大功率半导体激光器封装热应力研究
下载: 1801次
1 引言
凭借着体积小、质量轻、效率高以及易于调制等优点,大功率半导体激光器被广泛应用于材料加工、医疗和美容、**与**等领域[1-6]。目前,室温下连续工作的大功率半导体激光器的最高电光转换效率大约为70%[7],因此工作时将会产生大量的废热。如果不能及时将多余的热量释放出去,将会造成激光器管芯温度升高,导致材料禁带宽度发生变化,严重影响输出光束的稳定性。除此之外,激光器管芯与热沉材料之间的热膨胀系数不匹配,温度的变化将会导致热应力的产生,使输出光谱发生变化,若热应力过大,还会造成结合层开裂、管芯断裂等问题,严重影响器件的可靠性和寿命[8],因此对半导体激光器封装热应力的分析至关重要。
目前,通过实验分析热应力的方法[9]主要有应变计法、莫尔法、热光弹性法、X射线衍射法、中子衍射法等。通过实验方法分析热应力,不仅操作复杂、成本高,而且准确率较低。相比之下,软件模拟的方法已日渐成熟,若能合理设置模型边界和端口等条件,则可以获得与实验相一致的结果。2008年中国电子科技集团公司第十三研究所的王辉[8]利用有限元软件ANSYS分析了不同焊料封装的半导体激光器的热应力分布情况。2016年北京航空航天大学的全伟等[10]利用ANSYS软件设计仿真了一体化半导体激光器结构。2018年中国科学院西安光学精密机械研究所的陈天奇等[11]同样利用有限元软件ANSYS分析了不同封装结构和材料对大功率半导体激光器阵列热应力和Smile值的影响。
本文利用多物理场仿真软件COMSOL Multiphysics分别对不同焊料、不同厚度焊料以及不同厚度钨铜WCu次热沉封装的大功率半导体激光器巴条进行模拟,测量了不同封装条件下激光器巴条的光谱分布,并对模拟和实验结果进行分析,为优化设计大功率半导体激光器巴条的封装提供参考,对实际生产具有指导意义。
2 基于COMSOL Multiphysics的热应力仿真过程
所设计的仿真结构如
基于COMSOL Multiphysics软件的仿真步骤如下:首先,利用软件自带的模型向导,选择空间维度为三维结构,物理场为结构力学模块下的热应力(包括固体力学和固体传热)场,求解类型为稳态求解。按照
表 1. 相关材料参数
Table 1. Related material parameters
|
3 结果分析与讨论
3.1 不同焊料
目前,在大功率半导体激光器巴条的封装中,广泛使用的焊料主要有In和AuSn。In焊料属于软焊料[12],具有良好的塑性形变特性且应力较小,但高温环境容易导致焊层晶须的生长,从而使焊层热疲劳加速,产生严重的电迁移现象,导致激光二极管过早失效。AuSn焊料属于硬焊料[13],其抗疲劳、抗蠕变性能优异,屈服强度高,导热性能好,无需助焊剂,也不存在严重的电迁移现象,但延展性差,烧结过程会引入过大应力,因此对焊接工艺的要求更加严格。首先对In焊料和AuSn焊料封装的大功率半导体激光器巴条进行模拟,分析其工作时温度和热应力分布情况。模拟中,Cu热沉的尺寸为20000 μm×20000 μm×4000 μm,WCu热沉的尺寸为11000 μm×2000 μm×400 μm,In和AuSn焊料的尺寸均为11000 μm×2000 μm×10 μm,激光器芯片的尺寸为11000 μm×2000 μm×120 μm。
仿真结果如
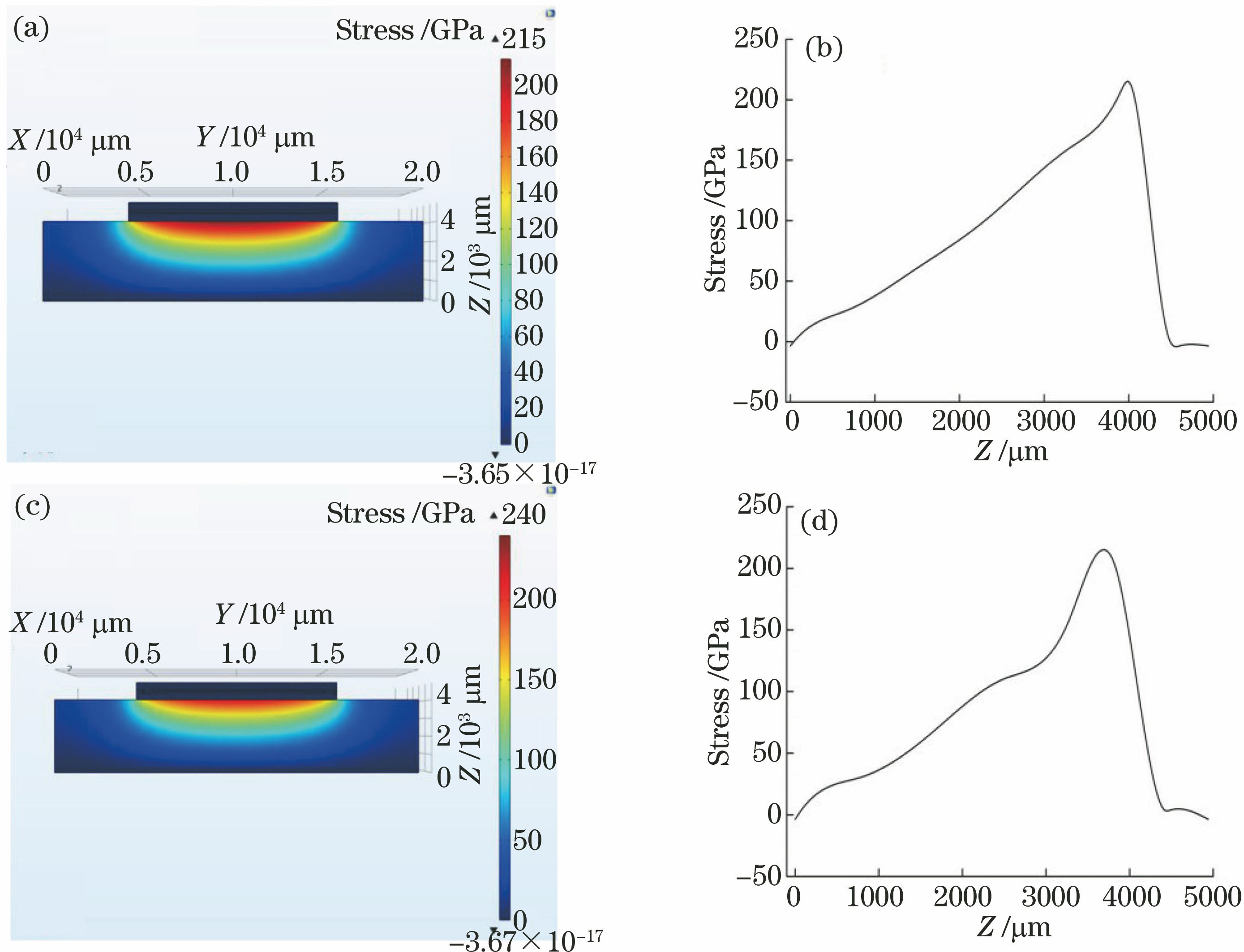
图 2. 不同焊料封装激光器热应力分布云图和端面中轴线上应力分布。(a) In焊料,热应力云图;(b) In焊料,端面中轴线上应力分布;(c) AuSn焊料,热应力云图 ;(d) AuSn焊料,端面中轴线上应力分布
Fig. 2. Nephograms of thermal stress distribution of laser dies with different solder packages and stress distributions on central axis of end face. (a) In solder, thermal stress nephogram; (b) In solder, stress distribution on central axis of end face; (c) AuSn solder, thermal stress nephogram; (d) AuSn solder, stress distribution on central axis of end face
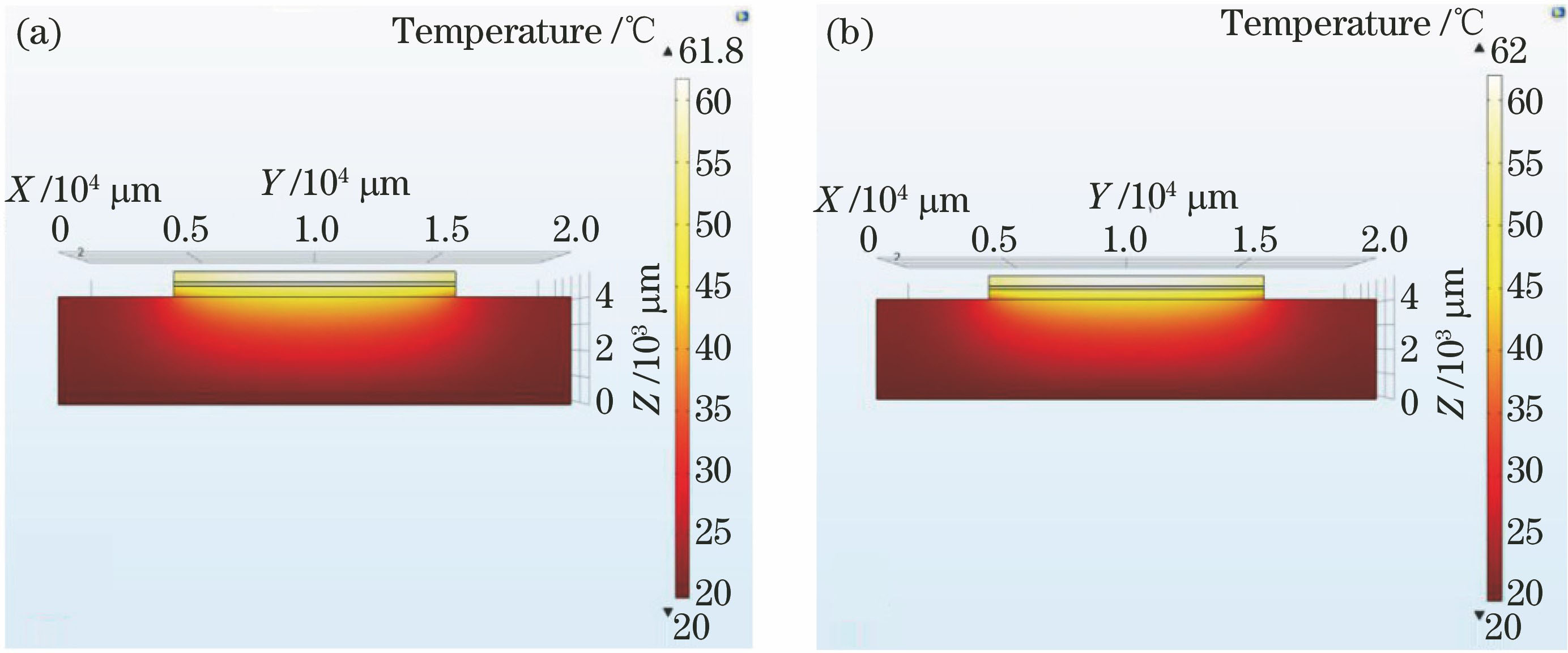
图 3. 不同焊料封装激光器温度分布。(a) In焊料;(b) AuSn焊料
Fig. 3. Temperature distributions of lasers with different solder packages. (a) In solder; (b) AuSn solder
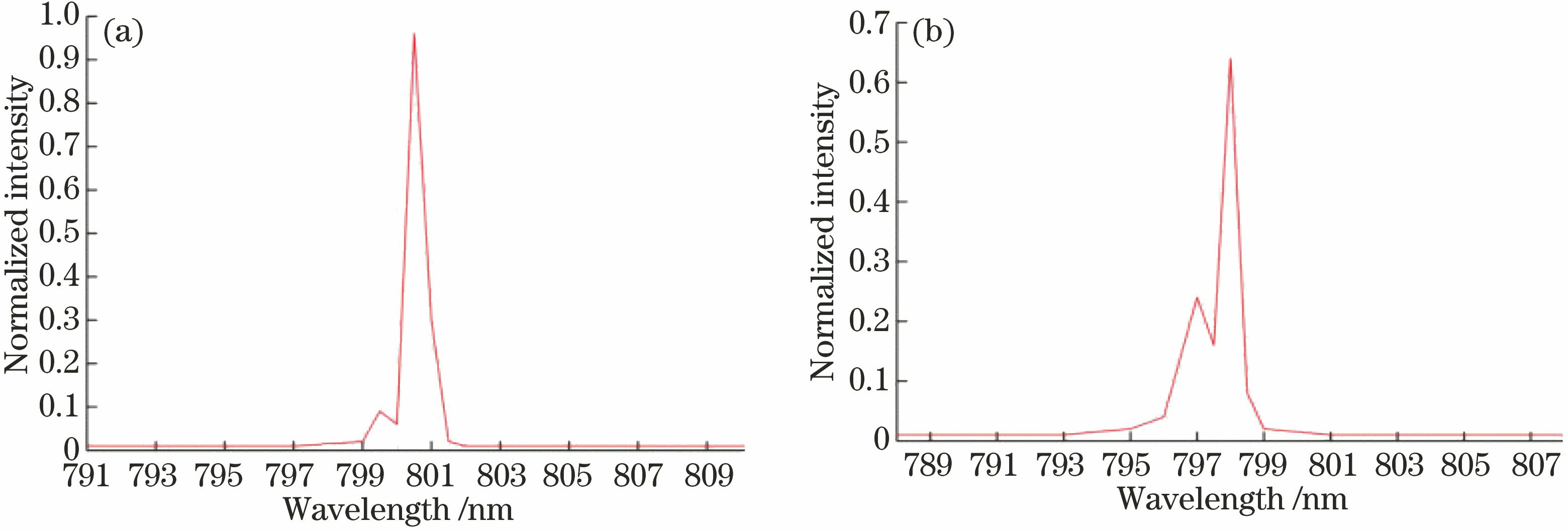
图 4. 不同焊料封装的激光器光谱分布。(a) In焊料;(b) AuSn焊料
Fig. 4. Spectral distributions of lasers with different solder packages. (a) In solder; (b) AuSn solder
3.2 不同厚度焊料
由
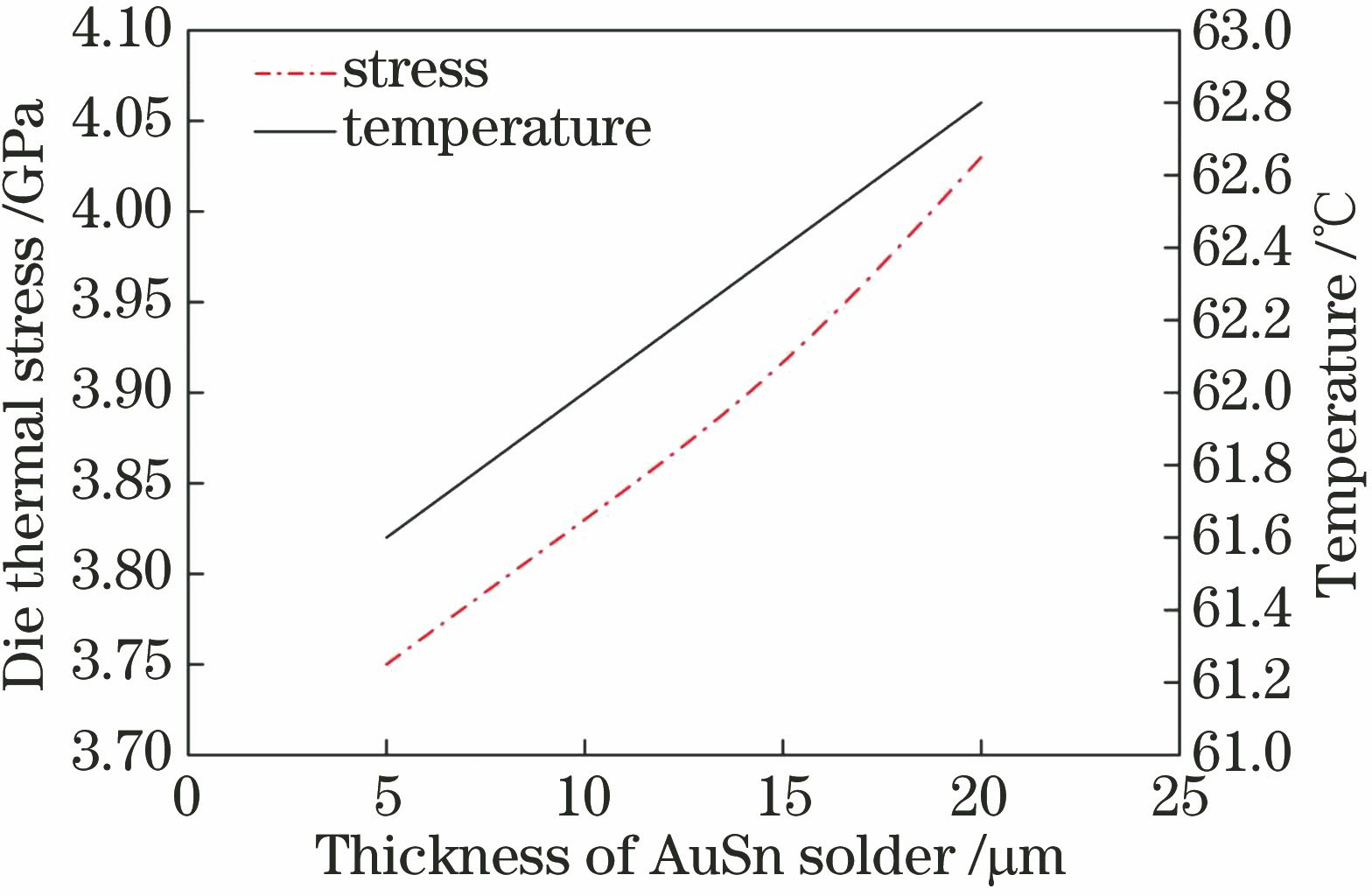
图 5. 不同厚度AuSn焊料封装的激光器芯片热应力和温度最大值分布
Fig. 5. Thermal stress and temperature maximum distribution of laser dies packaged by AuSn solders with different thicknesses
对激光器管芯内部热应力和温度的降低越有利,但在实际应用过程中却并非如此。若焊料厚度过薄,则可能会导致激光器管芯焊接不牢,或焊料分布不均匀,焊料层内部有空洞产生等。激光器焊接不牢,则可能会导致管芯与WCu次热沉之间开裂;而焊料层内部有空洞,则会导致局部热点效应,严重影响器件工作的稳定性和寿命。因此,焊料层厚度的确定是由多项因素共同决定的,有待于进一步优化。
3.3 不同厚度WCu次热沉
为了解决激光器管芯与Cu热沉热膨胀系数不匹配的问题,在大功率半导体激光器巴条的封装中常使用WCu次热沉作为过渡热沉,可以有效地缓解激光器管芯热应力过大的问题,对管芯起到保护作用。但相较于Cu热沉,WCu次热沉的热导率较差,若厚度过大,则会对激光器芯片的散热造成不利影响;若厚度过小,则起不到缓解热应力的作用,为此对不同厚度WCu次热沉对激光器管芯温度和热应力分布的影响进行了分析。目前,在实际生产中大功率半导体激光器巴条封装所使用的WCu次热沉的厚度约为400 μm,因此仿真中设置使用的WCu次热沉的厚度分别为300,350,400,450,500 μm。模拟中Cu热沉、AuSn焊料、激光器芯片的尺寸均与3.1节一致,激光器管芯的热应力和温度随WCu次热沉厚度的变化如
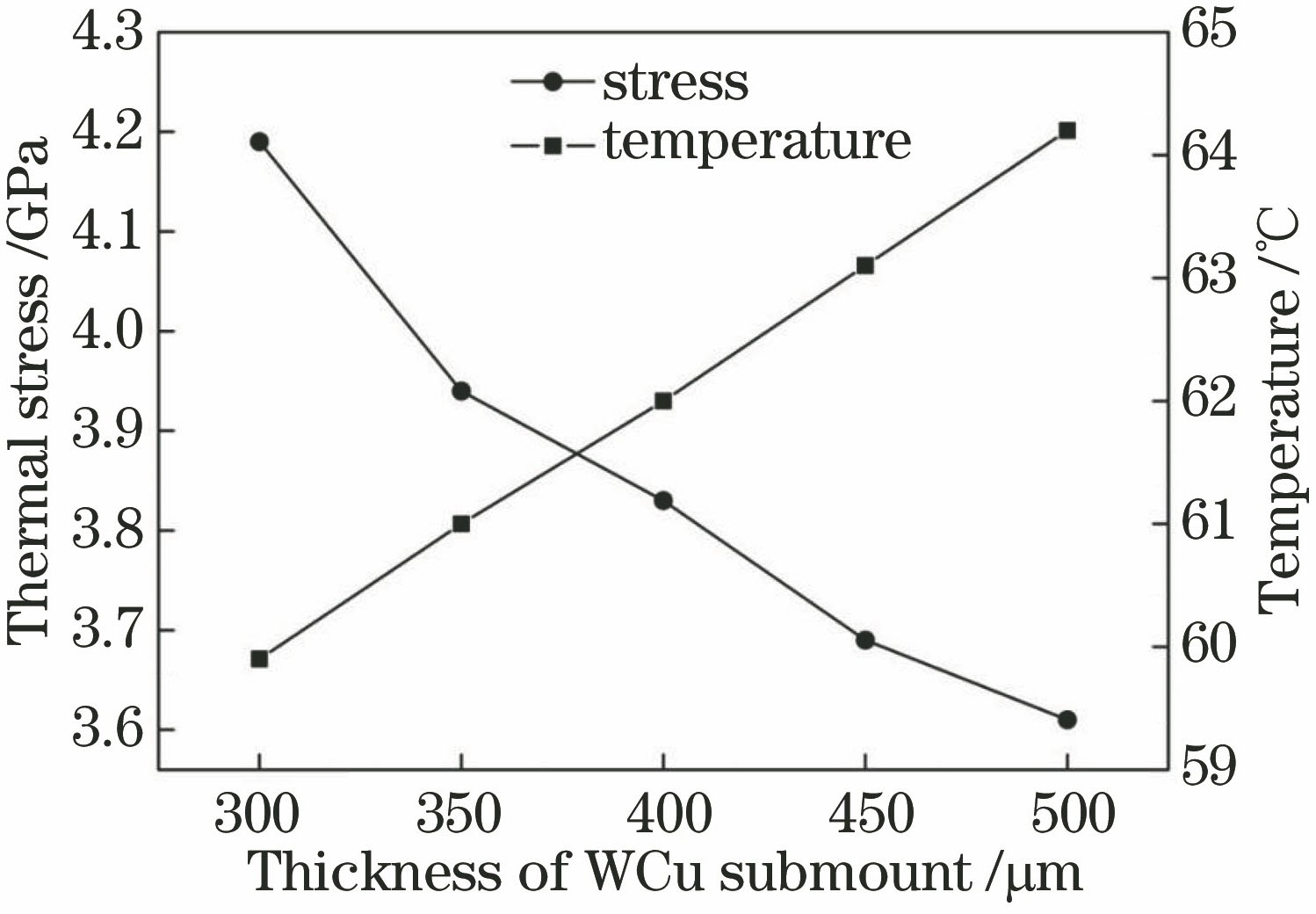
图 6. 不同厚度WCu次热沉封装的激光器管芯热应力和温度最大值分布
Fig. 6. Thermal stress and maximum temperature distribution of laser dies packaged by WCu submount with different thicknesses
从
4 结论
近年来,随着材料外延生长技术和芯片制备工艺的成熟,封装在大功率半导体激光器的应用中扮演的角色越来越重要。封装质量的好坏,直接决定了器件工作的稳定性和使用寿命。本文以808 nm大功率半导体激光器巴条的封装为研究对象,并结合多物理场仿真软件COMSOL Multiphysics,对不同焊料、不同厚度焊料和不同厚度WCu次热沉封装的激光器进行了相关的实验和模拟。研究结果表明:相较于AuSn焊料,In焊料封装的激光器管芯应力较低;减小焊料厚度,有利于降低激光器管芯的应力,但焊料厚度过薄, 则可能会导致激光器管芯焊接不牢或焊料分布不均匀、焊料层内部有空洞产生等现象。增加WCu次热沉的厚度,可以降低管芯受到的应力,但管芯温度上升,最优的WCu次热沉厚度为380 μm。
[1] Bachmann[\s]{1}F.[\s]{1}Industrial[\s]{1}applications[\s]{1}of[\s]{1}high[\s]{1}power[\s]{1}diode[\s]{1}lasers[\s]{1}in[\s]{1}materials[\s]{1}processing[J].[\s]{1}Applied[\s]{1}Surface[\s]{1}Science,[\s]{1}2003,[\s]{1}208/209:[\s]{1}125-[\s]{1}136.[\s]{1}
[2] BachmannF,[\s]{1}LoosenP,[\s]{1}PopraweR.[\s]{1}High[\s]{1}power[\s]{1}diode[\s]{1}lasers:[\s]{1}technology[\s]{1}and[\s]{1}applications[M].[\s]{1}New[\s]{1}York:[\s]{1}Springer,[\s]{1}2007,[\s]{1}128:[\s]{1}3888.[\s]{1}
[4] 王狮凌, 房丰洲. 大功率激光器及其发展[J]. 激光与光电子学进展, 2017, 54(9): 090005.
[5] 王立军, 宁永强, 秦莉, 等. 大功率半导体激光器研究进展[J]. 发光学报, 2015, 36(1): 1-19.
[6] 井红旗, 仲莉, 倪羽茜, 等. 高功率密度激光二极管叠层散热结构的热分析[J]. 发光学报, 2016, 37(1): 81-87.
[7] CrumpP,[\s]{1}GrimshawM,[\s]{1}WangJ,[\s]{1}et[\s]{1}al.[\s]{1}85%[\s]{1}power[\s]{1}conversion[\s]{1}efficiency[\s]{1}975-nm[\s]{1}broad[\s]{1}area[\s]{1}diode[\s]{1}lasers[\s]{1}at[\s]{1}-50[\s]{1}℃,[\s]{1}76[\s]{1}%[\s]{1}at[\s]{1}10[\s]{1}℃[C]∥2006[\s]{1}Conference[\s]{1}on[\s]{1}Lasers[\s]{1}and[\s]{1}Electro-Optics[\s]{1}and[\s]{1}2006[\s]{1}Quantum[\s]{1}Electronics[\s]{1}and[\s]{1}Laser[\s]{1}Science[\s]{1}Conference,[\s]{1}May[\s]{1}21-26,[\s]{1}2006,[\s]{1}Long[\s]{1}Beach,[\s]{1}CA,[\s]{1}USA.[\s]{1}New[\s]{1}York:[\s]{1}IEEE,[\s]{1}2016:[\s]{1}JWB24.[\s]{1}
[8] 王辉. 半导体激光器封装中热应力和变形的分析[J]. 半导体技术, 2008, 33(8): 718-720.
[9] 严宗达,[\s]{1}王洪礼.[\s]{1}热应力[M].[\s]{1}北京:[\s]{1}高等教育出版社,[\s]{1}1993:[\s]{1}93-[\s]{1}122.[\s]{1}
Yan[\s]{1}ZD,[\s]{1}Wang[\s]{1}HL.[\s]{1}Thermal[\s]{1}stress[\s]{1}[M].[\s]{1}Beijing:[\s]{1}Higher[\s]{1}Education[\s]{1}Press,[\s]{1}1993:[\s]{1}93-[\s]{1}122.[\s]{1}
[10] 全伟, 李光慧, 陈熙, 等. 一体化半导体激光器的ANSYS热仿真及结构设计[J]. 光学精密工程, 2016, 24(5): 1080-1086.
[11] 陈天奇, 张普, 彭勃, 等. 封装对大功率半导体激光器阵列热应力及Smile的影响[J]. 光子学报, 2018, 47(6): 129-139.
[12] 高松信, 魏彬, 吕文强, 等. 高功率二极管激光器失效特性研究[J]. 强激光与粒子束, 2005, 17(s1): 97-100.
[14] Liu[\s]{1}XS,[\s]{1}ZhaoW,[\s]{1}Xiong[\s]{1}LL,[\s]{1}et[\s]{1}al.[\s]{1}Packaging[\s]{1}of[\s]{1}high[\s]{1}power[\s]{1}semiconductor[\s]{1}lasers[M].[\s]{1}New[\s]{1}York:[\s]{1}Springer,[\s]{1}2015:[\s]{1}155-[\s]{1}166.[\s]{1}
袁庆贺, 井红旗, 仲莉, 刘素平, 马骁宇. 大功率半导体激光器封装热应力研究[J]. 中国激光, 2019, 46(10): 1001009. Qinghe Yuan, Hongqi Jing, Li Zhong, Suping Liu, Xiaoyu Ma. Thermal Stressin High-Power Semiconductor Laser Packaging[J]. Chinese Journal of Lasers, 2019, 46(10): 1001009.