熔石英玻璃激光损伤的三维应力场研究
下载: 1231次
Objective Fused silica has been used in a variety of applications, including high-power laser devices, owing to its excellent chemical stability and optical properties. However, the fused silica optical elements in high-power laser devices are easily damaged owing to various complex physical and chemical mechanisms, thereby the system stability is affected. Researchers have successively conducted a lot of basic and applied researches on laser induced damage. However, most of the existing researches focus only on the dynamic process of material surface damages caused by the interaction between optical materials and lasers, such as temperature distribution, material evaporation, and damaged pit morphological change. Many researches have been conducted on the thermal stress distribution on fused silica material surfaces. However, there are few studies on the stress field distributions inside materials along the direction of an incident laser. This study presents a detailed research and an analysis on temperature and damage morphological distributions of materials and clarifies the interaction mechanism between laser and matter from the three-dimensional stress viewpoint.
Methods To study the three-dimensional stress distribution of laser damaged optical components, this study establishes a finite element thermodynamic model describing the interaction between pulsed CO2 laser and fused silica. This model can simulate temperature evolution inside fused silica during laser irradiation, and can be used to analyze the initial damage morphology of the specimen and three-dimensional stress distribution inside the material after cooling. To ensure the accuracy of the constructed thermodynamic model, this study considers classical heat conduction, heat radiation, and heat loss caused by heat convection on the specimen surface. Solving the heat conduction equation, one can get the internal temperature distribution when laser interacts with fused silica. Simultaneously, using the obtained surface temperature of the specimen, one can get the depth of damage pit. However, a single thermoelastic equation is not enough to completely describe the change in the material cooling process, and the viscoelasticity of materials is also needed to be included to investigate the variation of strain and stress with time. Therefore, a generalized Maxwell model with a single element is introduced to represent the viscoelastic materials, and the three-dimensional stress distribution of laser damaged fused silica can be calculated after the material is cooled. Further, a more in-depth analysis of laser damage can be conducted.
Results and Discussion Based on the model we established above, we obtained the three-dimensional radial stress and hoop stress in fused silica along the direction of the incident laser. As for the difference between the two stresses, the corresponding parameters in the numerical simulation are selected according to the experimental ones, and the comparison between the experimental and simulation results shows that the two stresses have a completely consistent trend, which proves the accuracy of the numerical model describing the interaction between the pulsed CO2 laser and fused silica. Moreover, according to the interpretation of the obtained three-dimensional stress distribution, the radial stress within the depth of the damage pit appears as a compressive stress. The radial stress first increases to the maximum. After exceeding the damage depth, the radial stress gradually decreases until approaches zero. In addition, the internal radial stress of fused silica first reaches the maximum compressive stress value near the bottom of damage pit and then gradually transforms from the radial compressive stress to the tensile stress before gradually decreasing to zero along the axial direction. The hoop stress near damage pit appears as the compressive stress, similar to the radial stress. With the radius value decreasing, the hoop compressive stress is transformed into the tensile stress. The hoop stresses first increase along the z-axial direction until they reach the maximum value and then gradually decrease with the increase of depth until they become zero. In addition, the increase of laser pulse energy leads to the significant increase of the hoop and radial stresses and their influence ranges. These numerical calculation results, especially the three-dimensional hoop and radial stress distributions, are difficult to obtain with the traditional optical measurement technology.
Conclusion The traditional laser damage stress measurement experiment is complicated. It has a huge margin of error, and it is difficult to directly measure the radial and hoop stress distributions through this experiment; only the difference between these two stresses can be measured through this experiment. In this study, a finite element analysis method is used to establish a thermodynamic model describing the interaction between a pulsed CO2 laser and fused silica. Based on the obtained temperature evolution inside fused silica and the initial damage morphology of specimen during the laser heating process, the three-dimensional stress distribution inside the material is calculated. The thermodynamic model considers the classical heat conduction, heat radiation, and heat loss caused by heat convection on the specimen surface. The three-dimensional distribution of the difference between the radial and hoop stresses calculated using this numerical model has the same changing trend as that from the experiment, which proves the accuracy of the numerical model. Based on the calculation of the three-dimensional stress distribution, the relationship between the radial and hoop stress distributions, the depth of damage pit, the distance from damage pit, and laser pulse energy are also analyzed in detail. These results are helpful to establish a three-dimensional stress field inside fused silica and provide a theoretical basis for the improvement of CO2 laser repair process.
1 引言
随着激光技术的不断发展,激光器的输出功率越来越高,熔石英由于其优异的化学稳定性和良好的光学性能,被广泛用于制备透镜、光学窗口和偏振片等光学元件[1]。然而,在高功率激光装置中,熔石英光学元件容易发生损伤[2],损伤点周围的透过率、折射率和应力分布会对入射激光的强度和波前产生调制,影响光束质量,严重时还会对下游光学元件产生级联损伤,导致整个光学系统的性能迅速下降[3-4]。
为了进一步研究激光损伤机制和特性等,研究者开展了大量的研究。Yang等[5]使用红外辐射温度计获得了CO2激光加热下的熔石英玻璃表面温度;Dai等[6]对不同激光参数下的损伤区域的半径和深度进行了定量研究,并分析了样品损伤修复后的损伤耐性;Guignard等[7]基于干涉显微技术研究了熔石英和K9玻璃的残余应力;Gallais等[8]用光弹法研究了修复点周围的残余应力分布。虽然通过实验可以直接获得损伤的形貌、位置和应力分布等多种参数,但是激光损伤机理尚不清楚。建立激光损伤数值模型,并在此基础上深入研究激光损伤的原理、动力学特性以及机制已经成为重要的研究手段[9-12]。相比于实验直接测量,这种基于数值计算的方法能够更加深入地探索激光损伤的过程和产生机制,因此在激光损伤研究中获得了更为广泛的应用。Feit等[13]提出的质量去除模型定量描述了在激光功率和辐照时间影响下的损伤深度;叶成等[14]分别研究了单、双波长激光对熔石英样品损伤形貌以及损伤几率的影响;吴朱洁等[15]提出的二维热力学模型研究了K9玻璃前、后表面附近的损伤概率和损伤形貌,并分析了导致前、后表面损伤的主要因素。然而,大部分工作仅关注激光作用导致的材料表面损伤动力学过程,如温度分布[16-17]、材料蒸发[18]、损伤坑形貌变化[19-21]以及材料表面的热应力分布[22]等,但关于光入射方向的材料内部的应力场研究鲜有报道。研究表明,激光损伤会在熔石英玻璃内部产生应力,应力对入射激光波前的调制作用导致出射激光不均匀,进而可能引起下游光学元件的损伤[23-24]。因此,深入探究激光损伤后光学材料内部的应力变化同样是激光损伤研究的核心问题。
为了深入研究激光损伤中光学材料的三维应力分布,本文首先基于脉冲CO2激光与熔石英玻璃相互作用的有限元热力学模型,在分析讨论熔石英玻璃内部温度分布和表面初始损伤形貌的基础上,重点分析了熔石英玻璃冷却后内部的三维应力分布情况,重点探索了难以实验测量的径向和环向应力随深度和脉冲激光能量的变化。本文不仅对传统的温度和形貌开展了研究与分析,还从应力这一维度阐明了激光与物质相互作用的机理。
2 模型建立
基于熔石英玻璃内部均匀且各向同性这一简化的理论假设,本文使用有限元方法建立了脉冲CO2激光与熔石英玻璃相互作用的热力学模型,如
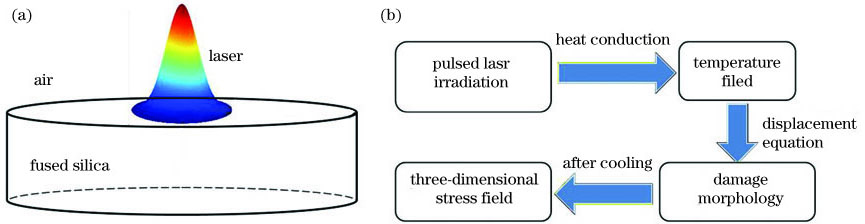
图 1. CO2激光与熔石英玻璃相互作用示意图。(a)三维数值模型;(b)流程图
Fig. 1. Schematic of interaction between CO2 laser and fused silica glass. (a) Three-dimensional numerical model; (b) flow chart
表 1. 熔石英玻璃的热力学参数
Table 1. Thermodynamic parameters of fused silica glass
|
脉冲激光能量被熔石英玻璃表面吸收,热量通过热传导扩散,相应的热传导方程[27]为
式中:ρ、C和k分别是熔石英玻璃的密度、比热容以及热导率;Q是熔石英玻璃吸收脉冲激光能量所产生的热源项;T是温度;t是时间。
为了研究体积热源对温度的影响,考虑激光能量在材料内部的扩散吸收,并假设吸收系数不随温度变化,体积热源(记为Q1)可根据朗伯-比尔定律计算获得[8],即
式中:R是样品表面反射率;r0是1/e2处的激光光斑半径;P(t)是激光功率随时间变化的函数; a是材料的吸收系数;r为径向坐标;z为轴向坐标。
激光功率函数P(t)的表达式为
式中:τ是激光的脉宽。在辐照时间内,激光以固定功率P1照射熔石英玻璃样品表面。
体积热源Q1考虑了熔石英玻璃中激光能量的衰减,且该衰减深度为z,材料的吸收系数根据样品折射率的虚部ni和激光波长λ计算得出[28],即
由于ni在很大程度上取决于温度,因此必须考虑温度对吸收系数a的影响。在这种情况下,本文使用熔石英玻璃的实验测量数据[29]进行数值计算。
材料表面反射率R为
式中:nr为熔石英玻璃折射率的实部。值得注意的是,表面反射率R(取决于折射率)随温度没有明显的变化,可以认为R是一个常数,实际计算中取0.15[28]。
另外,构建的数值模型还考虑了边界条件对温度的影响:
式中:T0是室温300K;h为对流换热系数,在模拟过程中取10W/(m2·K);(x,y,z)为坐标。考虑热传导、热辐射和热对流三种热传递方式,其中温度场求解的初始条件为T=T0。同时,考虑激光辐照过程中样品表面的热辐射损失,取表面辐射率f=0.8。
在此基础上求解热传导方程即(1)式得到熔石英玻璃温度分布,t时刻曲面 [xo,yo,z(t),t]处的凹坑深度[30]为
式中:T[xo, yo, z(t), t]为表面温度;P0为标准大气压;ρliq为熔石英玻璃液相密度;M为熔石英玻璃的相对分子质量;Ue为蒸发潜热;Tb为熔石英玻璃的沸点;R'为理想气体常数。
熔石英玻璃内部受激光加热发生热膨胀而产生材料位移,其热膨胀系数α为5·10-7K-1,并且不随温度明显变化。材料位移U满足
式中:ν为泊松比。
材料位移U在r和z方向上都有分量,其对应位移量分别为u和w,而小位移情况下的应变-位移关系为
式中:εr, εΦ, εz分别为半径方向、圆周切线方向、深度方向的应变。
已知熔石英玻璃的应变场后,可以求得应力场分布为
式中:σr为半径方向的径向应力;σΦ为圆周切线方向的环向应力;σz为深度方向的轴向应力;ε=εr+εΦ+εz;E为杨氏模量。
根据建立的脉冲CO2激光与熔石英玻璃相互作用的热力学模型,首先在考虑热传导、热辐射和热对流所引起的热损失的基础上,准确计算了激光损伤温度分布和表面损伤深度。为了验证有限元方法建立的CO2激光与熔石英玻璃相互作用热力学模型的准确性,使用与参考文献[ 31]中相同的数值参数,计算CO2激光辐照熔石英玻璃后径向和轴向的温度分布,获得与参考文献[ 31]相同的模拟结果,间接证明了热力学模型的准确性。然而,单一的热弹性方程不足以完全描述材料冷却过程中的变化,在此基础上需要考虑材料黏弹性以研究随时间变化的应变和应力,因此引入单分支广义麦克斯韦模型表征黏弹性材料[28],计算材料冷却后激光损伤熔石英玻璃三维应力分布,从而对激光损伤开展更加深入的分析。
3 分析与讨论
在光斑半径r0=350μm以及脉宽τ=1ms的脉冲CO2激光作用下,不同脉冲能量(1, 2.5,5.3J)激光辐照停止时熔石英玻璃内部的温度分布情况及其对应的表面初始损伤形貌如
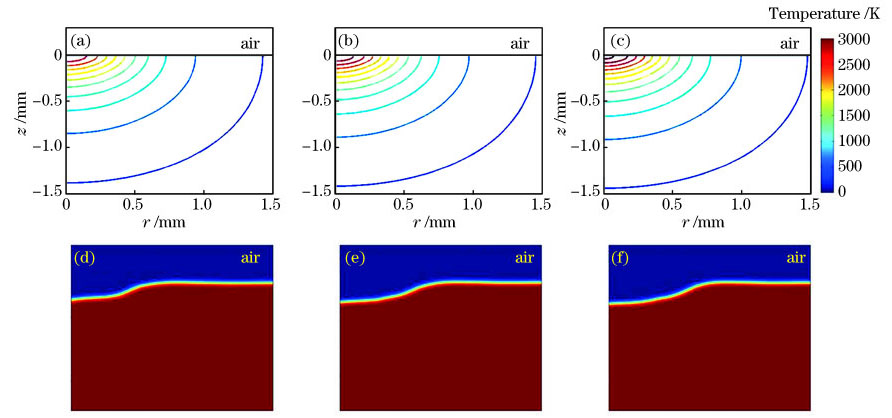
图 2. 不同脉冲能量辐照下样品内部的温度分布和表面初始损伤形貌。(a)(d) 1 J; (b)(e) 2.5 J; (c)(f) 5.3 J
Fig. 2. Temperature distributions inside sample and initial surface damage morphologies under irradiation with different pulse energies. (a)(d) 1 J; (b)(e) 2.5 J; (c)(f) 5.3 J
在加热过程中,熔石英玻璃吸收激光能量导致温度升高,当轴向温度超过熔石英玻璃软化温度(1850K)时,材料蒸发;而当轴向温度超过熔石英玻璃的沸点(2500K)时,材料汽化[28]。对于不同激光能量,样品表面损伤也并不相同,如
在激光辐照过程中,熔石英玻璃内部受热发生热膨胀,进而产生应变,应变会使初始的样品表面变形,从而降低光学元件表面质量。受热区域的熔石英玻璃较软,可以通过较小的材料位移释放热应力,当脉冲激光作用结束后,熔石英玻璃表面逐渐冷却,而内部材料无法移动,应力被“固定”在熔石英玻璃中,进而产生残余应力[32]。但是,在凹坑底部附近,材料在生成的凹坑边缘发生位移,释放了部分热应力[8]。随着冷却的进行,已发生热膨胀的固体材料会退回其初始位置,但是凹坑附近的材料由于损伤点的存在以及周围材料的受压约束而不能完全返回,因此在凹坑周围区域产生压应力。同时,由于固体和液体材料的相互作用以及快速的冷却速率,在材料内部出现拉应力。
但是在实际测量过程中,基于偏振测量的众多光学方法[8,33-36]测量所得的是两主应力之差,实际上是熔石英玻璃内部径向应力与环向应力之差,即σr-σΦ。因此本文在数值计算中首先考虑了实验能够测量得到的径向环向应力差。在不同能量的激光辐照停止后,熔石英玻璃逐渐冷却至室温,此时不同样品深度下的平面径向环向应力差分布如
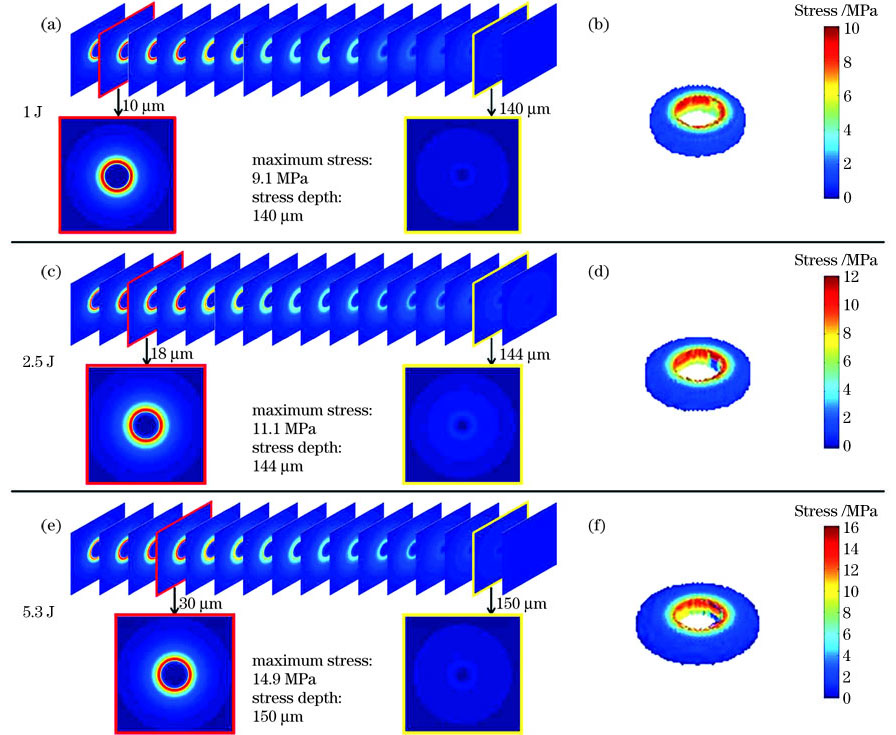
图 3. 不同脉冲能量下的二维和三维应力分布。(a)(b) 1J;(c)(d) 2.5J;(e)(f) 5.3J
Fig. 3. Two- and three-dimensional stress distributions under different pulse energies. (a)(b) 1J; (c)(d) 2.5J; (e)(f) 5.3J
为了进一步验证本文建立的脉冲CO2激光与熔石英玻璃相互作用的数值模型的准确性,使用本课题组构建的三维白光反射式全息显微系统,测量了存在激光损伤的熔石英玻璃的内部应力分布,其中激光是波长为10.6μm的CO2激光,脉冲激光能量为5.3J。在数值模拟中,根据实验选择相应的参数,
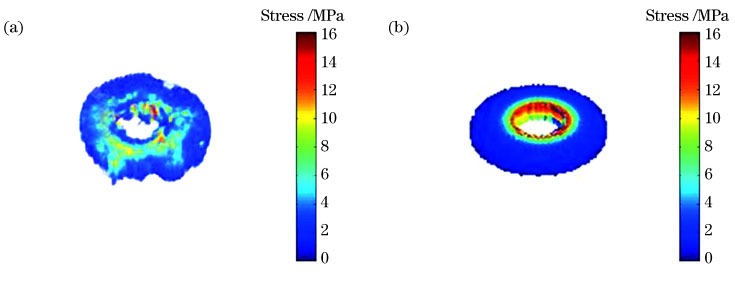
图 4. CO2激光损伤下的三维应力分布。(a)实验结果; (b)模拟结果
Fig. 4. Three-dimensional stress distributions under CO2 laser damage. (a)Experimental result; (b) simulation result
在实际情况中,相较于径向环向应力差这一相对值,分析径向应力和环向应力更有利于直观分析激光损伤元件性质。但是实验无法直接测量出熔石英玻璃内部的径向应力和环向应力分布,因此相较于直接实验测量,使用数值计算的方法能够获得更加直观的结果。在验证了数值模型的准确性后,本文进一步研究了径向应力σr和环向应力σΦ的分布情况,在上述相同激光能量辐照情况下,熔石英玻璃内部不同深度处的径向和环向应力分布情况如
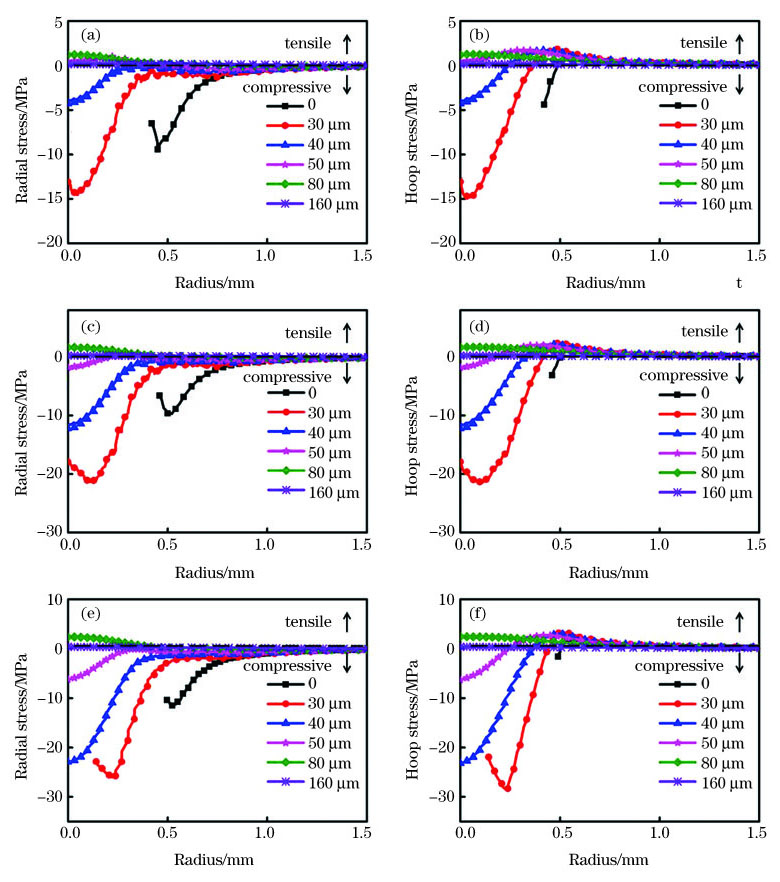
图 5. 不同激光能量下,不同样品深度处的径向应力和环向应力分布。(a)(b) 1 J; (c)(d) 2.5 J; (e)(f) 5.3 J
Fig. 5. Radial stress and hoop stress distributions at different sample depths under different laser energies. (a)(b) 1 J;(c)(d) 2.5 J; (e)(f)5.3 J
相较于径向应力,熔石英内部的环向应力分布情况更为复杂,损伤凹坑附近的环向应力与径向应力相似,均表现为压应力,但沿着半径方向,环向压应力转化为拉应力,在达到最大值后沿半径方向逐渐减小并趋近于零,如
最后研究了不同脉冲激光能量辐照下不同深度处熔石英玻璃的应力分布情况,如
以上数值模拟结果表明,利用本文建立的脉冲CO2激光与熔石英玻璃相互作用的数值模型不仅能够获得与实际实验测量一致的径向环向应力差,还能够直接获得径向和环向上的应力三维分布。另外,根据获得的三维应力分布可知,损伤凹坑深度范围内的径向应力表现为压应力,径向应力沿半径方向先增至最大后逐渐减小并趋近于零,超过损伤深度处的径向应力沿径向逐渐减小并趋近于零。此外,熔石英内部的径向应力在损伤凹坑底部附近取得最大值,并逐渐由径向压应力转化为拉应力,之后沿轴向逐渐减小为零;损伤凹坑附近的环向应力与径向应力相似,均表现为压应力,但沿着半径方向减小至零后,环向压应力转化为拉应力,在达到最大值后沿半径逐渐减小并趋近于零,此外,不同深度处的环向应力沿轴向先增大后减小,且无论是环向压应力还是拉应力,均在几乎相同深度处取得最大值,环向应力沿轴向逐渐减小至零;脉冲激光能量的增大导致环向应力与径向应力及其影响范围均有明显增加。这些数值计算结果,尤其是三维环向应力与径向应力的分布,是传统光学测量技术难以获得的。由于平面内各个参考点的折射率各不相同,材料特性由各向同性改为各向异性,不同分层下的径向应力和环向应力对通过该平面的入射激光波前有调制作用,入射激光的波前变化是各个分层影响的累加。关于应力对入射光的波前调制研究将是后续工作内容。
4 结论
使用有限元分析的方法建立了脉冲CO2激光与熔石英玻璃相互作用的数值模型,在获得激光加热过程中熔石英玻璃内部的温度演变规律及样品的初始损伤形貌的基础上,计算了材料内部的三维应力分布。该计算模型不仅考虑了经典的热传导与热辐射,还考虑了样品表面热对流所引起的热损失。对于存在激光损伤的熔石英玻璃内部的环向径向应力之差的三维分布,使用该模型获得的结果和使用三维白光反射式全息显微系统实际测量的结果吻合,证明了构建模型的准确性。此外,在计算三维应力分布的基础上,详细分析了径向应力和环向应力的分布与损伤坑深度、离损伤坑的距离和脉冲激光能量的关系。所得结果有助于熔石英玻璃内部三维应力场的建立,并为CO2激光修复工艺的改进提供了理论依据。
[3] 王家秋, 罗帅, 张彬. 热-机械耦合作用下黏结材料对变形镜应力特性的影响[J]. 激光与光电子学进展, 2018, 55(3): 030104.
[4] 曹珍, 贺洪波, 胡国行, 等. 多脉冲激光诱导熔石英体损伤的时间分辨研究[J]. 中国激光, 2019, 46(8): 0803001.
[7] Guignard F, Autric M, Baudinaud V. Temperature and residual stress evolution in CO2 laser irradiated glass[J]. Proceedings of SPIE, 1998, 3343: 534-545.
[8] Gallais L, Cormont P, Rullier J L. Investigation of stress induced by CO2 laser processing of fused silica optics for laser damage growth mitigation[J]. Optics Express, 2009, 17(26): 23488-23501.
[9] 李长安, 杨明冬, 全本庆, 等. 多层薄膜沉积的应力仿真分析[J]. 激光与光电子学进展, 2018, 55(4): 043101.
[10] 徐娇, 陈丽霞, 游兴海, 等. 表面杂质诱导薄膜元件的热应力损伤[J]. 光学学报, 2017, 37(6): 0614003.
[11] 钟发成, 吕雪明, 李佳桂, 等. 组合激光对单晶硅热作用的数值分析[J]. 激光技术, 2017, 41(5): 637-643.
[12] 李贺, 蔡继兴, 谭勇, 等. 毫秒激光辐照单晶硅的在线应力损伤研究[J]. 光学学报, 2016, 36(2): 0219002.
[14] 叶成, 邱荣, 蒋勇, 等. 1064 nm和532 nm纳秒激光同时辐照熔石英损伤规律的研究[J]. 强激光与粒子束, 2018, 30(4): 041003.
[15] 吴朱洁, 潘云香, 赵竞元, 等. 毫秒激光辐射K9玻璃的激光损伤研究[J]. 红外与激光工程, 2019, 48(8): 0805005.
[16] 张英聪, 沈华, 朱日宏. 连续激光辐照材料的三维温度场[J]. 中国激光, 2013, 40(8): 0806002.
[17] 严会文, 白忠臣, 秦水介, 等. 激光与熔融石英作用的温度累积研究[J]. 应用激光, 2015, 35(1): 44-47.
[18] 李世雄, 白忠臣, 黄政, 等. 激光诱导等离子体加工石英微通道机理研究[J]. 物理学报, 2012, 61(11): 115201.
Li S X, Bai Z C, Huang Z, et al. Study on the machining mechanism of fabrication of micro channels in fused silica substrates by laser-induced plasma[J]. Acta Physica Sinica, 2012, 61(11): 115201.
[19] 李熙斌, 王海军, 袁晓东, 等. CO2激光辐照对熔石英表面形貌与应力分布的影响[J]. 中国激光, 2011, 38(9): 0903002.
[20] Bertussi B, Cormont P, Palmier S, et al. Initiation of laser-induced damage sites in fused silica optical components[J]. Optics Express, 2009, 17(14): 11469-11479.
[21] 韩敏, 聂劲松, 叶庆, 等. 1.06 μm连续激光损伤CCD的进程及损伤对成像能力的影响[J]. 中国激光, 2018, 45(9): 0901004.
[22] 李世雄, 张正平, 秦水介, 等. 单个脉冲作用下熔融石英的温度和热应力研究[J]. 激光与红外, 2016, 46(7): 786-791.
Li S X, Zhang Z P, Qin S J, et al. Research on the temperature and thermal stress of fused silica irradiated by a laser pulse[J]. Laser & Infrared, 2016, 46(7): 786-791.
[23] Yang L, Liao W, Miao X X, et al. Quantitative measurement of CO2 laser-induced residual stress in fused silica optics[J]. Optical Engineering, 2015, 54(5): 057105.
[24] 渠旭, 蔡继兴, 王翼彬, 等. 1064 nm激光致熔石英损伤的数值模拟研究[J]. 强激光与粒子束, 2017, 29(4): 041003.
[25] Allcock G, Dyer P E, Elliner G, et al. Experimental observations and analysis of C O2laser-induced microcracking of glass[J]. Journal of Applied Physics, 1995, 78(12): 7295-7303.
[26] Rozenbaum O. De Sousa Meneses D, Auger Y, et al. A spectroscopic method to measure the spectral emissivity of semi-transparent materials up to high temperature[J]. Review of Scientific Instruments, 1999, 70(10): 4020-4025.
[27] Santos R. Miranda L C M. Theory of the photothermal radiometry with solids[J]. Journal of Applied Physics, 1981, 52(6): 4194-4198.
[28] Doualle T, Gallais L, Cormont P, et al. Thermo-mechanical simulations of CO2 laser-fused silica interactions[J]. Journal of Applied Physics, 2016, 119(11): 113106.
[30] Robin L, Combis P, Cormont P, et al. Infrared thermometry and interferential microscopy for analysis of crater formation at the surface of fused silica under C O2laser irradiation[J]. Journal of Applied Physics, 2012, 111(6): 063106.
[31] Yang S T, Matthews M J, Elhadj S, et al. Comparing the use of mid-infrared versus far-infrared lasers for mitigating damage growth on fused silica[J]. Applied Optics, 2010, 49(14): 2606-2616.
[32] Gardon R, Narayanaswamy O S. Stress and volume relaxation in annealing flat glass[J]. Journal of the American Ceramic Society, 1970, 53(7): 380-385.
[33] Dahmani F, Schmid A W, Lambropoulos J C, et al. Dependence of birefringence and residual stress near laser-induced cracks in fused silica on laser fluence and on laser-pulse number[J]. Applied Optics, 1998, 37(33): 7772-7784.
[34] 张伟, 朱秋东, 张旭升. 平板玻璃中部应力的偏振移相检测法[J]. 光学学报, 2018, 38(4): 0426001.
[35] Puncken O, Tünnermann H, Morehead J J, et al. Intrinsic reduction of the depolarization in Nd: YAG crystals[J]. Optics Express, 2010, 18(19): 20461-20474.
孙劭伟, 齐乃杰, 孔艳, 刘诚, 高淑梅. 熔石英玻璃激光损伤的三维应力场研究[J]. 中国激光, 2021, 48(1): 0101001. Shaowei Sun, Naijie Qi, Yan Kong, Cheng Liu, Shumei Gao. Three-dimensional Stress Fields of Laser Damaged Fused Silica[J]. Chinese Journal of Lasers, 2021, 48(1): 0101001.