选区激光熔化激光功率对316L不锈钢熔池形貌及残余应力的影响
下载: 1472次
1 引言
金属选区激光熔化(SLM)通过激光逐层熔化粉末而立体成形[1],由于其独特的成形理念与优势,近几年来在单件小批量难加工零件中有着越来越多的应用需求[2-3]。但SLM工艺参数对产品性能具有直接影响,尤其是工艺参数之间的匹配要求比较高,否则会导致成形件的微观结构、致密度、力学性能等出现差异,甚至形成制造缺陷,如气隙[4]、翘曲[5]、裂纹[6]、几何误差[7-8]等,进而导致成形件的质量降低或成形失败。在目前的SLM应用中,工艺匹配选择难度大,很多生产应用中需要多次调配实验参数,甚至会出现难以匹配到合适的工艺序列而不得不放弃采用该制造工艺成形零件的情况。文献[ 9]指出,影响产品性能的工艺参数有130多个,但最主要的影响参数有激光功率、扫描速度、层厚、激光吸收率、搭接率。研究发现,这些工艺参数不匹配首先会形成不均衡的温度场,导致产生较大的温度梯度,进而引起较大的热应力或内应力,这些应力在成形件冷却凝固后即为残余应力,这是一般成形缺陷的主要起因。目前已有很多文献报道了工艺参数的选择及其对应的基本力学性能,但不同工艺参数对应的熔池状态及成形件中热应力的规律仍不明朗。
2009年,陈光霞等[10]通过实验分析了激光功率、扫描速度、搭接率对SLM成形件表面粗糙度的影响,得到了搭接率对表面粗糙度影响最大,且在搭接率约为30%时表面粗糙度最小的结论。2012年,王黎等[11]通过实验研究了316L粉末的物理性能对SLM成形件的影响,得到了小粒径粉末的成形性能更好的结论。2016年,王沛等[12]对SLM成形316L不锈钢的组织进行了研究,结果发现:随着激光功率逐渐增大,孔洞缺陷和裂纹都明显减少,致密度逐渐提高;但随着扫描速度和扫描间距逐渐增大,孔洞及裂纹缺陷开始增多,致密度逐渐降低。2017年,闫程程等[13]通过实验研究了采用SLM工艺成形316L不锈钢时激光功率、搭接率、扫描方式的选择,并认为在大激光功率下,采用搭接率为30%,且扫描方式为跳转变向加工的试样的组织更细小。2018年,黄建国等[14]研究了激光功率、扫描速度和扫描间距等工艺参数对SLM成形TC4合金件微观组织及力学性能的影响,并得到了较优的一组工艺参数。
许多学者还通过实验对SLM工艺参数的选择进行研究,并尝试了不同工艺参数下的热应力仿真研究。2014年,Wu等[15]通过实验研究了316 L不锈钢棋盘式扫描孤岛面积对残余应力的影响,并比较了激光功率和扫描速度的影响,得到了面积越大应力越大的结论。2016年,Liu等[16]通过实验研究了SLM成形件的组织和残余应力,结果表明,在相同的激光功率下,扫描速度越慢,残余应力越大;扫描轨迹越长,残余应力越大。2017年,Yan等[17]经过研究后发现,H13成形件具有较高的残余压应力,这与激光粉末沉积冷却的时间有关,冷却时间越长,残余应力越大。2010年,Zaeh等[18]对单道多层试样进行了仿真,研究了4种扫描策略对温度场和残余应力的影响。2016年,Vastola等[19]采用有限元模拟获得了光束尺寸、粉末密度、基板预热对应力的影响,认为基板预热可大幅降低SLM成形件中的残余应力。2017年,Somashekara等[20]采用有限元APDL语言对三种填充方式的一层三道双丝焊接进行了数值模拟,然后采用X射线衍射实验测量了三种模式下成形件中的残余应力,并将其与仿真结果进行了对比,尽管测量结果与仿真结果存在较大误差,但仿真可以提供初步的预测。
综上可见,对于工艺参数的研究,从单一参数分析发展到了多参数混合分析,而且残余应力分析也从实验研究发展到了仿真研究[21]。采用实验研究工艺参数对成形件中残余应力的影响时,不会系统地给出各参数的影响规律,只是单一地考虑某一因素,或者将多个参数混合在一起进行实验,得到的是较为有限的几组工艺参数的笼统分析,只能在有限的实验方案下选择较优的一组工艺参数,不能清楚地分析其各参数对性能的影响。而有限元仿真限于目前的仿真模型网格粗大、仿真模型的层道数有限,很难进行多工艺参数的匹配仿真,而且仿真试样计算精度较低,不能较为准确地反映工艺参数的实际热力影响。基于此,本文首先通过分组实验方案,在三种激光功率下以不同的扫描速度和扫描方式制备SLM试样,并分别对三种功率参数下成形的试样按梯度进行多层残余应力的测量,并分别对三种功率参数下的成形试样按梯度进行残余应力多层测量、熔池形貌观察,以及激光功率的热力学理论分析,从而为实际生产提供理论借鉴。
2 实验方法
2.1 成形方式及工艺参数
以316L不锈钢粉末为原料,采用成形设备SLM 280进行SLM成形实验。316L不锈钢粉末颗粒如
表 1. SLM试样正交实验表
Table 1. Orthogonal experiment table of SLM sample
|
2.2 测试方法
试样的微观形貌测试采用HIROX KH-1300 3D光学显微镜进行,对成形截面进行熔池形貌的采集(
3 实验结果及讨论
每组工艺参数下成形三个试样,对其中的一个进行线切割,观察熔池形貌,其他两个试样不作任何处理,直接进行残余应力的测试。
3.1 激光功率对凝固熔池的影响
6组参数下成形的试样在截面方向上的熔池形貌如
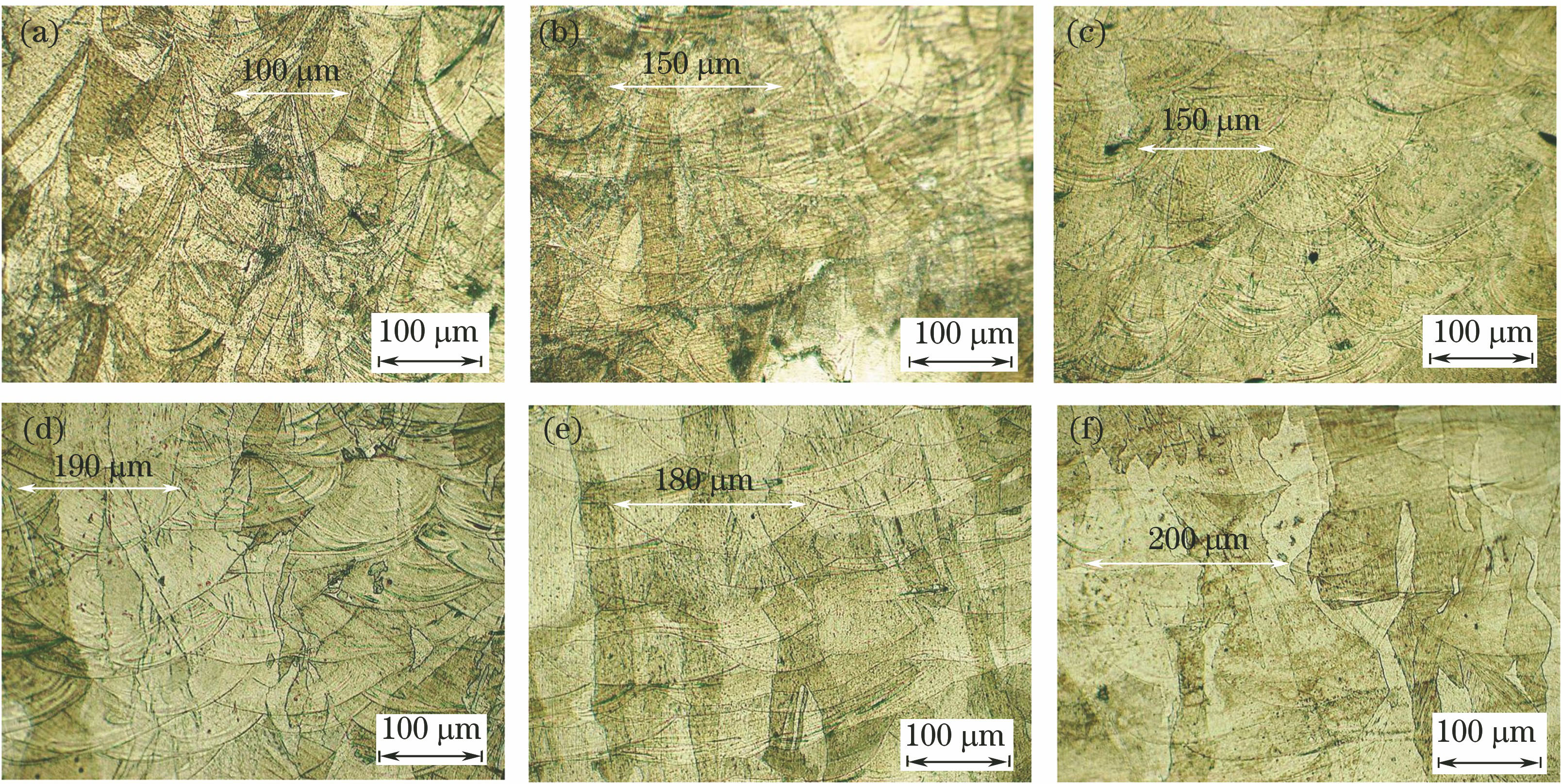
图 5. 不同工艺参数下SLM成形试样在截面方向上的熔池形貌。(a) P=160 W,v=600 mm/s, 棋盘式扫描(No.1);(b) P=160 W,v=600 mm/s, 条纹扫描(No.2);(c) P=200 W,v=800 mm/s, 条纹扫描(No.3);(d) P=200 W,v=600 mm/s, 条纹扫描(No.4);(e) P=200 W,v=600 mm/s, 棋盘式扫描(No.5);(f) P=240 W,v=800 mm/s, 条纹扫描(No.6)
Fig. 5. Morphologies of molten pool cross section of SLM formed samples for different process parameters. (a)P=160 W, v=600 mm/s, chess scanning (No.1);(b) P=160 W, v=600 mm/s, stripe scanning (No.2); (c) P=200 W, v=800 mm/s, stripe scanning (No.3); (d) P=200 W, v=600 mm/s, stripe scanning (No.4); (e) P=200 W, v=600 mm/s, chess scanning (No.5); (f) P=240 W, v=800 mm/s, stripe scanning (No.6)
3.2 激光功率对残余应力的影响
在分析激光功率对残余应力影响时,也将No.1和No.5参数、No.2和No.4参数、No.3和No.6参数下的成形试样进行对比,对不同剥层高度下的测试结果分别进行统计,结果如
由
将6组参数下成形试样的熔池直径与平均残余应力统计于
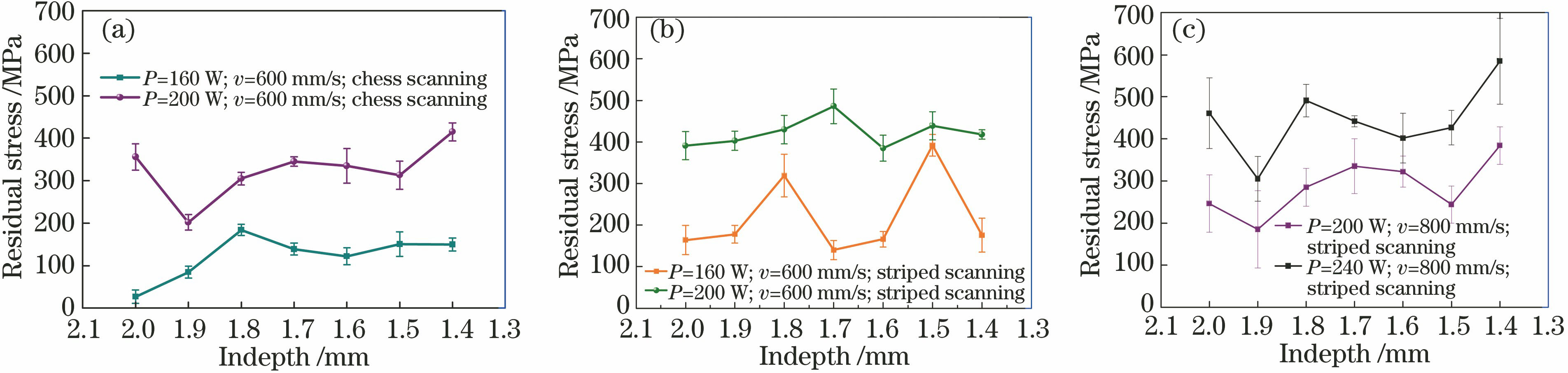
图 6. 不同工艺参数下SLM成形试样中的残余应力比较。(a) No.1与No.5;(b) No.2与No.4;(c) No.3与No.6
Fig. 6. Comparison of residual stresses in SLM formed samples with different process parameters. (a) No. 1 and No. 5; (b) No. 2 and No. 4; (c) No. 3 and No. 6
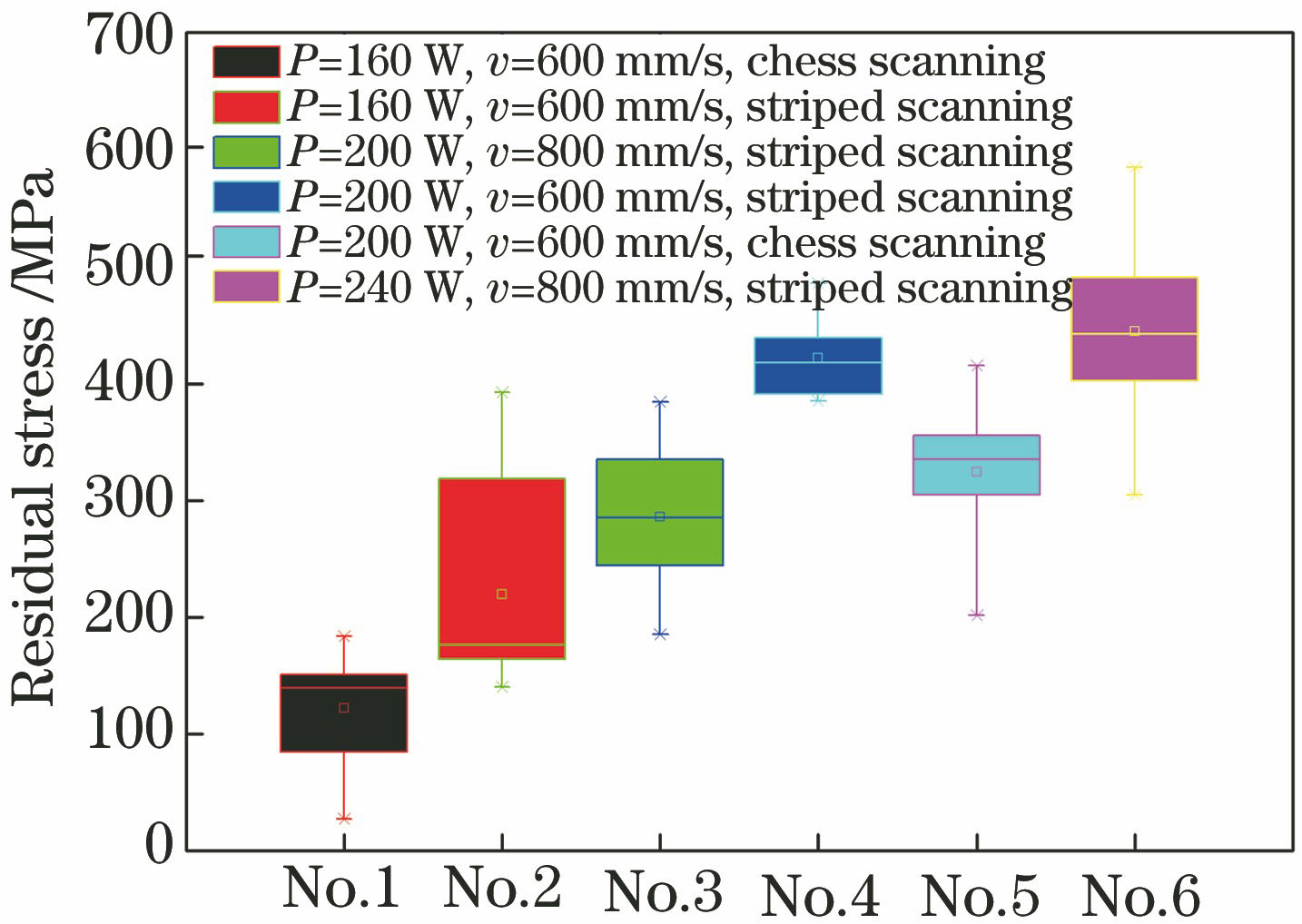
图 7. 不同工艺参数下SLM成形试样中平均残余应力的箱线图
Fig. 7. Average residual stress boxplots of SLM formed samples for different process parameters
3.3 激光功率影响的热力学分析
因为SLM激光热源是高斯热源模型,根据高斯热源热流密度的定义[22],从中心向外的最大热流密度以指数形式衰减,即
表 2. SLM试样的熔池直径和残余应力对比
Table 2. Comparison of molten pool diameters and residual stresses of SLM formed samples
|
式中:q为热流密度,单位为J/(m2·s);q0为光束中心位置处的最大能流密度(r=0);r为到光束中心的距离;ω为光束半径。
根据最大能流密度的定义
可知
式中:P为激光功率,单位为W;A为粉末材料的吸收率,用1减去材料的反射率和光的透射率即可得到(一般情况下取316L不锈钢粉末的吸收率为0.7)。
根据能流密度的定义(单位时间t内通过物体单位横截面积上的热量Q),可得到
式中:k为热导率,单位为W/(m·K);ΔT为高温端到低温端的温度差,单位为K;dr为当前层的材料厚度,单位为m;
在温度场分布已知的情况下,根据热应变的描述[23]
对于整个热弹塑性体有
即
式中:εth为热应变;αe为热膨胀系数;εf为受力应变;εii为三维弹塑性应变。由此可以得到,在激光熔融时,在相同的扫描速度下(即在相同的时间内),功率大,则产生的热量传导与辐射等的范围大,即熔池的尺寸大。此外,在材料热导率一定的情况下,功率大,则温度梯度大,温度更高,这会使得在相同的散热速率下,金属颗粒熔融持续的时间略长,故而金属原子的运动更加充分剧烈,不同的原子运动速率导致晶体排列的晶面夹角及晶界间距差异大[23],快速冷却后,较高的温度梯度使金属原子来不及到达一种新的平衡位置,所以凝固后的晶面夹角及晶界间距是一种杂乱无章的状态[24],导致在热作用下残留了内应力,即热应力[23]。因为激光运动的速度远大于冷却速率,所以当前一个整层接近于整体熔融再冷却,又由于边缘较中间位置的冷却速度大,故而最终形成了以最慢传热点为中心、边缘受拉、中心受压的应力分布[20],待整体试样冷却后即为残余应力。棋盘式扫描路径的长度为2 mm,而条纹式扫描路径的长度为4~6 mm,进一步结合
4 结论
对6组SLM工艺参数下成形试样的熔池形貌与残余应力进行了分析。为了保存应力的完准性,在不去除基板的情况下直接进行自动腐蚀剥层的残余应力测试。得到的主要结论如下:1)随着激光功率增大,热流密度增大,单位体积内的温度梯度增加,温度升高,形成的熔池尺寸较大,从而影响了熔池的实际搭接率。2)残余应力是由熔池温度和熔池大小等熔池特性的过大温度梯度造成的,激光功率越大,试样中的残余应力越大;可以通过合理的工艺参数匹配有效减小残余应力,在实际的SLM成形中,应根据粉末材料的属性,以达到熔池特性参数为参照进行合理的工艺参数设计。3)在满足材料属性的熔池条件下,SLM工艺参数的设计应尽可能选择较低的激光功率,提高扫描速度,缩短扫描轨迹,只要参数相互匹配使熔池的温度梯度合理,就不会出现应力过大或成形缺陷,也不会出现熔融不透、组织球化等现象。
[1] 杨永强, 陈杰, 宋长辉, 等. 金属零件激光选区熔化技术的现状及进展[J]. 激光与光电子学进展, 2018, 55(1): 011401.
[2] 刘萌. 3D打印SLM技术在机械自动化加工中的应用研究[J]. 数字技术与应用, 2015( 4): 107.
LiuM. Research on the application of 3D printing SLM technology in automatic machining[J]. Digital Technology and Application, 2015( 4): 107.
[3] 杨强, 鲁中良, 黄福享, 等. 激光增材制造技术的研究现状及发展趋势[J]. 航空制造技术, 2016( 12): 26- 31.
YangQ, Lu ZL, Huang FX, et al. Research on status and development trend of laser additive manufacturing[J]. Aeronautical Manufacturing Technology, 2016( 12): 26- 31.
[4] Sun Z J, Tan X P, Tor S B, et al. Selective laser melting of stainless steel 316L with low porosity and high build rates[J]. Materials & Design, 2016, 104: 197-204.
[5] 张凯, 刘婷婷, 张长东, 等. 基于熔池数据分析的激光选区熔化成形件翘曲变形行为研究[J]. 中国激光, 2015, 42(9): 0903007.
[6] Liu J, Yu H, Zhou T, et al. Effect of double quenching and tempering heat treatment on the microstructure and mechanical properties of a novel 5Cr steel processed by electro-slag casting[J]. Materials Science and Engineering: A, 2014, 619: 212-220.
[7] Paul R, Anand S, Gerner F. Effect of thermal deformation on part errors in metal powder based additive manufacturing processes[J]. Journal of Manufacturing Science and Engineering, 2014, 136(3): 031009.
[8] 朱小刚, 孙靖, 王联凤, 等. 激光选区熔化成形铝合金的组织、性能与倾斜面成形质量[J]. 机械工程材料, 2017, 41(2): 77-80.
Zhu X G, Sun J, Wang L F, et al. Microstructure, properties and inclined plane forming quality of aluminum alloy by selective laser melting[J]. Materials for Mechanical Engineering, 2017, 41(2): 77-80.
[9] Kamath C, El-Dasher B, Gallegos G F, et al. Density of additively-manufactured, 316L SS parts using laser powder-bed fusion at powers up to 400 W[J]. The International Journal of Advanced Manufacturing Technology, 2014, 74: 65-78.
[10] 陈光霞, 王泽敏, 关凯, 等. 工艺参数对SLM激光快速成型件表面粗糙度的影响[J]. 制造技术与机床, 2009( 12): 86- 89.
Chen GX, Wang ZM, GuanK, et al. Effects of parameters on surface roughness of samples by selective laser melting[J]. Manufacturing Technology & Machine Tool, 2009( 12): 86- 89.
[11] 王黎, 魏青松, 贺文婷, 等. 粉末特性与工艺参数对SLM成形的影响[J]. 华中科技大学学报(自然科学版), 2012, 40(6): 20-23.
Wang L, Wei Q S, He W T, et al. Influence of powder characteristic and process parameters on SLM formability[J]. Journal of Huazhong University of Science and Technology(Natural Science Edition), 2012, 40(6): 20-23.
[12] 王沛, 黄正华, 戚文军, 等. 基于SLM技术的3D打印工艺参数对316不锈钢组织缺陷的影响[J]. 机械制造文摘-焊接分册, 2016( 2): 2- 7.
WangP, Huang ZH, Qi WJ, et al. Effect of the 3D printing process parameters based on SLM technology on the structural defect of 316 stainless steel[J]. Welding Digest of Machinery Manufacturing, 2016( 2): 2- 7.
[13] 闫程程, 杨立军, 代文豪, 等. 工艺参数对激光选区熔化316L不锈钢表面质量的影响[J]. 热加工工艺, 2017, 46(20): 170-174.
Yan C C, Yang L J, Dai W H, et al. Effect of process parameters on surface quality of laser selective melting 316L stainless steel[J]. Hot Working Technology, 2017, 46(20): 170-174.
[14] 黄建国, 余欢, 徐志锋, 等. 基于SLM的工艺参数对TC4合金成形件性能的影响[J]. 特种铸造及有色合金, 2018, 38(4): 375-379.
Huang J G, Yu H, Xu Z F, et al. Effects of processing parameters on performance of TC4 alloy samples by selective laser melting[J]. Special Casting & Nonferrous Alloys, 2018, 38(4): 375-379.
[15] Wu A S, Brown D W, Kumar M, et al. An experimental investigation into additive manufacturing-induced residual stresses in 316L stainless steel[J]. Metallurgical and Materials Transactions A, 2014, 45(13): 6260-6270.
[16] Liu Y, Yang Y Q, Wang D. A study on the residual stress during selective laser melting (SLM) of metallic powder[J]. The International Journal of Advanced Manufacturing Technology, 2016, 87: 647-656.
[17] Yan J J, Zheng D L, Li H X, et al. Selective laser melting of H13: microstructure and residual stress[J]. Journal of Materials Science, 2017, 52(20): 12476-12485.
[19] Vastola G, Zhang G, Pei Q X, et al. Controlling of residual stress in additive manufacturing of Ti6Al4V by finite element modeling[J]. Additive Manufacturing, 2016, 12: 231-239.
[20] Somashekara M A, Naveenkumar M, Kumar A, et al. Investigations into effect of weld-deposition pattern on residual stress evolution for metallic additive manufacturing[J]. The International Journal of Advanced Manufacturing Technology, 2017, 90: 2009-2025.
[21] Mercelis P, Kruth J P. Residual stresses in selective laser sintering and selective laser melting[J]. Rapid Prototyping Journal, 2006, 12(5): 254-265.
[22] Hussein A, Hao L, Yan C Z, et al. Finite element simulation of the temperature and stress fields in single layers built without-support in selective laser melting[J]. Materials & Design (1980-2015), 2013, 52: 638-647.
[23] 姜传海, 杨传铮. 内应力衍射分析[M]. 北京: 科学出版社, 2013.
Jiang CH, Yang CZ. Internal stress diffraction analysis[M]. Beijing: Science Press, 2013.
[24] 边培莹. 热处理工艺对316L不锈钢粉末激光选区熔化成形的残余应力及组织的影响[J]. 材料热处理学报, 2019, 40(04): 90-97.
Bian P Y. Effect of heat treatment on residual stress and microstructure of 316L stainless steel powder formed by selective laser melting[J]. Transactions of Materials and Heat Treatment, 2019, 40(04): 90-97.
Article Outline
边培莹, 尹恩怀. 选区激光熔化激光功率对316L不锈钢熔池形貌及残余应力的影响[J]. 激光与光电子学进展, 2020, 57(1): 011403. Peiying Bian, Enhuai Yin. Effect of Laser Power for Metal Selective Laser Melting on Morphology of 316L Stainless Steel Molten Pool and Residual Stress[J]. Laser & Optoelectronics Progress, 2020, 57(1): 011403.