12): 1-4, 17.
[19] 于有生, 倪火炬, 温家伶. 铁基合金激光熔覆的研究[J]. 中国表面工程, 2004, 17(4): 24-27, 31.
[20] 邱星武.[\s]{1}激光熔覆制备AlCoCrCuFeNiTi系高熵合金涂层工艺及其组织性能研究[D].[\s]{1}西安:[\s]{1}西安理工大学,[\s]{1}2014.[\s]{1}
Qiu[\s]{1}XW.[\s]{1}Preparation[\s]{1}technology[\s]{1}and[\s]{1}microstructure[\s]{1}&[\s]{1}properties[\s]{1}of[\s]{1}AlCoCrCuFeNiTi[\s]{1}high-entropy[\s]{1}alloy[\s]{1}coatings[\s]{1}by[\s]{1}laser[\s]{1}cladding[D].[\s]{1}Xi'an:[\s]{1}Xi'an[\s]{1}University[\s]{1}ofTechnology,[\s]{1}2014.[\s]{1}
[21] 华小珍, 刘华英, 唐永进, 等. Mg对SiCp/Al复合材料腐蚀行为的影响[J]. 腐蚀科学与防护技术, 2011, 23(1): 13-17.
[22] 张俊旺, 王文先, 黄延平, 等. 奥氏体不锈钢焊缝金属的电化学腐蚀性能[J]. 焊接学报, 2007, 28(2): 103-107.
[23] 伍光凤.[\s]{1}BHW35钢热丝TIG堆焊接头组织及性能研究[J].[\s]{1}焊接,[\s]{1}2013([\s]{1}11):[\s]{1}23-[\s]{1}27.[\s]{1}
Wu[\s]{1}GF.[\s]{1}Microstructure[\s]{1}and[\s]{1}properties[\s]{1}of[\s]{1}surfacing[\s]{1}welded[\s]{1}joint[\s]{1}by[\s]{1}hot[\s]{1}tire[\s]{1}tungsten[\s]{1}inert-gas[\s]{1}welding[\s]{1}process[J].[\s]{1}Welding[\s]{1}&[\s]{1}Joining,[\s]{1}2013([\s]{1}11):[\s]{1}23-[\s]{1}27.[\s]{1}
[24] 赵方方, 孙会来, 孙宽. 45钢表面激光熔覆316L涂层显微组织与性能[J]. 激光与红外, 2007, 37(8): 712-714.
[25] 冯旭东.[\s]{1}低碳钢表面激光熔覆镍基涂层组织及耐蚀性研究[D].[\s]{1}焦作:[\s]{1}河南理工大学,[\s]{1}2011.[\s]{1}
Feng[\s]{1}XD.[\s]{1}Research[\s]{1}on[\s]{1}the[\s]{1}microstructure[\s]{1}and[\s]{1}corrosion[\s]{1}resistance[\s]{1}of[\s]{1}Ni-based[\s]{1}alloy[\s]{1}coatings[\s]{1}by[\s]{1}laser[\s]{1}cladding[\s]{1}on[\s]{1}the[\s]{1}soft[\s]{1}steel[D].[\s]{1}Jiaozuo:[\s]{1}Henan[\s]{1}Polytechnic[\s]{1}University,[\s]{1}2011.[\s]{1}
[26] 吴向清, 胡慧玲, 谢发勤, 等. 等离子喷涂镍基合金涂层的组织与耐蚀性[J]. 中国表面工程, 2011, 24(5): 13-17.
Article Outline
李俐群, 申发明, 周远东, 陶汪, 王威, 王树良. 超高速激光熔覆与常规激光熔覆431不锈钢涂层微观组织和耐蚀性的对比[J]. 中国激光, 2019, 46(10): 1002010. Liqun Li, Faming Shen, Yuandong Zhou, Wang Tao, Wei Wang, Shuliang Wang. Comparison of Microstructure and Corrosion Resistance of 431 Stainless Steel Coatings Prepared by Extreme High-Speed Laser Cladding and Conventional Laser Cladding[J]. Chinese Journal of Lasers, 2019, 46(10): 1002010.